锌合金压铸技术
锌合金压铸件表面处理

锌合金压铸件表面处理1. 简介锌合金压铸件是一种常见的金属零件,具有很高的强度和耐腐蚀性。
然而,其表面通常需要进行处理以提高外观和性能。
本文将详细介绍锌合金压铸件表面处理的方法和技术。
2. 表面处理方法2.1 机械处理机械处理是锌合金压铸件表面处理的基本方法之一。
它包括去毛刺、抛光和打磨等步骤。
去毛刺可以通过机械切削或研磨来完成,以去除零件表面的毛刺和尖锐边缘。
抛光和打磨则可以提高零件表面的光洁度和平整度。
2.2 化学处理化学处理是锌合金压铸件表面处理的另一种常用方法。
它主要包括酸洗、电镀和化学转化膜等过程。
酸洗可以去除锌合金表面的氧化物和污垢,提供一个干净的表面用于后续处理。
电镀可以在锌合金表面形成一层金属镀层,提高其外观和耐腐蚀性。
化学转化膜则可以在锌合金表面形成一层化学转化膜,提高其耐磨性和耐腐蚀性。
2.3 热处理热处理是一种常用的锌合金压铸件表面处理方法。
它包括热处理和热喷涂两种方式。
热处理可以改变锌合金的组织结构和性能,提高其硬度和强度。
热喷涂则可以在锌合金表面形成一层涂层,提高其耐磨性和耐腐蚀性。
3. 表面处理技术3.1 硅溶胶处理硅溶胶处理是一种常用的锌合金压铸件表面处理技术。
它通过在锌合金表面形成一层硅溶胶膜来提高其耐腐蚀性和耐磨性。
硅溶胶处理可以在常温下进行,具有成本低、工艺简单和效果显著的优点。
3.2 电化学抛光电化学抛光是一种通过电化学方法去除锌合金表面的氧化物和污垢的技术。
它可以提高锌合金表面的光洁度和平整度,使其具有更好的外观和耐腐蚀性。
3.3 电镀技术电镀技术是一种常用的锌合金压铸件表面处理技术。
它可以在锌合金表面形成一层金属镀层,如镍、铬或锌等,以提高其外观和耐腐蚀性。
电镀技术可以根据需要选择不同的金属镀层,以满足不同的要求。
3.4 化学转化膜技术化学转化膜技术是一种通过化学反应在锌合金表面形成一层转化膜的技术。
转化膜可以提高锌合金表面的耐磨性和耐腐蚀性,同时保持其原有的外观。
锌合金压铸技术3篇
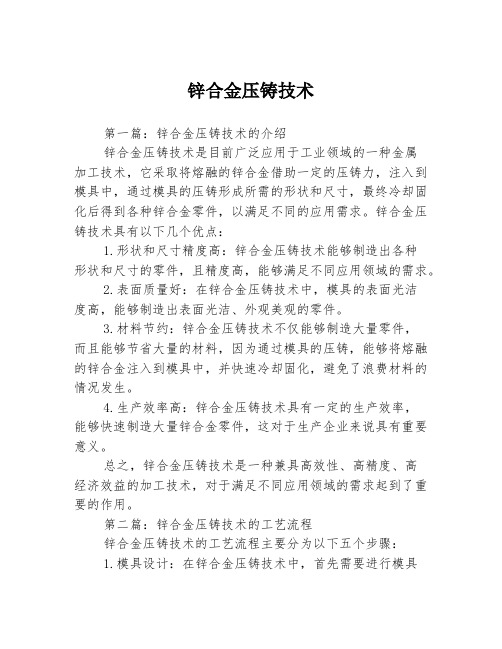
锌合金压铸技术第一篇:锌合金压铸技术的介绍锌合金压铸技术是目前广泛应用于工业领域的一种金属加工技术,它采取将熔融的锌合金借助一定的压铸力,注入到模具中,通过模具的压铸形成所需的形状和尺寸,最终冷却固化后得到各种锌合金零件,以满足不同的应用需求。
锌合金压铸技术具有以下几个优点:1.形状和尺寸精度高:锌合金压铸技术能够制造出各种形状和尺寸的零件,且精度高,能够满足不同应用领域的需求。
2.表面质量好:在锌合金压铸技术中,模具的表面光洁度高,能够制造出表面光洁、外观美观的零件。
3.材料节约:锌合金压铸技术不仅能够制造大量零件,而且能够节省大量的材料,因为通过模具的压铸,能够将熔融的锌合金注入到模具中,并快速冷却固化,避免了浪费材料的情况发生。
4.生产效率高:锌合金压铸技术具有一定的生产效率,能够快速制造大量锌合金零件,这对于生产企业来说具有重要意义。
总之,锌合金压铸技术是一种兼具高效性、高精度、高经济效益的加工技术,对于满足不同应用领域的需求起到了重要的作用。
第二篇:锌合金压铸技术的工艺流程锌合金压铸技术的工艺流程主要分为以下五个步骤:1.模具设计:在锌合金压铸技术中,首先需要进行模具设计。
模具的设计要考虑到锌合金压铸的工艺特点,尽可能的减少模具使用寿命和生产成本,同时满足零件的形状和尺寸等要求。
2.锌合金熔炼:将锌合金熔炼成一定温度的熔融状态,以便于注入到模具内。
3.注入模具:在锌合金熔炼完成后,需要借助一定的压铸力,将熔融的锌合金注入到模具中,按照所需的形状和尺寸进行压铸。
4.卸模、清理:待压铸完成后,将模具卸下,将形成的锌合金零件取出,并进行清理。
5.后处理:在锌合金压铸完成后,还需要进行热处理、机加工、表面处理等后续处理,以使得锌合金零件能够满足不同应用领域的需求。
以上就是锌合金压铸技术的工艺流程,对于使用锌合金压铸技术的企业来说,需要掌握这些工艺流程,以便在生产过程中更好地进行管理。
第三篇:锌合金压铸技术的应用领域锌合金压铸技术是一种使用广泛的金属加工技术,其应用领域非常广泛。
(完整版)锌合金压铸工艺
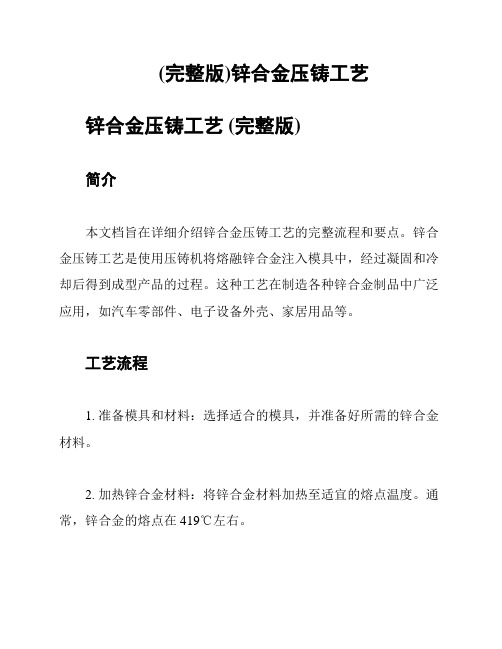
(完整版)锌合金压铸工艺锌合金压铸工艺 (完整版)简介本文档旨在详细介绍锌合金压铸工艺的完整流程和要点。
锌合金压铸工艺是使用压铸机将熔融锌合金注入模具中,经过凝固和冷却后得到成型产品的过程。
这种工艺在制造各种锌合金制品中广泛应用,如汽车零部件、电子设备外壳、家居用品等。
工艺流程1. 准备模具和材料:选择适合的模具,并准备好所需的锌合金材料。
2. 加热锌合金材料:将锌合金材料加热至适宜的熔点温度。
通常,锌合金的熔点在419℃左右。
3. 开模:将加热至熔融状态的锌合金注入模具中,并迅速封闭模具。
4. 凝固和冷却:在模具中冷却期间,锌合金开始凝固和冷却,逐渐形成成型产品的轮廓。
5. 压铸成型:当锌合金完全凝固并冷却后,打开模具,取出成型产品。
6. 修整和加工:对成型产品进行修整和加工,如去除余料、研磨打磨、表面处理等。
7. 检验和质量控制:对成型产品进行严格的检验和质量控制,确保产品符合规定的标准和要求。
8. 包装和出货:将合格的成型产品进行包装,并准备出货。
工艺要点- 模具设计:模具设计是锌合金压铸工艺成功的关键。
模具应考虑到产品的形状、尺寸、结构等因素,以确保成型产品的质量和完整性。
- 温度控制:锌合金在加热和冷却过程中的温度控制对于成型产品的质量至关重要。
合适的温度控制可以避免形成气孔、缩松等缺陷。
- 压力控制:适当的压力控制可以保证锌合金充分填充模具,并减少缺陷的发生。
- 材料选择:选择合适的锌合金材料,考虑其机械性能、耐腐蚀性能等因素,以适应不同产品的要求。
结论锌合金压铸工艺是一种高效、精确的制造方法,可以用于生产各种锌合金制品。
通过合理的工艺流程和要点的掌握,可以确保成型产品的质量和一致性。
在实际应用中,也需要根据具体情况进行工艺参数的优化和调整,以满足不同产品的需求。
锌压铸工艺
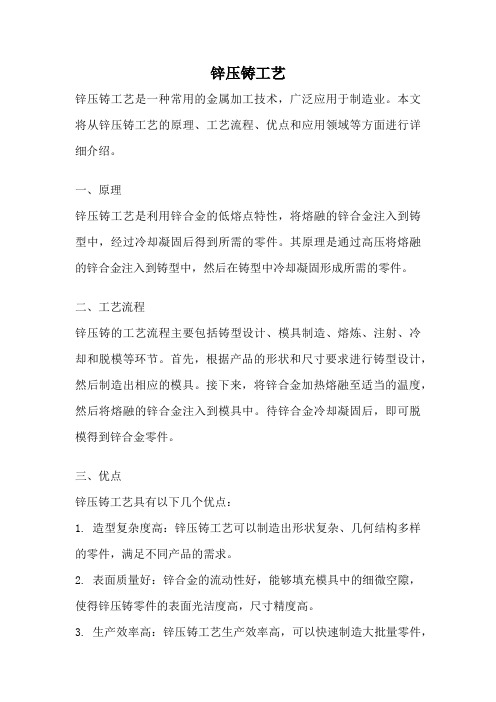
锌压铸工艺锌压铸工艺是一种常用的金属加工技术,广泛应用于制造业。
本文将从锌压铸工艺的原理、工艺流程、优点和应用领域等方面进行详细介绍。
一、原理锌压铸工艺是利用锌合金的低熔点特性,将熔融的锌合金注入到铸型中,经过冷却凝固后得到所需的零件。
其原理是通过高压将熔融的锌合金注入到铸型中,然后在铸型中冷却凝固形成所需的零件。
二、工艺流程锌压铸的工艺流程主要包括铸型设计、模具制造、熔炼、注射、冷却和脱模等环节。
首先,根据产品的形状和尺寸要求进行铸型设计,然后制造出相应的模具。
接下来,将锌合金加热熔融至适当的温度,然后将熔融的锌合金注入到模具中。
待锌合金冷却凝固后,即可脱模得到锌合金零件。
三、优点锌压铸工艺具有以下几个优点:1. 造型复杂度高:锌压铸工艺可以制造出形状复杂、几何结构多样的零件,满足不同产品的需求。
2. 表面质量好:锌合金的流动性好,能够填充模具中的细微空隙,使得锌压铸零件的表面光洁度高,尺寸精度高。
3. 生产效率高:锌压铸工艺生产效率高,可以快速制造大批量零件,提高生产效率和产品交付速度。
4. 材料性能优异:锌合金具有优异的机械性能和耐腐蚀性能,能够满足各种工业领域的使用要求。
四、应用领域锌压铸工艺在各个领域都有广泛的应用,特别是在汽车、电子、家电等制造业中应用较为广泛。
在汽车制造中,锌压铸工艺可以制造出汽车零部件,如发动机零件、传动系统零件等。
在电子领域,锌压铸工艺可以制造出各种外壳、散热器等电子元器件。
在家电制造中,锌压铸工艺可以制造出各种家电外壳、配件等。
锌压铸工艺作为一种常用的金属加工技术,在制造业中有着广泛的应用。
通过锌压铸工艺,可以制造出形状复杂、表面质量好的零件,提高生产效率和产品质量。
随着技术的不断发展,锌压铸工艺将在更多领域得到应用,为工业发展提供更多可能性。
锌合金压铸工艺

锌合金压铸工艺引言锌合金压铸工艺是一种常用于生产锌合金制品的制造方法。
锌合金具有优异的机械性能,耐腐蚀性和导电性能,因此在各种应用中广泛使用。
本文将介绍锌合金压铸工艺的基本原理、过程和应用。
通过阅读本文,您将了解锌合金压铸工艺的重要性以及如何实施该工艺以生产高质量的锌合金制品。
基本原理锌合金压铸工艺是利用锌合金在高温下液态流动性较好的特性,通过模具将熔化的锌合金注入模腔中,待冷却凝固后取出制品成型的一种制造方法。
其基本原理包括以下几个方面:1.熔炼锌合金:首先,将适量的锌合金料料放入熔炉中进行加热,使其达到熔化状态。
2.注射压铸:将熔化的锌合金通过注射机注入模具的模腔中。
注射机会将高压力施加在锌合金上,使其充分填充模腔,并确保产品形状的精度。
3.冷却凝固:注射完成后,等待锌合金在模具中冷却凝固。
冷却速度的控制是关键,既要保证产品快速凝固,又要避免产生内部缺陷。
4.脱模:冷却后,打开模具,取出凝固后的锌合金制品。
工艺流程锌合金压铸工艺通常包括以下几个步骤:1.设计模具:首先,根据产品的形状和尺寸设计模具。
模具通常由两部分组成:上模和下模。
上模和下模之间的空间形成了产品的形状。
2.准备锌合金料:根据产品的要求,准备适量的锌合金料。
合理的合金配比是保证产品质量的关键。
3.熔炼锌合金:将准备好的锌合金料放入熔炉中进行熔炼。
在熔炼过程中需要控制熔炉的温度和时间,以确保锌合金完全熔化并达到所需的熔融状态。
4.注射压铸:将熔化的锌合金倒入注射机中,通过高压将锌合金注入模具的模腔中。
注射过程需要控制注射机的压力和注射速度,以确保锌合金能够充分填充模腔。
5.冷却凝固:注射完成后,等待锌合金在模具中冷却凝固。
控制冷却速度可以通过调整模具温度和环境温度来实现。
6.脱模和后处理:冷却后,打开模具,取出凝固的锌合金制品。
根据产品的要求,进行必要的后处理,如去毛刺、抛光等。
应用领域锌合金压铸工艺被广泛应用于各个领域,特别是在以下几个方面具有重要意义:1.汽车工业:锌合金压铸工艺可用于生产汽车零部件,如发动机零件、变速器零件、制动系统零件等。
锌合金压铸技术

锌合金压铸技术第一篇:锌合金压铸技术简介锌合金压铸技术是一种常用的工艺,可以生产出高精度、复杂形状、表面质量好、工艺效率高、成本低等优点的制品。
锌合金压铸技术已广泛应用于汽车、电子、电器、通讯、仪器仪表、农业机械、建筑等领域。
1.锌合金压铸的优点(1)高精度:锌合金压铸机器的闭合压力高,使模具能在高压下封闭和固定,可以制造一个具有高精度和稳定尺寸的零件。
(2)优良外观:由于锌合金压铸具有高度的工艺性,可以生产出外观精美、表面光滑的制品,不需要二次加工。
(3)高效率:锌合金压铸生产周期短,具有高产量和低生产成本的优点。
(4)多样化:利用锌合金压铸可以生产出各种不同类型、不同大小、不同辨识符的零件。
(5)可循环利用:锌合金可重复循环使用,比较环保。
2.锌合金压铸的适用范围锌合金压铸适用于制造通讯设备、计算机零件、汽车零部件、LED灯、家居用品、办公家具等制品。
其中,汽车行业中,锌合金压铸技术已广泛使用在汽车仪表盘、方向盘、空调出风口、车门锁等零部件的生产;电子通讯行业中,锌合金压铸技术已普遍应用于手机壳、数码相机壳、笔记本电脑外壳等产品制造;此外,家具、建筑、医疗器械、工业制品等也都可以采用锌合金压铸生产技术。
3.锌合金压铸的生产工艺锌合金压铸的生产工艺主要包括:(1)模具制造:锌合金压铸所需模具质量对于制品成品质量有重大影响,必须制造和使用高质量模具。
(2)材料准备:制品的制作材料主要是锌合金,这种合金是由铝、铜和锌等多种金属元素组成的,必须要在高温下融合后才能应用。
(3)熔化:将经过精心调配的锌合金材料放入炉中熔化,使其达到所需温度和化学成分要求。
(4)注塑成型:经过一个先进的注塑过程,在流道和压铸腔中注入熔融的锌合金材料,使其填充模具的腔形,冷却后即可得到锌合金零件。
4.锌合金压铸的关键技术锌合金压铸与其他生产工艺相比,具有一些独特的关键技术,如下:(1)模具技术:模具技术对于制品的外观和尺寸精度有极大的影响。
锌压铸工艺
锌压铸工艺锌合金压铸熔炼是锌合金压铸过程的一个重要环节,熔炼过程不仅是为了获得熔炼的金属液,更重要的是得到化学成分符合规定,能使压铸件得到良好的结晶组织以及气体、夹杂物都很小的金属液。
在熔炼过程中,金属与气体的相互作用和金属液与坩埚的相互作用使成分发生变化,产生夹杂物和吸气。
所以制定正确的熔化工艺规程,并严格执行,是获得高质量铸件的重要保证。
常用锌合金压铸用锌合金熔炼方法:锌合金压铸件1.熔炼前准备坩埚使用前必须清理,去除表面的油污、铁锈、熔渣和氧化物。
工具:熔炼工具在使用前应清楚表面脏物,与金属接触的部分,必须预热并刷上涂料。
工具不能沾水,否则会引起熔液的飞溅及爆炸。
合金料:熔炼前要清理赶紧并预热,去除表面水分。
2.熔炼工艺过程准备好锌料、多孔把、锭槽、熔剂等,注意所以工具在使用前须先预热刷涂料烘干。
合上电源开关,启动燃料机开关,点燃火焰,盖上炉盖。
将温控器温度设定在420-430摄氏度向炉内加入碎锌料垫底,待其熔至办固态后向内加入锌锭。
及时清除锌埚液面上的浮渣,及时补充锌料,保持熔液面正常的高度,因为过多的浮渣和过低的液面都容易造成料渣进入压射系统,导致热作件拉伤、卡死。
停机时把锌熔液舀出,重新熔炼时按三段调温,可以避免冷料爆料和烧坏坩埚。
3.坩埚的使用和维护坩埚在使用前须先进行清理,去除表面的油污、铁锈、熔渣及氧化物。
使用过程中严禁向坩埚内砸放锌锭,以免损坏坩埚。
生产完成后停炉前须将坩埚内锌液舀干。
坩埚在使用过程中须根据表面涂料的脱落程度定期进行清理重喷。
以上就是锌合金压铸件熔炼工艺的大体操作步骤,希望您在看完这篇文章之后,可以对锌合金压铸件的熔炼工艺有一个大致的了解。
锌合金压铸技术
锌合金压铸技术锌合金压铸技术是一种应用广泛的金属加工方法,它在工业领域中扮演着重要的角色。
本文将介绍锌合金压铸技术的原理、应用领域以及发展趋势等方面。
锌合金压铸技术是一种通过在高温高压环境下,将熔化的锌合金注入到铸模中,并经过凝固后形成所需产品的一种金属加工方法。
其特点在于生产效率高、成本低、产品精度高以及表面光洁度好等优势。
锌合金压铸技术具有以下几个主要的原理:首先,通过预热的方式提高锌合金的流动性,以保证熔融合金在模具中流动平稳;其次,通过高压环境下的模具封闭,使得熔融合金能够迅速冷却凝固,从而形成所需产品;最后,通过模具的设计和排气系统,避免产生气泡等缺陷,提高产品质量。
锌合金压铸技术在众多领域中得到了广泛的应用。
首先,在汽车制造行业中,锌合金压铸技术可以制造轻量化零部件,提高汽车的燃油效率,并降低其总重量。
其次,在电子产品制造领域,锌合金压铸技术可以生产精密的外壳和散热结构,保证电子产品的正常运行。
此外,锌合金压铸技术还广泛应用于通信设备、军工制造、家居装饰等领域。
随着科技的快速发展,锌合金压铸技术也在不断创新和进步中。
首先,材料科学的进步使得锌合金的性能得到了提升,提高了产品的质量和可靠性。
其次,模具设计和制造技术的不断改进,使得锌合金的制造过程更加精确和高效。
此外,数字化制造技术的应用也在锌合金压铸技术中得到了体现,提高了生产过程的自动化程度和生产效率。
总结而言,锌合金压铸技术作为一种重要的金属加工方法,以其高效、低成本和高精度等优势,在各个领域得到了广泛的应用。
随着科技的不断发展,锌合金压铸技术将更加精细化、智能化,并在未来的工业生产中发挥更重要的作用。
锌合金压铸工艺
锌合金压铸工艺
锌合金压铸工艺是一种常见的金属压铸工艺,用于制造各种锌合金零件或产品。
以下是该工艺的主要步骤:
1. 准备模具:根据产品设计要求制作压铸模具,包括模具的上下模块、填充系统和冷却系统等。
2. 熔炼锌合金:将锌合金料材加热熔化,通常使用电炉或燃气炉来进行熔炼。
3. 充填模腔:将熔融的锌合金液体倒入压铸机的喷射系统中,通过高速注射将液态金属充填进模具腔体。
4. 压封模腔:当充填停止时,压铸机上的千斤顶系统会施加一定的压力来封闭模具腔体,确保零件的完整性。
5. 冷却和固化:待注射的锌合金在模具中冷却,逐渐凝固定形,通常采用水或空气冷却。
6. 打开模具:一段时间后,冷却的零件会变得坚固,压铸机打开模具,取出成品。
7. 喷砂和去毛刺:锌合金零件通常需要进行喷砂和去毛刺处理,去除表面的不平整和毛刺。
8. 进行二次加工和表面处理:根据产品要求,可能需要进行机加工、热处理、抛光、电镀等二次加工和表面处理。
以上是锌合金压铸工艺的主要步骤,不同零件的制造过程可能会有所不同,需要根据具体的产品要求进行调整。
锌合金压铸工作原理
锌合金压铸工作原理锌合金压铸是一种常见的金属加工方法,它利用压力将熔融的锌合金注入到模具中,随后冷却凝固成型。
这种工艺广泛应用于汽车、电子、机械等领域,因为它可以高效地生产各种形状的金属零件。
锌合金压铸的工作原理可以简单地概括为以下几个步骤:1. 准备模具:根据所需零件的形状和尺寸,制作模具。
模具通常由两部分组成,上模和下模,它们可以互相组合成零件的形状。
2. 加热锌合金:将锌合金加热到熔点,通常约为419℃。
锌合金的成分可以根据需要进行调整,以提供所需的机械性能和耐腐蚀性能。
3. 注入模具:一旦锌合金达到了适当的温度,就通过喷嘴将熔融的锌合金注入模具中。
注入时需要施加一定的压力,以确保锌合金充满整个模具腔。
4. 冷却凝固:注入模具后,锌合金会立即开始冷却,并逐渐凝固成型。
冷却时间通常在几秒钟到几分钟之间,具体取决于零件的尺寸和形状。
5. 脱模:当锌合金完全凝固后,模具会打开,将成型的零件取出。
在取出之前,需要确保零件已经达到足够的硬度和强度。
锌合金压铸的工作原理主要依靠锌合金的熔点和凝固过程来实现零件的成型。
通过控制加热温度、注入速度和冷却时间等参数,可以实现对零件质量的控制。
同时,模具的设计和制造也至关重要,它决定了零件的几何形状和尺寸精度。
锌合金压铸工艺的优点在于生产效率高、成本低、零件表面质量好等。
然而,在实际生产过程中还需要注意一些问题,如锌合金的脆性和易氧化性,模具的寿命和维护等。
通过不断改进工艺和技术,可以进一步提高锌合金压铸的质量和效率。
锌合金压铸工作原理简单明了,通过熔融、注入、冷却凝固等步骤完成零件的成型。
它是一种重要的金属加工方法,广泛应用于各个领域。
随着科技的进步和工艺的改进,锌合金压铸将会在未来发展出更广阔的应用前景。
- 1、下载文档前请自行甄别文档内容的完整性,平台不提供额外的编辑、内容补充、找答案等附加服务。
- 2、"仅部分预览"的文档,不可在线预览部分如存在完整性等问题,可反馈申请退款(可完整预览的文档不适用该条件!)。
- 3、如文档侵犯您的权益,请联系客服反馈,我们会尽快为您处理(人工客服工作时间:9:00-18:30)。
锌合金压铸技术
熱流道設計已廣泛應用在注塑工藝上,而且證明相當成功,它的好處是減少流道回收,提高注塑件質量,熱室鋅壓鑄的熱流道系統是嶄新的設計,要充分瞭解它的好處,最好先探討鋅流道的差不多原理及其隱藏成本。
文章上半部詳述壓鑄流道對成本的影響,下半部分則介紹壓鑄熱流道的好處及應用。
鑄件流道的損耗
對壓鑄有所認識的都會明白,流道或余料是鑄件的一部分,雖然沒有利潤價值,但在生產過程中是無法幸免。
這部分的成本一般只計算為鑄件成本的固定比率。
同時,鑒於鋅合金的可回收性,本地最常見的處理方法是實時投回機爐翻熔,由於需要操纵質量問題,用中央熔爐回收流道或廢品亦漸為業界所同意(圖1)。
至於爐渣,規模較大的壓鑄廠可能會自行回收,一般會把這些余料售回原料供貨商,換回新料。
本地的鋅料回收價一般為新料的五至七成。
若沒有良好的環保條件,處理爐渣易造成空氣污染。
以一台160噸熱室壓鑄機為例,每次生產至少150克流道(不包括溢流井),假設以三班生產,生產週期為20秒,機器使用率有80%,年產澆口流道便達190噸。
另一例子:以一台80噸機計算,每次生產100克流道,同樣的假設但生產週期改為12秒,年產流道更超過210噸。
由此可見,流道設計影響成本的重要性。
各種回收方式
在回收方法當中,直接把流道投回機爐為最
簡單和節省成本的方法。
翻熔剛生產的流道
無須預熱,而且減少存放的空間,但专门難
操纵熔料的質量,包括爐渣較多,爐溫難以
操纵,合金成份亦無法得知;更重要的是,
它依賴操作員工的工藝,如投入新料的比
例,觀察爐水的變化,而員工把溢流井、飛
邊投入機爐,不但會令情況更差,這種把廢
品直接翻熔的方法亦隱藏了高次品率、模具
設計及壓鑄參數不穩定的問題,令治理人員
無法有效地作出改善。
此方法不適宜生產表
面質量要求較高之鑄件,且難以正確計算流
道損耗成本。
中央熔爐回收水口及次品開始流行於產量大的壓鑄廠,它的好處特不明顯,确实是集中處理回收料能够提高熔爐效率,操纵合金質量。
假如以金屬液從中央爐直接加入機爐,壓鑄機料溫可保持穩定,少爐渣,如配以自動加料操纵,液面高度變化可減至最低。
目前流行的中央熔爐分為數類:有較大容量的鑄鐵坩堝爐,不銹鋼坩堝爐,及連續熔化型非坩堝爐。
鋅液運輸亦分為數類:有天車式液料運輸,有地面推車式(無軌或有軌)保溫爐(附有送料裝置)運輸及保溫槽式重力輸送裝置,將機爐與中央爐相連。
它的缺點是投資較大,只適合單一種合金(這裡暫不討論小型坩堝爐),車間佔地較大,因此小型壓鑄廠(五台機以下)則不太適合,而且舊廠房難於改造配合,故一般只會在建新廠房時才會重新規劃。
使用小型坩堝爐翻熔澆口料,由於缺乏規模效益,成本會較中央熔爐高,因此不以此作計算參考。
翻熔成本的計算
就以使用中央熔爐的方式計算流道的翻熔成本作為參考。
以一所公司有五台80噸或160噸壓鑄機為例,假設該設備的投資為50
萬,分十年攤分。
每年處理約1000噸流道回收料(實際情況應和新料按比例熔化,這裡純粹方便計算翻熔成本)。
每公斤澆口料之翻熔Array成本為$0.93,按上述
以五台機的計算,
生產1000噸流道水
口,涉及金額近一千
萬,如包括次品的回
收,此數字更為驚人
(如平均鑄重為100克
而次品率5%,週期12
秒,五台機計算,
回收之次品約為53
噸)。
雖然,處理數量
但這裡並沒有計算環
由此可見,
成本相當驚人,
必需盡量降低成本。
此,
是操纵成本的重要關
鍵。
攤分流道成本的計算方式
水口的翻熔成本必須算入鑄件的生產成本,最常見的做法是以用料乘固定百分比計算。
例如,原料價為$10/公斤,水口翻熔成本為鑄件重量的3%,計算鑄件材料價時便會用$10.3。
此方法雖然簡單,但可能令成本計算出現偏差,並隱藏起真實的水口回收成本。
現在可用以下例子作一比較:
鑄件A淨重400克,水口流道重100克。
鑄件B淨重同為400克,水口流道重量則為250克。
如用固定百分比計算:
鑄件A與鑄件B的成本應同為($10.3 x 0.4)= $4.12。
如用實際回收成本計算:
鑄件A應為($10 x 0.4 + $0.93 x 0.1) = $4.093
鑄件B應為($10 x 0.4 + $0.93 x 0.25) = $4.233
這差別看似細小,但以20秒作生產週期,機器使用率為80%及以三班生產,每台機每年生產1,261,440次來計算,差別如下:
如用固定比例法,鑄件A與B的成本一樣,但實際上鑄件B的成本較高。
從這案例看出,用固定比例法計算鑄件B,不但低估了生產成本,更間接鼓勵設計者不以減少水口流道的重量為目標,應該推廣實際成本法的應用(見下表)。
要減低澆口重量,較常見的是短澆口(短唧咀)設計,及減薄定模板厚度。
它使用較長的機器射咀(一般較正常長20mm),配合深穴的進澆口模具設計,以減少澆口重量,以下是一項嶄新的熱室壓鑄澆道設計。
熱室壓鑄澆道設計
壓鑄澆道是金屬液從射咀流入模腔的路徑,它是由直澆道及橫澆道的分支組成。
由於需要附著鑄件及便於脫模,直澆道必須要有斜度。
同時,動模板上的分流塊,能够減低直澆道的厚度;在分流塊裡加冷卻水道,方便平衡模熱、縮短冷卻時間及拉出鑄件並頂出。
澳洲CSIRO機構在70年代初期的研究發現,在可同意的誤差下,鋅合金液在壓鑄情況下可歸納為:
•液態表現為非壓縮性流體
•符合一般流體力學原理
•雷諾數值(Reynold number)高,顯示流動過程為紊流。
根據以上研究結果,理想的金屬液流動狀態應為:
1. 流道剖面為圓形
圖2:
由於圓周/面積比數值最低,圓形剖面
管道的表面阻力最低,因此壓力損失亦
最低。
比起相等梯形剖面積,周邊少20%
以上。
(圖2)
2. 流動管道為直線
彎曲管道會產生偏流,把氣泡混入熔液,並造成壓力損失。
尤其當彎曲半徑/管道直徑比小於1,壓力損耗急速增加。
3. 流道剖面往液流方面漸次縮小
管道剖面急促改變,不論變大或變小,均會造成高壓力損耗及產生渦流。
最佳的方案是剖面漸次縮小,以補償管道面造成的阻力損耗。
傳統設計的缺點
目前流行的流道在設計上與理想的流動狀態相違:
1. 流動剖面變化時大時小,造成渦流(Eddy current)(圖3)
2. 橫澆道剖面為梯形,死角位置容易產生冷隔
(Cold flake),不利表面要求高的鑄件。
3. 橫澆道與直澆道的急促彎曲角會造成偏流捲氣(Flow separation) (圖4)
圖
3:
圖
4:
要填補以上缺憾,就要用較大的壓力以抵消高壓力損耗,這樣會導至飛邊,降低鑄件尺寸精度,及縮短模具壽命。
此外,渦流捲氣導至鑄件內部氣孔,電鍍或烤漆時起泡,及增加溢流井來
排出雜渣氣泡(圖5)。
短澆口設計雖然可節省澆口重量,但無助於解決以上問題。
HOTFLO壓鑄熱流道設計
圖5:
熱流道系統在注塑工藝上已廣泛受應用,它減低了水口回收的問題,對減低注塑件困氣亦有专门大幫助。
相同的概念正應用於熱室鋅壓
鑄上,從事壓鑄工藝的澳洲HOTFLO公司的壓鑄熱流道系統的工作原理(圖6和7a-7e)。
圖
6:
圖
7a:
圖
7b:
圖
7c:
圖
7d:
圖
7e:
該設計不再需要動模上的分流錐,機器上的射咀緊貼鎖合環(Clamping ring),熱流道的杯套(Sprue bush)裝在定模板上,由發熱條加熱至400℃以上,令鋅液不會在杯套內凝固,導流塊(Sprue tip)裝在動模板,金屬液由射咀進入杯套,經過導流塊再流入橫澆道。
整個流道的剖面為圓形並漸次變小,導流塊的彎曲設計使壓力損耗及渦流捲氣的情況減至最低
(圖8)。
鑄件的凝固過渡在這彎曲位置前,杯套內的鋅液流回「鵝頸」,鑄件冷卻後開模頂出。
HOTFLO熱流道的特點
•大大縮短冷流程(圖9),過長的冷流程會產生冷紋,不利於生產
表面要求高之鑄件,HotFlo熱流
道可改善這一缺點。
圖
8:
•流道剖面全程均為
圓形,由於面積最小,
令熱流失、表面阻
力減至最低。
相對於
現時通用的梯形設
計,存在死角容易
產生冷隔,圓形設計
更顯優越。
過去由於
分流錐設計的主導
下,分流錐上的流道
呈梯形,因此餘下
的橫澆道亦跟隨其形
狀。
此外,漸變的梯
圖9:。