8D培训课件Ppt
合集下载
8D培训讲义PPT45页
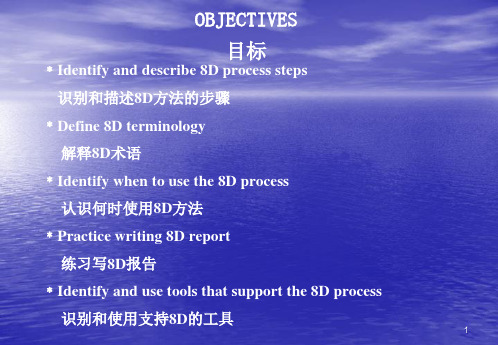
Agree on Team小组达成协议: *Workgroup guidelines工作组指导方针
*Structure结构 *Goals目标 *Roles任务 *Procedures程序
11
D1:TEAM FORMATION D1:成立小组
Work Group Guidelines工作组指导方针
☆ Agreement on the task and objective同意分配的任务及目标 ☆ Check on timing检查时间 ☆ Keep work visible 保存工作记录 ☆ Use supporting information from manual使用指南中的支持信息 ☆Define roles rotate 定义角色转换 ☆ Need any help需要帮助
存在于实际与非实际之间的偏差 Operational Definition操作型定义 *What’s wrong with what? (Object and defect)
什么事情出现什么问题?(对象和缺陷) Or或者 *What am I having trouble with and what is the trouble?
OBJECTIVES 目标
﹡Identify and describe 8D process steps 识别和描述8D方法的步骤
﹡Define 8D terminology 解释8D术语
﹡Identify when to use the 8D process 认识何时使用8D方法
﹡Practice writing 8D report 练习写8D报告
我有什么问题,并且问题是什么?
17
D2: DESCRIBE THE PROBLEM D2:描述问题
*Structure结构 *Goals目标 *Roles任务 *Procedures程序
11
D1:TEAM FORMATION D1:成立小组
Work Group Guidelines工作组指导方针
☆ Agreement on the task and objective同意分配的任务及目标 ☆ Check on timing检查时间 ☆ Keep work visible 保存工作记录 ☆ Use supporting information from manual使用指南中的支持信息 ☆Define roles rotate 定义角色转换 ☆ Need any help需要帮助
存在于实际与非实际之间的偏差 Operational Definition操作型定义 *What’s wrong with what? (Object and defect)
什么事情出现什么问题?(对象和缺陷) Or或者 *What am I having trouble with and what is the trouble?
OBJECTIVES 目标
﹡Identify and describe 8D process steps 识别和描述8D方法的步骤
﹡Define 8D terminology 解释8D术语
﹡Identify when to use the 8D process 认识何时使用8D方法
﹡Practice writing 8D report 练习写8D报告
我有什么问题,并且问题是什么?
17
D2: DESCRIBE THE PROBLEM D2:描述问题
8D培训教材(PPT 66页)

编号: ###
原因测试工作表
名称:生锈的曲轴
A+表示对关 键问题的答案 是肯定的。
A-表示对关键 问题的答案是 否定。
A?表示对关 键问题的答案 有待研究。
D4—发现并验证根本原因 测试潜在的根本原因
采用常规和传传统智慧 ▪一个小组成员 ▪小组集体智慧 ▪常理并非总正确,而传统智慧也不是永远明智 实验设计 为了查找根本原因,必须要进行正规的试验,例如 ▪就一个因素进行实验设计 ▪就几个因素进行实验设计
通过确定谁、什么、何时、何处、为什么、如何和
多大等定量来说明问题
超越现象 在问题描述中不要误用现象 使用问题确定单
D2——描述问题 描述问题的指南
范例
产品Product: 0 261 208 323
失效地点Location: 0-KM
数量Quantity: 126只
生产日期Prod. Date: 见附表
D2——描述问题
意图 让参加的人员理解: 定义问题对8-D方法的重要
性
妥当描述问题所用的技巧
确定顾客问题所用的程序
(建立数据库)
内容 描述问题的指南 解决问题的表单 更新8-D报告 解决问题查核清单
D2——描述问题 描述问题的指南
用顾客的口勿定义问题 利用常理 使用5W/2H问题
D3—实施并验证临时措施 缺点
成本高 着重于现象 灌输自满情绪 短期行为
D3—实施并验证临时措施 范围
内部作业 存储 正在进行的工作 供应商 返修中心 转送中 顾客处 所有发运和服务地
D3—实施并验证临时措施 验证
验证实施措施
验证为纠正措施奏效提供证明 可以由下述各项验证:样件、试生产、模拟 验证持续措施 验证临时纠正措施是否持续有效。这是因为始措施看
原因测试工作表
名称:生锈的曲轴
A+表示对关 键问题的答案 是肯定的。
A-表示对关键 问题的答案是 否定。
A?表示对关 键问题的答案 有待研究。
D4—发现并验证根本原因 测试潜在的根本原因
采用常规和传传统智慧 ▪一个小组成员 ▪小组集体智慧 ▪常理并非总正确,而传统智慧也不是永远明智 实验设计 为了查找根本原因,必须要进行正规的试验,例如 ▪就一个因素进行实验设计 ▪就几个因素进行实验设计
通过确定谁、什么、何时、何处、为什么、如何和
多大等定量来说明问题
超越现象 在问题描述中不要误用现象 使用问题确定单
D2——描述问题 描述问题的指南
范例
产品Product: 0 261 208 323
失效地点Location: 0-KM
数量Quantity: 126只
生产日期Prod. Date: 见附表
D2——描述问题
意图 让参加的人员理解: 定义问题对8-D方法的重要
性
妥当描述问题所用的技巧
确定顾客问题所用的程序
(建立数据库)
内容 描述问题的指南 解决问题的表单 更新8-D报告 解决问题查核清单
D2——描述问题 描述问题的指南
用顾客的口勿定义问题 利用常理 使用5W/2H问题
D3—实施并验证临时措施 缺点
成本高 着重于现象 灌输自满情绪 短期行为
D3—实施并验证临时措施 范围
内部作业 存储 正在进行的工作 供应商 返修中心 转送中 顾客处 所有发运和服务地
D3—实施并验证临时措施 验证
验证实施措施
验证为纠正措施奏效提供证明 可以由下述各项验证:样件、试生产、模拟 验证持续措施 验证临时纠正措施是否持续有效。这是因为始措施看
8D培训课程(共38张PPT)
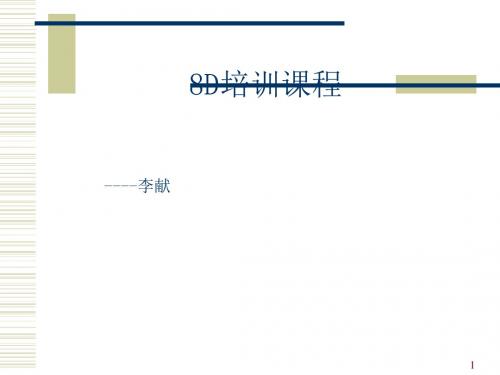
25
1.成立小组
按问题涉及范围确定小组成员:
责属单位:
生管课、销售课、库管课、品保课 责属人员: 贾正羽、庄卫年、赵晓明、许 丽
26
2.问题描述
1999年11月4日; 浙江精密机械厂; 浙江精密机械厂—包装车间; 包装ALT-5检测器时,使用20μ MHT 机用膜一拉就断; 如何 : 在IPEX预拉型缠绕机上使用,转速为 30M/MIN,预拉后倍数为3 。 为什么:机用膜卷端口破损; 多少 : 20卷中目前发现6卷有问题。
8D培训课程
----李献
1
8D方法
8D:所谓8D方法(eight disciplines),又 称团队导向问题解决步骤,是福特公司处 理问题的一种方法,亦适用于制程能力指 数低于其应有值时有关问题的解决。
2
何謂8D
此方式是团队运作导向以事实为基础,避 免个人主见的介入,使问题的解决能更具 条理。 此方式宜由公司各部门人员的共同投入, 求得创造性及永久性的解决方案。 此方式可适用于任何问题,而且能促进相 关目标的各部门间有效的沟通。
27
何时 何人 何地 何事
: : : :
3.执行和确认临时措施
品保课立即派员到浙江精密机械厂检查 全部20μ MHT机用膜,并挑出有问题的 膜。(许丽 完成日期99/11/05) 对挑选出的破损20μ MHT机用膜运回公 司,按数补给浙江精密机械厂。并确认 补货后的情况。(许丽 完成日期99/11/05) 对现有生产、贮存、出货的20μ MHT机 用膜进行全数检验。(许丽 完成日期99/11/05)
3
8D 精神
面对问题不可以各自为 政、自我本位主义,否 则将无法有效解决问题。
1.成立小组
按问题涉及范围确定小组成员:
责属单位:
生管课、销售课、库管课、品保课 责属人员: 贾正羽、庄卫年、赵晓明、许 丽
26
2.问题描述
1999年11月4日; 浙江精密机械厂; 浙江精密机械厂—包装车间; 包装ALT-5检测器时,使用20μ MHT 机用膜一拉就断; 如何 : 在IPEX预拉型缠绕机上使用,转速为 30M/MIN,预拉后倍数为3 。 为什么:机用膜卷端口破损; 多少 : 20卷中目前发现6卷有问题。
8D培训课程
----李献
1
8D方法
8D:所谓8D方法(eight disciplines),又 称团队导向问题解决步骤,是福特公司处 理问题的一种方法,亦适用于制程能力指 数低于其应有值时有关问题的解决。
2
何謂8D
此方式是团队运作导向以事实为基础,避 免个人主见的介入,使问题的解决能更具 条理。 此方式宜由公司各部门人员的共同投入, 求得创造性及永久性的解决方案。 此方式可适用于任何问题,而且能促进相 关目标的各部门间有效的沟通。
27
何时 何人 何地 何事
: : : :
3.执行和确认临时措施
品保课立即派员到浙江精密机械厂检查 全部20μ MHT机用膜,并挑出有问题的 膜。(许丽 完成日期99/11/05) 对挑选出的破损20μ MHT机用膜运回公 司,按数补给浙江精密机械厂。并确认 补货后的情况。(许丽 完成日期99/11/05) 对现有生产、贮存、出货的20μ MHT机 用膜进行全数检验。(许丽 完成日期99/11/05)
3
8D 精神
面对问题不可以各自为 政、自我本位主义,否 则将无法有效解决问题。
8D培训教材(PPT 55页)

階段, 穩定製程使產量固定是很重要的 • 待標準建立了並且穩定了, PDCA 則是用來
改變製程提昇水準. 但是一旦製程一改變, 又會馬上變得不穩定, 需要以SDCA加以穩 定化
PDCA 與 SDCA
屬於兵力的提昇 (提昇製程的能力)
AP CD
AP CD
AS CD
AS CD
屬於兵力的維持 (2將0 製of 程11穩1 定化)
5.最適策實施
16 of 111
f 111
C-A-P-D-C-A
• 檢視現狀-再對策-企劃-實行-檢核-行動 • 是問題解決型QC改善歷程 • 注重在已發生問題的處理 • 在PDCA循環注重在Do, 故Do的內部尚有小
型的PDCA循環,直到問題改善為止 • 小規模的改進,非大刀闊斧的改革
CA-PDCA 循環輪
工程師不知 有Hold Lot
ON HOLD LOT 太多
工程師太忙 沒時間處理
工程師未 作處置
工程師待
工程師忘記
客戶指示
有Hold Lot
客戶Release
good Hold reject Hold Yield
太高不合理
12 of 111
客戶要求作 工程分析
客戶一直 未回覆
待客戶 新程式
PDCA 的介紹
• 水準不足良率損失Chronics: 良率水準不足 。發生眾多批數,其良率相對低於水準內 的良率。
f 111
如何管理異常良率
• 有效管理異常可以 – 將干擾降低 – 提昇 Xbar 水準 (幫助不大, 因為屬於少數)
• 暫時管制措施是重要的 – 第一件事就是將產品 “Hold” – 再來才是解決問題, 預防問題的再發
ON HOLD LOT 太多
改變製程提昇水準. 但是一旦製程一改變, 又會馬上變得不穩定, 需要以SDCA加以穩 定化
PDCA 與 SDCA
屬於兵力的提昇 (提昇製程的能力)
AP CD
AP CD
AS CD
AS CD
屬於兵力的維持 (2將0 製of 程11穩1 定化)
5.最適策實施
16 of 111
f 111
C-A-P-D-C-A
• 檢視現狀-再對策-企劃-實行-檢核-行動 • 是問題解決型QC改善歷程 • 注重在已發生問題的處理 • 在PDCA循環注重在Do, 故Do的內部尚有小
型的PDCA循環,直到問題改善為止 • 小規模的改進,非大刀闊斧的改革
CA-PDCA 循環輪
工程師不知 有Hold Lot
ON HOLD LOT 太多
工程師太忙 沒時間處理
工程師未 作處置
工程師待
工程師忘記
客戶指示
有Hold Lot
客戶Release
good Hold reject Hold Yield
太高不合理
12 of 111
客戶要求作 工程分析
客戶一直 未回覆
待客戶 新程式
PDCA 的介紹
• 水準不足良率損失Chronics: 良率水準不足 。發生眾多批數,其良率相對低於水準內 的良率。
f 111
如何管理異常良率
• 有效管理異常可以 – 將干擾降低 – 提昇 Xbar 水準 (幫助不大, 因為屬於少數)
• 暫時管制措施是重要的 – 第一件事就是將產品 “Hold” – 再來才是解決問題, 預防問題的再發
ON HOLD LOT 太多
8D培训课件ppt43页2514

8D –D6实施和确认永久性纠正措施
验证PCA
l 要证明问题已经被彻底解决了,如果不能证明,你就不能说 问题解决了
l 在验证PCA前,要确定已经取消了临时措施,否则临时措施 可能掩盖永久措施的真实效果
l 验证最重要的是客户跟踪:
Ø 确定客户对你的结果是否满意 Ø 确定问题已真正被解决 Ø 是否已通过对客户需求的关注,提高了公司的信誉及客户满意度
8D –D7预防问题再次发生
为什么要预防问题的再次发生
l 如果一个问题需要采用8D,那么至少一个系统、程序或 政策使得问题发生和逃出。
l 通常系统的问题由沿用的程序、政策和前一个组织、技术 和能力引起的。
l 这些沿用的内容通常是: Ø 过时的 Ø 完全不充分的 Ø 未遵循的
8D –D7预防问题再次发生
培训内容 l 8D的概述 l 8D的特点 l 8D过程概述 l 8D不合格实例
8D 概述
• 8D(8-Discipline),即8个解决问题的固定步骤;也可称为 TOPS(Team Oriented Problem Solving)即团队导向问题解 决方法
• 二战期间,美国政府率先采用一种类似8D的流程——“军事 标准1520”,又称之为“不合格品的修正行动及部署系统” 。 1987年,福特汽车公司首次用书面记录下8D法,在其一份 课程手册中这一方法被命名为“团队导向的问题解决法”
为什么要制定ICA
维护系统继续运行 为8D小组找到问题的根本原因争取时间 保护顾客利益和满意度不受影响 保证质量,节约因问题继续产生的成本
8D –D3 实施并验证临时纠正措施ICA
制定ICA的四个步骤
验证ICA(
措施)
选择ICA
执行ICA
8D培训课程ppt73页
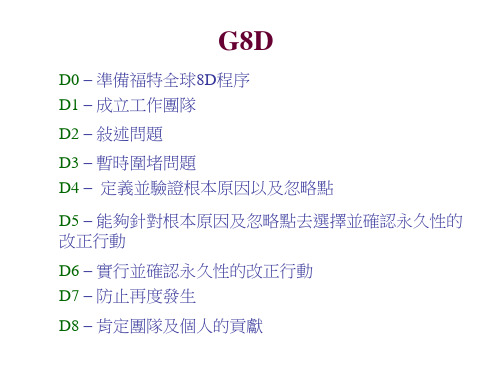
主题1:印刷下机甲苯含量小于5mg/m2合格率
D1 紧急处置
序号 紧急事件定义 处置等级 规格值
紧急处置措施
负责人员
SOP
1.印刷速度降低至200m/min,并
依据《溶剂残留超标处置办法》 领机
一级
逐项排查原因 5-10mg/m2
2.所生产的产品通知当班PQC管
控,依据《溶剂残留超标处置办 当班PQC
当班PQC每订单稽核
2.2.1烘箱温度设置未执 2.2.1印刷领机未按要
行标准
求设定印刷温度
当班PQC每订单稽核
2.2烘箱温度达不到 要求
2.2.2烘箱传感器失灵
2.2.2.2烘箱传感器老 化
機
2.2.3烘箱加热系统损坏
委托在9月30日前对设备烘箱的传感器进 行全面的检查
委托在9月30日前对设备烘箱的传感器进 行全面的检查
4.1.1 设备磨损
測
4.2 GC检测不 准确
4.2.1 设备故障
加强油墨进料的检测
10月20日前请设备厂家校正一次 10月20日前请设备厂家保养一次
D3 柏拉图
不良次数(个) 不良比率(%)
项 不良 失败金额 比率 累计 次 原因 (千元) (%) (%)
1 油墨释放
6
性差2 溶剂添加源自4过量3 烘箱温度
机
请保全对每个烘箱电机进行检查, 如有隐患,立即停机维修
2.3.1印刷烘箱设计风 量不足
2.2印刷排风量不 足
2.3.2印刷排风量未按 规定设置
在保证产品质量的前提下,将目前 的排风量设置在最大值
每个订单施行当班PQC首末检查
D4局部对策-印刷下机甲苯含量>5mg/m2
項 目
品质部培训8D课程PPT培训课件
实施永久措施
总结词
制定并实施永久措施,从根本上解决问题, 防止问题再次发生。
详细描述
在8D方法实施流程中,实施永久措施是为 了从根本上解决问题,防止问题再次发生。 这些措施应该是经过深思熟虑和充分验证的, 具有长期性和稳定性。在实施永久措施的过 程中,团队需要密切关注措施的效果,及时 调整和完善,以确保问题得到彻底解决。
详细描述
在8D方法实施流程中,实施临时措施是为了控制问题的进一步发展,减轻其对产品、过程和客户的影 响。这些措施通常是紧急的、临时的,旨在稳定局势,为后续的深入分析和改进提供基础。
确定并验证根本原因
总结词
深入分析问题,找出根本原因,为制定 永久措施提供依据。
VS
详细描述
在8D方法实施流程中,确定并验证根本 原因是关键的一步。团队需要运用科学的 方法和工具,对问题的根本原因进行深入 分析,并对其进行验证。只有确定了问题 的根本原因,才能制定出有效的永久措施 ,从根本上解决问题。
04
8D方法应用案例分析
应用案例一:汽车行业中的8D方法应用
总结词
广泛采用、标准化流程
VS
详细描述
汽车行业是8D方法应用最为广泛的领域 之一。各大汽车制造商采用8D方法来解 决生产过程中出现的各种质量问题,确保 产品的一致性和可靠性。通过标准化流程 ,8D方法在汽车行业中实现了高效的问 题解决和持续的质量改进。
02
8D方法实施流程
成立专项团队
总结词
组建跨部门、跨领域的团队,确保问题解决的有效性和效率。
详细描述
在8D方法实施流程中,第一步是成立一个由不同部门和领域专家组成的专项团 队,以确保问题解决的全面性和专业性。这个团队应该具备丰富的经验和技能, 能够针对不同的问题进行深入分析和有效解决。
8D培训教材ppt课件
Never repeat a problem. 不让问题重现
*
Congratulate the team 团队庆祝
8
8 D Problem Solving, Autoliv Standard AS63
Reinforces behavior 增强了领导力 Reinforces teamwork 增强了团队精神 Improves culture 提升了企业文化
Use Data 使用数据 Pictures/sketches of Desired and Actual conditions实际与期望情况下的照片和草图 “Go and See” approach 去现场观察 Compare OK and NOT OK conditions比较 “OK” 和 “NOT OK” 的情况 “A well defined problem is 50% solved.”当一个问题有了很好的定义,那该问题就已经解决了一半
*
5 Why Tool 5个为什么
Ask “why” to understand problems 通过问”为什么来理解问题 Ask “why” at least 5 times. 至少问5次”为什么” Ask as many “whys” as you can, then go 1 more 尽量多问几次”为什么” Verify that the “whys” are true 验证这些”为什么”是正确的 Gather data, go and see.收集现场收集数据 Try to turn the problem on and off 试着还原并解决问题
*
End 结束
课件部分内容来源于网络,如对内容有异议或侵权的请及时联系删除! 此课件可编辑版,请放心hy!”
*
Congratulate the team 团队庆祝
8
8 D Problem Solving, Autoliv Standard AS63
Reinforces behavior 增强了领导力 Reinforces teamwork 增强了团队精神 Improves culture 提升了企业文化
Use Data 使用数据 Pictures/sketches of Desired and Actual conditions实际与期望情况下的照片和草图 “Go and See” approach 去现场观察 Compare OK and NOT OK conditions比较 “OK” 和 “NOT OK” 的情况 “A well defined problem is 50% solved.”当一个问题有了很好的定义,那该问题就已经解决了一半
*
5 Why Tool 5个为什么
Ask “why” to understand problems 通过问”为什么来理解问题 Ask “why” at least 5 times. 至少问5次”为什么” Ask as many “whys” as you can, then go 1 more 尽量多问几次”为什么” Verify that the “whys” are true 验证这些”为什么”是正确的 Gather data, go and see.收集现场收集数据 Try to turn the problem on and off 试着还原并解决问题
*
End 结束
课件部分内容来源于网络,如对内容有异议或侵权的请及时联系删除! 此课件可编辑版,请放心hy!”
8D报告培训 ppt课件
拉就断; ·如何:在IPEX预拉型缠绕机上使用,转速为30M/MIN ,
预拉后倍数为3; ·为何:机用膜卷端口破损; ·多少:20卷中目前发现6卷有问题。
04 8D步骤-D3 临时对策
临时应对之法。在永久性对策尚未确定之前 ,先对问题进行实施围堵行动,以使内部/外 部顾客免受问题的继续困扰。
1、防止继续产生不良品。
04 8D步骤-D3 临时对策
临时对策 长期对策
消除问题 及后果
消除问题 原因
只能治标 (可能再发)
可以治本 (不会再发)
04 8D步骤-D4 原因分析
用统计工具列出可以用来解释问题起因的所 有潜在原因,再分别针对每一可能原因予以 测试,最终确定产生问题的根本原因。
1、列可能原因时要周全。
5M1E
1、一定是针对根本原因来 制订措施,一个原因可能有 几条措施。
需考 虑的 问题
2、措施尽量具体化。
3、及时对已经明确的措施进 行验证。
04 8D步骤-D6 跟踪检查
应对以下方面进行验证:临时措施,长期措 施,问题的现状。验证已实施的措施是否将 问题彻底消除(短期措施,长期措施,即其 它类似的流程),并且不会产生其它的问题 。
02
04
临时措施实施中,应 及时跟踪和验证其效果。
04 8D步骤-D3 临时对策
为消除已发现的不合 格或其他不期望情况 的原因所采取的措施
。
区别
采取纠正措施 是为了防止再 发生,采取预 防措施是为了 防止发生。
为消除潜在不合格或 其他潜在不期望情况 的原因所采取的措施 。
纠正措施 (亡羊补牢)
预防措施 (未雨绸缪)
• “太阳当空照,花儿对我笑,小鸟说早早早……”
预拉后倍数为3; ·为何:机用膜卷端口破损; ·多少:20卷中目前发现6卷有问题。
04 8D步骤-D3 临时对策
临时应对之法。在永久性对策尚未确定之前 ,先对问题进行实施围堵行动,以使内部/外 部顾客免受问题的继续困扰。
1、防止继续产生不良品。
04 8D步骤-D3 临时对策
临时对策 长期对策
消除问题 及后果
消除问题 原因
只能治标 (可能再发)
可以治本 (不会再发)
04 8D步骤-D4 原因分析
用统计工具列出可以用来解释问题起因的所 有潜在原因,再分别针对每一可能原因予以 测试,最终确定产生问题的根本原因。
1、列可能原因时要周全。
5M1E
1、一定是针对根本原因来 制订措施,一个原因可能有 几条措施。
需考 虑的 问题
2、措施尽量具体化。
3、及时对已经明确的措施进 行验证。
04 8D步骤-D6 跟踪检查
应对以下方面进行验证:临时措施,长期措 施,问题的现状。验证已实施的措施是否将 问题彻底消除(短期措施,长期措施,即其 它类似的流程),并且不会产生其它的问题 。
02
04
临时措施实施中,应 及时跟踪和验证其效果。
04 8D步骤-D3 临时对策
为消除已发现的不合 格或其他不期望情况 的原因所采取的措施
。
区别
采取纠正措施 是为了防止再 发生,采取预 防措施是为了 防止发生。
为消除潜在不合格或 其他潜在不期望情况 的原因所采取的措施 。
纠正措施 (亡羊补牢)
预防措施 (未雨绸缪)
• “太阳当空照,花儿对我笑,小鸟说早早早……”
8D培训教材(PPT 103页)
Develop a Problem Statement 陈述问题
制定一个问题陈述:
•
确定对象及其缺陷(问“什么东西出什么问题啦?
”)
•
使用多次问“为什么”这样的技巧,定义发生问题
的对象是什么,及其相应的缺陷到底是什么?
Repeated Why’s
反复问“为什么”
一旦对象和缺陷确定了,下一步就是对它们细化
Team Roles 团队角色
团队成员应该以高效率的方式工作
8D的过程依赖于所有团队成员的努力来达到团 队的目标
为达到团队目标,每个成员扮演一个角色
The Team Leader团队领导
团队领导是一个在整个8D过程中负责领导团队成员的人,这个人有领导能力和 人际关系的技能。
The Team Leader团队领导
Welcome
8D
课程内容
章节:
8D过程及分析工具概述 D0 问题识别 D1 组建团队 D2 陈述问题 D3 执行并验证临时措施 D4 确定并验证根本原因 D5 验证永久措施 D6 执行并确认永久措施 D7 预防问题重现
Course Objectives 课程目标
完成这门课程之后你应该能够:
它某个地方 • 问题什么时候发生,什么时候不发生,但是也许某个
时候还会发生 • 问题严重程度有多大,没有多大,但也是其它某个状
况
Is/Is Not Worksheets 是/不是 工作表
在8D过程中,你可以利用“是/不 是” 工作表来帮助你确定并追踪 问题的细节。这张表能帮助你按 照合理的方式制定一个详细的问
D1的重点是组建团队(为解决问题并 执行纠正措施做准备)
D1 Section Objectives D1阶段目标
- 1、下载文档前请自行甄别文档内容的完整性,平台不提供额外的编辑、内容补充、找答案等附加服务。
- 2、"仅部分预览"的文档,不可在线预览部分如存在完整性等问题,可反馈申请退款(可完整预览的文档不适用该条件!)。
- 3、如文档侵犯您的权益,请联系客服反馈,我们会尽快为您处理(人工客服工作时间:9:00-18:30)。
8D培训
一汽解放汽车有限公司质保部
二O一二年八月
8D 概述 8D 过程概述 8D 过程介绍 8D课程总结
8D概述
8D的来源:
8D是福特公司解决问题的标准方法
–背景: – ISO/TS16949 解决问题—8.5.2.1 组织应有一个确定的过程用于解决问题,使根本原 因得到识别并消除。 若有顾客规定的解决问题的方式,则组织应采用此 方式。
可观察的:它描述了问题的可见迹象;
可测量的:它描述了“多少”或“多少频度”,以定量的术语指 明了问题的范围。
可控制的:一个可控制的问题是一个可以在6到12个月内解决的 问题。如果一个问题太大,它应被分解成几个更小的可控制的问 题。
例子:我们公司比主要的竞争对手在交付零件的流程 上平均多花10天以上的时间 具体的-----交付流程多花的时间 可观察的-----从内部报告和顾客反馈 可测量的-----交付的时间以天来测量 可控制的-----限制在交付流程中 问题描述的标准:一个有效的问题描述 ●不能暗示原因 在问题描述中暗示原因可能误导解决问题; 例子:我们公司比我们主要的竞争对手在交付零件的流程 上平均多花10天以上的时间,在零件运送前,可减少文件 批准耽搁时间。
……
Cpk分析
D1 建立小组
D1 建立小组 建立一个小组来解决问题和执行修正计划,小组成员应
具有过程和产品知识、所需的时间、权威和需要的技能。
概述: D1过程的中心是建立解决问题和执行修正行动所需的小
组。
建立小组的必要性:
– “D1 建立小组” 为8D过程的真正开始。 – 极少有一个人具有所有需要的资源、资料和技能来解决
– 用“重复的为什么技术” 精炼对象和缺陷
–一旦对象和缺陷建立了,下一步是精炼它们
–问“那个对象为什么出现那个缺陷”来精炼初步的问题
–继续问“为什么”直到不能肯定回答。如果原因未知并 且需要找到根本原因,最后一个对象和缺陷就是问题陈 述
–再三地问“那个对象为什么出现那个缺陷”的过程称为 重复问为什么技巧
什么是8D?
– 由1个准备步骤和8个正式步骤组成,具体如下: D0:为8D过程做准备 D1:成立小组 D2:问题的描述 D3:确定临时纠正措施(ICA)的开发 D4:确定和验证根本原因和问题逃出点 D5:确定和验证针对根本原因和问题逃出点的永久性纠正措施( PCA) D6:实施和确认PCA D7:防止再发生 D8:承认小组及个人的贡献
– 这些步骤用来客观地确定、定义和解决问题并防止相似问题的再 次发生。
8D的有效实施需要其他质量工具的支持 ✓可靠性 ✓设计验证,产品和过程确认 ✓工艺技术 ✓潜在失效模式及后果分析 (FMEA) ✓控制计划 ✓生产件批准程序 (PPAP)/节拍生产 ✓统计过程控制(SPC) ✓试验设计 (DOE)
一个复杂的问题。 – 一组合适的人员能够包括所有必须的资源和聚集每一个
人所具有的技能。 确定小组成员时应考虑:
– 将人数限制在4-10人。 – 选取具有恰当的技能、知识、资源、权威等的人员。 – 选取具有不同背景的人员。 – 根据需要变更小组成员。
小组角色:
–8D小组一旦建立,小组成员需要尽可能有效地工作。 –8D过程依靠每一位小组成员的努力来达到小组的目标。 –每位小组成员扮演一个角色。 –每一个角色集中在功能上而不是每一个成员,这可以帮助
●不能提出改进方案 在不知道原因的情况下,不可能找出某种 有效的改进措施。
例子:我们公司比我们主要的竞争对手在交付零件的流程上平均 多花10天以上的时间,安装一个计算机化的交付程序来加速处理 过程。
●不能给予责备 问题描述中给予责备会减少人们参与解决问题 的积极性,而且在不知道问题原因的情况下责备可能是错误的。
– 所选择的完成8D过程的小组成员没有技术知识。 – 仅有一两个人实施该过程。
成立8D团队
建立一个团队,团队成员 具备相关产品的知识,有解决 问题需要的时间和授予的权限 ,具有所要求的解决问题和实 施纠正措施的技术素质,团队 必须有一个指定的带头人;
团队成员由与问题密切相 关的技术人员或管理人员、相 关的质量工程师组成。
D0 准备8D
D0 准备8D过程(包括必要时的ERA) 根据现象评估8D过程是否需要。 如果需要,应采取紧
急反应行动(Emergency Response Action----ERA)来保护 顾客,并开始8D过程。 为什么要为8D过程作准备:
–8D的过程是很精深的。可能涉及大量的时间、人员和资 源。当然也会浪费大量的时间、人员和资源。
怎样描述问题
–问题陈述 –问题描述 问题陈述:是确定未知原因引起的问题的对象和缺陷的
简单、简明的陈述。
–怎样进行问题陈述 –识别对象和缺陷(问“什么出现了什么问题”) – “什么问题”是缺陷 – “什么出了问题”是对象 –问‘什么出了什么问题’能够帮助小组以问题 陈述所需的两个基本要素为中心(对象和缺 陷)。
A
B
C
D
Who Responsibility
Jim Sue Lynn Bill/Jim
……
时间管理
D2 描述问题
D2 描述问题 通过‘什么出现什么问题’来描述内部/外部的问题,用量
化的术语细化问题。
为什么要描述问题 : –要想成为一个有效的问题解决者,必须在采取行动前 知道尽可能多的关于问题的描述。 –D2 阶段应尽可能准确地定义问题 –在D2阶段的任何不清楚和不准确都会导致小组得到错 误的原因和采取错误的修正行动。
相关的QC工具
团队宪章
业务个案 目标陈述
机遇陈述 项目范围
项目计划
团队人选
行动计划
TASKS TASKS
ACTIVITIES ACTIVITIES
RESP.
START
DUE
RESP.
START
DUE
STATUS &ACTIONS
Gantt Chart (Pilot)
What
When
Task
Jan Feb Mar Apr May
…….
Frequency Count
Percent
相关的QC工具
Histogram of x Normal
4
Mean 1.285
StDev 0.1316
N
15
3
2
1
0
1.0
1.1
1.2
1.3
1.4
1.5
1.6
x
直方图
Pareto Chart of Defect
400
100
80 300
60
200
145
40
100
96
48
58
20
32
29
0
0
Defect
PCBA 马 达 响 外 观 投 影 虚 风 扇 响 Other
Count
145
96
48
32
29
58
Percent
35.5
23.5
11.8
7.8
7.1
14.2
Cum %
35.5
59.1
70.8
78.7
85.8
100.0
ห้องสมุดไป่ตู้排列图
Cpk=0.852
控制图
-6 4 14 24 34 44 54 64 74
8D的使用时机
– 外部客户要求使用8D报告 – 公司内部重复发生不合格的纠正措施 – 重大客户抱怨时。 8D的目的
– 通过准确完成8D过程,防止问题的再发生并改进整个制 造系统。
– 确定根本原因,成功实施纠正措施计划(CAP)
8D问题的提出
– 对于产品、过程出现重复发生不合格时,应采用8D方法做 反应。
– 在会议中重新叙述和记录小组的决定 – 使小组的决定可见 – 管理小组的文件
记录员:
– 书写和分发会议纪要 – 为小组提供管理支持 – 确保每一个小组成员都有机会做贡献 协调员:
– 集中于小组维护 – 同小组一起工作解决冲突 – 在每个G8D阶段提出建议 成员:
– 找出答案 – 执行行动 常见性错误
改写:一车间生产的泵有2%不能通过安全/耐久性试验,因此必须 报废 。
要想成为一个有效的问题 解决者,必须在采取行动 前知道尽可能多的关于问 题 的 描 述 。 在 D2 阶 段 的 任 何不清楚和不准确都会导 致小组得到错误的原因和 采取错误的纠正行动。
用可量化的术语,如与该 问题有关的人员、内容、 时间、地点、原因、方式 和程度(5W1H)等详细说 明内部/外部顾客的问题。
–判别使用8D过程是合适的。如果不合适,那么,您可能 用其它方法来解决每一个单一的问题。
紧急反应行动(ERA): 紧急反应行动是在决定是否采用8D时用来保护顾客和受 影响的各方面的任何行动。
通常由领导(对问题负责和授权解决问题 的人)决定是否执行ERA。在任何情况下 都需要评估是否需要ERA。 有时需要不止一个ERA来完全保护我们的顾客。例如,一个ERA 用来保护顾客,另一个用来保护他们免受第一个ERA带来的副作用。
– 与最终产品质量有关的问题及其纠正措施需通报特殊或重 点顾客的应采用8D方法。
顾客将通过确认8D报告来决定这些问题是否已经回答:
– 对零件的知识进行了充分论证。 – 完全确定了根本原因并聚焦于该原因。 – 问题逃出点已经被识别。 – 确定与根本原因相匹配的纠正措施。 – 纠正措施计划的验证已经被确定。 – 包括了实施纠正措施的时间计划。 – 有证据显示供方将把纠正措施纳入整个系统。
紧急反应行动(ERA)的选择和验证
–当您验证ERA时,要在行动执行前证明ERA能够保护顾客并不会产生 新的问题。
–可以在非生产产品上验证ERA,例如样件或计算机模拟计算。 紧急反应行动(ERA)的执行和确认:
一汽解放汽车有限公司质保部
二O一二年八月
8D 概述 8D 过程概述 8D 过程介绍 8D课程总结
8D概述
8D的来源:
8D是福特公司解决问题的标准方法
–背景: – ISO/TS16949 解决问题—8.5.2.1 组织应有一个确定的过程用于解决问题,使根本原 因得到识别并消除。 若有顾客规定的解决问题的方式,则组织应采用此 方式。
可观察的:它描述了问题的可见迹象;
可测量的:它描述了“多少”或“多少频度”,以定量的术语指 明了问题的范围。
可控制的:一个可控制的问题是一个可以在6到12个月内解决的 问题。如果一个问题太大,它应被分解成几个更小的可控制的问 题。
例子:我们公司比主要的竞争对手在交付零件的流程 上平均多花10天以上的时间 具体的-----交付流程多花的时间 可观察的-----从内部报告和顾客反馈 可测量的-----交付的时间以天来测量 可控制的-----限制在交付流程中 问题描述的标准:一个有效的问题描述 ●不能暗示原因 在问题描述中暗示原因可能误导解决问题; 例子:我们公司比我们主要的竞争对手在交付零件的流程 上平均多花10天以上的时间,在零件运送前,可减少文件 批准耽搁时间。
……
Cpk分析
D1 建立小组
D1 建立小组 建立一个小组来解决问题和执行修正计划,小组成员应
具有过程和产品知识、所需的时间、权威和需要的技能。
概述: D1过程的中心是建立解决问题和执行修正行动所需的小
组。
建立小组的必要性:
– “D1 建立小组” 为8D过程的真正开始。 – 极少有一个人具有所有需要的资源、资料和技能来解决
– 用“重复的为什么技术” 精炼对象和缺陷
–一旦对象和缺陷建立了,下一步是精炼它们
–问“那个对象为什么出现那个缺陷”来精炼初步的问题
–继续问“为什么”直到不能肯定回答。如果原因未知并 且需要找到根本原因,最后一个对象和缺陷就是问题陈 述
–再三地问“那个对象为什么出现那个缺陷”的过程称为 重复问为什么技巧
什么是8D?
– 由1个准备步骤和8个正式步骤组成,具体如下: D0:为8D过程做准备 D1:成立小组 D2:问题的描述 D3:确定临时纠正措施(ICA)的开发 D4:确定和验证根本原因和问题逃出点 D5:确定和验证针对根本原因和问题逃出点的永久性纠正措施( PCA) D6:实施和确认PCA D7:防止再发生 D8:承认小组及个人的贡献
– 这些步骤用来客观地确定、定义和解决问题并防止相似问题的再 次发生。
8D的有效实施需要其他质量工具的支持 ✓可靠性 ✓设计验证,产品和过程确认 ✓工艺技术 ✓潜在失效模式及后果分析 (FMEA) ✓控制计划 ✓生产件批准程序 (PPAP)/节拍生产 ✓统计过程控制(SPC) ✓试验设计 (DOE)
一个复杂的问题。 – 一组合适的人员能够包括所有必须的资源和聚集每一个
人所具有的技能。 确定小组成员时应考虑:
– 将人数限制在4-10人。 – 选取具有恰当的技能、知识、资源、权威等的人员。 – 选取具有不同背景的人员。 – 根据需要变更小组成员。
小组角色:
–8D小组一旦建立,小组成员需要尽可能有效地工作。 –8D过程依靠每一位小组成员的努力来达到小组的目标。 –每位小组成员扮演一个角色。 –每一个角色集中在功能上而不是每一个成员,这可以帮助
●不能提出改进方案 在不知道原因的情况下,不可能找出某种 有效的改进措施。
例子:我们公司比我们主要的竞争对手在交付零件的流程上平均 多花10天以上的时间,安装一个计算机化的交付程序来加速处理 过程。
●不能给予责备 问题描述中给予责备会减少人们参与解决问题 的积极性,而且在不知道问题原因的情况下责备可能是错误的。
– 所选择的完成8D过程的小组成员没有技术知识。 – 仅有一两个人实施该过程。
成立8D团队
建立一个团队,团队成员 具备相关产品的知识,有解决 问题需要的时间和授予的权限 ,具有所要求的解决问题和实 施纠正措施的技术素质,团队 必须有一个指定的带头人;
团队成员由与问题密切相 关的技术人员或管理人员、相 关的质量工程师组成。
D0 准备8D
D0 准备8D过程(包括必要时的ERA) 根据现象评估8D过程是否需要。 如果需要,应采取紧
急反应行动(Emergency Response Action----ERA)来保护 顾客,并开始8D过程。 为什么要为8D过程作准备:
–8D的过程是很精深的。可能涉及大量的时间、人员和资 源。当然也会浪费大量的时间、人员和资源。
怎样描述问题
–问题陈述 –问题描述 问题陈述:是确定未知原因引起的问题的对象和缺陷的
简单、简明的陈述。
–怎样进行问题陈述 –识别对象和缺陷(问“什么出现了什么问题”) – “什么问题”是缺陷 – “什么出了问题”是对象 –问‘什么出了什么问题’能够帮助小组以问题 陈述所需的两个基本要素为中心(对象和缺 陷)。
A
B
C
D
Who Responsibility
Jim Sue Lynn Bill/Jim
……
时间管理
D2 描述问题
D2 描述问题 通过‘什么出现什么问题’来描述内部/外部的问题,用量
化的术语细化问题。
为什么要描述问题 : –要想成为一个有效的问题解决者,必须在采取行动前 知道尽可能多的关于问题的描述。 –D2 阶段应尽可能准确地定义问题 –在D2阶段的任何不清楚和不准确都会导致小组得到错 误的原因和采取错误的修正行动。
相关的QC工具
团队宪章
业务个案 目标陈述
机遇陈述 项目范围
项目计划
团队人选
行动计划
TASKS TASKS
ACTIVITIES ACTIVITIES
RESP.
START
DUE
RESP.
START
DUE
STATUS &ACTIONS
Gantt Chart (Pilot)
What
When
Task
Jan Feb Mar Apr May
…….
Frequency Count
Percent
相关的QC工具
Histogram of x Normal
4
Mean 1.285
StDev 0.1316
N
15
3
2
1
0
1.0
1.1
1.2
1.3
1.4
1.5
1.6
x
直方图
Pareto Chart of Defect
400
100
80 300
60
200
145
40
100
96
48
58
20
32
29
0
0
Defect
PCBA 马 达 响 外 观 投 影 虚 风 扇 响 Other
Count
145
96
48
32
29
58
Percent
35.5
23.5
11.8
7.8
7.1
14.2
Cum %
35.5
59.1
70.8
78.7
85.8
100.0
ห้องสมุดไป่ตู้排列图
Cpk=0.852
控制图
-6 4 14 24 34 44 54 64 74
8D的使用时机
– 外部客户要求使用8D报告 – 公司内部重复发生不合格的纠正措施 – 重大客户抱怨时。 8D的目的
– 通过准确完成8D过程,防止问题的再发生并改进整个制 造系统。
– 确定根本原因,成功实施纠正措施计划(CAP)
8D问题的提出
– 对于产品、过程出现重复发生不合格时,应采用8D方法做 反应。
– 在会议中重新叙述和记录小组的决定 – 使小组的决定可见 – 管理小组的文件
记录员:
– 书写和分发会议纪要 – 为小组提供管理支持 – 确保每一个小组成员都有机会做贡献 协调员:
– 集中于小组维护 – 同小组一起工作解决冲突 – 在每个G8D阶段提出建议 成员:
– 找出答案 – 执行行动 常见性错误
改写:一车间生产的泵有2%不能通过安全/耐久性试验,因此必须 报废 。
要想成为一个有效的问题 解决者,必须在采取行动 前知道尽可能多的关于问 题 的 描 述 。 在 D2 阶 段 的 任 何不清楚和不准确都会导 致小组得到错误的原因和 采取错误的纠正行动。
用可量化的术语,如与该 问题有关的人员、内容、 时间、地点、原因、方式 和程度(5W1H)等详细说 明内部/外部顾客的问题。
–判别使用8D过程是合适的。如果不合适,那么,您可能 用其它方法来解决每一个单一的问题。
紧急反应行动(ERA): 紧急反应行动是在决定是否采用8D时用来保护顾客和受 影响的各方面的任何行动。
通常由领导(对问题负责和授权解决问题 的人)决定是否执行ERA。在任何情况下 都需要评估是否需要ERA。 有时需要不止一个ERA来完全保护我们的顾客。例如,一个ERA 用来保护顾客,另一个用来保护他们免受第一个ERA带来的副作用。
– 与最终产品质量有关的问题及其纠正措施需通报特殊或重 点顾客的应采用8D方法。
顾客将通过确认8D报告来决定这些问题是否已经回答:
– 对零件的知识进行了充分论证。 – 完全确定了根本原因并聚焦于该原因。 – 问题逃出点已经被识别。 – 确定与根本原因相匹配的纠正措施。 – 纠正措施计划的验证已经被确定。 – 包括了实施纠正措施的时间计划。 – 有证据显示供方将把纠正措施纳入整个系统。
紧急反应行动(ERA)的选择和验证
–当您验证ERA时,要在行动执行前证明ERA能够保护顾客并不会产生 新的问题。
–可以在非生产产品上验证ERA,例如样件或计算机模拟计算。 紧急反应行动(ERA)的执行和确认: