激光切割技术的研究与应用
激光切割技术在金属制造业中的应用

激光切割技术在金属制造业中的应用激光切割技术是一种高精度、高速度、低成本、无损伤的加工工艺,已经在金属制造业中得到广泛应用。
本文将从激光切割技术的基本原理、激光切割设备的分类和应用、激光切割技术在金属加工中的优点和应用案例三个方面详细介绍激光切割技术在金属制造业中的应用。
一、激光切割技术的基本原理激光切割技术是利用高能量密度的激光光束,对金属材料进行光化学、热化学反应的过程。
激光束通过准直光学装置后,被聚焦到非常小的光斑点上,达到高能量密度,这使得工件表面很快被局部加热到高温,达到融化或者气化的状态,而后利用氧化反应或机械挤压的作用形成微细切割缝。
二、激光切割设备的分类和应用激光切割设备可以按激光系统、控制系统、切割头、电气系统等参数不同,分类为飞行光路激光切割机、射柱光路激光切割机、光纤激光切割机、半导体激光切割机等几类。
现在金属材料切割摆脱了激光的限制,综合应用了多重技术,提高了切割质量和效率,并且在多个领域取得了广泛的应用,如:1、航空航天制造飞机零件和发动机部件,大部分采用3D激光切割机进行生产,这种设备可以对钛合金、铝合金、不锈钢等难加工金属进行切割,切割质量高、效率高、成本低,是航空航天业里的常见设备。
2、汽车制造激光切割技术应用到汽车制造中,制造各种汽车板材、车门、车底板等,快速、精准的零件制造是实现汽车制造过程自动化的重要一步。
3、建筑制造在建筑制造领域中广泛应用于制造各种屋顶和铝合金装饰材料,如窗户、门、玻璃幕墙、屋顶保温等。
三、激光切割技术在金属加工中的优点与应用案例1、精度高激光切割机的划割线可达0.1mm,切割精度高,可以满足一些对精度要求很高的场合,如电子工业中计算机及其配件的加工、汽车工业在车身制造中的孔洞加工等。
2、切割面质量高激光切割边缘粗糙度低,无毛刺、无裂缝、无氧化皮等缺陷,可高效保证材料的减弱。
3、模具加工在制造车间中,激光切割还可以应用于电极板、钢板弯曲成型、线切割、钣金加工等方面。
激光切割实验报告

激光切割实验报告激光切割实验报告激光切割是一种高精度、高效率的切割技术,广泛应用于工业生产和科学研究领域。
本实验旨在探究激光切割的原理、参数对切割质量的影响以及其在实际应用中的潜力。
一、激光切割原理激光切割是利用激光束的高能量密度将工件表面局部加热至熔化或汽化,通过气流将熔融或气化的材料吹散,从而实现切割的过程。
激光切割具有热影响区小、切割速度快、切割质量高等优点,适用于各种材料的切割。
二、实验装置和参数设置本实验采用了一台高功率CO2激光切割机,激光功率为2000W,切割速度可调节。
实验材料选择了不锈钢板,厚度为2mm。
实验过程中,我们分别调节了激光功率、切割速度和气流压力等参数,以观察其对切割质量的影响。
三、实验结果与分析通过实验,我们发现激光功率对切割质量有明显影响。
当激光功率过低时,切割速度较慢,切割面不光滑,存在较大的毛刺;而当激光功率过高时,切割过程过于猛烈,容易导致材料熔化过度,出现熔渣和裂纹。
因此,选择适当的激光功率是保证切割质量的关键。
切割速度也是影响切割质量的重要参数。
实验中我们发现,在一定范围内,切割速度的增加会导致切割面的质量下降。
这是因为切割速度过快时,激光束在材料上停留的时间较短,无法充分加热材料,导致切割面出现不完全熔化的现象。
因此,选择适当的切割速度是保证切割质量的关键。
气流压力对切割质量也有一定影响。
适当增加气流压力可以将熔融或气化的材料及时吹散,防止其在切割面上重新凝固,从而保证切割面的光洁度。
但是,气流压力过大会导致切割过程中材料被吹散,影响切割线的精度。
因此,选择合适的气流压力是保证切割质量的关键。
四、激光切割在实际应用中的潜力激光切割技术在工业生产中有着广泛的应用前景。
首先,激光切割可以实现对各种材料的高精度切割,适用于金属、非金属等多种材料。
其次,激光切割速度快、效率高,能够大幅提高生产效率。
此外,激光切割无需接触工件表面,避免了传统切割方式中刀具磨损和材料变形的问题。
激光应用在材料加工中的研究

激光应用在材料加工中的研究一、引言激光作为一种集光、电、机等多学科于一体的综合应用技术,在材料加工领域发挥着重要的作用。
本文将就激光应用在材料加工中的研究进行探讨,分别从激光切割、激光焊接和激光钻孔三个方面进行讨论,以期对相关领域的科研和实践工作提供参考。
二、激光切割技术及其应用激光切割是激光加工技术中的重要分支之一,其将高能密度的激光束直接作用于材料表面,通过瞬间的能量转化,使材料迅速升温并融化、汽化,从而实现切割目的。
激光切割技术在材料加工领域具有广泛的应用。
首先,激光切割技术对于薄板材料的切割具有独特优势。
激光束的高能量密度和小热影响区使其能够实现精细、高速的切割,广泛应用于金属薄板的制作。
其次,激光切割技术对于非金属材料的切割也有成熟的应用。
如对于石材、玻璃等材料,激光切割技术能够实现精细的切割,并避免了传统机械切割中易产生的缺陷和损伤。
三、激光焊接技术及其应用激光焊接是利用激光束的高能量密度和小热影响区,将材料加热至熔点以上并进行熔化的一种焊接方法。
激光焊接技术具有焊缝狭窄、熔深度大、焊缝成形好等特点,在材料加工领域得到广泛应用。
激光焊接技术在汽车制造、航空航天、电子设备等领域具有重要的应用。
在汽车制造中,激光焊接技术可以实现车身零部件的高效焊接,提高产品质量和生产效率。
在航空航天领域,激光焊接技术可以应对复杂结构的焊接需求,提高焊接质量和可靠性。
在电子设备制造中,激光焊接技术可以实现微观焊接,满足电子器件的小型化和高密度集成要求。
四、激光钻孔技术及其应用激光钻孔技术是利用激光束的高能量密度和小热影响区,在材料表面产生融化、汽化等热效应,从而实现对材料的钻孔。
激光钻孔技术在制造业中得到了广泛应用,尤其在微细孔加工中具有独特优势。
激光钻孔技术可以实现无接触、高精度的孔加工,广泛应用于微电子器件的制作、精密模具加工等领域。
此外,激光钻孔技术还可以应对复杂材料的孔加工需求,如钨、钛合金等高强度材料。
激光切割技术国内进展及应用案例论文

激光切割技术国内进展及应用案例学院:机械工程学院系:机械制造班级:11机制2班制作人:刘卓聿、雷丰源指导老师:龚老师【摘要】随着我国国民经济的快速发展,我国正从一个制造大国向制造强国迈进。
激光加工制造技术是一项集光、机、电于一体的先进制造技术,在许多行业中已得到了越来越普遍的应用。
而在工业生产中,激光切割占激光加工的比例大约在70﹪以上,是激光加工行业中最重要的一项应用技术。
本文深入浅出地介绍了目前常用的激光切割技术,而且内容丰富、实用性强。
【关键词】激光加工、激光切割技术目录一、激光切割的基本技术二、激光切割技术的优点三、激光切割技术的发展四、国内激光技术现况五、激光切割技术的分类5.1汽化切割5.2熔化切割5.3氧化融化切割5.4控制断裂切割六、激光切割技术的应用七、参考文献一、激光切割的基本技术激光:(LASER-Light Amplification of Stimulate Emission Radiation)是利用原子或分子受激辐射的原理,使工作物质受激而产生的一种单色性高,方向性强,亮度高的光束。
激光器:激活介质、激活装置、光学谐振腔激光器按工作介质来分类分为固体激光器、液体激光器、气体激光器、半导体激光器,此为,还有化学激光器和自由电子激光器等。
原理:利用高功率密度的激光束来穿过材料表面,在极短的时间内将材料加热到几千甚至上万度,使材料融化或者气化,并用高压气体将融化或者汽化的物质从切缝中吹走,以达到切割材料的目的。
经过30多年的发展,现已开发的激光器超过200多种,种类繁多,特点各异,用途也各不相同。
虽然激光器的种类繁多,但目前适用于激光切割的工业化和YAG激光器。
激光器主要是CO2激光加工技术是利用激光束与物质相互作用的特性对材料(包括金属与非金属)进行切割、焊接、表面处理、打孔、微加工等的一门技术。
二、激光切割技术的优点激光加工技术与传统加工技术相比具有很多优点,所以得到如此广泛的应用。
激光切割技术的原理与应用
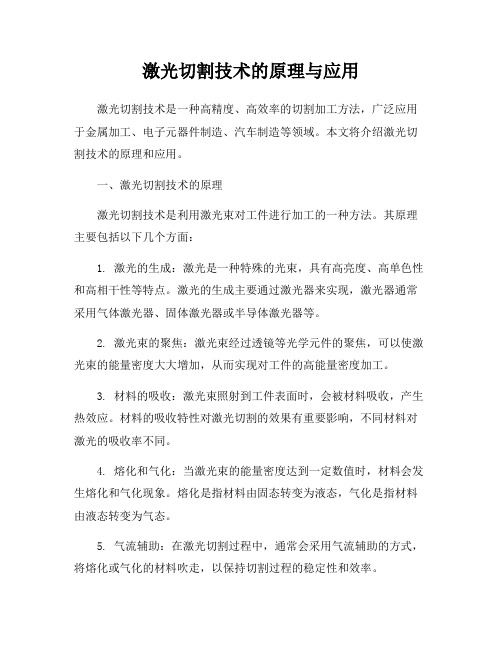
激光切割技术的原理与应用激光切割技术是一种高精度、高效率的切割加工方法,广泛应用于金属加工、电子元器件制造、汽车制造等领域。
本文将介绍激光切割技术的原理和应用。
一、激光切割技术的原理激光切割技术是利用激光束对工件进行加工的一种方法。
其原理主要包括以下几个方面:1. 激光的生成:激光是一种特殊的光束,具有高亮度、高单色性和高相干性等特点。
激光的生成主要通过激光器来实现,激光器通常采用气体激光器、固体激光器或半导体激光器等。
2. 激光束的聚焦:激光束经过透镜等光学元件的聚焦,可以使激光束的能量密度大大增加,从而实现对工件的高能量密度加工。
3. 材料的吸收:激光束照射到工件表面时,会被材料吸收,产生热效应。
材料的吸收特性对激光切割的效果有重要影响,不同材料对激光的吸收率不同。
4. 熔化和气化:当激光束的能量密度达到一定数值时,材料会发生熔化和气化现象。
熔化是指材料由固态转变为液态,气化是指材料由液态转变为气态。
5. 气流辅助:在激光切割过程中,通常会采用气流辅助的方式,将熔化或气化的材料吹走,以保持切割过程的稳定性和效率。
二、激光切割技术的应用激光切割技术具有高精度、高效率、无接触等优点,因此在许多领域得到广泛应用,主要包括以下几个方面:1. 金属加工:激光切割技术在金属加工领域应用广泛,可以对不同种类的金属材料进行高精度切割,如不锈钢、铝合金、铜等。
2. 电子元器件制造:激光切割技术在电子元器件制造中起到关键作用,可以实现对微小零件的精确切割和加工,提高生产效率和产品质量。
3. 汽车制造:汽车制造中需要大量的金属零部件,激光切割技术可以实现对汽车零部件的高效加工,提高生产效率和降低生产成本。
4. 激光雕刻:除了切割,激光技术还可以应用于雕刻领域,如激光雕刻木材、皮革、塑料等材料,实现精美的图案和文字刻画。
5. 医疗器械制造:激光切割技术在医疗器械制造中也有重要应用,可以实现对各种材料的精确切割和加工,满足医疗器械的高要求。
激光切割技术的研究现状
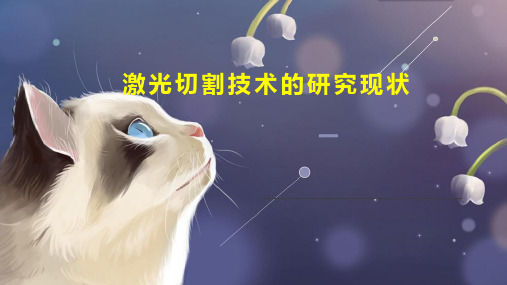
3、高效加工:激光切割技术的速度很快,能够在短时间内完成大量材料的切 割和加工。这使得激光切割技术在批量生产中具有显著优势,可大大提高生产 效率。
三、激光切割技术的优势
相较于传统的切割技术,激光切割技术具有以下优点:
1、精度高:激光束的直径通常在0.1-0.5mm之间,能够实现精确的切割和打 孔。此外,激光切割技术的热影响区小,可减少对周围材料的损伤。
此外,激光切割技术在不同领域的应用也取得了显著的成果。在汽车制造领域, 激光切割技术已成为汽车零部件精密切割的主要方法之一,具有高精度和高效 率等特点。在航空航天领域,激光切割技术对于高强度、轻质材料以及复杂形 状的零部件切割具有显著优势,能够大大提高生产效率和降低成本。
激光切割技术的研究方法
激光切割技术的研究方法主要包括文献调研、实地调研和实验验证。文献调研 主要从学术论文、专利、行业报告等方面收集相关资料,对激光切割技术的原 理、工艺流程、应用领域等进行深入研究。实地调研主要是对激光切割设备生 产厂家、使用企业进行访谈和实地考察,了解激光切割技术的实际应用情况和 问题。实验验证是在实验室条件下,通过实验对比不同参数设置、不同材料对 激光切割效果的影响,为优化切割工艺提供依据。
激光切割技术的成果与不足
激光切割技术的研究已经取得了显著的成果,主要表现在以下几个方面:
1、关键技术的研发和应用:激光切割技术的关键技术包括激光器、光束传输 与聚焦、切割路径规划、切割参数设置等。这些技术的不断研发和应用,提高 了激光切割的精度和效率。
2、成本较高:激光切割设备价格较高,对于一些中小型企业来说,投资成本 较高,存在一定的经济压力。此外,激光切割设备的维护和升级也需要一定的 成本。
2、速度快:激光束的功率和速度可以快速完成切割和打孔任务,从而大大提 高生产效率。
激光切割技术的原理与应用
激光切割技术的原理与应用激光切割是一种利用激光照射物体,使其发生熔化和蒸发从而实现切割的技术。
相对于传统切割技术,激光切割具有精度高、速度快、加工范围广等优点,因此在各行业的制造过程中都有广泛应用。
一、激光切割的原理激光切割技术的原理类似于激光焊接技术,不同的是,激光切割需要采用高能量密度的激光束,因为切割涉及到材料的熔化和蒸发。
激光束在照射物体时会产生能量,随着能量密度的升高,材料表面温度升高,材料发生熔化和蒸发,同时由于激光束微小的热影响区域,因此能够实现高精度的切割。
一般来说,激光切割技术的原理可以分为四个阶段:1.激光束的照射:激光束在切割头中聚焦,形成一个高能量密度的点。
2.材料的加热:激光束能量被吸收并转换为热能,使材料表面温度升高。
3.材料的蒸发:由于激光束微小的热影响区域,材料表面开始熔化,形成一个熔池,然后随着能量密度的升高,熔池内部发生均匀的蒸发。
4.激光束的穿透:激光束透过物体的开口,形成所需要的片断。
二、激光切割的应用激光切割技术广泛应用于以下领域:1.金属切割:激光切割技术可以对各种类型的金属进行切割,包括不锈钢、钛、铝、铜、钢等材料。
在金属切割领域,激光切割技术具有操作简单、成本低、自动化程度高等优点。
2.汽车制造:激光切割技术可以用于汽车制造中各种复杂形状的零件制造,例如底板、车门、天窗等。
与传统切割技术相比,激光切割能够更有效地减少材料损耗,提高零件的精度,并可以在生产过程中实现自动化。
3.电子制造:在电子制造领域中,激光切割技术可以用于制造各种形状大小的开口,在显示器制造、半导体制造等领域中都具有广泛的应用。
4.建筑业:激光切割技术可以用于建筑业中的各种不同类型的建筑材料切割,例如玻璃、金属板、木板等材料,可以用于实现建筑物中的文化雕刻、装饰、门窗、吊顶等部分的制作。
三、激光切割的未来发展激光切割技术在工业制造领域的应用愈发广泛,随着激光切割技术的不断发展完善,其应用范围也在逐年拓展,成为工业制造的重要环节之一。
激光切割调研报告
激光切割调研报告激光切割是一种利用激光束对工件进行切割的加工方法。
相比传统的切割方法,激光切割具有精度高、切割速度快、加工灵活等优点,因此在工业领域得到广泛应用。
本调研报告旨在对激光切割进行深入研究,并对其应用前景进行评估。
一、激光切割的原理和工艺流程激光切割的原理是利用高能量密度的激光束对工件进行瞬间加热,使其熔化或汽化,进而达到切割的目的。
激光切割工艺流程主要包括以下几个步骤:首先是激光源的选取,根据实际需求选择波长和功率适当的激光源;其次是激光束的聚焦,通过透镜对激光束进行聚焦,提高光束的能量密度;然后是切割参数的设定,包括激光功率、切割速度、气体流量等;最后是对工件进行切割,激光束照射在工件上,进行切割操作。
二、激光切割的应用领域激光切割技术广泛应用于各个工业领域,主要包括以下几个方面:1. 金属加工领域:激光切割可用于金属板材、钢管、金属零件等的切割加工,具有高精度、高速度的优势。
2. 汽车制造领域:激光切割可用于汽车板材的切割、零件的加工,提高生产效率和产品质量。
3. 电子电器领域:激光切割可用于电路板、半导体材料等的切割,具有高精度、无接触等特点。
4. 精密机械领域:激光切割可用于精密机械零件的切割、加工,提高加工质量和效率。
三、激光切割的优点和挑战激光切割相比传统的切割方法具有以下优点:1. 高精度:激光束切割精度高,可以实现微米级别的精度要求。
2. 高速度:激光切割速度快,可以大幅提高生产效率。
3. 加工灵活:激光切割可以对各种形状的工件进行切割,适应性强。
4. 无接触加工:激光切割是无接触加工,避免了物理接触引起的损伤。
5. 自动化程度高:激光切割可以与计算机控制系统相结合,实现自动化操作。
然而,激光切割仍然面临一些挑战:1. 设备成本高:激光切割设备价格昂贵,对初创企业和中小型企业来说门槛较高。
2. 能源消耗大:激光切割需要消耗大量的电力和气体,成本较高。
3. 材料限制:激光切割对材料有一定的限制,对一些特殊材料难以处理。
激光切割技术在钢板加工中的应用研究
激光切割技术在钢板加工中的应用研究第一章:引言钢板是机械加工和建筑工程中常用的材料之一,因其硬度高、韧性好、耐腐蚀等特点,被广泛应用于各行各业中。
而激光切割技术则是一种现代化的钢板加工技术,其速度快、精度高、可靠性好等特点被越来越多地应用于钢板加工的领域中。
本文将从激光切割技术的基本原理、设备结构及工艺流程等几个方面,探讨激光切割技术在钢板加工中的应用研究。
第二章:激光切割技术的基本原理激光切割技术是一种利用激光束对物体进行加工的技术,其基本原理是利用激光束对钢板进行热加工,使钢板部分受热蒸发,从而达到对钢板进行切割的目的。
其操作流程如下:1.将激光器发出的激光束集中到光斑上;2.将光斑聚焦到钢板上;3.钢板局部受热蒸发,形成切口;4.激光束和钢板分别移动,完成切割。
第三章:激光切割技术的设备结构激光切割技术的设备结构包括三部分:激光器、光纤传输系统和切割系统。
其中,激光器主要用于产生高能高稳定的激光束;光纤传输系统主要用于将激光束传输到切割系统上;切割系统则主要用于将激光束聚焦到钢板上,并移动完成切割。
第四章:激光切割技术的工艺流程激光切割技术的工艺流程包括以下几个步骤:1.钢板上涂抹保护液,以保护钢板不受氧化的影响;2.将钢板放置在激光切割机工作台上,调整钢板位置,使其对准光斑;3.开启激光切割机,调整相关参数,如激光功率、切割速度等;4.激光切割机进行热加工,实现钢板切割;5.切割完成后,对钢板进行后处理,如去除保护液、打磨等。
第五章:激光切割技术在钢板加工中的应用研究激光切割技术在钢板加工中应用广泛,如下:1.在船舶工业中,利用激光切割技术,可将海事运输的需要的不锈钢板进行切割。
由于钢板是船舶上使用最多的材料之一,激光切割技术的应用,大大节省了人力和成本。
2.在机床制造领域,可利用激光切割机对各类机器底座,导轨板等零件进行切割加工。
激光切割技术的应用,极大地提高了加工的效率和精度。
3.在建筑领域,激光切割技术可实现对钢板雕刻等艺术处理,如钢板上雕刻楼房或汽车形状的图案等。
金属加工行业领域激光切割技术的创新与应用
金属加工行业领域激光切割技术的创新与应用随着科技的不断进步,金属加工行业领域的切割技术也得到了长足的发展和创新。
其中,激光切割技术作为一种高效、精确和可靠的加工方法,逐渐在金属加工行业中得到广泛应用。
本文将介绍金属加工行业领域激光切割技术的创新与应用。
第一部分:激光切割技术的发展历程激光切割技术起源于20世纪60年代,并在不断的研究和改进中逐渐成熟。
最早的激光切割系统采用CO2激光器,其具有高功率、高光束质量和高光电转换率等优点。
然而,由于CO2激光器波长较长,不适用于某些金属材料的切割。
随后,光纤激光器的出现填补了这一空白,其波长较短,对金属材料具有较好的切割效果。
第二部分:激光切割技术的创新随着科技的进步,激光切割技术也在不断创新中得到提升。
首先,激光切割的速度得到了显著提高。
新型激光器的出现使激光切割的速度更快,切割效果更加精细。
其次,激光切割的精度有了质的飞跃。
新一代的激光切割系统采用了先进的光学技术和自动化控制技术,大大提高了切割的精度和稳定性。
此外,激光切割技术还实现了对不同形状、不同材料的金属进行精确切割,为金属加工行业带来了更广阔的应用空间。
第三部分:激光切割技术的应用领域激光切割技术在金属加工行业中有着广泛的应用。
首先是钢铁行业,激光切割技术可以对各种厚度的钢板进行高效、精确的切割,应用于船舶制造、汽车制造等领域。
其次是家电行业,激光切割技术可用于切割家电产品的外壳,使其具备更好的外观和质量。
此外,激光切割技术还在建筑、航空航天、电子等领域中得到了广泛应用,为这些行业的发展提供了强有力的支持。
结论:激光切割技术作为金属加工行业领域的一种创新加工方法,其在速度、精度和应用领域上都得到了长足的发展。
随着科技的不断进步,相信激光切割技术将继续创新和提升,为金属加工行业带来更多的发展机遇和挑战。
- 1、下载文档前请自行甄别文档内容的完整性,平台不提供额外的编辑、内容补充、找答案等附加服务。
- 2、"仅部分预览"的文档,不可在线预览部分如存在完整性等问题,可反馈申请退款(可完整预览的文档不适用该条件!)。
- 3、如文档侵犯您的权益,请联系客服反馈,我们会尽快为您处理(人工客服工作时间:9:00-18:30)。
激光切割技术的研究与应用姓名:张国涛学号:08010705 专业班级:机电工程学院08级基地2班摘要:该技术采用激光束照射到钢板表面时释放的能量来使不锈钢熔化并蒸发。
激光源一般用二氧化碳激光束,工作功率为500~2500瓦。
该功率的水平比许多家用电暖气所需要的功率还低,但是,通过透镜和反射镜,激光束聚集在很小的区域。
能量的高度集中能够进行迅速局部加热,使不锈钢蒸发。
此外,由于能量非常集中,所以,仅有少量热传到钢材的其它部分,所造成的变形很小或没有变形。
利用激光可以非常准确地切割复杂形状的坯料,所切割的坯料不必再作进一步的处理。
而且激光切割技术的研究工作已取得许多重要成果,诸如在加工有机玻璃、激光切割中的焦点位置检测方法等;此外,激光切割在现代生活中的应用也很广泛。
关键词:激光切割;研究;应用;方法;检测;下面就加工有机玻璃的激光切割技术的研究及激光切割中的焦点位置检测方法的研究和激光切割技术的应用作简要介绍。
一、加工有机玻璃的激光机切割技术研究加工有机玻璃的激光机切割速度快、精度高,定位准确。
可生产工艺礼品、面板镜片机箱、模型玩具、广告灯箱招牌展示用品、包装盒等。
激光应用于切割和焊接薄金属板已有30年了,通过聚焦光束局部地加热材料。
这种方法灵活性好,经济效益高,在很多工业应用领域大放异彩。
其实玻璃有比金属更低的热传导,所以激光应该可以顺理成章地应用于玻璃的切割。
事实上,一些公司早在70年代即开始发展成套系统,当时使用的是千瓦输出功率水平的CO2激光器。
但是,因为功率水平高,对玻璃造成不容忽视的热影响,以致融化局部材料,所以当时的激光切割技术难以保证整齐、平滑的切割边缘,在许多应用场合中,仍然需要打磨切割边缘。
同时,当时CO2激光器的价格非常昂贵,令人生畏。
近来,一些工程人员和学者发现了应用较低功率的激光器使玻璃分离,同时不对玻璃造成融化等热影响的玻璃切割方法。
这种方法说来复杂,涉及细节技术很多,其基本原理是利用激光引致的应力使玻璃"分离"。
期间,得益于封离型CO2激光器技术的发展和成熟,激光切割玻璃技术更显得经济、实用。
在我们的研究中,使用平均输出功率为150W的CO2激光器(Coherent公司的K-150型),通过聚焦光路在玻璃表面形成椭圆型的聚焦点,椭圆的聚焦焦点保证了激光能量在切割线两侧的均匀的和最优化的分布。
玻璃强烈地吸收10.6微米的激光,所以几乎所有的激光能量都被玻璃表面15微米吸收层所吸收,相对玻璃表面移动激光光点形成所需的切割线。
选择合适的移动速度,保证既有足够的激光热量在玻璃上形成局部的应力纹样分布(设定的切割线),同时又不会将玻璃融化。
激光切割中另一个关键部件是淬火气(水)嘴,随着激光光点的移动,淬火气(水)嘴将冷空气(水)吹到玻璃表面,对受热区域进行快速淬火,玻璃将沿着应力最大的方向产生断裂,从而将玻璃沿着设定的方向分离。
粤铭激光雕刻机切割机打标机需要说明的是,为了引发玻璃产生断裂,需要首先用机械法在切割线的起点划出微小的起始裂痕。
与传统的机械切割法相比,这种新的方法有几个重要的优点。
首先,这是一步即可完成的、干燥的加工过程。
边缘光滑整齐,不需要后续的清洁和打磨。
并且,激光引致的分离过程产生高强度、自然回火的边缘,没有微小裂痕。
使用这种方法,避免了不可预料的裂痕和残破,降低了次品率,提高了产量。
①边缘强度因为边缘质量优秀,以及加热/淬火过程中的自然回火效应,激光切割的边缘强度非常高。
Jena的Otto-Schott-Insititut研究所根据DIN5230011参数做了独立的测试,相关数据已公开发布。
采用这种新方法,与机械法加工后又打磨的样品相比,边缘强度提高了30%左右。
②厚度和切割速度限制切割速度的有3个因素:玻璃的厚度、材料的热膨胀系数、以及激光器的输出功率。
在这个测试中,我们使用150W输出功率的CO2激光器切割a=7.2 x 10-6、厚度为1.1mm的玻璃,直线切割,速度为500mm/秒。
作为比较,硬质金属轮切割同样厚度同种玻璃的速度可达1500mm/秒。
但是,即使是在注重速度的应用中,这种差异也将被激光切割所带来的经济性和质量优势所弥补。
同时,我们都相信,进一步的加工过程优化以及采用更高输出功率的激光器进行切割都会容易地将加工速度提高2至3倍。
曲线切割③应用长远来说,激光引致的分离技术将在许多玻璃的切割应用中取代机械法。
近期,激光切割已在下述的三个应用领域中显示强大的技术优势,它们是:CRTS,平板显示,以及汽车的风挡玻璃等的切割等。
有些应用需要对玻璃进行特殊的后续处理,比如,某些安全玻璃元件须经温度硬化处理,以及多数带硅镀层的平板显示器元件必须经过温度退火等。
激光引致分离法也配合这些特殊的后处理,我们用激光法切割了100个4mm厚的玻璃片,在特殊热处理过程中,没有一片被破坏。
二、激光切割中的焦点位置检测方法研究激光切割加工具有切割精度高、切割速度快、热效应低、无污染、无噪音等优点,在汽车、船舶、航空航天和电子工业中都得到了广泛的应用。
而激光切割加工质量与激光焦点与工件之间的相对位置有着密切的关系,保证激光焦点和切割对象之间的合理的相对位置是保证激光切割加工质量的关键之一。
激光焦点和被加工对象之间的相对位置可以通过电感位移传感器和电容传感器来检测,在使用中各有优缺点。
电感传感器的响应频率较低,不太适用于高速加工和像!维加工这样需要非接触检测的场合;电容传感器,具有响应速度快,检测精度高等优点,但在使用过程中存在非线性和易受激光切割加工过程中产生的等离子云和喷渣的干扰的影响。
下面将系统讨论激光切割加工中激光焦点位置误差的产生途径和自动消除误差的控制系统的组成。
在此基础上分别讨论了两种传感器检测系统组成以及实际使用中存在的不足和克服的方法。
1 激光切割过程中焦点位置误差的产生在激光切割过程中,产生焦点和被加工对象表面之间相对位置发生变化的因素很多,被加工工件表面凸凹不平、工件装夹方式、机床的几何误差以及机床在负载力下的变形、工件在加工过程中的热变形等都会造成激光焦点位置和理想给定位置(编程位置)发生偏差。
有些误差(如机床的几何误差)具有规律性,可以通过定量补偿方法进行补偿,但有些误差为随机误差,只能通过在线检测和控制来消除,这些误差是:1.1 工件几何误差激光切割的对象为板材或覆盖件型零件,由于各种?因的影响,加工对象表面具有起伏不平,且在切割过程中的热效应的影响也会产生薄板零件的表面变形,对于1维激光加工,覆盖件在压制成型过程中也会产生表面的不平,所有这些,都会产生激光焦点与被加工对象表面的位置与理想位置发生随机变化。
1.2 工件装夹装置产生的误差激光切割加工的工件是放在针状工作台上,由于加工误差、长时间与工件之间的磨损和激光的烧伤,针床会出现凸凹不平,这种不平也会产生薄钢板和激光焦点之间的位置的随机误差。
1.3 编程产生的误差在1维激光切割加工过程中,复杂曲面上的加工轨迹是通过直线、圆弧等拟合的,这些拟合曲线和实际曲线存在一定误差,这些误差使得实际焦点和加工对象表面的相对位置和理想编程位置产生一定误差。
而有些示教编程系统也会引入一些偏差。
2 激光切割过程中焦点位置在线检测与控制系统的组成激光切割焦点位置在线检测与控制系统由控制器、检测系统、执行装置等部分组成。
根据焦点位置检测控制系统和系统的关系,焦点位置检测控制系统分为独立式和集成式两种。
独立式焦点位置检测与控制系统采用单独的坐标轴进行焦点位置误差的补偿控制,机械结构复杂,成本较高,但可与各种数控系统和激光切割机床配合使用。
而集成式采用激光切割机床本身的一个进给轴(对平面加工)或多个进给轴的合成(对于1维切割加工)运动来进行焦点位置误差的补偿。
这种方式具有结构简单、成本低,易于调整等优点,但要求和数控系统统一设计,对数控系统的开放性要求较高。
2.1 电容传感器检测电路电容传感器检测电路由调谐振荡器、信号放大器、晶体稳频振荡器、同步电路、混频电路、信号处理电路等将电容量信号变成对应频率的脉冲信号,通过对脉冲信号进行频率采样和处理,得到相应的电容量。
这里的电容为切割喷嘴和切割对象之间两个极板形成的电容。
显然其电容量除了与两个极板的面积有关外,还与极板之间的介质、极板之间的距离有关。
而这个距离就与激光聚焦镜和工件之间的距离有关,也就是与激光焦点与工件之间的距离有关,所以电容量近似和焦点位置与切割对象之间的距离有关。
这就是电容传感器检测焦点位置的原理。
可以看出,频率和焦点位置误差之间的关系为非线性关系,必须通过计算机进行线性化处理。
同时,由于电容量还和极板之间的介质有关,所以检测结果容易受加工过程中产生的等离子云和喷渣影响,必须加以克服。
2.2 电感传感器检测电路由于采用了最新的大规模集成电路,电感传感器的检测电路比较简单,且集成电路采用了新的调制解调方法和算法,减少了以前的检测外差式调频检测电路方法由于传感器的激励信号的相角、频率以及幅值漂移对检测结果的影响,大大提高了检测精度和稳定性。
传感器信号通过处理后得到与传感器测头位移成正比的电压信号,通过变换电路转换成相应的频率信号,通过计算机处理得到了焦点的位置误差信号。
3 切割过程中等离子云对焦点位置检测系统的影响在工件尚未被切穿的瞬间,激光和金属相互作用,在喷嘴和加工对象之间产生云雾状等离子体,改变电容极板之间的介质,从而对电容传感器产生干扰。
在正常切割过程中,辅助气体将等离子体从切缝中吹散,对电容传感器产生影响较小。
但如果加工速度太快和刚开始切割时,由于工件未被完全切穿,激光照射点附近会产生等离子体云,对电容传感器产生干扰,严重时甚至使传感器无法正常工作,严重影响加工质量。
4 传感器优化设计技术减少等离子云对检测结果的影响等离子体对电容传感器的干扰是由于等离子体改变了电容两极板之间的介质。
因此,为了消除等离子体对电容传感器的干扰,就要使电容两极板之间的介质不受等离子体的影响,可以加大圆环形极板的中心小孔和将电容传感器移至等离子云以外两种方法来实现。
(1)要消除等离子体对电容量的影响,就要将等离子体置于电容传感器的极板之外。
考虑到等离子云是沿切割点周围分布的,将圆环形极板的中心小孔直径扩大至2~3mm并嵌入绝缘的耐高温陶瓷材料,由于电容传感器极板是空心的,在不考虑边缘效应的情况下,照射点附近的等离子体云对传感器电容量和检测值不产生影响,所以采用这种办法能有效地减小等离子云的干扰影响。
(2)对于平面激光切割加工,还可以通过机械传动方法进行间接测量。
即通过一机械装置跟随被加工对象运动,将机械装置的上端和检测传感器形成极板,通过检测传感器和这个机械装置之间的距离来间接检测激光焦点和被加工对象之间的位置。