加氢精制再生催化剂的合理使用
废催化剂的处理与资源化

废催化剂的处理与资源化目前全世界石油炼制催化剂的年用量超过40万吨,其中裂化催化剂占86%左右。
在裂化催化中失活的催化剂多采用掩埋法进行处理。
由于废催化剂中含有一些有害的重金属,因此采用填埋法处理废催化剂会造成土壤污染,若填埋时不做防渗处理,这些废催化剂被雨水淋湿后,会使其中重金属如镍、锌等溶出,造成水环境污染。
而且废催化剂颗粒较小,一般粒径为20~80微米,易随风飞扬(如一个300万吨的炼油厂,每年向周围大气中排放的裂化催化剂近1000吨),增加空气中总悬浮颗粒的含量,污染大气环境,成为大气污染不可忽视的来源之一。
另外,制造这些催化剂需要耗用大量贵重金属、有色金属及其氧化物,废催化剂有用金属的含量并不低于矿石中相应金属的含量。
因此,从控制环境污染和合理利用资源两方面考虑,均应对其进行回收利用。
目前,日本、美国均已建立催化剂回收公司,如日本的三井公司等。
随着工业的发展,我国废催化剂的数量也逐年增加,其回收工作也引起了一定的重视。
一、废催化剂的再生催化剂在使用一段时间后,常因表面结焦积炭、中毒、载体破碎等原因失活。
河北科技大学通过对担载了少量稀土氧化物、颗粒较小的超稳Y型分子筛裂化催化剂失活原因的分析,提出了废催化剂如下再生处理流程:焙烧—酸浸—水洗—活化—干燥。
其中焙烧是烧去催化剂表面的积炭,恢复内孔;酸浸是除去镍、钒的重要步骤;水洗是将黏附在催化剂上的重金属可溶盐冲洗下来;活化是恢复催化剂的活性;干燥是去除水分。
实验结果表明,废催化剂再生后镍含量可去除73.8%,活性可恢复95.7%,催化剂表面得到明显的改善;再生后催化剂的性能达到平衡催化剂的要求,可以返回系统代替50%的新催化剂使用。
国外一些炼油厂已基本实现了废加氢精制催化剂的再生,通过物理化学方法,去除催化剂上的结焦,回收沉积金属,再对催化剂进行化学修饰,恢复其催化性能。
这种方法在国外已推行多年,取得了较好的效果,不仅避免了污染,同时也有较好的经济效益。
柴油加氢催化剂的再生及工业应用

柴油加氢催化剂的再生及工业应用张文吉(中国石化 镇海炼化分公司,浙江 宁波 315207)[摘要]通过对比某炼厂3.0 Mt/a 柴油加氢装置使用新剂和再生剂的运行情况,分析和评估了加氢精制催化剂和裂化改质催化剂的再生活性。
试验结果表明,加氢精制催化剂通过再生,催化剂的活性基本恢复,可以满足国Ⅵ排放标准的车用柴油生产需求;裂化剂F -50通过再生保留了部分裂化改质性能,石脑油收率可达6.50%,与设计值接近,适合柴油加氢装置的改质使用。
[关键词]柴油加氢;催化剂;再生;裂化改质[文章编号]1000-8144(2021)03-0264-04 [中图分类号]TE 624 [文献标志码]ARegeneration and industrial application of diesel hydrogenation catalystZhang Wenji(Sinopec Zhenhai Refining & Chemical Company ,Ningbo Zhejiang 315207,China )[Abstract ]The regeneration activities of hydrofining catalyst and cracking catalyst were analyzed and evaluated by comparing the operation of new catalyst and regeneration catalyst in a 3.0 Mt/a diesel hydrogenation unit of a refinery. The results show that the activity of the hydrofining catalyst is basically recovered after regeneration ,which can meet the diesel production requirements of national Ⅵ emission standard. The cracking agent F-50 retains part of the cracking and upgrading performance through regeneration ,and the naphtha yield can reach 6.50%,which is close to the design value ,so it is suitable for the upgrading of diesel hydrogenation unit.[Keywords ]diesel hydrogenation ;catalyst ;regeneration ;cracking upgradingDOI :10.3969/j.issn.1000-8144.2021.03.011[收稿日期]2020-10-21;[修改稿日期]2020-12-16。
加氢精制催化剂的制备及在石油化工中的应用

加氢精制催化剂的制备及在石油化工中的应用【摘要】目前,加氢精制催化剂在化工业是比较常用的催化剂,但其大多数为负载型催化剂。
负载型催化剂的活性在随着相关理论及制备技术的进步而日益提高。
但是,负载型催化剂也有自身的局限性,载体比表面积和孔体积是影响其有效活性的金属负载量的主要原因,因此催化剂活性的提高受到一定的约束。
非负载型催化剂的活性组分含量高,原因是其不用载体,它具有活性密度大,加氢脱硫、脱氮和芳烃饱和能力强的优点。
本文先对非负载型加氢精制催化剂的制备进行了分析,然后对非负载型加氢精制催化剂在石油化工中的应用进行了探讨。
【关键词】非负载型加氢精制催化剂石油化工制备应用活性分组的选择、活性组分的结合方式的状态决定了催化剂性能的好坏。
要使催化剂活性高,就必须有较大的比表面积和孔容以及适宜的孔径,活性组分的利用率与比表面积和孔容息息相关;适宜的孔径可以提高催化剂的反应活性,因为其可以提高反应物在催化剂中的扩散能力;催化剂的抗积碳能力依赖于高的比表面积和较大的孔容,这样可以使催化剂的寿命延长。
传统的负载型催化剂靠载体提供较大的表面积和孔容。
而制备非负载型催化剂的难点在于催化剂自身的高的比表面积、适宜的孔径和孔容。
1 非负载型加氢精制催化剂的制备与传统的负载型催化剂区别不大,氧化态非负载型加氢精制催化剂也是要预硫化的,其材料是钼酸铵、钨酸铵。
它的制作方法有沉淀法和固定相反应法两种,并且其制备工艺较简单,成本也比较低,在工业上已得到应用。
1.1 共沉淀法domokos等制备非负载催化剂的原理是通过过度金属组分盐溶液共沉淀,先配备一定量的混合溶液,这个溶液是可溶性钼酸盐(如钼酸铵)和镍盐(如硝酸镍)的混合体,然后对其进行加热,温度至80℃即可,而后用硝酸调节其ph值,调节到2.8即可,在得到澄清溶液的基础上,在该溶液里加入二氧化硅,与此同时,缓慢加入氨水溶液,使之ph值达到6.8,待溶液沉淀后,进行过滤和干燥,催化剂前提由此生成。
加氢催化剂再生
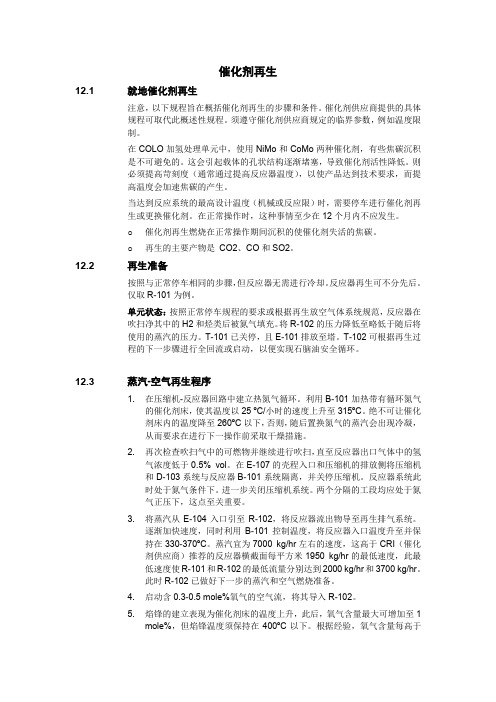
催化剂再生12.1 就地催化剂再生注意,以下规程旨在概括催化剂再生的步骤和条件。
催化剂供应商提供的具体规程可取代此概述性规程。
须遵守催化剂供应商规定的临界参数,例如温度限制。
在COLO加氢处理单元中,使用NiMo和CoMo两种催化剂,有些焦碳沉积是不可避免的。
这会引起载体的孔状结构逐渐堵塞,导致催化剂活性降低。
则必须提高苛刻度(通常通过提高反应器温度),以使产品达到技术要求,而提高温度会加速焦碳的产生。
当达到反应系统的最高设计温度(机械或反应限)时,需要停车进行催化剂再生或更换催化剂。
在正常操作时,这种事情至少在12个月内不应发生。
o催化剂再生燃烧在正常操作期间沉积的使催化剂失活的焦碳。
o再生的主要产物是CO2、CO和SO2。
12.2 再生准备按照与正常停车相同的步骤,但反应器无需进行冷却。
反应器再生可不分先后。
仅取R-101为例。
单元状态:按照正常停车规程的要求或根据再生放空气体系统规范,反应器在吹扫净其中的H2和烃类后被氮气填充。
将R-102的压力降低至略低于随后将使用的蒸汽的压力。
T-101已关停,且E-101排放至塔。
T-102可根据再生过程的下一步骤进行全回流或启动,以便实现石脑油安全循环。
12.3 蒸汽-空气再生程序1. 在压缩机-反应器回路中建立热氮气循环。
利用B-101加热带有循环氮气的催化剂床,使其温度以25 ºC/小时的速度上升至315ºC。
绝不可让催化剂床内的温度降至260ºC以下,否则,随后置换氮气的蒸汽会出现冷凝,从而要求在进行下一操作前采取干燥措施。
2. 再次检查吹扫气中的可燃物并继续进行吹扫,直至反应器出口气体中的氢气浓度低于0.5% vol。
在E-107的壳程入口和压缩机的排放侧将压缩机和D-103系统与反应器B-101系统隔离,并关停压缩机。
反应器系统此时处于氮气条件下。
进一步关闭压缩机系统。
两个分隔的工段均应处于氮气正压下,这点至关重要。
加氢精制催化剂及工艺技术精选全文

可编辑修改精选全文完整版加氢精制催化剂及工艺技术▪加氢精制技术应用概况▪加氢精制主要反应及模型化合物加氢反应历程主要反应模型化合物加氢反应历程典型工艺流程▪加氢精制工艺技术重整原料预加氢催化剂及工艺二次加工汽油加氢精制催化剂及工艺煤油加氢精制催化剂及工艺劣质二次加工柴油加氢精制催化剂及工艺进口高硫柴油加氢精制催化剂及工艺焦化全馏分油加氢精制催化剂及工艺石蜡加氢精制催化剂及技术▪加氢精制催化剂加氢精制技术应用概况抚顺石油化工研究院(FRIPP)是国内最早从事石油产品临氢催化技术开发的科研机构。
几十年来,FRIPP在轻质馏分油加氢精制、重质馏分油加氢处理、石油蜡类加氢精制、渣油加氢处理和临氢降凝等领域已开发成功5大类共30个品牌的商业催化剂,先后在国内45个厂家共115套加氢精制/加氢处理工业装置上应用,累计加工能力超过4000万吨/年。
FRIPP加氢精制技术开发的经历:•1950s 页岩油加氢技术•1960s 重整原料预精制技术•1970s 汽、煤、柴油加氢精制技术•1980s 石油蜡类加氢精制技术•1990s 重质馏分油加氢精制技术、渣油加氢处理技术FRIPP加氢精制系列催化剂:•轻质馏分油 481、481-3、FH-5、FH-5A、FDS-4、FDS-4A、FH-98•重质馏分油 3926、3936、CH-20、3996•柴油临氢降凝 FDW-1•石油蜡类 481-2、481-2B、FV-1•渣油 FZC-10系列、FZC-20系列、FZC-30系列、FZC-40系列、FZC-100系列、 FZC-200系列、FZC-300系列FRIPP加氢精制催化剂工业应用统计(1999年):加氢精制主要反应及模型化合物加氢反应历程加氢精制主要反应加氢精制主要反应为加氢脱硫、加氢脱氮、加氢脱氧、烯烃与芳烃的饱和加氢,以及加氢脱金属。
其典型反应如下:1、加氢脱硫2、加氢脱氮3、加氢脱氧4、烯烃加氢饱和5、芳烃加氢饱和6、加氢脱金属(1)沥青胶束的金属桥的断裂(详见图3)式中 R,R'--芳烃;M--金属钒。
加氢催化剂的分类、功能及选用
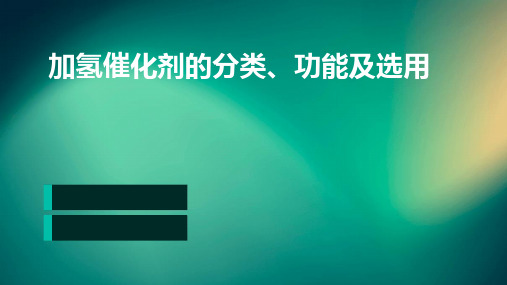
其他类型催化剂
金属有机框架(MOF)催化剂
具有多孔性、大比表面积和可调的孔径等特点,为加氢反应提供了更多的可能 性。
碳基催化剂
以碳材料为载体,通过引入活性组分制备的催化剂,在加氢反应中表现出良好 的活性和稳定性。
03 加氢催化剂功能
加速氢气活化与解离
降低氢气活化能
加氢催化剂能够降低氢气分子的活化能,使其更容易解离为氢原子,从而参与加 氢反应。
提高反应速率和选择性
提高反应速率
催化剂能够降低反应的活化能,从而 加快反应速率,提高生产效率。
提高反应选择性
通过选择合适的催化剂,可以使得目 标产物在反应中的选择性得到提高, 减少副产物的生成。
降低反应温度和压力
降低反应温度
催化剂可以降低反应的活化能,从而使得反应在较低的温度下就能进行,有利于节能和 减少副反应。
降低反应压力
某些加氢催化剂能够在较低的压力下促进加氢反应的进行,从而减少设备投资和操作成 本。
04 加氢催化剂选用原则
适应性原则
01
催化剂应与反应物和产物相容, 避免产生副反应或毒化催化剂。
02
催化剂应适应反应条件,如温度 、压力、氢气流速等,以确保催 化活性和选择性。
经济性原则
催化剂应具有较低的成本和较高的活 性,以降低加氢反应的成本。
作用
加氢催化剂在石油化工、有机合 成、精细化工等领域具有广泛的 应用,能够提高产品的收率和质 量,降低生产成本和能源消耗。
发展历程及现状
发展历程
自20世纪初发现加氢催化剂以来,随着科学技术的不断进步和工业生产的不断发展,加氢催化剂的种类和性能得 到了极大的丰富和提升。从最初的简单金属催化剂到后来的复合催化剂、分子筛催化剂等,加氢催化剂的研究和 应用不断取得新的突破。
催化剂级配技术在加氢精制装置上的工业应用
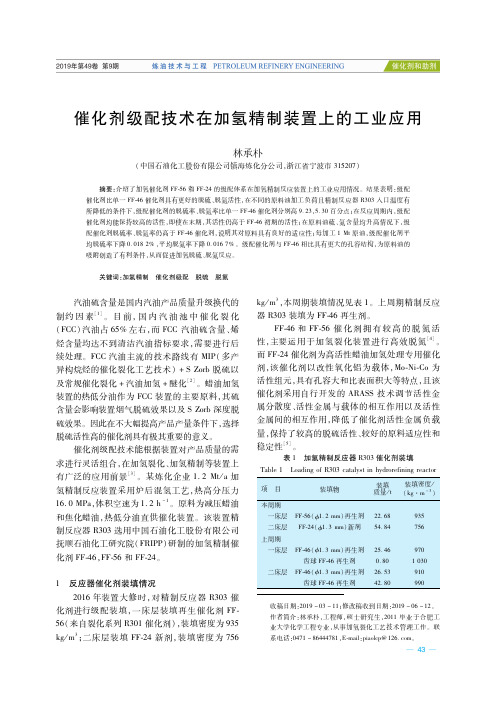
化剂进行级配装填,一床层装填再生催化剂 FF 56(来自裂化系列 R301催化剂),装填密度为 935 kg/m3;二床层装填 FF24新剂,装填密度为 756
kg/m3,本周期装填情况见表 1。上周期精制反应 器 R303装填为 FF46再生剂。
387 442 542 4.4 931.3 2.18
2086
0.85 471.1 322.4 80.3 359.7
1.01 460.4 322.5 91.0 365.4
1.10 411.8 325.9 84.4 364.1
139.8
407 465 554 3.6 936.9 2.33
2147
1.18 410.8 326.0 88.5 365.8
— 43—
2 催化剂初期生产情况
装置不同进料负荷下生产工况进行了对比。
为比较催化剂级配的效果,对大修开工后本 2.1 原料油性质及主要操作参数
周期(2016年 5月 3日—2016年 7月 5日)与上
不同进料负荷下精制原料油性质及主要操作
周期(2013年 10月 29日—2014年 11月 25日) 参数见表 2。
齿球 FF46再生剂
装填 装填密度 / 质量 /t (kg·m-3)
22.68 54.84
935 756
25.46 0.80 26.53 42.80
970 1030 910 990
收稿日期:2019-03-11;修改稿收到日期:2019-06-12。 作者简介:林承朴,工程师,硕士研究生,2011毕业于合肥工 业大学化学工程专业,从事加氢裂化工艺技术管理工作。联 系电话:0471-86444781,Email:piaolcp@126.com。
制氢原料精制催化剂选用及实际操作中的问题

制氢原料精制催化剂选用及实际操作中的问题摘要:本文通过对制氢原料气精制催化剂的化学性质及物理结构进行简介,从而界定其选用原则,并提醒大家在实际生产中的应用关键词:硫化物催化剂转化率中图分类号:p578.2 文献标识码:a 文章编号:前言制氢原料中的硫化物对其生产过程中所使用的一系列催化剂都有毒害作用,尤其对含镍的转化催化剂、甲烷化催化剂、含铜的低变催化剂和甲醇合成催化剂以及以铁为活性组份的氨合成催化剂都会造成毒害。
虽然一段炉允许最高质量分数在0.5×10-6下操作,但对其活性仍有一定的影响,一般要求硫质量分数小于0.1×10-6。
近十几年来迅速发展的以炼厂气(催化干气、焦化干气)为制氢(合成氨)的廉价原料,其气体组成主要为c1~c4的烷烃,也含有较多的烯烃和有机硫,烯烃含量一般在6%~20%,有机硫化物含量在200μg/g左右,硫的形态也较复杂。
因此,对于此类原料中的烯烃及有机硫,必须采用加氢转化催化剂将其烯烃转化为烷烃,有机硫转化为h2s之后,再通过氧化锌脱硫剂将原料中的总硫的质量分数降至0.1×10-6。
精制催化剂活性组份及物理结构化学组成及结构常用的有机硫加氢转化催化剂有co-mo系、ni-mo系、ni-co-mo 系等,最常用的是以al2o3为载体的co-mo系。
ni-mo系和ni-co-mo系则更适用于加氢气源中碳氧化物含量较高及烯烃含量较高时的加氢转化过程,在石油炼制中应用较为广泛。
fe-mo系适用于co体积分数小于8%,烯烃体积分数小于5%的焦炉气中有机硫的加氢转化过程。
co-mo- al2o3催化剂,又称“钼酸钴”催化剂,其组份大致可分为三类:一是无催化活性的al2o3和coal2o4;二是具有中等催化活性的coo、moo3、co-moo4;三是催化活性较高的co、mo氧化物的复合物。
这些氧化物中的一部分在操作过程中吸收硫化合物而被硫化,生成的硫化物继续保持加氢脱硫活性,并成为起主要催化作用的活性物质。
- 1、下载文档前请自行甄别文档内容的完整性,平台不提供额外的编辑、内容补充、找答案等附加服务。
- 2、"仅部分预览"的文档,不可在线预览部分如存在完整性等问题,可反馈申请退款(可完整预览的文档不适用该条件!)。
- 3、如文档侵犯您的权益,请联系客服反馈,我们会尽快为您处理(人工客服工作时间:9:00-18:30)。
加氢精制再生催化剂的合理使用摘要:简要讨论了加氢精制再生催化剂的特点,说明了再生催化剂降级使用的技术方案是完全可行的,并介绍了在再生催化剂装填和硫化过程中,与新鲜催化剂的差别,及应该注意的事项。
关键词:加氢精制再生催化剂合理使用前言石油馏分的加氢工艺技术是目前生产清洁燃料应用最广泛、最成熟的主要加工手段之一,在石油化工企业中所占的地位越来越重要。
近年来,随着炼油企业加氢精制工业装置加工量的逐渐增加,所使用加氢催化剂的品种越来越多,数量也越来越大,经过烧焦再生后继续使用的再生催化剂的品种和数量也越来越多。
目前,全世界约有18 kt/a加氢催化剂需要再生[1],而预计其中的加氢精制催化剂至少在10 kt/a以上。
因此,如何合理使用加氢精制再生剂,使之发挥更大的作用,提高炼油企业的经济效益变得越来越重要。
加氢精制催化剂经过1 个周期的运转,由于积炭等原因造成活性下降,必须经过烧焦再生处理后才能使催化剂的活性得到恢复,并继续使用。
在正常使用的情况下,加氢精制催化剂可以再生1~2 次,催化剂总寿命在6~9 a之间。
加氢精制再生催化剂的开工过程原则上与新鲜催化剂是一致的,但是也有一些不同之处。
这主要是因为:再生催化剂的物理性质,如比表面积、孔容积和机械强度等都发生了变化;再生剂的催化活性要比新鲜剂低一些;再生剂上残留的硫、炭和其它杂质,对开工中催化剂的硫化过程会产生一定的影响。
如果再生催化剂完全按新鲜催化剂的开工方法进行,将会造成开工成本提高,和因过量的硫化氢对设备腐蚀而造成的安全隐患,以及不能充分发挥催化剂的活性和稳定性,影响工业装置长周期安全稳定运转。
本文主要讨论了加氢精制催化剂再生剂的合理使用及开工工艺过程中应当注意的一些问题。
1 加氢精制再生催化剂的特点再生催化剂与新鲜催化剂相比,孔容积和比表面积都比新催化剂略有降低。
这主要是由于积炭和杂质沉积堵塞催化剂孔道,降低了孔容积和比表面积,使催化剂活性金属的利用率降低,造成再生后的催化剂活性有所下降。
表1列出了某柴油加氢精制催化剂新鲜剂与再生剂的理化性质。
表1 新鲜催化剂与再生剂的理化性质Table1 The physicochemical properties of fresh catalyst and regenerated catalyst催化剂再生剂新鲜剂孔容积/(mL•g-1) 0.46 0.48表面积/(m2•g-1) 218 226耐压强度/(N•cm-1) 172 168堆积密度/(g•cm-3) 0.90 0.88硫含量,% 0.58 -碳含量,% 0.22 - 由表1可以看出,再生催化剂的孔容积和表面积较新鲜催化剂要小;新催化剂上没有硫和碳,而再生催化剂上有0.58%的硫和0.22%的碳。
加氢催化剂的新剂与再生剂的物理化学性质是不同的。
因此,在使用过程中也应该有所差异。
2 加氢精制再生催化剂的降级使用2.1 再生催化剂降级使用的可行性有些催化剂经过再生后,活性仍然达不到使用要求,或者由于石油产品质量升级换代,再生后的催化剂活性不能满足炼油企业的需要,这些催化剂除了少部分低价出售给金属回收单位进行金属回收处理外,绝大多数催化剂被掩埋。
这样既对环境造成污染,也是对资源的浪费。
在大型炼油企业的运营成本中,催化剂的采购费用已占相当大的比例。
为了充分发挥再生催化剂的作用,可以将再生剂应用在加氢工艺条件比较缓和,对催化剂活性要求较低的加氢工业装置上,即再生剂的降级使用。
下面列出了国内某大型炼油企业柴油加氢催化剂的降级使用情况。
该催化剂已经累计使用了近6 a,在柴油加氢装置上的使用寿命已到了末期,催化剂的加氢活性不能满足柴油馏分产品质量的要求。
为了降低企业生产成本,提高催化剂利用率,最终决定将催化剂再生后应用在航煤加氢装置上,生产3#喷气燃料。
为此,以国外直馏煤油为原料进行了可行性试验。
采用该再生催化剂,在氢分压3.5 MPa、反应温度220/240 ℃、体积空速2.7 h-1、氢油体积比300等工艺条件下,进行了直馏航煤加氢脱硫醇的活性评价试验,结果见表2。
表2 再生剂活性评价结果Table2 The evoluation results of regenerated cata lyst项目数值工艺条件氢分压/MPa 3.5体积空速/h-1 2.7氢油体积比300反应温度/℃220 240油品性质煤油原料精制油硫含量/(μg•g-1) 1258 670 291脱硫率,% 46.7 76.9密度(20 ℃)/( g•cm-3)0.7876 0.7865 0.7862硫醇硫/(μg•g-1) 99.7 4.6 4.4博士试验不通过通过通过冰点/℃-61 -60 -60 由表2可见,采用该再生催化剂在氢分压3.5 MPa、体积空速2.7 h-1、反应温度220 ℃/240℃及氢油体积比300等比较缓和工艺条件下,精制煤油硫醇硫含量满足小于20 μg/g要求,其它性质均满足国标3#喷气燃料的指标要求,说明再生催化剂降级使用的技术方案是完全可行的。
2.2 再生催化剂降级使用的经济效益以加工量1.0 Mt/a的航煤加氢精制装置,使用35 t再生催化剂为例,可节省催化剂采购费用约668.5×104 RMB¥,经济效益显著。
3 加氢精制再生催化剂开工工艺3.1 催化剂的装填3.1.1 补充新鲜催化剂的装填新鲜催化剂经过1 个周期的运转并进行再生处理后,通常会有一定量的损失。
所以,一般需要补充1 部分新鲜催化剂,这部分新催化剂的装填位置应该慎重考虑。
如果装置处理的原料油为直馏馏分油或以直馏馏分油为主,应将新鲜催化剂装填在催化剂床层的下部。
这是因为直馏原料油虽然只含有较少量的烯烃和硫、氮化合物等杂质,加氢过程的温升较小,但新鲜催化剂的加氢活性较高,如果将其装在催化剂床层的上部,很容易造成新催化剂迅速结焦而失活。
新催化剂装填在床层下部时,原料油首先与活性较低的再生催化剂接触,然后再与活性较高的新催化剂接触,形成1 个催化活性由低到高的过渡过程,这对新鲜催化剂活性的充分发挥,以及装置的长周期稳定运转是比较有利的。
当加工的原料油是以2 次加工油为主时,由于含有较多的烯烃和硫、氮化合物等杂质,加氢反应温升较大,这时将新鲜催化剂装在床层下部就不合适了,应该将新催化剂与再生催化剂混合装填在催化剂床层的中部。
这是因为催化剂床层中部的温度接近平均反应温度,上部有催化活性较低的再生催化剂的过度性保护,也不会有因为床层下部反应温度过高而造成催化剂严重结焦的问题,可以更充分地发挥这部分新鲜催化剂的使用效率。
3.1.2 床层顶部再生催化剂的装填从反应器中将失活催化剂卸出、装桶和烧焦再生时,通常要求按照催化剂的上、中、下床层分开进行,以便对不同性状的催化剂分别处理。
必要时,可将顶床层催化剂用撇头的方法,从反应器顶部卸出,单独装桶和烧焦再生。
床层顶部的催化剂通常会沉积较多的杂质,通过烧焦再生的方法,通常难以恢复催化活性,因而与下部床层催化剂相比活性较低。
建议将这部分催化剂经过再生后仍然装填在催化剂床层的上部,这样可以对下部床层催化剂起到保护作用,又可以延缓顶部床层的结焦速度。
如果沉积的杂质含量和催化剂的耐压强度指标超过了规定的再生催化剂的要求,建议不要再继续使用这部分催化剂,应该补充部分新鲜催化剂,以防止由于催化剂活性太低和压力降上升过快造成非计划性停工。
3.2 再生催化剂的硫化3.2.1 新剂和再生剂的硫化再生催化剂的硫化与新催化剂的硫化方法是一致的,但应注意硫化剂的使用量与新催化剂有一定差别。
新催化剂所需硫化剂量比较容易确定,一般按催化剂理论需硫量的1.2~1.3 倍来准备,只要催化剂的总量确定,所需硫化剂量也就确定下来了。
而影响再生催化剂需硫量的因素较多,如果也按新鲜催化剂的方法来确定硫化剂量,会由于注硫量太多造成循环氢系统中硫化氢浓度过高,且持续偏高。
这样不但由于过多使用硫化剂而增加了开工成本,同时由于循环氢中过量硫化氢会腐蚀设备和管线,对装置的安全生产也造成了隐患。
表3为某种加氢精制催化剂硫化过程的要求。
表3 加氢精制催化剂硫化要求[2]T able3 the re que st during sulf ur ization of hy drofining cata ly st反应器入口温度/℃升温速度/(℃·h-1) 恒温参考时间/h 循环氢H2S含量,(v) %常温→15015~20 150 3 150→230 10~15 8 实测 230 - 8 0.3~0.8 230→290 10~15 5 实测 290 - 6 0.5~1.0 230→320 10~15 3 实测 320 6 0.5~1.0 3202 >1.0在加氢催化剂硫化过程中,按上表指标要求控制,可以达到较为满意的硫化效果。
根据实际生产目的不同,也可以进行适当的调整。
图1为某柴油加氢装置新催化剂和再生催化剂开工硫化时的循环氢中硫化氢浓度的变化曲线。
2 次开工所使用的硫化剂均是按新催化剂需要量准备的,硫化工艺过程也是一致的。
012345102030硫化时间,h循环氢中H 2S ,%图1 催化剂硫化时硫化氢含量变化曲线Fig.1 Change of H 2S content during sulfurization of catalyst由图1可以看出,当实际需硫量均按新催化剂需要量注入时,新催化剂硫化时,循环氢中硫化氢含量变化较平稳,可以稳定控制在理论范围之内;而再生剂硫化时,由于硫化过程中硫化剂注入量相对较多,循环氢中的硫化氢浓度始终较高,最高甚至达到4(v )%以上。
这对催化剂硫化效果没有明显提高,但是对设备管线的腐蚀是比较严重的,多余的硫化氢大多要送到硫磺回收系统或排到火炬烧掉,造成资源浪费,增加开工成本,产生的SOx 对大气也有一定的的污染。
3.2.2 再生催化剂硫化剂用量的确定首先计算出催化剂的理论需硫量。
按照下列化学反应方程式和该催化剂的总金属含量,可以计算出准确的理论需硫量。
[3]CS 2+4H 2=2H 2S +CH 4 C 2H 6S 2+3H 2=2H 2S +2CH 4 WO 3+2H 2S +H 2=WS 2+3H 2OMoO 3+2H 2S +H 2=MoS 2+3H 2O 3NiO +2H 2S +H 2=Ni 3S 2+3H 2O 9CoO+8H 2S +H 2=Co 9S 8+9H 2O 再生催化剂需硫量应首先考虑失活催化剂经过再生后仍然残存的少量硫和碳。
残留的硫主要与活性金属以硫酸盐的形式存在,这部分金属很难再与新注入的硫化剂所产生的硫化氢反应生成金属硫化物;残留的碳主要以积炭的形势覆盖在催化剂内表面的活性金属表面上,这也阻碍了硫化氢与活性金属的硫化反应。