冲压模具设计指导示范
冲压模具设计指导

冲压模具设计指导一、概述冲压模具是冲压件生产的关键工具,设计合理的冲压模具是保证冲压件质量和生产效率的重要因素。
冲压模具设计包括模具结构设计、尺寸配合设计、工作零件设计等内容。
本文将从设计原则、设计流程和设计要点三个方面对冲压模具设计进行指导。
二、冲压模具设计原则1.设计合理性:冲压模具的结构应简单、经济、合理,能够满足产品的要求,使得生产效率和质量最大化。
2.加工性:冲压模具的设计应考虑加工工艺要求,便于加工设备操作和加工过程管理。
3.换模方便性:冲床换模是生产过程中常进行的操作,模具设计应方便快捷,以提高生产效率。
4.模具的可靠性:冲压模具在使用过程中应具有良好的稳定性,防止失效和事故的发生。
5.维修性:冲压模具设计时应注意易损件的保护和更换外加助你。
6.经济性:冲压模具的设计要经济合理,尽量减少材料消耗和成本。
三、冲压模具设计流程1.确定冲压工艺:对冲压件进行分析、测量,确定冲压工艺包括料厚、材料强度、冲压力等参数。
2.制定模具结构:根据冲压工艺确定的参数,制定模具结构,包括上模、下模和导向机构等。
3.设计模具零件:根据模具结构设计要求,分别设计上下模具板、模具座、导向柱、导向套、顶杆等零件。
4.设计尺寸配合:根据模具结构和工作零件的要求,设计各零件的尺寸配合,包括孔径、螺纹等。
5.绘制图纸:按照设计要求和标准,绘制出冲压模具的详细图纸。
6.模具加工:根据图纸进行模具加工,包括车、铣、刨、磨等工艺。
7.模具调试:对制作好的模具进行调试,包括安装、调整和检测等工作。
四、冲压模具设计要点1.结构设计要合理:冲压模具的结构要简单合理,能够保证冲压工艺的要求,并便于加工和维修。
2.冲裁间隙要合适:冲裁间隙是指上模和下模接合部分的厚度,过大会影响产品的尺寸精度,过小会导致模具损坏或卡死。
3.材料选择要合理:冲压模具的材料要选择硬度高、耐磨、耐疲劳和耐冲击的材料,如合金钢。
4.强度计算要准确:冲压模具的各零件的强度要进行准确计算,以保证模具的稳定性和安全性。
冲压模具设计和制造实例
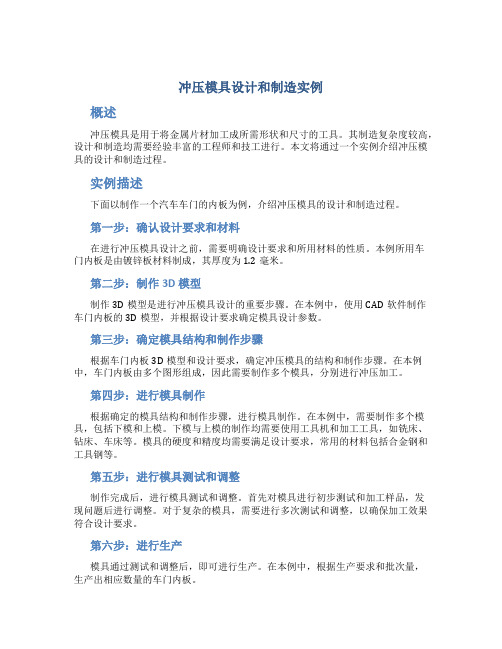
冲压模具设计和制造实例概述冲压模具是用于将金属片材加工成所需形状和尺寸的工具。
其制造复杂度较高,设计和制造均需要经验丰富的工程师和技工进行。
本文将通过一个实例介绍冲压模具的设计和制造过程。
实例描述下面以制作一个汽车车门的内板为例,介绍冲压模具的设计和制造过程。
第一步:确认设计要求和材料在进行冲压模具设计之前,需要明确设计要求和所用材料的性质。
本例所用车门内板是由镀锌板材料制成,其厚度为1.2毫米。
第二步:制作3D模型制作3D模型是进行冲压模具设计的重要步骤。
在本例中,使用CAD软件制作车门内板的3D模型,并根据设计要求确定模具设计参数。
第三步:确定模具结构和制作步骤根据车门内板3D模型和设计要求,确定冲压模具的结构和制作步骤。
在本例中,车门内板由多个图形组成,因此需要制作多个模具,分别进行冲压加工。
第四步:进行模具制作根据确定的模具结构和制作步骤,进行模具制作。
在本例中,需要制作多个模具,包括下模和上模。
下模与上模的制作均需要使用工具机和加工工具,如铣床、钻床、车床等。
模具的硬度和精度均需要满足设计要求,常用的材料包括合金钢和工具钢等。
第五步:进行模具测试和调整制作完成后,进行模具测试和调整。
首先对模具进行初步测试和加工样品,发现问题后进行调整。
对于复杂的模具,需要进行多次测试和调整,以确保加工效果符合设计要求。
第六步:进行生产模具通过测试和调整后,即可进行生产。
在本例中,根据生产要求和批次量,生产出相应数量的车门内板。
冲压模具的设计和制造是一项复杂精细的工作,需要技术水平和经验。
本例通过一个车门内板的制作过程,展示了冲压模具设计和制造的详细步骤,包括确认设计要求和材料、制作3D模型、确定模具结构和制作步骤、进行模具制作、进行模具测试和调整以及进行生产。
这些步骤都需要严密的操作和高水平的技术,以确保最终的产品质量。
冲压模具设计课程设计指导书DOC

《冲压模具设计》课程设计指导书《冲压模具设计》课程设计指导书一、课程设计的性质与目的冲模课程设计是冲压工艺及模具设计课程的一个重要环节,是运用所学知识的一次综合练习。
其主要目的是:·1.使学生初步掌握冲压工艺过程的拟定和模具结构设计与计算的步骤和方法:2.巩固、深化所学的基础及专业知识,培养独立工作能力;3.提高学生使用国标、手册和图册的能力。
二、课程设计的任务在两周的时间内完成下列任务,统一交到指定的地点。
1.拟定冲压件的工艺过程,并填写工艺过程卡1份;2.填写凸、凹模(及凸凹模)的加工工艺卡片;3.设计指定冲压件的其中一道工序的冲压模(每人设计一副不同的模具),并绘制装配图和凸、凹模零件图:1套;(注:①指定冲压件的生产批量可以根据需要进行更改;②未注尺寸公差按GB/T15055的m级)4.编写设计说明书1份,约20页左右。
三、设计原则1.装配图的零件必须完整,保证冲出合格的工件;2.模具结构简单,寿命长,成本低且与生产批量相适应;3.操作方便,安全.四、设计前的准备1.熟悉设计任务书,明确设计任务和要求;2.了解冲压零件的形状,尺寸精度和表面粗糙度,材料等技术要求和生产批量;3.配备资料:(1)冲压设备资料:从此资料中选择冲压设备的类型,规格,查出漏料孔尺寸,模柄孔尺寸,闭合高度,工作台面尺寸等,为模具设计作准备:(2)冲模标准化资料;(3)其他参考资料:《冷冲模设计》手册,《冷冲模结构图册》.五、冲模课程设计的一般步骤及方法1.分析冲压件的工艺性冲裁件的工艺性主要从冲裁件的形状,尺寸(最小孔边距,孔径,材料厚度,最大外形)精度,表面粗糙度,材料性能等逐项分析,确定冲压工序图,若有不符者,应与指导老师协商更改或采取相应的措施。
2.确定合理工艺方案(1)确定基本冲压工序的性质:冲孔,落料,冲搭边,切料边等.(2)根据基本工序的性质,数量,结合工件的形状尺寸,公差要求,材料性能,生产批量,冲压设备,模具加工条件等因素,考虑模具类型的同时确定工序组合和先后顺序,在满足冲件质量要求的前提下,选择一个经济合理的工艺方案,填写工艺过程卡片。
ug冲压模具设计教程 (1)全文

第3步
第4步 为第1工位上最左边的3mm孔废料设计冲裁凹 模镶块
1
2
3
4
5 6
模型里包括了两个实体,一个是描画零件自身外形的实体 零件〔Ture Body〕,一个是用来在模板上开设零件装置孔的 工具实体〔False Body〕
第5步 为新拔出的凹模镶块设计落料孔。
1
2
3
4
两个复选框区分控制BBP 和DS板上落料孔的数量。假设 用户将For each scrap复选框 选中,所选的多块废料在BBP 和DS板上区分生成各自的落料 孔。否那么,多块废料将在 BBP和DS板上共用一个落料孔 。
ug冲压模具设计教程
2024/8/26
第8章 冲裁组件设计
普通冲裁设计 精细冲裁设计
【设计】:包括普通冲裁设计和精细冲裁设计; 【阵列】:可以创立、编辑和删除一个矩形或圆形的组件阵列 ;【关联】:在废料和冲裁组件之间树立一种关联性,包括位置 关联和外形关联;
练习 冲裁组件设计 pierce 文件夹中的a8_control_000装配体。
第10步 为凹模镶块设计落料孔。
1
2 3
第11步 为废料设计冲头,此废料的尺寸信息必需手工交互 查询。
2 1
3
1
3 2
4 5
留意:当特征更新失败 时,尽量将组件生成,抑 制失败的特征。组件生成 后,要反省更新失败的缘 由并修正其中的效果。
第12步 重定位P8R冲头。
124 356 7第13步 编辑P8R冲头,修正更新失败的blend特征。
2
3
4
1
2 3
练习 弯曲组件设计
用工程初始化从bend文件夹翻开a8_control_000.prt
冲压模具设计指导下

冲压模具设计指导(下)要使尺寸标注正确,就要把握尺寸标注的“思路”。
前面要求绘制所要零件图的图形而先不标注任何尺寸,就是为了在标注尺寸时能够统筹兼顾,用一种正确的“思路”来正确地标注尺寸。
下面以图5倒装复合模为例阐述尺寸标注的“思路”。
(1)标注工作零件的刃口尺寸根据模具设计法则,先标注基准件上刃口尺寸(即冲孔击模和落料上的要使尺寸标注正确,就要把握尺寸标注的“思路”。
前面要求绘制所要零件图的图形而先不标注任何尺寸,就是为了在标注尺寸时能够统筹兼顾,用一种正确的“思路”来正确地标注尺寸。
下面以图5倒装复合模为例阐述尺寸标注的“思路”。
(1)标注工作零件的刃口尺寸根据模具设计法则,先标注基准件上刃口尺寸(即冲孔击模和落料上的刃口尺寸),再标注对应件上的刃口尺寸(即击凹模上的刃口尺寸);但符合模中也可将击凹模作为基准件,击模、凹模作为对应件进行尺寸标注。
所有零件图的图形绘好后,先找出本模具的工作零件即击凹模7、冲孔击模12和27、落料凹模26,把着三张图纸对照起来,按照尺寸布置后安排好的“地点”标注刃口尺寸。
这样可保证刃口尺寸标注的正确性。
(2)标准想关零件的相关尺寸相关尺寸正确,各模具零件才能装配组成一幅模具,必须保证正确。
在上模部分,相关尺寸的标注建议按照“自上而下”的顺序进行。
先从工作零件凹模26开始,观察装配图6,与该零件模具相关的零件有内六角螺钉24、销钉25推块11、冲孔击模13,应从分析着些相关关系入手进行“相关尺寸”的标注。
凹模26与销钉25成H7/m6配合,故销钉孔直径为Ф8H7。
销钉25要通过26、13、1 4、16等模板,其中与26与16成H7/m6配合,因此上模座16上销钉孔直径也应为Ф8H7,可立即在上模座16的零件图上标出该尺寸。
而销钉通过13、14模板的孔是应有0.5~1mm的间隙,因此13、14上相应的过孔直径为Ф9,也应在相应的图纸上立即标出。
凹模26与3个M8的内六角螺钉24是螺纹连接,因此凹模26的图纸上对应螺纹孔应标注为3-M8;螺钉24也同过16、13、14、16等模板,其中与13、14、16上的过孔也有0.5~1mm的间隙,相应的图纸上应立即标注Ф9,各模板上的螺纹孔距均为Ф9,各模板上的螺纹孔距均为Ф56一并标出。
ug冲压模具设计实例

ug冲压模具设计实例设计一款汽车门锁芯冲压模具。
1. 首先,确定产品的尺寸和形状要求。
门锁芯通常由锁体、锁舌和锁芯等组成,需要测量这些组件的尺寸,以确定设计时的模具尺寸。
2. 创建三维模型。
使用UG软件创建一个汽车门锁芯的三维模型,包括锁体、锁舌和锁芯等部分。
根据设计要求,通常需要考虑材料的厚度、强度和针对不同零件的加工和操作要求。
3. 添加冲头和模具组件。
将冲头和模具组件加入到模型中,冲头是用于对工件进行变形和冲压的工具,而模具则主要用于支撑和定位工件。
4. 进行模拟分析。
使用UG软件进行模拟分析,验证模具的可行性和工艺性。
可以模拟冲压过程中的变形情况,以确保模具设计合理。
5. 完善模具设计。
根据模拟分析的结果,对模具进行优化和修改,确保模具设计满足产品要求,并且可以在冲压过程中保证产品的质量。
6. 生成工程图和模具零件图。
使用UG软件生成详细的工程图和模具零件图,包括模具的各个部件和尺寸。
这样可以为制造过程提供指导。
7. 制造模具。
根据工程图和模具零件图,进行模具的制造和加工。
模具通常由钢材制成,需要进行精密的加工和装配。
8. 进行冲压实验。
使用制成的模具,对样件进行冲压实验,测试模具的性能和产品质量。
根据实验结果,对模具进行再次优化和调整。
9. 修理和维护模具。
定期进行模具的维护和保养,以确保模具的使用寿命和性能。
修理时,需要使用UG软件进行分析和设计。
10. 模具的使用。
将制作好的模具用于批量生产汽车门锁芯,以满足市场需求。
以上是一个UG冲压模具设计的实例,其中涉及到了模型创建、模具设计、模拟分析、工程图生成、模具制造和冲压实验等环节。
实际的冲压模具设计过程中,可能还需要考虑材料、工艺和生产成本等因素,以确保模具设计的效果和经济性。
冲压模具设计实例讲解

冲压模具设计实例讲解1. 引言冲压模具是用于制作零部件的工具,广泛应用于汽车、电子、家电等行业。
本文将通过一个冲压模具设计实例,为读者介绍冲压模具设计的根本流程和本卷须知。
2. 设计背景我们以一款汽车车门为例,说明冲压模具的设计过程。
车门是汽车的重要部件之一,需要经过冲压加工来获得所需的形状和尺寸。
3. 设计流程3.1 确定产品要求在冲压模具设计之前,首先要明确产品的要求。
包括车门的尺寸、形状、材料以及制造工艺要求等。
3.2 制定模具设计方案根据产品要求,我们可以开始制定模具设计方案。
主要包括冲头、模座、模具顶板等部件的尺寸、形状和结构设计。
3.3 3D建模在制定模具设计方案后,我们可以使用CAD软件进行3D建模。
这样可以更直观地了解模具的结构、尺寸和装配关系。
3.4 模具加工制造根据3D模型,我们可以进一步进行模具零部件的加工制造。
主要包括数控加工、电火花加工、磨削等工艺。
3.5 模具装配和调试将加工好的模具零部件进行装配,并进行模具调试。
确保模具的各个部位协调运转,到达设计要求。
4. 冲压模具设计的本卷须知4.1 材料选择在冲压模具设计中,材料的选择非常重要。
一般情况下,应选用高强度、高韧性、耐磨损的材料,以保证模具的使用寿命和精度。
4.2 精度要求冲压模具对产品的精度要求很高,因此在设计过程中要考虑到产品的尺寸、形状等因素,并进行适宜的修正和优化。
4.3 加工工艺冲压模具的加工工艺对模具的质量和性能起着决定性的作用。
因此,在制造过程中要选择适宜的加工工艺,并确保加工精度和质量。
4.4 模具保养模具使用后需要定期进行保养和维护,以延长模具的使用寿命。
包括清洁、润滑、更换易损件等工作。
5. 总结冲压模具的设计过程需要考虑产品要求、制定设计方案、进行3D建模、加工制造、装配和调试等多个环节。
同时要注意材料选择、精度要求、加工工艺和模具保养等方面的问题。
通过本文的实例讲解,读者可以更深入地了解冲压模具设计的根本流程和本卷须知。
冲压模具设计和制造实例

冲压模具设计和制造实例冲压模具是指在金属板材冲压加工过程中使用的一种专业加工工具。
它是将板材经过模具的加工,使其按照设定的形状和尺寸进行变形或者分割的过程。
下面将为大家介绍一个冲压模具设计和制造的实例。
该实例是针对手机外壳的冲压模具设计和制造。
手机外壳是指手机整机的外部保护壳。
它起到保护手机内部电子元器件的作用,同时也是消费者对手机外观的第一印象。
因此,制造外观精美、质量可靠的手机外壳对手机制造商来说非常重要。
在这个实例中,冲压模具设计和制造的大致步骤如下:1.确定模具结构和尺寸:根据手机外壳的设计图纸,确定模具的结构和尺寸。
模具结构可以分为上模、下模和顶出模组成。
上模和下模通过导柱进行定位,保证模具的稳定性。
通过翻转上模和下模可以实现对外壳内外表面的冲压。
顶出模是用于排出冲压件的模块。
2.模具材料选择:根据冲压工件的材料和厚度,选择适合的模具材料。
常用的模具材料有工具钢和硬质合金。
工具钢具有良好的热处理性能和可磨削性,适合制造形状复杂的模具。
硬质合金具有高硬度和抗磨损性能,适合制造耐磨性能要求高的模具。
3.绘制模具零件图纸:根据模具结构和尺寸,绘制模具零件的图纸。
主要包括上模、下模、顶出模的轮廓形状和孔位等。
根据零件图纸可以制造模具的零件。
C加工模具零件:使用数控加工设备,根据模具的零件图纸进行加工。
零件加工包括铣削、钻孔和螺纹加工等。
通过CNC加工可以保证模具的精度和质量。
5.模具装配和调试:将加工好的模具零件进行装配和调试。
根据模具装配图纸进行模具组装,同时通过调试模具使其达到冲压工艺要求。
6.冲压试产:将手机外壳材料放入模具中,进行试产。
通过试产可以检验模具的设计和制造是否合理,以及工件的质量和尺寸是否符合要求。
如果不符合要求,需要进行修改和调整。
7.产品化生产:在通过冲压试产验证无误后,可以开始进行产品化生产。
根据市场需求和订单量,确定冲压模具的加工数量,进行批量生产。
通过以上的步骤,一个手机外壳的冲压模具设计和制造就完成了。
- 1、下载文档前请自行甄别文档内容的完整性,平台不提供额外的编辑、内容补充、找答案等附加服务。
- 2、"仅部分预览"的文档,不可在线预览部分如存在完整性等问题,可反馈申请退款(可完整预览的文档不适用该条件!)。
- 3、如文档侵犯您的权益,请联系客服反馈,我们会尽快为您处理(人工客服工作时间:9:00-18:30)。
冲压模具设计指导模具课程设计是一个重要的专业教学环节,这个数学环节的目的:ﻭ(1)帮助学生具体运用和巩固《模具设计与制造》课程及相关的理论知识,了解设计冲压模的一般程序。
(2)是使学生能够熟练地运用有关技术资料,如《冷冲模国家标准》、《模具设计与制造简明手册》、《冷冲压模具结构图册》及其它有关规范等。
ﻭ(3)训练学生初步设计冷冲压模具的能力,为以后的工作打下初步的基础。
ﻭ1 冲压模设计的准备工作根据课程设计目的,设计课题由指导教师用“设计任务书”的形式下达,课题难度以轻度复杂《如冲孔落料复合模》为宜。
设计工作量根据课程设计时间安排情况,由指导教师酌定。
ﻭ1.1 研究设计任务ﻭﻭ学生应充分研究设计任务书,了解产品用途,并进行冲压件的工艺性及尺寸公差等级分析,对于一些冲压件结构不合理或工艺性不好的,必须征询指导教师的意见后进行改进。
在初步明确设计要求的基础上,可按以下步骤进行冲压总体方案的论证。
ﻭﻭ第一步,酝酿冲压工序安排的初步方案,并画出各步的冲压工序草图;第二步,通过工序安排计算及《冷冲压模具结构图册》等技术资料,验证各步的冲压成型方案是否可行,构画该道工序的模具结构草图。
第三步,构画其它模具的结构草图,进一步推敲上述冲压工序安排方案是否合理可行。
ﻭ第四步,冲压工序安排方案经指导教师过目后,即可正式绘制各步的冲压工序图,并着手按照“设计任务书”上的要求进行课程设计。
1.2资料及工具准备ﻭ课程设计开始前必须预先准备好《冷冲模国家标准》、《模具设计与制造简明手册》、《冷冲压模具结构图册》等技术资料,及图板、图纸、绘图仪器等工具。
也可将课程设计全部或部分工作安排在计算机上用Auto CAD等软件来完成,相应地需事前调试设备及软件、准备好打印用纸及墨盒等材料。
ﻭ1.3设计步骤ﻭﻭ冲压模课程设计按以下几个步骤进行。
ﻭ(1)拟定冲压工序安排方案、画出冲压工序图、画出待设计模具的排样图(阶段考核比例为15%)(2)计算冲裁力、确定模具压力中心、计算凹模周界、确定待设计模具的有关结构要素、选用模具典型组合等,初选压力机吨位(25%);ﻭ(3)确定压力机吨位(5%);ﻭ(4)设计及绘制模具装配图(25%);ﻭ(5)设计及绘制模具零件图(25%);(6)按规定格式编制设计说明书(5%);(7)课程设计面批后或答辩(建议对总成绩在10%的范围内适度调整)。
ﻭ1.4 明确考核要求ﻭﻭ根据以上6个阶段应该形成的阶段设计成果实施各阶段的质量及考核,从而形成各阶段的考核成绩。
其中课程设计面批或答辩不仅有助与当面指出学生的各类设计错例,也是课程设计考核的重要手段。
最终的考核成绩在6个阶段考核成绩的基础上,由指导教师结合考勤记录及面2冲裁模结构批或答辩记录对总成绩在10%左右的范围内适度调整。
ﻭﻭ设计示范ﻭﻭ2.1排样论证的基本思路ﻭ排样论证的目的是为了画出正确的模具排样图。
一个较佳的排样方案必须兼顾冲压件的公差等级、冲压件的生产批量、模具结构和材料利用率等方面的因素。
ﻭ1) 保证冲压件的尺寸精度ﻭﻭ图1所示冲压件,材料为10钢板,料厚1mm,其未注公差尺寸精度等级为IT12,属一般冲裁模能达到的公差等级,不需采用精冲或整修等特殊冲裁方式。
从该冲压件的形状来看,完全可以实现少、无废料排样法。
但该冲压件的尺度精度等级决定了应采用有废料排样法。
ﻭ图1冲压件及排样图2)考虑冲压件的生产批量ﻭﻭ该冲压件的月生产批量为3000件,属于中等批量的生产类型,因此不考虑多排、或一模多件的方案(该方案较适宜大批量生产,约几十万件以上);也不考虑采用简易冲裁模常用的单、直排方案,根据成批生产的特点,再结合该冲压的形状特点,以单斜排、一模一件、3)提高原材料利用率ﻭﻭ在绘制排样图的过程中,级进排样方案为宜。
ﻭﻭ应注意提高冲压原材料的利用率。
但提高原材料的利用率,不能以大幅提高冲裁模结构的复杂程度为代价。
图2所示是垫圈冲压件及其冲裁排样图。
如果单纯为了提高原材料的利用率而采用三排或三排以上、一模多件的冲载方案,虽然确实有助于提高原材料的利用率,但模具制造成本却随之大幅提高,其结果往往得不偿失。
ﻭﻭ排样图上搭边值设计是否合理,直接影响到原材料的利用率和模具制造的难易程度。
总是采用最小许用搭边值[amin]、[a 1min]往往人为地提高了模具的制造难度,而在通常情况下却并不能提高原材料的利用率。
以一条长1000mm的料条为例,若对图2所示的垫圈冲压件以[amin]=0.8mm进行排样,可排(1000-0.8)/(34+0.8)=28.7个,实际为28个;若以a=1.5mm进行排样,则可排(1000-1.5)/(34+1.5)=28.1个。
可见每个步距上省下0.7mm长的料,最终整张条料上并不能多排一个工件,两者的利用率是完全相同的。
除使用卷料进行冲压外,一般搭边值均应在[amin]的基础上圆整(料宽尺寸也须圆整),以降低模具制造难度。
ﻭ图2垫圈冲压件及冲裁排样图4) 模具结构论证在保证产品尺寸公差等级的前提下,应尽量简化模具结构复杂程度,降低模具制造费用,这是设计模具的铁则。
图2所示的垫圈冲压件,因外形比较简单,且壁厚较大,所以采用复合模冲裁排样方案就比采用级进模冲裁的方案好。
ﻭ倒装复合模的结构比顺装复合模简单,所以应优先考虑采用倒装复合模。
最终能否采用复合模冲裁方案以及采用何种复合模结构的关键是验算冲压件的最小壁厚。
经验算垫圈冲压件的最小壁厚,可用倒装复合模冲裁方案。
2.2选择压力机及确定压力中心示范ﻭ根据图2复合模冲裁排样图,经计算模具工艺总力P∑=10.32(tf),可初步选择J23-16F压力机。
记录有关技术参数供今后校核用。
最大封闭高度:205mm;封闭高度调节量:45mm;工作台尺寸前后:300mm、左右:450mm;垫板尺寸厚度:40mm;孔径:Φ210mm;模柄孔尺寸直径:Φ40mm;模柄孔深度:60mm。
ﻭ计算压力中心的方法教材上已有详尽的介绍。
要计算出压力中心的精确位置既繁锁又无必要。
除了少数几种情况,例如:精密冲裁模具、多工位自动级进模和一些造价昂贵的模具为保险起见需要精确计算外,一般情况下,可以根据对称原理把压力中心大致定在条料宽向的中心线和送料方向上最远的两个凸模(有侧刃时,侧刃也算作凸模)距离的中线的交合点”O”上,只要这个0点与实际压力中心之间的偏距小于模柄半径(已知模柄直径为Φ40mm),就能达到模具平稳工作要求;而一旦0点与实际压力中心之间的偏距超出模柄半径的范围,就要调整各凹模洞口在凹模板上的位置,使实际压力中心进入模柄半径范围内。
ﻭﻭ2.3冷冲模国家标准的使用ﻭﻭ根据图2复合模冲裁排样图,结合模具制造工艺,圆形模板比矩形模板加工简便,因此本模具就采用圆形模板。
首先要计算圆形凹模板的轮廓尺寸:厚度H=K·b1=0.4×38=15.2mm;直径D=L1+2l1=34+2×22=78mm。
查阅GB2858.4-81,根据”就近就高”的原则初定凹模周界:H×D=16×Φ80。
ﻭ1. 确定模具的主要结构要素根据垫圈产品图排样方案论证结果,已确定本模具采用倒装式复合模结构。
在此基础上,尚须确定如下结构要素。
ﻭ(1) 确定送料方式ﻭ模具相对于模架是采用从前往后的纵向送料方式,还是采用从右往左的横向送料方式,这主要取决于凹模的周界尺寸。
如L(送料方向的凹模长度)<B(垂直于送料方向的凹模宽度)时,采用纵向送料方式;L>B时,则采用横向送料方式;L=B时,纵向或横向均可。
就本例的圆形凹模板而言,其送料方式应采用纵向送料。
另外采用何种送料方式,还得考虑压力机本身是开式还是闭式而定。
(2)确定卸料形式ﻭ模具是采用弹压卸料板,还是采用固定卸料板,取决于卸料力的大小,其中材料料厚是主要考虑因素。
由于弹压卸料模具操作时比固定卸料模具方便,操作者可以看见条料在模具中的送进动作,且弹压卸料板卸料时对条料施加的是柔性力,不会损伤工件表面,因此实际设计中尽量采弹压卸料板,而只有在弹压卸料板卸料力不足时,才改用固定卸料板。
随着模具用弹性元件弹力的增强(如采用矩形弹簧),弹压卸料板的卸料力大大增强。
根据目前情况,当材料料厚约在2mm以下时采用弹压卸料板,大于2mm时采用固定卸料板较为贴近实际。
本模具所冲材料的料厚为1mm,因此可采用弹压卸料板。
(3)模架形式ﻭ如采用纵向送料方式,适宜采用中间导柱导套模架(对角导柱导套模架也可);横向送料适宜采用对角导柱导套模架:而后侧导柱导套模架有利于送料(纵横向均可且送料较顺畅),但工作时受力均衡性和对称性比中间导柱导套模架及对角导柱导套模架差一些;四角导柱导套模架则常用于大型模具;而精密模具还须采用滚珠导柱导套。
本模具采用中间导柱导套模架,一是对纵2. 向送料方式较适宜,二是中间导柱导套模架工作时受力比较均衡、对称。
ﻭﻭ典型组合选择示范计算凹模周界及确定模具的主要结构是为了选用合适的模具结构典型组合。
根据本模具采用纵向送料方式、弹压卸料板、倒装复合模、中间导柱导套模架及凹模周界为H×D=16×Ф80,可从《冷冲模国家标准》查到复合模圆形厚凹模典型组合(GB2873.3-81)。
各模具零件的标准外形尺寸H×D如下:ﻭ(1)上垫板(GB2858.6-81)4×Ф801块; ﻭ(2)固定板(GB2858.5-81) 12×Ф801块;ﻭ(3)凹模(GB2858.4-81) (22×Ф80)调整至18×Ф80 1块; ﻭ(4)卸料板(GB2858.5-81) 10×Ф80 1块;(5)固定板(GB2858.5-81) 14×Ф80 1块;(6)下垫板(GB2858.6-81)4×Ф801块;ﻭﻭ本典型组合推荐使用3只M8的紧固螺钉、2只Ф8的圆柱销、3只杆部直径为Ф8的台肩式卸料螺钉、凸凹模的推荐长度为42mm、配用模架闭合高度在140~165mm之间。
ﻭﻭ有了模具结构的典型图,模具设计就大为简化。
只要根据排样图中凸模或凸凹模的位置,分别把各个凸模或凸凹模画入典型组合可,并相应地在凹模板或凸凹模上开制相应的凹模洞口及在其它零件上画出漏料孔、打料系统等,就可得到一张完整又正确的装配图。
3. 非标准模具的对照设计ﻭﻭ有些矩形凹模板根据计算结果会很难选到一个合适的标准凹模板。
例如某狭长冲压件,其凹模周界的计算值:H×L×B=20×60×125,与之最为接近的标准凹模板尺寸为:H×L×B=20×125×125,仍相差悬殊。
解决的办法是根据H×L×B=20×125×125的标准凹模板找到模具的典型组合,同样根据该典型组合构画装配图,只是把模具内的所有模板的L尺寸全部换成非标准尺寸60mm,而尺寸H及B保持不变,进行必要的有限非标准设计。