数控技术论文中英文摘要
数控话题英语作文

数控话题英语作文As a major topic in the field of manufacturing, numerical control (NC) technology has played a criticalrole in modern industry. It has greatly improved the efficiency and accuracy of production processes, and has become an indispensable tool in the manufacturing industry. In this essay, I will discuss the significance of numerical control technology, its development and application, andits future prospects.First and foremost, numerical control technology has significantly improved the efficiency and precision of manufacturing processes. By using computer-aided design (CAD) and computer-aided manufacturing (CAM) systems, manufacturers are able to program machines to perform complex tasks with a high degree of accuracy. This has led to a reduction in production time and costs, as well as an increase in the quality of manufactured products. In addition, numerical control technology has enabled the automation of many manufacturing processes, leading to increased productivity and reduced labor costs.Furthermore, the development of numerical control technology has had a profound impact on various industries, including aerospace, automotive, and electronics. In the aerospace industry, for example, numerical control technology has enabled the production of complex and lightweight parts for aircraft and spacecraft. In the automotive industry, it has facilitated the mass production of vehicles with consistent quality and precision. In the electronics industry, numerical control technology has been used to manufacture intricate components for electronic devices. Overall, numerical control technology has revolutionized the way products are designed and manufactured, and has contributed to the advancement of various industries.Looking ahead, the future of numerical control technology is promising. With the rapid advancement of computer technology and the Internet of Things (IoT), numerical control systems are becoming more intelligent and interconnected. This has led to the development of smart factories, where machines and processes are connected and can communicate with each other in real time. This level of connectivity and intelligence will further improve theefficiency and flexibility of manufacturing processes, and will enable the production of highly customized and personalized products. Additionally, the integration of artificial intelligence and machine learning into numerical control systems will further enhance their capabilities, allowing for autonomous decision making and adaptive manufacturing processes.In conclusion, numerical control technology has greatly impacted the manufacturing industry, leading to increased productivity, efficiency, and precision. Its development and application have transformed various industries and have paved the way for the future of manufacturing. With the continuous advancement of technology, numerical control systems will continue to play a crucial role in the evolution of manufacturing processes and the production of high-quality products.数控技术作为制造业的重要话题,在现代工业中发挥着至关重要的作用。
数控技术专业英文介绍范文
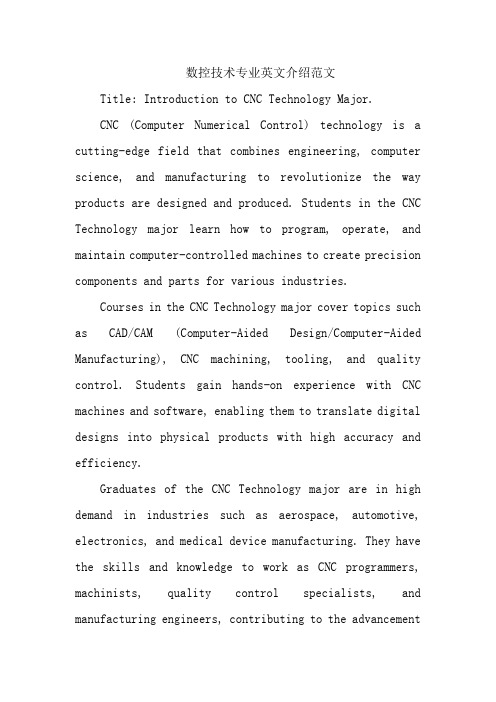
数控技术专业英文介绍范文Title: Introduction to CNC Technology Major.CNC (Computer Numerical Control) technology is a cutting-edge field that combines engineering, computer science, and manufacturing to revolutionize the way products are designed and produced. Students in the CNC Technology major learn how to program, operate, and maintain computer-controlled machines to create precision components and parts for various industries.Courses in the CNC Technology major cover topics such as CAD/CAM (Computer-Aided Design/Computer-Aided Manufacturing), CNC machining, tooling, and quality control. Students gain hands-on experience with CNC machines and software, enabling them to translate digital designs into physical products with high accuracy and efficiency.Graduates of the CNC Technology major are in high demand in industries such as aerospace, automotive, electronics, and medical device manufacturing. They have the skills and knowledge to work as CNC programmers, machinists, quality control specialists, and manufacturing engineers, contributing to the advancementof technology and innovation in manufacturing processes.By studying CNC Technology, students not only acquire technical skills but also develop problem-solving abilities, critical thinking, and attention to detail. This major prepares individuals for exciting and rewarding careers in the fast-paced world of advanced manufacturing.标题:数控技术专业介绍。
有关数控的英文作文

有关数控的英文作文1. CNC technology has revolutionized the manufacturing industry, allowing for precise and efficient production of complex parts and components.2. The use of computer-controlled machines has significantly reduced the need for manual labor in the production process, leading to increased productivity and cost savings for manufacturers.3. CNC machines are capable of performing a wide range of tasks, from cutting and drilling to milling and shaping, with high levels of accuracy and consistency.4. The programming of CNC machines requires specialized skills and knowledge, as operators must understand the machine's capabilities and limitations in order to create effective programs.5. One of the key advantages of CNC technology is itsability to produce identical parts with minimal variation, ensuring that products meet strict quality standards.6. The flexibility of CNC machines allows for rapid reconfiguration and retooling, making it easier for manufacturers to adapt to changing production requirements and market demands.7. As CNC technology continues to advance, the potential for automation and integration with other manufacturing processes is becoming increasingly feasible, leading to even greater levels of efficiency and productivity.。
数控专业的英语作文带翻译

English is the primary language for scientific and technological information exchange. By improving your English writing skills, you can access the latest technological developments, research findings, and industry trends, which will enhance your professional knowledge and expertise in numerical control.
Numerical Control Major English Writing with Translation
With the rapid development of manufacturing industry, the demand for numerical control professionals with proficient English skills is increasing. As a numerical control major student, it is essential to master professional English writing, which will benefit your future career development. In this article, we will discuss the importance of English writing for numerical control majors and provide useful tips and examples to improve English writing skills in this field.
数控技术外文文献翻译

数控技术外文文献翻译(含:英文原文及中文译文)英文原文The development trend of numerical control technology AbstractThe current trends in the development of numerical control technology and equipment in the world and the status quo of the development and industrialization of CNC equipment technology in China are briefly introduced. On this basis, we discuss the development of CNC technology and equipment in China under the new environment of China's accession to the WTO and further opening to the outside world. The importance of improving the level of China's manufacturing informatization and international competitiveness, and put forward some views on the development of China's CNC technology and equipment from both strategic and strategic aspects.The technological level and degree of modernization of the equipment industry determine the level of the entire national economy and the degree of modernization. Numerical control technology and equipment are the development of emerging high-tech industries and cutting-edge industries (such as information technology and its industries, biotechnology and its industries, aviation, aerospace, etc.) (Defense Industry Industry) enabling technology and basic equipment. Marx oncesaid that “the difference between various economic times is no t what is produced but how it is produced and what labor data it is used to produce”. Manufacturing technology and equipment are the most basic production materials for human production activities, and numerical control technology is the core technology of today's advanced manufacturing technologies and equipment. In the manufacturing industry of the world today, CNC technology is widely used to improve manufacturing capabilities and levels, and to improve the adaptability and competitiveness of dynamic markets. In addition, various industrialized countries in the world have also listed numerical control technology and numerical control equipment as strategic materials of the country. They not only take significant measures to develop their own numerical control technologies and their industries, but also have the key technology and equipment of “high-precision” numerical control. Our country adopts a policy of blockade and restriction. In short, the vigorous development of advanced manufacturing technologies centered on numerical control technology has become an important way for all developed countries in the world to accelerate economic development and improve their overall national strength and national status.Numerical control technology is a technology that uses digital information to control mechanical movement and work process. Numerical control equipment is a mechatronic product formed by thepenetration of new technologies represented by numerical control technology into traditional manufacturing industries and emerging manufacturing industries, namely, so-called digital equipment. Its technical scope covers many fields: (1) machinery manufacturing technology; (2) information processing, processing, and transmission technology; (3) automatic control technology; (4) servo drive technology;(5) sensor technology; (6) software Technology and so on. Keywords: CNC technology, machinery manufacturing, information processing, sensors1 Development Trends of Numerical Control TechnologyThe application of numerical control technology has not only brought about revolutionary changes in the traditional manufacturing industry, but also made manufacturing a symbol of industrialization. With the continuous development of numerical control technology and the expansion of application fields, he has made important contributions to the national economy and people's livelihood (IT, automotive The development of light industry, light industry, medical care, etc. is playing an increasingly important role, because the digitalization of the equipment required by these industries is a major trend of modern development. From the current trend of numerical control technology and its equipment development in the world, its main research hotspots are the following aspects [1~4].1.1 New trends in high-speed, high-precision processing technology and equipmentEfficiency and quality are the mainstays of advanced manufacturing technology. High-speed, high-precision machining technology can greatly improve efficiency, improve product quality and grade, shorten production cycle and increase market competitiveness. To this end, the Japanese Advanced Technology Research Institute will list it as one of the five major modern manufacturing technologies. The International Association of Production Engineers (CIRP) has identified it as one of the central research directions for the 21st century.In the passenger car industry, the production cycle of 300,000 vehicles per year is 40 seconds per vehicle, and multi-species processing is one of the key issues that must be addressed for car equipment. In the aviation and aerospace industries, the parts processed by them are mostly thin-walled. With thin ribs, the rigidity is poor, and the material is aluminum or aluminum alloy. These ribs and walls can be processed only when the high cutting speed and cutting force are small. Recently, the method of “hollowing out” large-size aluminum alloy billets has been used to manufacture large parts such as wings and fuselage to replace multiple parts and assembled by numerous rivets, screws, and other coupling methods to obtain strength, stiffness, and reliability of components. improve. All of these require high-speed, high-precision andhigh-flexibility for processing equipment.From the standpoint of EMO2001, the feed rate of high-speed machining centers can reach 80m/min, or even higher, and the airspeed can reach around 100m/min. At present, many automobile plants in the world, including China's Shanghai General Motors Corporation, have adopted a part of the production line consisting of a high-speed machining center to replace the combined machine tools. The HyperMach machine tool feed rate of CINCINNATI, USA is up to 60m/min, the speed is 100m/min, the acceleration is 2g, and the spindle speed has reached 60,000r/min. It takes only 30 minutes to machine a thin-walled aircraft part, and the same part takes 3h for general high-speed milling and 8h for normal milling; the spindle speed and acceleration of the twin-spindle lathe of DMG, Germany, reach 12*!000r/mm respectively. And 1g.In terms of machining accuracy, in the past 10 years, the machining accuracy of ordinary CNC machine tools has increased from 10μm to 5μm, precision machining centers have increased from 3~5μm to 1~1.5μm, and ultra-precision machining precision has begun to enter the nanometer level. (0.01μm).In terms of reliability, the MTBF value of foreign numerical control devices has reached more than 6000 hours, and the MTBF value of the servo system has reached more than 30,000 hours, showing very highreliability.In order to achieve high-speed, high-precision machining, the supporting functional components such as electric spindles and linear motors have been rapidly developed and the application fields have been further expanded.1.2 Rapid development of 5-axis simultaneous machining and compound machiningThe use of 5-axis simultaneous machining of 3D surface parts allows cutting with the best geometry of the tool, resulting in not only a high degree of finish, but also a significant increase in efficiency. It is generally considered that the efficiency of a 5-axis machine tool can be equal to 2 3-axis linkage machines. Especially when using ultra-hard material milling tools such as cubic boron nitride for high-speed milling of hardened steel parts, 5-axis simultaneous machining can be compared with 3-axis linkage. Processing to play a higher efficiency. In the past, due to the complexity of the 5-axis linkage CNC system and the host machine structure, the price was several times higher than that of the 3-axis linkage CNC machine tool, and the programming technology was more difficult, which restricted the development of 5-axis linkage machine tools.At present, due to the emergence of electric spindles, the structure of the composite spindle head that realizes 5-axis simultaneous machining isgreatly simplified, its manufacturing difficulty and cost are greatly reduced, and the price gap of the numerical control system is reduced. As a result, the development of composite spindle head type 5-axis linkage machine tools and compound machine tools (including 5-sided machine tools) has been promoted.At the EMO2001 exhibition, the new 5-axis machine tool of Nippon Machine Tool Co., Ltd. adopts a compound spindle head, which can realize the processing of four vertical planes and processing at any angle, so that 5-sided machining and 5-axis machining can be realized on the same machine tool. It can realize the processing of inclined surface and inverted cone. Germany DMG company exhibited DMUV oution series machining center, which can be processed in five-face machining and five-axis linkage in a single clamping. It can be directly or indirectly controlled by CNC system control or CAD/CAM.1.3 Intelligentization, openness, and networking have become major trends in the development of modern digital control systemsThe 21st century CNC equipment will be a certain intelligent system. The intelligent content is included in all aspects of the CNC system: in order to pursue the processing efficiency and processing quality in the intelligent, such as the process of adaptive control, process parameters automatically Generated; To improve the driving performance and the use of convenient connection intelligent, such as feed-forward control,adaptive calculation of motor parameters, automatic identification load automatic selection model, self-tuning, etc.; simplify the programming, simplify the operation of intelligent, such as smart The automatic programming, intelligent man-machine interface, etc.; as well as the contents of intelligent diagnosis, intelligent monitoring, convenient system diagnosis and maintenance.In order to solve the problems of traditional CNC system closure and industrial application of CNC application software. At present, many countries have conducted research on open numerical control systems such as NGC of the United States, OSACA of the European Community, OSEC of Japan, and ONC of China. The openness of numerical control systems has become the future of CNC systems. The so-called open CNC system is the development of CNC system can be in a unified operating platform, for machine tool manufacturers and end users, by changing, adding or cutting structure objects (CNC function), to form a series, and can be convenient to the user's special The application and technology are integrated into the control system to quickly realize open numerical control systems of different varieties and different grades to form brand-name products with distinctive personality. At present, the architecture specification, communication specification, configuration specification, operation platform, numerical control system function library and numerical control system function software development toolof open CNC system are the core of current research.Networked CNC equipment is a new bright spot in the international well-known machine tool exposition in the past two years. The networking of CNC equipment will greatly satisfy the requirements of information integration for production lines, manufacturing systems, and manufacturing companies. It is also the basic unit for realizing new manufacturing models such as agile manufacturing, virtual enterprise, and global manufacturing. Some famous domestic and foreign CNC machine tools and numerical control system manufacturing companies have introduced relevant new concepts and prototypes in the past two years. For example, at the EMO 2001 exhibition, the “Cyber Production Center” exhibited by Japan's Mazak company Mazak Production Control Center (CPC); Okuma Machine Too l Company, Japan exhibited “ITplaza” (Information Technology Plaza, IT Plaza); Open Manufacturing Environment (Open Manufacturing Environment, OME), exhibited by Siemens, Germany Etc., reflecting the trend of the development of CNC machine tools to the direction of the network.1.4 Emphasizing the Establishment of New Technology Standards and Specifications1.4.1 About Design and Development of CNC SystemsAs mentioned above, the open CNC system has better versatility, flexibility, adaptability, and expandability. The United States, theEuropean Community, and Japan have implemented strategic development plans one after another, and have conducted the open architecture system specification (OMAC). , OSACA, OSEC) research and development, the world's three largest economies in the short term carried out almost the same set of scientific plans and norms, indicating that the arrival of a new revolution in digital technology. In 2000, China began to conduct research and development of the regulatory framework for China's ONC numerical control system.1.4.2 About CNC StandardsCNC standards are a trend in the development of manufacturing informatization. The information exchange in the 50 years since the birth of CNC technology was based on the ISO 6983 standard. That is how the G and M codes describe how to process. The essential feature is the processing-oriented process. Obviously, he has been unable to meet the high speed of modern CNC technology. The need for development. For this purpose, a new CNC system standard ISO14649 (STEP-NC) is being researched and developed internationally. Its purpose is to provide a uniform data model that can describe the entire life cycle of a product without relying on a neutral mechanism of a specific system. , in order to achieve the entire manufacturing process, and even the standardization of product information in various industrial fields. The emergence of STEP-NC may be a revolution in CNC technology. It will have aprofound impact on the development of CNC technology and even the entire manufacturing industry. First, STEP-NC proposes a brand-new manufacturing concept. In the traditional manufacturing concept, NC machining programs are concentrated on a single computer. Under the new standard, NC programs can be distributed on the Internet. This is the direction of open and networked CNC technology. Secondly, STEP-NC CNC system can also greatly reduce the processing drawings (about 75%), processing program preparation time (about 35%) and processing time (about 50%).At present, European and American countries attach great importance to the research of STEP-NC, and Europe has initiated STEP-NC's IMS plan ( Participation in this program comes from 20 CAD/CAM/CAPP/CNC users, vendors and academic institutions in Europe and Japan. STEPTools of the United States is the developer of global manufacturing data exchange software. He has developed a SuperModel for the information exchange of CNC machine tools. Its goal is to describe all machining processes with a unified specification. This new data exchange format has now been validated on prototype prototypes equipped with SIEMENS, FIDIA and European OSACA-NC numerical control systems.2 Basic Estimates of China's CNC Technology and Its Industrial DevelopmentCNC technology in China started in 1958. The development process in the past 50 years can be roughly divided into three stages: the first stage from 1958 to 1979, which is the closed development stage. At this stage, the development of numerical control technology is relatively slow due to the limitations of foreign technology and China's basic conditions. The second stage is the introduction of technology during the “sixth and fifth” periods of the country, the “seventh five-year plan” period, and the “eighth five-year plan period,”and it will be digested and absorbed to initially establish the stage of the national production system. At this stage, due to the reform and opening up and the country’s attention, as well as the improvement of the research and development environment an d the international environment, China’s CNC technology has made great progress in research, development, and localization of products. The third stage is the implementation of industrialization research in the later period of the "Eighth Five-Year Plan" and the "Ninth Five-Year Plan" period of the country, entering the stage of market competition. At this stage, the industrialization of domestically-manufactured CNC equipment has achieved its essenceSexual progress. At the end of the “Ninth Five-Year Plan” period, the domestic market share of domestic CNC machine tools reached 50%, and the number of domestically-manufactured numerical control systems (pervasive models) also reached 10%.Looking at the development process of CNC technology in China in the past 50 years, especially after four five-year plans, the overall results are as follows:a. It lays the foundation for the development of CNC technology and basically masters modern CNC technology. China has now basically mastered the basic technologies from numerical control systems, servo drives, numerical control mainframes, special planes and their accessories. Most of these technologies already have the basis for commercial development. Some technologies have been commercialized and industrialized.b. Initially formed a CNC industrial base. Based on the research results and the commercialization of some technologies, we have established numerical control system production plants such as Huazhong Numerical Control and Aerospace Numerical Control which have mass production capabilities. Lanzhou Electric Machinery Factory, Huazhong Numerical Control and a number of servo systems and servo motor manufacturers, as well as a number of CNC machine manufacturers such as Beijing No. 1 Machine Tool Plant and Jinan No. 1 Machine Tool Plant. These production plants have basically formed China's CNC industrial base.c. Established a basic team of CNC research, development and management talents.Although significant progress has been made in the research, development, and industrialization of numerical control technology, we must also soberly realize that the research and development of high-end numerical control technologies in China, especially the status quo of the technological level of industrialization and the actual needs of China There is a big gap. Although our country's development speed is very fast in the vertical direction, the horizontal ratio (compared with foreign countries) not only has a gap in the level of technology, but also has a gap in the development speed in certain aspects, that is, the gap in the technological level of some highly sophisticated numerical control equipment has expanded. From the international point of view, the estimated level of China's numerical control technology and industrialization is roughly as follows:a. On the technical level, it will be about 10 to 15 years behind the advanced level in foreign countries, and it will be even bigger in terms of sophisticated technology.b. At the industrialization level, the market share is low, the variety coverage is small, and scale production has not yet been established; the specialized production level of functional components and the complete set capacity are low; the appearance quality is relatively poor; the reliability is not high, and the degree of commercialization is insufficient; The domestic CNC system has not established its own brand effect, andthe user's confidence is insufficient.c. On the ability of sustainable development, the research and development and engineering capabilities of pre-competitive numerical control technology are weak; the application of numerical control technology is not strong; the research and formulation of related standard specifications is lagging behind.The main reasons for analyzing the above gaps are as follows:a. Awareness. Insufficient understanding of the arduous, complex and long-term characteristics of the domestic CNC industry process; Insufficient estimates of market irregularities, foreign blockades, killings, and systems; and insufficient analysis of the application level and capabilities of CNC technology in China.b. Systematic aspects. From the point of view of technology, attention has been paid to the issue of CNC industrialization. It has been a time to consider the issue of CNC industrialization from the perspectives of system and industry chain; there is no complete supporting system of high-quality supporting systems, perfect training, and service networks. .c. Mechanisms. Bad mechanisms have led to brain drain, which in turn has restricted technological and technological route innovations and product innovations, and has constrained the effective implementation of planning. It is often planned to be ideal and difficult to implement.d. Technical aspects. Enterprises have little ability to independentlyinnovate in technology, and the engineering ability of core technologies is not strong. The standard of machine tools is backward, the level is low, and the new standard of CNC system is not enough.3 Strategic Thinking on the Development of CNC Technology and Industrialization in China3.1 Strategic ConsiderationsChina is a manufacturing country, and we must try to accept the transfer of the front-end rather than the back-end in the industrial transfer of the world. That is to master the advanced manufacturing core technologies, otherwise, in the new round of international industrial restructuring, China's manufacturing industry will further “empty core”. At the expense of resources, the environment, and the market, we may obtain only the international "processing centers" and "assembly centers" in the world's new economic structure, rather than the status of manufacturing centers that master core technologies. This will seriously affect our country. The development of modern manufacturing.We should pay attention to numerical control technology and industrial issues from the perspective of national security strategy. First of all, we must look at social security because manufacturing industry is the industry with the largest number of employed people in China. Manufacturing industry development can not only improve the people’s living standards, but also ease the country’s The pressure of employmentguarantees social stability. Secondly, from the perspective of national defense security, Western developed countries classify high-precision numerical control products as national strategic materials and implement embargoes and restrictions on China. The “Toshiba Incident” and the “Cox Report” "This is the best illustration.3.2 Development StrategyFrom the perspective of China’s basic national conditions, taking the country’s strategic needs and the market demand of the national economy as the guide, and aiming at improving the comprehensive competitiveness and industrialization le vel of China’s manufacturing equipment industry, we can use systematic methods to choose to dominate the early 21st century in China. The key technologies for the development and upgrade of the manufacturing equipment industry and supporting technologies and supporting technologies for supporting industrialization development are the contents of research and development and the leap-forward development of the manufacturing equipment industry. Emphasizing the market demand as the orientation, that is, taking CNC terminal products as the mainstay, and driving the CNC industry with complete machines (such as large-scale CNC lathes, milling machines, high-speed, high-precision and high-performance CNC machine tools, typical digital machines, key equipment of key industries, etc.). development of. The focus is on the reliability and production scale of CNC systems andrelated functional components (digital servos and motors, high-speed spindle systems and accessories for new equipment, etc.). Without scale, there will be no high-reliability products; without scale, there will be no cheap and competitive products; of course, CNC equipment without scale in China will be difficult to come to the fore. In the research and development of high-precision equipment, we must emphasize the close integration of production, learning, research, and end-users, and aim at “doing, using, and selling off” as a goal, and implement national research on the will of the country to solve the urgent need of the country. . Before the competition, CNC technology emphasizes innovation, emphasizes research and development of technologies and products with independent intellectual property rights, and lays a foundation for the sustainable development of China's CNC industry, equipment manufacturing industry, and even the entire manufacturing industry.中文译文数控技术的发展趋势摘要本文简要介绍了当今世界数控技术及装备发展的趋势及我国数控装备技术发展和产业化的现状, 在此基础上讨论了在我国加入WTO 和对外开放进一步深化的新环境下, 发展我国数控技术及装备、提高我国制造业信息化水平和国际竞争能力的重要性, 并从战略和策略两个层面提出了发展我国数控技术及装备的几点看法。
关于数控技术的英语作文

关于数控技术的英语作文英文回答:Computer Numerical Control (CNC) Technology.Computer numerical control (CNC) technology is a method of automated machining that uses a computer to control the movement of a machine tool. This allows for precise and repeatable movements, which are essential for many manufacturing processes.CNC machines are used in a wide variety of industries, including aerospace, automotive, and medical. They are capable of producing complex parts with tight tolerances. CNC machines can also be used to automate repetitive tasks, which can save time and money.There are two main types of CNC machines:Open-loop CNC machines use a computer to generate thecommands that control the machine tool. However, the computer does not receive any feedback from the machine tool, so it cannot correct for errors.Closed-loop CNC machines use a computer to generate the commands that control the machine tool, and they also receive feedback from the machine tool. This allows the computer to correct for errors, which results in greater accuracy and precision.CNC machines are a powerful tool that can be used to produce complex parts with tight tolerances. They are also capable of automating repetitive tasks, which can save time and money.中文回答:数控技术。
数控技术专业英文介绍范文

数控技术专业英文介绍范文English: The CNC technology major is designed to train students in the principles and practical skills of computer numerical control (CNC) machining. Students will learn how to use computer programs to control and operate machines such as lathes, milling machines, and grinders to produce precision parts and components. They will also study topics such as machining strategies, tooling selection, blueprint reading, and quality control. In addition to hands-on experience in CNC programming and machine operation, students will also receive training in CAD/CAM software, CNC equipment maintenance, and troubleshooting techniques. Graduates of this program will be well-equipped to pursue careers in industries such as aerospace, automotive, medical device manufacturing, and more, where precision machining is essential for producing high-quality products.中文翻译: 数控技术专业旨在培养学生掌握计算机数控(CNC)加工的原理和实践技能。
数控论文带英文版

数控论文带英文版第一篇:数控论文带英文版Development and maintenance of CNC1946 On the birth of the world's first electronic computer, which indicates that human beings created to enhance and replace the mental part of the tool.It is human in the agricultural, industrial society created a tool that is enhanced compared to manual qualitative leap, he entered the information society for human foundation.Half a century, and the core of computer-driven information technology, both through the TV, modern communications, improve the quality of human life, but also improve productivity fast forward, creating a history of human civilization, the production history of the era.The rapid development of information technology led directly to the arrival of the knowledge economy.In 1952, computer technology applied to the machine.Born in the United States first CNC machine puters and control technology in the application of machinery equipment manufacturing industry within the century's most significant technological advances.Since then, the conventional machine produced a qualitative change.Nearly half a century, has undergone two phases of CNC machine tools and the development of six generations.(1)Numerical control(NC)phase(1952-1970 years) early computing speed is low, which was affected scientific computing and data processing is not large, can not meet the requirements of real-time control machine tools.People have used digital logic circuits, “ride” into a dedicated computer as numerical control machine tool system, known as the hardware connection NC(HARD WIREDNC), referred to as NC(NC).With thedevelopment of components, at this stage after three generations, that in 1952 the first generationthe transistor;1965, the third generationpresent)In 1970, GM has a small computer and into mass production there.Its operation faster than the fifties and sixties have increased significantly, more than a special “ride” into a dedicated computer, low cost, high reliability.So it came as a CNC porting the core components, entered a computer numerical control(CNC)stage.By 1971, INTEL Corporation in the United States the world's first computer of the two core componentsthe microprocessor;1990, the sixth generationBASED).CNC system nearly five decades gone through two stages six generation of development, but development to the fifth generation only after a fundamental solution to the reliability is low, the price is extremely expensive, extremely convenient application is very critical issue.Thus, even in industrialized countries, large-scale numerical control system has been applied and popularity in the late seventies early eighties after the thing, that is numerical control technology after nearly three decades of development before wider application to.Abroad has been renamed as early as the computer numerical control(ie CNC), while China is still often called numerical control(NC).So we talk about everyday, “NC” in essence is that “computer numerical control” of C machine tool numerical control system is the core component, therefore, the maintenance of CNC machine tool numerical control system is mainly to maintain.After a NC system for a longer period of use, performance of electronic components to aging or damaged, and some mechanical parts especially, to try to extend the lifetime of components and parts wear cycle, to prevent all kinds of failures, particularly fatal accidents theoccurrence of the numerical control system must be routine maintenance.T o sum up, pay attention to the following aspects.1 NC system maintenance formulate rulesRegulations according to the characteristics of various components to determine their maintenance regulations.Expressly provided, such as what areas need cleaning every day(such as CNC system input / output unit-optical reading machines for cleaning, inspection is well-oiled machine structural parts, etc.), which parts should be regularly checked or replaced(such as brush DC servo motors and commutator should be checked once a month).(2)As less as possible open CNC ark and high voltage ark of the doorBecause in machining workshop in the air of general contain oil mist, dust and even metal powder.Once they fall within the NC system or electrical components on printed circuit, easily lead to decreased insulation resistance between components, and even lead to damage to components and printed circuits.Some users in the summer to make long-term work overload CNC system, CNC cabinet door open to heat, which is not desirable kind of approach will eventually lead to accelerated damage to the CNC system.The correct way is to reduce the numerical control system of the external ambient temperature.Therefore, there should be a strict requirement, unless the necessary adjustments and repairs, just open the doors is not allowed, but not allowed to open doors when in use.Regular cleaning the ark of the numerical control heat ventilation systemShould every day to check on the numerical control system each cooling fan is functioning properly, should inspect working environment condition, every half an year or quarterly review of a duct filter whether jam phenomenon.If excessive dust build-upInternet filter, the need for timely clean-up, otherwise it will cause the temperature inside the high numerical control system(generally not exceed 55 ℃), resulting in overheating or NC alarm system does not work reliably.4 CNC systems are often used to monitor voltage produced by FANUC CNC system, allowing the grid voltage rating of 85% to 110% of range fluctuations.If you exceed this range, it will cause the system not working properly, or even cause damage to electronic components within the NC system.5 periodic replacement of memory battery FANUC CNC production company within the system memory in two ways:(1)No batteries to keep the magnetic bubble memory.(2)the need to maintain the CMOS RAM with battery device is not powered on CNC system in order to maintain the contents of the storage period, with internal rechargeable battery to maintain the circuit, in the NC system is powered by the +5 V power supply through a diode to the CMOS RAM power, and can charge the rechargeable battery;cut off power when the numerical control system is replaced by a battery to maintain the information in CMOS RAM, under normal circumstances, even if the battery has not yet expired, the battery should be replaced once a year, in order to ensure that the system can work properly.In addition, we must note that the battery replacement should be carried out under the NC system power C long-term maintenance when not in numerical order to improve system utilization and reduce the numerical control system failure, CNC machine tools should be used at full capacity, and not long idle, for some reason, resulting in long idle CNC system, in order to numerical control system to avoid damage, please note the following two points:(1)should always power to the CNC system, especially in high humidity environment of therainy season and even more so, lock the machine does not move in the case(that is, the servo motor does not turn time), let dry run CNC e of electrical components to disperse their heat moisture within the NC system, to ensure stable and reliable performance of electronic devices, proved in the air humidity areas, power is to reduce the failure rate is often an effective measure.(2)CNC machine tool feed servo drives using DC and DC servo spindle drive, brush should be removed from the DC motor, so as not due to chemical corrosion, the commutator surface corrosion, resulting in change to the performance deterioration, and even entire motor damage.At present, the field of sheet metal stamping, CNC punching machine / CNC turret punch press with its fast, high precision machining, mold versatile, flexible products, etc., are widely er in choosing a quality mold, its use and maintenance of the level of direct impact to the workpiece machining quality and mold life.Mold control equipment is also an important part of operating costs.First,ensure the best mold clearanceMould clearance is to point to the punch into the next model, the sum of the clearance between the sides.It and thickness, material and the stamping process and suitable mould clearance, can guarantee good punching quality, reduce burr and collapse and keep the sheet metal level off, effectively prevent take material, prolong die life.Through the examination of stamping waste, we can determine whether appropriate mould clearance.If too much clearance waste will be rough rolling fractures and smaller light face.The greater the clearance, fractures and light the viewpoint of the formation of surface and the more they can form punching edge and fracture, appear even a thin rim bumps.Conversely, if the clearance is too small, waste will besmall Angle fractures and larger light face.When slot, step blunt, cutting local stamping, lateral force will make the punch deflection and cause unilateral gap is too small, sometimes edge migration will scratch lower die, causing the lower die quickly wear.Mould to best clearance stamping, waste of fractures and bright surface with the same Angle, and overlap each other, so that can make the cutting force minimum, punching the burr was very small.Second, timely grinding can effectively extend the life of the mold if too large of a workpiece or stamping burrs generated when abnormal noise may die passivation.Check the punch and the die, when its blade edges have a radius of approximately 0.10mm wear arc, it is necessary sharpening of.Practice has shown that frequent small amounts of sharpening rather than waiting until non-grinding mill can not be again when, not only to maintain good quality of the workpiece, reducing the blanking force, but die life can be extended more than doubled.In addition to knowing when to die grinding, the grinding master the correct method is especially important.Mold grinding procedure is as follows:1)grinding, it will punch a vertical grip on the surface grinder's magnetic chuck or fixture within the V-groove, each grinding capacity of 0.03 ~ 0.05mm, repeat until the punch grinding sharp, the maximum amount of grinding is generally 0.1 ~ 0.3mm.2)the use of sintered aluminum oxide grinding wheel, the hardness D ~ J, grit sizes 46 to 60, preferably for high-speed steel grinding wheel.3)When the grinding force or mold near the wheel, add coolant to prevent overheating and cracking the mold or annealing, should be required in accordance with the manufacturer of high quality multi-purpose coolant.4)The amount of feed wheel down 0.03 ~ 0.08 mm, lateral feed rate0.13 ~ 0.25 mm, lateral feed rate 2.5 ~ 3.8m/min.5)After grinding, oil stone polished edge, remove the burr, and grind the radius of 0.03 ~ 0.05 mm round, to prevent edge cracking.6)punch to the magnetic treatment and sprayed with oil to prevent rust.Third, the elimination and reduction of adhesive material way because when the pressure and heat stamping, sheet metal fine particles will bond to the surface of the punch, resulting in poor quality punching.Removal of binder used fine whetstone grinding, sanding should be directed to the direction of movement with the same punch, so the light will avoid the generation of further binder.Do not use gauze and other coarse grinding, to avoid the punch surface is more rough and more prone to sticky material.Reasonable die clearance, good stamping process, and the necessary lubrication sheet, will reduce the production of sticky material.Prevent overheating, the general lubrication of the way, this will reduce the friction.If you can not waste lubricating or rebound occurs, may take the following approach: alternate punch than the same size turns punching,Can make its repeated in before use have long cooling time.Overheating will use all die.Through the programming control changing mould, the interrupt their long time of repetition of work, or reduce its pressing frequency.Four, blunt is when the deformation of sheet metal porous to prevent measuresIf in a rush on board a porous, due to the accumulation of shear stress plank cannot maintain level.Every time punching, around the hole material will down deformation, causing the surface appears on the sheet metal tensile stress, and under the surface have compressive stress.For a small amount of punching, and its effect is not obvious, but when punching quantity is increased, the pull, compressive stress somewhere inaccumulation, until materials.Eliminate such deformation of a method is: to every one KongChong cut, and then returns to the rest of the punching holes.So although also can produce stress, but easing in the same direction order stamping of stress at accumulation, also can make the two groups before and after the stress of offset each other holes, so as to prevent the deformation of sheet metal.Five, try to avoid cutting through the narrow strip materialWhen the used for cutting width of less than in the process of sheet metal sheet thickness, lateral force for and make the punch to bending deformation, make side of the gap is too small or wear is intensified, serious scratch when the mould, make fluctuation mode and damage.Suggestions don't step blunt width of less than 2.5 times the thickness of the narrow a sheet metal sheet.Cutting through the narrow strip material, sheet metal tend to turn into the mode of open, and not be completely cut off, and even wedge dies profile.If can't avoid the above situation, the proposed use output slabs supported the role of the punch fully guided mold.Six, the punch surface hardening and the applicable scopeAlthough heat treatment and surface coating can improve the punch surface properties, but is not the solution to the problems and prolong die life is pressing the general method.Generally speaking, the coating surface hardness and improve the punch that side lubricity improved, but in large tonnage, hard materials stamping, these advantages in about 1000 times after stamping and disappeared.According to the following circumstance can use surface hardening the punch: Blunt soft or sticky materials(such as aluminum);Blunt thin non-abrasive materials(such as glass epoxypieces);Blunt thin hard material(such as stainless steel);Frequent point blunt;Abnormal lubrication.Surface hardening usually adopts of titanium coating and seepage nitrogen, method, its surface hardening layer thickness for 12 ~ 60 μ m molecular structure, it is a part of the matrix punch, and not only is the coating.Surface hardening of the mould can press usually way further.Through the surface hardening will lower mould in the stainless steel plate wear behavior, but can not prolong its service life, and the appropriate and timely lubrication, according to procedures, burrs, is the effective way.Seven, CNC turret punch die a neutral is bad for the overhaulIf a punch mould to neutral is bad, cause mould fast passivation, workpiece machining quality is poor, can the following maintenance: Check the level of the machine tool, when necessary to adjust;Check and lubrication of model hole on the wheel and the direction key, if there is damage timely repair;Clean the next mould seat, so as to lower die accurate installation, check and its key or the keyway wear and, when necessary, to change;Use the special mandrel calibration mould location, such as a deviation adjust in time.The contents of the situation is usually concerned, in view of the press and the concrete types die specifications are different, the user should combine the actual to know and summarizing the experience, and displays the best use of the mould performance.数控的发展及设备维护浅谈1946年诞生了世界上第一台电子计算机,这表明人类创造了可增强和部分代替脑力劳动的工具。
- 1、下载文档前请自行甄别文档内容的完整性,平台不提供额外的编辑、内容补充、找答案等附加服务。
- 2、"仅部分预览"的文档,不可在线预览部分如存在完整性等问题,可反馈申请退款(可完整预览的文档不适用该条件!)。
- 3、如文档侵犯您的权益,请联系客服反馈,我们会尽快为您处理(人工客服工作时间:9:00-18:30)。
摘要
Abstract
数控技术是用数字信息对机械运动和工作过程进行控制的技术, 是现代化工业生产中的一门发展十分迅速的高新技术。
数控装备是以数控技术为代表的新技术, 应用于传统制造产业和新型制造业形成的机电一体化产业, 即所谓的数字化装备。
本文简要分析了数控机床高速化、高精度化、可靠性、工艺复合性和多轴化等发展趋势,并提出了我国数控机床发展中存在的一些问题。
Numerical control technology is the technology controlled to mechanical movement and work process with digital information. I t’s a very rapidly developing technology in modern industrial production. Numerical control equipment is the new technology represented by numerical control technology forms to the manufacture industry of the tradition and infiltration of the new developing manufacturing industry, namely the so-called digital equipment. This paper analyzes the development trend of numerical control machine tools of high-speed, high-accuracy, reliability, process complex and multi-axis, and presents some of the problems existing in the development of China’s numerical control machine tools.
关键词:精度材料市场竞争力
Keywords: accuracy material market competitive
I。