QJ1E47FMD发动机运动学及动力学仿真计算
发动机的动态模型及其调速仿真应用

×μ1 ×μ2 + Pbase。对于用执行器电控的发动机 ,各转
速工况下最大供油量由软件决定 ,在仿真计算过程
中
,取
μ 1
= 1。
采用方法 1加载 ,由于在不同的负荷 、不同的转速
工况下 ,其示功图均不相同 ,故需试验测取 ;实际工作
中 ,不可能测取所有示功图 ,中间点仍需通过插值获
取 ;并且 ,试验工作量大 。在试验数据足够的前提下 ,
© 1994-2010 China Academic Journal Electronic Publishing House. All rights reserved.
第 1期
杨 鲲等 : 发动机的动态模型及其调速仿真应用
41
图 1 曲柄连杆机构简图
p:气缸压力 ; A rea:活塞顶部表面积 ; Fp :活塞顶部 受力 ; Fn :活塞侧向力 ; Fl : 连杆轴向力 ; Fk : 曲柄径向 力 ; Ft :曲柄切向力 ; R:曲柄半径 ; l :连杆长度 ;α:曲轴 转角 ;β:连杆摆角 ;ω:曲轴角速度 ; M ei:瞬时单缸输出 扭矩 。 1. 2 示功图加载
(1 - 江苏大学机械工程学院 江苏镇江 212013 2 - 江苏大学汽车与交通工程学院 )
摘 要 :建立柴油机动态模型及对调速过程进行仿真 ,是柴油机实现电控的基础性工作 。针对柴油机电 子调速器参数整定实验量大且参数影响规律性不强的特点 ,本文建立了发动机运行过程的动态物理模 型 。利用该模型可分析各参数对发动机控制的影响进行仿真 ,并利用仿真的结果指导 6105Q 柴油机数 字式电子调速器的参数整定实验 。实验结果表明 ,该模型能够满足电子调速器参数仿真的要求 。 关键词 :电子调速器 仿真 物理模型 中图分类号 : TK414. 3 文献标识码 : A 文章编号 : 1671 - 0630 (2006) 01 - 0040 - 06
气流谐振发电机的计算流体动力学仿真方法

气流谐振发电机的计算流体动力学仿真方法王海龙;庄雷;马旭辉;刘奇;柯伟【摘要】气流谐振发电机作为一种引信电源在国外已经应用于多种型号引信,而在我国现有的实验方法和设备不能满足对气流谐振发电机进一步研究的要求.针对此问题,将计算流体动力学(CFD)方法引入气流谐振发电机分析.该方法与一般计算流体动力学仿真的不同点是:采用结构化网格,假设膜片在气流谐振发电机工作过程中始终是静止的,并对模型进行了简化处理,定义了时间步长.采用此方法对不同入口压力条件下气流谐振发电机的工作状况进行的仿真与理论分析和实验结果相吻合,而且本方法可以对局部和总体的不同时间的流场进行细致描述,这是实验方法不能实现的.%As a kind of fuze power,air driven fluidic resonance generator has been used in many fuzes aboard. The existing experimental method and facility can not satisfy the requirements of further research in air driven fluidic resonance generator. Aiming at this situation,a CFD method was introduced to the analysis of air driven fluidic resonance generator. This method used a structure mesh, which assumed that the diaphragm was always stable during the working process of air driven fluidic resonance generator, and the time step was delinked. By using this method, the simulation result showed that the performance of air driven fluidic resonance generator in different inlet pressure accorded with theoretical analysis and experiment result Further more, partial and general fluid field could be described in detail by this method, which could not be completed by experimental method.【期刊名称】《探测与控制学报》【年(卷),期】2012(034)003【总页数】6页(P29-34)【关键词】引信;气流谐振发电机;仿真【作者】王海龙;庄雷;马旭辉;刘奇;柯伟【作者单位】机电动态控制重点实验室,陕西西安710065;西安机电信息技术研究所,陕西西安710065;西安机电信息技术研究所,陕西西安710065;西安机电信息技术研究所,陕西西安710065;西安机电信息技术研究所,陕西西安710065【正文语种】中文【中图分类】TJ430.20 引言电源作为引信的重要组成部件之一,常用的储备电池,有化学电源、热电池等,这种电池能量较大,经长期储存后发电噪音大、电压不稳,且体积大、机构复杂、通用性差。
液体火箭发动机起动过程的动态仿真计算

液体火箭发动机起动过程的动态仿真计算
液体火箭发动机起动过程的动态仿真计算可以包括以下几个方面的内容:
1. 燃料供给系统:通过模拟燃料供给系统中的燃料泵、阀门等组件的工作过程,计算燃料的流量和压力变化。
模拟燃料的进口流量和压力随时间的变化,并结合燃油喷嘴的特性,计算燃料在发动机燃烧室中的分布情况。
2. 燃烧室:考虑燃烧室中的压力、温度、速度等参数的变化情况,模拟燃烧室中燃料和氧化剂的混合、燃烧过程。
根据燃烧室中的工作状态,计算燃料的燃烧效率等相关指标。
3. 推力系统:通过综合考虑燃料的燃烧产生的高温高压气体以及喷嘴的设计特性,计算发动机产生的推力大小和推力方向的变化。
同时,根据推力的作用方向和大小,计算火箭的加速度和速度变化。
以上是液体火箭发动机起动过程的动态仿真计算的基本内容,根据实际需求和模型复杂度的不同,还可以包括更多的细节。
实际的仿真计算往往需要借助专业的仿真软件,例如MATLAB、Simulink等,通过建立相应的数学模型,进行计算和模拟。
同时,还需要根据实际的发动机参数和工作条件,对仿真模型进行验证和调整,以保证计算结果的准确性和可靠性。
基于MATLAB的汽车动力性模拟仿真方法
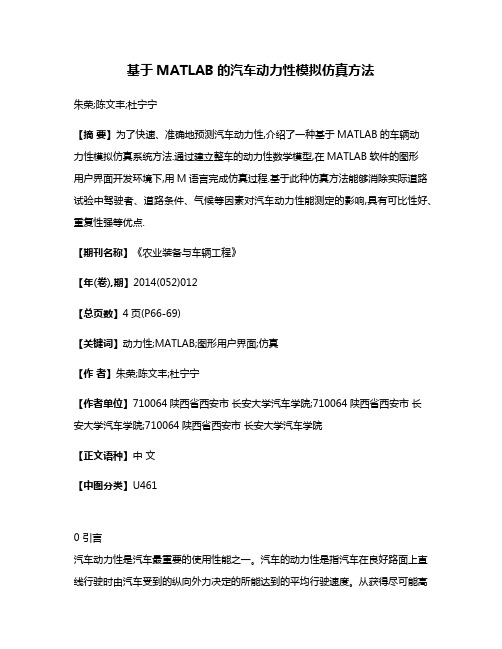
基于MATLAB的汽车动力性模拟仿真方法朱荣;陈文丰;杜宁宁【摘要】为了快速、准确地预测汽车动力性,介绍了一种基于MATLAB的车辆动力性模拟仿真系统方法.通过建立整车的动力性数学模型,在MATLAB软件的图形用户界面开发环境下,用M语言完成仿真过程.基于此种仿真方法能够消除实际道路试验中驾驶者、道路条件、气候等因素对汽车动力性能测定的影响,具有可比性好、重复性强等优点.【期刊名称】《农业装备与车辆工程》【年(卷),期】2014(052)012【总页数】4页(P66-69)【关键词】动力性;MATLAB;图形用户界面;仿真【作者】朱荣;陈文丰;杜宁宁【作者单位】710064陕西省西安市长安大学汽车学院;710064陕西省西安市长安大学汽车学院;710064陕西省西安市长安大学汽车学院【正文语种】中文【中图分类】U4610 引言汽车动力性是汽车最重要的使用性能之一。
汽车的动力性是指汽车在良好路面上直线行驶时由汽车受到的纵向外力决定的所能达到的平均行驶速度。
从获得尽可能高的平均行驶速度的观点出发,汽车的动力性主要可由三方面的指标来评定:(1)汽车的最高车速;(2)汽车的加速时间;(3)汽车的最大爬坡度[1]。
MATLAB是一款主要面对科学计算、可视化和交互式程序设计的高科技计算环境的软件,它集数值分析、矩阵计算、科学数据可视化和非线性动态系统建模与仿真等许多强大功能于一体,能满足服务于科研、工程设计和科学领域的许多有效数值计算的需要[2]。
利用MATLAB对汽车动力性进行建模和仿真,能够清晰地清楚汽车的各个参数的变化对汽车动力性的影响情况,有利于在汽车设计及改进时参数的选取。
1 动力性仿真模型的建立1.1 发动机外特性拟合模型当汽车发动机节气门全开时,发动机的功率p、转矩T以及燃油消耗率b与发动机转速n之间的关系曲线称为发动机外特性曲线[1]。
在进行发动机动力性计算时,我们只需获得转矩和转速之间的关系即可。
汽车发动机起动过程的动力学仿真_李红朋

800 r/m in所需的时间不超过 0. 4 s,其起动过程的动
力学模型和边界条件为 :
Te + Tg - TF - TL - Tre = Jω
∫ 60
2π
t
ωd
0
t
≥
800
,
( 17)
t ≤ 0. 4
式中 : Te ———电机的驱动力矩 ; J ———发动机机组与电机机组转换在曲轴上的转
动惯量 ;
© 1994-2010 China Academic Journal Electronic Publishing House. All rights reserved.
第 28卷第 6期 李红朋 ,等 : 汽车发动机起动过程的动力学仿真
摩擦阻力矩计算公式为 :
Tv
=
0.
26GLs r | ω
K| .
( 10)
式中 : G———单个气缸内气门的数量 ;
Ls ———气门弹簧的载荷 ; ω———曲轴角速度.
1. 4 附属部件运行阻力矩 Ta
Ta 包括水泵 、机油泵 、燃油泵 、发电机等附属部件
的运行阻力矩及空载下曲轴和凸轮轴的磨擦阻力矩 ,
其输出扭矩跟踪发动机曲轴阻力矩变化 ,将大大增加
电机控制器件的开关频率 ,对元件寿命产生不利影响.
本文根据电机低速下的恒扭矩特性 ,对电机采取最大
转矩 /电流控制 ,保证 ISG电机在低速下按最大扭矩运
行 ,以满足发动机起动过程的动力性要求.
3 ISG电机驱动控制与建模
3. 1 ISG电机的数学模型 ISG电机为永磁同步电机 ,本文采用矢量控制对
5
活塞摩擦阻力矩由活塞环摩擦阻力矩
TF
和
液体火箭发动机起动过程的动态仿真计算

液体火箭发动机起动过程的动态仿真计算建筑工地材料管理是确保工地所需材料的供应、储存、使用和管理的过程。
有效的材料管理可以提高施工效率、降低成本并确保工程质量。
以下是一些建筑工地材料管理的关键要点:1.采购计划和供应链管理:根据施工计划和需求,制定材料采购计划,包括确定所需材料的种类、规格、数量和供应时间等。
建立和维护与供应商的良好合作关系,使供应链畅通,并确保及时供应所需材料。
2.材料验收:在材料到达工地之前,进行严格的验收,确保所采购的材料符合规格和质量要求。
验收包括检查材料的外观、尺寸、标识和质量证明文件等。
3.材料储存和保管:建立合理的仓储系统和安全储存区域,以确保材料的安全、干燥和防盗。
分类储存不同类型的材料,遵循先进先出原则,保持清洁和整齐,并提供适当的标识和清单。
4.材料使用和计划控制:根据施工计划和实际需求,合理安排并记录材料的使用。
制定并执行材料使用计划,避免浪费和过度采购,提前储备所需材料,确保施工进度的顺利进行。
5.废料和回收利用:将废料进行分类和妥善处理,实施合理的废物管理。
对可回收的材料进行回收利用,以减少浪费和对环境的负面影响。
6.追溯和记录:建立材料追溯和记录系统,记录材料的采购、验收、储存、使用和废弃等信息。
通过建立档案和文档,可以跟踪和追溯材料的来源和使用情况。
7.监督和培训:建立监督机制,定期检查和评估材料管理的执行情况。
提供培训和指导,确保所有相关人员了解材料管理的重要性和操作要点。
综上所述,合理的建筑工地材料管理对于提高施工效率、控制成本和保证工程质量至关重要。
通过计划采购、严格验收、有效储存和使用、废料处理和记录追溯等措施,可以实现优秀的材料管理。
液体火箭发动机起动过程的动态仿真计算

液体火箭发动机起动过程的动态仿真计算
液体火箭发动机起动过程的动态仿真计算涉及到许多因素,包括燃料供给系统、点火系统、燃烧室压力和温度的变化、喷嘴推力等关键参数的计算。
首先,需要确定液体燃料的流量和压力,液体燃料包括燃料和氧化剂。
根据燃料的供给系统设计,可以计算出燃料的流量和压力随时间的变化。
接下来,需要确定点火系统的工作原理和触发时机。
根据点火系统的设计和点火时刻,可以确定点火点的温度和压力变化。
随后,根据燃烧室的设计和燃料供给系统的流量和压力,可以计算出燃烧室内的压力和温度随时间的变化。
这需要考虑燃烧室内的热力学效应和燃料的燃烧速度。
最后,根据燃气的压力和温度,可以计算出喷嘴的推力。
喷嘴的推力取决于燃料的流量、压力和喷嘴的设计。
通过对以上过程的仿真计算,可以得到火箭发动机起动过程中关键参数随时间的变化情况,如燃料流量、压力和温度的变化,喷嘴推力的变化等。
这些数据可以用于分析火箭发动机的性能和优化设计。
需要注意的是,火箭发动机起动过程的动态仿真计算涉及到液体力学、热力学、燃烧学等多学科知识,因此需要综合利用相关的模型和数值计算方法进行计算。
同时,需要考虑计算过程
中的误差和不确定性,以及不同工况下的不同影响因素,以提高计算的准确性和可靠性。
风力发电机组主机架动力学仿真

风力发电机组主机架动力学仿真风力发电机组主机架动力学仿真风力发电机组是一种利用风能转化为电能的设备。
其核心部件是主机架,它承载着风轮、发电机等重要组件。
主机架的动力学仿真是设计和优化风力发电机组的重要工作之一。
本文将按照逐步思考的方式,介绍风力发电机组主机架动力学仿真的步骤。
第一步:建立数学模型主机架的动力学仿真需要建立一个数学模型,以描述主机架的运动和力学特性。
首先,考虑主机架的几何形状和材料特性,确定主机架的刚度和质量分布。
然后,基于牛顿第二定律,建立主机架的运动方程。
此外,还需考虑风轮叶片和发电机等附加质量对主机架的影响,将其纳入模型中。
第二步:确定边界条件在进行仿真之前,需要确定主机架的边界条件。
这包括风速、风向和风轮转速等外部环境条件,以及主机架的初始位置和速度等内部条件。
边界条件的选择对仿真结果具有重要影响,需根据实际情况进行准确确定。
第三步:求解运动方程利用数值计算方法求解主机架的运动方程。
可以采用常用的数值积分方法,如龙格-库塔法或欧拉法,对主机架的运动进行离散化处理。
通过迭代计算,可以得到主机架在不同时间点上的位置和速度。
第四步:分析仿真结果根据仿真结果,可以对主机架的动力学性能进行评估和分析。
可以计算主机架的振动幅值、频率和应力等参数,以评估其结构的稳定性和可靠性。
此外,还可以分析主机架在不同风速和转速下的响应特性,为优化设计提供参考。
第五步:优化设计根据仿真结果,对主机架进行优化设计。
可以通过调整主机架的几何形状、材料特性和连接方式等,改善其动力学性能。
为了有效地进行优化设计,还可以利用多目标优化算法,综合考虑结构的稳定性、可靠性和经济性等方面的要求。
总结:风力发电机组主机架动力学仿真是一项重要的工作,可以帮助设计师评估主机架的结构性能、分析其响应特性,并为优化设计提供指导。
通过逐步思考,建立数学模型、确定边界条件、求解运动方程、分析仿真结果和优化设计,可以逐步深入地进行主机架动力学仿真工作,为风力发电机组的设计和优化提供有效支持。
- 1、下载文档前请自行甄别文档内容的完整性,平台不提供额外的编辑、内容补充、找答案等附加服务。
- 2、"仅部分预览"的文档,不可在线预览部分如存在完整性等问题,可反馈申请退款(可完整预览的文档不适用该条件!)。
- 3、如文档侵犯您的权益,请联系客服反馈,我们会尽快为您处理(人工客服工作时间:9:00-18:30)。
QJ147FMD发动机运动学及动力学仿真计算
一、QJ147FMD发动机的参数:
标定转速:6000r/min 曲轴半径:19.6mm 连杆长度:80mm 缸径:47mm
曲柄连杆比:0.245
二、曲柄连杆机构再ADAMS软件中的仿真计算:
上图是燃气的爆发压力和往复惯性力以及合力的曲线图。
上图是用ADAMS软件仿真计算出的往复惯性力和理论计算的比较图。
粉色——理论计算,蓝色——仿真计算。
理论计算:max=745N,min=-1230N; 仿真计算:max=546.6316N,min=-901.3991N.
出现上诉的原因个人理解是:
(1)仿真计算的往复加速度=理论计算的往复加速度,那么产生仿真计算所得到的往复惯性力和理论计算所得到的往复惯性力之所以不同的原因就在于往复质量的计算;(2)在理论计算中,往复质量的计算是由活塞组的质量+连杆小头的质量,而在小头质量的换算过程中教科书上介绍的方法一般有两种,即两质量和三质量系统来等效代替
连杆。
并且可以确定的是用三质量系统来代替两质量系统计算的更为精确只是计算起来比较困难。
那么我们可以推想如果可以的话用四质量系统来代替连杆所得到的结果应该比三质量系统来代替连杆是不是更为精确?如果答案是肯定的,那么我们就有理由相信:用无数个质量点来代替连杆系统所计算得到的结果将会比2质量系统来代替连杆计算的精度要高很多,这一点用ADAMS软件可以轻松的做到。
(3)现在我们来做一个对比,即同一个连杆用两质量系统和三质量系统分别来代替的时候,同一个连杆在换算到连杆小头质量是如何变化的?很容易想到用三质量系统来代替连杆的时候换算到连杆小头的质量应该比两质量换算到连杆小头的质量要小,那么我们有理由相信:当用无数个质量点来代替连杆的时候,换算到连杆小头的质量要比教科书上按两质量系统来代替连杆换算到连杆小头出的往复质量要小。
(4)由于摩托车的发动机的转速很高,所以他的往复加速度很大。
我们这次所研究的发动机的加速度的数量级:几千。
可见,当往复质量减少1%时,则往复惯性力将减少几十牛。
(这也是我们在设计高速发动机的时候要注意减少往复惯性质量的原因,而我们按照理论公式来计算的时候,实际上已经人为的增大了往复质量。
)由以上的分析,我们有理由认为用ADAMS仿真软件来进行计算,所得到的结果比按纯理论方法所计算的更为精确。
三、主轴径的受力分析:
(1)我们用ADAMS软件,将所研究的发动机的轴径作为刚体并且还考虑到了轴承的安装位置以及曲柄系统的质心位置的影响之后所得到的曲轴主轴径的受力分析图。
上图是曲轴的两个轴径受力的极坐标图。
上图是两个主轴径在全局坐标系下,测得的X,Y方向的受力图。
红色——X, 蓝色——Y.在分析的时候,我们将两个主轴承沿着气缸中心线对称分布,由于曲柄系统的质心并没有在气缸中心线上,所以,两个主轴径的所受的X,Y方向的力并不是完全相同。
根据分析,我们可以得到在X方向:(轴径1 max=477.3892N min=-514.7356N; 轴径2 max=340.5474N min=-427.8788N);在Y方向:(轴径 1 max=6293.3142N min=-95.8769N轴径 2 max=6158.7966N min=-232.8003N)
(2)当改变其中一个轴承的位置时,测得的曲轴轴径的受力图(全局坐标系):
将轴承1的位置改变13mm(轴向移动)后的曲线:
X方向:
轴承1 max=381.9113N min=-411.7883N 轴承2 max=435.8553N min=-502.8516N
Y方向:
轴承1 max=5034.6514N min=-76.7015N 轴承2 max=7417.4595N min=-251.9444N 四、曲柄销轴径及连杆轴承受力分析图:
五、仿真曲线和理论计算曲线对比分析:
红颜色——ADAMS仿真得到的曲线
蓝颜色——理论计算得到的曲线
(上图是主轴径的极坐标曲线图)
红颜色——理论计算的曲线蓝颜色——仿真得到的曲线
左图:X方向的受力比较图,趋势一样。
理论:max=792.2713N min=-814.9004N 仿真:max=901.7466N min=-817.4795N
右图:Y方向的受力比较图,趋势一样。
理论:max=11989.8167N min=-690.6301N 仿真:max=12452.1109N min=-328.521N
上图是曲柄销受力的仿真和理论计算得到的极坐标图形的比较。
曲柄销x方向的受力图曲柄销y方向的受力图
上图是曲柄销所受的力在X,Y方向的对比图:通过对比可以发现理论计算和仿真得到的曲线有很好的吻合。
红颜色——仿真得到的曲线蓝颜色——理论计算得到的曲线
X方向:理论:max=4960N min=-845N 仿真:max=5104.251N min=-904.4363N
Y方向:理论:max=2070N min=-10300N 仿真:max=2037.2877N min=-10458.1308N。