汽车液压盘式制动器设计研究
汽车盘式制动器及其液压驱动机构的分析
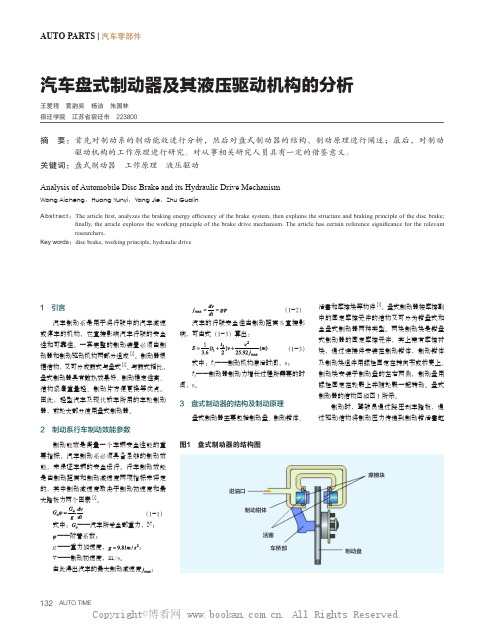
1 引言
汽车制动系是用于将行驶中的汽车减速 或停车的机构,它直接影响汽车行驶的安全 性和可靠性。一套完整的制动装置必须由制 动器和制动驱动机构两部分组成 [1]。制动器根 据结构,又可分成鼓式与盘式 [2]。与鼓式相比, 盘式制动器具有散热效果好、制动稳定性高、 结构紧凑重量轻、制动片方便更换等优点。 因此,轻型汽车及现代轿车所用的车轮制动 器,前轮大部分使用盘式制动器。
[J]. 农业开发与装备,2017(5),68-70. [3] 张雪文 . 浅析汽车盘式制动器设计 [J]. 时代
农机,2018,45(5),195-196.
AUTO TIME 133
Copyright©博看网 . All Rights Reserved.
关键词:盘式制动器 工作原理 液压驱动
Analysis of Automobile Disc Brake and its Hydraulic Drive Mechanism
Wang Aicheng,Huang Yunyi,Yang Jie,Zhu Guolin A b s t r a c t :The article first, analyzes the braking energy efficiency of the brake system, then explains the structure and braking principle of the disc brake;
制动时,驾驶员通过踩压刹车踏板,通 过驱动结构将制动压力传递到制动钳活塞缸
摩擦块
制动盘
132 AUTO TIME
Copyright©博看网 . All Rights Reserved.
图2 液压制动系示意图
2
3
面向紧凑型轿车的盘式制动器设计与优化研究
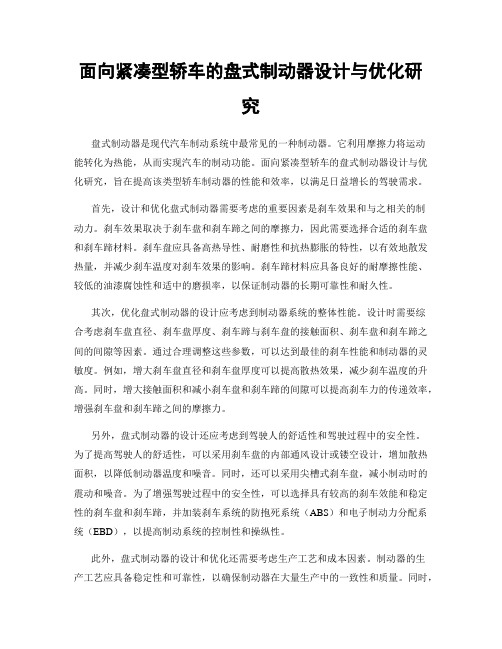
面向紧凑型轿车的盘式制动器设计与优化研究盘式制动器是现代汽车制动系统中最常见的一种制动器。
它利用摩擦力将运动能转化为热能,从而实现汽车的制动功能。
面向紧凑型轿车的盘式制动器设计与优化研究,旨在提高该类型轿车制动器的性能和效率,以满足日益增长的驾驶需求。
首先,设计和优化盘式制动器需要考虑的重要因素是刹车效果和与之相关的制动力。
刹车效果取决于刹车盘和刹车蹄之间的摩擦力,因此需要选择合适的刹车盘和刹车蹄材料。
刹车盘应具备高热导性、耐磨性和抗热膨胀的特性,以有效地散发热量,并减少刹车温度对刹车效果的影响。
刹车蹄材料应具备良好的耐摩擦性能、较低的油漆腐蚀性和适中的磨损率,以保证制动器的长期可靠性和耐久性。
其次,优化盘式制动器的设计应考虑到制动器系统的整体性能。
设计时需要综合考虑刹车盘直径、刹车盘厚度、刹车蹄与刹车盘的接触面积、刹车盘和刹车蹄之间的间隙等因素。
通过合理调整这些参数,可以达到最佳的刹车性能和制动器的灵敏度。
例如,增大刹车盘直径和刹车盘厚度可以提高散热效果,减少刹车温度的升高。
同时,增大接触面积和减小刹车盘和刹车蹄的间隙可以提高刹车力的传递效率,增强刹车盘和刹车蹄之间的摩擦力。
另外,盘式制动器的设计还应考虑到驾驶人的舒适性和驾驶过程中的安全性。
为了提高驾驶人的舒适性,可以采用刹车盘的内部通风设计或镂空设计,增加散热面积,以降低制动器温度和噪音。
同时,还可以采用尖槽式刹车盘,减小制动时的震动和噪音。
为了增强驾驶过程中的安全性,可以选择具有较高的刹车效能和稳定性的刹车盘和刹车蹄,并加装刹车系统的防抱死系统(ABS)和电子制动力分配系统(EBD),以提高制动系统的控制性和操纵性。
此外,盘式制动器的设计和优化还需要考虑生产工艺和成本因素。
制动器的生产工艺应具备稳定性和可靠性,以确保制动器在大量生产中的一致性和质量。
同时,制动器的成本也是设计中需要考虑的重要因素。
不同的刹车盘材料和制造工艺,以及不同的刹车蹄结构和材料,都会影响制动器的成本。
紧凑型轿车盘式制动器设计优化方案探究
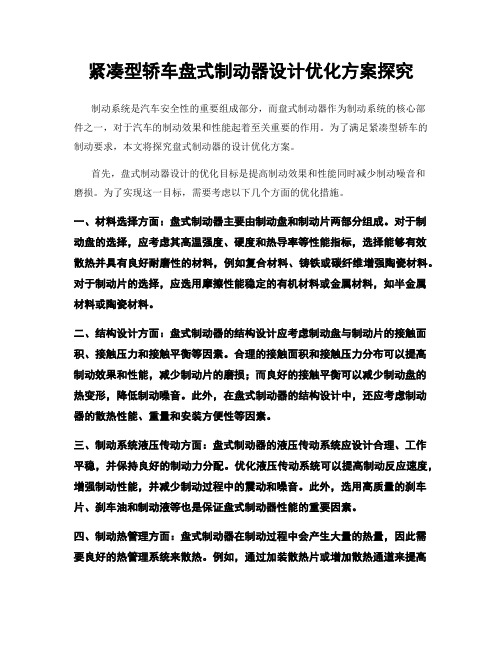
紧凑型轿车盘式制动器设计优化方案探究制动系统是汽车安全性的重要组成部分,而盘式制动器作为制动系统的核心部件之一,对于汽车的制动效果和性能起着至关重要的作用。
为了满足紧凑型轿车的制动要求,本文将探究盘式制动器的设计优化方案。
首先,盘式制动器设计的优化目标是提高制动效果和性能同时减少制动噪音和磨损。
为了实现这一目标,需要考虑以下几个方面的优化措施。
一、材料选择方面:盘式制动器主要由制动盘和制动片两部分组成。
对于制动盘的选择,应考虑其高温强度、硬度和热导率等性能指标,选择能够有效散热并具有良好耐磨性的材料,例如复合材料、铸铁或碳纤维增强陶瓷材料。
对于制动片的选择,应选用摩擦性能稳定的有机材料或金属材料,如半金属材料或陶瓷材料。
二、结构设计方面:盘式制动器的结构设计应考虑制动盘与制动片的接触面积、接触压力和接触平衡等因素。
合理的接触面积和接触压力分布可以提高制动效果和性能,减少制动片的磨损;而良好的接触平衡可以减少制动盘的热变形,降低制动噪音。
此外,在盘式制动器的结构设计中,还应考虑制动器的散热性能、重量和安装方便性等因素。
三、制动系统液压传动方面:盘式制动器的液压传动系统应设计合理、工作平稳,并保持良好的制动力分配。
优化液压传动系统可以提高制动反应速度,增强制动性能,并减少制动过程中的震动和噪音。
此外,选用高质量的刹车片、刹车油和制动液等也是保证盘式制动器性能的重要因素。
四、制动热管理方面:盘式制动器在制动过程中会产生大量的热量,因此需要良好的热管理系统来散热。
例如,通过加装散热片或增加散热通道来提高散热效果;同时,合理选择制动盘和制动片的材料,以提高其耐热性能,减少热膨胀和热衰减对制动性能的影响。
综上所述,紧凑型轿车盘式制动器的设计优化方案涉及材料选择、结构设计、液压传动和热管理等多个方面。
通过合理选择材料、改善结构设计、优化液压传动系统和加强热管理,可以提高制动效果和性能,减少制动噪音和磨损,进而提高紧凑型轿车的整体安全性和驾驶体验。
紧凑型轿车盘式制动器设计原理与优化探究
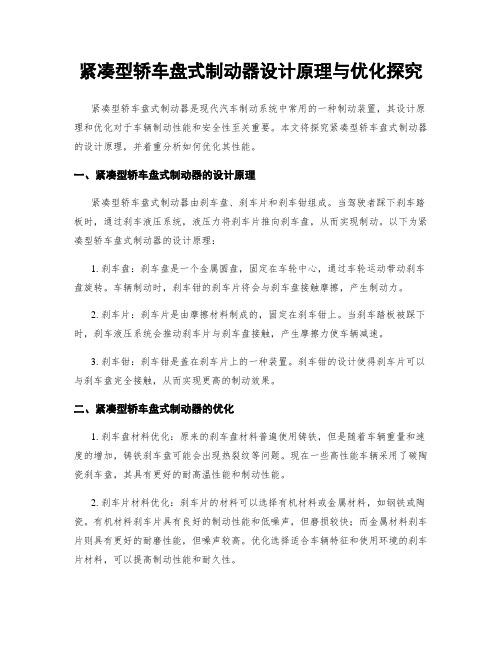
紧凑型轿车盘式制动器设计原理与优化探究紧凑型轿车盘式制动器是现代汽车制动系统中常用的一种制动装置,其设计原理和优化对于车辆制动性能和安全性至关重要。
本文将探究紧凑型轿车盘式制动器的设计原理,并着重分析如何优化其性能。
一、紧凑型轿车盘式制动器的设计原理紧凑型轿车盘式制动器由刹车盘、刹车片和刹车钳组成。
当驾驶者踩下刹车踏板时,通过刹车液压系统,液压力将刹车片推向刹车盘,从而实现制动。
以下为紧凑型轿车盘式制动器的设计原理:1. 刹车盘:刹车盘是一个金属圆盘,固定在车轮中心,通过车轮运动带动刹车盘旋转。
车辆制动时,刹车钳的刹车片将会与刹车盘接触摩擦,产生制动力。
2. 刹车片:刹车片是由摩擦材料制成的,固定在刹车钳上。
当刹车踏板被踩下时,刹车液压系统会推动刹车片与刹车盘接触,产生摩擦力使车辆减速。
3. 刹车钳:刹车钳是盖在刹车片上的一种装置。
刹车钳的设计使得刹车片可以与刹车盘完全接触,从而实现更高的制动效果。
二、紧凑型轿车盘式制动器的优化1. 刹车盘材料优化:原来的刹车盘材料普遍使用铸铁,但是随着车辆重量和速度的增加,铸铁刹车盘可能会出现热裂纹等问题。
现在一些高性能车辆采用了碳陶瓷刹车盘,其具有更好的耐高温性能和制动性能。
2. 刹车片材料优化:刹车片的材料可以选择有机材料或金属材料,如钢铁或陶瓷。
有机材料刹车片具有良好的制动性能和低噪声,但磨损较快;而金属材料刹车片则具有更好的耐磨性能,但噪声较高。
优化选择适合车辆特征和使用环境的刹车片材料,可以提高制动性能和耐久性。
3. 刹车钳结构优化:刹车钳结构的优化可以提高刹车系统的刚性和散热性能。
例如,采用多活塞刹车钳可以提供更均匀的刹车力分布,降低制动不平衡问题。
此外,增加刹车钳的散热设备,如散热片或风道,可以提高刹车系统的散热效果,避免制动衰减或制动失效。
4. 制动液压系统优化:制动液压系统的优化可以提高刹车踏板的感觉和操作性。
例如,采用更灵敏的刹车总泵和辅助助力器可以提高刹车踏板的响应速度和制动力度的调节。
液压盘式制动器驻车机构的研究
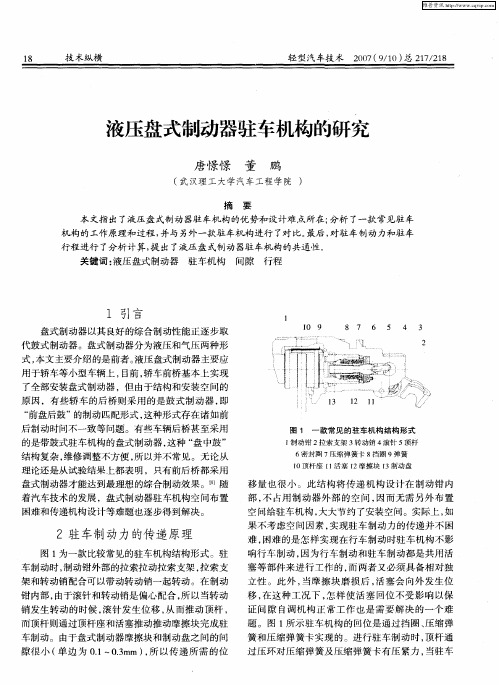
隙很小 ( 单边 为 0 0 m , 以传递所需 的位 . . m) 所 1 3
过 压 环对 压 缩 弹簧 及压 缩 弹簧 卡有 压 紧力 , 当驻 车
维普资讯
轻 型 汽车技 术
2 0 ( / 0 总 2 72 8 07 91 ) 1 / 1
技 术纵横
用 液压 或气压 驱 动 以避 免其 产生 故 障。表 1中所列 出的是 应用 于 图 1中驻 车 机构 车辆 的相关 参数
表 1 驻 车 机 构 应 用 车 辆 的 参 数表
项 目 数值 /单位 15 k 90 g 11 m 2m 3% 0
之 间 的间隙 ,顶 杆座会 相对 于顶 杆发生 旋 转位 移从 而影 响 了活 塞 的 正 常 回 位 。 杆 是 一 个 关 键 部 件 , 顶 因为它起 着承 上启 下 的作用 ,它 头部 的球 窝十 分重
6密封圈 7压缩弹簧卡 8挡圈 9弹簧
1 o顶杆 座 1 活 塞 1 擦 块 1 动 盘 1 2摩 3制
移 量 也很 小 。此 结 构 将 传 递 机 构设 计 在 制 动 钳 内 部 , 占用 制 动 器 外部 的 空 间 , 不 因而 无需 另外 布 置
空 间给驻 车机构 , 大节约 了安装 空 间 。实际上 , 大 如 果不 考 虑 空 间因素 , 实现驻 车 制 动力 的传 递
2驻车制动力 的传递原理
图 1 一款 比较 常见 的驻车机 构结 构形 式 。驻 为
车制 动时 , 动钳 外部 的拉 索拉动拉 索 支架 , 索支 制 拉
难, 困难 的 是怎 样 实现 在行 车 制 动时驻 车 机 构不 影 响行 车制 动 , 因为行 车 制动 和 驻车 制动 都 是共 用 活 塞等 部件 来 进行 工 作 的 , 两 者又 必须 具 备相 对 独 而
轿车盘式制动器设计及分析

关于?轿车盘式制动器的设计与分析?的开题报告062109233 陈文镇1.课题目的和意义近年来,随着车辆技术的进步和汽车行驶速度的提高,车辆制动器在车辆的平安方面表现得越来越明显。
目前汽车制动器主要分为鼓式和盘式两种,按照制动系统构造型式主要有机械式、气动式、液压式、气—液混合式。
它们的工作原理根本都一样,都是利用制动装置,用工作时产生的摩擦热来逐渐消耗车辆所具有的动能,以到达车辆制动减速,或直至停车的目的。
鼓式制动器是最早形式的汽车制动器,当盘式制动器还没有出现前,它已经广泛用于各类汽车上。
其刹车鼓的设计1902年就已经使用在马车上了,直到1920年左右才开场在汽车工业广泛应用。
然而随着汽车速度的提高和对制动性能的要求越来越高,现代乘用车的车轮除了使用铝合金车圈来降低运行温度外,还倾向于采用综合性能较好的盘式制动器。
盘式制动器逐渐开场取代了鼓式制动器在汽车上应用。
因此设计一个性能稳定同时平安可靠地盘式制动器很重要,并且通过盘式制动器设计计算,有助于初步掌握汽车新产品的开发与设计的方法,培养了汽车零部件的设计能力,提高了综合运用所学知识解决实际问题的能力,具有十分重要的意义。
2.国内开展现状随着我国汽车工业技术的开展,特别是轿车工业的开展,合资企业的引进,国外先进技术的进入,汽车上采应用盘式制动器配置才逐步在我国形成规模。
特别是在提高整车性能、保障平安、提高乘车者的舒适性,满足人们不断提高的生活物质需求、改善生活环境等方面都发挥了很大的作用。
在轿车、微型车、轻卡、SUV及皮卡方面:在从经济与实用的角度出发,一般采用了混合的制动形式,即前车轮盘式制动,后车轮鼓式制动。
因轿车在制动过程中,由于惯性的作用,前轮的负荷通常占汽车全部负荷的70%-80%,所以前轮制动力要比后轮大。
生产厂家为了节省本钱,就采用了前轮盘式制动,后轮鼓式制动的混合制动方式。
采用前盘后鼓式混合制动器,这主要是出于本钱上的考虑,同时也是因为汽车在紧急制动时,轴荷前移,对前轮制动性能的要求比拟高,这类前制动器主要以液压盘式制动器为主流,采用液压油作传输介质,以液压总泵为动力源,后制动器以液压式双泵双作用缸制动蹄匹配。
液压盘式刹车系统制动钳制动力矩的设计分析
液压盘式刹车系统制动钳制动力矩的设计分析摘要:起重设备盘式刹车由于具有制动力矩可调性好、操作惯性小、动作灵敏、易实现自动控制、使用维护方便等优点,在绞车制动系统中具有广阔的应用前景。
盘式刹车主要采用液压系统进行操作和控制,其液压系统性能好坏直接影响到盘式刹车的工作性能。
关键词:液压盘式刹车系统制动钳制动力矩;设计;液压钳盘式制动器的液压系统是制动器的动力中枢,所以,液压钳盘式制动器液压系统的开发设计对于提高制动系统的性能有重要意义。
一、特点1.制动钳结构:制动钳有固定钳式、浮动钳式、整体钳式和分体钳式。
固定钳式与浮动钳式比, 前者易于保证两侧制动衬垫退距相等, 易于实现制动衬垫磨损的自动补偿, 但后者的轴向尺寸较小。
运输绞车上制动钳的安装空间不成问题,因此采用了固定钳式。
整体钳式与分体钳式相比较, 前者刚性更好些, 但轴向尺寸较大, 结构也稍复杂,最后(运输绞车)制动钳设计为半分体式,两侧螺栓连接。
另外, 制动钳上设有销轴, 由它们来承受作用在制动衬垫上的摩擦力, 改善了增压缸的工作条件。
2.制动衬垫磨损自动补偿装置:磨损自动补偿机构有密封式、机械摩擦式、机械进给式等。
其中机械摩擦式具有结构紧凑、性能稳定、无级补偿等优点, 为常开式液压钳盘制动器所常用。
但存在制造精度要求高、调整和维护不便、制动衬垫稳定退距不能调整等缺点。
而运输绞车中研制的摩擦式补偿装置克服了上述不足。
3.制动液压回路的补油结构:目前同类型制动器的补油主要是通过制动液压缸密封皮碗的变形实现, 而且每次制动时密封皮碗都要稳定通过一个小孔, 这影响了皮碗的密封性能和工作寿命。
而运输绞车中制动液压回路的补油是通过一个特殊阀来实现的, 从而提高了密封圈的密封性能和工作寿命。
该结构构造简单, 性能稳定可靠, 工作寿命长。
4.油源采用两台泵并联布置,一台运转,一台备用。
一旦运转的泵出现故障,备用泵立即起动, 保证系统供油不受影响。
两台泵分别采用不同的驱动方式,一台采用电机驱动,一台采用气马达驱动. 若电路出现故障,可用气马达驱动备用油泵,向系统供油,进一步提高了系统的可靠性。
紧凑型轿车盘式制动器优化设计方案研究
紧凑型轿车盘式制动器优化设计方案研究引言:随着汽车工业的发展,紧凑型轿车在市场上的需求与日俱增。
为了满足消费者对安全性能和驾驶舒适性的要求,盘式制动器的设计方案变得尤为重要。
本文将研究紧凑型轿车盘式制动器优化设计方案,通过对设计参数的优化和材料的选择,提高制动器的性能和可靠性。
一、制动器的工作原理和发展趋势1. 制动器的工作原理:盘式制动器通过制动盘和制动片的摩擦力来减速车辆。
2. 制动器的发展趋势:随着车辆速度的提高和制动性能要求的增加,制动器的发展趋势主要包括以下几个方面:a. 提高制动器的制动力和散热性能;b. 减小制动器的尺寸和重量;c. 降低制动噪音和振动。
二、紧凑型轿车盘式制动器设计参数的优化紧凑型轿车盘式制动器的设计参数优化可以从以下几个方面进行研究:1. 制动片材料的选择:a. 优化制动片材料的摩擦系数和稳定性,以提高制动效果;b. 选择具有良好散热性和耐磨性的制动片材料,延长制动器的使用寿命。
2. 制动盘的设计和优化:a. 选择适当的制动盘材料,提高制动盘的强度和刚度;b. 优化制动盘的散热效果,降低制动盘的温度;c. 通过减少制动盘的质量和减小制动盘直径,降低制动器的重量。
3. 制动器液压系统的设计:a. 优化制动系统的液压传动比和制动启动压力,提高制动力的实时可调性;b. 选择高效的液压制动泵和制动器液压油,提高制动系统的快速响应性能。
4. 制动片和制动盘的接触过程模拟:a. 借助计算机仿真软件,对制动片和制动盘的接触过程进行模拟和分析;b. 通过优化制动片和制动盘的表面形状和接触压力分布,提高制动器的摩擦效果和制动性能。
三、制动器的性能测试和评估为了验证优化设计方案的效果,需要进行制动器的性能测试和评估。
测试项目包括:1. 制动力和制动距离的测试;2. 制动噪音和振动的测试;3. 制动器的散热性能测试。
测试结果将用于评估设计方案的有效性,并指导后续的改进和优化。
结论:通过对紧凑型轿车盘式制动器的优化设计方案的研究,可以提高制动器的性能和可靠性。
盘式制动器毕业设计
盘式制动器毕业设计一、选题背景盘式制动器是现代汽车制动系统中最常用的一种制动器,其优点包括制动效果好、散热能力强、使用寿命长等。
因此,本人选择盘式制动器作为毕业设计的研究对象。
二、研究目的本次毕业设计旨在通过对盘式制动器的设计和分析,掌握盘式制动器的工作原理和设计方法,并进一步提高自己的工程实践能力。
三、研究内容1. 盘式制动器原理分析通过对盘式制动器的结构和工作原理进行分析,了解盘式制动器的基本工作原理和特点。
2. 盘式制动器设计要点根据盘式制动器的工作原理和特点,探讨盘式制动器设计中需要考虑的因素,包括材料选择、摩擦系数计算、刹车片形状等。
3. 盘式制动器性能测试与优化通过对已经设计好的盘式制动器进行性能测试,了解其刹车效果和散热情况,并根据测试结果进行优化。
四、研究方法1. 理论分析法:通过文献资料和相关标准,了解盘式制动器的基本原理和设计要点。
2. 数值模拟法:通过使用有限元分析软件对盘式制动器进行模拟分析,了解其在不同工况下的受力情况和散热情况。
3. 实验测试法:通过对已经设计好的盘式制动器进行实验测试,了解其刹车效果和散热情况,并根据测试结果进行优化。
五、研究成果1. 盘式制动器设计图纸和材料清单根据所学知识和研究结果,完成盘式制动器的设计图纸,并列出所需材料清单。
2. 盘式制动器性能测试报告根据实验测试结果,撰写盘式制动器性能测试报告,包括刹车效果、散热情况等方面的数据分析和优化建议。
3. 相关论文发表将研究成果整理成论文,并提交相关期刊或会议进行发表。
六、进度安排1. 第一阶段(1周):文献资料查找和整理。
2. 第二阶段(2周):盘式制动器原理分析。
3. 第三阶段(3周):盘式制动器设计要点探讨。
4. 第四阶段(4周):盘式制动器数值模拟分析。
5. 第五阶段(5周):盘式制动器实验测试和性能优化。
6. 第六阶段(2周):论文撰写和修改。
七、预期效果通过本次毕业设计,我将深入了解盘式制动器的工作原理和设计方法,掌握有限元分析软件的使用技巧,提高自己的工程实践能力。
毕业论文盘式制动器的参数化设计
前言 (2)1 制动系概述 (3)1.1 制动系的功能 (3)1.2车轮制动时的工作原理 (3)1.3 制动系的要求 (4)1.4 车轮制动器类型 (4)置等组成。
(4)③鼓式制动器的带式制动器只用作中央制动器。
(5)1.5 盘式制动器 (5)加速通风散热提高制动效率。
(5)1.5.2盘式制动器的主要类型 (6)( 1 ) 固定钳式盘式制动器 (6)( 2 ) 浮动钳式盘式制动器 (7)( 3 ) 全盘式制动器 (7)1.5.3盘式制动器的优缺点 (8)( 1 )盘式制动器的优点 (8)2 基于Pro/E设计方法 (11)3 制动器参数化设计计算 (14)3.2 主要零部件的结构设计 (15)3.2.1制动盘 (15)图3.2 制动盘尺寸 (17)(2)参数输入 (17)3.2.2制动块 (18)(1)尺寸设计 (18)(2)参数输入 (19)结论 (27)致谢 (28)参考文献 (28)前言国内汽车市场迅速发展,随着汽车保有量的增加,带来的安全问题也越来越引起人们的注意,而制动系统则是汽车主动安全的重要系统之一。
因此,如何开发出高性能的制动系统,为安全行驶提供保障是我们要解决的主要问题。
另外,随着汽车市场竞争的加剧,如何缩短产品开发周期,提高设计效率,降低成本,提高产品的市场竞争力,已经成为企业成功的关键。
制动器是车辆的关键部件之一, 其性能的好坏直接影响整车性能的优劣, 因此, 制动器的设计在整车设计中显得相当重要。
本文详细地阐述了各类制动器的结构、工作原理、优缺点和发展前景,探讨了一种结构简单的盘式制动器。
对制动器的主要零件如制动盘、制动钳、制动块、摩擦衬片、活塞等进行了结构设计和计算,从而设计出一种比较精确的制动器。
根据设计与计算用Pro/E绘制出了该制动器的制动盘、制动钳、活塞、摩擦衬块等零件图和装配图。
本课题主要完成基于Pro/E三维造型技术进行盘式制动器参数化设计。
通过引入基于Pro/E特征的参数化造型思想,建立制动器典型的零部件模板库,模型设计计算完成后,通过参数化驱动从而得到所需的制动器模型。
- 1、下载文档前请自行甄别文档内容的完整性,平台不提供额外的编辑、内容补充、找答案等附加服务。
- 2、"仅部分预览"的文档,不可在线预览部分如存在完整性等问题,可反馈申请退款(可完整预览的文档不适用该条件!)。
- 3、如文档侵犯您的权益,请联系客服反馈,我们会尽快为您处理(人工客服工作时间:9:00-18:30)。
2009年第10期科技经济市场1汽车工业的发展在人类历史发展的过程中,“衣”、“食”、“住”、“行”始终是人类生存的四大需要,是人类发展、进步的最重要的基本条件。
而在“四大需要”中,“行”或“交通”的变化,在人类社会发展过程中是最突出的,它对社会进步的影响也是最大的。
汽车是作为一种交通工具而产生的,但发展到今天已经不能把它理解为单纯的“行”的手段。
因为“汽车化”改变了当代世界的面貌,它已经成为当代物质文明与进步象征及文明形态的一种代表。
中国汽车工业的振兴也必然会使中国的面貌焕然一新,在繁荣经济,促进四个现代化的实现,提高中国人民的生活水平,推动社会与地球上近四分之一的人类进步方面,发挥巨大的作用。
2汽车零部件的工业现状及水平在汽车行驶过程中,其零部件承受的载荷的大小和性质受着许多因素的影响。
汽车的可靠性与在其使用期间作用在其零部件上的实际载荷有关。
由于汽车的使用条件非常复杂,时间也不固定,有影响且变化的因素很多,致使在零件中的应力值会在很大的范围内变动,甚至应力性质也会改变。
因此,确定汽车零部件所承受的实际载荷要比确定其他机械产品的载荷复杂很多。
而引起零件产生应力的力有些是恒定的(例如重力、零件装配时产生的预紧力或过盈力),有些是不定的(例如汽车起步时和制动时产生的力,零件制造误差引起的力,发动机工作工况改变而引起转矩及力的改变,行驶阻力引起的力等等)。
在设计中为了校核零件的静强度,首先就要确定其危险断面及其所承受的最大载荷;为了校核零件的疲劳强度,除了可按相关文献给出的计算方法进行疲劳强度的计算校核外,还常常以其实测的载荷谱为基础编制加载语并按加载谱的加载程序加载,在疲劳试验台上进行试验验证。
可见,在设计中为了进行零部件的强度设计,首先要弄清其载荷工况、破坏机理,以便采取相应的强度计算方法进行有效的设计。
3汽车设计技术的发展汽车设计技术在近百年中也经历了由经验设计发展到以科学实验和技术分析为基础的设计阶段,进而自60年代中期在设计中引入电子计算机后又形成了计算机辅助设计(CAD)等新方法,并使设计逐步实现半自动化和自动化。
参阅相关权威资料了解到汽车设计的直接目的有以下三点:(1)提高汽车的技术水平,使其承载能力更强,使用性能更好,更安全,更可靠,更经济,更舒适,更机动,更方便,动力性更好,污染更少;(2)改善汽车的外观造型,特别对轿车来讲改善车身艺术效果,使其更美观、更科学、更新颖、更有时代感,往往是车型设计的重要目的,也是提高市场竞争力的重要手段;(3)改善汽车的经济效果,调整汽车在产品系列中的档次,以便改善其市场竞争地位并获得更大的经济效益。
电子计算机的出现和在工程设计中的推广应用,使汽车设计技术飞跃发展,设计过程完全改观。
汽车结构参数及性能参数等的优化选择与匹配、零部件的强度核算与寿命预测、产品有关方面的模拟计算或仿真分析、车身的美工造型等等设计方案的选择及定型、设计图纸的绘制,均可在计算机上进行。
4盘式制动器设计、计算分析模块4.1概述在轿车和中小型客车的设计中,一般其结构形式为前轮制动器采用浮钳式制动器,后轮制动器采用领从蹄自动定义浮销式鼓式制动器。
而对总重大于20KN-40KN 的客车而言,前轮也有采用固定钳式盘式制动器,后轮采用自增力自动定义浮销式鼓式制动器。
在根据汽车的整车参数分析了汽车的制动力、制动力矩之后,就可以根据具体的制动器结构形式作相关设计、计算、分析等工作。
4.2基本原理(1)确定柱式制动器制动钳体主要结构参数的计算方法:在初步计算制动器制动钳体结构参数时,盘式制动器效能因数BF 的值可定为0.8。
根据汽车前轮所需的最大理论制动力矩,初步选取制动钳体缸孔直径D 1可由下面的公式算出:M μ1=(P 1-P 10)Awc 1ηa .BF 1r 1……………1-1式中:Awc 1—盘式制动器制动钳体缸也的工作面积:(mm 2)BF 1—盘式制动器制动效能因数;P 10—前制动管路的开启压力;(M pa 或N/mm 2)ηa —主缸以后的机械效率;r l —制动盘有效半径;(m)P 1—前制动管压;(M pa 或N/mm 2)(2)确定盘式制动器计算用的最大制动力矩:由于考虑到汽车实际制动时的最大输出制动力矩与理论值受很多因素影响而发生改变,如制动衬片与制动盘接触时不一定非常均匀使加制动力、制动衬片的摩擦系数受温度变化而发生改变等一些因素。
这样用于计算的最大制动力矩应由下面公式算出:M 'u 1max=1.2M u 1max …………………1-2式中:M 'u 1max —用于计算的最大制动力矩(N.m )M u 1max —单个前轮制动器理论最大制动力矩(N.m )作者简介:王亮,在读硕士,现工作在淮阴工学院,承担汽车服务工程专业的课程讲授工作。
汽车液压盘式制动器设计研究王亮关荣(淮阴工学院,江苏淮安223001)摘要:本文主要是研究汽车液压盘式制动器设计计算程序,通过运用V isual B asic 6.0软件和A ccess 数据库实现制动系的计算机辅助设计,基于制动器中的零部件数目较多,在掌握了汽车工业发展的历史和现状、汽车设计技术理论知识构成以及汽车零部件的工业现状及水平的基础上,选取具有代表性的汽车液压盘式制动器设计、计算分析模块。
从模块功能的概述、基本原理以及程序设计流程三个方面进行完整的模块设计说明。
从而实现汽车液压盘式制动器设计的自动化,提升整车的安全性能。
关键词:制动系;程序库;盘式制动器;模块技术平台趤趽科技经济市场(3)确定盘式制动器有效制动半径:设计盘式制动器时,在前制动管压和制动钳缸孔直径确定之后,制动器有效制动半径越大,则制动力矩越大。
但受到轮辋内径的限制,制动盘与轮辋之间应保持相当的间隙,否则不仅散热条件太差,而且轮辋受热可能粘住内胎。
盘式制动器有效制动半径的计算,如图1所示图1盘式制动器的有效制动半径参考图设:衬块与制动盘之间的单位压力为P1,则在任意微元面积RdRdθ上的摩擦力对制动盘中心的力矩为M P1R2dRdθ(μ为制动衬块与制动盘之间的摩擦系数),而单侧制动块加于制动盘的制动力矩为:单侧衬片加于制动盘的总摩擦力:故有效半径:……………………………1-3式中:R2—制动钳摩擦衬块外径(mm)R1—制动钳摩擦衬块内径(mm)而制动盘直径D b可由下面公式算出:D b=(0.64~0.74)D r…………………………………1-4式中:D b—制动盘直径;(mm)D r—汽车轮胎轮辋直径;(mm)那么,在式1-3有效半径的计算中,R2的取值一般与D b/2相同,而R1的值为R2与衬块宽度之差,而衬块宽度b1一般由供销商提供标准。
(4)确定盘式制动器制动钳缸孔直径D l将式1-2算出的M'u1max代入1-1得出:…………………………………1-5式中:P1m ax—前轮制动器最大制动管路压力;(M pa或N/mm2)P10—取0.05~0.14M pa;ηa—取0.8;BF1—取0.8;P1m ax—取12M pa~13M pa;(5)比较制动钳缸孔直径D1与R2-R1的值的大小D1与(R2-R1)相差的数值一般控制在6mm之内。
即:-6≤D1-(R2-R1)≤6…………………………………1-6在计算中,只有式1-6成立,D1的值才能基本上确定。
4.3基本流程基本流程图如图2所示图2程序流程图4.4程序设计界面图34.5程序设计代码(部分)Public Function BrakePan(P1max As Double,P10As Double, Awc1As Double,na As Double,_'Bf1As Double,R1As Double,R2As Double,_'M u1As Double,D1As Double,Tstr AsString)技术平台趥趭2009年第10期科技经济市场''Dim r11As Double'Dim M u1maxp As Double'Public Function BrakePanM u1(P1max As Double,P10As Double, Awc1As Double,na As Double,_Bf1As Double,R1As Double,R2As Double,_M u1As Double)Dim r11As Double'Dim M u1maxp As DoubleCall BrakePanr1(R1,R2,r11)M u1=(P1max-P10)*Awc1*na*Bf1*r11End Function4.6程序运行结果(见图4)5结语汽车液压盘式制动器作为制动系中的主要部件之一,在整车安全性这一最人性化的性能参数中起着举足轻重的作用,它的性能优劣与否,直接关乎乘车及驾车人员的生命安全,因此,它的设计必须要求准确、合理,处处体现以人为本的科学设计理念。
在了解汽车工业发展的历史和现状、汽车设计技术理论知识构成以及汽车零部件工业现状及水平的基础上,选取具有代表性的汽车液压盘式制动器设计、计算分析模块,从模块功能的概述、基本原理以及程序设计流程三个方面进行完整的模块设计说明。
相信在将计算机中的Visual Basic6.0及数据库知识充分合理地应用在液压式制动器的设计思想中,将会有利于汽车液压盘式制动器更好地行使其职能,从而提升整车的安全性能,推动汽车工业朝着更加安全更加可靠的方向发展。
参考文献:[1]Johannesson,HansL.ParajmetrieeomPuteraidedhydraulieeylinderdesign. CylinderProduet,modeling.AmerieanSocietyofMeehaniealEngineers, DesignEngineeringDivision ublieation)1990PublbyASMEP297一304,1990.[2]R udolfLimPert.BrakeDesignSafety.SeeondEdition. SocietyofAutomotiveEngineers.Ine.[3]王国荣.VisualBasic6.0数据库程序设计.北京:人民邮电出版社,2000.[4][美]ErioBrierley等VisualBasic6开发人员指南.北京:机械工业出版社,1999.[5]李玉琳主编.液压元件与系统设计.北京:机械工业出版社,1994(11).[6]余志生.汽车理论.北京:机械工业出版社,1990.[7]张洪欣.汽车设计.北京:机械工业出版社,1989.[8][美]L埃克霍恩等.汽车制动系统.北京:机械工业出版社,1998.图4M atlab是一种高效能的、用于科学和工程计算的计算机语言,它通过简单编程,能使复杂计算变得相当容易,并能实现计算和图像一体化,从而使数学分析和计算成为轻松和有意义的事情。