压铸件设计要点
压铸件设计要点

压铸件经验之谈压铸件设计经验:注:由于合金金属散热较好,很难形成瞬间难却时候局部先后冷却现象。
而合金的收缩率也很小,很难难导致塑料产品缩水现象。
故,设计压铸件时候,不需要严格的厚度相对均匀。
注:压铸件厚度的建议。
铝、镁压铸件厚度,当面积小于25CM平方时,最小厚度是0.8,合适厚度是2.0.当面积在25~100之间,最小厚度是1.2,合适厚度是2.5.当面积在100~500之间,最小厚度是1.8,合适厚度是3.0.当面积在500以上,,最小厚度是2.5,合适厚度是3.5.锌金厚度要求,可以设计为:铝合金厚度-0.3~-0.5。
注:压铸件的其他建议。
1.过度之处需要设计圆角。
2.厚度需要均匀过度。
3.最小孔为0.5MM,为了模具的寿命。
4.避免尖角。
5.避免模具上产生薄钢。
注:拔模角一般为2度。
注:压铸件因为是金属材料,设计时候,倘若精度不够,后期可以切削加工。
注:另外,螺纹及螺纹孔,模具费用是比较贵的,产品量少的情况下,建议后期加工。
什么是压铸?压铸是一种利用高压强制将金属熔液压入形状复杂的金属模内的一种精密铸造法。
压铸的设备:压铸机由于压铸合金的不同,在基本上可分成二大类,即冷室机、热室机。
冷室机适合铜、镁、铝等高温合金之压铸,而热室机则应用于锌、锡、铅等压铸机一般能提供150万帕注射压力。
压铸件采用的材料:铝合金铝镁系铝锌系铝铜系锌合金镁合金注:由于压铸材料铝合金含杂质太多,不能氧化便面处理。
氧化的效果很不理想我司可提供压铸模具生产,压铸产品生产。
工程部可以免费提供设计技术支持。
Q—Q:369589423。
压铸工艺及压铸模具设计要点

压铸工艺及压铸模具设计要点压铸工艺及压铸模具设计要点压铸是一种利用压力将液态金属注入模具中,通过冷却凝固形成定形零件的制造方法。
压铸产品在重量、强度、尺寸方面都有非常高的准确性和稳定性,被广泛应用于汽车、摩托车、电子、通讯设备、家电等产业中,成为目前工业生产中不可或缺的一种制造技术。
下面将从压铸工艺及压铸模具设计要点两个方面进行阐述。
一、压铸工艺1. 材料准备:首先需要准备液态金属,一般使用的是微量合金钢、铝合金、镁合金、铜合金等牌号。
材料的纯度、质量直接影响产品的质量。
2. 模具设计:由于压铸的成形过程主要依靠模具的形状和大小,所以模具设计非常重要。
模具一般由流道、高压室、模腔等主要部分组成,需要用CAD 设计软件绘制出预想的产品三维模型,然后进行分析预测。
3. 夹具安装:很多压铸厂家采用自动化流水线作业,这样可以让夹具自动加载模具。
夹具的准确安装和保持最佳状态对产品稳定的尺寸和质量有着至关重要的作用。
4. 液态金属注入:注入过程需要注意金属温度的控制,因为如果注入过热的金属会造成热缩,也会加快金属与模具接触面损耗的速度。
注入金属的速度和压力也需要掌握恰当的水平。
5. 压力保持和冷却:完成注入后,需要将模具保持一定的压力,通常设置的保持时间在15-20秒之间,直到金属凝固成型,然后通过水冷却或空气冷却来加速金属的冷却,降低模腔温度,以便后续顺利脱模。
6. 脱模:经过强制冷却后,模具表面的金属固化成型,可以脱模取出。
如果模具内存在脱模困难的产品,则采用震动或喷水技术来辅助脱模。
二、压铸模具设计要点1. 模具材料:模具材料的决定因素是金属的特性和成本。
有些材料具有良好的抗磨损性和耐腐蚀能力,例如CrMoV 钢,有些材料则具有良好的导热性和导电性能,例如铝合金。
选用模具材料需要考虑两方面因素:一、材料的使用寿命;二、成本。
2. 模具结构:模具结构需要考虑到成品的尺寸、线条、强度和表面质量等因素。
通常情况下,模具结构应该是四侧对称的,以确保在生产过程中的稳定性和成品准确性。
压铸件设计规范详解

压铸件设计规范详解压铸件是指利用压铸工艺将熔融金属注入模具中,经过凝固和冷却后得到的零件。
由于该工艺具有生产效率高、成本低、制造精度高等优点,被广泛应用于汽车、航空航天、电子等领域。
为了保证压铸件质量和安全性,需要遵循一系列的设计规范。
下面将详细介绍压铸件设计规范。
一、材料选择1.铝合金:常用的有A380、A383、A360等。
根据使用条件和要求,选择合适的铝合金材料,确保压铸件具有良好的强度和塑性。
2.压铸型腔材料:常用的有铜合金、热处理工具钢等。
要选择适当的材料,以耐高温和磨损。
二、模具设计1.模具设计必须满足压铸件的要求,保证铸件的尺寸精度和表面质量。
2.模腔设计要考虑到铸件收缩率、冷却速度等因素,以避免产生缺陷和变形。
3.合理安排模具冷却系统,保证压铸件内部和表面的冷却均匀。
三、尺寸设计1.压铸件的尺寸设计应符合产品技术要求和工艺要求,确保功能和安装的需要。
2.避免设计尺寸太小或太薄,以免产生破裂和变形。
3.设计保证良好的表面质量,避免设计中出现接触不良、挤压不足等问题。
四、壁厚设计1.壁厚不应过薄,以免影响产品的强度和刚性。
2.避免壁厚过大,以减少成本和缩短冷却时间。
3.边缘和角部应注意壁厚过渡,避免产生应力集中。
五、设计角度和半径1.设计时应根据铝合金的流动性选择合适的角度和半径。
2.避免设计尖锐角度和太小的半径,以免产生气孔和挤压不足。
3.设计角度和半径应保持一定的一致性,避免因设计不当导致铸件变形和收缩不均匀。
六、设计放射状构件1.当压铸件具有放射状构件时,要合理设计放射状梁的位置和数量,以充分利用材料,并减少成本。
2.注意放射状构件的设计不应影响整体结构的强度。
七、设计排气系统1.设计时要考虑到铸件内部的气孔、气泡等气体排出问题。
2.合理安排和设计排气道,以保证良好的注模效果和铸件质量。
八、设计孔和螺纹1.设计孔和螺纹时应遵循标准规范,确保质量和安装的可靠性。
2.孔和螺纹的位置和尺寸应符合产品要求,保证压铸件的功能和使用要求。
五金、铝合金压铸件的结构设计、生产工艺和相关模具

五金、铝合金压铸件的结构设计、生产工艺和相关模具一、铝合金压铸件的结构设计作为五金制品的一种,铝合金压铸件在工业生产中具有很重要的作用,它广泛应用于汽车零部件、摩托车零部件、自行车零部件、电工设备、航空航天领域等。
铝合金压铸件的结构设计是非常重要的,它直接影响到产品的质量和使用性能。
1.结构设计原则(1)设计合理性:要求产品设计合理,能够满足产品的使用要求和生产工艺要求。
(2)易于加工:要求产品的结构设计能够方便加工和生产,减少生产成本。
(3)适应性强:要求产品的结构设计能够适应不同的工艺要求和使用环境。
2.结构设计要点(1)壁厚:对于铝合金压铸件来说,壁厚的设计是非常重要的,壁厚太厚容易造成收缩不均匀、气泡、裂纹等问题,壁厚太薄则会影响产品的强度和稳定性。
(2)加工余量:在设计铝合金压铸件时需要考虑到加工余量,保证产品在结束后进行加工时不会出现问题。
(3)结构形式:产品的结构形式要具有设计的合理性和美学性,能够顺应现代的审美观念。
(4)浇口设计:浇口的设计直接影响到产品的成型质量,需要设计合理的浇口位置和形式。
3.结构设计方法(1)CAD设计:利用CAD软件进行产品的三维设计和分析,可以有效地减少设计过程中的错误和成本。
(2)模具设计:根据产品的结构设计进行模具的设计,保证产品的生产质量和效率。
二、铝合金压铸件的生产工艺铝合金压铸件的生产工艺是一个复杂的过程,需要结合材料特性和模具设计才能完成。
生产工艺的质量直接关系到产品的质量和性能。
1.型腔填充铝合金压铸件的成型过程是通过将铝合金在一定的温度下充入模具中,并施加一定的压力来完成的。
型腔填充是成型过程中的关键一步,需要确保模具内的铝合金能够充分填满型腔,避免气泡和缩松等问题的产生。
2.固化冷却在型腔充填完成后,需要将模具进行固化冷却,使铝合金在模具中凝固成型。
固化冷却过程中需要控制温度和时间,保证产品的成型质量。
3.反压和除渣在成型后的铝合金压铸件表面可能会出现一些氧化物和杂质,需要进行反压和除渣处理,保证产品的表面质量。
压铸件零件设计的注意事项

压铸技术基础(一)压铸的几个基本问题铸件的收缩根据压铸的特点,铸件的收缩规律大致如下:1. 冷却凝固时,包紧成型零件,并受这些零件所阻碍,收缩量就比较小2. 薄壁铸件的收缩量比厚壁铸件小3. 大铸件的收缩百分率比小铸件的收缩百分率小4. 压铸成形后,留模时间愈长,收缩量愈小5. 形状复杂的铸件比简单铸件收缩量小6. 同一铸件的不同尺寸部位,各处于上不同的情况时,各自的收缩率有可能不相同7. 铸件的收缩是在实体上产生的,故在空档部位上,有时它的实际收缩可能使该部位的尺寸变大此外,铸件的收缩可能与工艺因素,操作方面(如分型面的清理、涂料涂层的厚薄)有关。
上述的收缩规律性只是针对一些特定条件而言,生产中,常常应根据实际情况加以综合的考虑。
内浇口速度为便于生产中对内浇口速度的选定,将铸件的壁厚与内浇口速度的关系列于表中。
在选取用内浇口速度时,可以考虑下列情况1. 铸件形状复杂时,内浇口速度可高些2. 合金浇入温度低时,内浇口速度可高些3. 合金和模具材料的导热性能好时,内浇口速度应高些p b —压室内作用于金属上的压力(公斤/厘米2),此处实为填充比压,符号应为pb c,但为叙述方便,直接用p b列出h s —压室的压力头高度(厘米)v c —冲头速度(厘米/秒)但是,对于压铸过程来说,对上述表示式可作如下的分析:内浇口处通过金属流之前的压力p n,在模具上开有足够的排气道的情况下,相当于大气压力,而压室内作用于金属上地压力p b(实为填充比压)则甚大于大气压力,故移项后,p b-p n的差值与p b十分接近,所以p n项可忽略不计。
内浇口的压力头高度h n和压室的压力头高度相差只有几厘米,因此,可按相等看待,在等式的两边的抵消而消除。
冲头速度v c与内浇口速度v n相比,由于面积F S和F n相差十几倍甚至几十倍,故冲头速度总是比内浇口速度小十几倍或几十倍,况且在伯努利方程式中还是一个平方数,因此,v c也不予计入。
压铸件的基本结构设计内容

压铸件的基本结构设计内容咱们今天聊一聊压铸件的基本结构设计内容。
可能你一听“压铸件”三个字,心里就想着这又是什么高大上的东西,其实吧,压铸件就跟咱们平时看到的那些金属零件差不多,差别就是它们是通过压铸工艺来做出来的,简单说,就是把熔化的金属像倒水一样压进一个模具里,冷却固化后就成了咱们需要的形状。
好啦,说到压铸件的设计内容,其实可以分为好几个方面来讲。
首先就是模具设计。
咱们先不说别的,单单这个模具就很考究了。
压铸模具的设计就像是为每个压铸件量身定做衣服,不合适的话,结果就没法穿出来,穿不上也就算了,还可能会导致材料浪费、成型不良等等一大堆麻烦。
模具的设计要求非常高,既要保证零件的精准度,又得考虑到金属在模具里流动的状态,必须考虑冷却系统,甚至是脱模的角度,像是个全方位的“专业护理”。
别看模具小,做不好就能让整个生产过程泡汤,真的是“细节决定成败”啊。
咱们得聊聊压铸件的结构设计。
这个“结构”啊,其实就是零件的形状、厚度分布、壁厚均匀度等等一系列的事。
想象一下,你在做一道菜,如果配料不匀,或者火候控制不好,那味道肯定会差,压铸件也是一样。
设计的好,能让熔融金属在模具里流得顺畅,零件出来时就能不留气孔、不变形,质量自然过关。
特别是壁厚,千万不能忽视!有的地方厚的像土豆饼,有的地方薄得像纸片,做出来的零件要么沉,要么轻,怎么可能不出问题呢?所以啊,这壁厚的均匀性就像做菜时的火候,一定要掌握得当。
然后呢,咱得说说压铸件的材料选择。
这也是个大问题。
有些零件要承受大负荷,有些则得耐高温,甚至得防腐蚀,材料得根据这些要求来选。
可能是铝合金,有时候可能是锌合金,每种金属的性质不一样,决定了它适用的范围和效果。
所以呢,选材可不是随便选选的,而是需要经过精密计算的。
想象一下,你买东西时会货比三家,那在压铸件的设计中,选材也是一样,要根据具体的需求来决定。
对了,还得提一提设计时的考虑问题,比如说气体排放问题。
金属熔化后,容易产生气体,若是设计不合理,这些气体可能就会被困在零件里面,导致气孔、气泡,影响零件的强度。
压铸件产品设计注意规范

圆角半径R 0.5 0.5
压铸合金 圆角半径R
铝、镁合金
1.0
铜合金
1.5
我司现采用的圆角一般取R1.5。
表3 铸造圆角半径的计算(mm)
相连接两壁的厚度
图例
圆角半径
相等壁厚
rmin=Kh rmax=Kh R=r+h
不等壁厚
r≥(h+h1)/3 R= r+(h+h1)/2
说明:①、对锌合金铸件,K=1/4;对铝、镁、合金 铸件, K=1/2。
0~0.3% 2 % ~4%
说明:①、表内深度系指固定型芯而言,,对于活动的单个型芯其深度还可以适当 增加。
②、对于较大的孔径,精度要求不高时,孔的深度亦可超出上述范围。
对于压铸件自攻螺钉用的底孔,推荐采用的底孔直 径见表6。
表6 自攻螺钉用底孔直径(mm)
螺纹规格d M2.5 M3 M3.5 M4 M5 M6
一般采用的加强筋的尺寸按图 1选取:
t1=2 t /3~t;t2=3 t /4~t; R≥t/2~t; h≤5t; r≤0.5mm (t—压铸件壁厚,最大不超过
6~8mm)。
四、铸孔和孔到边缘的最小距离
1)铸孔
压铸件的孔径和孔深,对要求不高的孔可 以直接压出,按表5。
表5 最小孔径和最大孔深
②、计算后的最小圆角应符合表2的要求。
2) 脱模斜度
设计压铸件时,就应在结构上留有 结构斜度,无结构斜度时,在需要之处, 必须有脱模的工艺斜度。斜度的方向, 必须与铸件的脱模方向一致。推荐的脱 模斜度见表4。
表4 脱模斜度
合金
配合面的最小脱模 非配合面的最小脱
斜度
模斜度
α
外表面α 内表面β 外表面α 内表面β
压铸件结构设计和压铸工艺
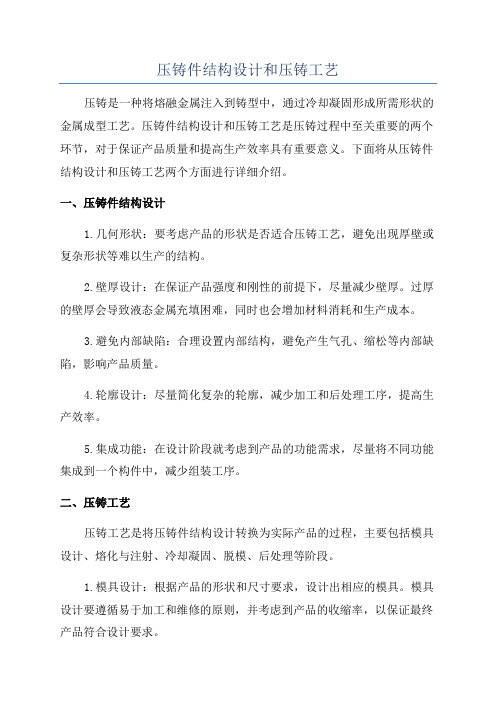
压铸件结构设计和压铸工艺压铸是一种将熔融金属注入到铸型中,通过冷却凝固形成所需形状的金属成型工艺。
压铸件结构设计和压铸工艺是压铸过程中至关重要的两个环节,对于保证产品质量和提高生产效率具有重要意义。
下面将从压铸件结构设计和压铸工艺两个方面进行详细介绍。
一、压铸件结构设计1.几何形状:要考虑产品的形状是否适合压铸工艺,避免出现厚壁或复杂形状等难以生产的结构。
2.壁厚设计:在保证产品强度和刚性的前提下,尽量减少壁厚。
过厚的壁厚会导致液态金属充填困难,同时也会增加材料消耗和生产成本。
3.避免内部缺陷:合理设置内部结构,避免产生气孔、缩松等内部缺陷,影响产品质量。
4.轮廓设计:尽量简化复杂的轮廓,减少加工和后处理工序,提高生产效率。
5.集成功能:在设计阶段就考虑到产品的功能需求,尽量将不同功能集成到一个构件中,减少组装工序。
二、压铸工艺压铸工艺是将压铸件结构设计转换为实际产品的过程,主要包括模具设计、熔化与注射、冷却凝固、脱模、后处理等阶段。
1.模具设计:根据产品的形状和尺寸要求,设计出相应的模具。
模具设计要遵循易于加工和维修的原则,并考虑到产品的收缩率,以保证最终产品符合设计要求。
2.熔化与注射:将所需的金属材料加热至液态,然后通过注射机将熔融金属注入到模具中。
注射过程需要控制注射速度和压力,保证金属充填完整且无气泡。
3.冷却凝固:在模具中进行冷却凝固,使注入的金属逐渐凝固。
冷却过程需要控制温度和时间,以保证产品的结晶组织均匀性和性能稳定性。
4.脱模:凝固后的产品从模具中取出,包括冷却水冲洗和振动脱模等工序。
脱模过程需要注意避免产品的变形和损坏。
5.后处理:包括修磨、去毛刺、清洗、表面处理等工序。
后处理旨在提高产品表面质量和机械性能,并满足特定的外观要求。
总结:压铸件结构设计和压铸工艺是相互关联的,一个合理的结构设计可以提高生产效率和产品质量,而一个良好的压铸工艺可以保证结构设计的实施效果。
因此,在进行压铸件结构设计和压铸工艺选择时,需要综合考虑产品的功能要求、材料特性、生产成本等因素,以达到最佳的工艺效果。
- 1、下载文档前请自行甄别文档内容的完整性,平台不提供额外的编辑、内容补充、找答案等附加服务。
- 2、"仅部分预览"的文档,不可在线预览部分如存在完整性等问题,可反馈申请退款(可完整预览的文档不适用该条件!)。
- 3、如文档侵犯您的权益,请联系客服反馈,我们会尽快为您处理(人工客服工作时间:9:00-18:30)。
压铸件经验之谈
压铸件设计经验:
注:由于合金金属散热较好,很难形成瞬间难却时候局部先后冷却现象。
而合金的收缩率也很小,很难难导致塑料产品缩水现象。
故,设计压铸件时候,不需要严格的厚度相对均匀。
注:压铸件厚度的建议。
铝、镁压铸件厚度,当面积小于25CM平方时,最小厚度是0.8,合适厚度是2.0.
当面积在25~100之间,最小厚度是1.2,合适厚度是2.5.
当面积在100~500之间,最小厚度是1.8,合适厚度是3.0.
当面积在500以上,,最小厚度是2.5,合适厚度是3.5.
锌金厚度要求,可以设计为:铝合金厚度-0.3~-0.5。
注:压铸件的其他建议。
1.过度之处需要设计圆角。
2.厚度需要均匀过度。
3.最小孔为0.5MM,为了模具的寿命。
4.避免尖角。
5.避免模具上产生薄钢。
注:拔模角一般为2度。
注:压铸件因为是金属材料,设计时候,倘若精度不够,后期可以切削加工。
注:另外,螺纹及螺纹孔,模具费用是比较贵的,产品量少的情况下,建议后期加工。
什么是压铸?
压铸是一种利用高压强制将金属熔液压入形状复杂的金属模内的一种精密铸造法。
压铸的设备:
压铸机由于压铸合金的不同,在基本上可分成二大类,即冷室机、热室机。
冷室机适合铜、镁、铝等高温合金之压铸,而热室机则应用于锌、锡、铅等压铸机一般能提供150万帕注射压力。
压铸件采用的材料:
铝合金
铝镁系
铝锌系
铝铜系
锌合金
镁合金
注:由于压铸材料铝合金含杂质太多,不能氧化便面处理。
氧化的效果很不理想
我司可提供压铸模具生产,压铸产品生产。
工程部可以免费提供设计技术支持。
Q—Q:369589423。