XX公司品质检验标准
公司产品质量检验标准

公司产品质量检验标准导言:在现代市场经济中,产品质量是企业生存和发展的基石。
为确保公司产品质量并满足客户需求,制定一套严格的质量检验标准至关重要。
本文旨在介绍公司产品质量检验标准的重要性,以及制定和执行该标准的方法和程序。
一、质量检验标准的意义1.客户满意度:质量检验标准是保证产品质量的重要手段,通过明确产品的质量要求和检验方法,能够有效减少产品质量问题,提高产品质量,满足客户需求,增强客户满意度。
2.企业声誉:公司产品的质量是企业形象和信誉的重要体现。
有一套完善的质量检验标准,能够为企业树立良好的品牌形象,增强企业竞争力。
3.效率提升:通过质量检验标准,能够指导生产制造过程中的质量控制,及时发现和解决问题,减少产品不合格,提升生产效率,降低成本,实现持续改进和发展。
二、质量检验标准的制定方法1.明确质量指标:根据公司产品的特点和行业要求,明确产品的质量指标,例如产品的外观、尺寸、材质、性能等。
同时,要考虑用户需求和市场反馈,确保质量指标与市场需求相匹配。
2.制定检验方法:根据产品的质量指标,制定相应的检验方法。
检验方法应该具有科学性、可操作性和有效性,能够准确判断产品是否符合质量要求。
3.确定检验标准:通过对产品性能、技术指标等方面的测试和比较,确定产品的质量检验标准。
这些标准可以参考国家标准、行业标准以及公司内部的专业标准。
三、质量检验标准的执行程序1.采样:按照一定的规则和方法,从生产批次中抽取样品进行检验。
采样方法应该具有代表性,能够准确反映整个批次产品的质量状况。
2.检验:根据质量检验标准,对样品进行检验,包括外观、尺寸、性能等方面的检测。
检验应该由专业人员进行,并确保检验结果的准确性和可靠性。
3.判定:根据检验结果,判断样品是否符合质量标准要求。
如果样品合格,则整个批次产品可以继续流通;如果样品不合格,则需要采取相应的纠正措施,例如修复、返工或报废等。
4.记录和报告:对每一次的质量检验结果进行记录,并及时形成检验报告。
品质检验标准
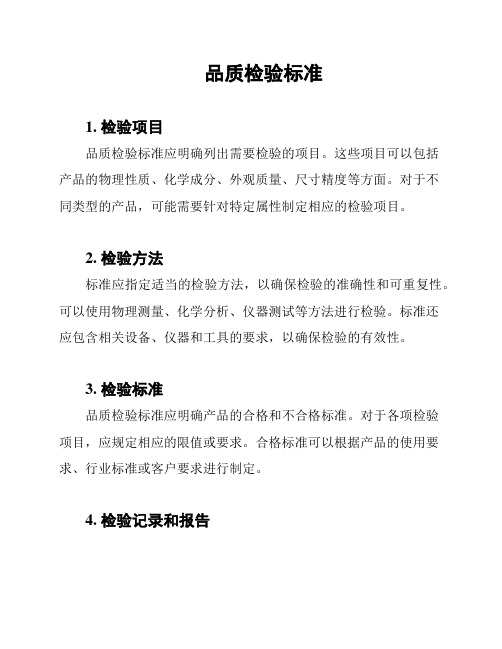
品质检验标准
1. 检验项目
品质检验标准应明确列出需要检验的项目。
这些项目可以包括
产品的物理性质、化学成分、外观质量、尺寸精度等方面。
对于不
同类型的产品,可能需要针对特定属性制定相应的检验项目。
2. 检验方法
标准应指定适当的检验方法,以确保检验的准确性和可重复性。
可以使用物理测量、化学分析、仪器测试等方法进行检验。
标准还
应包含相关设备、仪器和工具的要求,以确保检验的有效性。
3. 检验标准
品质检验标准应明确产品的合格和不合格标准。
对于各项检验
项目,应规定相应的限值或要求。
合格标准可以根据产品的使用要求、行业标准或客户要求进行制定。
4. 检验记录和报告
为了保证品质检验的可追溯性,标准应规定检验记录和报告的要求。
记录应包括检验项目、检验方法、检验结果等信息。
报告应明确标识产品的品质状态,并提供必要的证明和支持文件。
5. 反馈和改进
标准应鼓励对检验结果进行反馈和改进。
当产品不符合检验标准时,应制定相应的纠正和预防措施,以确保类似问题不再发生。
检验结果和改进措施应记录并保存,用于持续改进产品的品质。
6. 标准更新
品质检验标准应定期进行评估和更新,以适应技术和行业的发展。
标准的更新应经过充分的研究和讨论,并依据可靠数据和信息进行调整。
以上是关于品质检验标准的一些基本要点。
通过严格遵守和执行这些标准,厂家和生产者可以提高产品的品质,满足市场需求,并增强竞争力。
公司产品质量检测标准
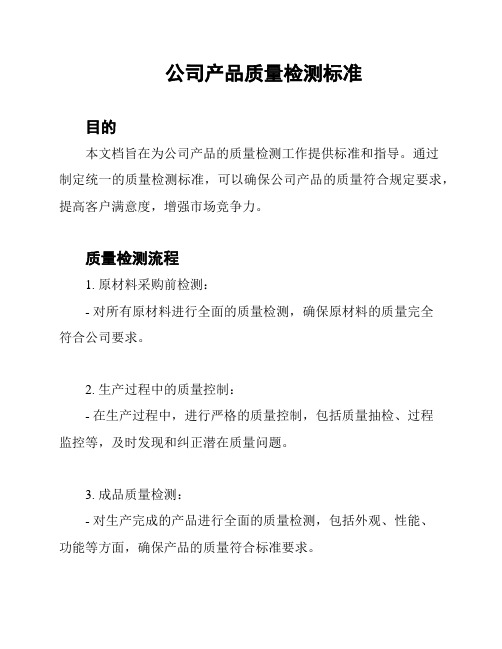
公司产品质量检测标准目的本文档旨在为公司产品的质量检测工作提供标准和指导。
通过制定统一的质量检测标准,可以确保公司产品的质量符合规定要求,提高客户满意度,增强市场竞争力。
质量检测流程1. 原材料采购前检测:- 对所有原材料进行全面的质量检测,确保原材料的质量完全符合公司要求。
2. 生产过程中的质量控制:- 在生产过程中,进行严格的质量控制,包括质量抽检、过程监控等,及时发现和纠正潜在质量问题。
3. 成品质量检测:- 对生产完成的产品进行全面的质量检测,包括外观、性能、功能等方面,确保产品的质量符合标准要求。
4. 质量报告和记录:- 每一批产品质量检测完成后,及时生成质量报告,并进行记录,以备后续追溯和分析。
5. 不合格产品处理:- 对于不符合质量要求的产品,采取及时的整改措施,修正质量问题,确保产品符合质量标准。
6. 客户投诉处理:- 对于客户投诉的产品质量问题,进行及时调查并处理,确保客户满意度和信任度。
检测标准1. 外观检测:- 检查产品的外观是否符合设计要求,包括颜色、形状、尺寸等方面。
2. 功能性检测:- 根据产品的功能要求,进行相应的功能性检测,确保产品的性能和功能正常。
3. 安全性检测:- 对产品的安全性进行检测,包括使用过程中是否存在安全隐患等方面。
4. 耐久性检测:- 对产品的耐久性进行检测,包括产品的使用寿命、耐用性等方面。
5. 抗压性检测:- 对产品的抗压性进行检测,确保产品在正常使用过程中不易变形或损坏。
注:以上检测标准仅为示例,具体检测标准应根据公司产品的特点和要求进行制定。
检测设备和方法1. 质量检测设备:- 配备先进的质量检测设备,确保检测结果准确可靠。
2. 检测方法:- 根据产品的特点和要求,确定相应的检测方法,确保检测工作的科学性和有效性。
质量检测责任1. 质量部门:- 负责组织和实施产品的质量检测工作,并确保检测结果的准确性和可靠性。
2. 生产部门:- 配合质量部门的工作,确保生产过程中的质量控制和质量检测工作的顺利进行。
某公司质量检验流程及主要检验标准
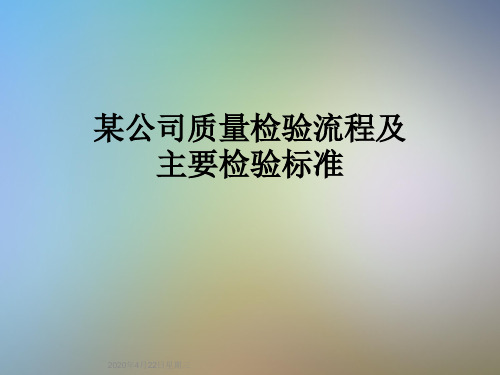
4.产品质量检验
➢ 公司自投产以来,始终坚持全过程的质量控制理念,从原 材料入厂到成品出厂的整个生产流程上合理的配置资源, 建立了完善的质量检验检测体系。
➢ 在主要生产工序上,共设置了12个专业质量检查站,确保 各工序转移产品质量合格;
➢ 武汉商检所常年驻厂监制、复检;
4.产品质量检验—检验流程图
5.各工序主要检验标准
4.端面切斜度
5.各工序主要检验标准
5.弯曲度
5.各工序主要检验标准
三、熔炼分析 执行Q/TGGK01-2004“管坯牌号和化学成分表”
四、酸浸低倍 执行TGGJ05-2000
5.各工序主要检验标准
酸浸低倍检出的缺陷有: 皮下裂纹、皮下气泡、中不裂纹、心部裂纹、锁孔
、洁净度、翻皮、白点、异金属夹杂物等,各类缺 陷级别为0~3级、0~4级或0~5级不等。
5.2检验批大小 ——一个检验批中产品的数量。 5.3检验批样本 ——从一个检验批中抽取的一个或多个能够 代表该检验批的产品。
1.有关质量的概念和术语
举例说明 GB5310-95检验批大小
1.有关质量的概念和术语
GB5310-95检验批样本
1.有关质量的概念和术语
API 5CT
1.有关质量的概念和术语
1.有关质量的概念和术语
➢全面质量管理阶段:全员、全过程、全企业的质量管理,强 调过程质量控制,争取一次把事情做好。
1.有关质量的概念和术语
3.验证——通过对供方提供的客观证据(如质量证明书、检验 报告等)进行检查,并与规定要求进行比较,确认其是否合格 的活动。 4.试验——按照程序确定一个或多个特性。
1.有关质量的概念和术语
13. 过程能力指数 CPK (Process Capability index) ——过 程能力指数,是指工序在一定时间里,处于控制状态(稳定状 态)下的实际加工能力。它是工序固有的能力,或者说它是工 序保证质量的能力。 ➢CPK计算方法:
XX公司进货检验及验证记录
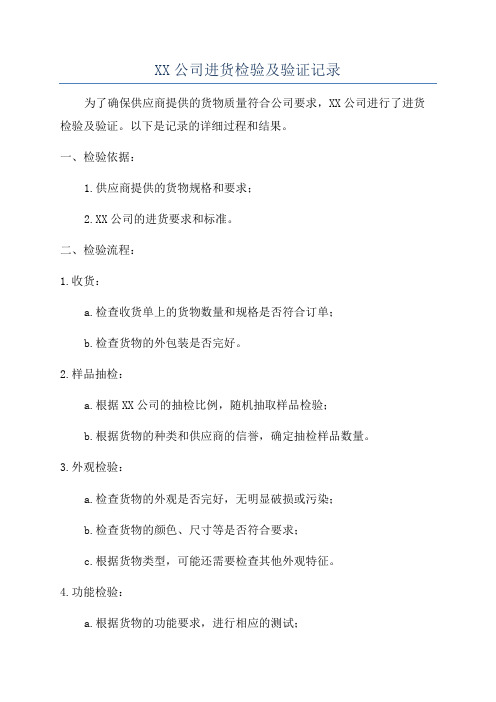
XX公司进货检验及验证记录为了确保供应商提供的货物质量符合公司要求,XX公司进行了进货检验及验证。
以下是记录的详细过程和结果。
一、检验依据:1.供应商提供的货物规格和要求;2.XX公司的进货要求和标准。
二、检验流程:1.收货:a.检查收货单上的货物数量和规格是否符合订单;b.检查货物的外包装是否完好。
2.样品抽检:a.根据XX公司的抽检比例,随机抽取样品检验;b.根据货物的种类和供应商的信誉,确定抽检样品数量。
3.外观检验:a.检查货物的外观是否完好,无明显破损或污染;b.检查货物的颜色、尺寸等是否符合要求;c.根据货物类型,可能还需要检查其他外观特征。
4.功能检验:a.根据货物的功能要求,进行相应的测试;b.使用适当的设备和工具进行测试;c.检查货物是否满足功能要求。
5.温湿度检验:a.如果货物对温湿度要求比较高,检测货物的温湿度是否在要求范围内。
6.样品保留:a.检验合格的样品保留一定数量;三、检验结果:1.合格:a.检验结果符合货物的规格和要求;b.符合XX公司的进货要求和标准。
2.不合格:a.检验结果不符合货物的规格和要求;四、记录和保存:1.对每次进货检验进行详细记录,包括:a.检验日期、时间和地点;b.检验人员和样品信息;c.检验结果和意见;d.检验后的处理和反馈。
2.检验记录保存至少一年,以备参考和追溯。
五、持续改进:1.根据进货检验的结果和反馈,优化进货标准和要求;2.对供应商的质量控制进行定期评估和审核。
以上是XX公司的进货检验及验证记录。
通过严格的检验流程和有效的记录保存,XX公司确保所采购的货物质量符合要求,并持续优化进货标准和要求,以提高供应链的效率和质量。
IQC品质检验报告

IQC品质检验报告日期:2024年10月20日检验单位:XX公司检验对象:产品A检验标准:Q/XX-001-2024一、检验目的:本次检验旨在确认产品A的主要材料和零部件的质量状况是否符合公司的质量标准,以确保产品的质量稳定和可靠性。
二、检验内容:1.检验产品A的外观质量,包括表面光洁度、颜色一致性等。
2.检验产品A的尺寸和形状是否符合设计要求。
3.检验产品A的机械性能,包括拉伸强度、抗压强度等。
4.检验产品A的耐磨性和耐腐蚀性。
三、检验方法:1.外观检验:通过目测和触摸,检验产品的表面是否平整、光滑,颜色是否均匀。
2.尺寸和形状检验:使用千分尺和量规等工具,测量产品的各个尺寸和形状参数。
3.机械性能检验:使用拉力试验机和压力试验机等设备,测试产品的拉伸强度和抗压强度。
4.耐磨性和耐腐蚀性检验:通过摩擦测试和腐蚀试验,评估产品的耐磨性和耐腐蚀性能。
四、检验结果:1.外观质量:产品A的外观质量良好,表面光洁度高,颜色均匀一致。
2.尺寸和形状:产品A的尺寸和形状符合设计要求,各项参数稳定可靠。
3.机械性能:产品A的拉伸强度和抗压强度均达到标准要求,具有较高的可靠性。
4.耐磨性和耐腐蚀性:产品A经过耐磨性和耐腐蚀性测试,表现出较好的耐用性和稳定性。
五、结论:产品A经过本次IQC品质检验,各项指标均符合公司的质量标准,具有良好的外观质量、尺寸稳定性和机械性能。
建议在生产过程中进一步加强质量控制,确保产品品质的稳定和可靠性。
六、检验人员:主检人:XXX检验员:XXX。
XX公司品质检验标准要点

濕空氣被凝聚。 1.30 濺渣—焊點周圍因焊接作業產生的小金屬顆粒。 1.31 脫焊—焊點分離。 1.32 燒傷—點焊或熔接作業因溫度過高而產生。 1.33 焊痕—焊接后留下的痕跡,塗裝后仍可見到。 1.34 膜厚—產品表面處理層的厚度。 1.35 硬度—塗料、材料質地堅固程度。 1.36 附著性—表面涂膜處理層或印刷,燙金與母材之間的結合力。 1.37 光澤度—產品表面的光澤反射率。 1.38 耐衝擊性—表面涂膜層與母材之間的結合程度 及塗膜堅韌程度。 1.39 耐溶劑性—表面涂膜層,印刷及燙金與酒精的化學反應。 1.40 耐磨性—表面涂膜層,印刷及燙金的耐磨程度。 1.41 流漆—塗裝后表面有單個或多個如水滴般的漆點。 1.42 凝漆—塗裝后漆面有單一的漆團,此漆團與噴點明顯不同。 1.43 溢漆—噴到不需要或不得噴到漆的地方。 1.44 魚眼—某個區域固定出現不同亮度的魚眼形亮點。 1.45 橘皮—表面出現類似橘子皮之狀況。 1.46 磨痕—指研磨后所造成的痕跡。 1.47 掉漆—漆異常脫落,如碰、撞…等。
4.2.5 觀察時間(見下表):
檢測員 0.8以上(含矯正后)
待測物
(示意圖)
Code Viewing Time
CiassA 7 秒/100mm×100mm
CiasB 5 秒/100mm×100mm
CiasC 3 秒/100mm×100mm
5.1 所有的機構、電器特性、功能要求以圖面為准,關於機 構尺寸公差如圖面 未 直 接 於 尺 寸 后 標 注 其 公 差,則 本 公 司 孔 的 尺 寸 公 差 以 ±0.07mm 管 制,其 他 尺寸以±0.20mm 進行管制,除非客戶有更為嚴格或特別要求。 QE 人員可視 需要在 SIP 制定時縮小其公差,以利於生產管制,如東驊供貨商的產品有 因 SIP 縮小公差管制的問題被判拒收,且可証實是東驊事前未有通知廠商 時,當批可以東驊盡量吸收的原則協調處理,但供貨商必須於下批改善。
公司检验标准

1.目的为了使本厂原材料检验、半成品过程检验、成品检验严格按标准实施,确保产品质量稳定,满足顾客需求。
2.范围本标准适用于质检部实施首检、抽检、终检全过程的控制。
3.职责3.1质检部主管负责按国家标准要求:即①《冷扎钢板和钢带尺寸、外形、重量及允许编差》。
(GB708-88)②《热扎钢板和钢带尺寸、外形、重量及允许编差》(GB709-88)及本厂制订的检验标准,开展质量检验工作。
确保成品、半成品合格率100%。
3.2采购部主管负责按本标准采购,并要求供方提供《产品质量报告》即①化学成份;②力学性能;③金相组织(钢晶力度6-10级)。
4.检验标准4.1.3本厂原材料检验常规性检验关注点:4.1.3.1 冷轧钢(热轧板)a、长度、宽度、厚度的尺寸按采购单要求验收;b、表面的平整度和粗糙度。
(无划伤、无锈蚀、无变形、无剥裂);c、硬度;(由采购部进料时抽样测试并提供相关检测报告)d、数量是否缺少;(由原料仓库员清点)4.1.3.2 特殊材料(如:不锈钢、不锈铁、耐垂纹等),根据产品要求进行进料检验a、规格(长度、宽度、厚度的尺寸按采购单验收);b、表面平整、无刮划痕迹,覆膜无划破、无脱皮现象;c、镜面材料是否达到产品要求的效果;d、硬度;(由采购部进料时抽样测试并提供相关检测报告)测量工具:千分尺、卷尺;测量方法:目测、破坏性试验。
4.2各工序检验标准4.2.1激光割(A工序)检验标准。
a. 钢板利用率95%以上;b. 尺寸公差±0.12mm;c. 表面:平整、无锈蚀、无剥裂、无划伤、无变形;d. 成型件无毛刺;e. 成型件按型号、规格分类摆放整齐;f. 首检品有标示,g. 不接受上道工序不合格品;h. 新员工有培训记录。
测量工具:游标、千分尺、卷尺;测量方法:目测、4.2.2数控冲(B工序)检验标准。
a. 材料利用率95%以上b. 完全冲透无冲压痕迹;c. 表面:平整、无锈蚀、无划伤、无变形、无毛刺{毛刺高度L≤5%t(t为板厚)};d. 尺寸公差±0.12mm;e. 首检品有标示,f. 成型件按型号、规格分类摆放整齐;g. 不接受上道工序不合格品;h. 新员工有培训记录。
- 1、下载文档前请自行甄别文档内容的完整性,平台不提供额外的编辑、内容补充、找答案等附加服务。
- 2、"仅部分预览"的文档,不可在线预览部分如存在完整性等问题,可反馈申请退款(可完整预览的文档不适用该条件!)。
- 3、如文档侵犯您的权益,请联系客服反馈,我们会尽快为您处理(人工客服工作时间:9:00-18:30)。
缺點類型
1.產 品 缺 點 類 型 (除 包 裝 材 料 以 外 之 產 品 ) 刮傷—因受外在影響對產品表面造成之線凹痕或痕跡 (分有感刮
傷和無感刮傷。以指甲輕刮受損部位,如有指甲受阻及斷差感則為有感刮 傷)。
凹 凸 痕 — 材 料 受 力 撞 擊 /擠 壓 或 加 工 作 業 造 成 表 面 異 常 凸 起 或 凹 陷 (表 面 並 未 出 現 目 視 可 見 的 破 裂 )。
(切斷面斑點鏽 斷 面 斑 點 鏽 蝕 不 允 斷 面 斑 點 狀 鏽 蝕 允
蝕不允許) 許)
許)
面積≦
面積≦2.0mm2 允
面積≦4.0mm2 允
0.3mm2 允許 1 處 許 2 處
許3處
擦傷
臟污
拉模 變形 材質不符
色差
針孔 電極黑影 電擊
不允許
不允許
不允許 不允許 不允許
不允許
不允許 不允許 不允許
1 表面等級區 電腦機殼等級面定義: 4.1.1.1 A 級面:指在操作或使用時客戶經常可見的表面,如產 品的正面、上面、兩側面。通常會進行重點的裝飾和表面處理,如 塗裝、咬花、裝飾性電鍍、印刷、燙金等。在上面與側面部份如果 未進行類似重點的裝飾和表面處理時可視為 B 級面。 4.1.1.2 B 級面:在操作或使用時客戶只是偶爾看到的表面,如 后面、底面邊緣部份。通常進行適度的裝飾和表面處理。 4.1.1.3 C 級面:正常的操作和使用時客戶基本上看不見,通常 只有通過正常操作外的移動、翻轉、拆卸等動作才能看見的面,如 底面、產品內部各面。
有爭議的缺點項目,若同時經五位以上檢驗員,判定為允收時,則該缺失 列為允收,如仍有質疑時,轉請品管部門主管人員裁示。
對模稜兩可的缺失,雖檢驗員初次檢驗判為允收,但第二次檢驗發現屬缺 失時,仍判定為不合格,若有爭議, 轉請品管部門主管人員裁示。
如產品在前段檢驗過程中發現各項品質標准所列缺失,而在后制程加工可 以掩蓋,其完工后品質特性未降低者,在制造者的申請下,該缺失項目可列為 允收(如鐵材外觀缺失在衝制過程中會被切除;電鍍、烤漆可掩蓋的缺陷;烤 漆 溢 漆 等 )。
(兩 用 型 水 平 式 圖 示 )
4.1.3 Notebook 等級面定義
4.1.3.1 A 級面:機台前面、上面(背蓋)及掀開 LCD 后機台正
面部分。
4.1.3.2 B 級面:機台兩側面。
4.1.3.3 C 級面:機台底部及機台后側面。
4.1.4 Notebook 等級面參考圖
A面 B面
C面(機台底部)
產品設計為可開啟的面板內面、拉門內面等,該面列為 A 面。如零部件產 品有用於散件出貨,則其等級面定義比照進行,通常定為 A 級面,可明顯判斷 為背立面時定為 B 級面。
產品的平面度需符合圖面或客戶要求。通常以不超過該部位全長的 2/1000 為驗收標准。
3
當所述之相關品質標准有衝突時,以符合所有品質標准之水准為原則進行 判定。
斷 線 — 指 印 刷 的 油 墨 于 印 刷 時 由 于 太 濃 或 表 面 不 平 (如 咬 花、雜 質 ),而 無 法到達適當位置,而有中途不全的現象。 重影—指印刷圖案有兩層或以上的陰影,常出現于重覆印刷。 不全—指印刷作業過程中,因作業疏忽,造成圖案不完整。 字符圖案—字的形體以及圖的形狀與式樣。 錯位—未依規定位置進行加工。 缺件—未依規定數量進行加工。 錯件—未依規定零件進行加工。 欠鑄—壓鑄件因注料不足或因模具因素造成產品殘缺。 冷料—產品表面有一層未能完全溶合的材料。
撞傷—材料受力撞擊而造成的損傷,且產品表面有破裂受損及斷 差感。 擦傷—指材料表面因相互接觸摩擦所導致的損傷。
臟污— 一般為加工過程中,不明油漬或污物附著造成。 雜質—通常是產品表面處理層中含有無法去除的雜物。 變形—指因扭曲、擠壓、撞擊等因素導致的外觀形狀與機構特性 的變異。 材質不符—使用非指定的原材料。 斷裂—部份材料与主體分离斷裂或產生裂紋。 毛邊—在產品邊緣棱角部位出現的粗糙或尖銳凸起物。 異色—與基材顏色有差異之塊、線、點狀不良。 修飾不良—人為的一些修飾動作不當所造成。 色差—顏色與標准的偏差。 氧化—金屬材料與空氣中的氧起化學變化,而失去原有特性,如
5
凝漆—塗裝后漆面有單一的漆團,此漆團與噴點明顯不同。 溢漆—噴到不需要或不得噴到漆的地方。 魚眼—某個區域固定出現不同亮度的魚眼形亮點。 橘皮—表面出現類似橘子皮之狀況。 磨痕—指研磨后所造成的痕跡。 掉漆—漆異常脫落,如碰、撞…等。 異物殘留—在生產制程中,由于作業疏忽,致外物殘留于工件。 溢墨—指印刷的油墨于印刷時由于太稀或表面不平,而四處溢流。
4.1.2 電腦機殼等級面參考圖:
4.1.2.1 純直立式:
A 級面 兩側 面
A 級面 前面及
上面(
B 級面 后板面及底面邊緣部份
A面 左側面 (臥放 時的上面)
A面 上
4.1.2.2 兩用型:
A 級面 右側邊及底
C級
面
底面及內部
各面
B
級面
C級 面
內部 各面
后板 面
(兩 用 型 直 立 式 圖 示 )
1.外觀允收標准
金屬件及其加工組成品質標准
7
缺點類型
A面
判定標准 B面
C面
允許寬
允許寬<0.2mm、
0.2mm、長 3mm 以
允許寬<0.4mm 以
長<10mm 以下無感刮
刮 傷 下無感刮傷二
下,長<40mm 以下,刮
傷三條,條與條之間距
條,條與條之間距
傷三條.
離在 70mm 以上.
離 70mm 以上.
次
次 次
次 次 主 主 次
次 次 次
8
缺點類型
白斑 水紋 吐酸 脫層翹皮 過度酸洗 電鍍堆積
A面 不允許 不允許 不允許 不允許 不允許 不允許
判定標准
B面 不允許 不允許 不允許 不允許 不允許 不允許
C面 不允許 不允許 不允許 不允許 不允許 不允許
判 定
主 次 次 主 次 主
2.其 它 相 關 品 質 要 求
鉚合件須鉚合到位且牢固平整,不可有毛刺、松動之現象。
抽牙孔須完全,不得缺角或殘留毛頭且其孔徑需符合要求。
拉 釘 (包 括 所 有 鋁 制 拉 釘 和 鐵 制 拉 釘 )拉 完 后 , 須 完 整 , 不 得 破 損 、 殘 尾 、
檢測員 以上(含矯正后)
(示意圖)
待測物
Code Viewing Time
CiassA 7 秒/100mm×
100mm
CiasB 5 秒/100mm×
100mm
CiasC 3 秒/100mm×
100mm
所有的機構、電器特性、功能要求以圖面為准,關於機構尺寸公差如圖面 未直接於尺寸后標注其公差,則本公司孔的尺寸公差以±0.07mm 管制,其他尺 寸 以 ±0.20mm 進 行 管 制,除 非 客 戶 有 更 為 嚴 格 或 特 別 要 求。QE 人 員 可 視 需 要 在 SIP 制定時縮小其公差,以利於生產管制,如東驊供貨商的產品有因 SIP 縮小 公差管制的問題被判拒收,且可証實是東驊事前未有通知廠商時,當批可以東 驊盡量吸收的原則協調處理,但供貨商必須於下批改善。
4
生鏽。 模痕—通常指衝壓過程中,材料表面處理層受到模面擠壓表面產
生的痕跡或殘破剝落,易發在折彎成形產品面之邊緣,或是需要衝制刻印 之處。
拉模—一般指衝制產品拉伸或卸料不良以及射出,壓鑄產品脫模 時被模具邊拉拖所造成之不良。
縮水—產品表面因材料熱脹冷縮作用,造成凹陷的現象。 短射或多料—灌料量不足或因模具缺失、位置不當而產生多余的材料。
允許不得有露底 允許不得有露底
材之擦傷
材之擦傷
不允許
面積≦0.50mm2,允 許三處(距離大于 50mm)
不允許 不允許
不允許 不允許
不允許
不允許
不允許
不允許表面鹽處 理產生的差異,其他 成因的色差可接受.
允許ψ0.2mm 以
允許ψ0.4mm 以
下1個
Байду номын сангаас
下兩個
不允許
不允許
不允許
不允許
判 定
次
次 主 次 次
碰傷
面積≦0.2
面積≦1.0 mm2 允 面積≦2.0mm2 允許
mm2 允許 1 處 許 1 處
2處
斷裂
不允許
不允許
不允許
毛邊
須通過 UL 1439 不允許
測試或無刺手之感覺
材料厚度 5%以下
模痕 氧化 凹凸痕
允許不得有露底 允許無手感之模
不允許
材之模具痕
具痕
表面不允許
表面不允許(切
表面不允許(切
水口—注塑、壓鑄工件的進料口。 頂針印—模具頂料銷所造成的印痕。 頂白—比背景顏色白,常出現于頂針背面。 結合線—也叫溶化線,像是重新交接線,這種結合可以是不同灌料口灌入 后之結合,也可以是因為零件外形使原料分支流動后結合。 過火—射出過程高溫高壓,材料燃燒,所留下的燒焦或黑痕。 咬花大小不一—此為塑膠模具成型循環時,因壓力不一所造成的。 流 痕 — 熱 塑 膠 流 質 因 潮 濕 空 氣 凝 聚 影 響,于 射 出 成 型 后 在 表 面 上 呈 現 波 浪 或條紋現象。 壓 力 痕 — 此 為 塑 膠 模 具 成 型 循 環 時,大 量 熱 塑 膠 流 質 流 動 受 到 循 環 壓 力 影 響,射出料會造成銀灰色閃亮條紋。 氣孔—加工時卷入氣體而產生的孔狀不良。 气泡—加工時卷入氣體而產生的泡狀不良。 起瘡—斑痕或銀灰色條紋,射出料氣泡造成。該氣泡形成一般是因為潮濕 空氣被凝聚。 濺渣—焊點周圍因焊接作業產生的小金屬顆粒。 脫焊—焊點分離。 燒傷—點焊或熔接作業因溫度過高而產生。 焊痕—焊接后留下的痕跡,塗裝后仍可見到。 膜厚—產品表面處理層的厚度。 硬度—塗料、材料質地堅固程度。 附著性—表面涂膜處理層或印刷,燙金與母材之間的結合力。 光澤度—產品表面的光澤反射率。 耐衝擊性—表面涂膜層與母材之間的結合程度及塗膜堅韌程度。 耐溶劑性—表面涂膜層,印刷及燙金與酒精的化學反應。 耐磨性—表面涂膜層,印刷及燙金的耐磨程度。 流漆—塗裝后表面有單個或多個如水滴般的漆點。