塑料橡胶模具技术条件
橡胶塑料注射成型机通用技术要求及检测方法

橡胶塑料注射成型机通用技术要求及检测方法一、橡胶塑料注射成型机的基本概念及分类橡胶塑料注射成型机是一种用于生产各种橡胶、塑料制品的专用设备。
它按照工艺要求将加热后的塑料或橡胶通过高压注入模具中,形成所需的产品。
根据其结构和工艺特点,橡胶塑料注射成型机可分为液压式、电动式和混合式三种。
二、通用技术要求1. 设备选型:应根据生产工艺要求选择适当的注射成型机,考虑到产品大小、形状、材质等因素。
2. 操作人员:操作人员必须经过专业培训,掌握安全操作规程和设备使用方法,并进行定期检查维护。
3. 原材料:使用符合国家标准或行业标准的原材料,并进行充分检验,确保质量合格。
4. 模具设计:模具应根据产品要求设计制造,确保产品质量和生产效率。
5. 清洁卫生:设备周围环境应保持清洁卫生,避免灰尘和异物进入设备内部。
6. 维护保养:设备应定期进行维护保养,检查各部位的紧固件和电气元件是否正常。
三、检测方法1. 温度检测:使用温度计或红外线测温仪等设备对注射成型机的加热器、油路和模具进行温度检测,确保温度符合要求。
2. 压力检测:使用压力表或传感器等设备对液压系统进行压力检测,确保液压系统工作正常且稳定。
3. 流量检测:使用流量计等设备对液压系统的流量进行检测,确保系统流量符合要求。
4. 电气性能检测:使用万用表等设备对电气元件进行测试,确保电气性能良好。
5. 机械性能检测:通过试验模具生产出样品进行拉伸、弯曲等力学性能测试,确保产品质量符合要求。
6. 整机性能测试:将注射成型机与模具组装在一起进行整机性能测试,包括注塑速度、注塑压力、产品重量和尺寸等方面的测试。
(GBT 3672.1-2002) 橡胶制品的公差 第1部分 尺寸公差
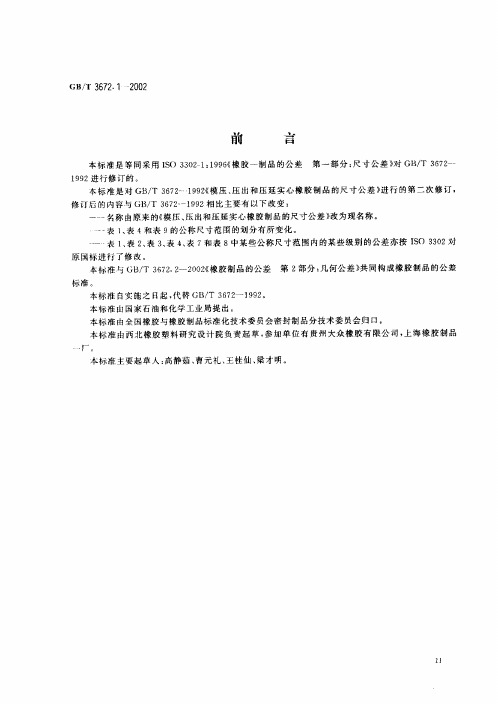
2 引用标准
下列 标 准 所包含的条文,通过在本标准中引用而构成为本标准的条文。本标准出版时,所示版本均 为有效。所有标准都会被修订,使用本标准的各方应探讨使用下列标准最新版本的可能性。
GB /T 3 21-198。 优先数和优先数系 GB /T 2 941-1991 橡胶试样环境调节和试验的标准温度、湿度及时间(eqvI SO 471:1995) GB /T 5 723-1993 硫化橡胶或热塑性橡胶 试验用试样和制品尺寸的测定
5.2 分级
本节 对 实 心模压制品的固定尺寸和合模尺寸(见 5-3)规定了四个公差级别,即: 。) M 1级 ,适用于精密模制品。这类模制品要求精密的模具,每一模具的模腔较少,胶料严密控制 等,因而成本高。为了避免测量仪器使橡胶产生变形,需要使用光学比较仪或其他类似的测量仪。这类 部件要求昂贵的控制和检验程序。 b) M 2级 ,适用于高质量模制品,其中包括 M1所要求的许多严密控制。 。) M 3级 ,适用于良好质量的模制品 d) M 4级 .适用于尺寸控制不严格的模制品。 5.3 固定尺 寸与合模尺寸 在模 III-,制 造一种橡胶产品时 所使用的胶料比充满模腔所需的要多,而这多余的胶料就溢出。这种 溢料往往阻碍模具部件完全闭合,从而影响成品的尺寸。
72小时。测量应在向买方发货之 日后或产品投人使用之前(以时间较短的为准)三个月之内完成,测量 应经环境调节后(见 GB/T 2941)在标准温度下进行。应注意保证不使产品经受有害的贮存条件(见 ISO 2230)并保证产品在测量过程中不变形。 3.2 试验仪器 3.2.1 应视情况使用下列一种或一种以上类型的仪器进行测量。 3.2.1.1 实心产品可用刻度盘测微规测量.测微规的测足对硬度等于或大于 35I RHD的橡胶应施加
毕业设计(论文)-塑料端盖注塑模具设计
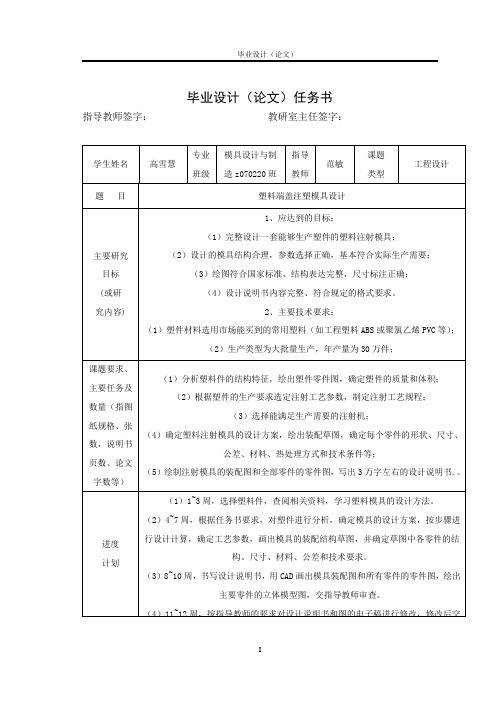
毕业设计(论文)任务书指导教师签字:教研室主任签字:学生姓名高雪慧专业班级模具设计与制造z070220班指导教师范敏课题类型工程设计题目塑料端盖注塑模具设计主要研究目标(或研究内容)1、应达到的目标:(1)完整设计一套能够生产塑件的塑料注射模具;(2)设计的模具结构合理,参数选择正确,基本符合实际生产需要;(3)绘图符合国家标准、结构表达完整,尺寸标注正确;(4)设计说明书内容完整、符合规定的格式要求。
2、主要技术要求:(1)塑件材料选用市场能买到的常用塑料(如工程塑料ABS或聚氯乙烯PVC等);(2)生产类型为大批量生产,年产量为30万件;课题要求、主要任务及数量(指图纸规格、张数,说明书页数、论文字数等)(1)分析塑料件的结构特征,绘出塑件零件图,确定塑件的质量和体积;(2)根据塑件的生产要求选定注射工艺参数,制定注射工艺规程;(3)选择能满足生产需要的注射机;(4)确定塑料注射模具的设计方案,绘出装配草图,确定每个零件的形状、尺寸、公差、材料、热处理方式和技术条件等;(5)绘制注射模具的装配图和全部零件的零件图,写出3万字左右的设计说明书.。
进度计划(1)1~3周,选择塑料件,查阅相关资料,学习塑料模具的设计方法。
(2)4~7周,根据任务书要求,对塑件进行分析,确定模具的设计方案,按步骤进行设计计算,确定工艺参数,画出模具的装配结构草图,并确定草图中各零件的结构、尺寸、材料、公差和技术要求。
(3)8~10周,书写设计说明书,用CAD画出模具装配图和所有零件的零件图,绘出主要零件的立体模型图,交指导教师审查。
(4)11~12周,按指导教师的要求对设计说明书和图的电子稿进行修改,修改后交主要参考文献(1)于保敏塑料成型工艺与模具设计 .北京:清华大学出版社2009 (2)王鹏驹塑料模具设计及制造 .北京:机械工业出版社,2005 (3)杨占尧塑料模具典型结构设计实例 .北京:华工工业出版社,2008 (4)冯爱新 .塑料模具工程师手册上海:科学技术出版社,1998指导教师签字:教研室主任签字:年月日毕业设计零件图端盖塑料模具设计摘要本课题主要是针对端盖的模具设计,通过对塑件进行工艺的分析和比较,最终设计出一副注塑模。
塑料模具的设计与成型工艺

塑料模具的设计与成型工艺摘要:塑料成形是一种以人工合成金属树脂材料为基本合成原材料,加入其他一定量化学添加剂,在一定的工作压力、温度下,制成一定形状,并在室温下长久保持形状不变的材料。
塑料是20世纪末期发展壮大起来的一类工业新型材料,包装材料工业、日常用品制造工业,机械工业,医疗器械等工业领域。
医疗器械等领域。
塑料模具产品设计的基本技术要求之一是企业能不断生产研制出能在尺寸,精度,外观及热物理及流体力学性能等各方面条件均能充分满足实际使用性能要求的优质材料塑件。
在进行模具生产使用时,应该要力求模具生产过程效率高,自动化管理程度高,操作方便,寿命长;在应用模具结构制造工艺方面,要求模具结构设计合理,制造容易,成本低。
引言:20世纪70年代以来,石油危机持续爆发虽然使得目前我国大型塑料制品加工制造产业的主要产品原料价格上涨,其宏观经济发展趋势仍然受到很多较大一定程度的宏观经济因素抑制和被经济抑制。
所以,改善塑料的性能、推广和使用先进的模具设计制造技术,研究塑料快速成型技术显得尤为重要。
塑料模具是使塑件成型的主要工具,它可使塑件获得一定的结构形状及所需性能。
其发展受到很大程度的抑制抑制。
所以,改善塑料的性能、推广和使用先进的模具设计制造技术,研究塑料快速成型技术显得尤为重要。
塑料模具是使塑件成型的主要工具,它可使塑件获得一定的结构形状及所需性能。
用特殊模具工艺生产制造出来的的新型塑件产品具有高工艺复杂程度,高质量一致性,高操作精度、高生产率以及低材料消耗率等几大特点。
一、塑料模具简介塑料产品是用各种零件作为材料后再进行加工再成型而得以获得的一种产品。
而腔体模具就是一种利用其本身特定的腔体密闭性和腔体部件去加工成型,从而可以做成一种具有一定整体形状和大小尺寸的大型塑料金属制件的一种工具。
1、用新型机械塑料模具自动加工塑料生产工艺制造加工出来的的新型柔性塑件塑料制品。
它具有高度易操作和低精度、高性能和低一致性、高生产率和低使用材料资源消耗率等几个新的显著特点。
塑胶零、部件加工通用技术要求和测试方法

塑胶零、部件加工通用技术要求和测试方法一、透明塑胶件:技术要求:1.粗糙度Ra0.4考核制品光面的模具面;2.粗糙度Ra25考核制品毛面的模具面;3.制品要求成型完整、边缘无披锋,表面不得有磕碰、刮伤、杂点、夹水纹、缩水、变形及裂痕等外观缺陷;4.对于多模穴制件需在内表面的非配合面上增加模号和材料的回收标志;对于分模线及水口、顶针的位置,均需在开模前经相关结构设计人员确认后才能正式开模;5.未注圆角为R0.2~0.3,未注脱模斜度均按注塑件成型要求选取,常取1°或较小值(一般情况下,制件内表面脱模斜度要大于外表面的脱模斜度);6.图中所有尺寸按GB∕T 14486-2008《塑料模塑制件尺寸公差》或SJ/T 10628-1995《塑胶制件尺寸公差》标准中所规定的要求选取,各尺寸均为制品注塑成型后应达到的尺寸(未考虑注塑成型时缩水的影响);7.图中线性尺寸和角度尺寸的未注公差,分别按GB/T 1804-2000《一般公差未注公差的线性尺寸和角度尺寸的公差》标准中m 级和 f 级选取;未注形状和位置公差,均按GB∕T 1184-1996《形状和位置公差未注公差值》标准中H级选取;8.带*标志的尺寸为影响装配及性能的重要尺寸,加工、检验人员要特别注意此类尺寸控制;9.成形前胶料应进行预热干燥,生产和检验人员要注意成形后制件表面质量,制件不得有扭曲、变形等。
二、非透明塑胶件:技术要求:1.粗糙度Ra0.4 考核制品光面的模具面;2.粗糙度Ra25考核制品毛面的模具面;3.制品要求成型完整、边缘无披锋,表面不得有磕碰、刮伤、杂点、夹水纹、缩水、变形及裂痕等缺陷;4.对于多模穴制件在其内表面的非配合面上增加模穴号和材料回收标志;对于分模线及水口、顶针的位置,均需模具供应商在开模前把模具资料经相关开发设计人员确认后才能正式开模;5.未注圆角为R0.2~0.3,未注脱模斜度均按注塑件成型要求,常取1°或较小值(一般情况下,制件内表面脱模斜度要大于外表面的脱模斜度);6.图中所有尺寸按GB∕T 14486-2008《塑料模塑制件尺寸公差》或SJ/T 10628-1995《塑胶制件尺寸公差》标准中所规定的要求选取,各尺寸均为制品注塑成型后应达到的尺寸(未考虑注塑成型时缩水的影响);7.带*标志的尺寸为影响装配及性能的重要尺寸,生产及检验人员要特别注意此类尺寸;8.图中线性尺寸和角度尺寸的未注公差,分别按GB/T 1804-2000《一般公差未注公差的线性尺寸和角度尺寸的公差》标准中m 级和f 级选取;未注形状和位置公差,均按GB∕T 1184-1996《形状和位置公差未注公差值》标准中H级选取;9.表面处理:外表面喷漆(喷油),如颜色为银灰色,喷涂层厚度:30~60um(内表面喷漆:20~30um;外表面喷漆:30~45um;打底漆:15±5um;喷面漆:25±5um),其表面光亮,不允许有颗粒、露底、起皱、多喷、异色等外观缺陷;喷层附着力要求能通过百格测试,其附着力要求≥4B,即用3M 600#胶纸粘贴,在同一位置进行3次(或2次)相同的试验,该镀层脱落总面积≤5%)为合格;10.表面电镀:镀铬(Cr3+),镀层厚度:20~50um(先以镀铜、镍做底,表面镀铬,即Cu15Ni20Cr0.4),外观光亮,表面不允许有气泡、凹坑、漏镀、划伤、黑点、锈斑及镀层脱落等缺陷,镀层附着力要求做百格测试,用胶带在同一位置进行3次(或2次)相同的试验,附着力要求≥4B,该镀层总脱落总面积≤5﹪为合格。
(塑料橡胶材料)常用塑料注塑工艺参数
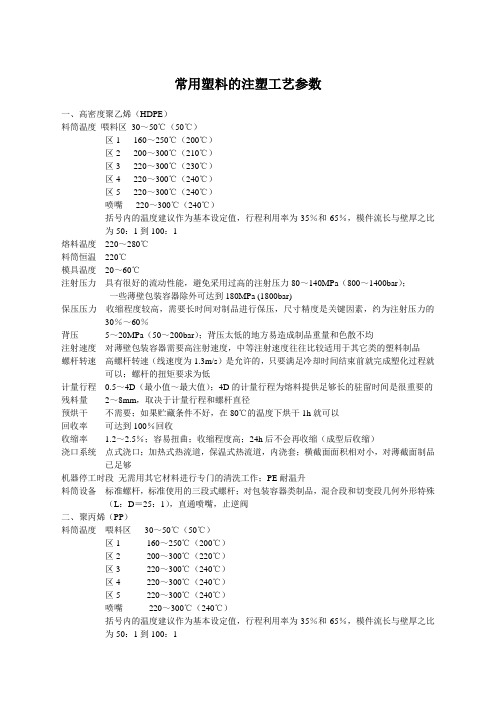
常用塑料的注塑工艺参数一、高密度聚乙烯(HDPE)料筒温度喂料区30~50℃(50℃)区1 160~250℃(200℃)区2 200~300℃(210℃)区3 220~300℃(230℃)区4 220~300℃(240℃)区5 220~300℃(240℃)喷嘴220~300℃(240℃)括号内的温度建议作为基本设定值,行程利用率为35%和65%,模件流长与壁厚之比为50:1到100:1熔料温度220~280℃料筒恒温220℃模具温度20~60℃注射压力具有很好的流动性能,避免采用过高的注射压力80~140MPa(800~1400bar);一些薄壁包装容器除外可达到180MPa (1800bar)保压压力收缩程度较高,需要长时间对制品进行保压,尺寸精度是关键因素,约为注射压力的30%~60%背压5~20MPa(50~200bar);背压太低的地方易造成制品重量和色散不均注射速度对薄壁包装容器需要高注射速度,中等注射速度往往比较适用于其它类的塑料制品螺杆转速高螺杆转速(线速度为1.3m/s)是允许的,只要满足冷却时间结束前就完成塑化过程就可以;螺杆的扭矩要求为低计量行程0.5~4D(最小值~最大值);4D的计量行程为熔料提供足够长的驻留时间是很重要的残料量2~8mm,取决于计量行程和螺杆直径预烘干不需要;如果贮藏条件不好,在80℃的温度下烘干1h就可以回收率可达到100%回收收缩率 1.2~2.5%;容易扭曲;收缩程度高;24h后不会再收缩(成型后收缩)浇口系统点式浇口;加热式热流道,保温式热流道,内浇套;横截面面积相对小,对薄截面制品已足够机器停工时段无需用其它材料进行专门的清洗工作;PE耐温升料筒设备标准螺杆,标准使用的三段式螺杆;对包装容器类制品,混合段和切变段几何外形特殊(L:D=25:1),直通喷嘴,止逆阀二、聚丙烯(PP)料筒温度喂料区30~50℃(50℃)区1 160~250℃(200℃)区2 200~300℃(220℃)区3 220~300℃(240℃)区4 220~300℃(240℃)区5 220~300℃(240℃)喷嘴220~300℃(240℃)括号内的温度建议作为基本设定值,行程利用率为35%和65%,模件流长与壁厚之比为50:1到100:1熔料温度220~280℃料筒恒温220℃模具温度20~70℃注射压力具有很好的流动性能,避免采用过高的注射压力80~140MPa(800~1400bar);一些薄壁包装容器除外可达到180MPa (1800bar)保压压力避免制品产生缩壁,需要很长时间对制品进行保压(约为循环时间的30%);约为注射压力的30%~60%背压5~20MPa(50~200bar)注射速度对薄壁包装容器需要高的注射速度(带蓄能器);中等注射速度往往比较适用于其它类的塑料制品螺杆转速高螺杆转速(线速度为1.3m/s)是允许的,只要满足冷却时间结束前完成塑化过程就可以计量行程0.5~4D(最小值~最大值);4D的计量行程为熔料提供足够长的驻留时间是很重要的残料量2~8mm,取决于计量行程和螺杆转速预烘干不需要;如果贮藏条件不好,在80℃的温度下烘干1h就可以回收率可达到100%回收收缩率 1.2~2.5%;收缩程度高;24h后不会再收缩(成型后收缩)浇口系统点式浇口或多点浇口;加热式热流道,保温式热流道,内浇套;浇口位置在制品最厚点,否则易发生大的缩水机器停工时段无需用其它材料进行专门的清洗工作;PP耐温升料筒设备标准螺杆,标准使用的三段式螺杆;对包装容器类制品,混合段和切变段几何外形特殊(L:D=25:1),直通喷嘴,止逆阀三、聚苯乙烯(PS)料筒温度喂料区30~50℃(50℃)区1 160~250℃(200℃)区2 200~300℃(210℃)区3 220~300℃(230℃)区4 220~300℃(230℃)区5 220~300℃(230℃)喷嘴220~300℃(230℃)括号内的温度建议作为基本设定值,行程利用率为35%和65%,模件流长与壁厚之比为50:1到100:1熔料温度220~280℃料筒恒温220℃模具温度15~50℃注射压力具有很好的流动性能,避免采用过高的注射压力80~140MPa(800~1400bar)保压压力注射压力的30%~60%;相对较短的保压时间背压5~10MPa(50~100bar);在背压太低的地方,熔料中易产生气泡(制品中有灰黑纹路)注射速度普遍较快,多级注射以制品形状为依据;对薄壁的包装容器应该尽可能快,必要时使用蓄能器螺杆转速高螺杆转速(最大线速度为1.3m/s)是允许的;但为取得好的效果,塑化过程应该缓慢同冷却时间一样计量行程0.5~4D(最小值~最大值);4D的计量行程为熔料提供足够长的驻留时间是很重要的残料量2~8mm,取决于计量行程和螺杆转速预烘干不需要;如果贮藏条件不好,在80℃的温度下烘干1h就可以回收率可达到100%回收收缩率0.3%~0.6%浇口系统点式浇口;加热式热流道,保温式热流道,内浇套;相对较小的横截面为足够机器停工时段无需用其它材料进行专门的清洗工作;PS耐温升料筒设备标准螺杆,直通喷嘴,止逆阀四、聚氯乙烯-未增塑(PVC-U)料筒温度喂料区30~50℃(50℃)区1 140~160℃(150℃)区2 165~180℃(170℃)区3 180~210℃(190℃)区4 180~210℃(200℃)区5 180~210℃(200℃)喷嘴180~210℃(200℃)括号内的温度建议作为基本设定值,行程利用率为35%和65%,模件流长与壁厚之比为50:1到100:1熔料温度210~220℃料筒恒温120℃模具温度30~60℃注射压力80~160MPa(800~1600bar)保压压力不可设置太高,注射压力的40~60%,以模件和浇口为依据背压鉴于它的热敏感性,正确设置背压是很关键的;螺杆转动摩擦产生的热量(关闭热量输入控制)比从料筒加热圈产生的热量更好;背压不超过30MPa(300bar)注射速度不要设置太高并小心物料产生剪切效应;制品易产生变性或锐边的地方,应绝对需要多级注射速度螺杆转速使用允许的最低设置,最大速度折合线速度为0.2m/s;如果必要,延迟塑化以确保在冷却时间长的情况下,计量操作在低螺杆转速时能在冷却时间结束前完成;需要高扭矩并保持均匀计量行程 1.0~3.5D残料量应较小:1~5mm,取决于计量行程和螺杆直径;螺杆在安装料筒时确保最小配合预烘干如果贮藏条件不好,在70℃的温度下烘干1h就可回收率允许在材料没有热分解的状态下再生利用收缩率0.5%~0.7%浇口系统直浇口,片式浇口或圆片式浇口较好,对小的制品也可采用点式浇口;浇口朝着制品的方向应有圆弧过渡机器停工时段关闭加热,无背压塑化,允许熔料驻流2~3mm,然后像挤出机那样缓慢操作机器;重复操作直到料筒温度降到160℃,然后挤出余料,清空料筒料筒设备硬质PVC螺杆;有些需要料筒有加热圈和冷空气吹气装置;螺杆头有螺槽或没有螺槽,直通喷嘴五、增塑聚氯乙烯(P-PVC)料筒温度喂料区30~50℃(50℃)区1 140~160℃(150℃)区2 150~180℃(165℃)区3 160~220℃(180℃)区4 160~220℃(190℃)区5 160~220℃(190℃)喷嘴160~220℃(200℃)括号内的温度建议作为基本设定值,行程利用率为35%和65%,模件流长与壁厚之比为50:1到100:1熔料温度200~220℃料筒恒温120℃模具温度30~50℃注射压力80~120MPa(800~1200bar)保压压力注射压力的30%~60%背压5~10MPa(50~100bar)注射速度为了获得好的表面质量,注射不应该太快(如果必要,采用多级注射)螺杆转速设置中等螺杆转速,最大折合线速度为0.5m/s计量行程 1.0~3.5D残料量2~6mm,取决于计量行程和螺杆直径预烘干不需要;只有在贮藏条件不好,在70℃的温度下烘干1h就可回收率允许在材料没有热分解的状态下再生利用收缩率1%~2.5%浇口系统对小的制品可采用点式浇口;浇口朝着制品的方向应有圆弧过渡机器停工时段关闭加热,无背压塑化,操作几次挤出循环料筒设备标准螺杆,止逆环,直通喷嘴六、尼龙6(PA6)料筒温度喂料区60~90℃(70℃)区1 230~240℃(240℃)区2 230~240℃(240℃)区3 240~250℃(250℃)区4 240~250℃(250℃)区5 240~250℃(250℃)喷嘴230~240℃(250℃)括号内的温度建议作为基本设定值,行程利用率为35%和65%,模件流长与壁厚之比为50:1到100:1喂料区和区1的温度是直接影响喂料效率,提高这些温度可使喂料更平均熔料温度240~250℃料筒恒温220℃模具温度60~100℃注射压力100~160MPa(1000~1600bar),如果是加工薄截面长流道制品(如电线扎带),则需要达到180MPa(1800bar)保压压力注射压力的50%;由于材料凝结相对较快,短的保压时间已足够。
tpr注塑工艺技术
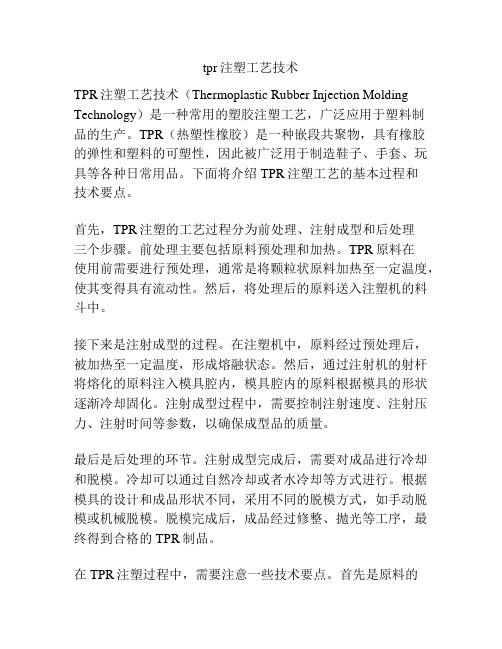
tpr注塑工艺技术TPR注塑工艺技术(Thermoplastic Rubber Injection Molding Technology)是一种常用的塑胶注塑工艺,广泛应用于塑料制品的生产。
TPR(热塑性橡胶)是一种嵌段共聚物,具有橡胶的弹性和塑料的可塑性,因此被广泛用于制造鞋子、手套、玩具等各种日常用品。
下面将介绍TPR注塑工艺的基本过程和技术要点。
首先,TPR注塑的工艺过程分为前处理、注射成型和后处理三个步骤。
前处理主要包括原料预处理和加热。
TPR原料在使用前需要进行预处理,通常是将颗粒状原料加热至一定温度,使其变得具有流动性。
然后,将处理后的原料送入注塑机的料斗中。
接下来是注射成型的过程。
在注塑机中,原料经过预处理后,被加热至一定温度,形成熔融状态。
然后,通过注射机的射杆将熔化的原料注入模具腔内,模具腔内的原料根据模具的形状逐渐冷却固化。
注射成型过程中,需要控制注射速度、注射压力、注射时间等参数,以确保成型品的质量。
最后是后处理的环节。
注射成型完成后,需要对成品进行冷却和脱模。
冷却可以通过自然冷却或者水冷却等方式进行。
根据模具的设计和成品形状不同,采用不同的脱模方式,如手动脱模或机械脱模。
脱模完成后,成品经过修整、抛光等工序,最终得到合格的TPR制品。
在TPR注塑过程中,需要注意一些技术要点。
首先是原料的选择和配方的确定。
根据成品的用途和要求,选择合适的TPR原料,并确定配方。
在注塑过程中,要保持原料的稳定性,避免其分解或变质。
其次是模具的设计和制造。
模具的设计需要考虑到成品的尺寸、形状等因素,合理设置模具腔、冷却系统等,并确保模具的精度和质量。
此外,注塑机的选择和调试也对成品的质量有重要影响。
注塑机需要具备稳定的压力、温度和流量控制系统,以确保稳定性和一致性的生产过程。
总结起来,TPR注塑工艺技术是一种常用的塑胶注塑工艺,通过前处理、注射成型和后处理三个步骤,可以生产出质量优良的TPR制品。
注塑类内外饰模具通用技术规范

3.26.2 其余零件按照双方协商制定,并满足模具寿命和使用要求。 3.27 注塑成型模具表面有皮纹时,皮纹样式必需符合长安公司提供的皮纹样板 (CTF 样板)及皮纹深度、范围要求。
第 7 页 共 23 页
3.28 内饰件(外饰件)有皮纹要求时,为了具有同一风格装饰效果纹理,模具 型腔的选材必须保持一致。 3.29 模具零件品牌及材料要求。 严禁私自变更和长安达成一致的模具制造过程中所选用的钢材、热流道、关 重标准件等,(如有异议,请提交申请,经长安同意后方可使用)。 3.29.1 模具供应商必须提供相关材料必须证明所备材料符合本要求。若对模具 材料选择若有异议,需书面提出建议,双方商议确认最终材料要求。 3.29.2 模具主要部件材料明细参考下表:
第 2 页 共 23 页
目
录
1.范围 2.规范性引用文件 3.基本要求 4.流道系统 5.液压机构、抽芯及复位机构 6.冷却系统 7.滑块、斜顶机构 8.导向、锁紧及镶拼 9.顶出系统 10.模具安装、起吊 11.品质要求 12.检查 13.项目管理 14.设计变更 15.提交资料 16.其他要求
3.30 在成型部位中,产品和模具均要做断差,采取天包地方式,中小型模具 0.05mm, 大型模具 0.1mm,保险杠等 0.15mm,对于影响内外饰精致工艺 的部位须另单独提出。 4、流道系统 4.1 热流道要求: 4.1.1 供应商模具数据流道系统信息须符合长安汽车股份有限公司 《模流分析报 告》中关于模具流道信息的要求,其主要包含:流道的分类(模具中采用热 流道还是冷流道),流道的截面形状(圆形、梯形、椭圆形等)、流道的尺 寸大小、浇口的形式(点浇口、侧浇口、潜伏式浇口等)、浇口的尺寸大小、 浇口的位置以及浇口的数量等。 4.1.2 浇口套与注塑机喷嘴的配合要求良好,无漏胶。 4.1.3 升温时间要求:热流道 200℃/30min;热喷嘴 200℃/20min;并且能够有 热电偶等加热控制装置对热流道进行精确控制。 4.1.4 热流道总成要耐受在 100-300℃的工作温度所产生的热变形以及需能耐
- 1、下载文档前请自行甄别文档内容的完整性,平台不提供额外的编辑、内容补充、找答案等附加服务。
- 2、"仅部分预览"的文档,不可在线预览部分如存在完整性等问题,可反馈申请退款(可完整预览的文档不适用该条件!)。
- 3、如文档侵犯您的权益,请联系客服反馈,我们会尽快为您处理(人工客服工作时间:9:00-18:30)。
塑料、橡胶模具技术条件(HB2198-89)1 主题内容与适用范围本标准规定了塑料、橡胶模具的零件加工和装配的技术要求以及模具的材料及材料代用、验收、包装、运输和保管的基本规定。
本标准适用于塑料、橡胶模具的设计、制造及验收。
2 引用标准GB4170 塑料注射模具零件技术条件GB8846 塑料成型模具术语及定义GB1801 公差与配合尺寸至500mm孔、轴公差带与配合GB1804 公差与配合未注公差尺寸的极限偏差GB1184 形状和位置公差未注公差的规定GB1239 普通圆柱螺旋弹簧GB196 普通螺纹基本尺寸HB0—84 热固性塑料模塑制品技术条件HB5888 航空辅机产品用字体和符号3 技术要求3.1 零件的加工要求3.1.1 要求镀铬的成型表面,应进行抛光、镀铬、抛光。
铬层厚度为0.005~0.01mm,铬层应均匀,不允许有积铬、腐蚀及剥落等缺陷。
3.1.2模具成型零件之间的配合,其同一配合部分各处应保持一致,如图A-1左图R与A、B一致;在未注公差处按已注明公差的配合要求,如图A-1右图R与A、B一致。
3.1.3 塑料及硬橡胶模具,成型表面未注明脱模斜度时,不允许有影响脱模的反斜度及其它缺陷。
3.1.4 模具分型面及组合件的结合面应很好贴合,局部间隙不大于0.02mm 。
3.1.5 模具成型表面的内外锐角、尖边,图样上未注明圆角时,允许有半径不大于0.3 mm 的圆角(分型面及结合面除外)。
当不允许有圆角时,应在图样上注明。
3.1.6 成型表面及构成成型表面的角度偏差,图样未注明时,其极限偏差按表A-1规定。
属配合角度时,需同时满足3.1.2条或3.1.4条规定(图A-2)。
表A-1 角度短边长度L(mm ) ≤10 >10~50 >50~120 >120~400 >400 角度值 ±45′ ±30′ ±15′ ±7′ ±5′ 极限 偏差线性值 (mm )±0.013L±0.013L±0.013L±0.013L±0.013L3.1.7 成型表面非转接半径R 的偏差,图样未注明时,其极限偏差按表A-2规定(图A-3、 图A-4)。
属配合表面时(图A-4),需同时满足3.1.2条或3.1.4条规定。
表A-2 (mm) 非转接 半径R ≤6 >6~18 >18~50 >50~120 >120~250 >250~500 >500~800 >800 凹R 0 -0.2 0 -0.3 0 -0.4 0 -0.6 0 -0.8 0 -1.1 0 -1.4 0 -1.7 极限偏差凸R+0.2 0+0.3 0+0.4 0+0.6 0+0.8 0+1.1 0+1.4 0+1.7 03.1.8 成型表面转接半径r 及倒角C 的偏差,图样未注明时,其极限偏差按表A-3规定(图 A-5、图A-6)。
属配合表面时(图A-6),需同时满足3.1.2条规定。
表A-3转接半径如r或倒角C(mm)0.2 0.3~0.5 >0.5~1 >1~3 >3~6 >6~30 >30~120 r或C 极限偏差(mm)±0.013±0.013±0.013±0.013±0.013±0.013±0.013 45°角的极限偏差±5°±2°30′3.1.9 成型表面的汉字、数字、字母、符号的规格尺寸应符合HB5888的规定并排列整齐均匀。
所注位置尺寸,图样未注明公差时,其极限偏差按GB1084的Js15(Js15)。
3.1.10 螺纹型芯、螺纹型环的螺纹首、尾的起止点(P/3处)按图A-7的规定,过渡长度按表A-4规定。
表A-4 (mm) 螺纹直径螺距PD(d) ≤1 >1~2 >2≤10 ~2 ~3—>10~20 ~3 ~4 ~6>20~30 ~4 ~6 ~8>30~48 ~5 ~8 ~10>48 ~6 ~10 ~103.1.11垂直分型面模具的锥面(或斜面)及滑块、锁紧楔的斜面应进行配磨,并进行着色检验,其接触面达80%以上,并分布均匀。
3.1.12图样中未注明公差的一般尺寸(成型零件及结构零件的非配合尺寸)其极限偏差按GB1804,其孔按H13、轴按h13, 长度按Js14。
3.1.13图样中螺纹的基本尺寸按GB196;偏差按GB197,内螺纹按7H,外螺纹按6h 。
3.1.14斜拉杆安装孔的角度偏差,图样未注明时,其偏差按表A-1规定。
滑块上的斜孔与其配做。
3.1.15模具所用圆柱形螺旋弹簧应符合GB1239YI型的技术要求。
其制造偏差按GB1239的2级精度。
同一用途的同一规格弹簧,两端磨平时要求高度一致,允许偏差±0.5mm。
3.1.16模具中各承压板(模板)的两承压面的平行度公差按GB1184附录一的5级。
3.1.17导柱、导套孔对模板平面(分型面)的垂直度公差按GB1184附录一的4级。
导柱、导套之间的配合按H7/f7。
3.1.18模板上供开模用的孔、槽及卸模板上所属的相应各孔的位置度公差及孔组位置度公差不大于Ф0.5Zmm;或相应各孔配做(图A-8)。
3.1.19模具中安装螺钉(螺栓)之螺纹孔及其通孔的位置度公差不大于ФZmm;或相应各孔配做(图A-9)。
3.1.20 固定式压模及注射模所用垫块和支撑件,与模板接触之端面均应分别在同一平面内,其支撑件端面应高出垫块端面0.03~0.05mm,并分别对A面的平行度公差t按GB1184附录一的5级(图A-10)。
3.1.21 导柱(直导柱、台肩导柱)其配合部位的大径与小径的同轴度公差t按GB1184附录一的5级(图A-11)。
3.1.22导套(直导套、带头导套)外圆与内孔的同轴度公差t按GB1184附录一的5级(图A-12)。
3.1.23主流道衬套的中心锥孔应研磨抛光,不得有影响脱浇口的各种缺陷。
3.1.24图样中未注明的非工作锐角、尖边均需倒钝。
3.2装配要求3.2.1顶出制品的推杆的端面与所在的相应型面保持齐平,允许推杆端面高出型面不大于0.1mm(图A-13)。
3.2.2注射模的复位杆,其端面应与模具分型面齐平,允许低于分型面不大于0.03 mm(图A-14)。
3.2.3多型腔模具的相同镶件及凸模、凹模的承压面装配后应在同一平面内,并对A面的平行度公差不大于0.02mm(图A-15)。
3.2.4 型芯、凸模、镶件等,其尾部高度尺寸h未注明公差时,其端面应在装配后与其相配的零件齐平(图A-16)。
3.2.5 制品同一表面的成型腔分布在上、下模(或动、定模)或两半模时,装配后沿分型面的错边不大于0.05mm,并其组合尺寸不超过型腔允许的极限尺寸(图A-17)。
3.2.6凸模与凹模(或与模套、加料腔)装配后的配合间隙,应保持周围均匀。
3.2.7半溢式压缩模的凸模工作端面与凹模承压面之间;模具中上、下型芯之间;上、下型芯与分型面之间等要求贴合的表面,允许有不大于0.03mm的间隙(图A-18)。
3.2.8需保证同轴的两个以上零件,其同轴度(或位置度)必须保证装配要求,使各配合零件能顺利装卸,活动自如(图A-19)。
3.2.9模具导向件的导向部分,装配后保证滑动灵活,无卡滞现象。
3.2.10卸模架的顶杆铆接后修正,不允许松动。
工作端面应保持齐平,并对A面的平行度公差不大于0.1mm.。
顶杆铆接后的垂直度公差不大于Ф0.5Zmm(图A-20)。
3.2.11移动式压模中顶出制品的顶杆与顶杆板铆接或装配后,工作端面应保持齐平,并对A面的平行度公差不大于0.05mm(图A-21);或端面尺寸偏差为±0.05mm(图A-22)。
铆接处铆接后修平,不允许松动。
铆接或装配后的位置度公差不大于Ф1.3Zmm(图A-21、A-22)。
3.2.12模具中供两次分型用的拉杆、拉板装配后,各工作面应在同一平面内,允许其极限偏差为±0.1mm(图A-23)。
3.2.13模具装配后,两安装平面应保持平行,其平行度公差按GB1184附录一的6级。
3.3终合要求3.3.1模具、模架及其零件的工作表面,不应有碰伤、凹痕、裂纹、毛刺、锈蚀等缺陷。
3.3.2经热处理后的零件,硬度应均匀,不允许有脱碳、软点、氧化斑点及裂纹等缺陷。
热处理后应清除氧化皮、脏物和油污等。
3.3.3配通用模架用模具,装配后两侧面应进行同时磨削加工,以保证模具能顺利装入模架(图A-24)。
3.3.4多型腔模具,在适当位置(包括制品的非装饰、非配合表面处)用电笔或其他方法依次标记出顺序号(图A-25)。
3.3.5模具的冷却水通道应保证畅通。
其堵头、管接头及密封处,在使用时不应有渗漏现象。
3.3.6有电加热的模具,绝缘处及加热元件与模具之间用兆欧表进行检查,其交流绝缘电阻应等于无穷大。
4材料及材料代用4.1模具所用材料应与图样规定材料相符,并应符合国家标准或有关标准的规定。
4.2模具材料允许代用,代用材料的机械性能不得低于规定材料的使用要求,并做好代料记录。
4.3在主要零件的非工作面上打上该零件所用材料的牌号及热处理硬度。
5验收规则5.1模具按本技术条件和图样进行检查和尺寸检验,并将成型尺寸作详细记录。
5.2试模合格后的模具应连续生产50~100模零件作为质量稳定性检查或根据用户的要求进行质量稳定性检查。
5.3模具经检验或试模合格后,应清除脏物并涂防锈剂。
运输、、保管包装、、运输6包装6.1模具应根据运输要求进行包装,包装形式和方法由生产厂自行决定。
6.2模具在保管、搬运中应防止碰伤、受潮、锈蚀。
7其它本技术条件包括之内容,在设计图样中可不另注明。
凡有特殊要求,需在图样中注明,不受本技术条件限制。
如有本技术条件以外的技术要求,由供需双方协商确定。