压铸件简介及设计原则
压铸件简介及设计原则

表2 压铸件的最小圆角半径(mm)
压铸合金 圆角半径R 压铸合金 圆角半径R
锌合金
铝锡合金
0.5
0.5
铝、镁合金
铜合金
1.0
1.5
压铸圆角一般取:1/2壁厚≤R≤壁厚
表3 铸造圆角半径的计算(mm)
相连接两壁的厚度 图例 圆角半径
相等壁厚
r=Kh R=r+h
h
R
说明:①、对锌合金铸件,K=1/4;对铝、镁、合金铸件, K=1/2。 ②、计算后的最小圆角应符合表2的要求。
螺纹
1)外螺纹可以铸出,由于铸件或模具结构的需要,采用两 半分型的螺纹型环时,需留有0.2~0.3mm加工余量。可铸出的 最小螺距为0.75mm,最小螺纹外径6mm,最大螺纹长为螺距的8 倍。 2)内螺纹虽然可以铸出,但要通过使用机械装置转动压铸 模中的型芯,使模具结构更复杂,而增加成本。所以一般先铸 出底孔,再由机械加工成内螺纹。
压铸零件的设计原则
1、正确选择压铸件的材料; 2、合理确定压铸件的尺寸精度;
压铸件的公差等级与精度
我司一般采用IT12级。 压铸件公差等级IT:11~13(见表7)。 mm
铸件基本尺寸 10~18 18~30 30~50 公差等级 IT11 0.11 0.13 0.16 0.19 IT12 0.18 0.21 0.25 0.30 IT13 0.27 0.33 0.39 0.46
铝合金压铸件最小的铸造斜度
外表面 1° 内表面 1°30′ 型芯孔(单边) 2°
加强筋
加强筋的设置可以增加零件的强度和刚性, 同时改善了压铸的工艺性。 但须注意: ① 分布要均匀对称; ② 与铸件连接的根部要有圆角; ③ 避免多筋交叉; ④ 筋宽不应超过其相连的壁的厚度。当壁 厚小于1.5mm时,不宜采用加强筋。
压铸件设计规范
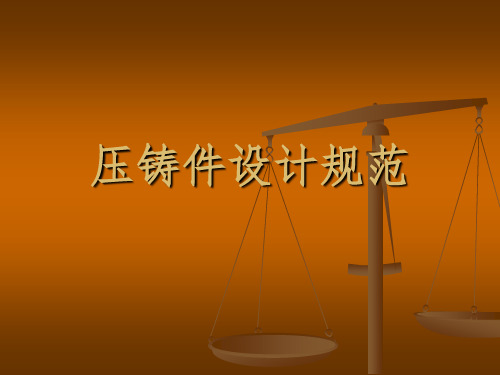
2.0
+1 -0.4
表9 推荐铰孔加工余量(mm)
公称孔径D
≤6
铰孔余量
0.05
>6~10 0.1
> 10 ~18 >18 ~30 >30 ~50 >50 ~60
0.15
0.2
0.25
0.3
我司现采用的机加工余量一般取0.3~0.5mm。
②、计算后的最小圆角应符合表2的要求。
2) 脱模斜度
设计压铸件时,就应在结构上 留有结构斜度,无结构斜度时,在需要 之处,必须有脱模的工艺斜度。斜度的 方向,必须与铸件的脱模方向一致。推 荐的脱模斜度见表4。
表4 脱模斜度
合金
锌合金 铝、镁合金
铜合金
配合面的最小脱模 斜度
外表面α 内表面β
0°10′ 0°15′ 0°30′
推荐采用的机加工余量及其偏差值见表8。铰孔余 量见表9。
表8 推荐机加工余量及其偏差(mm)
基本尺寸 每面余量
≤100
0.5
+0.4 -0.1
>100~250
0.75
+0.5 -0.2
> 250 ~400
1.0
+0.5 -0.3
> 400 ~630
1.5
+0.6 -0.4
> 630 ~1000
>500
0.5
1.5
0.8
2.0
0.8
2.0
0.8
1.5
1.0
1.8
1.22.51来自22.51.5
2.0
1.5
2.2
1.8
3.0
1.8
3.0
2.0
2.5
2.0
2.5
压铸件加强筋设计的基本原则

压铸件加强筋设计的基本原则一、前言压铸件是一种广泛应用于工业制造领域的零部件,其具有高强度、高精度、高效率等优点,因此得到了广泛的应用。
在压铸件的设计中,加强筋是一个非常重要的设计要素,其可以增加零部件的强度和刚度,提高零部件的使用寿命和可靠性。
本文将从压铸件加强筋设计的基本原则出发,对相关知识进行详细阐述。
二、加强筋的作用1. 增加零部件的强度和刚度:在压铸件中添加合适数量和位置的加强筋,可以有效地增加零部件的抗拉、抗弯等力学性能。
2. 提高零部件的使用寿命和可靠性:通过合理设置加强筋可以减少零部件在使用过程中产生变形或破坏现象,从而提高其使用寿命和可靠性。
3. 降低材料成本:通过增加加强筋可以降低材料所需数量,从而达到节约成本的目的。
三、基本原则1. 加强筋应该沿着主要受力方向设置:在压铸件的设计中,应该根据零部件所处的受力状态,确定加强筋的位置和数量。
一般情况下,加强筋应该沿着主要受力方向设置,以提高零部件在受力情况下的抗拉、抗弯等性能。
2. 加强筋应该设置在受力集中部位:在压铸件的设计中,应该将加强筋设置在受力集中的部位,以提高零部件在受力情况下的抗拉、抗弯等性能。
同时,在设置加强筋时还需要考虑到其与其他零部件之间的相互作用关系。
3. 加强筋应该尽可能地避免对其他零部件造成影响:在压铸件的设计中,加强筋不仅要考虑到自身的作用效果,还需要考虑到其对其他零部件造成影响。
在设置加强筋时需要尽可能地避免对其他零部件造成影响。
4. 加强筋应该具有合理的截面形状和尺寸:在压铸件的设计中,加强筋不仅要考虑到其位置和数量,还需要考虑到其截面形状和尺寸。
一般情况下,加强筋的截面形状应该选择合理的几何形状,如矩形、圆形等。
同时,在选择加强筋的尺寸时还需要考虑到其所需的材料成本和工艺难度。
5. 加强筋应该具有合理的连接方式:在压铸件的设计中,加强筋不仅要考虑到其位置、数量、截面形状和尺寸,还需要考虑到其与其他零部件之间的连接方式。
压铸件的设计规范标准介

压铸件的设计规范标准介压铸件的设计一定要考虑到压铸件壁厚、压铸件铸造圆角和脱模斜度、加强筋、压铸件上铸孔和孔到边缘的最小距离、压铸件上的长方形孔和槽、压铸件内的嵌件、压铸件的加工余量七个方面。
铸造圆角设计规范:通常压铸件各个部分相交应有圆角(分型面处除外),可使金属填充时流动平稳,气体也较容易排出,并可避免因锐角而产生裂纹。
对于需要进行电镀和涂饰的压铸件,圆角可以均匀镀层,防止尖角处涂料堆积。
压铸件的圆角半径R一般不宜小于1mm,最小圆角半径为0。
5mm。
压铸件内的嵌件设计规范:首先,压铸件上的嵌件数量不宜过多;其次,嵌件与压铸件的连接必须牢固,同时要求在嵌件上开槽、凸起、滚花等;再次,嵌件必须避免有尖角,以利安放并防止铸件应力集中,铸件和嵌件之间如有严重的电化腐蚀作用,则嵌件表面需要镀层保护;最后,有嵌件的铸件应避免热处理,以免因两种金属的相变而引起体积变化,使嵌件松动。
压铸件铸造圆角设计规范:通常压铸件各个部分相交应有圆角(分型面处除外),可使金属填充时流动平稳,气体也较容易排出,并可避免因锐角而产生裂纹。
对于需要进行电镀和涂饰的压铸件,圆角可以均匀镀层,防止尖角处涂料堆积。
压铸件的圆角半径R一般不宜小于1mm,最小圆角半径为0。
5mm。
压铸件壁厚的设计规范:薄壁比厚壁压铸件具备更高的强度和更好的致密性,鉴于此,压铸件设计中应该遵循这样的原则:在保证铸件具有足够强度和刚性的前提下应该尽可能减少壁厚,并保持壁厚具有均匀性。
实践证明,压铸件壁厚设计一般以2。
5-4mm为宜,壁厚超过6mm的零件不宜采用压铸工艺生产。
压铸件壁太厚、壁太薄对铸件质量影响的表现:如果设计中铸件壁太薄,会使金属熔接不好,直接影响铸件强度,同时会给成型造成困难;壁太厚或者严重不均匀时,容易产生缩瘪及裂纹,另一方面,随着壁厚的增加,压铸件内部气孔、缩松等缺陷也随之增多,同样会降低铸件强度,影响铸件质量。
压铸件设计规范详解

压铸件设计规范详解压铸件是指利用压铸工艺将熔融金属注入模具中,经过凝固和冷却后得到的零件。
由于该工艺具有生产效率高、成本低、制造精度高等优点,被广泛应用于汽车、航空航天、电子等领域。
为了保证压铸件质量和安全性,需要遵循一系列的设计规范。
下面将详细介绍压铸件设计规范。
一、材料选择1.铝合金:常用的有A380、A383、A360等。
根据使用条件和要求,选择合适的铝合金材料,确保压铸件具有良好的强度和塑性。
2.压铸型腔材料:常用的有铜合金、热处理工具钢等。
要选择适当的材料,以耐高温和磨损。
二、模具设计1.模具设计必须满足压铸件的要求,保证铸件的尺寸精度和表面质量。
2.模腔设计要考虑到铸件收缩率、冷却速度等因素,以避免产生缺陷和变形。
3.合理安排模具冷却系统,保证压铸件内部和表面的冷却均匀。
三、尺寸设计1.压铸件的尺寸设计应符合产品技术要求和工艺要求,确保功能和安装的需要。
2.避免设计尺寸太小或太薄,以免产生破裂和变形。
3.设计保证良好的表面质量,避免设计中出现接触不良、挤压不足等问题。
四、壁厚设计1.壁厚不应过薄,以免影响产品的强度和刚性。
2.避免壁厚过大,以减少成本和缩短冷却时间。
3.边缘和角部应注意壁厚过渡,避免产生应力集中。
五、设计角度和半径1.设计时应根据铝合金的流动性选择合适的角度和半径。
2.避免设计尖锐角度和太小的半径,以免产生气孔和挤压不足。
3.设计角度和半径应保持一定的一致性,避免因设计不当导致铸件变形和收缩不均匀。
六、设计放射状构件1.当压铸件具有放射状构件时,要合理设计放射状梁的位置和数量,以充分利用材料,并减少成本。
2.注意放射状构件的设计不应影响整体结构的强度。
七、设计排气系统1.设计时要考虑到铸件内部的气孔、气泡等气体排出问题。
2.合理安排和设计排气道,以保证良好的注模效果和铸件质量。
八、设计孔和螺纹1.设计孔和螺纹时应遵循标准规范,确保质量和安装的可靠性。
2.孔和螺纹的位置和尺寸应符合产品要求,保证压铸件的功能和使用要求。
压铸件壁厚设计原则
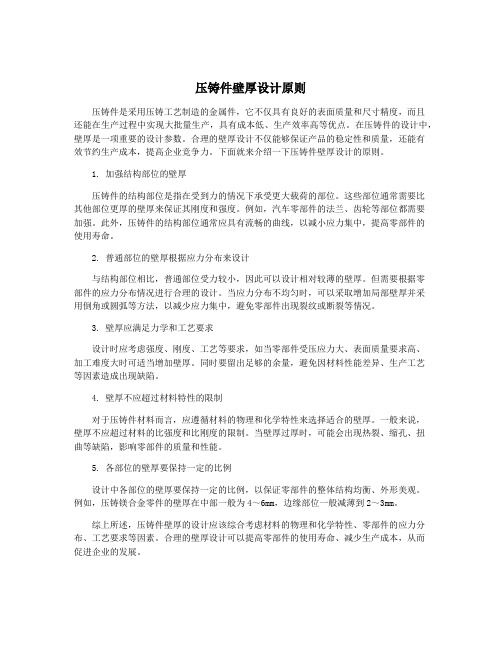
压铸件壁厚设计原则压铸件是采用压铸工艺制造的金属件,它不仅具有良好的表面质量和尺寸精度,而且还能在生产过程中实现大批量生产,具有成本低、生产效率高等优点。
在压铸件的设计中,壁厚是一项重要的设计参数。
合理的壁厚设计不仅能够保证产品的稳定性和质量,还能有效节约生产成本,提高企业竞争力。
下面就来介绍一下压铸件壁厚设计的原则。
1. 加强结构部位的壁厚压铸件的结构部位是指在受到力的情况下承受更大载荷的部位。
这些部位通常需要比其他部位更厚的壁厚来保证其刚度和强度。
例如,汽车零部件的法兰、齿轮等部位都需要加强。
此外,压铸件的结构部位通常应具有流畅的曲线,以减小应力集中,提高零部件的使用寿命。
2. 普通部位的壁厚根据应力分布来设计与结构部位相比,普通部位受力较小,因此可以设计相对较薄的壁厚。
但需要根据零部件的应力分布情况进行合理的设计。
当应力分布不均匀时,可以采取增加局部壁厚并采用倒角或圆弧等方法,以减少应力集中,避免零部件出现裂纹或断裂等情况。
3. 壁厚应满足力学和工艺要求设计时应考虑强度、刚度、工艺等要求,如当零部件受压应力大、表面质量要求高、加工难度大时可适当增加壁厚。
同时要留出足够的余量,避免因材料性能差异、生产工艺等因素造成出现缺陷。
4. 壁厚不应超过材料特性的限制对于压铸件材料而言,应遵循材料的物理和化学特性来选择适合的壁厚。
一般来说,壁厚不应超过材料的比强度和比刚度的限制。
当壁厚过厚时,可能会出现热裂、缩孔、扭曲等缺陷,影响零部件的质量和性能。
5. 各部位的壁厚要保持一定的比例设计中各部位的壁厚要保持一定的比例,以保证零部件的整体结构均衡、外形美观。
例如,压铸镁合金零件的壁厚在中部一般为4~6mm,边缘部位一般减薄到2~3mm。
综上所述,压铸件壁厚的设计应该综合考虑材料的物理和化学特性、零部件的应力分布、工艺要求等因素。
合理的壁厚设计可以提高零部件的使用寿命、减少生产成本,从而促进企业的发展。
压铸件结构设计规范
压铸件结构设计压铸件结构设计是压铸工作的第一步。
设计的合理性和工艺适应性将会影响到后续工作的顺利进行,如分型面选择、内浇口开设、推出机构布置、模具结构及制造难易、合金凝固收缩规律、铸件精度保证、缺陷的种类等,都会以压铸件本身工艺性的优劣为前提。
1、压铸件零件设计的注意事项⑴、压铸件的设计涉及四个方面的内容:a、即压力铸造对零件形状结构的要求;b、压铸件的工艺性能;c、压铸件的尺寸精度及表面要求;d、压铸件分型面的确定;压铸件的零件设计是压铸生产技术中的重要部分,设计时必须考虑以下问题:模具分型面的选择、浇口的开设、顶杆位置的选择、铸件的收缩、铸件的尺寸精度保证、铸件内部缺陷的防范、铸孔的有关要求、收缩变形的有关要求以及加工余量的大小等方面;⑵、压铸件的设计原则是:a、正确选择压铸件的材料;b、合理确定压铸件的尺寸精度;c、尽量使壁厚分布均匀;d、各转角处增加工艺园角,避免尖角。
⑶、压铸件分类按使用要求可分为两大类,一类承受较大载荷的零件或有较高相对运动速度的零件,检查的项目有尺寸、表面质量、化学成分、力学性能(抗拉强度、伸长率、硬度);另一类为其它零件,检查的项目有尺寸、表面质量及化学成分。
在设计压铸件时,还应该注意零件应满足压铸的工艺要求。
压铸的工艺性从分型面的位置、顶面推杆的位置、铸孔的有关要求、收缩变形的有关要求以及加工余量的大小等方面考虑。
合理确定压铸面的分型面,不但能简化压铸型的结构,还能保证铸件的质量。
⑷、压铸件结构的工艺性:1)尽量消除铸件内部侧凹,使模具结构简单。
2)尽量使铸件壁厚均匀,可利用筋减少壁厚,减少铸件气孔、缩孔、变形等缺陷。
3)尽量消除铸件上深孔、深腔。
因为细小型芯易弯曲、折断,深腔处充填和排气不良。
4)设计的铸件要便于脱模、抽芯。
5)肉厚的均一性是必要的。
6)避免尖角。
7)注意拔模角度。
8)注意产品之公差标注。
9)太厚太薄皆不宜。
10)避免死角倒角(能少则少)。
11)考虑后加工的难易度。
压铸件结构设计规范
压铸件结构设计压铸件结构设计是压铸工作的第一步。
设计的合理性和工艺适应性将会影响到后续工作的顺利进行,如分型面选择、内浇口开设、推出机构布置、模具结构及制造难易、合金凝固收缩规律、铸件精度保证、缺陷的种类等,都会以压铸件本身工艺性的优劣为前提。
1、压铸件零件设计的注意事项⑴、压铸件的设计涉及四个方面的内容:a、即压力铸造对零件形状结构的要求;b、压铸件的工艺性能;c、压铸件的尺寸精度及表面要求;d、压铸件分型面的确定;压铸件的零件设计是压铸生产技术中的重要部分,设计时必须考虑以下问题:模具分型面的选择、浇口的开设、顶杆位置的选择、铸件的收缩、铸件的尺寸精度保证、铸件内部缺陷的防范、铸孔的有关要求、收缩变形的有关要求以及加工余量的大小等方面;⑵、压铸件的设计原则是:a、正确选择压铸件的材料;b、合理确定压铸件的尺寸精度;c、尽量使壁厚分布均匀;d、各转角处增加工艺园角,避免尖角。
⑶、压铸件分类按使用要求可分为两大类,一类承受较大载荷的零件或有较高相对运动速度的零件,检查的项目有尺寸、表面质量、化学成分、力学性能(抗拉强度、伸长率、硬度);另一类为其它零件,检查的项目有尺寸、表面质量及化学成分。
在设计压铸件时,还应该注意零件应满足压铸的工艺要求。
压铸的工艺性从分型面的位置、顶面推杆的位置、铸孔的有关要求、收缩变形的有关要求以及加工余量的大小等方面考虑。
合理确定压铸面的分型面,不但能简化压铸型的结构,还能保证铸件的质量。
⑷、压铸件结构的工艺性:1)尽量消除铸件内部侧凹,使模具结构简单。
2)尽量使铸件壁厚均匀,可利用筋减少壁厚,减少铸件气孔、缩孔、变形等缺陷。
3)尽量消除铸件上深孔、深腔。
因为细小型芯易弯曲、折断,深腔处充填和排气不良。
4)设计的铸件要便于脱模、抽芯。
5)肉厚的均一性是必要的。
6)避免尖角。
7)注意拔模角度。
8)注意产品之公差标注。
9)太厚太薄皆不宜。
10)避免死角倒角(能少则少)。
11)考虑后加工的难易度。
压铸件结构设计和压铸工艺
压铸件结构设计和压铸工艺压铸是一种将熔融金属注入到铸型中,通过冷却凝固形成所需形状的金属成型工艺。
压铸件结构设计和压铸工艺是压铸过程中至关重要的两个环节,对于保证产品质量和提高生产效率具有重要意义。
下面将从压铸件结构设计和压铸工艺两个方面进行详细介绍。
一、压铸件结构设计1.几何形状:要考虑产品的形状是否适合压铸工艺,避免出现厚壁或复杂形状等难以生产的结构。
2.壁厚设计:在保证产品强度和刚性的前提下,尽量减少壁厚。
过厚的壁厚会导致液态金属充填困难,同时也会增加材料消耗和生产成本。
3.避免内部缺陷:合理设置内部结构,避免产生气孔、缩松等内部缺陷,影响产品质量。
4.轮廓设计:尽量简化复杂的轮廓,减少加工和后处理工序,提高生产效率。
5.集成功能:在设计阶段就考虑到产品的功能需求,尽量将不同功能集成到一个构件中,减少组装工序。
二、压铸工艺压铸工艺是将压铸件结构设计转换为实际产品的过程,主要包括模具设计、熔化与注射、冷却凝固、脱模、后处理等阶段。
1.模具设计:根据产品的形状和尺寸要求,设计出相应的模具。
模具设计要遵循易于加工和维修的原则,并考虑到产品的收缩率,以保证最终产品符合设计要求。
2.熔化与注射:将所需的金属材料加热至液态,然后通过注射机将熔融金属注入到模具中。
注射过程需要控制注射速度和压力,保证金属充填完整且无气泡。
3.冷却凝固:在模具中进行冷却凝固,使注入的金属逐渐凝固。
冷却过程需要控制温度和时间,以保证产品的结晶组织均匀性和性能稳定性。
4.脱模:凝固后的产品从模具中取出,包括冷却水冲洗和振动脱模等工序。
脱模过程需要注意避免产品的变形和损坏。
5.后处理:包括修磨、去毛刺、清洗、表面处理等工序。
后处理旨在提高产品表面质量和机械性能,并满足特定的外观要求。
总结:压铸件结构设计和压铸工艺是相互关联的,一个合理的结构设计可以提高生产效率和产品质量,而一个良好的压铸工艺可以保证结构设计的实施效果。
因此,在进行压铸件结构设计和压铸工艺选择时,需要综合考虑产品的功能要求、材料特性、生产成本等因素,以达到最佳的工艺效果。
压铸件设计原则
压铸件
压铸工艺对压铸件结构的要求
1 . 从简化模具结构、延长模具使用寿命考虑
1)铸件的分型面上应尽量避免圆角
2)避免模具局部过薄
3)避免压铸件上互相交叉的不通孔
4)避免内侧凹
2 . 改进模具结构,减少抽芯部位。
3 . 方便压铸件脱模和抽芯。
压铸件的分类
按压铸件的材料分,可分为铝合金压铸件、锌合金压铸件、镁合金压铸件以及铜合金压铸件等。
按用途划分,可分为结构类压铸件和装饰类压铸件等。
按应用场合划分,可分为汽车类压铸件、3C产品压铸件、玩具类压铸件等。
还可以按照形状、壁厚等特征划分。
压铸件分型面上尽量避免圆角避免模具局部过薄
避免压铸件上互相交叉的不通孔
铝合金压铸件
锌合金压铸件
汽车零部件
镁合金压铸件
装饰类压铸件
玩具类压铸件(车架)。
- 1、下载文档前请自行甄别文档内容的完整性,平台不提供额外的编辑、内容补充、找答案等附加服务。
- 2、"仅部分预览"的文档,不可在线预览部分如存在完整性等问题,可反馈申请退款(可完整预览的文档不适用该条件!)。
- 3、如文档侵犯您的权益,请联系客服反馈,我们会尽快为您处理(人工客服工作时间:9:00-18:30)。
一般采用的加强筋的尺寸按表5选取:
t1
壁厚
t≤3
t>3
t1
t1=0.6t~t t2=0.75t~t h≤5t r≤0.5mm R≥0.5t~t (0.4~0.7)t (0.6~1)t
h
t2
R
高度h
t
t2
最小圆角r 最小圆角R
图1
(t—压铸件壁厚,最大不超过6~8mm)
加强筋的设计原则: 1、受力大,减小壁厚,改善强度。 2、对称布置,壁厚均匀,避免缩孔气孔。 3、与料流方向一致,避免乱流。 4、避免在肋上设置任何零部件。 压铸件筋的厚度应小于所在壁的厚度,一般取 该处的厚度的2/3~3/4。
表1
壁厚处的面积 a×b(cm2)
压铸件的最小壁厚和正常壁厚
锌合金
铝合金
镁合金
铜合金
壁厚h(mm) 最 小 ≤25 >25~100 0.5 1.0 正 常 1.5 1.8 最 小 0.8 1.2 正 常 2.0 2.5 最 小 0.8 1.2 正 常 2.0 2.5 最 小 0.8 1.5 正 常 1.5 2.0
压铸模
压铸件
压铸特点: (1)金属液是在压力下填充型腔的,并在更高的 压力下结晶凝固,常见的压力为15—100MPa。 (2)金属液以高速充填型腔,通常在10—50米/秒, 有的还可超过80米/秒,(通过内浇口导入型腔的 线速度—内浇口速度),因此金属液的充型时间极 短,约0.01—0.2秒(须视铸件的大小而不同)内 即可填满型腔。
合金 最小螺距(P) 最小螺纹外径 最大螺纹长度
外
锌 铝 0.75 1 6 10
内
10 20
外
8P 6P
内
5P 4P
压铸圆角
ቤተ መጻሕፍቲ ባይዱ壁厚
3RU 壳体
脱模斜度
加强筋
总结
压铸是最先进的金属成型方法之一,随 着压铸技术的不断提高,压铸合金不再局限 于有色金属的锌、铝、镁和铜,压铸件的尺 寸和重量,也会随压铸机的功率不断增大而 增大。 所以压铸工艺的前景十分广阔。
铝合金压铸件最小的铸造斜度
外表面 1° 内表面 1°30′ 型芯孔(单边) 2°
加强筋
加强筋的设置可以增加零件的强度和刚性, 同时改善了压铸的工艺性。 但须注意: ① 分布要均匀对称; ② 与铸件连接的根部要有圆角; ③ 避免多筋交叉; ④ 筋宽不应超过其相连的壁的厚度。当壁 厚小于1.5mm时,不宜采用加强筋。
壁厚
压铸件的壁厚对铸件质量有很大的影响。 铸件壁太薄时,使金属熔接不好,影响铸 件的强度,同时给成型带来困难;壁厚过大或 严重不均匀则易产生缩松及裂纹。
铝合金压铸件砂孔标准
壁厚 (mm)
可适用的壁厚 (mm)
内部砂孔可接受的标准 X射线照片:比例1:1
表面砂孔可接受的标准 X射线照片:比例1:1
h1
不等壁厚
r
r≥(h+h1)/3 R= r+(h+h1)/2
脱模斜度
设计压铸件时,就应在结构上留有结构斜度,无结构 斜度时,在需要之处,必须有脱模的工艺斜度。斜度的方 向,必须与铸件的脱模方向一致。推荐的脱模斜度见表4。
表4 脱模斜度
配合面的最小脱模 斜度
外表面α 锌合金 铝、镁 合金 铜合金 0°10′ 0°15′ 0°30′
锌合金
420℃
6/1000
3#,5#, 2#,ZA8
热室,冷 室
镁合金
650℃
5/1000
AZ91, AM50, AS41
30~ 40MPa
40~ 60MPa
70~ 100MPa
热室,冷 室
铝合金
720℃
6/1000
ADC12, A380
30~ 40MPa
40~ 80MPa
80~ 120MPa
冷室
孔洞类缺陷是压铸中公认的主要缺陷之一,铝合金中 金属液流动过程的卷气和凝固过程的收缩是产生孔洞类型 缺陷的主要原因。 这不仅使铸件力学性能下降,不宜进行热处理,而且降 低了压铸件的耐压性和气密性,限制了压铸件的使用。因 此,研究超低速压铸工艺以减少压室及型腔中气体含量,并 同时采用合理的铸造压力以减少或消除铸件的缩孔、缩松 十分必要。压铸时理想流态应是慢压射冲头慢速前进,排 出压室中的气体,直至合金液充满压室,再选择合适的快压 射速度,在合金液不凝固的情况下充满型腔,然后压射冲头 以高速、高压施加于合金液上,使压铸件在静压力作用下 凝固,以获得表面光洁、轮廓清晰、内部组织致密的压铸 件。
压铸的优点:产品质量好,生产效率高,经济 效果优良。 压铸的缺点:压铸合金受限制, 目前的压铸合 金只有锌、锡、铅、铜、镁、铝等六种;设备 费用昂贵 ;不宜小批量生产。
2.压铸机的分类 压铸机分热压室压铸机和冷压室压铸机两 大类。 热压室压铸机与冷压室压铸机的合模机构 是一样的,其区别在于压射、浇注机构不同。 热压室压铸机的压室与熔炉紧密地连成一个整 体,而冷压室压铸机的压室与熔炉是分开的。
3.2
Up to3.2mm
15.9
Over3.2 to 25.4mm
砂孔等级区别
Level 1 1级 X射线照片:比例1:1
Level 2 2级 X射线照片:比例1:1
Level 3 3级 X射线照片:比例1:1
Level 4 4级 X射线照片:比例1:1
0.5~0.7mm 3个/10cm2 0.5~1.0mm 0.7~1.0mm 1个/10cm2 1.0~1.5mm
压铸零件的设计原则
1、正确选择压铸件的材料; 2、合理确定压铸件的尺寸精度;
压铸件的公差等级与精度
我司一般采用IT12级。 压铸件公差等级IT:11~13(见表7)。 mm
铸件基本尺寸 10~18 18~30 30~50 公差等级 IT11 0.11 0.13 0.16 0.19 IT12 0.18 0.21 0.25 0.30 IT13 0.27 0.33 0.39 0.46
谢谢
螺纹
1)外螺纹可以铸出,由于铸件或模具结构的需要,采用两 半分型的螺纹型环时,需留有0.2~0.3mm加工余量。可铸出的 最小螺距为0.75mm,最小螺纹外径6mm,最大螺纹长为螺距的8 倍。 2)内螺纹虽然可以铸出,但要通过使用机械装置转动压铸 模中的型芯,使模具结构更复杂,而增加成本。所以一般先铸 出底孔,再由机械加工成内螺纹。
表2 压铸件的最小圆角半径(mm)
压铸合金 圆角半径R 压铸合金 圆角半径R
锌合金
铝锡合金
0.5
0.5
铝、镁合金
铜合金
1.0
1.5
压铸圆角一般取:1/2壁厚≤R≤壁厚
表3 铸造圆角半径的计算(mm)
相连接两壁的厚度 图例 圆角半径
相等壁厚
r=Kh R=r+h
h
R
说明:①、对锌合金铸件,K=1/4;对铝、镁、合金铸件, K=1/2。 ②、计算后的最小圆角应符合表2的要求。
50~80
80~120 120~180 180~250 250~315
0.22
0.25 0.29 0.32
0.35
0.40 0.46 0.52
0.54
0.63 0.72 0.81
3、压铸件的形状结构 a、压铸件上应消除内侧凹,以保证压铸件 从压型中顺利取出; b、避免或减少抽芯部位; c.壁厚; d.压铸圆角; e.脱模斜度; f.加强筋; g.螺纹。
a
h
>100~500
>500
1.5
2.0
2.2
2.5
1.8
2.5
3.0
4.0
1.8
2.5
3.0
4.0
2.0
2.5
2.5
3.0
b
压铸圆角
压铸件各部分相交应有圆角(分型面处除外), 使金属填充时流动平稳,气体容易排出,并可避免因 锐角而产生裂纹。对于需要进行电镀和涂饰的压铸件, 圆角可以均匀镀层,防止尖角处涂料堆积。 铸造圆角半径的计算见表3。
冷室压铸机
热室压铸机
热室压铸机原理图
冷室压铸机
3.压铸的过程:
预热
精加工
去飞边
喷脱模剂
压入
熔融合金液流动
冷却凝固
4.压铸材料
金属液 温度 收缩 率 种类 承受轻负 承受较大 气密性面 荷的零件 负荷的零 大壁薄零 的压力 件的压力 件的压力 13~ 20MPa 20~ 30MPa 25~ 40MPa 压铸机
压铸件简介及设计原则
报告人:沈斌磊 时间:2012-03-29
目录
压铸介绍 压铸零件的设计原则
压铸介绍
1.压铸概念 2.压铸机的分类 3.压铸过程 4.压铸材料
1. 压铸概念 压铸模锻工艺是一种在专用的压铸模锻机上完 成的工艺。它的基本工艺过程是:是一种将熔融合 金液倒入压室内,以高速充填钢制模具的型腔,并 使合金液在压力下凝固而形成铸件的铸造方法。
合金
非配合面的最小脱 模斜度
内表面β 外表面α 内表面β 0°15′ 0°15′ 0°45′ 0°30′ 0°30′ 1° 0°45′ 1° 1°30′
配合面指的是在装配时要与其他零件互相接触的面。
斜度作用是减少铸件与模具型腔的摩擦,减 少推出力、抽芯力,容易取出铸件;保证铸件表面 不拉伤;保证表面光洁;延长压铸模使用寿命,铝 合金压铸件一般最小铸造斜度如下:
5个10cm/2 0.5~1.5mm 10个/10cm2 0.5~4.0mm 15个/10cm2 1个/10cm2 1.5~4.0mm 1个/10cm2 4.0~ 10mm 1个/10cm2
备注:如果没有特别说明,0.50mm及以下的气孔不作为砂孔的 评估控制范围内,此要求适用于铝合金压铸件的内部和加工表 面。