用橡胶制作模具
阀圈橡胶模具设计2
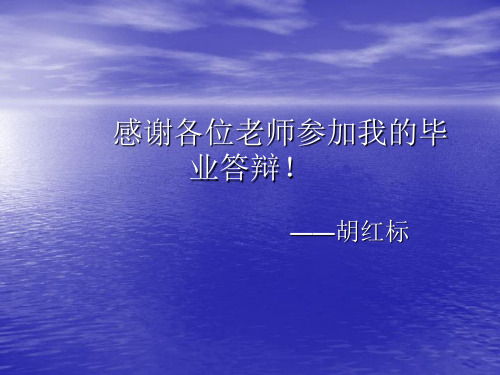
模具,简称橡胶注压模。此种成形工艺,是利用注压 机的压力,将已塑化好的胶料由螺杆或柱塞经喷嘴直 接注入模腔,完成成形并进行硫化的一种生产方法。 注压成形的特点,是把成形和硫化过程合为一体,成 形周期短,废边料少,劳动强度低,生产效率高,产 品质量好。目前,广泛用于橡胶密封圈、橡胶复合制 品、减振制品及胶鞋等橡胶制品生产。
计算应力状态
➢ 设计任务 设计参数:
设计要求
橡胶件的成型工艺性能分析
• 产品名称:船用中心型船用蝶阀阀圈(150
型)
• 产品材料: 丁腈橡胶 • 产品数量:中批量(<10万模) • 胶件尺寸:图中所示 塑件质量:160g • 胶件颜色:黑色 • 胶件要求:胶件外侧表面较光滑,产品的主
要工作面为内径部分圆弧面因此该处不能出 现流痕、气泡,塑件收缩率为1.4%,零件表 面按HG6-409-79三条(3)项要求,一般尺 寸公差按HB5522-80三级精度。
橡胶传递模:用于橡胶制品传递成形工艺方法的一类
模具,简称橡胶传递模。传递成形就是将混炼过的、 限量的胶条对压料柱塞施压,迫使胶料流经模具的浇 注系统注满模腔,经硫化定型后便可获得外观质量较 好和尺寸精度较高的橡胶制品。
橡胶传递模结构,虽然较压模复杂,但特适于薄壁、 细长、易弯曲以及形状较复杂的橡胶制品成形。采用 此类模具生产的橡胶制品,致密性好,质量也较高。
橡胶挤出模:用于挤出成形各种橡胶型材的一 类模具,简称橡胶挤出模。挤出成形工艺是生 产橡胶产品的主要方法之一。它是利用挤出机 使胶料在螺杆推动下,连续不断地向前运动, 然后借助于挤出口模,挤压出各种所需截面形 状的半成品,以完成不用造型或其他作业过程。 它具有连续、高效、甚至不用金属模具,就能 成形与制造多种不同截面形状的空心或实心半 成品,以达到初步造型的目的。而后进过冷却 定型,输入到硫化罐内进行硫化或作为压制法 所需的预成形半成品胶料。该模具在橡胶工业 中,亦占有及其重要的位置。
橡胶模具构造及保养培训资料

不同清洗方法能力对比
○:好 △:一般 ×:差
洗模方法一览表
洗模种类
喷砂 (树脂)
洗模 原理
物理性
洗模液
化学性
洗模橡胶 化学性
干冰
物理性
清洗能力 污垢状态 模腔状态
工作
用途
基本
使用 模具类型 价格 比例
堆积 物
表面 薄膜
平面
细小 部位
深沟 部位
防锈 性能
工作 时间
操作 升温 废弃 性 时间 成型
平压 模
特点:
优点:没有压料槽、操作方便模具、结构简单,模具廉价。
缺点:⑴毛边厚度方向尺寸精度难调整出来。
⑵产品容易产生材料不足的不良品。
型腔゙
导柱(位置定位用) 导套(位置定位用)
二.模具的基本认识
A.模具由钢材制造,其中模腔部采用优质模具钢。
B.橡胶模具一般由两板或三板模板组成,接触面为分模面(P.L 面).板与板之间是由导柱和导套进行对准定位。
②生产效率高、质量稳定
③水口废料产生少。
缺点:①毛边厚度方向尺寸精度难调整出来。
②对于壁厚产品容易产生材料不足的不良品。
定位环 热流道
隔热板
流道套 型腔
⑵.真空注入模具
真空注入模具:它是将搅炼过的、形状简单的、限量一定的橡胶料或胶
块半成品放入注入模压料槽中,通过压料板的压力挤压
橡胶料,并使橡胶料通过浇注系统进入模具型腔中硫化
C.模具型腔决定产品的形状.规格.尺寸.外观光洁度。
D.模板表面有表面处理:1.无电镀
2.电镀硬铬
橡胶模具专业术语

橡胶模具专业术语1. 哎呀,咱橡胶模具里有个词叫“分型面”呢。
这就好比是一块蛋糕要切成两块的那个切割面,模具就是沿着这个分型面分开和合拢的。
比如说做个橡胶小鸭子玩具的模具,分型面就在小鸭子身体中间那条线上,这样才能顺利把做好的小鸭子从模具里取出来。
2. 你知道“脱模斜度”不?这可是个超重要的东西呀!就像人从滑梯上滑下来一样,要是滑梯是直上直下的(没有斜度),人就很难下来。
橡胶模具里的零件如果没有脱模斜度,橡胶制品就不容易从模具里脱出来。
就像我之前做的那个橡胶瓶盖模具,因为脱模斜度没设计好,费了好大劲儿才把瓶盖取出来,可把我急坏了!3. “浇口”这个术语可不能小瞧哦。
它就像水龙头一样,是橡胶材料流入模具的入口。
想象一下,你要给一个大水桶注水,那个注水的小口子就是浇口。
我有个朋友做橡胶鞋底模具的时候,浇口的大小没调好,结果橡胶流动不均匀,鞋底有的地方厚有的地方薄,那可真是个大麻烦呢。
4. 咱来说说“流道”吧。
这流道呢,就像是给汽车导航的道路一样,引导着橡胶材料在模具里流动。
如果流道设计得弯弯曲曲又狭窄,橡胶就像堵车时的汽车一样,走得磕磕绊绊。
我同事做一个橡胶小饰品的模具,流道设计得不合理,最后饰品有些地方都没填充好,他那个懊悔呀。
5. “模腔”这个词,其实就是橡胶成型的小房间。
你把橡胶材料放进去,就像把小种子种在花盆里一样,在这个模腔里,橡胶就会变成我们想要的形状。
我记得我第一次做橡胶齿轮模具的时候,模腔的精度不够,那做出来的齿轮就像缺了几颗牙的嘴巴,难看又不实用。
6. 哟,“冷却水道”这词也很关键呢。
它就像是给发烧的人头上敷的湿毛巾,能给模具降温。
要是没有冷却水道,模具就会一直处于高温状态,就像人在大夏天穿了棉袄一样难受。
我见过一个工厂做大型橡胶模具,因为冷却水道堵塞了,模具过热,生产出来的橡胶产品质量特别差。
7. “顶出机构”可是个“大救星”啊。
它就像一个小助手,在橡胶制品成型后,把制品从模具里顶出来。
橡胶成型工艺及模具设计

挤出机由螺杆、机身、机头(包括口型和芯型)、 机架和传动装置等部件组成。
一、螺杆
螺杆种类: 按螺纹分:单头、双头、 三头 按螺距分:等距收敛式和 复合螺纹等 按螺杆外形分:圆柱形、
圆锥形
二、机身(机筒)
机筒为中空圆筒,为了及时散发
和提供热量,机筒备有夹套,可通入
冷却水和蒸汽。
三、机头与口型
1.机头 ①直向形机头 如圆筒形、喇叭形 ②T形、Y形
5. 必须进行硫化才能使用,热塑性弹性体除外。
6. 必须加入配合剂。
其它如比重小、硬度低、柔软性好、气密性好等 特点,都属于橡胶的宝贵性能。
橡胶基本加工工艺
无论什么橡胶制品,都要经过混炼和硫化这两个 过程。橡胶基本加工工艺主要包括塑炼、混炼、 压延、压出、成型和硫化等。另外,对于一些特 殊产品还包括注压、浇注和黏合。
聚合单体:氯丁二烯 ★一般工作温度:-35~120℃
★特性:耐候性、耐臭氧性、阻燃、耐热性及耐化学 药品性均好 ★用途:轮胎内衬层、低压电线电缆、输送带、减震 橡胶、窗户密封条、胶粘剂、胶布、涂料 ★参考价格:3.0~3.5万元/吨
硅胶 (Q )
聚合单体:主链由硅原子和氧原子交替组成 ★一般工作温度:-93~250℃ ★性能:使用温度范围最广,毒性最低、具生理惰性、 透气性好、电绝缘性好,物理机械性能较差 ★用途:胶管、胶带、胶辊、电绝缘制品、人造皮肤、 器官等. ★参考价格:7.0~8.0万元/吨
三元乙丙胶 ( EPDM )
聚合单体: 乙烯\丙烯\第三单体 ★一般工作温度:-50~150℃ ★性能:耐老化耐臭氧性、耐极性液体、耐水及 过热水、水蒸气好、耐电性能好 ★用途:电线电缆绝缘层、汽车玻璃除水条、窗户密 封条、 蒸汽胶管、输送带等 ★参考价格:2.8~3.3万元/吨
橡胶模具

差 位 位置度
跳 圆跳动
动 全跳动
2020/7/18
曲轴
第三节 模具结构设计
一、压模结构设计及设计原则 (一)结构类型及分型面的选择 1.分型面的概念 将模具型腔分割成两个及两个以上可分离
部分的分割面称为分型面。
图13-6 O形密封圈模的两种分型面
2020/7/18
第三节 模具结构设计
2.分型面的选择原则 (1)保证制品易取出
1、孔与轴的概念
1)孔 2)轴
孔
+0
基本尺寸
上偏差
2020/7/18
es=0 基准轴h
基准孔H EI=0
基本偏差代号 a、b、c d、e、f cd、ef、fg g j 、 js j~n p~zc
使用要求 大间隙和热动配合
用于旋转运动 用于尺寸较小的旋转运动件
用于滑动或定位配合 用于与轴承相配合的轴
图13-l 橡胶矩形圈模 1—下模板;2—上模板;3—启模口;4—制品; 5—排气孔; 6—余料槽;7—定位销
2020/7/18
第一节 概 述
(二)分类 橡胶模具按模制方式可分为压模,压
铸模和注射模三种。
2020/7/18
第一节 概 述
1.压模 压模是将一定形状的胶料,加入
敞开的型腔内,用压机闭模加压,在 平板硫化机或立式硫化罐中硫化成型 的一种模具,它结构简单、造价低廉 、应用广泛。根据成型型腔的闭合形 式有开放式、封闭式和半封闭式之分 。
2020/7/18
2020/7/18
2020/7/18
2020/7/18
2020/7/18
2020/7/18
2020/7/18
2020/7/18
橡胶成型工艺及模具设计教程文件
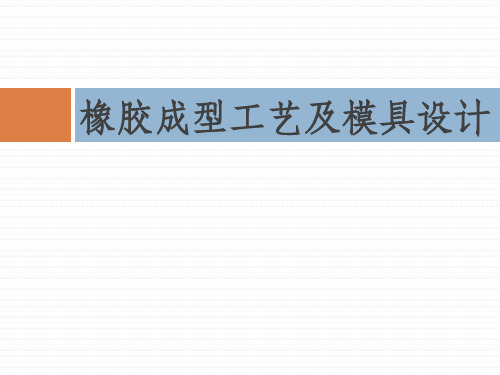
低温塑炼:机械降解为主
塑 机械塑炼法
炼 的 方 法 化学塑解法
高温塑炼:自动氧化降解 为主机械力强化橡胶与氧 的接触
混炼
指在炼胶机上将各种配合剂加入到 一、定义 橡胶中制成混炼胶的工艺过程
二、混炼的 目的和意义
1.保证产品的质量 2.适合于进一步的加工 3.高效节能
生胶的混炼性
第一种状态:不能紧包前辊 原因:混炼温度低,胶料的可塑性小。
第二种状态:紧包前辊 原因:温度适宜,胶料的可塑性中。
第三种状态:脱辊——出兜 原因:温度略高,胶料的可塑性略大。
第四种状态:粘流态包辊 原因:温度太高,可塑度太大
压延
压延—指将混炼胶在压延设备上制成胶片或与骨架 材料制成胶布半成品的工艺过程。
压延
压片 贴合 压型 挂胶(贴胶、擦胶)
从原理上看,压延过程主要是通过两个辊筒 作用把胶料辗压成具有一定厚度和宽度的胶片 的过程。
贴合是通过压延机将两层薄胶片贴合成一层胶 片的作业。 贴合工艺方法: 二辊压延机贴合 三辊压延机贴合 四辊压延机贴合
压型
压型是将胶料压制成一定断面形状的半成品或 表面有花纹的胶片。
压型工艺要求规格准确,花纹清晰,胶料密致, 故要求胶料收缩变形率小及配方中含胶率不宜过高。
压纺织物挂胶是使纺织物通过压延机辊筒间隙,使 其表面挂上一层薄胶,制成挂胶帘布或挂胶帆布, 作为橡胶制品的骨架层。
贴胶
贴胶是利用压延机上转速相同 辊筒的压力将一定厚度的胶片贴于 纺织物上。
压力贴胶
进行贴合的两辊筒之间有积胶, 利用积胶的压力将胶料挤压到布缝 中去。
擦胶
擦胶是利用辊速不同所产生的剪切 力和辊筒的压力,将胶料挤擦入纺 织物的缝隙中,以提高胶料与纺织 物的附着力。
橡胶类模具设计规范 (节选)

xxxx纯橡胶产品模具设计技术规范1目的为规范xxxx纯橡胶产品设计(以下简称公司产品)轴套类产品模具设计,特编制本标准。
2 使用范围本规范适用于本公司轴套类产品模具设计。
3 引用标准无4 轴套类模具的组成4.1 轴套类模具由上模板、中模板、下模板、型芯、定位销、定位套、导向销、导向套、抬耳等主要部分组成。
5 流道设计要求5.1 排布流道时,应避免流道分支处与上一级流道交汇处出现尖角,应圆弧过渡。
5.2 流道排布应平衡,避免出现不对称,影响注射效果,流道壁面粗糙度小于Ra 018μm。
5.3 流道末端处,应设有冷料穴,伸出长度一般为10mm。
6 轴套类产品特点6.1按轴套组成形式,设计模具前应了解轴套类产品结构、材质、产品材料性能6.1.1 A类轴套:由内管、外管加橡胶体构成。
A类轴套(带铁骨架)一般情况下设计成上、中、下三模板结构。
例如A类轴套还包括铝骨架、尼龙骨架。
由于铝骨架、尼龙骨架刚度较小在注射时由于注射压力变形量较大,在设计时中板应设计成哈夫块结构,以避免由于骨架膨胀造成卸件困难。
6.1.2 B类轴套:内管加橡胶体构成。
B类轴套模具为方便卸件一般情况下设计为哈夫块结构。
6.1.3外管为翻边的骨架,在设计时应注意上板能将翻边压住,避免外管上下移动造成产品尺寸不合格。
例如6.2安装部位精度要求安装部位包括定位销与模板销孔定位,装配为过盈配合以保证装配性能,一般定位销尺寸比销孔尺寸大0.05mm为宜。
6.3.4模具材料及热处理一般情况下模板需经热处理调质,考虑到模具成本原因。
模板多用45#钢,硬度要求为HRC28-32度;模芯材质为P20,硬度要求为HRC33-38;开发初期单腔模具一般采用未调质的45#钢。
7 分型面的选择7.1 分型面的数目应少且为平面。
7.2不影响产品的外观质量。
在分型面处不可避免地出现飞边,因此应避免在外观光滑面上设计分型面。
7.3分型面一般不取在装饰外表面或带圆弧的转角处。
橡胶模具加工流程

橡胶模具加工流程嘿,朋友们!今天咱来聊聊橡胶模具加工流程这档子事儿。
你说橡胶模具加工像不像一场奇妙的冒险呀!咱就从设计开始说起吧。
这设计啊,就好比是给要盖的房子画蓝图,得想得特别周到才行。
你得根据要做的橡胶制品的样子、大小,精心设计出模具的样子,这可不能马虎,不然做出来的东西可就走样啦!这要是没设计好,那不就像做饭没放盐,总觉得少了点啥。
然后呢,就是材料的选择啦。
就跟咱挑衣服似的,得选质量好的、合适的面料。
橡胶模具的材料也得好好挑,要耐用、能经得住各种折腾的。
要是选了个不靠谱的材料,那在加工过程中出问题可就麻烦喽!接下来就是加工啦!这可是个精细活儿。
就好像雕刻大师在雕琢一件艺术品一样,得小心翼翼、一点一点地来。
先用各种工具把材料加工成需要的形状,这过程可不能着急,得慢慢来,不然一不小心就毁了。
加工好了还不算完事儿,还得进行打磨呢!这就像是给人化妆,得把那些粗糙的地方都打磨得光滑细腻。
这样做出来的模具,用起来才顺手,做出来的橡胶制品才漂亮。
再说说装配吧,这就跟搭积木似的,得把各个部分准确地安装在一起。
要是装得不好,那可就松松垮垮的,还怎么干活呀!最后就是检验啦!这可太重要啦,就跟考试检查卷子似的,得认真看看有没有问题。
要是有瑕疵,那可不行,得赶紧改正。
你说这橡胶模具加工是不是挺有意思的呀!从设计到最后的检验,每一步都不能马虎,都得用心去做。
这就跟人生一样,每一个阶段都得认真对待,才能有一个好的结果。
咱再想想,要是每个环节都马马虎虎的,那最后做出的橡胶模具能好用吗?肯定不行呀!所以呀,咱做什么事儿都得认真负责,这样才能做出好东西来。
总之呢,橡胶模具加工流程可真是个有趣又有挑战的过程。
只有用心去做,才能做出高质量的模具,才能生产出让人满意的橡胶制品。
大家可别小瞧了这小小的橡胶模具,它背后可是凝聚了好多人的心血和努力呢!希望大家都能重视这个过程,让我们的橡胶制品行业越来越好!。
- 1、下载文档前请自行甄别文档内容的完整性,平台不提供额外的编辑、内容补充、找答案等附加服务。
- 2、"仅部分预览"的文档,不可在线预览部分如存在完整性等问题,可反馈申请退款(可完整预览的文档不适用该条件!)。
- 3、如文档侵犯您的权益,请联系客服反馈,我们会尽快为您处理(人工客服工作时间:9:00-18:30)。
用橡胶制作模具
用橡胶制作模具是从80年初开始使用的一种简易模具。
由于模具使用橡胶制成,必须在真空条件下将塑料注入模具中成形,所以也称为真空注模成形法。
到80年代中期,已有400多台真空注模装置投入运转。
并生产了一批汽车零件、电子电器零件、各种玩具零件及工艺美术制品等。
在小批量生产方面收到了缩短模具制造周期和降低生产成本的效果。
模具的结构
橡胶模是一种用手工在真空中注入塑料的模具,因而结构简单,如图1所
示。
在注入塑料之前,将橡胶模的两个半模对合后,用紧固带将其固紧。
在两个半模的分型面处插入注塑漏斗,即可在真空中注入塑料。
模具的制作过程
橡胶模的制作过程如图2所示。
首先用金属、塑料或木材等材料制作母型。
然后在母型的一端接上浇口材料(图3)。
这样在制成的橡胶模分型面处有一浇口,可插上注塑漏斗进行浇注。
然后将接上浇口料的母型放入浇注框中(图4)。
浇注框的内形即为橡胶模的外形,应保证有足够的型腔壁厚。
对已决定配比的硅橡胶主剂和固化剂进行搅拌后放入真空装置中,在减压真空条件下抽去搅拌时混入的空气(图5),约需7~10分钟。
下一步是将浇注框放入真空装置中进行浇注。
把母型全部埋没,并保证浇注上平面处型腔也有足够的壁厚(图6)。
对已浇成的橡胶模具再进行真空抽气。
尽量抽去混入橡胶模具中的空气(图7)。
抽气后将浇注框移出真空装置外,在室温下放置10~15小时,待其固化。
当完全固化后,即将橡胶模具从浇注框中取出。
沿浇口处将橡胶模切开,形成两块半模,并取出母型(图8)。
将两半模对合在一起即成为一副橡胶模具。
用橡胶模浇注塑件的过程
用橡胶模浇注塑件的过程如图9所示。
首先对主剂塑料和固化剂进行计量,并分别置于真空装置中进行抽气。
通过玻璃窗口确认其抽气状态,排出主剂和固化剂中水份和空气。
打开橡胶模具,对型腔喷乙醇进行清洗。
为便于脱模,再在型腔表面喷硅脱模剂。
然后将两半模对合,并在两边垫上垫板后用紧固带将橡胶模紧固在一起,插上漏斗,即可进行浇注。
将已抽气的主剂和固化剂混合搅拌(图10)。
再将混合料在真空中浇入橡胶模中(图11)。
在停止减压排气作业后,由室内大气压将退出来的塑料挤入型腔中(图12)。
然后待塑料在模具中完全固化。
若放在温中,则可加速固化。
开模时应先取下漏斗,松开紧固带,然后拆去两侧垫板。
用手工轻轻地将橡胶模沿分型面处打开。
再从橡胶模中取出塑件(图13),
取出塑件后,首先去除浇口废料。
然后对分型面处的废边和去除浇口废料后的部位进行精加工。
用橡胶模浇注成形的塑料及用途
基本上所有塑料均可用橡胶模浇注成形,如聚氨酯浇注塑料、环氧树脂,以及聚酯塑料、丙烯酸酯塑料、聚乙烯塑料等。
但橡胶模的渗透性很强,由于溶胀作用而使橡胶模具发生变形。
因而,用橡胶模浇注成形的主要是聚氨酯和环氧树脂两种材料。
最近开发了一种称为BT树脂的新材料。
这种材料的性能非常适合于用橡胶模浇注成形,受到各方面的关注。
通常把浇注塑料分成以下3种类型。
1.硬质类
目前用得最多的是热固性聚氨酯。
大多被用于试制汽车内装件及办公室机器中的塑料零件。
2.透明类
这主要是用环氧树脂制造的各种透明塑件。
3.软质类
主要是各种设备中的橡胶零件。
橡胶模的特点
通过多年的使用,可将橡胶模的特点归纳如下。
1.使用寿命通常为成形20~30件,最多可达到200件,能满足试制新产品样件数量的需要。
2.制模周期短,通常为1~3天。
浇注一只塑件的时间约为2小时。
因而在几天之内即可提供塑料样件。
3.由于在真空中浇注,所以塑件中的气泡极少,可成形高精度塑件,并由于硅橡胶的收缩极小,因而复映性能极佳,可真实地复映木纹、皮纹等各种装饰纹。
又由于硅橡胶具有一定的弹性,对于侧面的浅槽可采用强迫脱模。
4.不会因壁厚不同而出现气孔。
还可成形壁厚为0.5mm的薄壁件。
5.可成形带螺钉等金属嵌件的塑件。
6.制作母型的材料多样化。
可在金属、木材、塑料、石膏等材料中自由选择。
只是用木材制作母型时需进行填料处理。
硅橡胶的硬化温度是从室温到60℃,因具有高耐热性所以不必进行特殊加工,但浇注透明件时,母型表面必须达到镜面。
7.可对浇注塑料色及对浇注件进行涂装和真空电镀。
只要将浇注件在溶剂中进行蒸气洗净处理即可。
8.制作硅橡胶模具不需要特殊的熟练技术。
9.需减少模具的变形时,可用金属嵌件对橡胶模进行增强。
10.由于硅橡胶模具随温度变化略有变动,因而必须进行严格的温度控制。
真空浇注装置
按使用目的选用装置
1.新产品试制部门,其使用目的是为了快速制造样机的极少量零件,降低样机生产成本及保守新产品的设计秘密。
2.为客户加工试制样件的专业工厂,和现有手工操作加工样件同时使用,以缩短样件的交货时间,降低生产成本。
还可接受小批量生产的任务。
3.生产塑料制品的专业厂,为本厂开发新产品试制样件或接受客户订货后首先进行小批量试生产,以保证大批量生产时的产品质量,并以此作为接受多品种、小批量生产任务的一种加工手段。
真空浇注装置类型
1.手工操作型
这是一种最基本的类型。
塑料的计量、混合、浇注和脱模均用手工操作。
这种类型多适用于试制项目生产数量少的场合。
调换浇注塑料也比较方便。
2.手工操作加自动出料型
这是一种由手工操作加自动混料和出料装置的类型。
这种类型适用于生产数量较多或浇注件体积大而用料较多的场合。
3.半自动型
这是一种自动混合和定量出料后由手工操作浇注和脱模的类型。
这种类型设备在换料以后必须对混合部分用溶剂进行清洗。
它也具有手动功能。
4.全自动型
这是一种通过按钮即可对塑料自动进行定量、混合、出料、浇注及出模,调换材料时能自动用溶剂进行清洗。
这种类型适用于生产数量较多的场合。
用户应充分掌握各种类型真空浇注装置的使用特性,并根据试制品的数量,试制品的大小选择合适的类型。
目前,真空浇注装置还在不断完善,对各部份进行组合化,将更适合于用户的需要。
使用实例
按钮式电话机壳体
原来用手工加工10只样件的费用27,000美元。
现改用橡胶模浇注成形后,制作母型的费用为2,700美元。
制作硅橡胶模的费用2,600美元,浇注10只样件的总费用(材料费、人工费及使用设备费)共7,000美元。
合计为12,300美元,降低成本的55%。
传真机外壳
原来用手工加工10只样件的费用共40,000美元。
改用橡胶模浇注成形后,制作母型的费用为4,000美元。
制作橡胶模的费用为5,000美元,浇注10只样件的总费用为14,000美元。
合计23,000美元,降低成本约40%。
汽车保险杠
原来用手工加10只样件的费用共70,000美元。
改用橡胶模浇注成形后,制作母型的费用为7,000
美元。
制作硅橡胶模的费用为5,000美元。
浇注10只样件的总费用为5,000美元。
合计17,000美元,降低成本约76%。