超高强度钢
超高强度钢
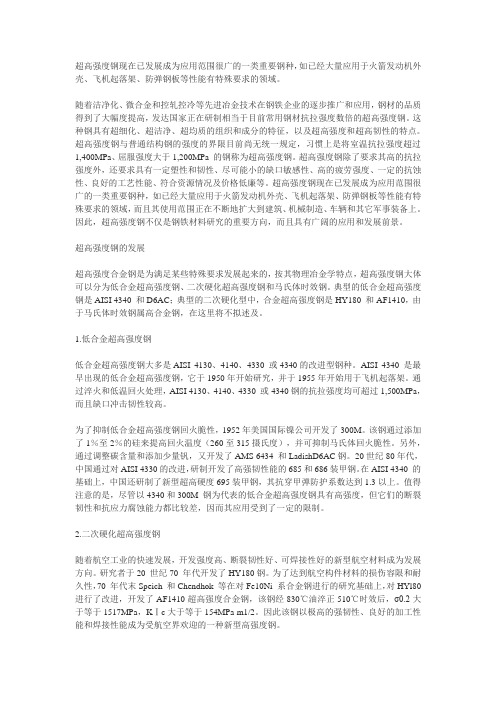
超高强度钢现在已发展成为应用范围很广的一类重要钢种,如已经大量应用于火箭发动机外壳、飞机起落架、防弹钢板等性能有特殊要求的领域。
随着洁净化、微合金和控轧控冷等先进冶金技术在钢铁企业的逐步推广和应用,钢材的品质得到了大幅度提高,发达国家正在研制相当于目前常用钢材抗拉强度数倍的超高强度钢。
这种钢具有超细化、超洁净、超均质的组织和成分的特征,以及超高强度和超高韧性的特点。
超高强度钢与普通结构钢的强度的界限目前尚无统一规定,习惯上是将室温抗拉强度超过1,400MPa、屈服强度大于1,200MPa 的钢称为超高强度钢。
超高强度钢除了要求其高的抗拉强度外,还要求具有一定塑性和韧性、尽可能小的缺口敏感性、高的疲劳强度、一定的抗蚀性、良好的工艺性能、符合资源情况及价格低廉等。
超高强度钢现在已发展成为应用范围很广的一类重要钢种,如已经大量应用于火箭发动机外壳、飞机起落架、防弹钢板等性能有特殊要求的领域,而且其使用范围正在不断地扩大到建筑、机械制造、车辆和其它军事装备上。
因此,超高强度钢不仅是钢铁材料研究的重要方向,而且具有广阔的应用和发展前景。
超高强度钢的发展超高强度合金钢是为满足某些特殊要求发展起来的,按其物理冶金学特点,超高强度钢大体可以分为低合金超高强度钢、二次硬化超高强度钢和马氏体时效钢。
典型的低合金超高强度钢是AISI 4340 和D6AC;典型的二次硬化型中,合金超高强度钢是HY180 和AF1410,由于马氏体时效钢属高合金钢,在这里将不拟述及。
1.低合金超高强度钢低合金超高强度钢大多是AISI 4130、4140、4330 或4340的改进型钢种。
AISI 4340 是最早出现的低合金超高强度钢,它于1950年开始研究,并于1955年开始用于飞机起落架。
通过淬火和低温回火处理,AISI 4130、4140、4330 或4340钢的抗拉强度均可超过1,500MPa,而且缺口冲击韧性较高。
为了抑制低合金超高强度钢回火脆性,1952年美国国际镍公司开发了300M。
高强钢和超高强度钢定义

高强钢和超高强度钢的定义及特点1. 引言高强钢和超高强度钢是现代材料科学和工程领域中的两个重要概念。
随着工业技术的不断发展,对材料强度和性能的要求也越来越高。
高强钢和超高强度钢以其卓越的力学性能和广泛的应用领域而备受关注。
本文将对高强钢和超高强度钢的定义、特点和应用进行详细介绍。
2. 高强钢的定义和特点高强钢是指抗拉强度大于等于540MPa的钢材。
相对于普通碳素钢,高强钢具有以下特点:2.1 强度高高强钢的抗拉强度大于等于540MPa,远高于普通碳素钢的抗拉强度。
这使得高强钢在承受大的外力时能够更好地抵抗变形和破坏,提高了结构的安全性和可靠性。
2.2 韧性好高强钢不仅具有高强度,而且具有较好的韧性。
在承受外力时,高强钢能够发生一定程度的塑性变形,从而吸收外力的冲击能量,减少结构的破坏。
这使得高强钢在工程结构中能够更好地应对地震、风载等复杂环境的作用。
2.3 可焊接性好高强钢通常具有良好的可焊接性,可以通过常规的焊接工艺进行连接。
这使得高强钢在工程施工中更加方便快捷,降低了施工难度和成本。
2.4 重量轻相对于普通碳素钢,高强钢的强度更高,但密度相对较低,因此具有较轻的重量。
这使得高强钢在汽车、航空航天等领域得到广泛应用,可以减轻结构自重,提高载荷能力和燃油效率。
3. 超高强度钢的定义和特点超高强度钢是指抗拉强度大于等于980MPa的钢材。
相对于高强钢,超高强度钢具有以下特点:3.1 极高的强度超高强度钢的抗拉强度远远超过普通钢材,达到甚至超过980MPa。
这使得超高强度钢在工程中可以承受更大的荷载,应用于更为苛刻的环境中。
3.2 卓越的韧性超高强度钢在具有极高强度的同时,韧性也相对较好。
这是通过合理的化学成分设计和热处理工艺实现的。
超高强度钢能够在承受外力时发生较大的塑性变形,从而吸收更多的冲击能量,提高结构的抗震性能。
3.3 优异的耐蚀性超高强度钢通常具有良好的耐蚀性,能够在恶劣的环境中长期使用而不受腐蚀的影响。
超高强度钢
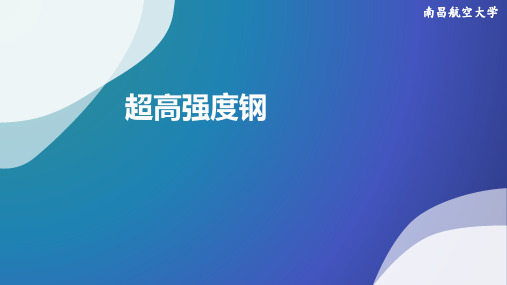
南昌航空大学
01 化学成分
碳 C :0.27~0.34 硫 S :≤0.020 镍 Ni:1.40~1.80
硅 Si:0.90~1.20 锰 Mn:1.00~1.30
磷 P :≤0.020
铬 Cr:0.90~1.20
02
力学性能
抗拉强度 σb (Mpa):1)1767; 2)1627 伸长率 δ5 (%):1)12;2)13 断面收缩率 ψ (%):50 冲击韧性值 αku (J/cm2):1)79;2)90 试样尺寸:棒材
THANK YOU!
南昌航空大学
• 合金元素含量较低,一般在2.5%以下。 • 这类钢合金元素含量低,成本低,生产工艺简单,广泛用于制造飞机大梁、起落架
构件、发动机轴、固体火箭发动机壳体和化工高压容器等。
01 定义与分类
南昌航空大学
中合金超高强度钢(Medium-alloy ultra-high strength steel)
• 热作模具钢的改型钢,典型钢种有4Cr5MoSiV钢。这类钢的含碳量约0.4%, 合金元素总含量约8%,具有较高的淬透性。
01 定义与分类 二、马氏体时效钢( maraging steel)
南昌航空大学
• 含碳小于0.03%,钢中主要合金元素为镍,钴,钼,钛
• 火箭发动机壳体、飞机起落架和关键连接件等航空航天及深海技术中重要 结构件。
02
30CrMnSiNi2A 飞机起落架
南昌航空大学
02 飞机起落架
30CrMnSiNi2A 飞机起落架
南昌航空大学
• 起落架是飞机上重要而特别的部件,它不参与机体的结构和性能, 却极大地影响飞机的使用和安全。
• 30CrMnSiNi2A是我国广泛使用的一种综合性能良好的低合金超高 强度钢,主要用于制造飞机起落架、机翼、发动机壳等受力结构件, 及高压连接件和高扭短轴零件。
常见车身钢材的种类

常见车身钢材的种类车身钢材是指用于汽车车身的金属材料。
由于不同部位对材料的要求不同,因此车身钢材也有多种不同的种类。
下面将介绍几种常见的车身钢材。
1. 高强度钢高强度钢是一种具有较高屈服强度和抗拉强度的钢材。
在汽车制造中,高强度钢被广泛应用于车身结构的关键部位,如车顶、车门、底盘等。
高强度钢可以提高汽车的结构强度和刚度,同时减轻车身重量,提高燃油经济性和碰撞安全性能。
2. 超高强度钢超高强度钢是一种具有更高屈服强度和抗拉强度的钢材。
它通常用于汽车车身的保护部位,如车身柱、侧门梁等。
超高强度钢的使用可以提高汽车的抗碰撞能力,保护车内乘员的安全。
3. 不锈钢不锈钢是一种具有耐腐蚀性能的钢材。
在汽车制造中,不锈钢常用于外部装饰件、排气系统和零部件等。
不锈钢不容易生锈,能够保持车身的美观和耐用性。
4. 钢铝复合材料钢铝复合材料是由钢与铝两种金属材料通过冷轧、热轧等工艺复合而成的一种材料。
在汽车制造中,钢铝复合材料常用于车身结构的关键部位,如车顶、车门等。
钢铝复合材料既具有钢材的高强度和刚度,又具有铝材的轻量化特点,能够在保证车身强度的同时减轻车身重量。
5. 镀锌钢板镀锌钢板是一种将钢板表面镀上一层锌的材料。
在汽车制造中,镀锌钢板常用于车身的防腐处理。
镀锌钢板具有良好的防腐性能,能够延长车身的使用寿命。
6. 硅钢硅钢是一种具有高硬度和低磁导率的钢材。
在汽车制造中,硅钢常用于汽车发动机的磁性材料。
硅钢能够降低发动机的磁滞损耗,提高发动机的能效和动力性能。
7. 高铝钢高铝钢是一种含铝量较高的钢材。
在汽车制造中,高铝钢常用于车身结构的关键部位,如车顶、车门等。
高铝钢具有良好的抗腐蚀性能和可焊性,能够提高车身的耐久性和安全性能。
总结:车身钢材的种类有很多,每种材料都有其特定的应用领域和优势。
通过合理选择和使用车身钢材,可以提高汽车的结构强度、降低车身重量、提高燃油经济性和碰撞安全性能。
未来随着科技的进步,车身钢材将不断创新和发展,为汽车行业带来更多的可能性。
钢材标号和强度等级

钢材标号和强度等级
钢材的标号和强度等级是根据其化学成分、热处理和力学性能等方面的特点而确定的。
常见的钢材标号和强度等级如下:
1. 碳素结构钢:Q195、Q215、Q235、Q275、Q345,以及其它牌号。
强度等级为A、B、C、D、E级,分别对应不同的屈服强度范围。
2. 低合金高强度结构钢:Q345B、Q345C、Q345D、Q345E等牌号,强度等级为Q、R、T级,分别对应不同的屈服强度范围。
3. 超高强度钢:国内目前有Q550D、Q690D、Q890D、Q960D等牌号。
强度等级为E级及以上,屈服强度范围高于550MPa。
4. 不锈钢:常见的牌号有304、316、321、904L等。
强度等级为1级至3级,分别对应不同的力学性能参数。
5. 合金钢:包括高速钢、工具钢、铸造合金钢等,其强度等级和标号也会因材料组成和工艺特点而有所不同。
需要注意的是,钢材的标号和强度等级并不是一一对应的,同一个标号的钢材可能存在不同的强度等级。
不同的使用场合和要求,也需要选择不同强度等级的钢
材来满足要求。
超高强度钢

超高强度钢超高强度钢一般是指屈服强度大于1380MPa的高强度结构钢。
20世纪40年代中期,美国用AISI4340结构钢通过降低回火温度,使钢的抗拉强度达到1600~1900MPa。
50年代以后,相继研制成功多种低合金和中合金超高强度钢,如300M、D6AC和H一11钢等。
60年代研制成功马氏体时效钢,逐步形成18Ni马氏体时效钢系列,70年代中期,美国研制成功高纯度HP310钢,抗拉强度达到2200MPa。
法国研制的35NCDl6钢,抗拉强度大于1850MPa,而断裂韧度和抗应力腐蚀性能都有明显的改进。
80年代初,美国研制成功AFl410二次硬化型超高强度钢,在抗拉强度为1860MPa时,钢的断裂韧度达到160 MPa·m以上,AFl410钢是目前航空和航天工业部门正在推广应用的一种新材料。
中国于50年代初研制成功30CrMnSiNi2A超高强度钢,抗拉强度为1700MPa。
70年代初,结合中国资源条件,研制成功32Si2Mn2MoVA和40CrMnSiMoVA(GC一4)钢。
1980年以来,从国外引进新技术,采用真空冶炼新工艺,先后研制成功45CrNiMoVA (D6AC)、34Si2MnCrMoVA (406A)、35CrNi4MoA、40CrNi2Si2MoVA(300M)和18Ni马氏体时效钢,成功地用于制做飞机起落架、固体燃料火箭发动机壳体和浓缩铀离心机简体等。
目前超高强度钢已形成不同强度级别系列,在国防工业和经济建设中发挥着重要的作用。
现在,以改变合金成分提高超高强度钢的强度和韧性已很困难。
发展超高强度钢的主要方向是开发新工艺、新技术,提高冶金质量,如采用真空冶炼技术,最大限度降低钢中气体和杂质元素含量,研制超纯净超高强度钢;通过多向锻造和形变热处理,改变钢的组织结构和细化晶粒尺寸,从而提高钢的强度和韧性,例如正在发展的相变诱发塑性钢(TRIP钢)等。
一超高强度钢的合金成分、组织和特性(1)中碳低合金超高强度钢此类钢是通过淬火和回火处理获得较高的强度和韧性,钢的强度主要取决于钢中马氏体的固溶碳浓度。
超高强度钢的分类
超高强度钢的分类
超高强度钢是一种热处理钢,具有极高的强度和硬度,可用于制造高强度零件。
根据其合金元素和热处理方法的不同,超高强度钢可以分为以下几类:
1. 低合金超高强度钢:其合金元素主要为铬、钼、钛等,常用
的热处理方法包括淬火和回火,以及TMCP(控制轧制和温度机械控
制处理)。
2. 高合金超高强度钢:其合金元素主要为钼、钴、钨、铬等,
热处理方法一般为淬火和回火,在加工过程中需要采用高温固溶处理。
3. 马氏体双相钢:其主要合金元素为锰、硅、铬等,具有双相
组织结构,强度和塑性均较高,常用的热处理方法包括淬火和回火、等温淬火等。
4. 颗粒强化钢:利用颗粒的固溶强化作用来提高钢的强度,常
用的颗粒包括碳化物、氮化物、氧化物等,热处理方法一般为淬火和回火。
超高强度钢具有广泛的应用前景,主要用于航空航天、汽车、造船、桥梁等领域。
不同类型的超高强度钢根据其特点和应用需求,可以选择不同的热处理方法和合金元素组成。
- 1 -。
超高强度钢
超高强度钢
超高强度钢是一种在现代工程材料中具有重要地位的材料。
它以其卓越的力学性能和优异的耐腐蚀性能而受到广泛关注。
本文将探讨超高强度钢的制备方法、特性和应用领域。
制备方法
超高强度钢的制备方法主要包括热处理、合金设计和工艺优化。
通过合理的热处理过程,可以调控钢材的结构和性能。
合金设计则是通过添加特定元素,调整钢材的组织结构,提高其强度和耐久性。
工艺优化包括热压成型、热轧等工艺,在制备过程中对钢材进行加工和调整,以获得更好的性能。
特性
超高强度钢具有高强度、高硬度、优异的韧性和良好的耐磨性。
这些特性使得超高强度钢在航空航天、汽车制造、建筑工程等领域有着广泛的应用前景。
与普通钢相比,超高强度钢具有更高的强度和更轻的重量,可以减少结构的重量,提高材料的使用效率。
应用领域
超高强度钢在汽车轻量化领域有着重要的应用。
通过使用超高强度钢,可以减轻汽车的质量,提高燃油效率,降低尾气排放。
此外,超高强度钢还被广泛应用于航空航天领域,用于制造飞机机身、发动机等部件,提高飞机的安全性和性能。
总的来说,超高强度钢作为一种重要的工程材料,在现代工程中发挥着重要的作用。
随着科学技术的不断进步,超高强度钢的应用范围将会不断扩大,为人类创造出更多的可能性。
以上是关于超高强度钢的简要介绍,希望能对读者有所启发。
如果您对超高强度钢感兴趣,可以深入了解其相关知识,探索更多应用领域。
谢谢阅读!。
超高强度钢的发展及展望
超高强度钢的发展及展望摘要:超高强度钢是一种在常规合金结构钢基础上发展而成的超高强度高韧性合金钢。
其在航空等相关行业中的应用较为广泛,基于此,文章首先对超高强度钢的分类以及相关应用进行了分析,接着对其发展前景进行介绍,希望能够提供相关借鉴。
关键词:超高强度钢;发展;前景引言近年来,我国的军工、冶金、矿山、航空航天以及航海等相关的行业随着科学技术的进步得到了迅速的发展,这也就意味着将会有越来越多的目光集中在超高强度钢的研制以及应用中。
在常温状态下,超高强度钢的拉伸强度高于1470MPa,屈服强度则大于1380MPa。
在我国的航空起落架、精密齿轮以及高端轴承钢中对其的应用较为广泛,可以作为高端产品的理想选择。
超高强度钢的性能和很多因素都有着较大的关系,其中主要包括了化学成分、内部组织、负载以及外部环境等,这也就意味着未来超高强度钢的主要研究和发展方向要朝着低成本以及绿色环保的方向发展。
1.超高强度钢发展和应用目前我国超强钢主要可以从合金成分的总量和冶金特性来进行分类。
按照合金元素的总量,可以分为低、中高三种,其中,总合金含量在5.0wt%~10.0wt%之间,低合金超高强度钢低于5.0wt%,超过10.0wt%的是高合金超高强度钢,中间是中高合金超高强度钢。
按照其冶金特性,可以将其划分为低合金超高强度钢、二次硬化超高强度钢以及超高强度马氏体时效钢。
下面将根据第二类来说明。
1.1低合金超高强度钢的发展及应用情况低合金超高强钢是一种低合金马氏体结构钢,其合金元素含量低于5.0wt%,其主要原因是马氏体中的碳含量。
1950年,美国首先研制出AISI4340超高强钢,它的主要用途是用于飞机的升降平台。
采用 Mo、 Ni、 Cr、 Si、 Vi等主要合金元素,经淬火-低温回火处理后,其屈服强度超过1300 MPa。
该产品的碳含量应控制在0.30wt%~0.50wt%之间,以获得高强度、高塑性、高韧性和焊接性能。
汽车钢材强度等级划分
汽车钢材的强度等级划分通常根据其材料的力学性能和强度参数进行分类。
以下是常见的汽车钢材强度等级划分:
低强度钢(Low-Strength Steel):属于传统的钢材类型,强度较低。
主要用于车身结构的一些非承载部位和内饰部件。
中强度钢(Medium-Strength Steel):具有中等强度的钢材,可以提供一定的结构刚度和抗弯性能。
常用于车身结构的承载部位和部分安全关键部件。
高强度钢(High-Strength Steel):具有较高强度和优良的抗拉、抗压和抗弯性能。
高强度钢在提供车身刚度和抗冲击性能的同时,也能减轻车身重量。
常用于车身结构的关键部位和安全结构部件。
超高强度钢(Ultra-High-Strength Steel):具有极高的强度和优异的机械性能。
这类钢材通常由合金化钢、热处理钢和复合材料等构成,用于提供更高的刚度、抗冲击性能和安全保护。
常用于车身的安全关键部位和变形吸能结构。
- 1、下载文档前请自行甄别文档内容的完整性,平台不提供额外的编辑、内容补充、找答案等附加服务。
- 2、"仅部分预览"的文档,不可在线预览部分如存在完整性等问题,可反馈申请退款(可完整预览的文档不适用该条件!)。
- 3、如文档侵犯您的权益,请联系客服反馈,我们会尽快为您处理(人工客服工作时间:9:00-18:30)。
超高强度钢超高强度钢一般是指屈服强度大于1380MPa的高强度结构钢。
20世纪40年代中期,美国用AISI4340结构钢通过降低回火温度,使钢的抗拉强度达到1600~1900MPa。
50年代以后,相继研制成功多种低合金和中合金超高强度钢,如300M、D6AC和H一11钢等。
60年代研制成功马氏体时效钢,逐步形成18Ni马氏体时效钢系列,70年代中期,美国研制成功高纯度HP310钢,抗拉强度达到2200MPa。
法国研制的35NCDl6钢,抗拉强度大于1850MPa,而断裂韧度和抗应力腐蚀性能都有明显的改进。
80年代初,美国研制成功AFl410二次硬化型超高强度钢,在抗拉强度为1860MPa时,钢的断裂韧度达到160 MPa·m以上,AFl410钢是目前航空和航天工业部门正在推广应用的一种新材料。
中国于50年代初研制成功30CrMnSiNi2A超高强度钢,抗拉强度为1700MPa。
70年代初,结合中国资源条件,研制成功32Si2Mn2MoVA和40CrMnSiMoVA(GC一4)钢。
1980年以来,从国外引进新技术,采用真空冶炼新工艺,先后研制成功45CrNiMoVA (D6AC)、34Si2MnCrMoVA (406A)、35CrNi4MoA、40CrNi2Si2MoVA(300M)和18Ni马氏体时效钢,成功地用于制做飞机起落架、固体燃料火箭发动机壳体和浓缩铀离心机简体等。
目前超高强度钢已形成不同强度级别系列,在国防工业和经济建设中发挥着重要的作用。
现在,以改变合金成分提高超高强度钢的强度和韧性已很困难。
发展超高强度钢的主要方向是开发新工艺、新技术,提高冶金质量,如采用真空冶炼技术,最大限度降低钢中气体和杂质元素含量,研制超纯净超高强度钢;通过多向锻造和形变热处理,改变钢的组织结构和细化晶粒尺寸,从而提高钢的强度和韧性,例如正在发展的相变诱发塑性钢(TRIP钢)等。
一超高强度钢的合金成分、组织和特性(1)中碳低合金超高强度钢此类钢是通过淬火和回火处理获得较高的强度和韧性,钢的强度主要取决于钢中马氏体的固溶碳浓度。
含碳量增加,钢的强度升高;而塑性和韧性相应降低。
因此,在保证足够强度的原则下,尽可能降低钢中含碳量,一般含碳量在0.30~0.45%。
钢中合金元素总量约在5%左右,Cr、Ni和Mn在钢中的主要作用是提高钢的淬透性,以保证较大的零件在适当的冷却条件下获得马氏体组织,Mo、W和v的主要作用是提高钢的抗回火能力和细化晶粒等。
几种典型钢种的化学成分如表2·12.1。
该类钢通过淬火处理,在Ms点温度以下发生无扩散相变,形成马氏体组织。
采用适宜的温度进行回火处理,析出ε—碳化物,改善钢的韧性,获得强度和韧性的最佳配合。
提高回火温度(250—450℃回火)时,板条马氏体的ε—碳化物发生转变和残留奥氏体分解形成Fe3C渗碳体,钢的韧性明显下降,此现象称为回火马氏体脆性。
产生此种回火脆性的原因主要是由于钢中的硫、磷等杂质元素在奥氏体晶界偏聚和渗碳体沿晶界分布,降低了晶界结合强度。
300M钢等含有1.5%硅,能有效地仰制ε—碳化物转变和残留奥氏体分解,使钢的回火马氏体脆性温度提高到350~500℃。
硅在钢中只能提高回火马氏体脆性区的温度,但并不能减轻或消除此种脆性。
因此,只有降低钢中硫、磷等杂质元素的含量才能有效地消除超高强度钢的回火马氏体脆性。
中国研制的40CrNi2Si2MoVA钢是一种强度高,纯洁度要求严的低合金超高强度钢。
采用精炼脱硫的原材料,经过真空感应炉和真空白耗炉两次真空冶炼工艺,钢中硫和磷含量分别降低到0.002~0.003%和0.005~0.008%,明显改善了大截面锻件的横向塑性和韧性。
在抗张强度为1925MPa条件下,钢的断裂韧度达到85.1MPa√m。
经疲劳试验证明,用于制造飞机起落架可使寿命延长三倍以上,达到起落架与飞机机体同寿命的世界先进水平。
45CrNiMoVA和34Si2MnCrMoVA钢采用真空冶炼工艺,提高了钢的冶金质量。
当抗张强度在1600和1800MPa条件下,其断裂韧度分别达到105和93.6MPa√m。
用于制造中远程和近程固体燃料火箭发动机壳体取得了良好的效果。
(2)二-次硬化钢 H—11钢是最早研制成功和使用的中合金超高强度钢。
钢的含碳量约0.40%,含铬5%。
钢的淬透性高,一般零件在空气冷却条件下即可获得马氏体组织。
经500C 回火时,析出M2C(M表金属元素)和V4C3,产生二次硬化效应,钢的强度达到1962MPa以上。
该类钢具有较高的中温强度,除用于制做热作模具外还制做飞机发动机后框架等,在400~500℃工作条件下能承受较高的应力。
9Ni-4Co系列钢是高韧性超高强度钢,按照强度级别含碳量范围0.20~0.45%,通常使用的有HP9—4—20和HP9—4—30,含碳量分别为0.20%和0.30%。
该类钢经820℃加热后油淬,450~550℃回火,抗张强度为1400~1600MPa,断裂韧度达到90MPa√m以上。
AFl410钢近年来受到了航空和航天部门的极大重视,该类钢含有M、Co、Cr和Mo等合金元素(表2·12.2),经固溶和油淬处理形成高位错密度板条马氏体,在板条边界分布有少量残留奥氏体。
时效处理析出弥散分布的合金碳化物,从而获得高强度和高韧性。
从表2·12·2看出,钢中琉、磷含量控制到极低的水平,氮和氧分别为3ppm和7ppm。
因此,AFl410钢必须选用低硫、磷精料,采用真空感应和真空自耗重熔双联工艺,获得超纯净钢。
经油淬和时效处理,抗拉强度为1620MPa,断裂韧度达到190 MPa·m。
加入稀土金属可改变非金属夹杂物的形态和分布,进一步提高钢的韧性。
AFl410钢不仅强度高,韧性好,可焊性好,并且具有较高的抗应力腐蚀性能。
(3)马氏体时效钢该类钢含碳量极低,含有18~25%Ni。
当加热到高温时得到稳定的奥氏体组织,在空冷条件下可完全转变形成微碳马氏体。
Co在钢中的作用是提高Ms点,减少残留奥氏体量,降低Mo在马氏体中的固溶度,增加Mo的沉淀强化效应。
马氏体时效钢经固溶和时效处理,析出金属间化合物Ni3Mo、Ni3Ti和Ni3A1等产生弥散强化效应。
其中性能好,使用最广泛的是18Ni马氏体时效钢。
根据Mo和Ti含量不同,可获得几种强度级别的钢种(表2.12·3)。
马氏体时效钢在固溶处理后为超低碳马氏体组织,加工硬化指数低,冷加工成型性好。
在固溶状态下可焊性好,采用钨极氩气保护焊不需要预热和后热。
热处理时零件变形小,尺寸稳定。
但合金元素含量高致使钢的成本增高。
马氏体时效钢具有独特的优点,在较高的强度条件下使用安全可靠性好,固体火箭发动机壳体用18Ni马氏体时效钢,使用强度为1750MPa,浓缩铀离心分离机旋转简体用马氏体时效钢,使用强度达到2450MPa。
二超高强度钢的力学性能(1)超高强度钢的断裂韧性表2·12·4列出了几种典型超高强度钢的强度和韧性。
过去,随着使用强度不断提高,超高强度钢对缺口和裂纹的敏感性增大。
70年代初,随着断裂力学的发展,断裂韧度已成为衡量超高强度钢韧性的重要指标。
一般来说,钢的强度提高,往往断裂韧度降低。
如200级18Ni马氏体时效钢,当加载到钢的屈服强度时,不发生脆性断裂的部件表面允许存在的临界裂纹尺寸为8mm。
如果选用350级马氏体时效钢,当加载到屈服强度时,不发生脆性断裂允许存在的裂纹尺寸只有0.25mm。
如此微小的裂纹用无损探伤的方法是很难发现的。
因而就有发生低应力脆性破断的危险。
只有提高钢的断裂韧度,增加部件中容许存在的临界裂纹尺寸,才能提高钢的使用应力,充分发挥材料的潜力。
钢的断裂韧度取决于合金成分、组织结构和冶金质量。
图2 ·12.l为几种超高强度钢的断裂韧度(KIc)与抗拉强度(σb)的对应关系。
可以看出,材料的断裂韧度随抗拉强度升高而降低。
在相同的强度水平时,马氏体时效钢的断裂韧度最高。
不断提高超高强度钢的断裂韧度仍然是材料研究的一项重要任务。
(2)超高强度钢的抗腐蚀性能在介质环境中外加负荷远低于材料的过载断裂应力时超高强度钢就会发生应力腐蚀滞后脆性断裂。
超高强度钢在水介质中的应力腐蚀是氢致开裂过程,它受材料和环境中的氢所控制。
裂纹前沿的氢离子得到电子后生成氢原子进入钢中。
由于应力诱导扩散,氢原子向裂纹尖端最大三向应力处集聚,当富集的氢浓度达到某临界值时,材料就会发生滞后塑性变形,从而导致应力腐蚀裂纹的产生和扩展。
材料的应力腐蚀界限强度因子(KIscc)和裂纹扩展速率 (da/dt)反应了钢的本质特性,它主要取决于钢的化学成分、显微组织和冶金质量。
如图2.12,2所示,钢的KIxc随。
0.2升高而降低。
当钢的强度增加,使裂纹尖端的弹性应力场增强,促使氢向裂纹前沿集聚的驱动力增大,则比较容易达到氢浓度临界值,从而加速裂纹的形核和扩展。
选用高韧性材料,提高钢的纯净度和采用合适的热处理工艺都是提高钢的应力腐蚀滞后断裂性能的有效措施。
(3)超高强度钢的疲劳性能在承受交变载荷作用下超高强度钢的疲劳寿命主要取决于钢的疲劳强度极限和疲劳裂纹扩展速率(见2·8)。
几种超高强度钢的疲劳强度极限见表2.12.5。
钢的疲劳性能主要取决于钢的强度和韧性。
提高钢的冶金质量,改变钢中非金属夹杂物的形状、数量和分布对疲劳性能具有显著的影响。
三超高强度钢的新工艺、新技术(1)改进冶炼工艺采用真空自耗重熔或真空感应炉和真空自耗炉双联冶炼工艺,对改善超高强度钢的韧性有显著的效果。
断裂力学理论表明,钢的断裂韧度与钢中非金属夹杂物的平均间距的平方根成正比。
减少夹杂物的数量,增大夹杂物的平均间距,则断裂韧度提高。
图2·12·3为三种冶炼工艺的18Ni马氏体时效钢的KIc与σ0.2的对应关系。
可以看出,在相同强度下,双真空冶炼钢的KIc值最高。
飞机起落架用300M钢选用低硫、磷原料,采用双真空冶炼,钢中氢气降低到0.72ppm,硫含量降低到0.003%以下,明显改善大截面的横向塑性,横向断面收缩率与纵向的比值提高到0.80以上。
断裂韧度达到83MPa·m。
(2)改善热处理工艺 4340钢和300M钢采用1200℃高温淬火后,奥氏体晶粒尺寸由20μm增大到200μm左右。
由于高温加热,使碳化物充分溶解,减少第二相在晶界形核,并在马氏体板条边界形成厚100~200A残留奥氏体薄膜。
从而提高了钢的断裂韧度。
300M钢高温淬火后的断裂韧度提高到91.2 MPa·m。
但是由于晶粒粗大,冲击韧性明显下降。
形变热处理已经广泛用于提高超高强度钢的强度和韧性。