绕管换热器
螺旋缠绕管换热器的传热系数
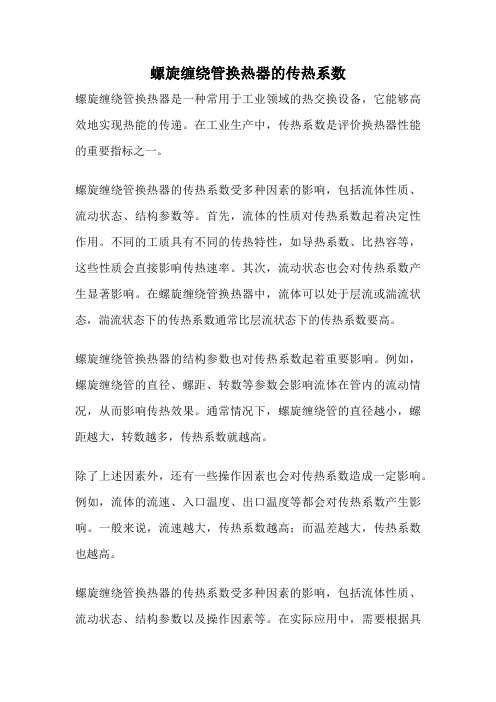
螺旋缠绕管换热器的传热系数
螺旋缠绕管换热器是一种常用于工业领域的热交换设备,它能够高效地实现热能的传递。
在工业生产中,传热系数是评价换热器性能的重要指标之一。
螺旋缠绕管换热器的传热系数受多种因素的影响,包括流体性质、流动状态、结构参数等。
首先,流体的性质对传热系数起着决定性作用。
不同的工质具有不同的传热特性,如导热系数、比热容等,这些性质会直接影响传热速率。
其次,流动状态也会对传热系数产生显著影响。
在螺旋缠绕管换热器中,流体可以处于层流或湍流状态,湍流状态下的传热系数通常比层流状态下的传热系数要高。
螺旋缠绕管换热器的结构参数也对传热系数起着重要影响。
例如,螺旋缠绕管的直径、螺距、转数等参数会影响流体在管内的流动情况,从而影响传热效果。
通常情况下,螺旋缠绕管的直径越小,螺距越大,转数越多,传热系数就越高。
除了上述因素外,还有一些操作因素也会对传热系数造成一定影响。
例如,流体的流速、入口温度、出口温度等都会对传热系数产生影响。
一般来说,流速越大,传热系数越高;而温差越大,传热系数也越高。
螺旋缠绕管换热器的传热系数受多种因素的影响,包括流体性质、流动状态、结构参数以及操作因素等。
在实际应用中,需要根据具
体情况来选择合适的结构参数和操作条件,以提高传热系数,从而提高换热器的效率。
通过合理设计和操作,螺旋缠绕管换热器能够更好地满足工业生产的需求,实现高效的热能传递。
缠绕管式换热器介绍

现场即可完成维修工作。 强
缠绕管式换热器与壳板换热器的比较
缠绕管式换热器作为一种高效换热器,除具备结构紧凑、高效节能、投资经济 性等高效换热器的一般特征外,还兼有其自身的独特优势。此类换热器的应用特 点,及其与板壳式换热器的比较优势如下:
1. 缠绕管式换热器的换热管采用层间反向螺旋缠绕的结构,极大地改变了流体流动状态,实现 强烈的湍流效果,提高了换热效率。因此,缠绕管式换热器可保证与板壳式换热器相近的换热 效率以及壳程侧更小的压降。
7. 缠绕管式换热器在停工期间对设备的检查、维修简单快捷,实施堵管方便,且完成堵管 后可靠性高。相比之下,板壳式换热器的维修就十分困难。
8. 缠绕管式换热器管、壳程均可进行单侧耐压试验,为设备现场查漏带来极大便利,最终 使得在极短时间内的现场紧急处理成为可能。而板壳式换热器几乎无现场维修的可能
缠绕管式换热器在重整芳烃装置的应用
2. 缠绕管式换热器能适应管、壳程两侧物流较大的温度差及压力差,不易泄漏,可靠性更高。
缠绕管式换热器与壳板换热器的比较
3. 缠绕管式换热器因其自身缠绕形式、柔性设置等特点,使得设备承受瞬间冲击的能力更强, 更好适应装置事故工况及非计划停车。
4. 板壳式换热器在开停工过程中有严格的升降温速度要求。而缠绕管式换热器本身对此类升降 温速度并非十分敏感,使得设备在开停工过程中的操作弹性及安全性大大增加。
缠绕管式换热器与壳板换热器的比较
板壳式换热器
缠绕管式换热器
结构型式
波纹板片叠装焊接
螺旋形换热管缠绕
承压性能
严格控制两侧压差,始终保持进料侧压力高于反应产物侧。
管、壳程允许单侧承压
泄漏 清洗 抗垢性能 温度变化适应性
存在内漏
绕管换热器

• 2.3缠绕管换热器都是竖直运行,下管板与管子间 易产生间隙腐蚀,这也是较常见的破坏形式之一.因 此,胀接要做到二点:一是要有合适的胀度,消除间 隙,防止腐蚀;二是防止过胀,导致管板塑性变形,降 低了胀接的可靠度. • 2.4九江绕管胀接的胀度在管子穿穿管前进行了试 验,选择80MPa的胀度(75-90MPa之间)
目录:
• 一、绕管换热器的基本介绍 • 二、绕管各部件加工步骤及注 意事项 • 三、操作与维护
一、绕管换热器的基本介绍:
• 1.绕管式换热器是在与管板相连的中心筒上, 以螺旋状交替缠绕数层小直径换热管形成 管束,再 将管束放入壳体内的一种换热器。 • 管束由多层螺旋缠绕的换热管组构成,每 层换热管以相反的方向缠绕,每层换热管 用垫条隔开,垫条厚度由工艺计算的流体 通道要求确定(九江项目采用2mm厚度)并 采用异型垫条控制换热管的螺旋升角。在 设计盘管时同一层使用相同长度的管子绕 制,在同一管程的流道上管子应均匀布置。
• 优点:结构紧 凑、可同时进行多种介质换热、管 内操作压力高、传 热管的热膨胀可自行补偿、换 热器易实现大型化等 特点,因此,成为大型煤化工 装置低温甲醇洗系统的首选换热设备。 • 缺点:主要为检修、清理困难,所以一般用于较清 洁的工艺介质。
• 2.绕管式换热器按其结构特点分为两类:管
程单股流流道型(称为单股流绕管式换热器),
• 1.20绕制完成以后,对绕管体外部使用厚度 为2mm的不锈钢皮进行包裹,以防伤到管 子,等待与筒体进行套装,由此夹套还起 到导流作用,夹套与设备壳体间应保持一 定距离。如下图片:(E1610为例)
2制造过程的控制
2.1盘管的控制.盘管控制的好坏直接影响到换热器 的换热效率,尤其是对结垢情况影响较大.因此,盘管 时必须使层间距适度,没有窄间隙死角,防止局部区域 布置不均匀,造成流体阻塞,降低流体的流通面积. 2.2焊接的控制.缠绕管的损坏形式最常见的是管口 泄漏,这是设备的关键部位.一般缠绕管换热器为了提 高换热效率,采用管子都比较小和薄,焊接容易产生缺 陷.因此,焊接必须严格控制线能量,焊缝要均匀和饱 满.
缠绕管式换热器介绍

降低成本
在满足性能要求的前提下,通过优化设计降 低制造成本和维护成本。
提高可靠性
通过优化设计,提高换热器的可靠性和使用 寿命。
计算流体动力学分析
流体动力学分析
利用计算流体动力学(CFD)技术,对流体的流动状态、传热过程和 流动阻力等进行模拟和分析。
缠绕管式换热器介绍
contents
目录
• 缠绕管式换热器概述 • 缠绕管式换热器的结构与材料 • 缠绕管式换热器的性能特点 • 缠绕管式换热器的设计与优化 • 缠绕管式换热器的安装与维护 • 缠绕管式换热器的发展趋势与展望
01
缠绕管式换热器概述
定义与特点
高效换热
由于管子采用螺旋缠绕方式,使 得冷热流体在管内外流动时能够 形成较大的温差,从而提高换热 效率。
优化流道设计
根据CFD分析结果,优化流道设计,改善流体流动状态,提高换热效 率。
性能预测
通过CFD分析,预测换热器的性能,为后续优化提供参考。
实验验证
将CFD分析结果与实验数据进行对比,验证模型的准确性和可靠性。
05
缠绕管式换热器的安装 与维护
安装注意事项
安装前应检查设备是 否完好无损,确保所 有部件符合要求。
定义
缠绕管式换热器是一种通过将管 子螺旋缠绕在芯棒上,再通过外 部固定圈进行固定的换热设备。
紧凑结构
由于管子紧密缠绕,使得换热器 体积较小,便于安装和维护。
耐高压
由于结构紧凑和管子较细,使得 换热器能够承受较高的压力。
适应性强
适用于各种不同的流体和温度条 件,可根据实际需求进行定制。
工作原理
01
冷热流体在管内外流动,通过 管壁进行热量交换。
缠绕管式换热器介绍

冷热流体通过 缠绕管内壁进
行热交换
热量通过管壁 和缠绕的波纹
板传递
冷热流体在管 间流动,实现
热量交换
热量通过管壁 和波纹板传递 给管外的冷却 水或加热介质
高效传热:缠绕管式换 热器采用独特的管内管 外缠绕结构,有效增加 换热面积,提高传热效 率。
耐高温高压:材料选 择优良,能够承受高 温高压的工况,保证 设备长期稳定运行。
解决方案:检查密封件和连接处,及时修复泄漏问题。
解决方案:检查换热器内部是否有堵塞或结垢,及时清理并进行调整。
汇报人:XX
核能发电:用于冷却反应堆,提高发电效率 火电发电:用于冷却锅炉,提高发电效率 风电发电:用于冷却涡轮机,提高发电效率 太阳能发电:用于冷却吸热器,提高发电效率
制药行业:用于 药品生产和加工 过程中的加热、 冷却和蒸发等工 艺流程,提高生 产效率和产品质 量。
化工行业:用于 各种化学反应过 程中的热交换, 如聚合、裂解、 蒸馏等,同时能 够承受各种腐蚀 性介质。
利用效率
海水淡化:用 于大规模海水 淡化工厂的换
热
PART FOUR
传热效率:选择传 热效率高的换热器, 以满足工艺要求。
耐腐蚀性:根据工 艺介质的腐蚀性选 择耐腐蚀的材料。
机械强度:考虑换 热器的机械强度, 以确保其稳定性和 安全性。
经济性:在满足工 艺要求的前提下, 选择价格合理的换 热器。
XX,a click to unlimited possibilities
汇报人:XX
CONTENTS
PART ONE
外部壳体:提供稳定的支撑和 保护,防止外部环境对换热器 的干扰
缠绕管:由多个薄壁金属管 绕成,用于热量交换
绕管换热器ppt课件

• 2.3缠绕管换热器都是竖直运行,下管板与管子间 易产生间隙腐蚀,这也是较常见的破坏形式之一.因 此,胀接要做到二点:一是要有合适的胀度,消除间 隙,防止腐蚀;二是防止过胀,导致管板塑性变形,降 低了胀接的可靠度.
• 2.4九江绕管胀接的胀度在管子穿穿管前进行了试 验,选择80MPa的胀度(75-90MPa之间)
11
二、绕管各部件加步骤及注意事项
• 1绕管各部件加步骤: • 1.1中心筒组对焊接 • 绕管束中心筒在制造 • 中起支承作用, • 因而要求有一定的强度和刚度, • 中心筒的外 • 径由换热管的最 • 小弯曲半径决定
12
1.2中心筒与管板焊接
13
1.3管板中心距检查≤3mm
14
1.4垫条点焊前对照图纸进行确认管板标识,检查管板介质 通道是否一致
27
1.16绕制中,使用管箍固定中,以防回 弹
28
1.17第一层绕制完,进行表面检查及100%气压试验
29
1.18气压试验压力8.5Mpa
30
1.18第二层绕制前,将垫条点焊在第一层的管箍上
31
第二层管子管箍固定,点焊时注意不要伤到管子
32
第二层的绕制方向与上一层方向相反,依次类推
33
1.19每层绕制完,需要对每一层的直径进行数据测量,对 照图纸,以防绕大。
2
目录:
• 一、绕管换热器的基本介绍 • 二、绕管各部件加工步骤及注
意事项 • 三、操作与维护
3
一、绕管换热器的基本介绍:
• 1.绕管式换热器是在与管板相连的中心筒上, 以螺旋状交替缠绕数层小直径换热管形成 管束,再 将管束放入壳体内的一种换热器。
• 管束由多层螺旋缠绕的换热管组构成,每 层换热管以相反的方向缠绕,每层换热管 用垫条隔开,垫条厚度由工艺计算的流体 通道要求确定(九江项目采用2mm厚度)并 采用异型垫条控制换热管的螺旋升角。在 设计盘管时同一层使用相同长度的管子绕 制,在同一管程的流道上管子应均匀布置。
缠绕式换热器介绍

缠绕式换热器介绍缠绕管式换热器不仅是大型化工工艺过程重要的设备,而且是一个高效节能的设备。
这些换热器结构复杂,价格昂贵,而且处于装置关键部位,因此一旦这些换热器发生泄漏,整套装置必须要停工,而且重新制造一台最快需要半年,企业的损失将非常巨大。
正常换热器的使用寿命一般在12~20年左右,企业可以根据实际使用情况和使用寿命的期限来有计划地进行更换,但是在国内也有很多企业由于对绕管换热器的全程管理不到位,使用了很短时间即发生了质量问题。
为了确保缠绕管换热器长周期运行,对缠绕管换热器使用的全过程管理十分必要。
1缠绕管式换热器简介缠绕管式换热器由绕管芯体和壳体两部分组成(图1)。
绕管芯体由中心筒、换热管、垫条及管卡等组成。
换热管紧密地绕在中心筒上(图2),用平垫条及异形垫条分隔,保证管子之间的横向和纵向间距,垫条与管子之间用管卡固定连接,换热管与管板采用强度焊加贴胀的连接结构,中心筒在制造中起支承作用,因而要求有一定的强度和刚度。
壳体由筒体和封头等组成。
它应用于工程的主要优点有[1]:a.结构紧凑,单位容积具有较大的传热面积。
对管径8~12mm的传热管,每立方米容积的传热面积可达100~170m2;b.可同时进行多种介质的传热;c.管内的操作压力高,目前国外最高操作压力可达21 56MPa;d.传热管的热膨胀可自行补偿;e.换热器容易实现大型化。
2缠绕管式换热器的工业应用情况在国外,缠绕管式换热器广泛应用于大型空气分离装置的过冷器及液化器(液体氧、液体氨装置),林德公司在合成氨甲醇洗系统中推出的缠绕管换热器系列正是充分发挥了该种换热器的作用。
缠绕管式换热器在我国目前主要应用于大化肥合成氨装置(美国德士古工艺)中甲醇洗工段[2],在全国共有近20套此类装置,每套装置中有6台缠绕管式换热器,这些换热器的具体情况见表1。
在我国最早十多套装置中的缠绕管换热器大都已更换,其中大都是已到使用寿命限期,但也有不少为管理不善而造成的损坏。
绕管换热器PPT课件
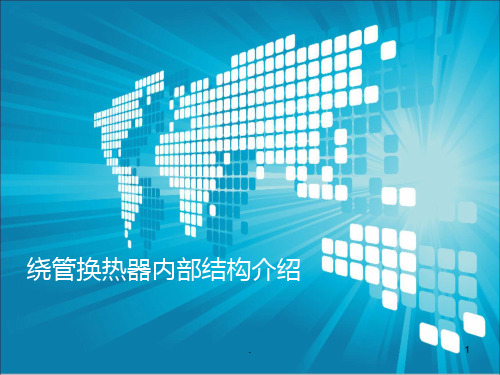
.
27
1.16绕制中,使用管箍固定中,以防回 弹
.
28
1.17第一层绕制完,进行表面检查及100%气压试验
.
29
1.18气压试验压力8.5Mpa
.
30
1.18第二层绕制前,将垫条点焊在第一层的管箍上
.
31
第二层管子管箍固定,点焊时注意不要伤到管子
.
32
第二层的绕制方向与上一层方向相反,依次类推
.
22
1.12管子绕制好一根,管箍进行固定,以防止管子回弹
.
23
1.13管箍固定管子,此处点焊时注意检查是否伤到 管子
.
24
1.14绕制时敲击使用皮锤进行敲击,以防伤到管子
.
25
1.15绕制中
.
26
• 其中,换热管的盘绕角一般为5~20度,例如 E1607盘绕角14-15度。绕管式换热器的特点是结 构紧凑,单位换热面积大,热损小,承压能力高。 一般高压流体在管内流动。换热管大部分呈盘绕 状,盘绕角较小,故管内、管外的清扫很困难, 所以管内、管外不适于走不洁的流体。
绕管换热器内部结构介绍
.
1
绕管换热器的发展史
• 我国20世纪70年代末引进的大化肥装置中采用德 国林德公司低温甲醇洗工艺单元中各有6台绕管换 热器;90年代初引进的德国鲁奇公司低温甲醇洗 工艺单元中各有2台绕管换热器;由于我国尚未掌 握绕管换热器的设计和制造技术,这些引进的装 置中绕管换热器完全依赖国外进口,设备的费用 昂贵。并且随着我国合成氨工业的发展,对低温 甲醇洗装置的需求量增加,对现有装置进行技术 改造实现增产的要求也与日剧增,在此形势下通 过国内科研、设计和制造单位的努力,该类设备 已实现国产化。
- 1、下载文档前请自行甄别文档内容的完整性,平台不提供额外的编辑、内容补充、找答案等附加服务。
- 2、"仅部分预览"的文档,不可在线预览部分如存在完整性等问题,可反馈申请退款(可完整预览的文档不适用该条件!)。
- 3、如文档侵犯您的权益,请联系客服反馈,我们会尽快为您处理(人工客服工作时间:9:00-18:30)。
a
27
1.16绕制中,使用管箍固定中,以防回 弹
a
28
1.17第一层绕制完,进行表面检查及100%气压试验
a
29
1.18气压试验压力8.5Mpa
a
30
1.18第二层绕制前,将垫条点焊在第一层的管箍上
a
31
第二层管子管箍固定,点焊时注意不要伤到管子
a
32
第二层的绕制方向与上一层方向相反,依次类推
a
11
二、绕管各部件加步骤及注意事项
• 1绕管各部件加步骤: • 1.1中心筒组对焊接 • 绕管束中心筒在制造 • 中起支承作用, • 因而要求有一定的强度和刚度, • 中心筒的外 • 径由换热管的最 • 小弯曲半径决定
a
12
1.2中心筒与管板焊接
a
13
1.3管板中心距检查≤3mm
a
14
1.4垫条点焊前对照图纸进行确认管板标识,检查管板介质 通道是否一致
36
a
37
a
38
2制造过程的控制
2.1盘管的控制.盘管控制的好坏直接影响到换热器 的换热效率,尤其是对结垢情况影响较大.因此,盘管 时必须使层间距适度,没有窄间隙死角,防止局部区域 布置不均匀,造成流体阻塞,降低流体的流通面积. 2.2焊接的控制.缠绕管的损坏形式最常见的是管口 泄漏,这是设备的关键部位.一般缠绕管换热器为了提 高换热效率,采用管子都比较小和薄,焊接容易产生缺 陷.因此,焊接必须严格控制线能量,焊缝要均匀和饱 满.
a
7
(图2-1)单股流绕管式换热器
序号 名称
序号 名称
1
下管箱
5
壳体
2下Leabharlann 板6外套筒3
中心筒
7
上管板
4
管束
8
上管箱
a
8
单股流绕管换热器实物图(E1610热再生塔进料加热器)
a
9
(图2-2)多股流绕管式换热器
序号 名称
序号 名称
1
下管箱
5
壳体
2
下管板
6
外套筒
3
中心筒
7
上管板
4
管束
8
上管箱
a
10
多股流绕管式换热器实物图(E1606洗涤塔段间冷 却器)
a
33
1.19每层绕制完,需要对每一层的直径进行数据测量,对 照图纸,以防绕大。
a
34
• 1.20绕制完成以后,对绕管体外部使用厚度 为2mm的不锈钢皮进行包裹,以防伤到管 子,等待与筒体进行套装,由此夹套还起 到导流作用,夹套与设备壳体间应保持一 定距离。如下图片:(E1610为例)
a
35
a
a
2
目录:
• 一、绕管换热器的基本介绍 • 二、绕管各部件加工步骤及注
意事项 • 三、操作与维护
a
3
一、绕管换热器的基本介绍:
• 1.绕管式换热器是在与管板相连的中心筒上, 以螺旋状交替缠绕数层小直径换热管形成 管束,再 将管束放入壳体内的一种换热器。
• 管束由多层螺旋缠绕的换热管组构成,每 层换热管以相反的方向缠绕,每层换热管 用垫条隔开,垫条厚度由工艺计算的流体 通道要求确定(九江项目采用2mm厚度)并 采用异型垫条控制换热管的螺旋升角。在 设计盘管时同一层使用相同长度的管子绕 制,在同一管程的流道上管子应均匀布置。
a
40
胀接试验胀度80MPa
a
41
胀接后PT检查
•
a
42
• 2.5换热管做水下气密性试验, • 注意试验用水,水中氯离子含量≤25mg/L
a
43
换热管做水下气密性试验,保压10分钟,无泄漏无变形,才 能进行绕制
a
44
三、操作与维护
• 缠绕管由于原料杂质问题引起质量问题的也不少, 按照设计要求,缠绕管式换热器用于介质杂质少.容 易清洗的场合,因为缠绕管换热器为了追求其紧凑 性,管间距与层间距的间距比较小,所以对原料的要 求也较高.一旦装置波动等就可能引发原料杂质多 而容易造成堵塞.因此,要有效地在操作上做好以下 几方面:
a
22
1.12管子绕制好一根,管箍进行固定,以防止管子回弹
a
23
1.13管箍固定管子,此处点焊时注意检查是否伤到 管子
a
24
1.14绕制时敲击使用皮锤进行敲击,以防伤到管子
a
25
1.15绕制中
a
26
• 其中,换热管的盘绕角一般为5~20度,例如 E1607盘绕角14-15度。绕管式换热器的特点是结 构紧凑,单位换热面积大,热损小,承压能力高。 一般高压流体在管内流动。换热管大部分呈盘绕 状,盘绕角较小,故管内、管外的清扫很困难, 所以管内、管外不适于走不洁的流体。
a
15
1.5介质通道进行标识,检查是否正确以防穿错管
a
16
1.6异型垫条用来确定管子的导程
a
17
1.7平垫条在中心筒上点焊
a
18
1.8中心筒上点焊异形垫条
a
19
1.9垫条点焊
a
20
1.10异形垫条用来固定管子在绕制过程中的导程, 犹如管子绕制过程的行驶轨道
a
21
1.11管箍,用来固定管子
a
39
• 2.3缠绕管换热器都是竖直运行,下管板与管子间 易产生间隙腐蚀,这也是较常见的破坏形式之一.因 此,胀接要做到二点:一是要有合适的胀度,消除间 隙,防止腐蚀;二是防止过胀,导致管板塑性变形,降 低了胀接的可靠度.
• 2.4九江绕管胀接的胀度在管子穿穿管前进行了试 验,选择80MPa的胀度(75-90MPa之间)
a
4
• 缠绕管式换热器由绕管芯体和壳体两部分组成。 绕管芯体由中心筒.换热管.垫条及管卡等组成.换 热管紧密地绕在中心筒上,用平垫条及异形垫条 分隔,保证管子之间的横向和纵向间距,垫条与管子 之间用管卡固定连接,换热管与管板采用强度焊加 贴胀的连接结构,中心筒在制造中起支承作用,因而 要求有一定的强度和刚度.壳体由筒体和封头等组 成。
绕管换热器内部结构介绍
a
1
绕管换热器的发展史
• 我国20世纪70年代末引进的大化肥装置中采用德 国林德公司低温甲醇洗工艺单元中各有6台绕管换 热器;90年代初引进的德国鲁奇公司低温甲醇洗 工艺单元中各有2台绕管换热器;由于我国尚未掌 握绕管换热器的设计和制造技术,这些引进的装 置中绕管换热器完全依赖国外进口,设备的费用 昂贵。并且随着我国合成氨工业的发展,对低温 甲醇洗装置的需求量增加,对现有装置进行技术 改造实现增产的要求也与日剧增,在此形势下通 过国内科研、设计和制造单位的努力,该类设备 已实现国产化。
a
5
• 优点:结构紧 凑、可同时进行多种介质换热、管 内操作压力高、传 热管的热膨胀可自行补偿、换 热器易实现大型化等 特点,因此,成为大型煤化工 装置低温甲醇洗系统的首选换热设备。
• 缺点:主要为检修、清理困难,所以一般用于较清 洁的工艺介质。
a
6
• 2.绕管式换热器按其结构特点分为两类:管 程单股流流道型(称为单股流绕管式换热器), 管程多股流流道型(称为多股流绕管式换热 器)。(如图2-1、2-2)