制动系统设计规范
制动系统设计规范
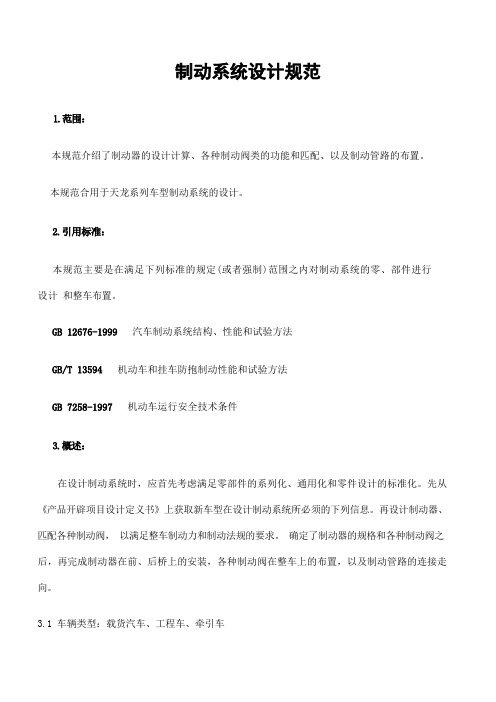
本规范介绍了制动器的设计计算、各种制动阀类的功能和匹配、以及制动管路的布置。
本规范合用于天龙系列车型制动系统的设计。
本规范主要是在满足下列标准的规定(或者强制)范围之内对制动系统的零、部件进行设计和整车布置。
汽车制动系统结构、性能和试验方法机动车和挂车防抱制动性能和试验方法机动车运行安全技术条件在设计制动系统时,应首先考虑满足零部件的系列化、通用化和零件设计的标准化。
先从《产品开辟项目设计定义书》上获取新车型在设计制动系统所必须的下列信息。
再设计制动器、匹配各种制动阀,以满足整车制动力和制动法规的要求。
确定了制动器的规格和各种制动阀之后,再完成制动器在前、后桥上的安装,各种制动阀在整车上的布置,以及制动管路的连接走向。
3.1 车辆类型:载货汽车、工程车、牵引车3.2 驱动形式:4×2、6×4、8×43.3 主要技术及性能参数:长×宽×高、轴距、空/满载整车重心高坐标、轮距、整备质量、额定载质量、总质量、前/后桥承载吨位、 (前/后)桥空载轴荷、 (前/后)桥满载轴荷、最高车速、最大爬坡度等。
3.4 制动系统的配置:双回路气/液压制动、弹簧制动、鼓/盘式制动器、防抱制动系统、手动/自动调整臂、无石棉磨擦衬片、感载阀调节后桥制动力、缓速器、排气制动。
本规范仅对鼓式制动器的各主要元件和设计计算加以阐述,盘式制动器的选型和计算将暂不列入本规范的讨论范围之内。
4.1 鼓式制动器主要元件:4.1.1 制动鼓:由于铸铁耐磨,易于加工,且单位体积的热容量大,所以,重型货车制动鼓的材料多用灰铸铁。
不少轻型货车和轿车的制动鼓为组合式,其圆柱部份用铸铁,腹板则用钢压制件。
制动鼓在工作载荷下将变形,使蹄、鼓间单位压力不均,带来少许踏板行程损失。
制动鼓变形后的不圆柱度过大,容易引起制动时的自锁或者踏板振动。
所以,在制动鼓上增加肋条,以提高刚度和散热性能。
中型以上货车,普通铸造的制动鼓壁厚为 13~18㎜。
刹车优先标准

刹车优先标准
一、刹车系统设计
刹车系统是汽车中至关重要的安全系统,其设计必须遵循严格的标准和规范。
在设计刹车系统时,应充分考虑车辆的重量、速度、轮胎尺寸、道路条件等因素,以确保刹车性能的可靠性和稳定性。
二、刹车响应时间
刹车响应时间是指从驾驶员踩下刹车踏板到刹车系统开始产生制动力矩的时间。
这个时间必须尽可能短,以保证车辆能够在最短的时间内减速停车。
刹车响应时间的标准应根据不同的车辆类型和用途来确定。
三、刹车压力调节
刹车压力调节是刹车系统的一个重要组成部分,它直接影响制动力矩的大小和分布。
刹车压力调节应当根据不同的道路条件和行驶状况进行调整,以保证制动力矩的适当和均匀分布。
四、刹车性能检测
刹车性能检测是确保刹车系统正常工作的必要手段。
应定期对刹车系统进行检测,包括刹车响应时间、制动力矩、刹车片磨损情况等,以保证刹车性能的可靠性。
五、刹车安全性评估
刹车安全性评估是对刹车系统在紧急制动情况下的性
能进行评估。
评估应包括在不同速度下的制动距离、制动稳定性、制动方向稳定性等方面,以确保车辆在紧急情况下能够安全停车。
六、刹车配件选择
刹车配件的选择对刹车系统的性能和可靠性有很大的影响。
选择高质量的刹车片、刹车盘、刹车油等配件,可以保证刹车的耐久性和稳定性。
七、刹车系统保养与维护
为了保持刹车系统的良好性能,应定期进行保养与维护。
这包括更换刹车片、清洗或更换刹车油、检查制动管路等,以防止制动失灵、制动力下降等问题的出现。
在维护过程中,应该严格遵守汽车制造商提供的维护指南和推荐程序,以确保安全和性能。
牵引车制动标准

牵引车制动标准
现代牵引车的制动系统扮演着至关重要的角色。
制动系统不仅需要提供强大的制动力,还必须符合严格的安全标准,以确保驾驶者和乘客的安全。
牵引车的制动系统被分为几个不同的部分,包括刹车片、刹车盘、刹车液和刹车手柄。
这些部件必须在各种条件下保持正常工作,并能够在紧急情况下迅速响应。
为了确保牵引车的制动系统符合安全标准,制动片必须具有适当的磨损指示器,以便驾驶员可以检查其是否需要更换。
刹车片金属材料必须符合特定的化学成分和物理属性,以确保其耐用性和性能。
刹车盘也必须进行定期检查和维护,以确保其表面平整并且没有裂纹或变形。
刹车液在牵引车的制动系统中起着至关重要的作用。
它必须具有适当的黏度和稳定性,以确保在高温下不会蒸发或沉淀。
此外,刹车液还必须能够有效地传输刹车力,并在制动操作后迅速恢复压力。
刹车手柄是牵引车制动系统的控制中心。
它必须具有灵活性和精确性,以便驾驶员可以准确地控制刹车力度。
此外,刹车手柄还必须易于操作,并在紧急情况下能够提供及时的制动响应。
总之,牵引车的制动系统设计和生产必须严格遵守相应的标准和规范。
这些标准确保制动系统的可靠性和安全性,为驾驶员和乘客提供安全而舒适的驾驶体验。
制动系统设计规范

制动系统设计规范制动系统是车辆安全性能的重要组成部分,其设计规范的制定对于保证车辆行驶安全具有重要意义。
以下是关于制动系统设计规范的一些考虑因素。
1.制动力量:制动系统必须能够提供足够的制动力量,以便在各种条件下可靠地将车辆停下来。
制动力量应根据车辆的质量、设计速度、使用环境等因素进行评估,并确保能够适应各种道路状况和紧急制动情况。
2.制动系统的灵敏度:制动系统的设计应考虑车辆行驶时的灵敏度。
制动踏板应有适当的行程和力度,以确保驾驶员能够精确地控制制动力的大小,并根据需要适时调整。
3.制动系统的稳定性:制动系统在使用过程中应保持稳定性。
制动力的分配应均匀,以防止车辆在制动时出现不稳定或抱死现象。
此外,制动系统的热稳定性也是一个重要考虑因素,以确保长时间高强度制动时不会出现制动衰减或失效。
4.制动信号传递的可靠性:制动系统的信号传递应能够准确可靠地反映制动操作的实际情况,以保证驾驶员和其他车辆能够及时、准确地对制动操作做出反应。
传感器和传输装置的设计应具有高可靠性,能够承受恶劣的环境条件,如高温、湿度、振动等。
5.制动系统的耐用性:制动系统的设计应具备耐用性,以适应长时间、高频率的使用。
制动片和制动盘的材料选择应具有较高的磨擦耐久性和热稳定性,以延长制动系统的使用寿命,并减少维修和更换的频率。
6.制动系统的自动化和智能化:随着科技的发展,制动系统也向着自动化和智能化的方向发展。
制动系统设计应考虑集成各种智能传感器和控制单元,以提高制动系统的响应速度和精确性,使得制动操作更加方便和安全。
7.制动系统的安全性:制动系统是车辆安全性的关键因素之一,其设计应确保系统在任何情况下都能保持完全可靠和安全。
例如,制动系统应具备防止制动衰减或失效的措施,如制动助力器、制动液液位警告装置等。
总之,制动系统设计规范的制定是为了确保车辆行驶的安全性能。
以上所列的因素只是设计规范的一部分,实际的设计规范还需要涵盖更多方面,以满足不同车型和使用环境的需求,并不断适应科技的发展。
13制动系统设计规范

13制动系统设计规范制动系统是一款车辆非常重要的安全系统,直接影响到车辆的制动性能和行车安全。
对于制动系统的设计规范,下面将从设备选型、布置设计、控制系统设计、保养与维护等方面进行详细阐述。
一、设备选型1.制动器选型:根据车辆的类型、质量和运行速度等因素选择适合的制动器,确保其能够承受对应的制动力,并具有稳定的制动性能。
2.主缸和助力器选型:根据车辆的质量和制动需求选择合适的主缸和助力器,确保能够提供足够的制动力,并具有快速响应和稳定性好的特点。
3.制动片/鼓选型:选择耐磨、散热性好、摩擦稳定的制动片/鼓,并根据车辆使用情况进行适当调整。
二、布置设计1.制动管路设计:设计合理的制动管路,确保制动力能够传递到各个轮子,并且管路布置尽量简洁,减少制动力的损失。
2.制动助力器布置:助力器应设置在主缸和制动器之间,布置合理,保证管路短连接,提高制动效果。
三、控制系统设计1.制动系统电气设计:根据车辆的特点,选择合适的电气元件和线路布置,确保电气系统的可靠性和稳定性。
2.制动踏板设计:踏板应符合人体工程学原理,力度适中,操作感受良好,能准确感知制动力大小和变化。
3.制动系统控制策略设计:根据车辆的特点和需求,制定合理的制动控制策略,确保制动力分配均匀、稳定。
四、保养与维护1.定期检查制动系统的工作状况,包括制动片/鼓磨损情况、制动液油位和油质、制动踏板行程、制动管路漏气等。
2.定期更换制动片/鼓和制动液,确保制动系统的正常工作和稳定性。
3.检查和保养助力器,确保其功能正常,能够提供足够的助力。
以上是对13制动系统设计规范的详细阐述,设计和保养制动系统时必须要考虑到车辆的特点和使用情况,确保其能够提供稳定、可靠的制动性能,保障行车安全。
同时,制动系统的设计和维护也需要参考相关的法律法规,以确保制动系统符合强制性标准,且能满足用户需求。
城际铁路供电与牵引系统的设计规范

城际铁路供电与牵引系统的设计规范一、引言城际铁路作为城市间的重要交通枢纽,供电与牵引系统的设计规范对于其安全、高效运行至关重要。
本文将详细介绍城际铁路供电与牵引系统的设计规范。
二、供电系统设计规范1. 供电系统设计原则(1) 可靠性原则:供电系统应具有高度可靠性,确保供电持续稳定。
(2) 安全性原则:供电系统应符合国家相关安全规定,确保人员和设备的安全。
(3) 经济性原则:供电系统应在满足要求的前提下,尽可能降低建设和运营成本。
2. 供电系统设计技术要求(1) 列车运行电压:根据运行速度和线路类型确定合适的列车运行电压,以确保牵引力和能耗的平衡。
(2) 轨道绝缘设计:合理设置绝缘节,确保电流的正常传输,防止漏电和故障。
(3) 供电系统馈线设计:根据线路长度和功率要求,合理配置馈线和变电站,确保电能的稳定输送。
(4) 地线设计:合理布置地线系统,确保接地电阻符合要求,提高供电系统的可靠性。
三、牵引系统设计规范1. 牵引系统设计原则(1) 高效性原则:牵引系统应具备高效节能的特点,减少能源消耗。
(2) 平稳性原则:牵引系统应具有平稳启动和制动的特性,确保乘客的乘坐舒适度。
(3) 可控性原则:牵引系统应具备可调节的特性,以适应不同运行条件和载重。
2. 牵引系统设计技术要求(1) 牵引电机选型:根据列车的负载和运行速度,选择合适的牵引电机,并确保电机的高效工作。
(2) 制动系统设计:设计可靠的制动系统,确保列车制动的平稳和安全。
(3) 传动系统设计:选择合适的传动方式,确保牵引力的传递和传动效率。
(4) 能量回馈系统:设计能量回馈系统,将列车制动时产生的能量反馈到电网,提高能源利用效率。
四、供电与牵引系统的协调设计1. 供电与牵引系统的关系供电系统和牵引系统是密切相关的,它们之间的协调设计对于高效、安全的运行至关重要。
供电系统提供所需的电能,而牵引系统将电能转化为牵引力,推动列车运行。
2. 协调设计原则(1) 考虑功率需求:供电系统应根据牵引系统的功率需求,设计合适的电气设备和供电方式。
公交制动布置方案

公交制动布置方案引言公交车是城市交通中重要的一部分,而制动系统是公交车安全运行的关键因素之一。
制动布置方案的设计合理与否直接关系到公交车的制动性能以及乘客的安全。
本文将介绍一种公交制动布置方案,旨在提高公交车的制动效果,并确保乘客的安全。
概述公交制动系统主要包括制动器、制动液、制动管路以及制动踏板等组成部分。
制动布置方案的核心是设计合理的制动管路,以便实现良好的制动效果。
下面将详细介绍公交制动布置方案的设计原则和实施步骤。
设计原则1. 制动平衡公交车是一种大型车辆,制动系统需要保证车辆在制动过程中的稳定性和平衡性。
因此,在制动布置方案中,需要合理安排前、后轮制动器的布置位置,使得制动力能够均匀地分配到各个轮胎上,以确保车辆的稳定制动。
2. 刹车响应时间短公交车的刹车响应时间直接关系到乘客的乘坐舒适度和安全性。
在制动布置方案中,需将制动液管路优化,缩短刹车指令的传递时间,确保刹车能够及时响应,提高制动的灵敏度。
3. 刹车力度可调公交车行驶过程中,不同的路况和载荷都会对制动性能产生影响。
因此,在制动布置方案中,应该考虑安装可调节刹车力度的装置,以便根据实际需求和情况对刹车力度进行调整。
实施步骤1. 制动器位置选择在制动器位置选择时,应考虑到车辆的布局和空间限制。
一般来说,前轮制动器安装在车辆前部,后轮制动器安装在车辆后部,以保证制动力的平衡。
同时,还应考虑到制动器与其他部件(如悬挂系统)的衔接和配合,确保制动器的安装牢固可靠。
2. 制动管路布置制动管路的布置要求紧凑、合理,并且尽量减小刹车液的压力损失。
在设计制动管路时,应考虑到管路的长度、直径、连接方式等因素。
另外,为了提高制动效果,可以采用分段布置管路的方式,即将管路分成不同的段落,以减小制动液的压力损失和传递时间。
3. 制动踏板设计制动踏板的设计也是制动布置方案中的重要环节。
制动踏板的设计应该符合人体工程学原理,并且具有良好的力传递特性。
保证乘客可以轻松踩下制动踏板,并且制动力能够准确地传递到制动器上。
铁路制动系统规章制度最新

铁路制动系统规章制度最新1. 引言铁路制动系统是铁路运输中至关重要的一个部分,它对列车的安全行驶起着至关重要的作用。
为了确保铁路运输的安全性、可靠性和高效性,制定和执行一套规范的制动系统规章制度是必要的。
本文将介绍铁路制动系统的相关规章制度的内容和要求。
2. 制动系统基本原则铁路制动系统的基本原则主要包括下列几个方面:2.1 制动力的准确控制铁路制动系统需要能够实现对列车制动力的准确控制,确保列车按照指定的速度适时停车。
制动力的控制需要根据列车的负荷、速度等因素进行合理的调整。
2.2 制动装置的可靠性制动装置必须具备良好的可靠性,确保在任何情况下都能够正常工作。
同时,需要定期对制动装置进行检测和维护,以确保其正常使用。
2.3 制动系统的统一标准制动系统的设计、使用和维护需要遵循统一的标准和规定,确保整个铁路网络中的列车制动系统的互通互用。
铁路制动系统的设备主要包括制动阀、制动缸、制动盘等组成部分。
对于这些设备的要求主要有以下几个方面:3.1 设备的可靠性和精度制动设备必须具备良好的可靠性,确保在各种条件下都能够正常工作。
同时,设备的精度也需要达到要求,以便准确控制制动力。
3.2 设备的平衡性和稳定性制动设备在工作时需要具备良好的平衡性和稳定性,以确保制动力的均匀分布和稳定施加。
3.3 设备的维护和检修制动设备需要定期进行维护和检修,以保持其良好的工作状态。
同时,对于有故障或者磨损的设备,需要及时更换或修复。
4. 制动系统的操作要求铁路制动系统的操作要求涵盖了列车运行中制动系统的启动、调整和停止等方面的内容。
4.1 启动制动系统的要求列车启动时,必须按照规定的程序进行制动系统的启动。
首先需要对制动装置进行检查,确保其正常工作。
然后按照规定的操作程序启动制动系统。
在列车运行中,需要根据实际情况对制动力进行调整。
这需要根据列车的运行速度和负荷等因素进行合理的操作,确保制动力的准确控制。
4.3 停车制动系统的要求列车停车时,制动系统需要确保列车能够按照预定的位置和速度停稳。
- 1、下载文档前请自行甄别文档内容的完整性,平台不提供额外的编辑、内容补充、找答案等附加服务。
- 2、"仅部分预览"的文档,不可在线预览部分如存在完整性等问题,可反馈申请退款(可完整预览的文档不适用该条件!)。
- 3、如文档侵犯您的权益,请联系客服反馈,我们会尽快为您处理(人工客服工作时间:9:00-18:30)。
制动系统设计规范1.范围:本规范介绍了制动器的设计计算、各种制动阀类的功能和匹配、以及制动管路的布置。
本规范适用于天龙系列车型制动系统的设计。
2.引用标准:本规范主要是在满足下列标准的规定(或强制)范围之内对制动系统的零、部件进行设计和整车布置。
GB12676-1999汽车制动系统结构、性能和试验方法GB/T13594机动车和挂车防抱制动性能和试验方法GB7258-1997机动车运行安全技术条件3.概述:在设计制动系统时,应首先考虑满足零部件的系列化、通用化和零件设计的标准化。
先从《产品开发项目设计定义书》上猎取新车型在设计制动系统所必须的下列信息。
再设计制动器、匹配各种制动阀,以满足整车制动力和制动法规的要求。
确定了制动器的规格和各种制动阀之后,再完成制动器在前、后桥上的安装,各种制动阀在整车上的布置,以及制动管路的连接走向。
3.1车辆类型:载货汽车、工程车、牵引车3.2驱动形式:4×2、6×4、8×43.3主要技术及性能参数:长×宽×高、轴距、空/满载整车重心高坐标、轮距、整备质量、额定载质量、总质量、前/后桥承载吨位、(前/后)桥空载轴荷、(前/后)桥满载轴荷、最高车速、最大爬坡度等。
3.4制动系统的配置:双回路气/液压制动、弹簧制动、鼓/盘式制动器、防抱制动系统、手动/自动调整臂、无石棉摩擦衬片、感载阀调节后桥制动力、缓速器、排气制动。
4.制动器:本规范仅对鼓式制动器的各主要元件和设计计算加以阐述,盘式制动器的选型和计算将暂不列入本规范的讨论范围之内。
4.1鼓式制动器主要元件:4.1.1制动鼓:由于铸铁耐磨,易于加工,且单位体积的热容量大,所以,重型货车制动鼓的材料多用灰铸铁。
不少轻型货车和轿车的制动鼓为组合式,其圆柱部分用铸铁,腹板则用钢压制件。
制动鼓在工作载荷下将变形,使蹄、鼓间单位压力不均,带来少许踏板行程损失。
制动鼓变形后的不圆柱度过大,容易引起制动时的自锁或踏板振动。
所以,在制动鼓上增加肋条,以提高刚度和散热性能。
中型以上货车,一般铸造的制动鼓壁厚为13~18㎜。
4.1.2制动蹄和摩擦片:重型货车的制动蹄多用铸铁或铸钢铸成,制动蹄的断面形状和尺寸应保证其刚度。
重型货车用无石棉摩擦片(GB12676-1999第4.1.3制动衬片应不含有石棉。
)的前片厚度为15㎜左右,后片厚度为18㎜左右。
摩擦片材料的性能应具有:高而稳定的摩擦系数,热衰退较缓和;耐磨性好;吸水率和吸油率低;较高的耐挤压强度和冲击强度;制动时没有噪声和有毒气体发出。
制动蹄和摩擦片可以铆接,也可以粘接。
粘接的优点在于衬片更换之前的使用厚度较大,但工艺复杂且不易更换衬片。
铆接衬片的工艺简单、噪声较小且易于更换。
东风汽车公司的制动衬片多采用铆接方式。
4.1.3制动底板:制动底板将承受全部制动反力矩,故应有足够的刚度。
刚度不足,将导致制动力矩减小,踏板行程加大,制动衬片磨损不均。
重型车多用铸造底板代替压制的制动底板。
4.1.4制动器间隙自动调整装置:制动鼓在不制动时应能自由运转,故制动鼓和制动衬片之间必须有一定的间隙。
鼓式制动器的设定间隙一般为0.2~0.5㎜。
采用自动调整装置(GB12676-1999第.1行车制动器的磨损应能自动调整。
但是,对于2N 和3N 类非公路车辆的制动器以及1M 和1N 类车辆的后制动器,可不强行要求安装自动调整装置。
……)时,制动器的间隙不需要人工精细调整,只需要进行多次全制动即可自动调整到设定间隙,并且在行车过程中能随时补偿过量间隙。
自动调整装置有间隙感应式和行程感应式两种,国内常用的是间隙感应式。
它感应制动器的间隙超过设定间隙值时,便自动加以调整到设定的间隙。
4.1.5制动气室:前桥制动器一般用膜片式的普通制动气室,中、后桥制动器一般用弹簧式制动气室,它的膜片气室部分用作行车制动,弹簧气室部分用作驻车制动或紧急制动。
膜片气室部分和弹簧气室部分的操纵气路完全独立,分别由脚制动和手制动控制。
膜片气室的优点在于结构简单,对气室壁的加工精度要求不高,但所容许的行程较小,膜片的使用寿命也较短。
不过,膜片的价格较低,且易于更换。
在工程车上很受欢迎。
而活塞气室的使用寿命较高,但对气室壁的加工精度要求较高,且不易适应恶劣的路况。
对非平衡式渐开线凸轮张开装置的制动器,有:式中1P 、2P ——凸轮对两蹄的张开力2a ——张开力对凸轮中心的力臂 h ——调整臂的臂长Q ——制动气室推杆的推力设制动气室工作压力为p ,则气室的作用面积为: 对活塞式制动气室:24D A π=,D 为活塞直径 对膜片式制动气室:)(1222d Dd D A ++=π其中D 为气室壳体在夹持膜片处的内径,d 为膜片夹盘直径。
气室的推杆行程为:δλa h l 2= 式中δ——制动器间隙λ——安全系数,取λ=2.2~2.4。
制动气室的工作容积为: 活塞式制动气室:l D Al V 24π== 膜片式制动气室:l d Dd D l A V ⋅++=⋅=)(6222π4.2制动器的设计计算:4.2.1制动器效能因数: 效能因数是鼓式制动器的一个非常重要的参数,它是制动器的输出力矩与输入力矩的比值。
设计制动器时,就是要在有限的制动器的空间里力争尽可能高的效能因数。
对于非平衡式凸轮张开装置的领、从蹄式制动器: 领蹄:1sin cos cos 1-=γβρλζk K t其中:R h /=ζ,R f k /=,R l /0=ρ,αβγλ-+= 从蹄:1sin cos 'cos 2+=γβρλζk K t 其中:R h /=ζ,R f k /=,R l /0=ρ,αβγλ+-=' 制动器效能因数:21214t t t t K K K K K += 式中:θ-领、从蹄摩擦片包角0θ-领从蹄摩擦片起始角α-最大压力线与摩擦片平分线的夹角γ-摩擦角β-等效法向合力与摩擦片平分线的夹角h -张开力对支点的力臂f -支点与制动鼓中心的距离0l -压力中心圆的直径R -制动鼓半径从上面的公式中可以看出:影响制动器效能因数的主要参数有摩擦片起始角0θ、摩擦片包角θ、制动蹄支承点与制动器中心的距离f 、制动鼓半径R 、张开力作用线到制动蹄支承点的力臂h 及摩擦片的摩擦系数μ。
摩擦片的片宽较大,对制动器吸热越好,也可减少磨损。
当输入力一定时,制动鼓的半径越大,则制动力矩就越大,且散热能力也越强。
但制动鼓的半径和摩擦片的片宽都受到轮辋内径的限制。
制动鼓与轮辋之间应保持一定的间隙,以改善制动器的散热条件。
一般情况下,制动鼓与轮辋直径之比为D/Dr=0.70~0.83。
制动鼓的半径R 和摩擦片的片宽b 是在轮辋内径的限制下确定的。
当摩擦片包角θ=90o ~100o 时,磨损最小,制动鼓温度最低,且制动效能最高。
θ再减小虽有利于散热,但单位压力过高将加速磨损。
而增大包角对减小单位压力的作用并不大,且将使制动作用不平顺,容易使制动器发生自锁。
所以,包角θ一般不大于120o 。
常将摩擦片布置在制动蹄的中央,故摩擦片起始角的大小为2900θθ-︒=。
张开力作用线到制动蹄支承点的力臂h 应尽可能大,以提高制动效能,h=1.6R 左右。
在保证两蹄支承端毛面不干涉的条件下,两支承端之间的距离尽可能小,所以,制动蹄支承点与制动器中心的距离f=0.8R 左右。
温度不同,摩擦片的摩擦系数也不同。
当温度在250oC 以下时,摩擦系数可保持在μ=0.35~0.4。
在计算制动器的制动力矩时,取μ=0.3可使计算结果更接近实际情况。
4.2.2制动力矩的计算:用效能因数法求制动蹄的制动力矩。
设制动蹄的制动力矩和输入张开力分别为μM 和P ,则KPR M =μ。
4.3制动性能验算:制动器的基本参数确定之后,制动器制动力矩的大小就已经确定了。
但该制动器能否满足整车性能的要求,需按照GB12676-1999和GB7258-1997的要求作进一步的验算。
4.3.1同步附着系数计算:式中:1b F -前桥制动器制动力(N)2b F -后桥制动器制动力(N)β-制动力分配系数0ψ-满载同步附着系数L -轴距(m)2L -汽车重心至后轴的纵向距离(m)g h -汽车重心高度(m)4.3.2满载时制动性能:当0ψψ<时)/(5)(2022max s m h L L g j g≥-+⋅=ψψψ 当0ψψ>时)/(5)(2011max s m h L L g j g ≥-+⋅=ψψψ 式中:1L -汽车重心至前轴的纵向距离(m)Ψ-附着系数g -重力加速度(m/s2)4.3.3剩余制动性能: 前失效时:)/(3.121s m h L gL j g≥+=ϕϕ 后失效时:)/(3.122s m h L gL j g ≥-=ϕϕ 4.3.4应急制动性能:4.3.5驻车制动性能:按GB12676-1999规定:驻车制动系必须使满载车辆停在18%坡道上(上坡或下坡);允许挂接挂车的车辆,牵引车的驻车制动系必须能使列车停在12%坡道上。
4.3.6比能量耗散率: 前桥制动器:2211/8.14mm W tAmv e ≤=β 后桥制动器:2212/8.14)1(mm W tAmv e ≤-=β式中:v-制动初速度1A-单个制动器的摩擦片面积t-制动时间4.3.7比摩擦力:M-单个制动器的制动力矩式中:5.制动阀:气制动管路系统中常用的制动阀类及总成有:空气压缩机、组合式空气干燥器(含卸载阀)、四回路保护阀、贮气筒、放水阀、取气阀、串联式双腔制动阀、快放阀、感载阀、弹簧制动气室、手控阀、差动式继动阀、挂车控制阀、分离开关及连接头、排气制动阀、缓速器、ABS电磁阀、单向阀、继动阀等。
5.1空气压缩机:空压机用来向汽车气制动系统或其它辅助用气装置提供必要的能源,即一定的气压和空气量。
空压机经皮带轮由发动机驱动。
空气经滤清器到达空压机吸气口,由进气门进入气缸。
气体被活塞压缩后,经排气门到达空压机供气口,再经干燥器、四保阀等进入贮气筒。
5.2组合式空气干燥器:由于经空压机压缩后的气体温度很高(一般在220℃左右),因此空气中包含的水分和油污将随同空气一起进入了管路中。
含有水蒸气的压缩空气,经过管道凝聚成水。
这些水分会引起金属零件锈蚀,橡胶密封件龟裂、润滑油脂分解失效,管路堵塞等故障,严重影响行车安全性。
特别在寒冷地区的冬季,滞留在管路中的水分容易冻结成冰,破坏阀的正常工作,甚至使制动操纵失效。
组合式空气干燥器利用分子筛作为干燥剂,采用与卸载阀一体的整体式结构,利用卸载阀排气的动作,使再生贮气筒中的压缩空气反向通过干燥筒,将干燥剂表面吸收的水分和油污排入大气,实现分子筛的再生活化,更长期有效地清洁压缩空气中的水分及其它杂质。