汽车盘式制动器设计
盘式制动器_毕业设计说明书参考

盘式制动器_毕业设计说明书参考(以下是机械设计专业的毕业设计说明书范例,供参考)毕业设计题目:盘式制动器设计一、题目来源及背景盘式制动器是用于汽车、摩托车等机动车辆的制动装置之一,具有制动力矩大、耐磨损、散热快等优点。
本毕业设计项目充分利用机械设计、材料学等方面知识,对盘式制动器的制动器件进行设计。
二、设计要求1. 主要技术指标:(1)制动力矩:大于100 N·m(2)使用寿命:大于2×10⁴次(3)材料:盘式制动器盘采用GCr15;制动蹄采用40Cr;制动片采用半金属材料。
2. 设计思路(1)整体结构设计:盘式制动器的整体结构以制动盘、制动蹄、制动片、制动器液压缸等组成。
其中,制动盘为主动件,制动蹄和制动片为被动件,液压缸提供制动力。
(2)制动盘设计:制动盘是盘式制动器的核心部件,由于需要承受制动力矩,因此采用GCr15高强度材料。
制动盘的直径和厚度由制动力矩、车辆重量等因素决定。
(3)制动片设计:制动片采用半金属材料,能够在制动过程中承受高温、高压。
制动片的表面采用刻花纹路,以增加摩擦面积和摩擦系数。
(4)制动蹄设计:制动蹄采用40Cr合金钢,具有足够的强度和硬度。
制动蹄的设计应考虑制动片与制动盘之间的间隙,以确保能够实现完整制动。
(5)液压缸设计:液压缸的设计应考虑到制动盘的直径和轮轴间隙,能够提供足够的制动力矩。
液压缸的设计也应考虑到防泄漏、稳定等因素。
三、设计过程1. 制动盘设计(1)根据制动力矩、车辆重量等因素确定制动盘的直径和厚度。
(2)采用CAD软件进行3D建模,并进行有限元分析,得出制动盘在制动力矩作用下的应力分布情况和变形情况。
(3)结合分析结果,调整制动盘的厚度和结构。
(4)根据制动盘的设计尺寸和结构参数,进行加工和表面处理,确保制动片和制动盘之间具有充分的接触面积和摩擦力。
2. 制动片设计(1)选择半金属材料作为制动片材料。
根据制动盘的直径和表面处理情况,设计制动片的形状和尺寸。
盘式制动器教学方案设计
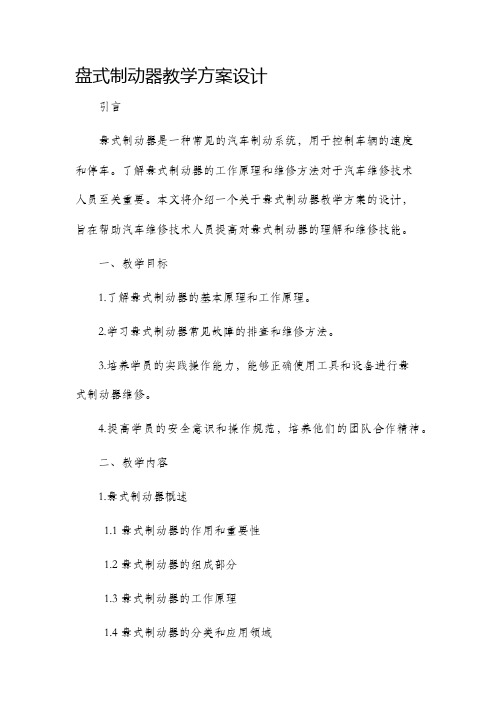
盘式制动器教学方案设计引言盘式制动器是一种常见的汽车制动系统,用于控制车辆的速度和停车。
了解盘式制动器的工作原理和维修方法对于汽车维修技术人员至关重要。
本文将介绍一个关于盘式制动器教学方案的设计,旨在帮助汽车维修技术人员提高对盘式制动器的理解和维修技能。
一、教学目标1.了解盘式制动器的基本原理和工作原理。
2.学习盘式制动器常见故障的排查和维修方法。
3.培养学员的实践操作能力,能够正确使用工具和设备进行盘式制动器维修。
4.提高学员的安全意识和操作规范,培养他们的团队合作精神。
二、教学内容1.盘式制动器概述1.1 盘式制动器的作用和重要性1.2 盘式制动器的组成部分1.3 盘式制动器的工作原理1.4 盘式制动器的分类和应用领域2.盘式制动器的结构和工作原理2.1 刹车片和刹车盘的结构和材料2.2 刹车片与刹车盘的接触方式2.3 刹车盘的热膨胀和退火2.4 刹车液和刹车缸的作用3.盘式制动器的故障排查和维修3.1 盘式制动器的常见故障3.2 盘式制动器故障的原因和预防措施3.3 盘式制动器的维修工具和设备3.4 盘式制动器维修的步骤和注意事项4.实践操作4.1 学员轮流进行盘式制动器的拆卸和装配操作4.2 制定实践操作计划,确保学员能够熟练掌握盘式制动器的维修过程4.3 督导学员的实践操作,提供必要的指导和帮助5.安全意识和操作规范5.1 盘式制动器维修中的常见安全隐患5.2 培养学员安全意识的方法和技巧5.3 制定安全操作规范和管理制度,确保学员的安全和项目的顺利进行三、教学方法1.理论授课:通过讲授课件、教材和案例分析等方式,向学员介绍盘式制动器的基本知识和理论框架。
2.实践操作:提供实验室和实际车辆,让学员进行盘式制动器的拆卸和装配操作,培养其实践操作能力。
3.讨论和互动:组织学员进行小组讨论和课堂互动,共同解决问题和加深对盘式制动器的理解。
4.案例分析:通过分析真实的盘式制动器故障案例,让学员掌握故障排查和维修的方法和技巧。
紧凑型轿车盘式制动器设计原理与优化探究
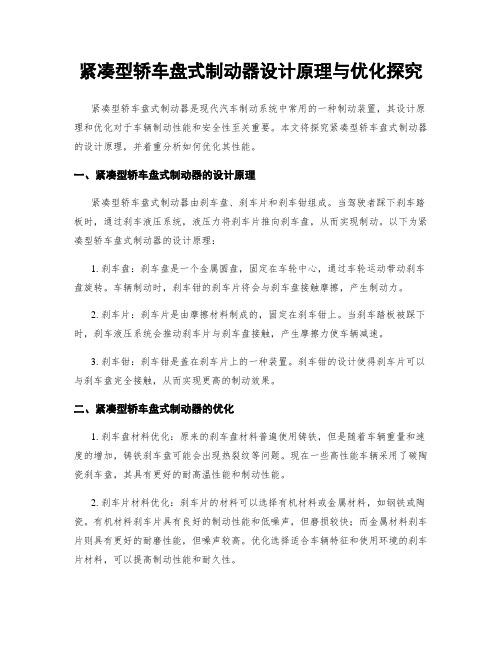
紧凑型轿车盘式制动器设计原理与优化探究紧凑型轿车盘式制动器是现代汽车制动系统中常用的一种制动装置,其设计原理和优化对于车辆制动性能和安全性至关重要。
本文将探究紧凑型轿车盘式制动器的设计原理,并着重分析如何优化其性能。
一、紧凑型轿车盘式制动器的设计原理紧凑型轿车盘式制动器由刹车盘、刹车片和刹车钳组成。
当驾驶者踩下刹车踏板时,通过刹车液压系统,液压力将刹车片推向刹车盘,从而实现制动。
以下为紧凑型轿车盘式制动器的设计原理:1. 刹车盘:刹车盘是一个金属圆盘,固定在车轮中心,通过车轮运动带动刹车盘旋转。
车辆制动时,刹车钳的刹车片将会与刹车盘接触摩擦,产生制动力。
2. 刹车片:刹车片是由摩擦材料制成的,固定在刹车钳上。
当刹车踏板被踩下时,刹车液压系统会推动刹车片与刹车盘接触,产生摩擦力使车辆减速。
3. 刹车钳:刹车钳是盖在刹车片上的一种装置。
刹车钳的设计使得刹车片可以与刹车盘完全接触,从而实现更高的制动效果。
二、紧凑型轿车盘式制动器的优化1. 刹车盘材料优化:原来的刹车盘材料普遍使用铸铁,但是随着车辆重量和速度的增加,铸铁刹车盘可能会出现热裂纹等问题。
现在一些高性能车辆采用了碳陶瓷刹车盘,其具有更好的耐高温性能和制动性能。
2. 刹车片材料优化:刹车片的材料可以选择有机材料或金属材料,如钢铁或陶瓷。
有机材料刹车片具有良好的制动性能和低噪声,但磨损较快;而金属材料刹车片则具有更好的耐磨性能,但噪声较高。
优化选择适合车辆特征和使用环境的刹车片材料,可以提高制动性能和耐久性。
3. 刹车钳结构优化:刹车钳结构的优化可以提高刹车系统的刚性和散热性能。
例如,采用多活塞刹车钳可以提供更均匀的刹车力分布,降低制动不平衡问题。
此外,增加刹车钳的散热设备,如散热片或风道,可以提高刹车系统的散热效果,避免制动衰减或制动失效。
4. 制动液压系统优化:制动液压系统的优化可以提高刹车踏板的感觉和操作性。
例如,采用更灵敏的刹车总泵和辅助助力器可以提高刹车踏板的响应速度和制动力度的调节。
汽车盘式制动系统结构设计

汽车盘式制动系统结构设计引言汽车盘式制动系统是汽车制动系统的一种常见形式,其作用是通过摩擦力产生的阻力来减速或停止车辆。
本文将介绍汽车盘式制动系统的结构设计,并以此为根底讨论其工作原理和常见故障排除方法。
结构设计汽车盘式制动系统主要由以下几个组成局部构成:1.制动盘:制动盘是安装在车轮上的一个圆盘状金属零件,通常由高温耐磨的铁合金制成。
制动盘上有一侧的外表是用来与制动片接触的,通过摩擦产生阻力。
2.制动片:制动片是与制动盘接触的摩擦材料,通常由复合材料制成,其中包含耐磨材料和散热材料。
制动片通过制动系统的控制装置对制动盘施加一定的压力,产生摩擦力以实现制动效果。
3.制动卡钳:制动卡钳是用来夹住制动片的装置,通常安装在制动盘的两侧。
当制动系统被激活时,制动卡钳会施加压力将制动片夹紧到制动盘上,产生足够的摩擦力。
4.制动液:制动液是传递力量的介质,通常由特殊的液体构成。
当制动系统被激活时,制动液被推动到制动卡钳中,使其施加压力到制动盘上,从而产生摩擦力。
工作原理当驾驶员踩下制动踏板时,制动系统的控制装置将力量传递到制动卡钳上。
制动卡钳通过施加压力将制动片夹住制动盘,从而产生摩擦力。
摩擦力将制动盘减速或停止旋转,进而实现车辆的减速或停止。
制动片与制动盘之间的摩擦力会产生热能,在制动过程中,热量需要通过制动盘和制动卡钳散发出去,以防止制动系统过热。
因此,制动盘和制动卡钳通常都会设计有良好的散热结构。
常见故障排除方法在使用过程中,汽车盘式制动系统可能会遇到一些故障,常见的故障及排除方法如下:1.制动片磨损:当制动片磨损到一定程度时,需要及时更换制动片。
定期检查制动片的磨损情况,并根据需要进行更换。
2.制动卡钳故障:制动卡钳可能出现卡钳卡死、卡钳失效等故障,此时需要更换或修复制动卡钳。
定期检查制动卡钳的工作状态,并进行维护和维修。
3.制动液泄漏:制动液泄漏可能导致制动系统失效,需要及时检查泄漏源并修复。
定期检查制动液的液位,以及检查制动管道和接头是否有泄漏。
轿车后轮盘式制动器设计

目录第一章绪论 (1)1.1制动系统的基本概念 (1)1.2 制动系统发展史 (2)1.3 研究方向 (3)1.4 课题主要内容: (3)1.5 课题研究方案: (4)第二章制动器的结构形式选择 (5)2.1 盘式制动器结构形式 (5)2.2 鼓式制动器结构形式简介 (5)2.3 7250型轿车制动器结构的最终确定 (7)第三章制动器主要参数选择 (9)3.1 制动力与制动力分配系数 (9)3.2 同步附着系数 (14)3.3 制动强度和附着系数利用率 (16)3.4 制动器最大制动力矩 (17)3.5 制动器因数 (19)3.6 驻车制动计算 (19)3.7 鼓式制动器主要参数的确定 (21)第四章制动器的设计 (23)4.1 盘式制动器主要参数的确定 (23)4.2 摩擦衬块的磨损特性计算 (24)4.2.1比能量耗散率 (24)4.2.2 比滑磨功 (25)4.3盘式制动器制动力矩的计算 (26)第五章盘中鼓制动器现状与未来 (29)5.1盘式制动器取代鼓式原因 (29)5.2 鼓式制动器现状 (30)5.3 DIH盘中鼓结构设计原因 (30)5.4盘中鼓式制动器未来 (31)5.5 盘中鼓需要发展的方向 (33)第六章制动器主要零部件的结构设计 (34)6.1 制动盘 (34)6.2制动钳 (35)6.3制动块 (35)6.4摩擦材料 (35)6.5制动器间隙的调整方法及相应机构 (36)第七章制动性能分析。
(38)7.1 制动性能评价指标 (38)7.1.1 制动效能 (38)7.1.2 制动效能的恒定性 (39)7.1.3 制动时汽车的方向稳定性 (39)7.2制动器制动力分配曲线分析 (40)参考文献 (42)第一章绪论1.1制动系统的基本概念令正在运行的车辆速度降低以至于停车,或者当进行下坡路段时可以用来稳定车辆的行驶速度,也可以令停在道路上的车保持不动,将能够完成如此相应功能的部件就是我们常说的车辆制动器;在车上装备一系列实现能够完成制动这一个功能装置,以便帮助驾驶员根据交通情况和路况做出相应反应与操作,这些对汽车进行外力可控的装置系统被称为制动系,而实现这功能的外力就是我们说的制动力。
基于性能要求的紧凑型轿车盘式制动器优化设计
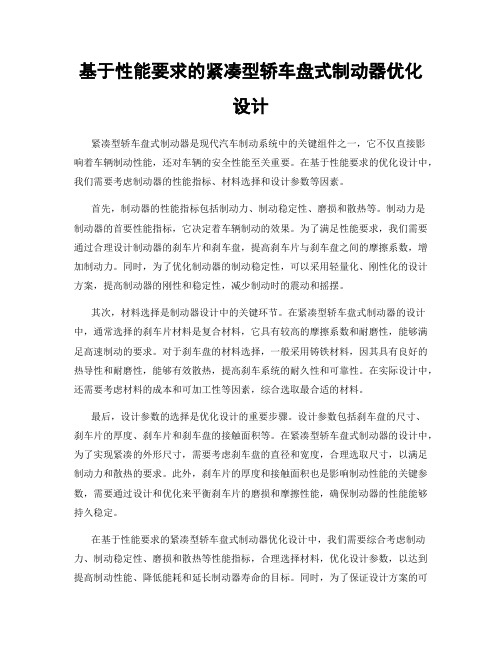
基于性能要求的紧凑型轿车盘式制动器优化设计紧凑型轿车盘式制动器是现代汽车制动系统中的关键组件之一,它不仅直接影响着车辆制动性能,还对车辆的安全性能至关重要。
在基于性能要求的优化设计中,我们需要考虑制动器的性能指标、材料选择和设计参数等因素。
首先,制动器的性能指标包括制动力、制动稳定性、磨损和散热等。
制动力是制动器的首要性能指标,它决定着车辆制动的效果。
为了满足性能要求,我们需要通过合理设计制动器的刹车片和刹车盘,提高刹车片与刹车盘之间的摩擦系数,增加制动力。
同时,为了优化制动器的制动稳定性,可以采用轻量化、刚性化的设计方案,提高制动器的刚性和稳定性,减少制动时的震动和摇摆。
其次,材料选择是制动器设计中的关键环节。
在紧凑型轿车盘式制动器的设计中,通常选择的刹车片材料是复合材料,它具有较高的摩擦系数和耐磨性,能够满足高速制动的要求。
对于刹车盘的材料选择,一般采用铸铁材料,因其具有良好的热导性和耐磨性,能够有效散热,提高刹车系统的耐久性和可靠性。
在实际设计中,还需要考虑材料的成本和可加工性等因素,综合选取最合适的材料。
最后,设计参数的选择是优化设计的重要步骤。
设计参数包括刹车盘的尺寸、刹车片的厚度、刹车片和刹车盘的接触面积等。
在紧凑型轿车盘式制动器的设计中,为了实现紧凑的外形尺寸,需要考虑刹车盘的直径和宽度,合理选取尺寸,以满足制动力和散热的要求。
此外,刹车片的厚度和接触面积也是影响制动性能的关键参数,需要通过设计和优化来平衡刹车片的磨损和摩擦性能,确保制动器的性能能够持久稳定。
在基于性能要求的紧凑型轿车盘式制动器优化设计中,我们需要综合考虑制动力、制动稳定性、磨损和散热等性能指标,合理选择材料,优化设计参数,以达到提高制动性能、降低能耗和延长制动器寿命的目标。
同时,为了保证设计方案的可行性和稳定性,我们还可以借助仿真模拟和实验验证等手段,对设计方案进行评估和优化,确保最终设计满足性能要求,提高紧凑型轿车的制动系统性能和安全性能。
紧凑型轿车盘式制动器设计原理与优化

紧凑型轿车盘式制动器设计原理与优化紧凑型轿车盘式制动器是一种重要的汽车制动装置,用于实现车辆的安全停车和减速。
它由制动盘、刹车片、刹车钳、制动油管等组成。
在制动过程中,制动器通过摩擦力将车轮减速或停止,确保车辆能够安全驾驶。
在紧凑型轿车盘式制动器的设计中,需要考虑以下几个关键方面:刹车片材料选择、刹车盘的设计、刹车钳的结构和制动油路。
首先,刹车片材料的选择对制动器的性能起着重要作用。
常见的刹车片材料有有机材料、半金属材料和陶瓷材料。
有机材料制动片具有制动效果好、噪音低的特点,但抗磨削性不高;半金属材料制动片抗磨削性能较强,但制动效果和噪音控制较差;陶瓷材料制动片具有良好的制动性能和噪音控制,但成本较高。
设计师需要根据车辆的使用情况、制动性能要求和成本等因素选择合适的刹车片材料。
其次,刹车盘的设计对制动器的性能也具有重要影响。
刹车盘的材料通常选择铸铁或复合材料。
铸铁刹车盘价格低廉,具有良好的散热性能,但易生锈和产生裂纹;复合材料刹车盘重量轻,使用寿命长,但成本较高。
在设计中,需要权衡这些因素,选择切合实际的刹车盘材料和结构。
第三,刹车钳的结构设计也是紧凑型轿车盘式制动器的重要组成部分。
刹车钳通常采用螺栓式或活塞式结构。
螺栓式刹车钳结构简单、重量轻,但制动力分配不均匀;活塞式刹车钳结构复杂,但能够更好地实现制动力的均衡分配。
设计师需要根据实际情况选择合适的刹车钳结构,并进行细致的参数优化。
最后,制动油路的设计为紧凑型轿车盘式制动器的正常运行提供了保障。
制动油路需要确保刹车片与刹车盘之间的摩擦力能够得到准确地传递,并且刹车油在高温高压环境下不易泄漏。
合适的油管材料和密封件是实现这一目标的重要因素,设计师需要选择耐高温高压的材料,并保证油路的紧密性。
在以上各个方面的设计中,还可以通过模拟仿真和实验验证来进行综合优化。
模拟仿真可以通过建立切实可行的数学模型,对各个参数进行优化,以获得最佳的设计方案。
实验验证可以通过在真实道路环境下进行刹车性能测试,评估设计方案的可靠性和可行性。
盘式制动器设计计算
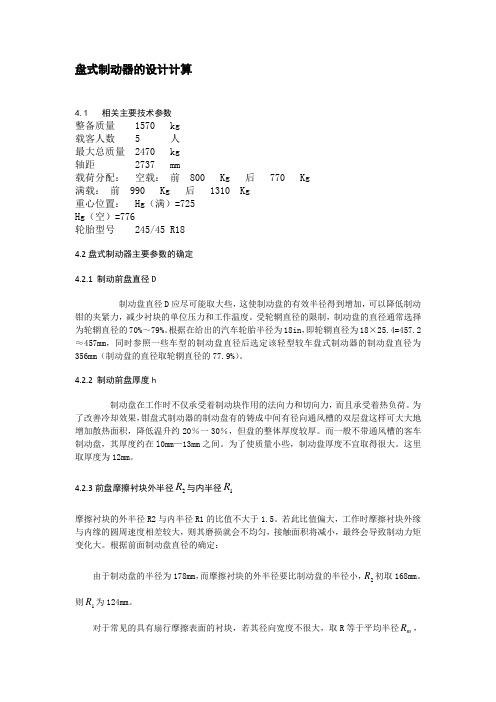
盘式制动器的设计计算4.1相关主要技术参数整备质量 1570 kg载客人数 5 人最大总质量 2470 kg轴距 2737 mm载荷分配:空载:前 800 Kg 后 770 Kg满载:前 990 Kg 后 1310 Kg重心位置: Hg(满)=725Hg(空)=776轮胎型号 245/45 R184.2盘式制动器主要参数的确定4.2.1制动前盘直径D制动盘直径D应尽可能取大些,这使制动盘的有效半径得到增加,可以降低制动钳的夹紧力,减少衬块的单位压力和工作温度。
受轮辋直径的限制,制动盘的直径通常选择为轮辋直径的70%~79%。
根据在给出的汽车轮胎半径为18in,即轮辋直径为18×25.4=457.2≈457mm,同时参照一些车型的制动盘直径后选定该轻型较车盘式制动器的制动盘直径为356mm(制动盘的直径取轮辋直径的77.9%)。
4.2.2制动前盘厚度h制动盘在工作时不仅承受着制动块作用的法向力和切向力,而且承受着热负荷。
为了改善冷却效果,钳盘式制动器的制动盘有的铸成中间有径向通风槽的双层盘这样可大大地增加散热面积,降低温升约20%一30%,但盘的整体厚度较厚。
而一般不带通风槽的客车制动盘,其厚度约在l0mm—13mm之间。
为了使质量小些,制动盘厚度不宜取得很大。
这里取厚度为12mm。
4.2.3前盘摩擦衬块外半径2R与内半径1R摩擦衬块的外半径R2与内半径R1的比值不大于1.5。
若此比值偏大,工作时摩擦衬块外缘与内缘的圆周速度相差较大,则其磨损就会不均匀,接触面积将减小,最终会导致制动力矩变化大。
根据前面制动盘直径的确定:R初取168mm。
由于制动盘的半径为178mm,而摩擦衬块的外半径要比制动盘的半径小,2R为124mm。
则1R,对于常见的具有扇行摩擦表面的衬块,若其径向宽度不很大,取R等于平均半径m同时也等于有效半径e R ,而平均半径mm R R R m 146221=+= 而式中1R 、2R 也就是摩擦衬块的内外半径,即mm R R 29221=+ 擦衬块的有效半径文献[3]R e =()()mm R R R R 14712848*32835008*2*3*221223132==-- (4—1)与平均半径R m =146mm 的值相差不大,且满足m=738.016812421==R R <1,()()4124.0738.1738.0122<==+m m 的要求, 所以取R=146mm 。
- 1、下载文档前请自行甄别文档内容的完整性,平台不提供额外的编辑、内容补充、找答案等附加服务。
- 2、"仅部分预览"的文档,不可在线预览部分如存在完整性等问题,可反馈申请退款(可完整预览的文档不适用该条件!)。
- 3、如文档侵犯您的权益,请联系客服反馈,我们会尽快为您处理(人工客服工作时间:9:00-18:30)。
1 机械工程学院毕业设计 题目:汽车盘式制动器设计 专业:车辆工程 班级: 姓名: 学号: 指导教师: 日期: 2016.5.26 2
目录 摘 要 ........................................................................................................................................ 3 前言 .......................................................................................................................................... 3 1绪论 ....................................................................................................................................... 4 1.1 制动系统设计的意义 ............................................................................................... 4 1.2 本次制动系统应达到的目标 ................................................................................... 4 2制动系统方案论证分析与选择 ........................................................................................... 4 2.1 盘式制动器 ........................................................................................................ 5 2.2 简单制动系 ........................................................................................................ 5 2.3 动力制动系 ........................................................................................................ 5 2.4 伺服制动系 ........................................................................................................ 6 2.5 液压分路系统的形式的选择 ................................................................................... 6 2.6 液压制动主缸的设计方案 ........................................................................................ 6 3盘式制动器概述 ................................................................................................................... 8 3.1制动盘 ................................................................................................................. 8 3.2制动摩擦衬块 ..................................................................................................... 9 3.3 盘式制动器操纵机构 ............................................................................................... 9 4制动系统设计计算 ............................................................................................................. 10 4.1 相关主要参数 .................................................................................................. 10 4.2 同步附着系数的分析 ...................................................................................... 11 4.3 分析计算法向作用力 ...................................................................................... 11
4.4 制动力矩分配系数的选取和计算 .............................................................. 12 4.5 制动器制动力矩的确定 .................................................................................. 12 4.6 盘式制动器主要参数确定 .............................................................................. 13 4.7 盘式制动器的制动力计算 .............................................................................. 15 4.8 制动器主要零部件的结构设计 ............................................................................. 16 5液压制动驱动机构的设计计算 ......................................................................................... 17 5.1 前轮制动轮缸直径d的确定 ................................................................................. 17 5.2 制动主缸直径0d的确定 ........................................................................................ 17
5.3 制动踏板力pF和制动踏板工作行程pS ............................................................... 18 第6章制动性能分析 ............................................................................................................ 19 6.1 制动性能评价指标 ................................................................................................. 20 6.2 制动效能 ................................................................................................................. 20 6.3 制动效能的恒定性 ................................................................................................. 20 6.4 制动时汽车方向的稳定性 ..................................................................................... 20 6.5 制动器制动力分配曲线分析 ................................................................................. 21
6 .6制动减速度j和制动距离。 ..................................................................................... 22 6.7 摩擦衬块的磨损特性计算 ..................................................................................... 22 7总结 ..................................................................................................................................... 24 参考文献 ................................................................................................................................ 25 致谢 ........................................................................................................................................ 25