邯钢2000m3高炉设计特点
邯宝2×3 200 m3高炉系统工程设计及采用的新技术

阀、泄压阀、流化装置、煤粉仓底部流化床及锥部流化嘴、喷煤阀、分配器以及关键的检测元件采用国外产品,其余设备均由国内供货。
(10)鱼雷罐修理库。
320t鱼雷罐修理库由冷却场、解体场、砌筑间及干燥场等作业区组成。
主要设备有:内衬解体机、装载机、切砖机、磨砖机、喷补机、给料、干燥设备等。
(11)铸铁机。
为解决高炉开炉初期生产的不适宜炼钢的铁水及炼钢车间定期检修时生产的一部分铁水,在作适当产能调整的同时,考虑设置铸铁机。
铸铁机主要技术参数:链轮中心距(斜长)74.48m;生产能力260t/h;铸铁机生产率70%;链带运行速度12~19m/min;铸铁块重量6×8kg。
2高炉系统工程公辅设施配置2.1公辅设施组成公辅设施主要有:机械化贮运(原、燃料供应设施、原煤贮运、水渣贮运)、热力设施(鼓风机站、冷风、蒸汽、压缩空气输配)、燃气设施(高炉煤气净化系统、TRT、高炉煤气、转炉煤气、焦炉煤气、氧气和氮气输配)、给排水设施(软水、净化水、工业水、消防水、生活水、雨水等)、通风除尘设施、空调采暖设施、电力输配、电气传动、仪表、计算机、自动化控制、电讯、总图运输、铁路信号、消防、安全、卫生、环保设施、地上、地下综合管网等系统。
2.2主要的公辅设施配置(1)机械化贮运。
由原燃料供应及返矿、粉焦运输、原煤贮运、水渣贮运组成。
烧结矿从烧结厂,球团矿、块矿、杂矿从原料场,通过3条皮带(B=1 200mm,Q=1 200t/h)运至高炉矿槽内;焦炭从焦化厂,通过l条皮带(B=1 400mm,Q=400t /h)运至焦槽内。
返矿和粉焦用皮带或汽车运输。
2座高炉喷吹用的原煤在一个面积为156 m×35 131的干煤棚内贮存,通过配煤后经皮带送入原煤仓。
水渣通过皮带送贮存量约2.2万t的水渣堆场,可用火车或汽车运出。
(2)热力设施。
2座高炉配鼓风机组3台,2台进口,1台国产,型号全部为AV90—15电动全静叶可调轴流压缩机组。
2000高炉系统工程投产报告
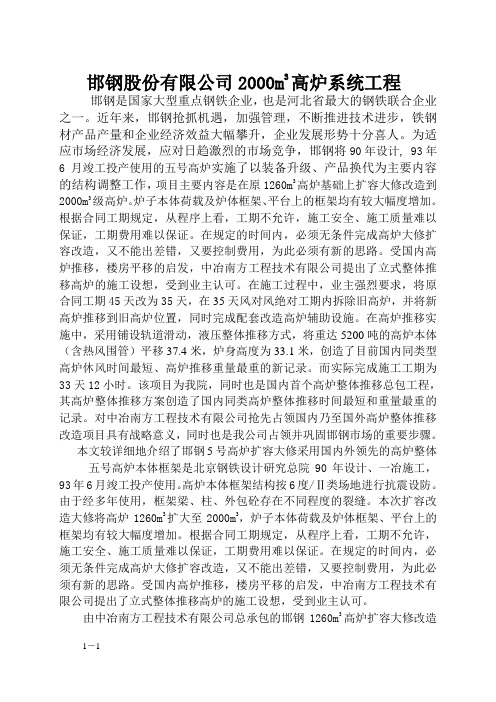
邯钢股份有限公司2000m3高炉系统工程邯钢是国家大型重点钢铁企业,也是河北省最大的钢铁联合企业之一。
近年来,邯钢抢抓机遇,加强管理,不断推进技术进步,铁钢材产品产量和企业经济效益大幅攀升,企业发展形势十分喜人。
为适应市场经济发展,应对日趋激烈的市场竞争,邯钢将90年设计, 93年6月竣工投产使用的五号高炉实施了以装备升级、产品换代为主要内容的结构调整工作,项目主要内容是在原1260m3高炉基础上扩容大修改造到2000m3级高炉。
炉子本体荷载及炉体框架、平台上的框架均有较大幅度增加。
根据合同工期规定,从程序上看,工期不允许,施工安全、施工质量难以保证,工期费用难以保证。
在规定的时间内,必须无条件完成高炉大修扩容改造,又不能出差错,又要控制费用,为此必须有新的思路。
受国内高炉推移,楼房平移的启发,中冶南方工程技术有限公司提出了立式整体推移高炉的施工设想,受到业主认可。
在施工过程中,业主强烈要求,将原合同工期45天改为35天,在35天风对风绝对工期内拆除旧高炉,并将新高炉推移到旧高炉位置,同时完成配套改造高炉辅助设施。
在高炉推移实施中,采用铺设轨道滑动,液压整体推移方式,将重达5200吨的高炉本体(含热风围管)平移37.4米,炉身高度为33.1米,创造了目前国内同类型高炉休风时间最短、高炉推移重量最重的新记录。
而实际完成施工工期为33天12小时。
该项目为我院,同时也是国内首个高炉整体推移总包工程,其高炉整体推移方案创造了国内同类高炉整体推移时间最短和重量最重的记录。
对中冶南方工程技术有限公司抢先占领国内乃至国外高炉整体推移改造项目具有战略意义,同时也是我公司占领并巩固邯钢市场的重要步骤。
本文较详细地介绍了邯钢5号高炉扩容大修采用国内外领先的高炉整体五号高炉本体框架是北京钢铁设计研究总院90年设计、一冶施工,93年6月竣工投产使用。
高炉本体框架结构按6度/Ⅱ类场地进行抗震设防。
由于经多年使用,框架梁、柱、外包砼存在不同程度的裂缝。
邯钢2000m~3高炉中修改善热风炉保温技术

图2 可以很明显看出改善后 的热风炉保温时
①烧炉前首先要关闭外接管道阀和空气管道 阀;②开烟道阀;③关废气均压阀;④开助燃空 气燃烧 阀;⑤开煤气燃烧 阀 ( 同时关 闭煤 气放 散 ) ⑥小 开助 燃 空气 调节 阀;⑦ 开煤 气切 断 ; 阀;⑧开煤气调节阀 5 ,点火燃烧 ;⑨逐步开 %
冶
1 0
金
能
源
Vo. No 131 .1
E RG F L RGI AL I NE Y OR ME I I U AL C NDUs RY T
Jn 2 1 a.02
邯钢 20 m 00 3高 炉 中修 改 善热 风 炉保 温 技 术
朱建 勇 魏航 宇 王文生 刘现停
进行 调节 。 22 参 数 的变化 .
的热风经 由蓄热室拱顶 、燃烧室拱顶、燃烧室热 风围管进入热风管道 ,最终由倒流管道排出。但 是一方面 5 号高炉中修时间比较长 ,风机需要一 直提供冷风 ,另外一方面热 风管道需要重 新砌
筑 ,反 吹时热 风没 有去路 ,因此进 行 了技术设 备
改造 。
改进 装置 主要 增加两 个 管道 ,一方 面是在 热
改进后的热风炉保温时温度变化平缓 ,一般 情况下不需要控制。燃烧室拱顶、蓄热室拱顶 、 硅铝砖界面和炉箅子温度变化很平稳。1h内这 2 些温度的变化曲线见图 2 。
风炉燃烧室热风出 口处 接一个调节烟道及阀门;
另外一方面在蓄热室后面的充压阀后面的冲压管 道处增加一处空气管道及阀门,此管道与大气直 接接 触 ,空气 管道 安装 图见 图 l 。
收稿 日 : 1 — 6 2 期 2 1 0 —7 0 朱建勇(93 ) 助I ; 61 河北省邯郸市。 18 一 , 0 03 5
2000m3高炉炉型设计及物料平衡计算

2000m3高炉炉型设计及物料平衡计算摘要:本设计要求建2000m3炼铁高炉。
设计主要内容包括高炉炉型设计计算及高炉本体立剖图,同时对所设计高炉的特点进行简述。
设计高炉有效容积为2000m3,高径比取,高炉利用系数取值为,据此设计高炉炉型。
设计本着优质、高产、低耗和对环境污染小的宗旨,为日产生铁4000t的高炉提供高炉内型设计。
并对2000m3炼铁高炉进行物料平衡计算,物料平衡计算是炼铁工艺计算中重要组成部分,它是在配料计算的基础上进行的。
整个物料平衡计算有配料计算和物料衡算两部分构成。
在配料计算过程中,进行了原料和燃料的全分析,渣铁成分及含量分析;在物料衡算过程中计算了包括鼓风量、煤气量以及物料收支总量等项内容的计算,并制作物料平衡表。
关键词:高炉发展;高炉炉型;炉型计算;物料平衡配料计算物料衡算物料平衡表绪论最近二十年来,日本和欧盟区的在役高炉座数由1990年的65座和92座下降到28座和58座,下降幅度分别为%和37%,但是高炉的平均容积却分别由1558m3和1690m3上升到4157m3和2063m3,上升幅度为%和22%,这基本代表了国外高炉大型化的发展状况。
高冶炼强度、高富氧喷煤比和长寿命化作为大型高炉操作的主要优势受到大家越来越高的关注和青睐,但是高炉大型化作为一项系统工程,它在立足自身条件的基础上仍须匹配的炼钢、烧结和炼焦能力。
我国近年推出的《钢铁产业发展政策》中规定高炉炉容在300m3以下归并为淘汰落后产能项目,且仍存在扩大小高炉容积的淘汰范围的趋势。
同时国内钢铁产业的快速发展均加速了世界和我国高炉大型化的发展进程。
由于大型化高炉具备的单位投资省、效能高和成本低等特点,从而有效地增强了其竞争力。
20世纪高炉容积增长非常快。
20世纪初,高炉炉缸直径4-5m,年产铁水约100000吨左右,原料主要是块矿和焦炭。
20世纪末,最大高炉的炉缸直径达到14-15m,年产铁水300-400万吨。
邯钢2000m 3高炉中修快速达产实践

te a tc e s h ril umma ie h x re c s o h r paa in a d o e ai fr trig up t e r ln d f a e rz st e e pe n e ft e p e rto n p r t i on o esa tn h e ie um c .
奠定 了 良好基 础 .
槽 旋转 驱 动装 置运行 正 常.
3 冷却 系统 . 业 水 试 水 正 常 , 压 水 压 大 于 ) 工 高 16 a 中压 水压 大 于 0 7 P , .MP , . M a 水路 畅 通 , 泄 露 , 无 软水 冷 却 系统 试 水 正 常 , 压 大 于 07 a水 路 畅 水 .MP ,
风管 系统 由 3部 分 组 成 : 别 是 铁 口孔 道 埋 设 管 路 分 段 , 内管路段 和 炉外管 路 连接段 . 个铁 口在 炉 内 炉 两 制作 泥包 , 泥包 用炮 泥 和碳 素料捣 打料 , 泥包 大 小 以
1 送 风 系 统 . 炉 鼓 风 机 正 常 , 风 能 力 大 于 ) 高 送 300m / i, 风 管道 系统 检 修 砌 筑完 毕 , 备 送 0 mn送 具 风条 件 , 阀 组 工 作 正 常 , 风 炉 烘 炉 保 温 工 作 正 各 热
王文生 ,魏航宇 ,胡 文强,杨 春生 ,张红 岗
2000m3级高炉铁口数目的选择

2000m3级高炉铁口数目的选择《高炉炼铁工艺设计规范》规定:2000m3级高炉的铁口数目为2~3个,渣口数目0个。
确定高炉铁口数目的主要因素是高炉日产铁量,从有利于炉缸和铁口维护的角度出发,一般每个铁口的昼夜出铁量约3500t。
影响高炉铁口数目的其它因素还有出铁制度、配罐、渣铁沟维护、总图布置等。
国内2000m3级高炉采用3个铁口的,更多地考虑了炉前设备的可靠性和出铁操作的稳定性因素。
国外大型高炉有减少铁口数目的趋势,在欧洲,2500m3级高炉大多采用了2个铁口,国内高炉未趋同这个趋势。
表1 国内2000m3级高炉采用2个铁口的情况随着大型高炉精料水平的提高,渣比一般在350kg/t以下,铁口排放炉渣的负荷逐渐降低;采用优质浇注料后,主沟和渣铁沟的寿命大大提高,主沟一次通铁量可达12万t以上,主沟和渣铁沟的维护工作量大为减少;若采用快干浇注料,主沟的修补工作(从热态拆沟到烘干后使用)可在12h以内完成;这些均为减少铁口数目创造了有利条件。
减少铁口数目的意义在于降低投资,减少占地,节省生产和维护成本。
对汉钢2200m3高炉,在炉前设备可靠性高、出铁操作稳定的前提下,两个铁口操作不存在重叠出铁的情况,出铁间隙时间在30min以上。
当一个铁口的主沟及渣铁沟检修时,在修沟时间内由一个铁口出铁,炉前通过以下措施来保证正常生产:1、适当减少出铁次数;2、提高炮泥强度;3、加强铁口深度管理,调整钻头直径,控制出铁时间;4、缩短开口时间;5、深化设备维护。
配合上述工况,设计考虑了采用成熟可靠的大推力泥炮和全液压一次性开口机;加大主沟及渣铁沟流通截面,主沟工作衬加厚等措施,使主沟一次使用时间延长至2个月以上。
1号2000m3高炉球式热风炉设计特点及应用

1 'O0 古炉球式热风炉设计特点及应用 -2 0m3  ̄
闭立钢 摘 张海峰 要 :介 绍柳 钢 1 0 m  ̄ 号20 0 3 _ , E高炉 配套 的球 式热风 炉 的设 计 与改进 、应 用效果 ,以及 相应 的干
法 除尘、 热风 炉操作优 化 措施 。
关 键词 :球 式 热风 炉 ;20 0 0 m 高炉 ;干 法除尘 ;球 床 ;操 作制度
耐火 球 直径 :7 m 5 m,6 m 0 m,5 m 0 m; 球床 全 高度 :95 .m; 耐火 球重 量 :117 ; 7t 总蓄热 面 积 :4 6 m ; 35 4
大容积高炉 。本文 阐述了柳钢 l 0 m高炉球 号2O0 3
式 热 风炉 的设 计 特 点 ,通 过 实 施优 化 操 作 制度 , 采 用PD I 控制 自动烧 炉 ,使 高炉 风 温 长 期稳 定 在 I10 8 ℃左右 ,为 高炉 强化 冶炼 提供 了有 力保 证 。
De e o v l pm e nd Ap i a i n o . nta plc H tSt v
BILi a g -g n ZHANG i・e Ha—fng
Ab t a t T e d s n a d i r v me t a d t e a p i ai n e f c f l g n ' No 1 0 m B . sr c : h e i n mp o e n n h p l t f t o i a g s g c o e u . 2 0 0 F P b l o tv a n r d c d t e c re p n ig d y d s n o t v p r t n o t z t n me s r s e b e h tso e w s i to u e . h o r s o d n r u ta d h tso e o e ai p i ai a u e o mi o wa n r d c d si t u e o Ke yW o d : P b l Ho S o e 2 0 m。 r s e b e t tv ; O 0 BE; Dr Du t o lc in P b l B d O e a i g S se y s C l t ; e b e e ; p r t y t m e o n
邯钢高炉热风炉设计特点及改进

邯钢高炉热风炉设计特点及改进王学伶(邯郸钢铁设计院有限公司,河北邯郸 056015)摘要:邯钢高炉热风炉有外燃式、霍戈文内燃改造式、顶燃式三种,这些热风炉均能为高炉提供较高的风温。
在生产实践中,经过不断改进,采取了加强“双预热”、助燃风富氧、优化热风管道系统等多项高风温措施,保证了热风炉的高温、长寿和高效。
关键词:高炉;热风炉;设计;特点;改进中图分类号:文献标识码:文章编号:1006-5008(2013)12-1 引言目前,邯钢共有6座高炉,其中老区有4座,4#高炉有效容积为1000 m3,5#高炉有效容积为2000 m3,7#高炉有效容积为2000 m3,8#高炉有效容积为3200 m3;新区有2座高炉,有效容积全部为3200 m3。
邯钢热风炉几乎涵盖了世界上所有先进热风炉的结构形式。
通过多年的生产实践和改造,这些热风炉均能为高炉提供较高的风温,为节能降耗做出了贡献,本文对邯钢热风炉的设计特点和生产实践进行分析。
2 热风炉设计特点(1)邯钢4#高炉热风炉。
4#高炉原容积为620m3,1997年扩容至1000 m3。
原有热风炉为3座内燃式,高炉扩容时,热风炉设计选择了首钢顶燃式,每座热风炉拱顶配备2台大功率陶瓷燃烧器;在热风炉和高炉之间设有热风下降管,以合理控制热风总管与环管连接中的高差问题。
(2)邯钢5#高炉热风炉。
5#高炉原容积为1260m3,于2005年扩容至容积为2000m3。
扩容时在原有3座外燃式新日铁热风炉基础上增加了一座热风炉,利用原来预留的第4座热风炉基础,热风炉系统其他部位作了必要改造。
热风炉为格栅式陶瓷燃烧器,具有适合配烧转炉煤气或焦炉煤气的能力。
采用相互独立的砌体结构,拱顶、锥体部、大墙砖、连接管道、格子砖砌体等均互为独立砌体。
本次设计采用独特的拱顶砌砖结构,可让各层砌体自由膨胀,完全消除其膨胀应力;完全消除了鼓风压力所产生的拉应力,这是热风炉长寿的重要技术。
为了提高热风炉结构的稳定性,在高温区分别使用了大块砖、带凹凸形砖和阶梯状砖等,而在各个开口部位则用异型砖组合砌筑,组合砖和标准砖连接处配置了花瓣状异型砖,以加强结构的稳定性,对提高热风炉寿命有好处。
- 1、下载文档前请自行甄别文档内容的完整性,平台不提供额外的编辑、内容补充、找答案等附加服务。
- 2、"仅部分预览"的文档,不可在线预览部分如存在完整性等问题,可反馈申请退款(可完整预览的文档不适用该条件!)。
- 3、如文档侵犯您的权益,请联系客服反馈,我们会尽快为您处理(人工客服工作时间:9:00-18:30)。
第19卷第6期2c100年12月炼铁IRt)NMAKINGV01.19.NL】6Decembef200.邯钢2000m3高炉设计特点王学伶焦英占邯郸钢铁有限责任公司摘要邯钢2000m’高炉是引进德国二手设备建造的.设计时进行了国内配套,采用丁槽下原燃料过筛、焦丁与烧结矿混装入炉、井罐无料钟炉顶、“陶瓷杯”炉底炉缸结构、底滤法水冲渣、煤粉浓相辅送、外燃式热风炉硬出铁场电除尘等多项先进技术。
关键词高炉二手设备设计改进Designcharacteristicof2000m3BFatHandanIron&SteelCo..Ltd.(HandanIron8SteejCo..Ltd.)WangXuelingJiaoYingzhanAbstractThe2000m’BFatHandanlron&SteelCo..LtdwasconstrucledusingthesecondhandequipmentimportedfromGermany.Duringdesigning,afewofadvancedtechniqueswereadopted,suchasscreeningofrawmaterialunderbins・mixedchargingof15--25mmsizecokenut,K.bell—lesslopwithparallelhoppers,ceramiccup。
".OCP”slaggranulation.densephasecoaltransportation.externalc(jrlfmstionhotstoveandcastbouseelectricdustcoltecfor,etc.KeywordsbLastfurnacesecond-bandequipmentdesignhnprovementI概况邯钢2000m3高炉系引进德国多特蒙德克虏伯公司3号高炉的设备和技术建造的。
多特蒙德克虏伯公司3号高炉的基本情况如下:高炉f艺布置紧凑,占地面积小;高炉矿槽为钢结构,料坑深度为一】8.5m.槽下设备全部布置在地坑内;料车有效容积为12n13.主卷扬由2台250kW的直流电机驱动,料坑内斜桥角度为44。
24’24”.出料坑后斜桥角度为46。
28’40”;并罐无料钟炉顶,料罐容积为2×24m3.气密箱采用加压煤气冷却和密封;高炉炉体为框架自立式结构.有效高度为25.55m.高径比为2.27.28个风口.修同日期r2000—09—05联系人:焦英占高级工程师:0560151河北省邯郸市邯郸钢铁奇限责任公司设计院・10-2个铁口,炉底、炉缸采用炭砖陶瓷杯结构,炉身为薄壁内衬;炉缸以下采用1二业水喷淋冷却,炉缸以上为“I”’型带勾头冷却壁与不带勾头冷却壁相结合结构,冷却壁采用软水密闭循环,并配有20m3膨胀罐;热风炉为4座马琴式外燃热风炉.高炉熔渣采用火车运输;两出铁场呈90。
布置.炉前设备为液压泥炮,液压气动开口机和液压摆动流嘴;煤气清洗采用比肖夫湿法除尘系统.即在洗涤塔内i殳置两级串联喉口,既能除尘又能调节炉顶压力;高炉风机为烧混合煤气的燃气轮机.炉前采用电除尘;各系统均采用计算机控制。
邯钢2000m’高炉设计围绕“高产、优质、低耗、长寿”的方针.结合邯钢的原燃料条件,遵循充分利用国外先进技术和设备的原则。
除供返料、矿槽、水冲渣、喷煤、高炉和热风炉耐火材料、各设备基础、各系统混凝土厂房及少量没备国内配套外,其余设施全部利用原高炉设备。
设计指标为:利用系数2.0,焦比350kg/t.煤比250kg/t,风温l150~1200(、,顶压0.150MPa。
2主要设计内容2.1供返料、矿槽系统根据邯钢具体条件。
供返料、矿槽系统全部重新设计。
矿槽为架卒式,为方便检修,槽下设备全部布置在标高士0.00mm以上。
高炉炉料结构采用高碱度烧结矿配进口富矿,熟料率为8j%。
原燃料供应考虑两路供料,即设直送系统和备用系统。
直送系统为烧结矿由400m2烧结机直送,焦炭由邯钢5、6号焦炉直送,块矿、杂矿由原料场直送;备用系统为原燃料伞部从1260m3高炉槽卜接出,输送至2000m3高炉槽上.这样使邯钢90m?烧结机的烧结矿和3、4号焦炉的焦炭也可供2000m3高炉使用.最大限度地保证r高炉正常生产。
矿槽部分设计时采用了15~25film焦丁回收技术,实现了矿焦混装入炉,以降低焦比,提高产量。
矿槽、焦槽并列布置,分别以高炉中心线为轴对称布置。
共没4个烧结矿槽(4×700m’)、2个块矿槽(2×700r[13)、4个杂矿槽(2×,120m。
}2×370Ill3)、4个焦炭槽(4×580m3)、1个碎矿仓(170m3)、1个碎焦仓(60m3)和1个焦丁仓(60m5)。
烧结矿和焦炭贮存时间分别为18h和24h。
烧结矿、块矿经手动闸门、l250mm×1500mm电动给料机送人1800mitt×4200rllrn烧结矿筛筛分,筛上物进入12m3称量漏斗称量.筛下物经皮带运至碎矿仓.由汽车运走。
杂矿经手动闸门、1250mm×1500Inlll电动给料机,送人6m3称量漏斗称鞋。
称量后的烧结矿、块矿及杂矿经皮带送入料坑内的矿右集中称量漏斗内,由料年(12ITI?)运至炉顶。
焦炭经手动闸门、i500mm×3300mm振动筛筛分.筛P物送人l2m。
称量漏斗称量,称量后经皮带运至料坑内的焦炭集中称量漏斗.冉料年运至炉顶。
筛下物运至碎焦仓.在碎焦仓上再次筛分,分为碎焦和焦丁,绛各自溜槽进入各自的贮仓;焦丁经闸门、皮带机进入焦丁称量漏斗(6in3),称量后与矿石混装.运至料坑内矿石集中称量漏斗.由料车运至炉顶。
2.2料坑及卷扬料坑内设2个矿石集中称量漏斗(12m3)和2个焦炭集中称量漏斗(12rll‘),存矿石集中称量漏斗和焦炭集中称萤斗之间设翻板机。
翻板机和称量漏斗闸门采用液压驱动。
上料仍采用斜桥、料车上料。
为了节省投资.料坑标高由18.5m抬高至15.5n1,斜桥角度不变,12m3料车不变,利用原料车卷扬机、滚筒.可满足高炉日产生铁4000I以上的要求。
2.3炉项系统炉顶设备全部利用原高炉设备,仍为并罐无料钟炉顶.料罐加高400mm.加高后料罐有效容积为2×28m3卜下密封阀直径为800mill.料流调节阀直径为700mill,全部为液压驱动,传动齿轮箱由加压煤气冷却和密封改用水冷N!封,冷却采用软水闭路循环.设有专门的冷却水系统,以保证冷却水压力稳定.将水温控制在允许范围之内。
原燃料由料车卸至炉顶移动受料车内,再根据料制卸至料罐.经摆动溜槽把料布到高炉内。
布料型式以环形布料为主,并可实现螺旋布料、扇形布料和定点布料。
料罐新设计二次均压.恢复一次均压。
一次均压采用半净煤气,二次均压采用氮气。
炉顶设计最高压力为0.165MPa.工作压力为0.】50MPa。
为了方便检修,炉顶设汁1台20t吊车,1台・11。
8t吊车。
2.t炉体系统高炉内型设计结台邯钢的原燃料条什,在理论计算的基础上参考f-I蚓内外同类型高炉的内型尺寸,本若尽量利用原有高炉设施的腺则.维持炉顶钢圈和铁『1标高不变.对内型的尺寸作广适当调整。
邯钒2000ITI。
南炉设有2个铁u,1个渣【j,28个风口,高径比为2,24,北铁层深度为2000mm。
高炉的主要特点足炉型较为矮胖,死铁层较深,风L】数11多.这样有利于高炉接受大风量进行强化冶炼,同时减轻r铁水环流埘炉缸内衬的冲刷。
高炉炉体框架和平台采』|j原高炉的炉体框架和平台.其结构形式为“自立式”.框架尺寸为l5m×15.2[In,高炉平台荷载和炉顶的主要荷载由该框架承受。
在框架r设有热风围管平台等6层平台.供安装设备和操作榆修使刚。
炉体冷却设备按国内的习惯和经验重新设计.炉底采刚砌砖底部埋设水冷管的水冷形式;炉缸以r由喷淋冷却改为全冷却壁冷却结构.拎却高度直到炉喉钢砖下沿。
炉体共没15段冷却壁.炉底、炉缸区(一~四段)采用光面冷却壁;炉腹区(五~六段)采用背部带蛇形管的镶砖冷却壁;炉腰及炉身下部(七~十段)采用凸台带双层冷却水管的镶砖冷却壁;炉身中上部(十一~十四段)为凸台带单崖水冷管的镶砖冷却壁,炉身上部(十五段)为倒扣光面冷却壁。
冷却壁内表面与炉型线重台。
一~三段材质为低铬铸铁。
四~十段材质为球墨铸铁,十一~十五段材质为低铬铸铁。
光面冷却壁与炉壳采用螺栓固定,其余冷却壁利用冷却壁进出水管上的保护套管,采JH固定点、滑动点和浮动点相结合的方式固定。
并在炉壳与进出水管间采用波纹补偿器进行密封.这样可避免水冷管的剪断.并保1It很好地密封。
・1’‘高炉冷却系统重新设计,水泉则全部利用原高炉水泵。
高炉冷却系统主要由炉体软水密闭循环冷却系统、炉底和热风炉软水峦闭循环冷却系统、高压净环水冷却系统以及中压净环水系统组成。
设计炉体软水密闭循环冷却系统(主要冷却炉体一~十三段冷却J{!处的内衬)时,将炉顶大平台上的201T13的膨胀罐改为啦气罐.以脱去生产过程中产生的气体;在炉顶液压站上层平台设置20n・。
膨胀罐.在罐内充N,.以保证系统压力稳定。
炉底和热风炉软水密闭循环冷却系统冷却炉底与热风炉脚门。
高压净环水冷却系统主要冷却风、渣L|小套。
中压净环水系统主要冷却十四、十五段冷却壁,风口中套,渣【J大中套;在炉役后期炉体喷淋也采川中压净环水。
高炉内衬全部重新设计。
炉底、炉缸砌体采用炭砖加陶瓷杯结构,炉底第一至四层为400ITIIll厚半石墨化炭砖,第五层为500FJlm厚微孔炭砖,第六,七层为陶瓷杯。
第一层陶瓷杯垫采用斜面压迫“人”字型砌筑.第二层陶瓷杯垫采用斜面压迫同心圆砌筑。
炉底、炉缸第六至十八层外层为微孔炭砖,内侧为陶瓷杯。
铁口、渣rl和风口均采用刚玉莫来石组合砖砌筑。
炉体采用“薄壁”内衬形式,炉腰及炉身砖衬厚度为450lnm。
炉腹、炉腰及炉身下部采用st。
N;结合SiC砖砌筑.炉身中下部采用烧成微孔铝炭砖砌筑,炉身上部采用浸磷高铝砖砌筑。
高炉风口设备重新制作,风口大套为铸钢件,不设冷却,二套和小套为铸铜件,且小套为黄流式风口。
送风支管由原高炉设备修理改造而成,并装有万向波纹管。
炉顶打水装置、十字测温装置及炉喉钢砖重新设计.探尺、炉顶点火枪等利用原有设备。
2.5热风炉系统采用4座马琴式外燃热风炉,呈一列分两组布置在高炉斜桥两侧、并没有热媒式换热器预热助燃空气和煤气,4座热风炉采用交错并联或两烧两迭的L作制度,年平均送风温度为I1IO~l200(。
热风炉系统除耐火材料及少量设备国内配套外.其余i{|5分包括热m炉的部分炉壳、阀门、波纹补偿器、助燃风机、热媒式换热器、检修吊ji,液压站,给排水管及梯于平台等均利用原有没备。