加工误差统计分析实验指导
基于FlashActionScript机械加工误差统计分析实验的设计与开发

量堕 l 塞 堕塑呈 JI , l 仃 壅竺 I
数 据 处理
分 布 图
均 值 极 差 图
【竖 二 堡l 垄 塑[ ! 二 ■真 l
— —
l — 输入零件 数量 H 加工模拟 I I 输
— — —
验 进 行 了计 算 机 虚 拟 设 计 开 发 。通 过 系 统 产 生具 有 一 定 规 律 的 随 机 数 据 ,或 者 根 据 实 际 加 工 得 到
郭德 伟 ,江
洁 ,闵
.
洁 ,柯 建宏
G UO — i2 JANG i M I i KE J a . o g’ De we 1 l , Je N Je , in h n
(. 1 昆明理工大学 机 电工程学院 ,昆明 6 0 9 ;2 红河学院 工学院 ,蒙 自 6 1 0 ) 503 . 6 1 0
图 l 示 。 1 手 导航 模 块 ,主 要展 示 本 系统 软 所 )新
件 的操 作 环 境 及 使 用 方 法 ,各 界 面 及 相 关 按 钮 的
意 义 等 ; ) 验 指 导 模 块 ,主 要 介 绍 本 实 验 的基 2 实
本 原 理 、方 法 、操 作 步骤 、实 验 意 义 等 ,并 提 供
教 学 模 式 受 到 了 巨 大 的 挑 战 ,这 时 虚 拟 实 验 教 学
便 成 了一 个 不 错 的 选择 ,特 别 是 基 于 网络 的虚 拟 实验 。 目前 我 国 对教 学 虚拟 实验 的研 究 还缺 乏
加工误差统计分析实验指导

加工误差统计分析实验一、实验目的1、巩固已学过的统计分析法的基本理论;2、掌握运用统计分析法的步骤;3、学习使用统计分析法判断和解决问题的能力。
二、实验设备与仪器电感测量仪、块规、千分尺、试件(滚动轴承滚柱)、计算机。
三、实验原理和方法在机械加工中,应用数理统计方法对加工误差(或其他质量指标)进行分析,是进行过程控制的一种有效方法,也是实施全面质量管理的一个重要方面。
其基本原理是利用加工误差的统计特性,对测量数据进行处理,作出分布图和点图,据此对加工误差的性质、工序能力及工艺稳定性等进行识别和判断,进而对加工误差作出综合分析。
1、直方图和分布曲线绘制1)初选分组数k2找出样本数据的最大值X imax和最小值X imin,并按下式计算组距:式中:k——分组数,按表选取;X max和X min——本组样本数据的最大值和最小值。
选取与计算的d值相近的且为测量值尾数整倍数的数值为组距。
3)确定组界各组组界为:min (i1)d2dX+-± (i=1,2,…,k),为避免样本数据落在组界上,组界最好选在样本数据最后一位尾数的1/2处。
4)统计各组频数频数,即落在各组组界范围内的样本个数。
频率=频数/样本容量5)画直方图以样本数据值(被测工件尺寸)为横坐标,标出各组组界;以各组频数为纵坐标,画出直方图。
6)计算总体平均值与标准差平均值的计算公式为 11n i i X X n ==∑ 式中:X i ——第i 个样本的测量值;n ——样本容量。
标准差的计算公式为s =7)画分布曲线若研究的质量指标是尺寸误差,且工艺过程稳定,则误差分布曲线接近正态分布曲线;若研究的资料指标是形位误差或其他误差,则应根据实际情况确定其分布曲线。
画出分布曲线,注意使分布曲线与直方图协调一致。
8)画公差带按照与以上分布曲线相同的坐标原点,在横轴下方画出被测零件的公差带,以便与分布曲线相比较。
公差根据试件类型、规格查国标手册可得到。
K-《机械制造技术基础》实验指导书g

《机械制造技术基础》实验指导书康献民五邑大学机电系2007年9月印刷目录实验一刀具角度的测量 2 实验二金属切削变形观察7 实验三车床几何精度检测及调整10 实验四切削要素对表面加工质量的影响 20实验五切削力的测量24 实验六车床静刚度测试28 实验七加工误差的统计分析32实验一刀具角度的测量实验项目性质:验证性实验计划学时:2学时一、实验目的1.学习测量车刀几何角度的方法及仪器使用。
2.加深对车刀几何角度的定义和理解。
二、实验内容和要求1.使用车刀量角台,测量给定外圆车刀的前角Y。
、后角α0、主偏角Kr和副偏角Kr,并将测量结果记入实验报告;了解刃倾角λs定义和作用。
2.每人测三把车刀,外圆、螺纹和切断刀各一把。
⒊根据测量结果,绘制车刀简图,并回答问题。
三、仪器及工具车刀量角台;5种车刀模型四、车刀量角台结构介绍与测量方法l.量角台的主要测量参数及其范围车刀量角台能测量主剖面和法剖面内的前角、后角、主偏角、副偏角以及刃倾角。
测量范围:前角(Y。
):—30°~+40°;后角(α0):<30°;主偏角(Kr):≤90°;副偏角(Kr')≤90°;刃倾角(λs):±45°2. 车刀量角台的组成⑴车刀量角台主要由底座、立柱、刻度板、指针、标尺、滑板及紧固螺钉等组成(如图1),松开锁紧螺钉10,刻度板8可绕立柱4旋转,并可用螺母5,将其调整到任意高度。
指针9可绕其轴在刻度板8上转动,对淮零点时,互相垂直的A、B平面则分别平行和垂直于底座1的工作面(即滑板和底座的上平面)。
⑵松开锁紧螺钉3,标尺11与标尺座2可绕立柱4旋转,标尺座2上零线与底座之零点对准时,固定在滑板14上的二档销之中心线垂直于标尺11。
⑶松开锁紧螺钉12,刻度板8可绕其水平轴旋转,旋转度数由指针7在度板6上指出。
⑷忪开锁紧螺钉15,滑板14可在底座上作横向滑动,行程70mm。
机械制造技术基础-A-实验指导书
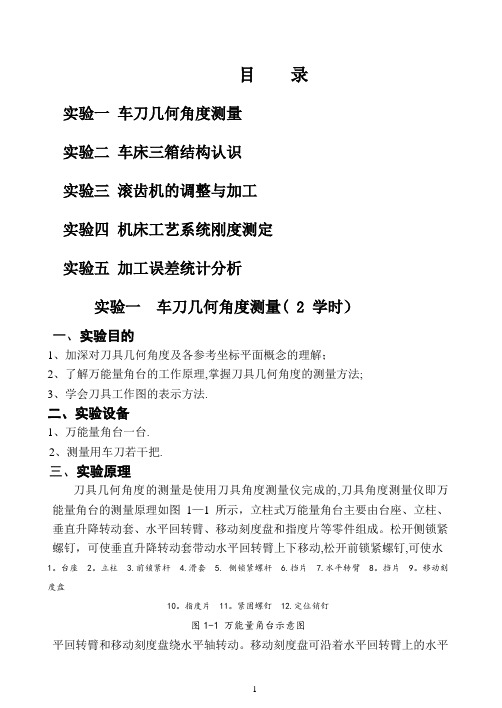
目录实验一车刀几何角度测量实验二车床三箱结构认识实验三滚齿机的调整与加工实验四机床工艺系统刚度测定实验五加工误差统计分析实验一车刀几何角度测量( 2 学时)一、实验目的1、加深对刀具几何角度及各参考坐标平面概念的理解;2、了解万能量角台的工作原理,掌握刀具几何角度的测量方法;3、学会刀具工作图的表示方法.二、实验设备1、万能量角台一台.2、测量用车刀若干把.三、实验原理刀具几何角度的测量是使用刀具角度测量仪完成的,刀具角度测量仪即万能量角台的测量原理如图1—1所示,立柱式万能量角台主要由台座、立柱、垂直升降转动套、水平回转臂、移动刻度盘和指度片等零件组成。
松开侧锁紧螺钉,可使垂直升降转动套带动水平回转臂上下移动,松开前锁紧螺钉,可使水1。
台座 2。
立柱 3.前锁紧杆 4.滑套 5. 侧锁紧螺杆 6.挡片 7.水平转臂 8。
挡片 9。
移动刻度盘10。
指度片 11。
紧固螺钉 12.定位销钉图1-1 万能量角台示意图平回转臂和移动刻度盘绕水平轴转动。
移动刻度盘可沿着水平回转臂上的水平槽水平移动,并根据测量需要紧固在某一确定位置。
指度片可绕螺钉销轴转动,其底部靠近被测量的表面,指针指示测量角度.用上述这些零件位置的变动,即可实现各参考平面内刀具角度的测量。
测量时,刀具放在台座上,以刀杆的一侧靠在两定位销内侧定位。
四、实验内容1)测量主偏角滑套上的“0”刻度对准立柱上的标定线,测量时只可上下移动,不得转动。
转动水平回转臂,使其上的“0”刻度线对准滑套上的标定线。
调整测量指度片,使指度片的底面与主切削刃重合,制度片的指针所指的角度为主偏角. 2)测量负偏角方法同上,只是让指度片的底面与副切削刃重合,指针所指读数为负偏角. 3)测量前角滑套上的“0”刻度对准立柱上的标定线后,再把滑套相对于标定线顺时针转动一个主偏角的余角,转动水平回转臂,使水平回转臂上的“90”刻度线对准滑套上的“90”刻度线,调整指度片,使指度片的底面与前刀面重合,制度片的指针所指的角度为。
加工误差的统计分析

(一)实验分布图
记录各组数据,整理成频数分布表(表4-5)
(一)实验分布图
根据表4-4所列数据画出直方图
(一)实验分布图
计算。 在直方图上作出最大极限尺寸Amax=60.06mm及最小极限尺寸Amin=60.01mm的标志线,并计算: =37.3μm; S =8.93μm。
(三)分布图分析法的应用
确定工序能力及其等级 (定义)工序能力:所谓工序能力是指工序处于稳定状态时,加工误差正常波动的幅度。当加工尺寸服从正态分布时,其尺寸分散范围是6σ,所以工序能力就是6σ。 (定义)工序能力系数:工序能力等级是以工序能力系数来表示的,它代表了工序能满足加工精度要求的程度。 当工序处于稳定状态度时,工序能力系数Cp按下式计算:
1.正态分布
可以看出,分布曲线的最大值与σ成反比。 当σ减小时,分布曲线向上伸展。由于分布曲线所围成的面积总是保持等于1,因此σ愈小,分布曲线两侧愈向中间收紧,分散范围越小。 σ是表征分布曲线形状的参数,亦即它刻划了随机变量X取值的分散程度。
1.正态分布
标准正态分布 总体平均值μ=0,总体标准差σ=1的正态分布称为标准正态分布。任何不同的μ和σ的正态分布都可以通过坐标变换 为标准的正态分布,故可以利用标准正态分布的函数值,求得各种正态分布的函数值。
一、加工误差性质
(定义)系统误差:在顺序加工一批工件中,其加工误差的大小和方向都保持不变,或者按一定规律变化,统称为系统误差。前者称常值系统误差,后者称变值系统误差。
常值系统误差 加工原理误差,机床、刀具、夹具和量具的制造误差、工艺系统的受力变形、机床、夹具、量具等磨损
变值系统误差 机床、刀具和夹具等在热平衡前的热变形误差,刀具的磨损等
切削实验指导书

车床静刚度测量一、实验目的1、熟悉车床静刚度的测定方法。
2、比较车床各部件刚度的大小,分析影响车床刚度的各种因素。
3、巩固和论证《机械制造工艺学》中有关系统刚度和误差复映规律的概念。
4、了解YDC-Ⅲ89型压电式车削侧力仪的工作原理、结构及使用方法。
二、实验条件为完成本实验,实验室提供如下实验条件:车床若干台,YDC-Ⅲ89型压电式车削侧力仪若干台,千分表若干只,百分表若干只,磁力表座若干只,游标卡尺若干把,千分尺若干把,以及刚性工件和工具若干。
三、实验要求1、实验前,请仔细阅读熟悉实验指导书,查找相关资料,弄清实验测量基本原理和测量方法,熟悉机床传动系统和操纵手柄的使用,最好还要明确分工。
2、自己选择实验仪器设备,设计实验方案和实验操作步骤,完成下列实验内容:⑴、用静止载荷法测量车床刚度并说明实验原理。
在0-1800N范围内,加力过程和减力过程的测力值均不应低于5个,即各部位的变形量记录在加力过程和减力过程中均不应低于5个。
⑵、用生产法测量车床的刚度,并说明实验原理。
⑶、分别设计静止载荷法测量车床刚度和生产法测量车床的刚度的实验方案。
⑷、分别制定静止载荷法测量车床刚度和生产法测量车床的刚度的实验操作步骤。
⑸、记录实验数据,分别计算用静止载荷法和生产法测量所得的床头、尾座、刀架和机床的刚度。
⑹、在同一坐标系上画出车床的床头、尾座和刀架各部位的刚度特性曲线图(包括加载和卸载)。
⑺、对实验结果进行分析。
四、主要实验仪器、设备简介㈠、车床车床的外形和传动系统操作参见车床空载功率测定中的介绍。
㈡、车削测力仪YDC-Ⅲ89型压电式三向车削测力仪力的测量仪器,既能够测量动态变化量,又能够测量静态变化量。
1测力仪的组成YDC-Ⅲ89型压电式三向车削测力仪由测力传感器、电荷放大器、接线盒、数据采集卡和计算机等5部分组成。
1、YDC-Ⅲ89型压电式车削侧力仪测力传感器结构YDC-III89型压电式三向车削测力仪的测力传感器是由一个带有弹性环的刀杆整体构件和一个装于其内的压电石英晶体三维力传感器构成,如图1所示,头部装有活动刀片,可以像普通车刀那样安装在刀架上车削工件。
机械制造工艺学实验指导书

《机械制造工艺学》实验指导书学院:机械工程与自动化学院所在系:机械工程系适用专业:机械设计制造及其自动化编写人:中北大学机械工程系2010年11月实验一:刚度实验一.实验目的1.了解机床(包括夹具)—工件—刀具所组成的工艺系统是一弹性系统;2.了解机床刚度对加工精度的影响;3.熟悉机床动刚度的测定方法;4.巩固和验证所学工艺系统刚度和误差复映的概念。
二.实验设备与仪器1.机床:普通车床, C620-1,Φ400⨯1000。
2.刀具:外圆车刀,硬质合金,角度 K r =45°,r 0=10°,λs =0°。
3.千分尺规格:(150~175mm ,175~200mm )。
4.毛坯材料:45号钢。
5.切削用量:主轴转速600转/分,进给量0.1mm/转,双边余量2.7mm 。
4.三盘刚度测定装置。
三.实验内容用动载荷测定法确定机床部件刚度。
四.实验原理设机床的刚性较差,刀具、工件刚度很大(变形忽略),根据课堂上讲述切削力作用点位置的变化对加工精度的影响所得出的公式,1111k k k k =++22尾系刀架主L-x x ()()L L得出111x=0k k k =+系1刀架主当时, (1) L 11111x=()24k k k k =++尾系2刀架主当时, (2)111x=L k k k =+尾系3刀架当时, (3) 联立以上三式,得111112(3)2k k k k =-++主系2系1系3 (4) 111112()2k k k k =-+刀架系2系1系3(5)111112(3)2k k k k =-++尾系2系1系3(6) 根据误差复映系数公式y1212k y p p F F a a ε-=-系, (7)根据切削原理 (8)式中:y zF F λ=——比例系数,与刀具几何形状、切削用量、刀具磨损等有关,一般来说0.3~0.5λ=,本实验取0.4λ=Z F C ——切削系数,与刀具几何参数及切削条件有关的系数,陶乾《金属切削原理》介绍214Z F C =8.9⨯。
实验四加工误差统计分析

实验四加工误差统计分析一、实验目的1 •通过实验使学生掌握用统计分析方法综合分析加工误差时所依据的基本理论、知识和方法。
2.加工一批工件,测量其加工尺寸,对测得的数据进行处理,用统计方法分析此工序的加工精度,要求绘制图形并进行分析。
二、实验属性本实验为综合性实验三、实验仪器及设备1 •实验测量件轴100件2.千分尺3.计算器四、实验要求1.实验前预习实验指导书,熟悉实验过程,制定实验方案。
2.认真测量、记录实验数据,计算、统计分析数据变化情况3.按照要求绘图分析。
4.按照实验报告要求完成实验报告。
五、实验原理在加工过程中,由于随机误差和系统误差的影响,使一批工件加工出来的尺寸各并相同。
通过测量一批工件的加工尺寸可画出频数直方分布图。
如果所取的工件数量较多,组距较小时,折线图就近似实际分布曲线。
在没有明显变值系统误差的情况下,工件的误差是由许多相互独立的微小随机误差所组成,则工件尺寸分布符合正态分布,如图3・1所示。
方程为:(X L)22 2式中X—工件的平均尺寸;均方根误差;x—工件尺寸。
工件尺寸可以近似被认为分布在X-3匚的范围内:工序的工艺能力系数为:式中T —图纸规定的工件的尺寸公差六、实验步骤1 •测量工件的加工尺寸,每个工件测量2次,记录测量结果2•绘制实验分布曲线,作图步骤:(1)找出这批工件加工尺寸的最大值Xnw(和最小值X“n ;(2)确定分组数K (建议K在7〜12之间)(3)计算组距d d二独仏(4)作出频数分布图;(5)计算X和SX(6)绘出实验分布图线(7)计算工序能力Cp , C P =-x) 心s十苫七、实验数据记录表八、实验数据处理・绘制点图(用坐标纸或用计算机编程来绘制)2・频数分布图3.绘制分布曲线九、思考题1・本工序点图说明什么问题?2・本工序的分布曲线图是否接近正态分布图?3•根据工序能力系数,确定本工序属于几级工序?。
- 1、下载文档前请自行甄别文档内容的完整性,平台不提供额外的编辑、内容补充、找答案等附加服务。
- 2、"仅部分预览"的文档,不可在线预览部分如存在完整性等问题,可反馈申请退款(可完整预览的文档不适用该条件!)。
- 3、如文档侵犯您的权益,请联系客服反馈,我们会尽快为您处理(人工客服工作时间:9:00-18:30)。
加工误差统计分析实验
一、实验目的
1、巩固已学过的统计分析法的基本理论;
2、掌握运用统计分析法的步骤;
3、学习使用统计分析法判断和解决问题的能力。
二、实验设备与仪器
电感测量仪、块规、千分尺、试件(滚动轴承滚柱)、计算机。
三、实验原理和方法
在机械加工中,应用数理统计方法对加工误差(或其他质量指标)进行分析,是进行过程控制的一种有效方法,也是实施全面质量管理的一个重要方面。
其基本原理是利用加工误差的统计特性,对测量数据进行处理,作出分布图和点图,据此对加工误差的性质、工序能力及工艺稳定性等进行识别和判断,进而对加工误差作出综合分析。
1、直方图和分布曲线绘制 1)初选分组数k
一般应根据样本容量来选择,参见下表。
2)确定组距d
找出样本数据的最大值X imax 和最小值X imin ,并按下式计算组距:
max min 11
X X R
d k k -=
=-- 式中:k ——分组数,按表选取;
X max 和X min ——本组样本数据的最大值和最小值。
选取与计算的d 值相近的且为测量值尾数整倍数的数值为组距。
3)确定组界
各组组界为:min (i 1)d 2
d
X +-± (i=1,2,…,k),为避免样本数据落在组界上,组界最好选在样本数据最后一位尾数的1/2处。
4)统计各组频数
频数,即落在各组组界范围内的样本个数。
频率=频数/样本容量 5)画直方图
以样本数据值(被测工件尺寸)为横坐标,标出各组组界;以各组频数为纵坐标,画出直方图。
6)计算总体平均值与标准差
平均值的计算公式为 1
1n
i i X X n ==∑
式中:X i ——第i 个样本的测量值; n ——样本容量。
标准差的计算公式为
s =7)画分布曲线
若研究的质量指标是尺寸误差,且工艺过程稳定,则误差分布曲线接近正态分布曲线;若研究的资料指标是形位误差或其他误差,则应根据实际情况确定其分布曲线。
画出分布曲线,注意使分布曲线与直方图协调一致。
8)画公差带
按照与以上分布曲线相同的坐标原点,在横轴下方画出被测零件的公差带,以便与分布曲线相比较。
公差根据试件类型、规格查国标手册可得到。
2、X -R 图绘制
1)确定样组容量,对样本进行分组
样组容量一般取m=2~10件,通常取4或5,即对试件尺寸依次按每4~5个一组进行分组,将样本划分成若干个样组。
2)计算各样组的平均值和极差
对于第i 个样组,其平均值和极差计算公式为
1
1m
i ij j X X m ==∑, max min i i i R X X =-
式中:i X ——第i 个样组的平均值; i R ——第i 个样组的标准差;
ij X ——第i 个样组第j 个试样的测量值; max i X ——第i 个样组数据的最大值;
min i X ——第i 个样组数据的最小值。
3)计算X -R 图的控制线
X -R 图的控制线为
样组平均值X 图的中线 1
1
m
k i i m
X X k ==
∑ 样组平均值R 图的中线 11m
k i i m R R k ==∑ 样组平均值X 图的上控制线 2U X X A R =+ 样组平均值R 图的上控制线 1U R D R = 样组平均值X 图的下控制线 2L X X A R =- 样组平均值R 图的下控制线 2L R D R = 式中:A 2、D 1、D 2——常数,见下表; k m ——样组个数。
4)绘制X -R 图
以组序号为横坐标,分别以各样组的平均值X 和极差R 为纵坐标,画出X -R 图,并在图上标出中线和上、下控制线。
3、工序能力系数计算
工序能力系数P C 按下式计算:=
6P T C σ(或P C P
δ=) 根据工艺能力系数P C 的大小,可将工艺分成5个等级。
(1) 1.67P C >,为特级,说明工艺能力过高,不一定经济。
(2)1.67 1.33P C ≥>,为一级,说明工艺能力足够,可以允许一定的波动。
(3)1.33 1.00P C ≥>,为二级,说明工艺能力勉强,必须密切注意。
(4)1.000.67P C ≥>,为三级,说明工艺能力不足,可能会出现少量不合格品。
(5)0.67P C ≤,为四级,说明工艺能力不行,必须加以改进。
一般情况下,工艺能力不应低于二级。
4、判别工艺过程稳定性
所谓工艺过程的稳定,从数理统计的原理来说,一个过程(工序)的质量参数的总体分布,其平均值
X 和均方根差σ在整个过程(工序)中若能保持不变,则工艺过程是最稳定的。
在点图上作出平均线和控制线后,就可按下表所列出的标准进行判断。
注意,同时满足表中左列3个条件,工艺过程稳定;表中右列条件之一不满足,即表示工艺过程不稳定。
四、实验步骤 1.对试件进行编号;
2.按试件的基本尺寸选用块规; 3.调校电感测量仪;
4.在电感测量仪上按序号顺次测量试件的外径,为保证测量的准确性和可靠性可在其上测量三个点,取其平均值,把结果填入表中。
5.清理实验现场,收拾所用仪器、量具、工具等。
6.整理实验数据,绘图。
五、思考题
(1)分布图主要说明什么问题?(2)X -R 图主要说明什么问题?
(3)分析产生加工误差的主要因素有哪些?(4)分析工艺过程稳定(或不稳定)的原因。