电火花成形加工实训
电火花成形加工实训

电火花成形加工实训实训二电火花冲孔落料模工具电极设计1、实训目的掌握电火花冲孔落料模的电极设计方法。
2、实训项目①、工具电极高度尺寸设计;②、工具电极水平尺寸设计。
3、实训器材计算器。
4、实训内容(1) 、冲孔落料模工艺分析电火花冲孔落料模是生产上应用较多的一种模具,由于形状复杂和尺寸精度要求高,因此它的加工是生产中的关键技术之一,特别是凹模加工。
通常的方法是用线切割加工凸模,再利用凸模作为工具电极在电火花成形机床上“反打”来加工凹模。
(2) 、工具电极的高度尺寸设计工具电极的高度尺寸取决于冲孔落料模的结构形式、模板厚度、电极材料、装夹方式、电极使用次数和电极制造工艺等一些因素( 见图1) ,可用下式表示L二KH+h+H2+(0 . 4〜0. 8)(n-l)KH式中L――设计工具电极高度;H ――凹模需要加工的深度;H i――当模板后部挖空时,电极所需加长部分的深度;H 2――一些小电极端部不宜开连接螺孔,而必须用夹具夹持电极尾部时,需要增加的夹持部分长度(约10〜20mm)n ―― —个电极使用的次数,一般情况下,多用一次电极需要比原有长度增加(0 . 4〜0. 8)倍;K——与电极材料、加工方式、型腔复杂程度有关的系数,对不同的电极材料,K取值不同,紫铜为2〜2. 5、黄铜为3〜3. 5、石墨为I . 7〜2、铸铁为2. 5〜3、钢为3〜3. 5,若加工硬质合金时,电极损耗会增大,因此,应适当增加电极长度。
(3)、工具电极水平尺寸设计工具电极的水平尺寸应比预定的冲孔截面尺寸均匀地缩小一个平面的放电间隙,即d=D-2S式中d ——工具电极的水平尺寸;D ――加工后冲孔尺寸;S――单面的放电间隙。
通常情况下,模具样图只标注凸模的具体尺寸,而凹模样图只标注与凸模的配合间隙,所以会存在如下情况:①、凸、凹模配合间隙等于放电间隙,此时电极尺寸与凸模完全相同;②、凸、凹模配合间隙小于放电间隙,此时电极尺寸应等于凸模尺寸减去放电间隙与配合间隙的差值;③、凸、凹模配合间隙大于放电间隙,此时电极尺寸应等于凸模尺寸加上放电间隙与配合间隙的差值。
电火花加工实习报告
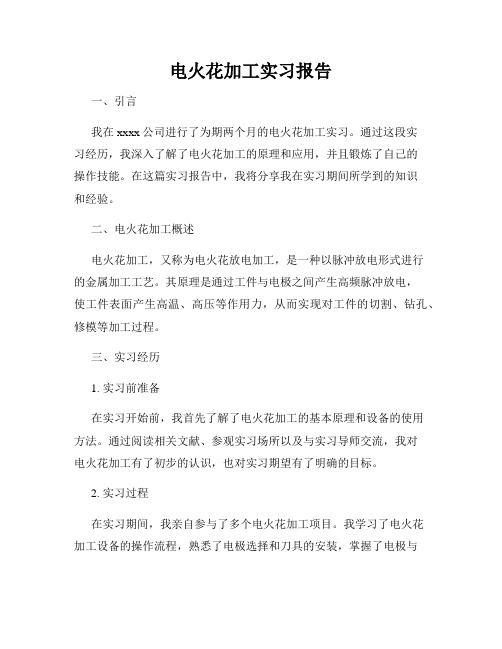
电火花加工实习报告一、引言我在xxxx公司进行了为期两个月的电火花加工实习。
通过这段实习经历,我深入了解了电火花加工的原理和应用,并且锻炼了自己的操作技能。
在这篇实习报告中,我将分享我在实习期间所学到的知识和经验。
二、电火花加工概述电火花加工,又称为电火花放电加工,是一种以脉冲放电形式进行的金属加工工艺。
其原理是通过工件与电极之间产生高频脉冲放电,使工件表面产生高温、高压等作用力,从而实现对工件的切割、钻孔、修模等加工过程。
三、实习经历1. 实习前准备在实习开始前,我首先了解了电火花加工的基本原理和设备的使用方法。
通过阅读相关文献、参观实习场所以及与实习导师交流,我对电火花加工有了初步的认识,也对实习期望有了明确的目标。
2. 实习过程在实习期间,我亲自参与了多个电火花加工项目。
我学习了电火花加工设备的操作流程,熟悉了电极选择和刀具的安装,掌握了电极与工件的定位方法。
我还学会了调整加工参数,如脉冲电流、脉冲宽度和放电时间等,以确保加工效果的准确性和稳定性。
3. 实习成果通过实习,我成功地完成了多个电火花加工项目。
我能够根据工件要求设计合适的工艺方案,并且能够熟练操作电火花加工设备进行加工作业。
同时,我还进一步了解了电火花加工与其他加工方式的不同之处,以及其在模具制造、航空航天等领域的应用。
四、实习收获1. 知识方面通过实习,我深入了解了电火花加工的原理和技术特点。
我学会了分析工件图纸和工艺要求,制定合适的加工方案,并且能够进行相应的设备调整和操作。
我还了解了电火花加工的优势和适用范围,为将来的工作奠定了坚实的基础。
2. 技能方面在实习期间,我通过不断的实操和反复练习,逐渐提升了自己的操作技能。
我能够独立完成加工任务,并且能够及时发现和解决操作中的问题。
我还锻炼了自己的团队协作能力,在与同事进行项目合作时能够有效地分工合作。
3. 心态方面实习期间的挑战使我更加明确了自己的职业目标和发展方向。
我对电火花加工产生了浓厚的兴趣,并且希望将来能够在这个领域有所成就。
电火花加工实习报告

电火花加工实习报告在学校的安排下,我进行了为期X周的电火花加工实习。
这次实习让我对电火花加工这一先进制造技术有了更深入的了解和实际操作经验。
电火花加工是一种利用脉冲放电产生的热能来蚀除金属材料的特种加工方法。
它在模具制造、航空航天、汽车工业等领域有着广泛的应用。
实习之初,指导老师为我们详细讲解了电火花加工的基本原理和设备结构。
电火花加工的基本原理是基于工具电极和工件电极之间脉冲性火花放电时的电腐蚀现象来蚀除多余的金属,以达到对零件的尺寸、形状及表面质量预定的加工要求。
设备主要由机床本体、脉冲电源、自动进给调节系统、工作液循环过滤系统和数控系统等部分组成。
在了解了理论知识后,我们开始熟悉电火花加工机床的操作。
机床的操作面板上有各种按钮和参数设置选项,如放电电流、放电脉冲宽度、放电脉冲间隔等。
这些参数的选择直接影响到加工的效果和效率。
刚开始操作时,我总是小心翼翼,生怕出错。
但在老师的耐心指导下,我逐渐掌握了操作要领,能够较为熟练地进行一些简单的加工操作。
在实际加工过程中,我深刻体会到了工艺参数的重要性。
不同的材料、形状和加工要求需要不同的工艺参数组合。
例如,对于硬度较高的材料,需要较大的放电电流和较短的脉冲宽度;而对于精度要求较高的零件,则需要较小的放电电流和较长的脉冲宽度,以减小放电能量,提高加工精度。
同时,工作液的选择和循环也对加工效果有着重要影响。
合适的工作液不仅能够冷却电极和工件,还能起到排屑和消电离的作用,保证加工的稳定性和质量。
为了更好地掌握电火花加工技术,我们还进行了一系列的加工实践。
首先是简单形状的零件加工,如方形、圆形等。
在这个过程中,我们主要练习了如何正确装夹工件和电极,如何设置工艺参数以及如何进行加工过程的监控。
随着操作的熟练,我们开始进行复杂形状零件的加工,如模具的型腔和型芯。
这就需要我们更加精细地设计电极,合理安排加工顺序,并不断调整工艺参数,以达到理想的加工效果。
在加工过程中,也遇到了一些问题和困难。
电火花实训报告总结

电火花实训报告总结在这次电火花实训中,我深入学习了电火花加工原理、工艺参数的调整、仪器设备的使用以及操作与安全规范等方面的知识。
通过实际操作和实验,我对电火花加工有了更深入的理解,并掌握了相关技能。
以下是我对这次实训的总结和反思。
一、实训内容本次电火花实训主要包括以下几个方面的内容:1. 电火花加工原理:通过学习,我了解到电火花加工是一种利用电脉冲放电的方式进行金属加工的方法。
电脉冲放电时,电极产生高强度的电场,使工件表面产生电火花,瞬间溶化并蒸发,从而实现加工的目的。
2. 工艺参数的调整:在实际操作中,我学会了根据不同的材料和加工需求来调整电火花加工的工艺参数,如电极大小、放电电压和放电时间等。
正确选择和调整这些参数对于电火花加工的质量和效率非常重要。
3. 仪器设备的使用:我们学习了电火花加工所需的各种仪器设备的使用方法和操作技巧,包括放电机床、电脉冲发生器等。
熟练掌握这些设备的使用对于实际操作和加工效果具有重要意义。
4. 操作与安全规范:在实训中,我们严格遵守电火花加工的操作规程和安全规范,从而保证了我们的人身安全和设备的正常运行。
了解和掌握这些规范对于保障工作安全非常重要。
二、实训成果通过这次电火花实训,我取得了以下几个方面的成果:1. 理论知识的提升:我对电火花加工的原理和工艺参数等方面有了较为深入的理解。
我了解到不同的加工材料和要求需要不同的工艺参数进行调整,这对于我实际应用电火花加工技术非常有帮助。
2. 实际操作技能的增强:通过反复的实际操作,我掌握了电火花加工的操作技巧,如如何调整电极大小、如何设置放电电压和时间等。
这使得我能够更加熟练地进行电火花加工。
3. 安全意识的提高:在实训过程中,我严格遵守操作规程和安全规范,增强了我的安全意识。
我清楚了解到电火花加工过程中存在电击、火花飞溅等安全隐患,因此在工作中要谨慎小心,保持设备正常和自身安全。
三、经验与不足在实训过程中,我也遇到了一些问题和不足之处:1. 对材料和工艺的选择还不够熟悉。
电火花加工厂实习报告

一、实习背景随着我国制造业的快速发展,特种加工技术在现代工业中扮演着越来越重要的角色。
电火花加工作为一种高效、精密的加工方法,广泛应用于航空航天、汽车制造、模具制造等领域。
为了深入了解电火花加工技术,提升自己的实践能力,我于2021年7月进入某电火花加工厂进行了为期一个月的实习。
二、实习目的1. 熟悉电火花加工的基本原理和工艺流程。
2. 掌握电火花加工设备的操作方法和维护保养技巧。
3. 提高自己的实际操作技能和解决实际问题的能力。
4. 了解电火花加工在工业生产中的应用和发展趋势。
三、实习内容1. 基本理论的学习在实习初期,我认真学习了电火花加工的基本原理、工艺流程、设备分类、加工参数选择等方面的理论知识。
通过查阅资料、请教师傅等方式,我对电火花加工有了初步的了解。
2. 实际操作在师傅的指导下,我逐步掌握了电火花加工设备的操作方法。
实习期间,我参与了以下几项实际操作:(1)电极加工:我学习了如何根据图纸要求,选择合适的电极材料、加工方法和加工参数,并熟练操作数控机床进行电极加工。
(2)工件加工:我学习了如何根据工件材料、形状和加工要求,选择合适的加工参数和工艺路线,并操作电火花加工设备进行工件加工。
(3)设备维护与保养:我学习了如何对电火花加工设备进行日常维护和保养,确保设备的正常运行。
3. 项目实践在实习过程中,我参与了一个实际项目,负责电火花加工设备的操作和维护。
在师傅的指导下,我独立完成了以下工作:(1)根据项目要求,制定加工工艺方案,包括电极加工、工件加工等。
(2)操作电火花加工设备,完成工件加工。
(3)对加工过程中出现的问题进行分析,并提出解决方案。
(4)对设备进行维护和保养,确保设备正常运行。
四、实习收获1. 理论知识与实践相结合:通过实习,我深刻体会到理论知识的重要性,同时将所学知识应用于实际操作中,提高了自己的实践能力。
2. 技能提升:在实习过程中,我熟练掌握了电火花加工设备的操作方法和维护保养技巧,提高了自己的技能水平。
电火花实习报告总结

一、实习背景随着我国制造业的快速发展,电火花加工技术在精密零件加工领域得到了广泛应用。
为了更好地了解电火花加工技术,提高自身实践能力,我于近期参加了为期两周的电火花实习。
本次实习主要在XX工厂进行,实习内容包括电火花加工设备的操作、编程、加工工艺等方面的学习。
二、实习目的1. 了解电火花加工技术的原理、设备、工艺及编程方法;2. 掌握电火花加工设备的操作技能,提高实际操作能力;3. 培养团队合作精神,提高沟通协调能力;4. 为今后从事相关行业工作打下坚实基础。
三、实习过程1. 理论学习实习期间,我首先进行了电火花加工技术的理论学习。
通过查阅资料、请教师傅,我了解到电火花加工的基本原理、设备类型、加工工艺等方面的知识。
同时,我还学习了电火花加工编程方法,为实际操作奠定了基础。
2. 设备操作在理论学习的基础上,我开始接触电火花加工设备。
在师傅的指导下,我逐步掌握了设备的操作方法。
实习过程中,我学习了以下几种设备的操作:(1)电火花线切割机床:了解机床的结构、功能及操作流程,掌握切割速度、进给速度、间隙等参数的调整方法。
(2)电火花成型机床:熟悉机床的结构、功能及操作流程,掌握加工参数的调整方法,如加工电流、加工电压、加工速度等。
(3)电火花微细加工机床:了解机床的结构、功能及操作流程,掌握加工参数的调整方法,如加工电流、加工电压、加工速度等。
3. 编程实践在设备操作的基础上,我进行了电火花加工编程实践。
通过学习编程软件,我掌握了编程的基本方法,能够根据工件图纸编写出相应的加工程序。
4. 加工工艺实习过程中,我还学习了电火花加工的工艺参数调整方法。
在师傅的指导下,我了解到加工电流、加工电压、加工速度、加工深度等参数对加工质量的影响,并学会了如何根据工件材料和加工要求调整工艺参数。
四、实习收获1. 理论知识方面:通过实习,我对电火花加工技术有了更深入的了解,掌握了设备操作、编程、工艺等方面的知识。
2. 实践能力方面:实习过程中,我熟练掌握了电火花加工设备的操作技能,提高了实际操作能力。
电火花加工实训报告
电火花加工实训报告实训报告:电火花加工一、实训背景和目的电火花加工是一种非接触式的金属加工技术,通过电火花放电的方式,在金属工件表面形成微小的放电坑,以达到加工工件的目的。
本次实训旨在使学生了解电火花加工的原理、设备和操作方法,并进行实际操作,掌握电火花加工技术。
二、实训内容1. 学习电火花加工原理和设备- 电火花加工原理:了解电火花加工的原理和基本概念。
- 电火花加工设备:学习电火花加工设备的组成和工作原理。
2. 实际操作电火花加工设备- 设备调试:了解电火花加工设备的使用方法和步骤,进行设备的调试和操作准备。
- 加工试验:选择合适的工件和加工参数,在电火花加工设备上进行加工试验。
- 加工控制:掌握电火花加工过程中的加工控制方法,如放电电流、脉冲间隔等参数的调整。
3. 检验和评估- 加工后工件测量与评估:使用测量工具对加工后的工件进行尺寸测量,评估加工质量。
- 实训总结与报告:对本次实训进行总结和报告,包括实际操作的心得体会和对电火花加工技术的理解。
三、实训过程和结果1. 学习电火花加工原理和设备在实训前,通过课堂学习和相关资料的阅读,了解了电火花加工的基本原理和设备。
2. 实际操作电火花加工设备实训时,首先进行了电火花加工设备的调试,包括电源的连接、电极的安装和工作台的调整等。
然后选择了一块金属工件,并根据加工要求调整了放电电流和脉冲间隔等参数。
经过多次试验和调整,最终得到了满意的加工效果。
3. 检验和评估使用测量工具对加工后的工件进行了尺寸测量,发现工件尺寸与设计要求基本一致,表明电火花加工的加工质量良好。
4. 实训总结与报告通过本次实训,我对电火花加工的原理、设备和操作方法有了更深入的了解,掌握了电火花加工技术。
在实际操作中,我也学会了调整加工参数和控制加工质量。
同时,我也体会到了电火花加工的优点和局限性,在实际应用中需要根据具体情况加以考虑。
四、实训心得与建议本次实训使我对电火花加工有了更深入的了解,通过亲自操作和加工实践,使我对电火花加工技术有了更深刻的认识。
电火花成型加工实验报告
电火花成型加工实验报告实验报告:电火花成型加工一、实验目的1.了解电火花成型加工的基本原理和工艺过程。
2.掌握电火花成型加工的操作方法和注意事项。
3.分析电火花成型加工的优缺点及应用领域。
二、实验原理电火花成型加工是指利用脉冲电流产生的高温等离子体在工件表面复杂轮廓上进行加工的一种非传统的精密加工方法。
其工作原理是通过脉冲电流在工件表面上形成电火花放电,从而使工件表面熔化或氧化剥离,形成所需形状的孔洞或凸台等特殊结构。
电火花加工适用于所有导电材料,特别适用于硬度高、脆性大、加工难度大的材料。
三、实验仪器和材料1.电火花加工设备:包括工作台、工作液、发生器等。
2.工件:导电材料,如金属。
3.电源:提供工作电流进行加工。
四、实验步骤1.准备工作:将工件放置在工作台上,调整加工参数。
2.加工操作:开启电源,选择合适的脉冲电流进行加工。
注意观察电火花放电效果,确保加工质量和加工精度。
3.停止加工:当脉冲电流达到预定加工时间后,停止加工,关闭电源,取出工件。
4.清洁工作:将加工过程中产生的废料和杂质清理干净,保持实验环境整洁。
五、实验结果与分析通过实验操作,完成了电火花成型加工的任务。
观察加工后的工件,可以看到形成了所需形状的孔洞或凸台等特殊结构。
加工质量和加工精度取决于加工参数的调整,调整电流大小和加工时间可以控制加工效果。
实验证实,电火花成型加工可以对导电材料进行精密加工,能够满足一些传统加工方法无法实现的任务。
六、实验心得通过本实验,我对电火花成型加工的原理和工艺过程有了更加深入的了解。
电火花成型加工是一种非常重要的非传统加工方法,它可以对导电材料进行高精度的加工,具有一定的优势和应用前景。
在实验操作过程中,要注意安全措施,避免发生意外事故。
此外,需要对加工参数进行合理的调整,以获得较好的加工效果。
这次实验让我更加熟悉电火花成型加工的操作方法和注意事项,对工程制造领域有一定的参考价值。
七、实验展望通过本次实验,我对电火花成型加工有了初步的认识,但仍然有许多不足之处。
关于电火花成型的实训报告
千里之行,始于足下。
关于电火花成型的实训报告电火花成型是一种利用电脑控制的高频电火花腐蚀现象将金属加工成所需形状的加工方法。
它具有高精度、高表面质量和复杂形状等优点,广泛应用于模具制造、航空航天、汽车零部件等行业。
为了更好地理解电火花成型的原理和工艺流程,我们进行了一次实训。
本次实训主要包括以下几个环节:设备调试、工艺参数设置、样件加工和质量检验。
首先是设备调试。
我们首先熟悉了电火花成型机床的主要结构和功能。
电火花成型机床由主机、辅助机构和控制系统组成。
主机是完成电火花加工任务的主体,包括电极系统、加工台、电源系统等。
辅助机构包括液压系统、自动换刀系统等,用于辅助加工。
控制系统是整个机床的核心,采用了先进的数控技术,可以实现高精度、高效率的加工。
在调试过程中,我们检查了设备的各个部件是否正常运行,并进行了简单的调整和维护。
接下来是工艺参数设置。
根据所要加工的零件的材料、形状和尺寸等要求,我们选择了合适的电极和工艺参数。
首先是电极的选择。
电极是电火花成型中的重要部件,直接影响到加工效果。
一般情况下,正电极用铜或铜合金制作,负电极用钼制作。
然后是工艺参数的设置。
工艺参数包括放电电压、放电电流、放电时间等,通过合理设置这些参数可以控制电火花的能量大小和作用时间,从而实现精准成型。
我们根据实际情况进行了调整,确保加工效果的质量。
第三步是样件加工。
在实际加工过程中,我们根据设备和工艺参数设置好后,将需要加工的零件安装到加工台上,并进行定位和夹紧。
然后启动机床,通过控制系统进行加工。
在加工过程中,电极会向工件表面靠近,当两者之间的距离达到一定值时,电火花会在两者之间产生,从而将金属加工成所需形状。
第1页/共2页锲而不舍,金石可镂。
不断地放电和停电,直到加工完成。
整个过程需要根据实际情况进行适当监控和调整,以确保加工效果的质量。
最后是质量检验。
加工完成后,我们对加工后的零件进行了质量检验。
主要包括尺寸和表面质量的检查。
电火花成形加工实训指导
电火花成形加工实训指导一、实训目的1、电火花成形机床的组成、工作原理和操作方法。
2、掌握电极材料的选择、结构形式及电极尺寸计算。
3、掌握电极和工件的装夹及校正定位。
4、掌握加工中电规准的选择及加工参数对被加工型腔质量的影响。
二、实训设备及材料1、电火花机车一台。
2、工具电极一根(材料为铜、石墨、或钢)3、工件材料为常用模具钢。
三、实训内容及步骤在实训教师的指导下,了解电火花加工机车的主要构成,机车和控制板上各旋钮及按键的功用,工件的装夹、平动量的调节及加工操作过程。
1、功能键的介绍(F1~F10)F1:手动放电。
在单节放电时使用即一段加工结束后机车停止。
F2:自动放电。
当有多段程序时,前一段放电结束F3:程序编制。
进行程序的编制。
F4:位置归零。
设定加工的起始点。
F 5:位置设定。
设定加工型腔的平面位置。
F6:找中心点。
当型腔位置在中心是用F6。
F7:EDM参数。
在加工过程中要改变参数是使用。
F8:机械参数。
厂家设定,没有必要不做改动。
F9:计时器归零。
加工时记下加工的时间,在加工开始时要归零。
F10:参数自动匹配。
一些主要加工参数可以在程序编制的时候编制好,但是如脉冲间隔、放电间隙等一些辅助参数可以在编制程序的时候编制好,也可以利用自动匹配的方法自动设定。
四、操作面版介绍在介绍控制面板前,要先将放电条件介绍给大家。
只有熟记放电条件的涵义,才能合理的编制程序并对放电过程中出现的问题加以解决。
B P:高压电流。
设置值大,电流大,火花大,加工的速度快,但表面的质量低,间隙大,设置值小则反之。
一般在粗加工时使用。
A P:低压电流。
设定范围在0~90之间,设定值大火花大,加工速度快,但表面的质量低,间隙大。
设置值小则表面质量高,间隙小。
在使用过程中要注意,电流大于9A时要浸油加工,以防止失火。
P A:脉宽。
与电流配合来决定表面粗糙度,一般是电流的20~30倍。
P B:脉宽间隔。
设定值小,效率高,但容易造成排渣不畅,在加工过程中一般要视电极的材料而定。
- 1、下载文档前请自行甄别文档内容的完整性,平台不提供额外的编辑、内容补充、找答案等附加服务。
- 2、"仅部分预览"的文档,不可在线预览部分如存在完整性等问题,可反馈申请退款(可完整预览的文档不适用该条件!)。
- 3、如文档侵犯您的权益,请联系客服反馈,我们会尽快为您处理(人工客服工作时间:9:00-18:30)。
电火花成形加工实训
实训四电火花工具电极找正
1、实训目的
掌握电火花工具电极的找正方法。
2、实训项目
电火花工具电极的找正。
3、实训器材
NH7135NC数控电火花成形机床、工具电极、精密刀口角尺、百分表。
4、实训内容
(1)、型腔模工艺分析
电火花加工中,工具电极的装夹尤其重要。
撞击方法可用钻夹头装夹,也可用专用夹具装夹,还可用瑞典3R夹具装夹。
工具电极的找正是要确保工具电极与工件的垂直,找正的方法主要有用精密刀口角尺找正、用百分表找正、用电火花放电找正和用工件模板找正。
(2)、工具电极的装夹
①、用钻夹头装夹工具电极先用内六角头扳手将装在主轴夹具上的内六角螺钉旋松,然后将装夹工具电极的钻夹头固定在主轴夹具上。
主轴夹具的装夹部分为900靠山的结构,可将钻夹头稳固地贴在靠山上,最后再用内六角扳手将主轴夹具上的内六角螺钉旋紧,完成工具电极的装夹(图1)。
②、用专用夹具装夹工具电极还可以采用电火花线切割加工出电极扁夹,作为专用的夹具来装夹工具电极,电极扁夹用于装夹某些尺寸比较小的扁状电极。
③、用瑞典3R夹具装夹工具电极采用瑞典3R夹具装夹工具电极时,3R夹具与工具电极固定在一起,在数控机床上加工,加工后再一同装夹到主轴上。
这样的方法解决了工具电极拆装后的重复定位问题。
图1 用钻夹头装夹工具电极
(3)工具电极的找正
①、用精密刀口角尺找正工具电极工具电极装夹完毕后,必须对工具电极进行找正,确保电极的轴线与工件保持垂直,图2所示为用精密刀口角尺找正工具电极。
具体校准方法如下:
图2 用精密刀口角尺找正工具电极图3 用百分表找正工具电极
a.按下手控盒上的“Z-”按钮,将工具电极缓缓放下,使工具
电极慢慢靠近工件,在与工件之间保持一段间隙后,停止下降工具电极。
b.沿X轴方向工具电极找正。
沿X轴方向将精密刃口角尺放置在工件(凹模)上,使精密刃口角尺的刀口轻轻与工具电极接触,移动照明灯置于精密刃口角尺的后方,通过观察透光情况来判断工具电极是否垂直。
若不垂直,可调节处于主轴夹头球形面上方的X轴方向调节螺钉。
c.沿Y轴方向工具电极找正。
沿Y轴方向将精密刀口角尺轻轻与工具电极接触,移动照明灯置于精密刀口角尺的后方,通过观察透光情况来判断工具电极是否垂直。
若不垂直,可调节处于主轴夹头球形面上方的Y轴方向调节螺钉。
d.工具电极的旋转找正。
工具电极装夹完成后,工具电极形状与工件的型腔之间常常存在着不完全对准的情况,此时需要对工具电极进行旋转找正。
找正方法是轻轻旋动主轴夹头上的调节电极旋转螺钉,确保工具电极与工件型腔对准。
②、用百分表找正工具电极由于精密刃口角尺的精度仍不是最高,因此在用角尺校准完毕后,还应用百分表进行找正。
图3所示为用百分表找正工具电极,找正步骤如下。
a.将磁性表座吸附在机床的工作台上,然后把百分表装夹在表座的杠杆上。
b.沿X轴方向工具电极找正。
首先将百分表的测量杆沿X轴方向上轻轻接触工具电极,并使百分表有一定的读数,然后按手控盒上
“Z+”或“Z-”按钮,使主轴(Z轴)上下移动,观察百分表的指针变化。
根据指针变化就可判断出工具电极沿X轴方向上的倾斜状况,再用手调节主轴机头上X轴方向上的两个调节螺钉,使工具电极沿x轴方向保持与工件垂直。
c.沿Y轴方向工具电极找正。
将百分表的测量杆沿Y轴方向上轻轻接触工具电极使百分表有一定的读数。
然后按手控盒上“Z+”或“Z-”按钮,使主轴(Z轴)上下移动,观察百分表指针变化。
根据指针变化就可判断出工具电极沿Y轴方向上的倾斜,再用手调节主轴机头上Y轴方向上的两个调节螺钉,使工具电极沿Y轴方向保持与工件垂直。
③、用工件模板找正工具电极操作时,将工件模板放置在工件电极上,工件模板上孔与加工型腔对齐,用工具电极来找正工件模板上的孔位。
一般工件模板上的孔采用线切加工,这种方法常在生产中采用,可快速对工具电极的加工位置进行找正。
5、实训思考题
①、如何装夹工具电极?各种装夹方法有哪些特点?
②、如何找正工具电极?。