石油天然气钢质管道无损检测最终版
SYT 0086-2003 石油天然气钢质管道无损检测
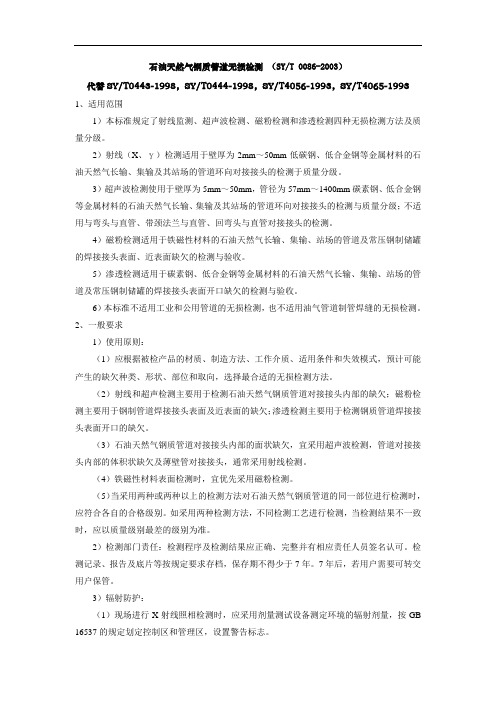
石油天然气钢质管道无损检测(SY/T 0086-2003)代替SY/T0443-1998,SY/T0444-1998,SY/T4056-1993,SY/T4065-19931、适用范围1)本标准规定了射线监测、超声波检测、磁粉检测和渗透检测四种无损检测方法及质量分级。
2)射线(X、γ)检测适用于壁厚为2mm~50mm低碳钢、低合金钢等金属材料的石油天然气长输、集输及其站场的管道环向对接接头的检测于质量分级。
3)超声波检测使用于壁厚为5mm~50mm,管径为57mm~1400mm碳素钢、低合金钢等金属材料的石油天然气长输、集输及其站场的管道环向对接接头的检测与质量分级;不适用与弯头与直管、带颈法兰与直管、回弯头与直管对接接头的检测。
4)磁粉检测适用于铁磁性材料的石油天然气长输、集输、站场的管道及常压钢制储罐的焊接接头表面、近表面缺欠的检测与验收。
5)渗透检测适用于碳素钢、低合金钢等金属材料的石油天然气长输、集输、站场的管道及常压钢制储罐的焊接接头表面开口缺欠的检测与验收。
6)本标准不适用工业和公用管道的无损检测,也不适用油气管道制管焊缝的无损检测。
2、一般要求1)使用原则:(1)应根据被检产品的材质、制造方法、工作介质、适用条件和失效模式,预计可能产生的缺欠种类、形状、部位和取向,选择最合适的无损检测方法。
(2)射线和超声检测主要用于检测石油天然气钢质管道对接接头内部的缺欠;磁粉检测主要用于钢制管道焊接接头表面及近表面的缺欠;渗透检测主要用于检测钢质管道焊接接头表面开口的缺欠。
(3)石油天然气钢质管道对接接头内部的面状缺欠,宜采用超声波检测,管道对接接头内部的体积状缺欠及薄壁管对接接头,通常采用射线检测。
(4)铁磁性材料表面检测时,宜优先采用磁粉检测。
(5)当采用两种或两种以上的检测方法对石油天然气钢质管道的同一部位进行检测时,应符合各自的合格级别。
如采用两种检测方法,不同检测工艺进行检测,当检测结果不一致时,应以质量级别最差的级别为准。
SYT4109-2005 石油天然气钢质管道无损检测

石油天然气钢质管道无损检测1范围本标准规定了射线检测、超声检测、磁粉检测和渗透检测四种无损检测方法及质量分级。
射线(X、γ)检测适用于壁厚为2mm~50mm低碳钢、低合金钢等金属材料的石油天然气长输、集输及其站场的管道环向对接接头的检测与质量分级。
超声检测适用于壁厚为5mm~50mm,管径为57mm~1400mm碳素钢、低合金钢等金属材料的石油天然气长输、集输及其站场的管道环向对接接头的检测与质量分级;不适用于弯头与直管、带颈法兰与直管、回弯头与直管对接接头的检测。
磁粉检测适用于铁磁性材料的石油天然气长输、集输、站场的管道及常压钢制储罐的焊接接头表面、近表面缺欠的检测与验收。
渗透检测适用于碳素钢、低合金钢等金属材料的石油天然气长输、集输、站场的管道及常压钢制储罐的焊接接头表面开口缺欠的检测与验收。
本标准不适用工业和公用管道的无损检测,也不适用油气管道制管焊缝的无损检测。
2规范性引用文件下列文件中的条款通过本标准的引用而成为本标准的条款。
凡是注日期的引用文件,其随后所有的修改单(不包括勘误的内容)或修订版均不适用于本标准,然而,鼓励根据本标准达成协议的各方研究是否可使用这些文件的最新版本。
凡是不注日期的引用文件,其最新版本适用于本标准。
GB/T 3323 钢熔化焊对接接头射线照相和质量分级GB11533 标准对数视力表GB 11924 辐射安全培训规定GB 16357 工业X射线探伤放射卫生防护标准GB/T16673 无损检测用黑光源(UV—A)辐射的测量GB 18465 工业γ射线探伤放射卫生防护要求GB 18871 电离辐射防护与辐射源安全基本标准JB/T 6063 磁粉探用磁粉技术条件JB/T 6065 磁粉探伤用标准试片JB/T 7902 线型像质计JB/T 7913 超声波检测钢制对比试块的制作与校验方法JB/T 8290 磁粉探伤机JB/T 9214 A型脉冲反射式超声波探伤系统工作性能测试方法JB/T 10061 A型脉冲反射式超声波探伤仪通用技术条件JB/T 10062 超声探伤用探头性能测试方法JB/T 10063 超声探伤用1号标准试块技术条件ZBY344 超声探伤用探头型号命名方法3术语和定义下列术语和定义适用于本标准。
石油天然气钢质管道无损检测-SY-T4109-2013

编号 SGB—1 SGB—2 SGB—3 SGB—4
SGB—5
SGB—6
200
平面
>360~600
>600
SRB对比试块
说明:Φ---被检管线外径; T---被检管线公称壁厚; h---内壁环状矩形槽的槽深; h=10%T且h≤1.5mm。
声能损失
仪器性能的调节
直探头测定,垂直线性,水平线性 斜探头测定,入射点,前沿距离,分辨力,折射角, 灵敏度余量
检测准备
检测面 探头移动区应清除飞溅、锈蚀、油污及其他外部 杂质,检测表面应修磨平整光滑,其表面粗糙度不应 超过6.3μm。焊缝及检测面应经外观检查合格方可进行 检测。
探头移动要求
探头移动区的确定应符合下列规定: 1.采用一次反射法检测时,探头移动区不应小于1.25P, P应按式(6.7.3)计算: P=2KT (6.7.3) 式中:P—跨距(mm); T—板厚(mm); K—声束在工件中的折射角β的正切值(tanβ)。 2.采用直射法检测时,探头移动区不应小于0.75P。
扫查方法
应采用单面双侧直射法和反射波法检测。 扫查灵敏度不应低于评定线灵敏度。 扫查速度不应大于150mm/s,当采用自动报警装臵扫 查时不受此限制;在平行扫查方向上,每个探头的 扫查路径应重叠,其范围至少为探头(压电晶片) 垂直于扫查方向尺寸的10%。
为探测纵向缺欠,探头应垂直焊缝中心线做矩形或 锯齿形扫查,探头前后移动范围应保证能扫查到全 部焊缝截面及热影响区,在保持探头垂直焊缝作前 后移动的同时,应作10°~15°的左右扫查。为观察 缺陷动态波形和区分缺陷信号或伪缺陷信号,确定 缺陷的位臵、方向和形状,可采用前后、左右、转 角、环绕等四种探头基本扫查方式。 检测横向缺欠时,应将波幅曲线灵敏度均提高6dB。 检测时,可在焊接接头两侧边缘使探头与焊接接头 中心线成10°~20°作两个方向的斜平行扫查。
浅析石油天然气钢质管道的无损检测

浅析石油天然气钢质管道的无损检测发表时间:2019-07-31T09:36:03.950Z 来源:《防护工程》2019年8期作者:李亚君1 童建军2 [导读] 石油天然气已经越发的成为我国的重要生产生活资源,小到百姓的日常生活,大到企业的生产乃至国防建设,都离不开石油及天然气这些重要资源的供给。
新疆广陆工程咨询有限公司新疆克拉玛依 8340001;新疆天维无损检测有限公司新疆克拉玛依 8340002 摘要:石油天然气已经越发的成为我国的重要生产生活资源,小到百姓的日常生活,大到企业的生产乃至国防建设,都离不开石油及天然气这些重要资源的供给。
在国际标准中,通常都是钢制管道,但是如何保证钢制管道的无损及安全有效的运行呢,这着实已经成为一个重要的待我们不断完善的一个重要课题。
关键词:天然气;设备;设计;标准体系;探讨一、前言作为石油天然气行业重要组成部分的天然气气田及管道建设,在近20年得到了迅速的发展,其技术标准和规范发挥了重要作用;目前对石油工业标准体系及相关标准开展研究和修订,必将促使我国石油天然气行业标准、规范进一步适应与国际接轨,满足我国石油天然气工业市场发展的要求。
二、研究石油天然气行业标准体系的意义和建议2.1标准、规范对工程建设的作用,在于保证工程的质量和所需的技术水平,而且在一定条件下还能起到节省投资的作用;如果某一个领域或某一个专业缺少了某一项标准、规范,设计人员就必须在设计中编制适用于该项工程的标准、规范,否则其工程质量就难于保证;由于设计人员在编制该项工程专用标准、规范时,受多方面因素影响,可能会提出过高的技术要求和检验项目,不单使制造施工工期加长,而且会加大工程投资。
由此可见编制一项通用的行业或国家标准、规范的重要性。
标准、规范从立项到编制、审批、正式实施,都应该是受控于行业标准体系中,之所以在工程设计、施工中会出现缺少某一项标准、规范或是标准、规范在内容或技术要求上不能满足工程建设的需要,或是相关的两个标准在某一条技术要求上发生矛盾,往往是由于标准体系不够健全,忽略了某些标准的立项,或是标准体系对其中的标准编制的目的和要求有问题所致,所以研究标准体系是在更高层次上来把握标准的立项和编制,是从宏观上从全局规划行业的标准、规范。
石油天然气钢质管道无损检测
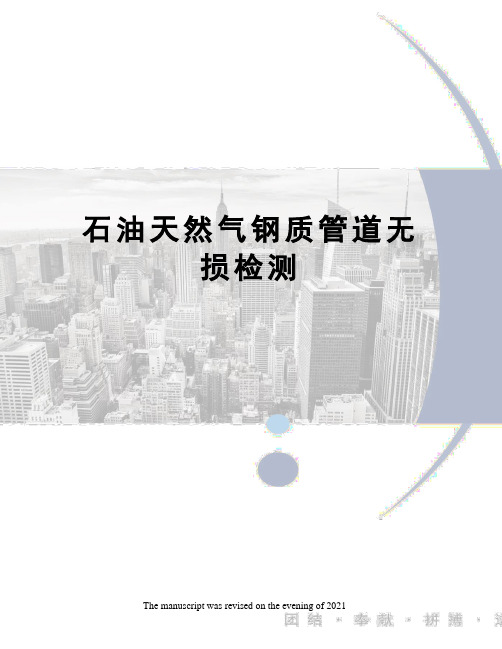
石油天然气钢质管道无损检测The manuscript was revised on the evening of 2021一、概述1 SY/T4109-2005编制背景和简要经过随着我国石油天然气管道工程建设的发展,管道无损检测技术也得到了很大的发展。
同时管道工程施工技术,特别是管道焊接技术的发展,对无损检测技术提出了新的要求。
为确保工程质量,进一步完善无损检测标准,根据原国家石油和化学工业局《关于下达2001年石油天然气、石油化工行业标准、修订项目计划的通知》(国石化政发(2000)410号)文件要求,由石油天然气管道局盘锦北方无损检测公司负责对SY4056-93《石油天然气管道对接焊缝射线照相及质量分级》、SY4065-93《石油天然气管道对接焊缝超声波探伤及质量分级》、SY/T 0444-98《常压钢制焊接储罐及管道磁粉检测技术标准》及SY/T 0443-98《常压钢制焊接储罐及管道渗透检测技术标准》进行了整合修订,修订后标准名称为《石油天然气钢质管道无损检测》。
本标准在修订过程中,编制人员遵照国家有关方针政策,进行了比较广泛的调查研究,在全面总结和吸纳多年石油天然气钢质管道无损检测经验和技术,充分考虑石油天然气钢质管道工程施工实际特点的基础上,积极参照采用国外有关先进标准,并多次以发函或会议形式征求相关方意见,经反复修改形成送审稿,于2004年12月在海南三亚通过了由石油工程建设专业标准化委员会施工分标委组织的标准审查会的审查。
2 SY/T4109-2005修订的指导思想(1)目前石油天然气管道(含集输管道及其站场),特别是油气长输管道正向着大口径、大壁厚、高钢级及高压力方向发展,而与之相配套的先进的焊接和无损检测技术及设备也在广泛采用。
作为无损检测标准,必须适应和满足这种变化。
另外,管道施工建设不仅要占领国内市场,而且还要走向世界。
因此,与国外标准接轨也是本次标准修订应考虑的的一个重要因素。
浅析石油天然气钢质管道的无损检测
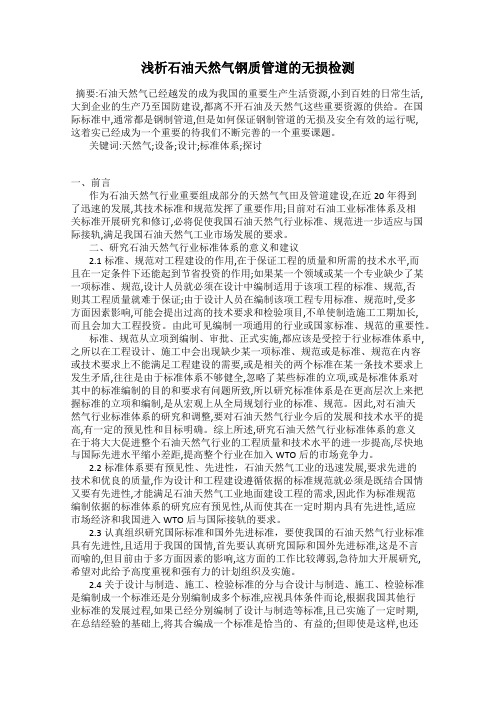
浅析石油天然气钢质管道的无损检测摘要:石油天然气已经越发的成为我国的重要生产生活资源,小到百姓的日常生活,大到企业的生产乃至国防建设,都离不开石油及天然气这些重要资源的供给。
在国际标准中,通常都是钢制管道,但是如何保证钢制管道的无损及安全有效的运行呢,这着实已经成为一个重要的待我们不断完善的一个重要课题。
关键词:天然气;设备;设计;标准体系;探讨一、前言作为石油天然气行业重要组成部分的天然气气田及管道建设,在近20年得到了迅速的发展,其技术标准和规范发挥了重要作用;目前对石油工业标准体系及相关标准开展研究和修订,必将促使我国石油天然气行业标准、规范进一步适应与国际接轨,满足我国石油天然气工业市场发展的要求。
二、研究石油天然气行业标准体系的意义和建议2.1标准、规范对工程建设的作用,在于保证工程的质量和所需的技术水平,而且在一定条件下还能起到节省投资的作用;如果某一个领域或某一个专业缺少了某一项标准、规范,设计人员就必须在设计中编制适用于该项工程的标准、规范,否则其工程质量就难于保证;由于设计人员在编制该项工程专用标准、规范时,受多方面因素影响,可能会提出过高的技术要求和检验项目,不单使制造施工工期加长,而且会加大工程投资。
由此可见编制一项通用的行业或国家标准、规范的重要性。
标准、规范从立项到编制、审批、正式实施,都应该是受控于行业标准体系中,之所以在工程设计、施工中会出现缺少某一项标准、规范或是标准、规范在内容或技术要求上不能满足工程建设的需要,或是相关的两个标准在某一条技术要求上发生矛盾,往往是由于标准体系不够健全,忽略了某些标准的立项,或是标准体系对其中的标准编制的目的和要求有问题所致,所以研究标准体系是在更高层次上来把握标准的立项和编制,是从宏观上从全局规划行业的标准、规范。
因此,对石油天然气行业标准体系的研究和调整,要对石油天然气行业今后的发展和技术水平的提高,有一定的预见性和目标明确。
石油天然气钢质管道无损检测-SY-T4109ppt课件
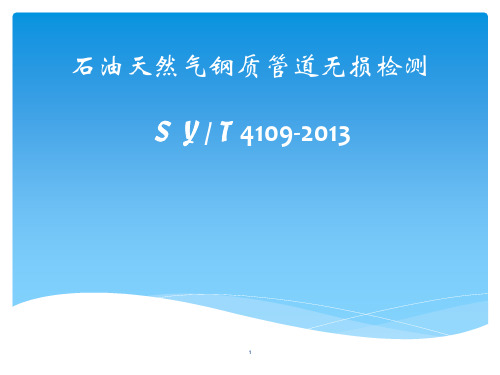
检测外径为57㎜~140㎜的对接环焊缝时,探头的接 触面应与管子外表面紧密接触,其边缘与管子外表 面的间隙不应大于0.5mm。
9
检测准备
检测面 探头移动区应清除飞溅、锈蚀、油污及其他外部
杂质,检测表面应修磨平整光滑,其表面粗糙度不应 超过6.3μm。焊缝及检测面应经外观检查合格方可进行 检测。
17
适用管外径范围Φ mm
57~89 >89~140 >140~210 >210~360 >360~600
>600
SRB对比试块
说明:Φ---被检管线外径; T---被检管线公称壁厚; h---内壁环状矩形槽的槽深; h=10%T且h≤1.5mm。
18
声能损失
19
仪器性能的调节
直探头测定,垂直线性,水平线性 斜探头测定,入射点,前沿距离,分辨力,折射角,
检测横向缺欠时,应将波幅曲线灵敏度均提高6dB。 检测时,可在焊接接头两侧边缘使探头与焊接接头 中心线成10°~20°作两个方向的斜平行扫查。
13
2、前后、左右、转角、环绕扫查 ▪前后扫查:确定缺陷水平距离和深度 ▪左右扫查:测定缺陷指示长度
▪转角扫查:确定缺陷取向 ▪环绕扫查:确定缺陷形状
14
10
探头移动要求
探头移动区的确定应符合下列规定:
1.采用一次反射法检测时,探头移动区不应小于1.25P, P应按式(6.7.3)计算:
P=2KT
(6.7.3)
式中:P—跨距(mm);
T—板厚(mm);
K—声束在工件中的折射角β的正切值(tanβ)。
2.采用直射法检测时,探头移动区不应小于0.75P。
石油天然气钢质管道无损检测(最终版)
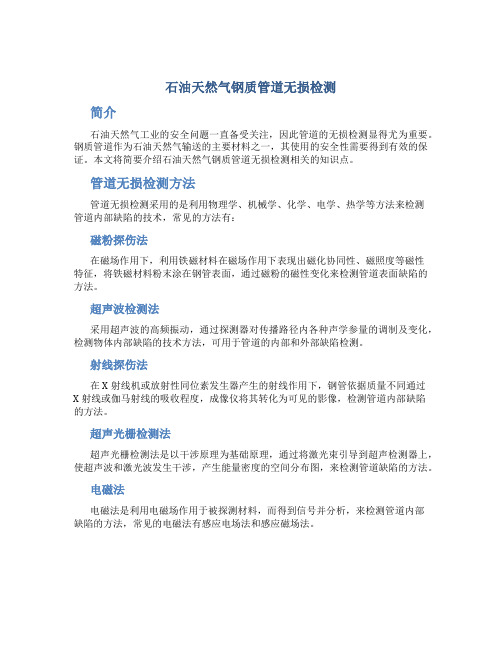
石油天然气钢质管道无损检测简介石油天然气工业的安全问题一直备受关注,因此管道的无损检测显得尤为重要。
钢质管道作为石油天然气输送的主要材料之一,其使用的安全性需要得到有效的保证。
本文将简要介绍石油天然气钢质管道无损检测相关的知识点。
管道无损检测方法管道无损检测采用的是利用物理学、机械学、化学、电学、热学等方法来检测管道内部缺陷的技术,常见的方法有:磁粉探伤法在磁场作用下,利用铁磁材料在磁场作用下表现出磁化协同性、磁照度等磁性特征,将铁磁材料粉末涂在钢管表面,通过磁粉的磁性变化来检测管道表面缺陷的方法。
超声波检测法采用超声波的高频振动,通过探测器对传播路径内各种声学参量的调制及变化,检测物体内部缺陷的技术方法,可用于管道的内部和外部缺陷检测。
射线探伤法在X射线机或放射性同位素发生器产生的射线作用下,钢管依据质量不同通过X 射线或伽马射线的吸收程度,成像仪将其转化为可见的影像,检测管道内部缺陷的方法。
超声光栅检测法超声光栅检测法是以干涉原理为基础原理,通过将激光束引导到超声检测器上,使超声波和激光波发生干涉,产生能量密度的空间分布图,来检测管道缺陷的方法。
电磁法电磁法是利用电磁场作用于被探测材料,而得到信号并分析,来检测管道内部缺陷的方法,常见的电磁法有感应电场法和感应磁场法。
管道无损检测重要性管道无损检测不仅可以发现管道内部的缺陷情况,也能提前预测管道的损耗情况,以及进行针对性的预防措施。
通过检测出管道的问题,可以采取及时有效的修复措施,保证了管道的安全运行,减少了意外事故的发生。
石油天然气工业的发展不仅需要精细的技术,也需要以人为本、保障安全的措施。
在钢质管道的制造、安装及运行过程中,因材料、设备、环境等因素,管道缺陷及其导致的事故风险无法避免。
因此,对于管道的无损检测需要时刻保持高度的重视和严肃的态度,以确保石油天然气工业的安全可靠运行。
- 1、下载文档前请自行甄别文档内容的完整性,平台不提供额外的编辑、内容补充、找答案等附加服务。
- 2、"仅部分预览"的文档,不可在线预览部分如存在完整性等问题,可反馈申请退款(可完整预览的文档不适用该条件!)。
- 3、如文档侵犯您的权益,请联系客服反馈,我们会尽快为您处理(人工客服工作时间:9:00-18:30)。
石油天然气钢质管道无损检测最终版Prepared on 22 November 2020一、概述1 SY/T4109-2005编制背景和简要经过随着我国石油天然气管道工程建设的发展,管道无损检测技术也得到了很大的发展。
同时管道工程施工技术,特别是管道焊接技术的发展,对无损检测技术提出了新的要求。
为确保工程质量,进一步完善无损检测标准,根据原国家石油和化学工业局《关于下达2001年石油天然气、石油化工行业标准、修订项目计划的通知》(国石化政发(2000)410号)文件要求,由石油天然气管道局盘锦北方无损检测公司负责对SY4056-93《石油天然气管道对接焊缝射线照相及质量分级》、SY4065-93《石油天然气管道对接焊缝超声波探伤及质量分级》、SY/T 0444-98《常压钢制焊接储罐及管道磁粉检测技术标准》及SY/T 0443-98《常压钢制焊接储罐及管道渗透检测技术标准》进行了整合修订,修订后标准名称为《石油天然气钢质管道无损检测》。
本标准在修订过程中,编制人员遵照国家有关方针政策,进行了比较广泛的调查研究,在全面总结和吸纳多年石油天然气钢质管道无损检测经验和技术,充分考虑石油天然气钢质管道工程施工实际特点的基础上,积极参照采用国外有关先进标准,并多次以发函或会议形式征求相关方意见,经反复修改形成送审稿,于2004年12月在海南三亚通过了由石油工程建设专业标准化委员会施工分标委组织的标准审查会的审查。
2 SY/T4109-2005修订的指导思想(1)目前石油天然气管道(含集输管道及其站场),特别是油气长输管道正向着大口径、大壁厚、高钢级及高压力方向发展,而与之相配套的先进的焊接和无损检测技术及设备也在广泛采用。
作为无损检测标准,必须适应和满足这种变化。
另外,管道施工建设不仅要占领国内市场,而且还要走向世界。
因此,与国外标准接轨也是本次标准修订应考虑的的一个重要因素。
(2)在检测工艺方面,应总结我国石油天然气企业在国内外长输管道施工检测的成功经验,积极吸纳国内外相关标准的长处来修订。
修改后标准,应具有科学性、先进性、简单实用、可操作性强的特点。
(3)验收标准部分应在原标准的基础上,充分考虑我国油气管道,特别是长输管道的实际情况,在满足和确保工程质量实际需要的前提下,参照国外先进标准来修订。
3 与原标准相比,SY/T4109-2005检测技术部分的特点(1)射线检测部分①本标准增加了下列内容:a 明确了本标准不仅适用于长输、集输管道的X、γ射线检测,也适用于其站场的检测,特别引进了Se75 γ射线的检测技术。
明确本标准不适用于工业和公用压力管道环焊缝的检测,也不适用于油气管道制管焊缝的检测。
b 明确了本标准照相技术等级相当于GB3323-1987的AB级。
c 针对长输管道采用低合金高强钢的特点,纳入了K值的概念,重视对横向缺欠的检出。
对于公称直径小于250㎜管道环缝双壁单影透照时,K值和一次透照长度给予适当放宽。
d 引入了新的辐射防护标准,划定控制区和管理区,并设置防护标志,严格规定检测人员及公众的安全防护。
e 明确了射线源和能量控制。
f 明确了曝光量推荐值与焦距的关系及γ射线最短曝光时间的控制。
g 明确了像质计放于胶片侧应提高一个像质指数。
②简化完善了原标准的相关条款:a 适用管壁厚度由2㎜~30㎜修改为2㎜~50㎜。
或b 更新了胶片的分类方法,对于γ射线检测,由于能量偏高,工件对比度低,选用T2胶片。
用提高胶片对比度的方法弥补工件对比度的不足。
T3c 将原标准双壁双影透照的界限由原来的Φ114㎜改为Φ89㎜,这与GB3323-1987和API std 1104相一致,并明确了小径管检测的要点。
d 根据长输管道检测的类型,完善了底片上的标记。
e 为便于爬行器的检测,参照EN1435-1997,只要满足底片质量和灵敏度要求,几何不清晰度可适当放宽,焦点到工件表面的距离L1可减少规定值的50%。
f 简化了缺欠深度的测定方法,取消沟槽式测深计,用缺欠黑度与较薄侧母材黑度比较来确定。
g 改变透照厚度T的计算方法。
Ah 底片的黑度范围:X射线~改为~;γ射线~改为~;有利于发现缺欠。
i 充实完善了射线检测报告的内容。
(2)超声波检测部分超声波检测管壁厚度由原来5㎜~30㎜修改为5㎜~50㎜,管径增至1400㎜;超声检测技术部分参照JB4730及DL/T820-2002等修订而成,重点解决了中薄壁管探头的选择及检测技术。
(3)磁粉和渗透检测部分磁粉和渗透检测技术部分在原标准基础上参照了JB4730、ASME、日本及欧洲标准修订而成。
4 验收部分验收部分主要参照了API std 1104 ,并总结了我国油气管道,特别是国家重点项目――西气东输管道工程的无损检测实践修订而成。
其中,射线和超声波验收部分的修改,严于《管道及有关设施的焊接》(API std 1104-1999)、《西气东输管道工程管道对接环焊缝射线检测》(Q/SY XQ6-2002)和《西气东输管道工程管道对接环焊缝全自动超声波检测》(Q/SY XQ7-2002),与《石油天然气管道对接焊缝射线照相及质量分级》(SY4056-93)和《石油天然气管道对接焊缝超声波探伤及质量分级》(SY4065-93)相比,个别条款做了适当放宽(国内外主要油气管道射线检测验收标准比较详见表1);磁粉和渗透的验收标准与原标准相当。
二标准条文解释1 范围(1)随着我国经济的快速发展,原标准规定的射线检测环向对接接头的壁厚范围2㎜~30㎜,超声波检测管壁厚度范围5㎜~30㎜、管径范围57㎜~1200mm,已不能满足要求,如举世瞩目的西气东输管道工程有的管壁厚度达到32㎜,管径为1016㎜;为满足目前工程实际需要,同时考虑今后石油天然气管道工程的发展,本标准将射线检测适用的管壁厚度范围修改为2㎜~50㎜,将超声波检测管壁厚度范围修改为5㎜~50㎜、管径范围修改为57㎜~1400mm。
但对于弯头与直管、带颈法兰与直管、回弯头与直管对接接头的检测面狭小、厚度不一,且从单侧检测易漏检,不易采用超声波检测,仍保留原标准的意见。
(2)磁粉检测的适用范围与原标准SY/T0444-98基本相同,只对原标准中管道磁粉检测适用的外径范围为70mm以上这一规定做了放宽,本标准不受此条限制,主要是考虑目前国内外磁轭式磁粉检测设备能满足磁极间距调整范围和保证磁极与工件良好接触。
(3)渗透检测的适用范围与原标准相同。
根据JIS Z 3050《管道焊缝的无损检测方法》对管道的不同要求,在渗透检测的验收条件上提出了一般要求和较严要求两种情况,即A标准和B标准。
这种规定比较符合工程实际情况,因此制定本标准时参照了 JIS Z 3050 的有关规定。
由于国内石油管道的检测已经采用API Std 1104,所以在编制本标准时也参考了其有关规定。
同时还参考了 ASME《锅炉及压力容器规范》第Ⅴ卷和第Ⅷ卷的有关内容。
由于日本在储罐施工和检测方面经验丰富,标准体系完善、系统、先进,我国大型储罐检测标准很多是参照日本检测标准相关内容制定的,因此本标准编制时,主要参照了日本JIS B 8501《钢制焊接储罐结构》附录3“无损探伤试验方法及其评定标准。
(4)本标准适用于石油天然气长输、集输及其站场的钢质管道焊缝检测,磁粉和渗透检测也适用于常压钢制焊接储罐焊缝的检测;不适用于工业和公用压力管道无损检测,也不适用于油气管道制管焊缝的无损检测。
工业管道、公用压力管道与长输管道不同之处在于:工业管道、公用压力管道一般处于人口稠密且多数与高温、高压、易燃、易爆的容器联结而成,一旦发生事故,将危及整个装置群,对人民的生命财产造成极大的损害。
在国外长输管道与工业、公用压力管道检测的界面划分很清楚,例如利比亚输油(气)管道工程,对于压力容器系统装置的工业管道及公用管道均采用ASME标准,对于长输管道、集输管道及其站场的钢质管道焊缝无损检测均采用API std 1104标准。
在我国工业管道和公用压力管道无损检测按相应法规标准的要求已纳入JB4730的检测范围。
油气管道制管焊缝的无损检测应按国家或行业相关法规、标准执行,故本标准也不适用于油气管道制管焊缝的无损检测。
2 规范性引用文件本标准在某些条文中引用和参考借鉴上述标准如射线检测中辐射防护参照GB18871、GB16357和GB18465标准;线型金属丝像质计的型号和规格参照JB/T 7902标准等。
这些标准都是目前最新版。
3 术语和定义图2 夹层未熔合(1)缺欠和缺陷的术语及定义,主要参照API std 1104的相关内容制定。
本章特别引入了“缺欠”这一新概念,并将其定义为:“按无损检测方法检出的不连续性”。
在这里要特别注意的是两个概念之间的区别和联系。
应该说“缺欠和缺陷”均为检出的不连续性。
缺陷即是缺欠,但缺欠并不一定是缺陷。
缺欠包括合格的和不合格的。
而缺陷则是不合格的。
(2)原标准对未熔合没有定义,只在验收标准中提到层间未熔合和坡口未熔合。
为了给未熔合一个确切的定义,本标准依据API std 1104将上述两种缺欠定义为夹层未熔合,并增加表面未熔合的概念,即将熔焊金属与母材之间未能完全熔化结合且延续到表面,定义为表面未熔合。
处于外表面的定义为外表面未熔合,处于根部内表面的定义为根部未熔合。
4 一般要求(1)每种检测方法都有它的长处和不足,都不是万能的,应根据具体情况具体处理。
射线检测具有便于定性、定量,直观,有据可查,可存档等特点;主要用于石油天然气钢质管道中、薄壁管对接接头内部缺欠的检测,对于体积状缺欠(如气孔、夹渣、体积状未焊透等)检出率高,但对于厚壁管道对接接头中的面状缺欠检出率较低。
超声检测主要用于石油天然气钢质管道中、厚壁管对接接头内部的面状缺欠(如裂纹、未熔合等)的检测;但定性难度大,受客观条件影响严重。
磁粉检测仅适用于铁磁性材料焊接接头表面和近表面缺欠的检测;对线状缺欠检出率高,对点状缺欠检出率低。
渗透检测主要用于检测焊接接头表面开口的缺欠,对点状缺欠特别敏感,对宽而浅的线状缺欠检出率较低。
(2)鉴于上述原因和压力容器检测常规方法的特点,当采用两种或两种以上的检测方法对同一部位进行检测时,应符合各自的合格级别。
如采用同种检测方法、不同检测工艺进行检测,当检测结果不一致时,应以质量级别最差的级别为准。
返修部位的检测应采用原检测方法和工艺进行。
例如凡超声检测不合格的,必须采用超声波复检。
(3)焊缝、焊接接头和对接接头的概念。
焊缝和焊接接头是两个不同概念。
焊缝是指焊件焊接后新形成的结合部分。
焊接接头是指用焊接方法连接的接头(简称焊头)。
焊接接头包括焊缝、熔合区和热影响区。
焊接接头主要形式有对接接头、T型接头、十字接接头、角接接头等。