板簧计算
汽车钢板弹簧设计计算1

#DIV/0! #DIV/0! #DIV/0!! #DIV/0! #DIV/0! #DIV/0!
#DIV/0! #DIV/0! #DIV/0! #DIV/0! #DIV/0! 0 #DIV/0! #DIV/0! #DIV/0! #DIV/0!
1
14)(1-μi-1)↑3Ki 12)*13)
15)Bi 14)+1 16)ξi=Bi-αi-2*Ci-2 n=6,ξn=ξ6
2.钢板弹簧总成刚 度C=6EIn/ln↑3/ξ
n (N/mm)
1)刚度差(C实-C 理)/C实*100 (%) 2)钢板弹簧总成挠 度fc=2*Pn/C (mm) 3)钢板弹簧的固有 频率N (Hz)=16/fc ↑0.5 (1.3~2.3Hz)
0
#DIV/0! #DIV/0! #DIV/0! #DIV/0! #DIV/0! #DIV/0! #DIV/0! 0 #DIV/0! #DIV/0! #DIV/0! #DIV/0! #DIV/0! #DIV/0!
0 -0.1889 -0.13115 #DIV/0! #DIV/0! #DIV/0! #DIV/0!
47 #DIV/0!
#DIV/0! #DIV/0! #DIV/0! #DIV/0! #DIV/0! #DIV/0! #DIV/0! #DIV/0! #DIV/0! #DIV/0! #DIV/0! #DIV/0! #DIV/0! #DIV/0! #DIV/0! #DIV/0!
45
#DIV/0! ###### ###### #DIV/0!
2.065591 #DIV/0! #DIV/0! #DIV/0! #DIV/0!
#DIV/0! #DIV/0! #DIV/0!
4.A(L/2,(n0-1)h↑ 3),B(S/2,nh↑3)两 点直线方程: (x-x1)/(x1x2)=(y-y1)/ (y1-y2) 即:x=ay+b x1=L/2 x2=S/2 a=(x1-x2)/(y1y2) b=x1-(x1-x2) *y1/(y1-y2) 5.求各片的弦长Li (xi)圆整为尾数为 1)最短片L1 L2 (单边) L3 L4 L5 L6 L7 L8 L9 L10 L11 L12 L13 L14 L15 n=6,Ln=L6
板簧中心距

板簧中心距板簧中心距是指两个平行板极限挤压状态下的距离,它是板簧设计中的一个重要参数。
在工业生产中,板簧作为一种重要的机械弹性元件,广泛应用于汽车、空调、铁路等领域。
下面我们就来探讨一下板簧中心距的几个关键点。
一、板簧中心距的重要性如果设计时对板簧中心距没有考虑周全,就会在实际应用中产生很多问题。
例如,在转向机的应用中,当板簧中心距设计不当时,会导致转向难度大、方向不稳定等问题,从而影响汽车行驶的安全性。
因此,正确合理地设计板簧的中心距至关重要,它直接关系到板簧的弹性特性和功能应用的效果。
二、板簧中心距的测量方法板簧中心距的测量主要有两种方法:一是通过计算得到,二是通过实际测试得到。
1. 计算法通过板簧弹性力学理论,对板簧的形变情况进行计算,然后得到板簧中心距。
板簧中心距 = (板簧自由长度 - 弯曲后长度)/ 2其中,板簧自由长度是指板簧未受力时的长度,弯曲后长度是指板簧在受力时的长度。
2. 测试法在实际使用中,板簧的形变情况受到多种因素的影响,因此,通过实际测量得到的板簧中心距更为准确可靠。
测试板簧中心距时,需要使用专用的测量工具,如光学直尺、激光距离计等。
三、板簧中心距的应用范围板簧中心距的应用范围非常广泛,主要涉及以下领域:1. 汽车行业板簧作为汽车悬挂系统的核心部件,它的中心距决定着汽车的稳定性和行驶舒适度。
2. 家电行业板簧作为家电产品的弹簧组件,主要应用于电冰箱、洗衣机等产品中,使得机器具有承重、防震、抗压等功能。
3. 机械制造行业板簧中心距的设计也应用在通用机床、工程机械、矿山机械等领域,为机械制造提供了重要支持。
四、板簧中心距的调节方法当板簧中心距不能满足产品设计要求时,可以通过以下调节方法来实现:1. 改变板簧的厚度和宽度板簧的厚度和宽度是影响板簧中心距的重要参数,根据实际需求可以调整板簧的厚度和宽度,从而达到合适的板簧中心距。
2. 调整工艺板簧的制造工艺也会影响板簧中心距的大小,可以通过改变制造工艺来调节板簧的中心距。
钢板弹簧行驶不能断裂(前板簧强度校核计算)

项目 输入参数 车轮静止力半径 前桥一级落差 后轮中心到弹簧座距离 前簧总片高
单位
cm cm cm cm
后簧总片高
cm
整车质心高度
M
前桥非簧载质量
n
后桥非簧载质量
n
前桥超载质量
n
后桥超载质量
n
前桥满载质量
n
后桥满载质量
n
后桥空载负荷
n
前轴空载负荷
n
轴距m
M
地面附着系数
弹性模量
N/mm2
前桥超载簧下载荷
结果
35.7 6 6.7 6.8
8
落差6.7斜垫板厚2.0 簧高11、斜垫板2.09
0.98 200 300
2355 4140 1597 2033 1005
1275
2.6 0.7
20580000.00
21119.00 37632.00 13970.00 38400.00 10535.00 6909.00
N
后桥超载簧下载荷
N
前桥满载簧下载荷
N
后桥满载簧下载荷
N
前桥空载簧下载荷
N
后桥空载簧下载荷
N
二、前板簧计算
1、前板簧计算输入参数
板簧规格表示
主片数
n1
副片数
n2
符号 Rc m1 m2 ∑h1 ∑h2 hg Gu1 Gu2 G1 G2 G1 G2
m2 m1 L ф
E
单面槽截面1300x75x9-6(2)g
T1+(P1d×La+T1×ha)×sinβ/((hb -ha)×sinβ+(La+Lb)cosβ)
吊耳满载时夹角(°)
β
单片板簧计算公式

单片板簧计算公式单片板簧是一种常见的弹簧结构,广泛应用于各种机械设备中。
它具有体积小、质量轻、弹性好等优点,因此在工程设计中得到了广泛的应用。
在设计单片板簧时,需要进行一定的计算,以确保其能够满足设计要求。
本文将介绍单片板簧的计算公式及其应用。
单片板簧的计算公式主要包括以下几个方面:弹性系数的计算、应力的计算、变形的计算等。
其中,弹性系数是单片板簧的重要参数,它反映了单片板簧在受力时的变形能力。
弹性系数的计算公式为:K = (3/2) (t^3) E / (l^3)。
其中,K为弹性系数,t为单片板簧的厚度,E为弹性模量,l为单片板簧的长度。
根据这个公式,可以计算出单片板簧的弹性系数,从而为后续的计算提供基础数据。
在计算单片板簧的应力时,需要考虑到单片板簧在受力时所产生的应力情况。
单片板簧的应力计算公式为:σ = M y / I。
其中,σ为单片板簧的应力,M为单片板簧所受的弯矩,y为单片板簧的受力点到中性轴的距离,I为单片板簧的惯性矩。
通过这个公式,可以计算出单片板簧在受力时所产生的应力大小,从而为单片板簧的强度设计提供依据。
除了弹性系数和应力的计算外,单片板簧的变形也是一个重要的计算内容。
单片板簧的变形计算公式为:δ = (M l^2) / (2 E I)。
其中,δ为单片板簧的变形,M为单片板簧所受的弯矩,l为单片板簧的长度,E为弹性模量,I为单片板簧的惯性矩。
通过这个公式,可以计算出单片板簧在受力时产生的变形量,从而为单片板簧的设计提供参考。
综上所述,单片板簧的计算公式涉及到弹性系数、应力和变形等多个方面。
在实际工程设计中,需要根据具体的设计要求和实际情况,选择合适的计算公式进行计算,以确保单片板簧能够满足设计要求。
同时,还需要对单片板簧的材料、工艺等方面进行合理的选择和设计,以确保单片板簧的性能和可靠性。
希望本文介绍的单片板簧计算公式能够为工程设计人员提供一定的参考和指导,帮助他们更好地进行单片板簧的设计与应用。
钢板弹簧总成弧高简便计算法
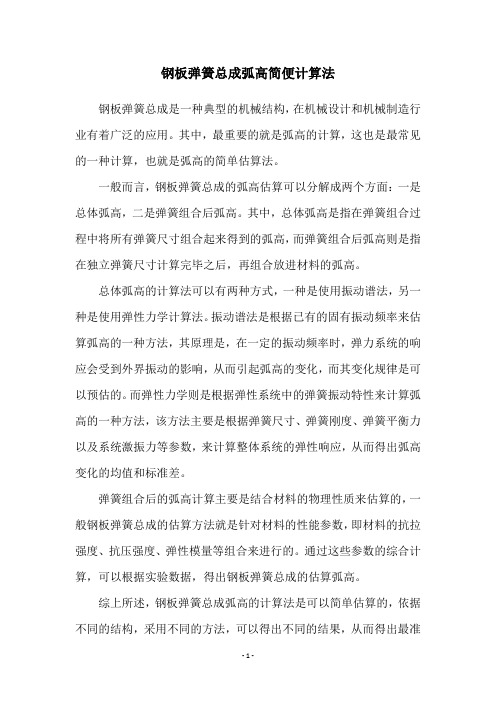
钢板弹簧总成弧高简便计算法钢板弹簧总成是一种典型的机械结构,在机械设计和机械制造行业有着广泛的应用。
其中,最重要的就是弧高的计算,这也是最常见的一种计算,也就是弧高的简单估算法。
一般而言,钢板弹簧总成的弧高估算可以分解成两个方面:一是总体弧高,二是弹簧组合后弧高。
其中,总体弧高是指在弹簧组合过程中将所有弹簧尺寸组合起来得到的弧高,而弹簧组合后弧高则是指在独立弹簧尺寸计算完毕之后,再组合放进材料的弧高。
总体弧高的计算法可以有两种方式,一种是使用振动谱法,另一种是使用弹性力学计算法。
振动谱法是根据已有的固有振动频率来估算弧高的一种方法,其原理是,在一定的振动频率时,弹力系统的响应会受到外界振动的影响,从而引起弧高的变化,而其变化规律是可以预估的。
而弹性力学则是根据弹性系统中的弹簧振动特性来计算弧高的一种方法,该方法主要是根据弹簧尺寸、弹簧刚度、弹簧平衡力以及系统激振力等参数,来计算整体系统的弹性响应,从而得出弧高变化的均值和标准差。
弹簧组合后的弧高计算主要是结合材料的物理性质来估算的,一般钢板弹簧总成的估算方法就是针对材料的性能参数,即材料的抗拉强度、抗压强度、弹性模量等组合来进行的。
通过这些参数的综合计算,可以根据实验数据,得出钢板弹簧总成的估算弧高。
综上所述,钢板弹簧总成弧高的计算法是可以简单估算的,依据不同的结构,采用不同的方法,可以得出不同的结果,从而得出最准确的弧高。
此外,由于计算技术的发展,目前也有一些计算机软件能够替代人工计算,为工程师提供计算支持,以更快、更精确地计算出最佳的钢板弹簧总成弧高,从而提高设计质量。
总之,钢板弹簧总成弧高简便计算法以及计算机软件计算技术的发展,都为机械行业提供了便利,无论是对机械设计过程,还是对机械制造过程,都有着重要的作用,能够提高机械产品的质量和性能。
钢板弹簧总成弧高简便计算法
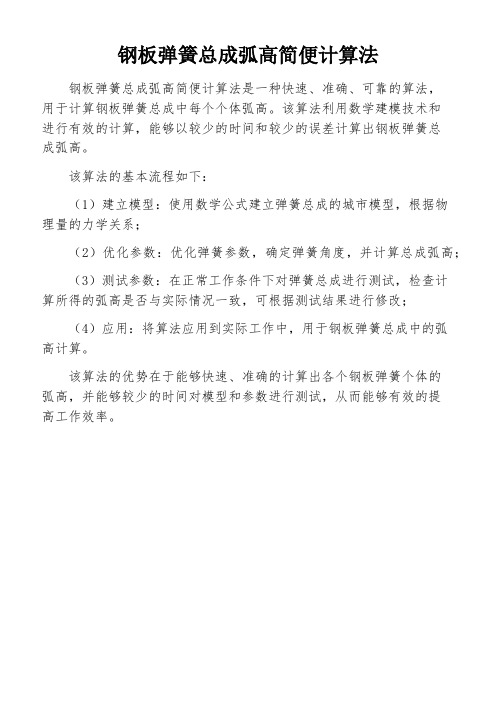
钢板弹簧总成弧高简便计算法
钢板弹簧总成弧高简便计算法是一种快速、准确、可靠的算法,
用于计算钢板弹簧总成中每个个体弧高。
该算法利用数学建模技术和
进行有效的计算,能够以较少的时间和较少的误差计算出钢板弹簧总
成弧高。
该算法的基本流程如下:
(1)建立模型:使用数学公式建立弹簧总成的城市模型,根据物
理量的力学关系;
(2)优化参数:优化弹簧参数,确定弹簧角度,并计算总成弧高;
(3)测试参数:在正常工作条件下对弹簧总成进行测试,检查计
算所得的弧高是否与实际情况一致,可根据测试结果进行修改;
(4)应用:将算法应用到实际工作中,用于钢板弹簧总成中的弧
高计算。
该算法的优势在于能够快速、准确的计算出各个钢板弹簧个体的
弧高,并能够较少的时间对模型和参数进行测试,从而能够有效的提
高工作效率。
EQ153系列钢板弹簧刚度计算

钢板弹簧EQ153-G-F的自由刚度K=216.7N/mm,夹紧刚度(K)=238.5N/mm(夹紧距108mm)总成弧高150±6mm(2).EQ153H1-F前钢板弹簧自由刚度计算(片厚15,60Si2Mn)钢板弹簧EQ153H1-F的自由刚度K=369.8N/mm,夹紧刚度(K)=410N/mm(夹紧距108mm)总成弧高140±5mm钢板弹簧EQ153H-F的自由刚度K=413.9N/mm,夹紧刚度(K)=455.5N/mm(夹紧距108mm)总成弧高145±5mm(4).EQ153K前钢板弹簧自由刚度计算(片厚13,55CrMnA)钢板弹簧EQ153K的自由刚度K=319.1N/mm,夹紧刚度(K)=356.2N/mm(夹紧距108mm)总成弧高150±3mm55CrMnA)(与EQ153K有啥区别?)钢板弹簧EQ153K-F的自由刚度K=319.1N/mm,夹紧刚度(K)=356.2N/mm(夹紧距108mm)总成弧高150±3mm(6).EQ153D后钢板弹簧自由刚度计算(片厚16,60Si2Mn)钢板弹簧EQ153D的自由刚度K=575.7N/mm,夹紧刚度(K)=690.4N/mm(夹紧距188mm)总成弧高165±6mm钢板弹簧EQ153H的自由刚度K=574.7N/mm,夹紧刚度(K)=689N/mm(夹紧距188mm)总成弧高165±6mm(仅比EQ153D少块斜铁)(8).EQ153K后钢板弹簧自由刚度计算(片厚18, 55CrMnA,片宽100)钢板弹簧EQ153K的自由刚度K=820.2N/mm,夹紧刚度(K)=?N/mm(夹紧距?mm)总成弧高100±8mm钢板弹簧EQ153TH的自由刚度K=750.4N/mm,夹紧刚度(K)=900N/mm(夹紧距188mm)总成弧高155±6mm(10).EQ153TH1后钢板弹簧自由刚度计算(片厚18, 60Si2Mn)钢板弹簧EQ153TH1的自由刚度K=758.3N/mm,夹紧刚度(K)=909N/mm(夹紧距188mm)总成弧高155±6mm(与EQ153TH相比,仅多块斜铁)片宽100)钢板弹簧EQ153K的自由刚度K=438.3N/mm,夹紧刚度(K)=?N/mm(作用长度?mm,夹紧距?mm)总成弧高100±8mm钢板弹簧EQ153D的自由刚度K=463.8N/mm,夹紧刚度(K)=850N/mm(作用长度1140mm,夹紧距188mm)总成弧高70±6mm钢板弹簧EQ153H的自由刚度K=471.7N/mm,夹紧刚度(K)=820.5N/mm(作用长度1150mm,夹紧距188mm)总成弧高70±6mm(14).EQ153TH副钢板弹簧自由刚度计算(片厚16, 60Si2Mn)钢板弹簧EQ153TH的自由刚度K=801N/mm,夹紧刚度(K)=1468N/mm(作用长度1140mm,夹紧距188mm)总成弧高70±6mm。
板簧计算
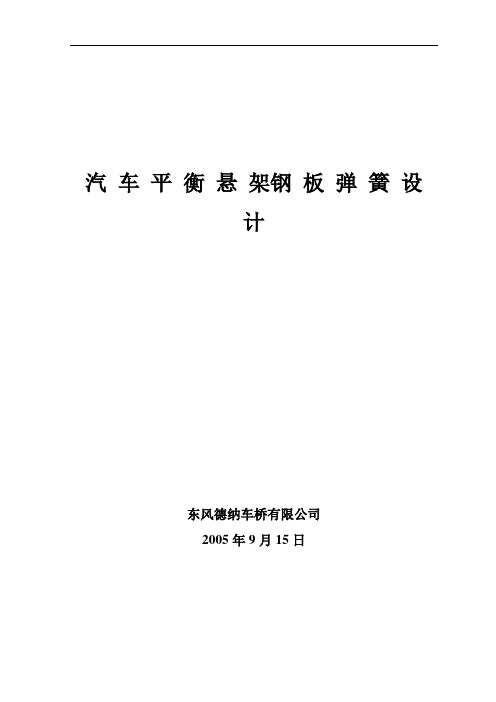
汽车平衡悬架钢板弹簧设计东风德纳车桥有限公司2005年9月15日一、钢板弹簧作用和特点a.结构简单,制造、维修方便;b.弹性元件作用;c.导向作用;d.传递侧向、纵向力和力矩的作用;e.多片弹簧片间摩擦还起系统阻尼作用;f.在车架或车身上两点支承,受力合理;g.可实现变刚度特性;h.相比螺旋弹簧和扭杆弹簧而言,单位质量的储能量较小,在同样的使用条件下,钢板弹簧要重一些。
二、钢板弹簧的种类、材料热处理及弹簧表面强化1.目前,汽车上使用的钢板弹簧常见的有以下几种:1)普通多片钢板弹簧;2)少片变截面钢板弹簧;3)两级变刚度复式钢板弹簧;4)渐变刚度钢板弹簧2.钢板弹簧材料的一般要求钢板弹簧与其它弹性元件一样,弹簧使用寿命与材料及制造工艺有很大关系,因此选用弹簧材料时应考虑以下几个方面因素1)弹性极限弹簧在弹性极限范围内变形时,希望弹簧储存的弹性变形能要大,而弹簧在单位中单位体积内储存的弹性变形能是与材料的弹性极限平方成正比,而与弹性模量与反比,因此从提高材料贮存的弹性变形能角度看,希望提高材料的弹性极限。
一般说材料抗拉强度高,弹性极限也高。
弹性极限与材料的化学成分和金相组织有较大关系,在弹簧钢中如果提高碳、硅、锰元素含量,可以提高材料弹性极限。
弹簧采用中温回火处理,能够得到具有较高弹性极限的回火屈氏体组织。
2)弹性模量 弹性模量有两种,即拉伸弹性模量E 和剪切弹性模量G 。
材料弹性模量愈小,材料变形和贮存的弹性变形能愈大。
从这个角度看,国外采用了弹性模量较低的增强树脂材料弹簧(FRP 弹簧)。
3)疲劳强度 由于弹簧多在交变载荷下工作,所以要求材料应有较高的疲劳极限,疲劳强度与材料抗拉强度b 和屈服强度s σ成正比,因此为了提高弹簧的疲劳强度,应设法提高材料的抗拉强度b σ和屈服强度与抗拉强度之比(b s σσ)。
4)淬透性 对于断面较厚的或变截面钢板弹簧,希望用淬透性较好的材料。
材料如不能淬透,淬火组织中将含有较多的非马氏体组织,使淬火后硬度降低。
- 1、下载文档前请自行甄别文档内容的完整性,平台不提供额外的编辑、内容补充、找答案等附加服务。
- 2、"仅部分预览"的文档,不可在线预览部分如存在完整性等问题,可反馈申请退款(可完整预览的文档不适用该条件!)。
- 3、如文档侵犯您的权益,请联系客服反馈,我们会尽快为您处理(人工客服工作时间:9:00-18:30)。
汽车平衡悬架钢板弹簧设计东风德纳车桥有限公司2005年9月15日一、钢板弹簧作用和特点a.结构简单,制造、维修方便;b.弹性元件作用;c.导向作用;d.传递侧向、纵向力和力矩的作用;e.多片弹簧片间摩擦还起系统阻尼作用;f.在车架或车身上两点支承,受力合理;g.可实现变刚度特性;h.相比螺旋弹簧和扭杆弹簧而言,单位质量的储能量较小,在同样的使用条件下,钢板弹簧要重一些。
二、钢板弹簧的种类、材料热处理及弹簧表面强化1.目前,汽车上使用的钢板弹簧常见的有以下几种:1)普通多片钢板弹簧;2)少片变截面钢板弹簧;3)两级变刚度复式钢板弹簧;4)渐变刚度钢板弹簧2.钢板弹簧材料的一般要求钢板弹簧与其它弹性元件一样,弹簧使用寿命与材料及制造工艺有很大关系,因此选用弹簧材料时应考虑以下几个方面因素1)弹性极限弹簧在弹性极限范围内变形时,希望弹簧储存的弹性变形能要大,而弹簧在单位中单位体积内储存的弹性变形能是与材料的弹性极限平方成正比,而与弹性模量与反比,因此从提高材料贮存的弹性变形能角度看,希望提高材料的弹性极限。
一般说材料抗拉强度高,弹性极限也高。
弹性极限与材料的化学成分和金相组织有较大关系,在弹簧钢中如果提高碳、硅、锰元素含量,可以提高材料弹性极限。
弹簧采用中温回火处理,能够得到具有较高弹性极限的回火屈氏体组织。
2)弹性模量 弹性模量有两种,即拉伸弹性模量E 和剪切弹性模量G 。
材料弹性模量愈小,材料变形和贮存的弹性变形能愈大。
从这个角度看,国外采用了弹性模量较低的增强树脂材料弹簧(FRP 弹簧)。
3)疲劳强度 由于弹簧多在交变载荷下工作,所以要求材料应有较高的疲劳极限,疲劳强度与材料抗拉强度b 和屈服强度s σ成正比,因此为了提高弹簧的疲劳强度,应设法提高材料的抗拉强度b σ和屈服强度与抗拉强度之比(b s σσ)。
4)淬透性 对于断面较厚的或变截面钢板弹簧,希望用淬透性较好的材料。
材料如不能淬透,淬火组织中将含有较多的非马氏体组织,使淬火后硬度降低。
虽然可以通过降低回火温度来达到所需要的硬度,但其机械性能较差。
为保证材料在整个截面内具有相同的机械性能,要求淬火时不仅表面而且心部也能淬透,且淬火后表面硬度和心部硬度相差不能太大。
综上所述,汽车钢板弹簧材料应具有较高的抗拉强度、屈服极限、疲劳强度及一定冲击韧性。
此外要求材料具有良好的淬透性,热处理不易脱碳等性能。
3. 钢板弹簧材料目前国内使用最多的弹簧钢板材料是钢Mn Si -,如Mn Si 260和MnA Si 260该钢种相当于美国9260SAE ,日本的7SUP 材料。
MnA Si 260弹簧钢含碳量在%7.0~%5.0左右,由于材料中含有硅、锰元素,经调质处理后明显提高了钢的弹性极限、屈强化及疲劳强度。
由于该种材料价格便宜,因此MnA Si 260弹簧钢在国内外得到广泛应用。
Mn Si -钢存在的主要问题是由于钢中硅的含量较高,增加了材料表面脱碳倾向,并容易形成较多硅酸盐夹杂物,影响弹簧使用寿命。
Mn Si 260、MnA Si 260弹簧钢适用于和生产厚度在mm 12以下的钢板弹簧。
为了提高弹簧钢材性能,新推出的SiMnVB 55弹簧钢。
由于该材料中减少了硅元素含量和加入了微量硼和少量钢元素,改善了钢的淬透性和回火稳定性,并起到细化晶料作用,从而提高了材料强度和韧性。
钢表面质量、淬透性能和脱碳敏感性均明显好于Mn Si 260弹簧钢,可适合生产厚度mm 20以下的钢板弹簧。
SiMnVB 55钢因含硼元素,对钢材冶炼工艺要求较严。
另外由于这种材料含合金元素比Mn Si 260多,所以材料价格较高。
除了Mn Si -钢之外,使用较多的还有钢B Mn Cr --,如CrMnA 55钢(相当于美5160SAE ,日本的A SUP 9)和CrMnBA 60钢(相当于美H B SAE 6051,日本的A CUP 11)。
这种弹簧钢不易脱碳,表面质量及淬透性能比较好,和弹簧钢相比,有较好的断裂韧度和缺口抗拉强度,这种弹簧钢特别是CrMnBA 60钢适合于大吨位汽车和变截面少片弹簧使用。
由于B Mn Cr --钢含有多种合金元素,钢材价格较贵。
表2 各种弹簧钢材化学成分4. 热处理热处理工艺一般是淬火加工中温回火。
淬火是把弹簧片坯料加热到3AC 以上C ︒50~30,如Mn Si 260、CrMnVB 55钢淬火温度控制在C ︒880~840;在该温度下保温足够时间,使簧片整个断面材料形成奥氏体组织;然后放入油中快速冷却,使奥氏体组织全部转换为马氏体组织,淬火后材料硬度大于或等于59HRC 。
由于马氏体组织硬度高,而且很脆,以及淬火过程中由奥氏体转变为马氏体时发生体积膨胀而产生较大应力,因此弹簧淬火后应进行回火处理,以得到回火屈氏体组织并消除内应力。
为了提高弹簧钢的弹性极限,回火温度控制在C ︒450~350。
如果想得到高的疲劳极限,回火温度应为C ︒500~450,淬火回火后弹簧硬度为47~40HRC 。
表3 各种弹簧钢材料热处理工艺及机械性能例如:46厂生产的少片前簧2912ZB6-010,用于EQ4196车型,钢板弹簧材料(各单片)为60CrMnBA(GB1222-84),钢板弹簧各单片全部经过应力喷丸处理,钢板弹簧各单片在装配前涂防锈漆层:H06-4环氧富锌底漆+表面黑漆QC-6甲,按EQY-乙。
钢板弹簧总成装配前端部间接触表面涂以石墨钙基润滑脂:3#-SHO369-92。
46厂生产的前簧2912ZB3A-010(共九片),用于EQ3286车型,钢板弹簧材料为55SiMnVB(GB1222-84),钢板弹簧各单片全部经过应力喷丸处理。
46厂生产的后钢板弹簧总成2913ZB3C-010(共九片),用于EQ3286、EQ3386车型,钢板弹簧材料为55SiMnVB(GB1222-84),钢板弹簧各单片全部经过应力喷丸处理。
5. 钢板弹簧表面强化弹簧表面质量对弹簧使用寿命影响较大,因此除了在弹簧生产中严桥控制表面质量外,还采取了喷丸和塑性压缩处理等表面强化技术处理。
1) 弹簧喷丸强化喷丸能提高弹簧使用寿命,是因为喷丸过程使弹簧在受拉表面产生一个残压应力层,弹簧工作时,使弹簧受拉表面拉应力相应减少。
一般说材料屈服极限越高,喷丸后得到的残余压应力也越大。
弹簧喷丸处理分自由喷丸和应力喷丸两种方式。
前者是弹簧片处于自由状态下进行喷丸,后者是弹簧片受拉表面在拉力状态进行喷丸。
自由喷丸在金属表面产生的残余压应力约为2/650~550mm N ,应力喷丸可达2/1350~1100mm N 。
试验表明,弹簧经应力喷丸后疲劳寿命可提高7~2倍。
另外,喷丸处理使弹簧片面产生大约mm 25.0~06.0的硬化层,因而能消除或改善弹簧片的表面缺陷,从而提高弹簧疲劳寿命。
2) 弹簧塑性压缩处理塑性压缩处理是对喷丸后听弹簧总成预加一定载荷,使弹簧表面产生残余压应力,当去掉载荷后,弹簧有一定塑性变形。
经塑性压缩处理的弹簧,在使用过程中能保持总成弧高不变,不再发生塑性变形。
此外,塑性压缩处理和弹簧喷丸处理一样,可以使弹簧表面产生一个残余压应力层。
弹簧塑性压缩处理时施加在弹簧上的载荷,应使弹簧表面产生的拉应力接近材料的屈服强度。
三、 钢板弹簧设计的已知参数1. 弹簧载荷根据整车布置给定的空、满载质量减去估算的非簧载质量,得到在每副弹簧上的承载质量。
一般将前、后轴,车轮,制动鼓及轮毂等总成视为非簧载质量,将传动轴、转向纵拉杆等总成一半也视为非簧载质量。
如果钢板弹簧布置在车桥上方,弹簧3/4的质量为非簧载质量;下置弹簧,弹簧1/4质量为非簧载质量。
2. 弹簧伸直长度应根据不同车型要求,由总布置给出弹簧伸直长度的控制尺寸。
在布置可能的情况下,尽量增加弹簧长度,这主要是考虑以下几个方面原因。
a) 由于弹簧刚度与弹簧长度的三次方成反比,因此从改善汽车平顺性角度看,希望弹簧长度长些好。
b) 在弹簧刚度相同情况下,长的弹簧在车轮上下跳动时,弹簧两卷耳孔距离相对较小,对前悬架来说,主销后倾角变化较小,有利于汽车行驶稳定性。
c) 增加弹簧长度可以降低弹簧工作应力和应力幅,从而提高弹簧使用寿命。
d) 增加弹簧长度可以选用片厚的弹簧,从而减少弹簧片数,并且片厚的弹簧对提高主片卷耳强度有利。
3. 悬架静挠度汽车簧载质量与其质量组成的振动系统固有频率是评价汽车行驶平顺性的主要参数。
悬架设计时根据汽车平顺性要求,应给出汽车空、满载时前、后悬架频率范围,见表1。
表1 汽车悬架的偏频、静挠度及动挠度如果知道频率0n ,那么悬架静挠度c f 为:()mm n f c 25109⨯= (1)选取悬架静挠度值时,希望后悬架静挠度值2c f 小于前悬架静挠度值1c f ,并且两值最好接近,一般推荐:()129.0~7.0c c f f = (2)为防止汽车在不平路面行驶时经常撞击缓冲块,悬架设计时必须给出足够的动挠度值d f 。
悬架动挠度值与汽车使用情况和静挠度值c f 有关,一般推荐:c d f a f = (3)城市公用车辆5.2~2=a ,公路用车辆5.3~5.2=a ,越野车辆5.3≥a 。
4. 弹簧满载弧高由于车身高度、悬架动行程及钢板弹簧导向特性等都与汽车满载弧高有关,因此弹簧满载弧值0f 应根据整车和悬架性能要求给出适当值,一般取mm f 30~100=。
有的车辆为得到良好的操纵稳定性,满载弧高取负值。
四、 钢板弹簧刚度和应力计算关于钢板弹簧刚度和应力计算,基于不同的假设计算方法各异。
在弹簧计算中有两种典型的而又截然相反的假设,即共同曲率法和集中载荷法。
1. 共同曲率法共同曲率法是假设钢板弹簧在任何载荷下,弹簧各片彼此沿整个长度无间隙接触,在同一截面上各簧片具有共同的曲率半径。
如果将多片弹簧各片展开,将展成一个平面是,组成一个新的单片弹簧(图1、图2)。
这个变宽度的单片弹簧力学特性和用共同曲率法假定的多片钢板弹簧是一样的,这样就可以用单片弹簧计算方法来计算多片钢板弹簧。
单片弹簧计算按其几何形状不同可以有两种计算方法。
一种是梯形单片弹簧(图1),另一种是按多片弹簧各片长度展开成的阶梯形单片弹簧(图2)。
1) 梯形单片弹簧图1 梯形单片弹簧计算梯形单片弹簧变形和应力,可以利用材料力学求小挠度梁方法计算。
梯形单片弹簧与等宽简支梁计算公式不同之处是引进了一个挠度系数δ,梯形单片弹簧刚度、变形、应力和比应力计算公式如下:()mm N L EJ K 348δ=(4)()mm K Q f =(5)()204mm NW QL =σ (6)()mm MPa W L EJ f c2012δσσ==(7)式中:K — 梯形单片弹簧刚度,mm N /; f — 梯形单片弹簧变形,mm ;σ — 梯形单片弹簧在根部(或中心螺栓处)应力,2/mm N ;σ — 弹簧比应力(单位变形应力),()mm mm N //2;E — 钢板弹簧材料弹性模量,取MPa E 51006.2⨯=; Q — 作用在弹簧上的载荷,取P Q 2=,N ;L — 梯形单片弹簧长度, l L 2=,mm ;0J — 梯形单片弹簧在根部的惯性矩, 4mm ;n bh J 1230= (8)0W — 梯形单片弹簧在根部的断面系数, 3mm ;n bh W 620= (9)b — 单片弹簧各片宽度, mm ;h — 单片弹簧各片厚度, mm ; δ — 挠度增大系数, mm ; ⎪⎭⎫ ⎝⎛+=n n 2104.15.11δ (10) n — 弹簧总片数;1n — 与主片等长片数。