经典8D案例
8D案例分析

8D案例分析概述:8D(Eight Disciplines)是一种解决问题的方法,特别适用于复杂问题的追踪和解决。
本文将通过一个实际案例,以分析8D方法的应用过程,帮助读者更好地理解和掌握此方法。
案例背景:某汽车制造公司生产线上出现了连续质量问题,导致产品退货率上升。
公司决定采用8D方法,解决这一问题,并提高生产效率。
D1 - 组建团队:针对该质量问题,公司领导决定成立一个8D团队,并指派一个质量经理担任团队领导。
团队成员包括制造经理、工程师、产品检验员和相关质量控制人员。
D2 - 描述问题:团队首先对问题进行描述,确切指出了产品的退货率上升,以及退货产品的基本特征和数量。
通过与客户的沟通,团队了解到问题主要发生在某一特定型号的发动机。
D3 - 短期解决方案:为了尽快应对问题,团队决定采取短期措施。
他们制定了一项临时方案,主要包括对退货产品进行严格的检查和分类,以及加强现场员工的培训和操作规范。
D4 - 找出根本原因:8D团队利用质量工具,如鱼骨图、5W1H法等,对问题进行深入分析。
最终确定了问题的根本原因是发动机组装工序中存在漏装关键零件的情况。
D5 - 采取纠正措施:确定了根本原因后,团队开始制定纠正措施。
首先,他们与供应商反馈了质量问题,并要求供应商进行改进。
同时,他们还设计了更加严格的工装夹具来确保关键零件的正确安装。
D6 - 验证效果:团队对纠正措施进行实施,并进行效果验证。
经过一段时间的生产检查和产品退货率的跟踪,结果显示退货率明显下降。
D7 - 预防措施:为了预防问题再次发生,团队进一步分析了可能导致问题的其他因素,并制定了一系列预防措施。
这些措施包括制定详细的工艺文件、提供员工培训以及建立质量检测站点等。
D8 - 确认效果:团队定期进行检查和评估,以确认纠正措施的长期效果。
通过追踪产品退货率和质量检查数据,团队发现问题已经完全解决,并且生产线的效率也有所提高。
总结:通过8D方法的应用,该汽车制造公司成功解决了连续质量问题,并取得了显著改善。
现实中的8D改善报告案例2024

引言概述:在现实生活中,8D改善报告是一种常用的问题解决方法。
它通过严谨的分析、合理的行动计划和持续的改善措施,帮助组织快速解决问题,并避免类似问题再次发生。
本文将通过介绍具体的案例,详细阐述8D改善报告的流程以及其在实际中的应用。
正文内容:1. 案例1:产品质量问题1.1 问题描述:某企业生产的某类产品由于设计问题导致一定比例的产品存在质量问题,客户投诉率较高。
1.2 数据收集和分析:收集了客户投诉数据、产品生产记录等相关数据,并进行了充分的数据分析,明确了问题的具体范围和影响。
1.3 原因分析:通过系统的分析方法,确定了产品设计中存在的缺陷以及相关工艺流程的不符合。
1.4 对策制定:制定了具体的对策方案,包括设计修正、工艺优化和检验加强等,以解决产品质量问题。
1.5 实施与效果评估:在实施对策方案的过程中,不断跟踪效果,并对改善效果进行评估,确保问题得到彻底解决和改善。
2. 案例2:供应链问题2.1 问题描述:某企业的供应链管理存在一系列问题,包括供货延迟、物料缺失等,严重影响了生产计划的执行。
2.2 数据收集和分析:通过对供应链各环节的数据收集和分析,确定了问题的具体表现形式和原因。
2.3 原因分析:通过对供应商管理、物料采购等流程进行分析,明确了问题的根本原因,包括供应商能力不足、交流沟通不畅等。
2.4 对策制定:制定了改善供应链问题的具体对策,包括供应商评估优化、加强沟通协作等。
2.5 实施与效果评估:通过实施对策方案,及时解决了供应链问题,并跟踪评估改善效果,确保问题得到全面解决。
3. 案例3:客户投诉处理问题3.1 问题描述:某企业在客户投诉处理方面存在问题,客户反映的问题无法及时得到解决,导致客户满意度下降。
3.2 数据收集和分析:收集了客户投诉数据和处理记录,通过对数据的分析,明确了问题的性质和频率。
3.3 原因分析:通过对投诉处理流程和人员培训情况的分析,找出了导致投诉处理问题的原因,包括流程不规范、人员技能欠缺等。
经典8D案例

某【2 】某公司TEL: FAX:a. 系統面;b. 防火牆掉效;1. 為何會生產出不良?Why 1:冲压模具偏移.冲头磨损.间隙太大导致折弯角度偏移上限.尺寸超差.1.折弯冲头磨损.间隙太大(如下图)Why 2:转换型号时模具相接不到位导致冲压同时出来的两个产品,有一个未倒角.1.模具相接不到位(如下图)2.未倒角(如下图)2. 為何未檢出不良?未磨练出不良主如果:我司磨练员掉职責任部門/人: 品德部完成時間:2011-3-19DISCIPLINE 5 IMPLEMENT PERMANENT CORRECTIVE ACTIONS (長期對策) EFFECTIVE DATE:2011-3-19 1. 若何生產出良品?Why 1:调剂机械.修复模具.責任部門/人: 工程部/李完成時間: 2011-3-21Why 2:转换型号时磨练员需做首件确认,磨练OK可进入量产,磨练NG通知工程部调剂模具.責任部門/人:品德部/吴完成時間: 2011-3-21Why 3:进程巡检发明平常需隔离标示产品,不得流入仓库,再通知功课员调剂机械.責任部門/人:临盆部/刘完成時間: 2011-3-21Why 4:进程巡检.最终终检需加严抽检,如发明不良不能流入仓库.責任部門/人: 品德部/吴完成時間: 2011-3-222. 若何檢出不良?制程首件确认.巡检,进程终检和出货磨练抽检如发明与磨练标准不符需隔离标示.責任部門/人: 品德部/吴完成時間:2011-3-22DISCIPLINE 6 VERIFY EFFECTIVENESS OF ACTIONS (后果確認) EFFECTIVE DATE:2011-3-21A.库存60k从新检讨发明有未倒角不良现象,现已隔离遴选处理,临盆部负责履行.1.隔离处理示图:B.工程部正在调试机械.修复模具确认后果OK.A.改良前:B.改良后:改良后随机抽样测试:90°±2°: 91.26.90.08.90.83.90.78.90.13.90.81.90.64.89.23.91.06.89.56平均值:90.43°10.16±0.12:10.12.10.24.10.08.10.18.10.20.10.15.10.16.10.21.10.18.10.11平均值:10.163DISCIPLINE 7 PREVENT RECURRENCE (預防再發) EFFECTIVE DATE: 2011-3-21QC-06-029-B。
8D报告案例分析
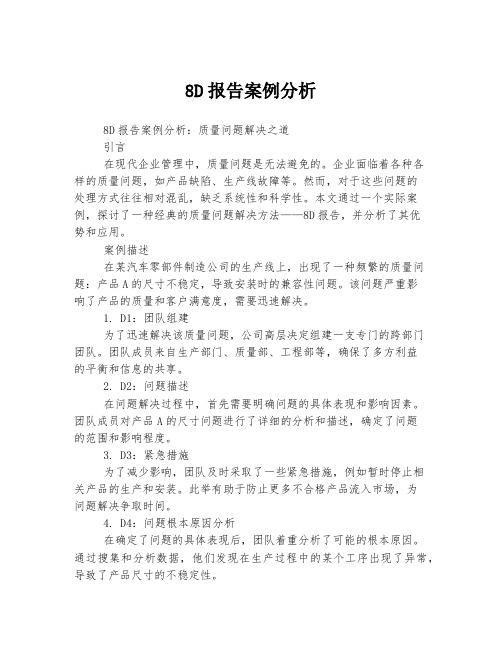
8D报告案例分析8D报告案例分析:质量问题解决之道引言在现代企业管理中,质量问题是无法避免的。
企业面临着各种各样的质量问题,如产品缺陷、生产线故障等。
然而,对于这些问题的处理方式往往相对混乱,缺乏系统性和科学性。
本文通过一个实际案例,探讨了一种经典的质量问题解决方法——8D报告,并分析了其优势和应用。
案例描述在某汽车零部件制造公司的生产线上,出现了一种频繁的质量问题:产品A的尺寸不稳定,导致安装时的兼容性问题。
该问题严重影响了产品的质量和客户满意度,需要迅速解决。
1. D1:团队组建为了迅速解决该质量问题,公司高层决定组建一支专门的跨部门团队。
团队成员来自生产部门、质量部、工程部等,确保了多方利益的平衡和信息的共享。
2. D2:问题描述在问题解决过程中,首先需要明确问题的具体表现和影响因素。
团队成员对产品A的尺寸问题进行了详细的分析和描述,确定了问题的范围和影响程度。
3. D3:紧急措施为了减少影响,团队及时采取了一些紧急措施,例如暂时停止相关产品的生产和安装。
此举有助于防止更多不合格产品流入市场,为问题解决争取时间。
4. D4:问题根本原因分析在确定了问题的具体表现后,团队着重分析了可能的根本原因。
通过搜集和分析数据,他们发现在生产过程中的某个工序出现了异常,导致了产品尺寸的不稳定性。
5. D5:纠正措施在确定了根本原因后,团队制定了一系列纠正措施。
例如,他们重新设计了工序的操作规范,加强了员工培训并引入了更先进的设备。
这些措施旨在消除根本原因并确保产品的稳定尺寸。
6. D6:纠正措施效果验证纠正措施的实施需要验证其有效性。
团队进行了进一步的测试和数据分析,确保新的工序设计和设备引入能够改善产品尺寸的稳定性。
7. D7:预防措施除了解决当前问题,团队还制定了一些预防措施,以避免类似问题再次发生。
这些措施包括对生产过程进行全面审查和改进,加强员工培训,以及建立监控系统等。
8. D8:团队总结与表扬在问题解决后,团队对整个过程进行总结,并表扬了各成员的贡献。
质量分析8d报告案例
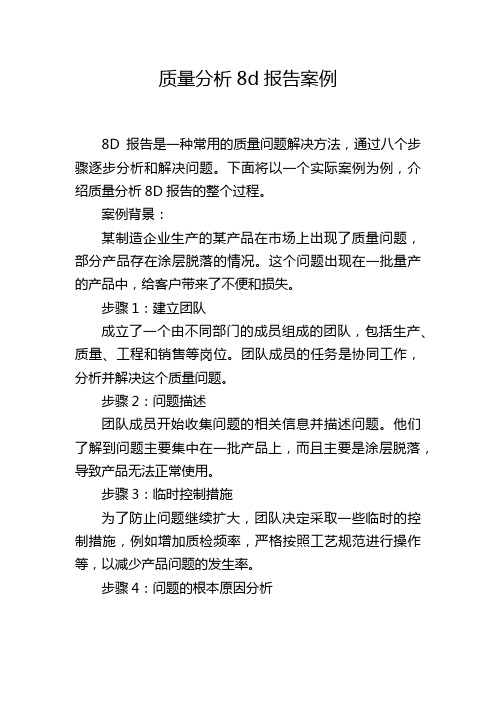
质量分析8d报告案例8D报告是一种常用的质量问题解决方法,通过八个步骤逐步分析和解决问题。
下面将以一个实际案例为例,介绍质量分析8D报告的整个过程。
案例背景:某制造企业生产的某产品在市场上出现了质量问题,部分产品存在涂层脱落的情况。
这个问题出现在一批量产的产品中,给客户带来了不便和损失。
步骤1:建立团队成立了一个由不同部门的成员组成的团队,包括生产、质量、工程和销售等岗位。
团队成员的任务是协同工作,分析并解决这个质量问题。
步骤2:问题描述团队成员开始收集问题的相关信息并描述问题。
他们了解到问题主要集中在一批产品上,而且主要是涂层脱落,导致产品无法正常使用。
步骤3:临时控制措施为了防止问题继续扩大,团队决定采取一些临时的控制措施,例如增加质检频率,严格按照工艺规范进行操作等,以减少产品问题的发生率。
步骤4:问题的根本原因分析团队成员使用常用的质量工具(如鱼骨图、5W1H分析等)进行问题的根本原因分析。
他们发现问题可能与涂层工艺、原材料质量等因素有关。
步骤5:制定长期解决方案基于问题的根本原因分析,团队成员制定了长期解决方案。
他们决定对涂层工艺进行优化,对原材料质量进行更加严格的控制。
同时,还计划对生产工艺进行改进,以提高产品的质量和可靠性。
步骤6:验证解决方案为了验证解决方案的有效性,团队进行了一系列实验和测试。
他们使用不同的涂层工艺和原材料质量进行生产,并对产品进行测试。
结果表明,解决方案确实有效,产品的质量得到了显著提升。
步骤7:实施长期解决方案基于验证结果,团队决定全面实施长期解决方案。
他们对生产流程进行调整,更新工艺规范,并与供应商合作加强原材料质量监控。
步骤8:预防措施为了防止类似问题的再次发生,团队制定了一系列预防措施。
他们决定加强内部培训,提高员工的质量意识和技能水平。
此外,还计划开展定期的质量检查和审查,以及建立质量指标和绩效评估体系。
通过以上八个步骤,团队成功解决了产品质量问题,并采取了一系列措施防止问题的再次发生。
8d报告案例范文

8D报告案例:汽车制造业中的质量问题解决1. 案例背景汽车制造业是一个竞争激烈的行业,汽车制造商需要不断提高产品质量以满足市场需求。
然而,由于生产过程中的各种原因,质量问题时常出现。
这就需要制造商采取措施解决问题,以降低不良率,提高产品质量。
本案例以某汽车制造商的一个具体质量问题为背景,展示了如何使用8D报告方法解决质量问题。
2. 案例过程2.1 问题发现在该汽车制造商的生产线上,某一型号的汽车在组装过程中出现了一定比例的漏油问题。
漏油问题不仅影响了汽车的外观和品质,还可能导致机械故障,给消费者带来不便和安全隐患。
因此,该问题被认为是一个严重的质量问题,需要尽快解决。
2.2 问题分析制造商成立了一个专门的团队来分析漏油问题。
团队首先进行了现场调查,观察了漏油现象发生的具体情况,并收集了相关数据和样本。
通过对数据和样本的分析,团队发现漏油问题主要发生在某一特定的组装工序中。
进一步的分析表明,问题可能是由于该工序使用的密封胶出现了质量问题,导致密封不完全,从而引起漏油。
2.3 制定解决方案基于问题分析的结果,团队制定了以下解决方案:1.更换密封胶供应商:通过与多家供应商的沟通和评估,选择一家质量可靠的密封胶供应商,以确保密封胶的质量稳定。
2.优化工艺参数:对组装工序的工艺参数进行优化,确保密封胶的使用量和施工方式合理,从而提高密封效果。
3.强化质量控制:加强对组装工序的质量控制,建立更严格的检查和测试流程,确保每辆汽车的密封质量符合标准。
2.4 实施解决方案制造商在生产线上实施了以上的解决方案。
他们与新的密封胶供应商建立了合作关系,并对工艺参数进行了调整。
此外,他们还培训了员工,提高了他们对质量控制的意识和能力。
2.5 结果评估在实施解决方案后,制造商对漏油问题进行了跟踪和评估。
经过一段时间的观察和测试,他们发现漏油问题得到了显著改善。
对于经过改进的生产线,漏油问题的发生率大大降低,质量得到了有效控制。
质量8D报告模板案例

质量8D报告模板案例一、背景介绍随着市场竞争的加剧,产品质量成为企业生存和发展的关键因素。
为了提高产品质量,企业需要建立一套完善的品质管理体系,并对产品质量问题进行有效的分析和改进。
8D报告作为一种常用的品质问题分析工具,旨在帮助团队系统地识别问题、找出根本原因并制定解决方案。
本文将介绍一个质量8D报告模板案例,帮助您更好地理解和应用8D报告。
二、8D报告概述1. 建立团队:确定团队成员,明确各自职责,确保团队具备解决问题的能力。
2. 描述问题:详细描述问题的症状、影响范围、严重程度等,以便团队成员对问题有清晰的认识。
3. 临时措施:在找到根本原因之前,采取临时措施以减轻问题的影响。
4. 确定并验证根本原因:通过数据分析和团队讨论,找出问题的根本原因,并验证其准确性。
5. 选择并验证永久纠正措施:针对根本原因,制定并验证永久性的纠正措施。
6. 实施并验证永久纠正措施:执行永久性纠正措施,并验证其有效性。
8. 团队认可:确保团队成员对问题解决过程和结果表示认可。
三、质量8D报告模板案例1. 建立团队:项目组成员包括研发、生产、品质、采购等部门,明确各自职责。
2. 描述问题:某产品在客户使用过程中出现故障,导致客户投诉。
故障现象为产品无法启动,影响范围为多个批次。
3. 临时措施:对故障产品进行维修,确保客户正常使用。
4. 确定并验证根本原因:通过分析故障产品,发现故障原因为电源模块设计缺陷,导致电源无法正常供电。
5. 选择并验证永久纠正措施:对电源模块进行重新设计,确保电源正常供电。
6. 实施并验证永久纠正措施:对已生产的产品进行电源模块更换,并对新设计进行验证,确保问题得到解决。
7. 预防措施:加强电源模块设计审查,提高设计质量;对供应商进行筛选,确保零部件质量。
四、8D报告的执行流程1. 确定问题:当出现品质问题时,要明确问题的性质、影响范围和严重程度。
2. 组建团队:根据问题的性质,组建一个跨部门的团队,包括相关领域的专家。
8D应用案例范文

8D应用案例范文8D是指一种用于解决问题和改进过程的方法,其中D分别代表所进行的八个步骤。
下面将展示一些8D方法的典型应用案例。
案例一:汽车生产线质量问题汽车制造公司的组装线上出现了一批汽车车身烤漆起皱的问题,给产品质量和用户满意度带来了严重影响。
该公司立即采用8D方法进行问题分析和解决。
D1:建立团队公司组建了一个跨部门的团队,包括生产、质量控制、工艺和烤漆等相关部门的专家和工程师。
D2:描述问题团队对车身烤漆起皱的问题进行了详细描述,包括问题发生的时间、地点、具体情况等。
D3:立即解决并限制问题通过对问题进行实地观察和实验验证,团队发现烤漆起皱是由于涂料配方中项物质的含量超标造成的。
团队立即采取措施,停止使用含有该物质的涂料,以避免进一步质量问题。
D4:寻找根本原因团队进行了更深入的分析,发现该物质超标是由供应商在生产过程中的失误所导致的。
团队与供应商进行沟通,并制定了新的质量规范和生产流程。
D5:实施纠正措施团队与供应商一起制定了一系列的纠正措施,包括提供培训、重新设定工艺参数、加强质量控制等,以确保不再出现类似问题。
D6:验证纠正措施的有效性团队进行了一段时间的监测和测试,确认纠正措施已经有效,车身烤漆起皱的问题没有再次发生。
D7:预防措施团队总结经验教训,以避免类似问题的再次发生,制定了更为严格的供应商管理制度和质量控制标准。
D8:表彰团队和总结经验公司对团队成员进行了表彰,并将这个案例作为培训教材,以帮助其他部门和团队更好地运用8D方法解决问题。
案例二:电子产品设计缺陷一家电子产品公司的新产品在上市后不久,出现了电池寿命短、系统崩溃和无法充电等问题。
公司立即采用8D方法来解决这些质量问题。
D1:建立团队公司成立了一个由工程师、质量控制人员和技术研发人员组成的团队,负责处理这些问题。
D2:描述问题团队对各个问题进行了详细描述,并收集了用户的反馈和意见。
D3:立即解决并限制问题团队对电池寿命短问题进行了深入调查,发现是由于电池充电控制电路设计缺陷导致。
- 1、下载文档前请自行甄别文档内容的完整性,平台不提供额外的编辑、内容补充、找答案等附加服务。
- 2、"仅部分预览"的文档,不可在线预览部分如存在完整性等问题,可反馈申请退款(可完整预览的文档不适用该条件!)。
- 3、如文档侵犯您的权益,请联系客服反馈,我们会尽快为您处理(人工客服工作时间:9:00-18:30)。
A、库存60k重新检查发现有未倒角不良现象,现已隔离挑选处理,生产部负责执行.
1、隔离处理示图:
B、工程部正在调试机器、修复模具确认效果OK.
A、改善前:B、改善后:
B、凡是有异常的产品需隔离标识待处理不能入库、或出货,防止不良品流出.
C、由于过程受机器影响很不稳定,品质部负责做过程能力分析,排除异常原因,监控过程,预防再次出现类似不良现象.
DISCIPLINE 8CUSTOMER FEEDBACK & COMMENT (客戶意見回饋)CLOSE DATE:
APPROVED BY:CHECKED BY:PREPARED BY:
改善后随机抽样测试:
90°±2°: 、、、、、、、、、
平均值:°
±:、、、、、、、、、
平均值:
DISCIPLINE 7 PREVENT RECURRENCE(預防再發)EFFECTIVE DATE:2011-3-21
A、为防止机器或模具出现类似情况,生产部需加强机器保养、工程部定期检查维修机器、模具.
SEPart Number #
Process Owner
Contact
Team Member
Telephone
DISCIPLINE 2 DESCRIBE THE PROBLEM(問題描述)DATE:
DearALL:
貴司某产品來料20K經我司IQC檢驗發現有尺寸偏差現象,圖面要求+/,
实际测量为;图面要求90+/-2,实际测量为,此角度偏大铆压后会出现PIN
脚歪斜,不良率75%;10±2°处未倒边,不良率为100%,此批不良判退貨,以上請知悉了解并處理,並請在3個工作日內回復8D報告.
DISCIPLINE 3IMPLEMENT CONTAINMENT PLAN(短期對策)DATE:
不良品清查防堵
類別
項目
批次
總數量
抽樣數
不良數
不良率
處理方式
供應商
在製
在庫
60K
30
15
50%
隔离挑选处理
在途
外包商
在製
在途
在庫
中山信音
在製
在途
部品在庫
成品在庫
DISCIPLINE 4 FIND THE ROOT CAUSE(真因分析)EFFECTIVE DATE:2011-319
a. 系統面; b.防火牆失效;
1. 為何會生產出不良
Why 1:冲压模具偏移、冲头磨损、间隙太大导致折弯角度偏移上限、尺寸超差.
1. 如何生產出良品
Why 1:调整机器、修复模具.
責任部門/人:工程部/李完成時間:2011-3-21
Why 2:转换型号时检验员需做首件确认,检验OK可进入量产,检验NG通知工程部调整模具.
責任部門/人:品质部/吴完成時間:2011-3-21
Why 3:过程巡检发现异常需隔离标示产品,不得流入仓库,再通知作业员调整机器.
QC-06-029-B
某某公司
TEL:FAX:
TO:
DATE:
FROM:
PAGE:
8D NO.:
CUSTOMER:
DISCIPLINE 1 USE TEAM APPROACH(改善團隊)
CAR Number #
Team
Internal Team
External Team
Customer Part Number #
Sales Owner
1、折弯冲头磨损、间隙太大(如下图)
Why 2:转换型号时模具相接不到位导致冲压同时出来的两个产品,有一个未倒角.
1、模具相接不到位(如下图)
2、未倒角(如下图)
2. 為何未檢出不良
未检验出不良主要是:我司检验员失职
責任部門/人:品质部完成時間:2011-3-19
DISCIPLINE 5 IMPLEMENT PERMANENT CORRECTIVE ACTIONS(長期對策)EFFECTIVE DATE:2011-3-19
責任部門/人:生产部/刘完成時間:2011-3-21
Why 4:过程巡检、最终终检需加严抽检,如发现不良不能流入仓库.
責任部門/人:品质部/吴完成時間:2011-3-22
2. 如何檢出不良
制程首件确认、巡检,过程终检和出货检验抽检如发现与检验标准不符需隔离标示.
責任部門/人:品质部/吴完成時間:2011-3-22