基于Workbench仿真的内燃机曲柄连杆机构动力学分析
发动机曲柄连杆机构动力学仿真分析平台研究
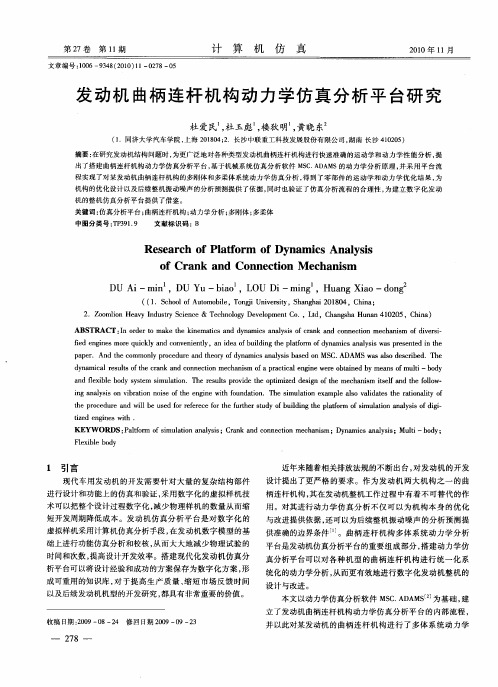
i n ls nv r i o eo ee gn i u d t n h es ua o x m l as v l a s ert n lyo n a a i o i a o n i f h n ew t f n a o .T i lt n e a pel o a d t i a t f g ys b tn s t i ho i m i i e t ao i h
( .同济大学汽车学院, 1 上海 2 10 2 0 84;.长沙中联重工科技发展股份有 限公司 , 湖南 长沙 4 0 0 ) 12 5
摘 要 : 研 究发 动 机 结 构 问题 时 , 更 广 泛 地 对各 种 类 型 发 动机 曲柄 连 杆 机 构进 行 快 速 准 确 的运 动 学 和 动 力 学 性 能 分 析 , 在 为 提
第2 卷 第1期 7 1
文 章 编 号 :0 6— 3 8 2 1 ) 1— 2 8—0 10 94 ( 00 l 0 7 5
计
算
机
仿
真
20 1 0 年1月 1
发 动 机 曲柄 连 杆 机 构 动 力 学 仿 真 分 析 平 台研 究
杜 爱民 杜 玉彪 楼狄 明 , 晓 东 , , 黄
o a k a d Co ne to e h n s f Cr n n n c i n M c a im
基于ANSYS Workbench发动机连杆有限元分析
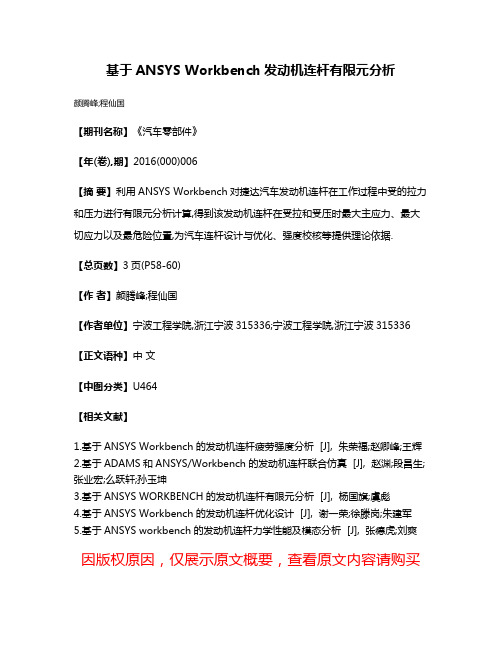
基于ANSYS Workbench发动机连杆有限元分析
颜腾峰;程仙国
【期刊名称】《汽车零部件》
【年(卷),期】2016(000)006
【摘要】利用ANSYS Workbench对捷达汽车发动机连杆在工作过程中受的拉力和压力进行有限元分析计算,得到该发动机连杆在受拉和受压时最大主应力、最大切应力以及最危险位置,为汽车连杆设计与优化、强度校核等提供理论依据.
【总页数】3页(P58-60)
【作者】颜腾峰;程仙国
【作者单位】宁波工程学院,浙江宁波315336;宁波工程学院,浙江宁波315336【正文语种】中文
【中图分类】U464
【相关文献】
1.基于ANSYS Workbench的发动机连杆疲劳强度分析 [J], 朱荣福;赵卿峰;王辉
2.基于ADAMS和ANSYS/Workbench的发动机连杆联合仿真 [J], 赵渊;段昌生;张业宏;么跃轩;孙玉坤
3.基于ANSYS WORKBENCH的发动机连杆有限元分析 [J], 杨国旗;虞彪
4.基于ANSYS Workbench的发动机连杆优化设计 [J], 谢一荣;徐滕岗;朱建军
5.基于ANSYS workbench的发动机连杆力学性能及模态分析 [J], 张德虎;刘爽因版权原因,仅展示原文概要,查看原文内容请购买。
基于ADAMS的单缸内燃机曲柄连杆机构动力分析 - 副本

293. [5] 闵剑青,徐梓斌,舒建武.铰链六杆机构的动力学分
析系统[J].机械传动,2005,20(2):31-33.
The Dynamic Analysis on the Crank-connecting Rod of Single-cylinder Internal Combustion Engine Base on ADAMS
ADAMS(Automatic Dynamic Analysis of Mechanical System)为 平 台 ,对 单 缸 内 燃 机 的 曲 柄 连 杆 机 构 进 行 了动力学分析的计算机模拟研究,以便提高工作效 率,更好地研究机构在工作过程中的运动规律、机 构运动过程中的惯性力对机体产生的干扰力以及惯 性力的平衡问题。
通过仿真发现:
1) 倾覆力矩 M 最大峰值的绝对值不随曲轴质
心位置和质量变化而变化,无法在内燃机内部获得
平衡,一般仅依靠足够大的安装基础来克服其引起
的振动。
2) 横 向 、 纵 向 干 扰 力 的 峰 值 Fx′max 和 Fy max 随 曲
轴质心位置和质量变化均呈 V 形折线,但对曲轴质
心位置变化更加敏感。
线方向,其值对曲柄连杆机构惯性力没有影响;由
于曲柄臂及平衡块结构的对称性, X 坐标一般近似
为 0,在模拟过程中不予考虑;而 Y 坐标值表述了
曲轴质心偏离曲轴旋转中心线的程度,故在模拟过
程中只考虑 Y 值的变化,令其在-25~10mm 之间变
化 。干 扰 力 FY 和 FX′ 最 大 峰 值 的 绝 对 值 随 曲 轴 质 心 位 置的变化规律如图 3 所示。
基于ANSYS_Workbench的曲柄摇杆机构刚柔耦合研究

基于ANSYS/Workbench的曲柄摇杆机构刚柔耦合研究发布时间:2022-08-08T08:14:01.550Z 来源:《科技新时代》2022年8期作者:谢兵飞[导读] 在现代化、机械化社会的发展背景下,机械设备正朝着轻质化、精密化的方向发展,现阶段,为了保证曲柄摇杆机构的质量能够满足机械设备的应用要求,应用ANSYS/Workbench有限元分析软件,对曲柄摇杆机构的刚柔耦合特性进行分析,明确其工作机理与优化方式,可以令曲柄摇杆机构更好地满足现代化机械设备的发展需要。
广东唯仁医疗科技有限公司 528051摘要:在对曲柄摇杆机构刚柔耦合性进行分析的过程中,本文先应用SolidWorks这一三维建模软件对曲柄摇杆机构进行了三维建模,然后将模型导入ANSYS/Workbench这一有限元分析软件中,对这一机构在实际工作过程中的变化情况进行了分析,然后建立了相应的有限元分析模型,从而得到了曲柄摇杆机构在某一时刻的变形与应力分布情况,以期能够给曲柄摇杆机构的后续优化带来启发。
关键词:ANSYS/Workbench;曲柄摇杆机构;刚柔耦合引言:在现代化、机械化社会的发展背景下,机械设备正朝着轻质化、精密化的方向发展,现阶段,为了保证曲柄摇杆机构的质量能够满足机械设备的应用要求,应用ANSYS/Workbench有限元分析软件,对曲柄摇杆机构的刚柔耦合特性进行分析,明确其工作机理与优化方式,可以令曲柄摇杆机构更好地满足现代化机械设备的发展需要。
一、基于ANSYS/Workbench的曲柄摇杆机构刚柔耦合研究意义曲柄摇杆机构作为用途极为广泛的一种平面连杆机构,主要由曲柄、摇杆相互铰链形成,在实际应用过程中能够实现连续回转与往复摆动两种动作间的相互转化,其中,曲柄为主动件,可以等速转动,摇杆为动作件,可以进行变速往返摆动,被广泛应用到了雷达天线俯仰机构、颚式破碎机构、牛头刨床进给机构等设备当中,并发挥了极为重要的作用,由于曲柄摇杆机构的运动精度会对机械设备性能产生直接影响,现阶段,为了保证曲柄摇杆机构的工作质量能够切实满足机械设备的实际需要,避免曲柄摇杆的刚柔耦合性质存在一定的问题,以ANSYS/Workbench为基础,对曲柄摇杆机构的刚柔耦合性质进行研究,并采用合适的方式,对其进行优化,已经成为切实提升曲柄摇杆机构质量,提升机械设备的运动精度降低,避免机械设备在使用过程中发生剧烈震动,影响设备工作质量,降低机械设备的使用寿命等问题,推动当前机械设备高质量发展的重要举措[1]。
曲柄连杆机构动力学分析与计算

第一章绪论1.1内燃机概述汽车自19世纪诞生至今,已经有100多年的历史了。
汽车工业从无到有,以惊人的速度在发展着,汽车工业给人类的近代文明带来翻天覆地的变化,在人类的文明进程中写下了宏伟的篇章。
汽车工业是衡量一个国家是否强大的重要标准之一,而内燃机在汽车工业中始终占据核心的地位。
内燃机是将燃料中的化学能转变为机械能的一种机器。
由于内燃机的热效率高(是当今热效率最高的热力发动机)、功率范围广、适应性好、结构简单、移动方便、比质量(单位输出功率质量)轻、可以满足不同要求等特点,已经广泛的应用于工程机械、农业机械、交通运输(陆地、内河、海上和航空)和国防建设事业当中。
因此,内燃机工业的发展对整个国民经济和国防建设都有着十分重要的作用。
1.1.1世界内燃机简史内燃机的出现和发明可以追溯到1860年,来诺伊尔(J.J.E.Lenoir1822~1900年)首先发明了一种叫做大气压力式的内燃机,这种内燃机的大致工作过程是:空气和煤气在活塞的上半个行程被吸入气缸内,然后混合气体被火花点燃;后半个行程是膨胀行程,燃烧的煤气推动着活塞下行,然后膨胀做功;活塞上行时开始排气。
这种内燃机和现代主流的四冲程内燃机相比,在燃烧前没有压缩行程,但基本思想已经有了雏形。
这种内燃机的热效率低于5%,最大功率只有4.5KW,1860~1865年间,共生产了约5000台。
1867年奥拓(Nicola u s A.Otto,1832~1891 年)和浪琴(EugenLangen,1833~1895年)发明了一种更为成功的大气压力式内燃机。
这种内燃机是利用燃烧所产生的缸内压力,随着缸内压力的升高,在膨胀行程时加速一个自由活塞和齿条机构,他们的动量将使得缸内产生真空,然后大气压力推动活塞内行。
基于Ansys Workbench柔体曲柄机构的动力学仿真研究
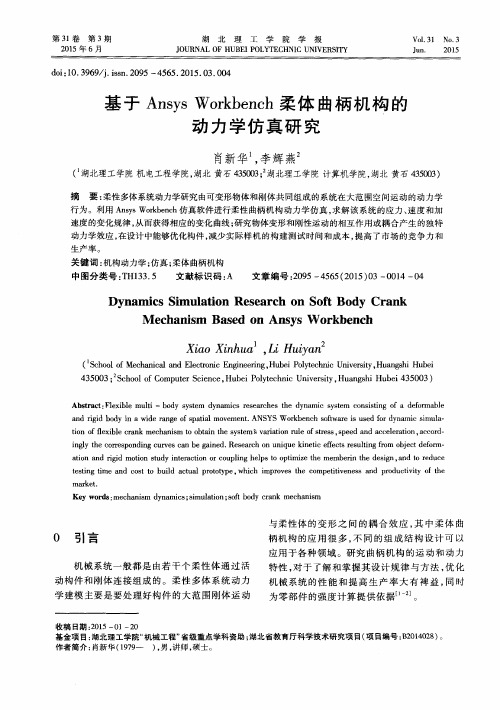
基于 A n s y s Wo r k b e n c h柔 体 曲柄 机 构 的 动 力 学 仿 真 研 究
肖新华 , 李辉燕
( 湖北理工学院 机电工程学院, 湖北 黄石4 3 5 0 0 3 ; 湖北理工学院 计算机学院, 湖北 黄石 4 3 5 0 0 3 )
摘 要 : 柔性多体系统动力学研究 由可变形物体和刚体共同组 成的系统在大范围空间运动 的动力学
Me c ha n i s m Ba s e d o n An s y s Wo r k b e n c h Xi a o Xi n h u a , L i Hu i y a n 2
( S c h o o l o f M e c h a n i c a l a n d E l e c t r o n i c E n g i n e e r i n g , H u b e i P o l y t e c h n i c U n i v e r s i t y , H u a n g s h i H u b e i
第3 1 卷 第 3期 2 0 1 5年 6月
湖
北
理
工
学
院
学
报
Vo 1 . 31 No . Fra bibliotek J OUR NAL OF HUB EI P O L YT E CHNI C UNI VE Rs 1 TY
J u n .
2 0 1 5
d o i : 1 0 . 3 9 6 9 / j . i s s n . 2 0 9 5— 4 5 6 5 . 2 0 1 5 . 0 3 . 0 0 4
i n g l y t h e c o r r e s p o n d i n g c u r v e s c a n b e g a i n e d . R e s e a r c h o n u n i q u e k i n e t i c e f f e c t s r e s u l t i n g f r o m o b j e c t d e f o m— r
基于ANSYS软件的内燃机连杆的有限元分析翻译

基于ANSYS软件的内燃机连杆的有限元分析R A Savanoor1, Abhishek Patil2*, RakeshPatil3 and Amit Rodagi2*Corresponding Author: Abhishek Patil,pabhishek170@连杆是连接活塞和曲轴的中间的连接部分的结构。
连杆的作用主要是负责传递推动和拉动的活塞销和曲柄销运动,从而将活塞的往复运动转化为曲轴的旋转运动。
一般连杆生产中使用的材料常见的是碳钢和铝合金连杆。
在本论文中我们在比较两种不同类型的碳钢和铝合金连杆的冯•米塞斯应力和总变形。
老驴三个材料参数进行有限元分析。
如,Von米塞斯应力和位移都从ANSYS软件中获得。
然后比较了铝合金和锻钢这两种不同的材料。
然后发现Al5083合金重量比较轻。
这导致连杆的重量减少63.19%。
关键词:连杆,活塞的往复运动,V on米塞斯应力,ANSYS简介连杆连接活塞与曲轴,它们形成了一个简单的机构,将直线运动转化为旋转运动。
由于活塞的推力,最大的应力出现在连杆的活塞端附近。
除承受燃烧室燃气产生的压力外,还承受纵向和横向的惯性力。
因此,连杆在一个很复杂的盈利状态下工作。
它即受交变的拉力、压应力又受弯曲应力。
连杆的主要损坏形势是疲劳断裂和过量变形。
连杆的工作条件要求连杆具有较高的强度和抗疲劳性能,又要求具有足够的刚性和韧性。
所以,在连杆外形、过度圆角等方面需严格要求,还应注意表面加工质量以提高疲劳强度。
拉伸应力和压缩应力是由于气体压力和弯曲应力的产生的,是由于离心力的作用,产生的偏心力。
因此,连杆的设计一般I-section提供的最大的刚度,能够在活塞端部获得最大应力并且增大刚度可以减少活塞端部的材料收到的应力,而且可以减轻连杆的重量。
曲轴连杆机构运动件的重量优化设计,不仅是节省材料及发动机重量降低,运动件质量对改善发动机整体的工作状况特别有效,ANSYS 形状优化的功能可以对活塞内腔、活塞销孔、连杆形状、曲轴圆角和曲柄臂尺寸进行优化设计。
第二章曲柄连杆机构动力学分析
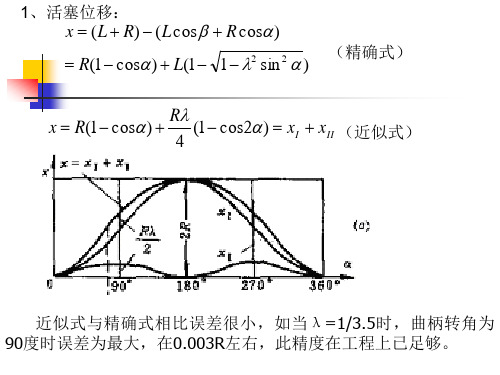
x (L R) (L cos R cos)
R(1 cos) L(1 1 2 sin 2 )
(精确式)
x
R(1 cos)
R
4
(1
c os2 )
xI
xII
(近似式)
近似式与精确式相比误差很小,如当λ=1/3.5时,曲柄转角为 90度时误差为最大,在0.003R左右,此精度在工程上已足够。
mCA
mC
L lA L
mCB
mC
L lB L
mC
lA L
对于有的高速发动机还须满足一个条件:
③ 两个换算质量对连杆质心的转动惯量之和等于原来连杆的转动惯
量,即
mCA
l
2 A
mCB
l
2 B
IC
式中IC为原连杆的转动惯量。但采用二质量替代系统时,在连杆 摆动角加速度下的惯性力矩要偏大 ΔMC=[(mCAlA2+mCBlB2)-IC]ε 为此,可用三质量替代系统:
a
R
2
cos
cos
c os2 c os3
R 2 cos cos2 sin
连杆摆角: arcsinsin
连杆摆动角速度:L
cos
1 2 sin 2
1/ 2
连杆摆动角加速度: L
2
(1 2
2 2 ) sin
1 2 sin
2 (1 sin 2 )
2 3/ 2
单缸切力曲线及六缸合成图 各轴颈输出扭矩
各轴颈输出扭矩如图
M TII M T (1) M TIII M TII M T (2)
M TIV M TIII M T (3) M TV M TIV M T (4)
- 1、下载文档前请自行甄别文档内容的完整性,平台不提供额外的编辑、内容补充、找答案等附加服务。
- 2、"仅部分预览"的文档,不可在线预览部分如存在完整性等问题,可反馈申请退款(可完整预览的文档不适用该条件!)。
- 3、如文档侵犯您的权益,请联系客服反馈,我们会尽快为您处理(人工客服工作时间:9:00-18:30)。
基于Workbench的仿真内燃机曲柄连杆机构动力学分析(机械与动力工程学院南京 211816)摘要:本文以S195 内燃机为例,对单缸内燃机的曲柄连杆机构简化模型进行了有限元分析。
根据力学分析结果和强度要求设计内燃机曲柄连杆机构结构,并应用UG软件建立该机构三维数字化虚拟装配模型,结合有限元理论及其分析软件ANSYS Workbench,模拟分析了曲柄连杆机构装配体动力学分析,结果表明,数字化模型结合装配体有限元分析,可解决曲柄连杆机构结构强度评价问题,有助于缩短汽油机开发周期和减少成本。
关键词:曲柄连杆,有限元分析,Workbench,动力学仿真。
Dynamic analysis of the crank connecting rod mechanismbased on Workbench simulation(Nanjing Technology of University, mechanical and power engineering,Yin Zhenhua, Nanjing, 211816)AbstractBased on the S195 diesel engine as an example, the crank connecting rod mechanism of single cylinder diesel engine was analyzed in finite element analysis. According to the mechanical analysis results and strength requirements, the structure of the engine crank connecting rod mechanism is designed, and the 3D digital virtual assembly model of the mechanism is established. Combined with the finite element theory and the analysis software ANSYS Workbench. The results show that the numerical model combined with the finite element analysis can solve the problem of structural strength evaluation of the crank link mechanism, which helps to shorten the development cycle and reduce the cost.Key words: crank connecting rod, finite element analysis, Workbench, dynamic simulation.0.引言随着发动机强化指标的不断提高,曲柄连杆机构的工作条件更加复杂[1-2]。
在多种周期性变化载荷的作用下,如何在设计过程中保证曲柄连杆机构中的主要部件曲轴具有足够的疲劳强度和刚度及良好的动静态力学特性成为机构设计中的关键性问题[3]。
由于在实际工况中曲轴承受活塞、连杆传递的爆发压力的交变载荷作用,受力情况极其复杂。
采用传统的单纯有限元分析方法,很难完成对曲轴运行过程中动态变化边界条件的描述[4-5]。
为了真实全面地了解曲轴在实际运行工况下的力学特性,本课题通过运用UG软件建立曲柄连杆机构各组成零件的几何模型,确定机构的质量特性参数,通过有限元分析软件Workbench仿真,分析曲轴和连杆在爆发压力和惯性力作用下的疲劳应力,由此可以清楚地了解曲轴和连杆在工作过程中各部分的应力,应变,迅速找到危险部位,为机构的优化设计奠定基础。
ANSYS Workbench 作为一款大型有限元分析软件不仅可以实现产品性能的快速优化, 并且可以得到输入变量和输出变量之间的关系曲线以及图像,同时也为结构的进一步优化提供了有价值的参考。
1.曲柄连杆机构的运动与受力1.1曲柄连杆机构的运动将曲柄连杆机构的曲轴中心设为原点,曲柄半径设为R ,连杆长度设为L ,α为曲轴转角,ω为曲轴转速。
根据力学推导,活塞的位移x ,速度v ,加速度a 的推导公式[6-7]如下:其中λ为连杆比, λ=R/L因此,根据活塞位移,速度,加速度的变化曲线可以得出曲柄连杆机构的运动特点如下:(1)即使曲轴做匀速运动,而活塞的速度却是不均匀的,在上、下止点处的速度为0,在α=90°稍前和270°稍后的位置达到速度最大值。
(2)由于活塞速度的变化,导致加速度的变化,在速度为零处的加速度最大,而速度最大处的加速度为0。
2 曲柄连杆机构装配体的受力曲柄连杆机构载荷主要是气缸内燃烧过程中产生的气体作用在活塞上表面的高温和高压,燃烧过程中活塞上表面的平均温度Tm 和平均放热系数a m 分别为:T m =∫T g a g d a 7200/∫a g d a 7200 a m =720−1�a g d a 7200 其中: g a 为瞬时放热系数,可由 Eichelberg 经验公式[8]:a g =1.166�p 2T g 3(1+0.85C m )计算得到;Tg 为燃烧的瞬时温度(℃),且有g T = PV (mR);P 为燃烧的瞬时压强(MPa);V 为气体容积(m 3);R 为常数;m 为气体质量(kg);Cm 为活塞平均速度(m/s). 燃烧过程中作用在活塞上表面的压力为:F n =πD 2P/4 其中Fn 为活塞顶的气体作用力,D 为活塞直径。
2. 建立曲柄连杆机构的三维实体模型研究选用应用比较广泛、功能强大的三维CAD 软件建立曲柄连杆机构的几何模型。
S195 内燃机曲柄连杆机构由活塞组、连杆组和曲轴组等三大部件组成。
内燃机曲柄连杆机构包括活塞组,连杆组和曲轴飞轮组三大部分[9]。
进行内燃机曲柄连杆机构多体系统仿真分析,首先需要利用UG工具软件建立各构件的三维实体模型,然后根据各构件之间的相互关系进行装配,从而得到整个机构的实体模型。
然后另存存为ANSYS通用的.IGS格式,导入到ANSYS Workbench 中,进行有限元模型的建立。
此时所建立的各构件均为刚体模型,利用这些模型可计算得到建立曲柄连杆机构运动学所需要的零件质量,质心位置及转动惯量等参数。
图1 曲柄连杆机构三维实体模型3. 多体系统动力学模型的建立将上述所建立多体系统模型导入机械系统仿真软件Workbench中,得到曲柄连杆机构动力学仿真分析模型。
此时的多体系统动力学分析模型中的全部构件均为刚体,所以,得到的是一个多刚体系统模型。
3.1 关键零部件柔性化处理由于实际的金属结构件都是弹性体,为了计算关键零部件的弹性特性对内燃机内部的激励载荷的影响,需要对曲轴,飞轮等主要零件进行柔性化处理。
经柔性化处理后,构件各部分之间用相对描述法来表示的,其变形运动可近似的通过离散的有限个自由度位移来表示,并且在弹性变形小的范围内,该位移可用模态向量及模态坐标的线性组合来描述[10],因此可以采用有限元法对零件进行离散化并进行模态综合分析,将其结果用于柔性体建模。
在有限元软件中,对所建立的柔性体模型进行模态综合分析,得到一个包含零件材料,节点,单元和模态信息的文件。
将通过有限元软件柔性化处理并替代原刚体模型中的对应刚体模型,则得到包含柔体的多体系统动力学仿真分析模型。
3.2 边界条件处理曲柄连杆机构多体系统仿真模型中,包含两类边界条件:一类是限制构件间相对运动关系的运动约束边界条件,另一类是内燃机工况边界条件。
3.2.1 运动约束边界条件运动约束边界条件是指对各构件的运动自由度进行限制,使之实现与真实机构完全相同的运动规律而施加的一类约束。
主要包括限制活塞只可以沿着缸筒直线运动的圆柱副,限制曲轴只可以发生绕其轴线转动的转动副,连杆大头只可以发生绕曲轴销转动的转动副等。
其中需要注意的是,事先要按照图纸的装配要求和制动器工作时各部件之间的接触情况定义接触关系。
定义的接触关系包括:1)曲柄和连杆、连杆和活塞的连接约束;2)各部件之间的运动约束,其中曲柄转速设置为2.09 rad/s(如图2),活塞沿着轴向做直线往复运动。
图2 运动约束示意图3.2.2 网格划分将简化后的曲柄连杆CAD 三维模型导入Workbench平台建立Static Structural静力学分析模的前处理模块中进行网格化,采用自动划分自由网格,单位选择为(mm,t,N,s,mv,mA),共划分了21953个节点,10856个单元。
如图3。
图3 网格划分情况示意图3.2.3工况载荷边界条件工程数据Engineering Date里材料属性设置为结构钢,弹性模量为2.1E11,泊松比为0.3,密度为7850kg/m3。
根据曲柄连杆工作情况,综合第一类自由约束和第三类表面载荷对有限元模型进行载荷定义。
载荷施加具体如图4,大小为0.3MPa。
图4 载荷示意图3.2.4 内燃机工况边界条件内燃机工况边界条件是指模拟内燃机实际工作状况的气体压力载荷和曲轴运动转速两种边界条件。
在具体施加缸内气体压力边界条件时,应根据多缸内燃机的发火顺序调整各活塞表面的气体压力相位。
惯性力载荷(包括往复运动惯性力和旋转运动惯性力两类)边界条件无需专门施加,它们将由所施加的曲轴转动角速度,以及ANSYS软件计算得到的各构件质量分布情况,以体积力的形式自动施加给相应构件。
4.仿真分析结果在机械系统仿真软件Workbench中,通过运动和气体压力驱动,完成曲柄连杆机构动力学仿真分析4.1 运动学仿真结果前述柴油机在标定工况下,内燃机的主轴承,承受来自曲柄连杆机构传递来的气压力和往复运动惯性力载荷,以及曲柄不平衡运转惯性力载荷,并传递给相应轴承座,沿此路线所传递的载荷是激发内燃机结构振动的最主要激励力之一,但是传统的轴承载荷分析方法无法计算曲轴等零部件弹性特性的影响,其分析结果误差较大。
对一台内燃机而言,在所有主轴承中,前后端头的两个轴承由于主要承受一个气缸的冲击激励,载荷幅值相对较小。
在本次分析中共分析了四个模:1)总变形;2)等效应力;3)总速度;4)总加速度。
根据分析报告,如表1所示,总变形的最大值为1.9232mm,如图5(a)在整个运动过程中其分布呈抛物线状,根据总变形云图,图6(a)知,变形最大且对结构有危险的是曲柄与连杆、连杆与活塞杆连接处。
这也是需要校核和加强的地方。
表1 分析结果DefinitionTypeTotalDeformationEquivalent (von-Mises)StressTotal VelocityTotalAccelerationBy TimeDisplay Time Last 2.1 s LastResultsMinimum 2.7666e-003 mm 4.4541e-003 MPa 0.43155 mm/s 0.91681 mm/s² Maximum 1.9232 mm 65.418 MPa 297.75 mm/s 632.27 mm/s²InformationTime 3. s 2.1 s 3. s Load Step 1Substep 30 21 30IterationNumber190 136 190根据分析报告,等效应力最大值为65.418MPa,且等效应力在整个运动行程中呈周期性变化,如图5(b)。