压铸件结构设计规范
2-3压铸件结构设计-53

表2-13 铸造圆角半径的设计计算 上一页 下一页 返回
4.压铸件的脱模斜度
为了保证压铸件能够从压铸模具中顺利脱出,在压铸件沿脱出方向上
的所有内表面都要有一定的斜度,该斜度称为脱模斜度。压铸件脱模 斜度的大小和压铸件的壁厚及合金种类有关。
压铸件壁厚↑,对型芯的抱紧力↑,脱模斜度↑;
收缩率及熔点↑,脱模斜度↑; 压铸件内表面或孔比外表面的脱模斜度要大。 在允许范围内,采用较大的脱模斜度,可减少推件力和抽芯力。
上一页 下一页 返回
表2-2 厚度尺寸公差(单位:mm)
表2-3 圆角半径尺寸的公差(单位:mm)
D4
表2-4 自由角度和自由锥度尺寸公差
表2-5 孔中心距尺寸公差(单位:mm)
2).表面形状和位置
压铸件的表面形状和位置主要由压铸模的成型表面决定,而压铸 模成型表面的形位公差精度较高,所以对压铸件的表面形位公差 一般不另行规定,其公差值包括在有关尺寸的公差范围内。对于 直接用于装配的表面,类似机械加工零件,在图中注明表面形状 和位置公差。
表2-9 压铸件机械加工余量(mm) 表2-10 压铸件铰孔加工余量
三、 压铸件结构设计
压铸件的结构设计是压铸生产中首先遇到的工作, 其设计的合理性和工艺适用性直接影响到后续工作
的顺利进行。设计压铸件除要满足使用要求外,同
时应该满足成型工艺要求,并且尽量做到模具结构 简单、生产成本低,达到设计的合理性、工艺性、 可制造性、经济性。
图2-4 改变凹区域方向消除抽芯受阻区域 图2-4 (a)形成区域A的活动型芯受到凸台K阻碍,无法抽出。 因此改变其方向,使区域A指向外侧,则可顺畅抽出,如图2-4 (b)所示。
(二)消除抽芯受阻区域
汽车关于压铸件的要求标准

汽车关于压铸件的要求标准汽车压铸件是指通过压铸工艺制造的汽车零部件,这些部件通常由铝合金、镁合金等金属材料制成。
为确保汽车压铸件在安全、性能和质量方面达到要求,制定了一系列的标准和规范。
以下是关于汽车压铸件的要求标准的一般性内容:1. 材料要求1.1 金属合金规定压铸件所使用的金属合金的种类和成分要求,通常包括铝合金、镁合金等。
合金的选择直接影响到压铸件的强度、耐腐蚀性等性能。
1.2 材料性能测试对金属合金进行强度、硬度、延伸性等性能测试,确保所选材料符合相应的标准。
2. 设计要求2.1 几何设计规定压铸件的几何设计要求,包括尺寸、形状、壁厚等,确保压铸件可以正确嵌入汽车结构中。
2.2 壁厚均匀性要求压铸件的壁厚均匀,避免因过薄或过厚导致的性能问题。
2.3 结构设计对于需要承受特定载荷或作用的压铸件,规定其结构设计,以确保在正常使用情况下不发生断裂或变形。
3. 制造工艺要求3.1 压铸工艺规定压铸件的生产工艺,包括压铸机的选择、压射速度、温度控制等,以保证压铸件的成形质量。
3.2 熔炼和浇铸对金属合金的熔炼和浇铸过程进行要求,确保合金的纯度和均匀性。
3.3 热处理如果需要对压铸件进行热处理,规定热处理工艺,以提高压铸件的强度和硬度。
4. 表面处理要求4.1 防腐处理规定压铸件的防腐处理方法,确保其在汽车使用中具有足够的抗腐蚀性能。
4.2 涂装要求对于需要进行涂装的压铸件,规定涂装的种类、颜色、附着力要求等,以提高压铸件的外观和耐候性。
5. 检测和测试要求5.1 尺寸检测规定对压铸件尺寸的检测方法和标准,确保其符合设计要求。
5.2 材料性能测试对压铸件材料进行硬度、拉伸、冲击等性能测试,以验证其性能是否符合要求。
5.3 缺陷检测规定对压铸件进行缺陷检测的方法,如X射线检测、超声波检测等,以确保压铸件内部不存在瑕疵。
6. 标志和包装规定在压铸件上标明必要的标志,以便追溯生产信息。
同时规定适当的包装方式,确保在运输过程中不受损。
压铸件结构设计规范

压铸件结构设计压铸件结构设计是压铸工作的第一步。
设计的合理性和工艺适应性将会影响到后续工作的顺利进行,如分型面选择、内浇口开设、推出机构布置、模具结构及制造难易、合金凝固收缩规律、铸件精度保证、缺陷的种类等,都会以压铸件本身工艺性的优劣为前提。
1、压铸件零件设计的注意事项⑴、压铸件的设计涉及四个方面的内容:a、即压力铸造对零件形状结构的要求;b、压铸件的工艺性能;c、压铸件的尺寸精度及表面要求;d、压铸件分型面的确定;压铸件的零件设计是压铸生产技术中的重要部分,设计时必须考虑以下问题:模具分型面的选择、浇口的开设、顶杆位置的选择、铸件的收缩、铸件的尺寸精度保证、铸件内部缺陷的防范、铸孔的有关要求、收缩变形的有关要求以及加工余量的大小等方面;⑵、压铸件的设计原则是:a、正确选择压铸件的材料;b、合理确定压铸件的尺寸精度;c、尽量使壁厚分布均匀;d、各转角处增加工艺园角,避免尖角。
⑶、压铸件分类按使用要求可分为两大类,一类承受较大载荷的零件或有较高相对运动速度的零件,检查的项目有尺寸、表面质量、化学成分、力学性能(抗拉强度、伸长率、硬度);另一类为其它零件,检查的项目有尺寸、表面质量及化学成分。
在设计压铸件时,还应该注意零件应满足压铸的工艺要求。
压铸的工艺性从分型面的位置、顶面推杆的位置、铸孔的有关要求、收缩变形的有关要求以及加工余量的大小等方面考虑。
合理确定压铸面的分型面,不但能简化压铸型的结构,还能保证铸件的质量。
⑷、压铸件结构的工艺性:1)尽量消除铸件内部侧凹,使模具结构简单。
2)尽量使铸件壁厚均匀,可利用筋减少壁厚,减少铸件气孔、缩孔、变形等缺陷。
3)尽量消除铸件上深孔、深腔。
因为细小型芯易弯曲、折断,深腔处充填和排气不良。
4)设计的铸件要便于脱模、抽芯。
5)肉厚的均一性是必要的。
6)避免尖角。
7)注意拔模角度。
8)注意产品之公差标注。
9)太厚太薄皆不宜。
10)避免死角倒角(能少则少)。
11)考虑后加工的难易度。
压铸件结构设计

h2≥0.8mm
a≤3°
压铸件加强筋的运用
3,作为散热加强;
4,作为装饰作用。
2,引导料流流向;
1,加强结构强度;
压铸件结构工艺性分析一
不好的案例
好的案例
说明
于型模中加工凹入文字较之加工凸出文字为困难﹒且模具寿命难以保证,使用后续刻加工﹐则与此相反。
1.5
0.014~0.020
6
0.056~0.084
2
0.018~0.026
7
0.066~0.100
2.5
0.022~0.032
8
0.076~0.116
3
0.028~0.040
9
0.088~0.138
3.5
0.034~0.050
10
0.100~0.160
4
0.040~0.060
合金浇注温度高时,填充时间可选长些。 模具温度高时,填充时间可选长些。 铸件厚壁部分离内浇口远时,填充时间可选长些。 熔化潜热和比热高的合金,填充时间可选长些。
好的案例
说明
陈学民
2021
2023
内容大纲
O1
产品的壁厚(模具成型的基础)
O2
产品的拔模(模具脱模的保障)
O3
产品的圆角(模具寿命的关键)
O4
加强筋的设计(结构优化的手段)
压铸件壁厚的设计
3.5
2.5
3.5
2.5
2.5
2.0
>500
3.0
1.8
3.0
1.8
2.2
1.5
>100~500
2.5
压铸件结构设计
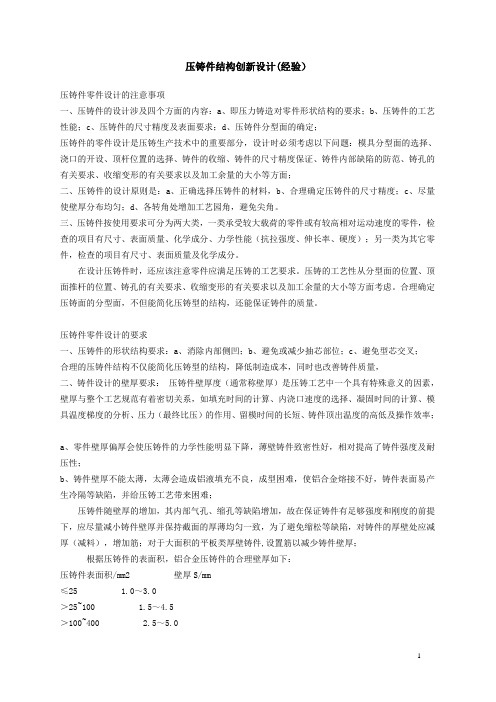
压铸件结构创新设计(经验)压铸件零件设计的注意事项一、压铸件的设计涉及四个方面的内容:a、即压力铸造对零件形状结构的要求;b、压铸件的工艺性能;c、压铸件的尺寸精度及表面要求;d、压铸件分型面的确定;压铸件的零件设计是压铸生产技术中的重要部分,设计时必须考虑以下问题:模具分型面的选择、浇口的开设、顶杆位置的选择、铸件的收缩、铸件的尺寸精度保证、铸件内部缺陷的防范、铸孔的有关要求、收缩变形的有关要求以及加工余量的大小等方面;二、压铸件的设计原则是:a、正确选择压铸件的材料,b、合理确定压铸件的尺寸精度;c、尽量使壁厚分布均匀;d、各转角处增加工艺园角,避免尖角。
三、压铸件按使用要求可分为两大类,一类承受较大载荷的零件或有较高相对运动速度的零件,检查的项目有尺寸、表面质量、化学成分、力学性能(抗拉强度、伸长率、硬度);另一类为其它零件,检查的项目有尺寸、表面质量及化学成分。
在设计压铸件时,还应该注意零件应满足压铸的工艺要求。
压铸的工艺性从分型面的位置、顶面推杆的位置、铸孔的有关要求、收缩变形的有关要求以及加工余量的大小等方面考虑。
合理确定压铸面的分型面,不但能简化压铸型的结构,还能保证铸件的质量。
压铸件零件设计的要求一、压铸件的形状结构要求:a、消除内部侧凹;b、避免或减少抽芯部位;c、避免型芯交叉;合理的压铸件结构不仅能简化压铸型的结构,降低制造成本,同时也改善铸件质量,二、铸件设计的壁厚要求:压铸件壁厚度(通常称壁厚)是压铸工艺中一个具有特殊意义的因素,壁厚与整个工艺规范有着密切关系,如填充时间的计算、内浇口速度的选择、凝固时间的计算、模具温度梯度的分析、压力(最终比压)的作用、留模时间的长短、铸件顶出温度的高低及操作效率;a、零件壁厚偏厚会使压铸件的力学性能明显下降,薄壁铸件致密性好,相对提高了铸件强度及耐压性;b、铸件壁厚不能太薄,太薄会造成铝液填充不良,成型困难,使铝合金熔接不好,铸件表面易产生冷隔等缺陷,并给压铸工艺带来困难;压铸件随壁厚的增加,其内部气孔、缩孔等缺陷增加,故在保证铸件有足够强度和刚度的前提下,应尽量减小铸件壁厚并保持截面的厚薄均匀一致,为了避免缩松等缺陷,对铸件的厚壁处应减厚(减料),增加筋;对于大面积的平板类厚壁铸件,设置筋以减少铸件壁厚;根据压铸件的表面积,铝合金压铸件的合理壁厚如下:压铸件表面积/mm2 壁厚S/mm≤25 1.0~3.0>25~100 1.5~4.5>100~400 2.5~5.0>400 3.5~6.0三、铸件设计筋的要求:筋的作用是壁厚改薄后,用以提高零件的强度和刚性,防止减少铸件收缩变形,以及避免工件从模具内顶出时发生变形,填充时用以作用辅助回路(金属流动的通路),压铸件筋的厚度应小于所在壁的厚度,一般取该处的厚度的2/3~3/4;四、铸件设计的圆角要求:压铸件上凡是壁与壁的连接,不论直角、锐角或钝角、盲孔和凹槽的根部,都应设计成圆角,只有当预计确定为分型面的部位上,才不采用圆角连接,其余部位一般必须为圆角,圆角不宜过大或过小,过小压铸件易产生裂纹,过大易产生疏松缩孔,压铸件圆角一般取:1/2壁厚≤R≤壁厚;圆角的作用是有助于金属的流动,减少涡流或湍流;避免零件上因有圆角的存在而产生应力集中而导致开裂;当零件要进行电镀或涂覆时,圆角可获得均匀镀层,防止尖角处沉积;可以延长压铸模的使用寿命,不致因模具型腔尖角的存在而导致崩角或开裂;五、压铸件设计的铸造斜度要求:斜度作用是减少铸件与模具型腔的摩擦,容易取出铸件;保证铸件表面不拉伤;延长压铸模使用寿命,铝合金压铸件一般最小铸造斜度如下:铝合金压铸件最小的铸造斜度外表面内表面型芯孔(单边)1°1°30′2°铸件的结构工艺性铸件中的基础件都是箱体形结构,并增设了很多加强筋,致使铸件结构形状较为复杂。
压铸产品结构设计的工艺要求

压铸类产品结构设计的工艺要求
压力铸造是将熔融状态或者(半)熔融状态合金浇入压铸机的压室,以极高的速度在高压的作用下充填在压铸模的型腔内,使熔融合金在高压下冷却凝固成型的方法。
常见的压铸材料包括:铝合金、锌合金、镁合金、铜合金等,铝合金又分为铝镁合金、铝铜合金、铝锌合金、铝硅合金等。
压铸类产品在结构设计时的工艺要求注意的几个方面。
①压铸件的厚度
压铸件产品的厚度一般指料厚,料的厚薄直接影响压铸的难易,一般情况下,压铸产品的料厚≥0.8mm,具体料厚根据产品设计。
压铸产品不会因为局部料厚产生缩水的现象,相反,在一些尖钢薄钢处要加料填充,避免模具强度低而损坏。
压铸产品的外观面局部最小料厚≥0.7mm,非外观面局部最小料厚度建议≥0.4mm,太薄会导致填充不良、无法成型,薄的区域面积也不能太大,否则无法成型。
②压铸件的拔模角
压铸件与塑胶件一样,内外表面都需要拔模角,压铸件外表面的
拔模角一般在1°~3°,内表面拔模角比外表面拔模角大一点,方便产品出模。
③压铸件的后续加工
压铸件有时达不到设计的要求,需要后续加工。
其中螺丝柱中的螺纹就是后续加工的,在设计产品时只需留出底孔就可以。
压铸件有深孔时,压铸件需要做出孔位置,再通过后续机械钻孔加工完成。
压铸件有些表面要求较高的精度,一般也需要后续加工,在设计时可在需要后续加工的地方留出加工余量,加工余量一般在0.5mm 左右。
④压铸件产品不能变形,一般是螺丝连接,在做扣位连接,连接的对应产品必须能变形,如塑胶产品等。
⑤压铸件产品加强筋不能太多,对于薄壁类零件,需适当设计加强筋,以增加产品的抗弯强度,防止产品变形损坏。
压铸件的基本结构设计内容

压铸件的基本结构设计内容咱们今天聊一聊压铸件的基本结构设计内容。
可能你一听“压铸件”三个字,心里就想着这又是什么高大上的东西,其实吧,压铸件就跟咱们平时看到的那些金属零件差不多,差别就是它们是通过压铸工艺来做出来的,简单说,就是把熔化的金属像倒水一样压进一个模具里,冷却固化后就成了咱们需要的形状。
好啦,说到压铸件的设计内容,其实可以分为好几个方面来讲。
首先就是模具设计。
咱们先不说别的,单单这个模具就很考究了。
压铸模具的设计就像是为每个压铸件量身定做衣服,不合适的话,结果就没法穿出来,穿不上也就算了,还可能会导致材料浪费、成型不良等等一大堆麻烦。
模具的设计要求非常高,既要保证零件的精准度,又得考虑到金属在模具里流动的状态,必须考虑冷却系统,甚至是脱模的角度,像是个全方位的“专业护理”。
别看模具小,做不好就能让整个生产过程泡汤,真的是“细节决定成败”啊。
咱们得聊聊压铸件的结构设计。
这个“结构”啊,其实就是零件的形状、厚度分布、壁厚均匀度等等一系列的事。
想象一下,你在做一道菜,如果配料不匀,或者火候控制不好,那味道肯定会差,压铸件也是一样。
设计的好,能让熔融金属在模具里流得顺畅,零件出来时就能不留气孔、不变形,质量自然过关。
特别是壁厚,千万不能忽视!有的地方厚的像土豆饼,有的地方薄得像纸片,做出来的零件要么沉,要么轻,怎么可能不出问题呢?所以啊,这壁厚的均匀性就像做菜时的火候,一定要掌握得当。
然后呢,咱得说说压铸件的材料选择。
这也是个大问题。
有些零件要承受大负荷,有些则得耐高温,甚至得防腐蚀,材料得根据这些要求来选。
可能是铝合金,有时候可能是锌合金,每种金属的性质不一样,决定了它适用的范围和效果。
所以呢,选材可不是随便选选的,而是需要经过精密计算的。
想象一下,你买东西时会货比三家,那在压铸件的设计中,选材也是一样,要根据具体的需求来决定。
对了,还得提一提设计时的考虑问题,比如说气体排放问题。
金属熔化后,容易产生气体,若是设计不合理,这些气体可能就会被困在零件里面,导致气孔、气泡,影响零件的强度。
压铸件壁厚设计原则
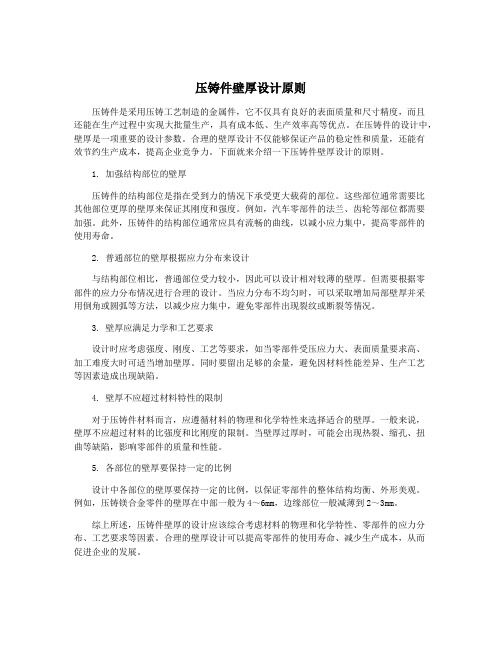
压铸件壁厚设计原则压铸件是采用压铸工艺制造的金属件,它不仅具有良好的表面质量和尺寸精度,而且还能在生产过程中实现大批量生产,具有成本低、生产效率高等优点。
在压铸件的设计中,壁厚是一项重要的设计参数。
合理的壁厚设计不仅能够保证产品的稳定性和质量,还能有效节约生产成本,提高企业竞争力。
下面就来介绍一下压铸件壁厚设计的原则。
1. 加强结构部位的壁厚压铸件的结构部位是指在受到力的情况下承受更大载荷的部位。
这些部位通常需要比其他部位更厚的壁厚来保证其刚度和强度。
例如,汽车零部件的法兰、齿轮等部位都需要加强。
此外,压铸件的结构部位通常应具有流畅的曲线,以减小应力集中,提高零部件的使用寿命。
2. 普通部位的壁厚根据应力分布来设计与结构部位相比,普通部位受力较小,因此可以设计相对较薄的壁厚。
但需要根据零部件的应力分布情况进行合理的设计。
当应力分布不均匀时,可以采取增加局部壁厚并采用倒角或圆弧等方法,以减少应力集中,避免零部件出现裂纹或断裂等情况。
3. 壁厚应满足力学和工艺要求设计时应考虑强度、刚度、工艺等要求,如当零部件受压应力大、表面质量要求高、加工难度大时可适当增加壁厚。
同时要留出足够的余量,避免因材料性能差异、生产工艺等因素造成出现缺陷。
4. 壁厚不应超过材料特性的限制对于压铸件材料而言,应遵循材料的物理和化学特性来选择适合的壁厚。
一般来说,壁厚不应超过材料的比强度和比刚度的限制。
当壁厚过厚时,可能会出现热裂、缩孔、扭曲等缺陷,影响零部件的质量和性能。
5. 各部位的壁厚要保持一定的比例设计中各部位的壁厚要保持一定的比例,以保证零部件的整体结构均衡、外形美观。
例如,压铸镁合金零件的壁厚在中部一般为4~6mm,边缘部位一般减薄到2~3mm。
综上所述,压铸件壁厚的设计应该综合考虑材料的物理和化学特性、零部件的应力分布、工艺要求等因素。
合理的壁厚设计可以提高零部件的使用寿命、减少生产成本,从而促进企业的发展。
- 1、下载文档前请自行甄别文档内容的完整性,平台不提供额外的编辑、内容补充、找答案等附加服务。
- 2、"仅部分预览"的文档,不可在线预览部分如存在完整性等问题,可反馈申请退款(可完整预览的文档不适用该条件!)。
- 3、如文档侵犯您的权益,请联系客服反馈,我们会尽快为您处理(人工客服工作时间:9:00-18:30)。
压铸件结构设计压铸件结构设计是压铸工作的第一步。
设计的合理性和工艺适应性将会影响到后续工作的顺利进行,如分型面选择、内浇口开设、推出机构布置、模具结构及制造难易、合金凝固收缩规律、铸件精度保证、缺陷的种类等,都会以压铸件本身工艺性的优劣为前提。
1、压铸件零件设计的注意事项⑴、压铸件的设计涉及四个方面的内容:a、即压力铸造对零件形状结构的要求;b、压铸件的工艺性能;c、压铸件的尺寸精度及表面要求;d、压铸件分型面的确定;压铸件的零件设计是压铸生产技术中的重要部分,设计时必须考虑以下问题:模具分型面的选择、浇口的开设、顶杆位置的选择、铸件的收缩、铸件的尺寸精度保证、铸件内部缺陷的防范、铸孔的有关要求、收缩变形的有关要求以及加工余量的大小等方面;⑵、压铸件的设计原则是:a、正确选择压铸件的材料;b、合理确定压铸件的尺寸精度;c、尽量使壁厚分布均匀;d、各转角处增加工艺园角,避免尖角。
⑶、压铸件分类按使用要求可分为两大类,一类承受较大载荷的零件或有较高相对运动速度的零件,检查的项目有尺寸、表面质量、化学成分、力学性能(抗拉强度、伸长率、硬度);另一类为其它零件,检查的项目有尺寸、表面质量及化学成分。
在设计压铸件时,还应该注意零件应满足压铸的工艺要求。
压铸的工艺性从分型面的位置、顶面推杆的位置、铸孔的有关要求、收缩变形的有关要求以及加工余量的大小等方面考虑。
合理确定压铸面的分型面,不但能简化压铸型的结构,还能保证铸件的质量。
⑷、压铸件结构的工艺性:1)尽量消除铸件内部侧凹,使模具结构简单。
2)尽量使铸件壁厚均匀,可利用筋减少壁厚,减少铸件气孔、缩孔、变形等缺陷。
3)尽量消除铸件上深孔、深腔。
因为细小型芯易弯曲、折断,深腔处充填和排气不良。
4)设计的铸件要便于脱模、抽芯。
5)肉厚的均一性是必要的。
6)避免尖角。
7)注意拔模角度。
8)注意产品之公差标注。
9)太厚太薄皆不宜。
10)避免死角倒角(能少则少)。
11)考虑后加工的难易度。
12)尽量减少产品内空洞。
13)避免有半岛式的局部太弱的形状。
14)太长的成形孔,或太长的成形柱皆不宜。
2、压铸件零件设计⑴、压铸件的形状结构a、消除内部侧凹;b、避免或减少抽芯部位;c、避免型芯交叉;合理的压铸件结构不仅能简化压铸型的结构,降低制造成本,同时也改善铸件质量。
⑵、壁厚压铸件的壁厚对铸件质量有很大的影响。
以铝合金为例,薄壁比厚壁具有更高的强度和良好的致密性。
因此,在保证铸件有足够的强度和刚性的条件下,应尽可能减少其壁厚,并保持壁厚均匀一致。
铸件壁太薄时,使金属熔接不好,影响铸件的强度,同时给成型带来困难;壁厚过大或严重不均匀则易产生缩瘪及裂纹。
随着壁厚的增加,铸件内部气孔、缩松等缺陷也随之增多,同样降低铸件的强度。
压铸件的壁厚一般以2.5 ~4mm为宜,壁厚超过6mm的零件不宜采用压铸。
推荐采用的最小壁厚和正常壁厚见表1。
最大壁厚与最小壁厚之比不要大于3:1(应设计壁厚均匀,保证足够强度与刚度的前提)。
压铸件壁厚度(通常称壁厚)是压铸工艺中一个具有特殊意义的因素,壁厚与整个工艺规范有着密切关系,如填充时间的计算、内浇口速度的选择、凝固时间的计算、模具温度梯度的分析、压力(最终比压)的作用、留模时间的长短、铸件顶出温度的高低及操作效率;a、零件壁厚偏厚会使压铸件的力学性能明显下降,薄壁铸件致密性好,相对提高了铸件强度及耐压性;b、铸件壁厚不能太薄,太薄会造成铝液填充不良,成型困难,使铝合金熔接不好,铸件表面易产生冷隔等缺陷,并给压铸工艺带来困难;压铸件随壁厚的增加,其内部气孔、缩孔等缺陷增加,故在保证铸件有足够强度和刚度的前提下,应尽量减小铸件壁厚并保持截面的厚薄均匀一致,为了避免缩松等缺陷,对铸件的厚壁处应减厚(减料)增加筋;对于大面积的平板类厚壁铸件, 设置筋以减少铸件壁厚。
1)压铸件壁厚与性能有关。
2)压铸件壁厚影响金属液填充型腔状态,最终影响铸件表面质量。
3)压铸件壁厚影响金属料消耗及成本。
在设计压铸件时,往往为保证强度和刚度的可靠性,以为壁越厚性能越好;实际上对于压铸件来说,随着壁厚增加,力学性能明显下降。
原因是在压铸过程中,当金属液以高压、高速的状态进入型腔,与型腔表面接触后很快冷却凝固。
受到激冷的压铸件表面形成一层细晶粒组织。
这层致密的细晶粒组织的厚度约为0.3m 左右,因此薄壁压铸件具有更高的机械性能。
相反,厚壁压铸件中心层的晶粒较大,易产生内部缩孔、气孔,外表面凹陷等缺陷,使压铸件的机械性能随着壁厚的增加而降低。
随着壁厚的增加,金属料消耗多,成本也增加。
但如果单从结构性计算出最小壁厚,而忽略了铸件的复杂程度时,也会造成液态金属充填型腔状态不理想,产生缺陷。
在满足产品使用功能要求前提下,综合考虑各后工序过程的影响,以最低的金属消耗取得良好的成型性和工艺性,以采取正常、均匀的壁厚为佳。
⑶、铸造圆角压铸件各部分相交应有圆角(分型面处除外),使金属填充时流动平稳,气体容易排出,并可避免因锐角而产生裂纹。
对于需要进行电镀和涂饰的压铸件,圆角可以均匀镀层,防止尖角处涂料堆积。
压铸件的圆角半径R一般不宜小于1mm,最小圆角半径为0.5 mm,见表2。
铸造圆角半径的计算见表3。
表铸造圆角半径的计算()说明:①、对锌合金铸件,K=1/4 ;对铝、镁、合金铸件,K=1/2 。
②、计算后的最小圆角应符合表2 的要求。
压铸件上凡是壁与壁的连接,不论直角、锐角或钝角、盲孔和凹槽的根部,都应设计成圆角,只有当预计确定为分型面的部位上,才不采用圆角连接,其余部位一般必须为圆角,圆角不宜过大或过小,过小压铸件易产生裂纹,过大易产生疏松缩孔,压铸件圆角一般取:1/2 壁厚≤R≤壁厚。
圆角的作用是有助于金属的流动,减少涡流或湍流;避免零件上因有圆角的存在而产生应力集中而导致开裂;当零件要进行电镀或涂覆时,圆角可获得均匀镀层,防止尖角处沉积;可以延长压铸模的使用寿命,不致因模具型腔尖角的存在而导致崩角或开裂。
圆角可使金属液流动顺畅,改善充型持性,气体容易排出。
同时,避免尖角产生应力集中而导致裂纹缺陷。
特别是压铸件需要电镀处理时,圆角对于保证其良好的电镀效果是十分必要的。
⑷、拔模斜度设计压铸件时,就应在结构上留有结构斜度,无结构斜度时,在需要之处,必须有脱模的工艺斜度。
斜度的方向,必须与铸件的脱模方向一致。
推荐的脱模斜度见表4。
②、表中数值仅适用型腔深度或型芯高度≤50mm,表面粗糙度在Ra0.1 ,大端与小端尺寸的单面差的最小值为0.03mm。
当深度或高度>50mm,或表面粗糙度超过Ra0.1 时,则脱模斜度可适当增加。
斜度作用是减少铸件与模具型腔的摩擦,容易取出铸件;保证铸件表面不拉伤;延长压铸模使用寿命,铝合金压铸件一般最小铸造斜度如下:为了顺利脱模,减少推出力、抽芯力,减少模具损耗,在设计压铸件时,应在结构上有尽可能大的斜 度。
从而减少压铸件与模具的摩擦,容易取出铸件,也使铸件表面不被拉伤,保证表面光洁。
⑸、加强筋 加强筋的设置可以增加零件的强度和刚性,同时改善了压铸的工艺性。
但须注意:① 分布要均匀对称;② 与铸件连接的根部要有圆角; ③ 避免多筋交叉;④ 筋宽不应超过其相连的壁的厚度。
当壁厚小于 1.5mm 时,不宜采用加强筋; ⑤ 加强筋的脱模斜度应大于铸件内腔所允许的铸造斜度。
大于或等于 设计原则:2 3 4筋的作用是壁厚改薄后,用以提高零件的强度和刚性,防止减少铸件收缩变形,以及避免工件从模具 内顶出时发生变形,填充时用以作用辅助回路(金属流动的通路) ,压铸件筋的厚度应小于所在壁的厚度, 一般取该处的厚度的 2/3~3/4 。
压铸件倾向采用均匀的薄壁,为了提高其强度和刚性,防止变形,不应单纯用增加壁厚的方法,而应 采用适当的薄壁加强筋达此目的。
加强筋应对称布置,厚度均匀,避免新的金属堆聚。
为减少脱模时的阻力,加强筋应有铸造斜度。
⑹、压铸孔和孔到边缘的最小距离1)铸孔 压铸件的孔径和孔深,对要求不高的孔可以直接压出,按表 5。
表 5 最小孔径和最大孔深孔径合金 类别 最小孔径 d ( mm )最大孔深( mm ) 孔的最小斜度一般的技术上可 能的盲孔 通孔d >5 d <5 d >5 d <5 锌合金 1.5 0.8 6d 4d 12d 8d 0~0.3% 铝合金 2.5 2.0 4d 3d 8d 6d 0.5 % ~ 1% 镁合金 2.0 1.5 5d 4d 10d 8d 0~0.3% 铜合金4.02.53d2d5d3d2 % ~ 4%说明:①、表内深度系指固定型芯而言, , 对于活动的单个型芯其深度还可以适当增加。
②、对于较大的孔径,精度要求不高时,孔的深度亦可超出上述范围。
铸件的孔应尽量铸出,这不仅可使壁厚均匀,减少热节,节约金属,而且可节省机加工工时。
压铸件可压铸出的孔的最小尺寸和深度,受到形成孔的型芯在型腔中的分布位置的制约。
细型芯在抽 出时易弯曲或折断,因此孔的最小尺寸和深度受到一定限制。
其深度应带有一定斜度,以便于抽芯。
对于压铸件自攻螺钉用的底孔,推荐采用的底孔直径见表6。
表 6 自攻螺钉用底孔直径( mm )般采用的加强筋的尺寸按表 5 选取:1、受力大,减小壁厚,改善强度。
、对称布置,壁厚均匀,避免缩孔气孔。
、与料流方向一致,避免乱流。
、避免在肋上设置任何零部件。
铸件较为常用的自攻螺钉规格为与,其采用的底孔直径如下表:为了保证铸件有良好的成型条件, 铸孔到铸件边缘应保持一定的壁厚,见图2。
图2b≥(1/4 ~1/3)t当t <4.5 时,b≥1.5mm3) 长方形孔和槽压铸件上的长方形孔和槽的设计推荐按表7 采用。
说明:宽度b 在具有铸造斜度时,表内值为小端部位值。
⑺、文字、标志、图案1) 用压铸铸出,应采用凸纹。
凸纹高度大于0.3m,以适应模具制造的特点。
2) 采用目前开始流行的新技术:“转移彩膜”,可将彩色的文字、标志、图案彩膜转印到压铸件表面。
3) 压铸出铸件后,用激光在铸件表面打出文字、标志、图案,可以打出非常细微的文字。
例: 平行纹(直纹)高0.7MM﹐间距1MM﹐角度60.5 。
外径Φ 34.5mm 共104 牙。
⑻、收缩率收缩率通常称为缩水。
它是指合金由液态凝固为固态,并冷却至室温时尺寸缩小的百分数,可用下式表示:K=(L 模-L 件)/L 件式中:L 模为模腔尺寸,L 件为铸件尺寸。
收缩率的大小与压铸件的结构特点、壁厚、合金的化学成分和工艺因素等有关。
锌合金的线收缩率一般为:自由收缩时取0.6 %~0.8 %,受阻收缩时取0.3 %~0.6 %。
表5 为有型芯的锌合金压铸件不同壁厚时的线收缩率参考值。
⑼、螺纹1)外螺纹可以铸出,由于铸件或模具结构的需要,采用两半分型的螺纹型环时,需留有0.2~0.3mm 加工余量。