常见金属热处理缺陷研究
金属热处理产生的组织缺陷

金属热处理产生的组织缺陷
金属热处理缺陷指在热处理生产过程中产生的使零件失去使用价值或不符合技术条件要求的各种补助,以及使热处理以后的后续工序工艺性能变坏或降低使用性能的热处理隐患。
最危险的缺陷为裂纹,其中最主要的是淬火裂纹,其次是加热裂纹、延迟裂纹、冷处理裂纹、回火裂纹、时效裂纹、磨削裂纹和电镀裂纹等。
导致淬火裂纹的原因:(1)原材料已有缺陷(冶金缺陷扩展成淬火裂纹);(2)原始组织不良(如钢中粗大组织或魏氏组织倾向大);(3)夹杂物;(4)淬火温度不当;(5)淬火时冷却不当;(6)机械加工缺陷;(7)不及时回火。
最常见的缺陷是变形,其中淬火变形占多数,产生的原因是相变和热应力。
残余应力、组织不合格、性能不合格、脆性及其他缺陷发生的频率和严重性较低。
内应力来源有两个方面:(1)冷却过程中零件表面与中心冷却速率不同、其体积收缩在表面与中心也不一样。
这种由于温度差而产生的体积收缩量不同所引起的内用力叫做“热应力”;(2)钢件在组织转变时比体积发生变化,如奥氏体转变为马氏体时比体积增大。
由于零件断面上各处转变的先后不同,其体积变化各处不同,由此引起额内应力称作“组织应力”。
《金属热处理缺陷分析及案例》完整版

第三章 热处理变形
一、产生原因:热处理应力引起。 二、对质量影响最大:淬火变形。 三、类别:尺寸变化和形状畸变。 四、影响因素: 1、成分(Mn、Cr、Si、Ni、Mo、B等 降低Ms点,减小淬火变形)。 工业上应用:微变形钢(含较多的Si、 W、V等合金元素)。
2、组织和应力状态:
(二)、热处理缺陷分析方法:
1、热处理缺陷的影响:直接影响产品质量、 使用性能和安全,所以准确分析和判断十分 重要。 2、分析方法:断口分析(裂源位置、扩展方 向、断裂性质和方式)、化学分析(材料成分、 沉积物、氧化物)、金相分析(晶粒、组织、 晶界)、力学性能试验(硬度、拉伸、冲出、 疲劳断裂韧度)、验证试验(原工艺和改进工 艺对比)、综合分析(得出缺陷产生的几种主 要原因,提出改进措施)。
第二章、热处理裂纹:
(一)、产生原因:内应力作用下发 生,最终断裂。条件是内应力>脆 断强度。 (二)、断裂类别: 1、裂纹按扩展程度:(失稳)可发 展裂纹、阻断裂纹(不断裂)。 2、断裂:脆性断裂和韧性断裂。多 数为脆性断裂(断口灰亮色)
(三)、加热不当形成的裂纹:
升温速度过快(多出现于灰铸铁、 合金铸铁、高锰钢、高合金钢铸 件)、表面增碳或脱碳[合金钢、低 碳马氏体钢20SiMn2MoV,高锰钢 (Mn13)]、过热或过烧(高速钢、不 锈钢)、氢致裂纹(条件:足够氢、 对氢敏感的金相组织和三向应力。 措施:脱氢、低温回火、自然时效、 低氢淬火)
2、按照危害程度分类:
(1)、第一类热处理缺陷: 最危险缺陷如裂纹,其中最 主要是淬火裂纹,其次加热 裂纹、延迟裂纹、冷处理裂 纹、回火裂纹、时效裂纹、 磨削裂纹和电镀裂纹等。
(2)、第二类热处理缺陷:
渗碳淬火裂纹的特征

渗碳淬火裂纹的特征
渗碳淬火裂纹是一种常见的金属热处理缺陷,它在工业生产中造成了许多问题。
渗碳淬火裂纹是指在渗碳淬火过程中,金属材料表面出现的裂纹。
这种裂纹通常呈现出一定的形态特征,以及与渗碳淬火过程相关的特定位置。
渗碳淬火裂纹的特征之一是其位置分布的特殊性。
这些裂纹通常出现在金属材料的表面或近表面区域,而不是内部。
这是因为渗碳淬火过程中,表面的渗碳层与内部材料的差异导致了内外应力的不平衡,从而导致了裂纹的形成。
渗碳淬火裂纹的形态特征也值得关注。
这些裂纹通常呈现出沿着材料表面方向延伸的线状形态,有时呈现出分叉或交叉的形式。
这是由于渗碳淬火过程中,不同位置的温度和应力分布不均匀,导致裂纹在材料表面上扩展的方式不同。
渗碳淬火裂纹的特征还包括其尺寸和密度。
这些裂纹通常呈现出不同的尺寸和密度,有些裂纹可能很细小,几乎看不到,而有些裂纹则较大且密集。
这是由于渗碳淬火过程中,金属材料的组织和化学成分的不均匀性,导致了裂纹的形成和分布的差异。
渗碳淬火裂纹还具有一定的方向性特征。
这些裂纹通常沿着材料表面方向延伸,与材料的应力和变形方向有关。
这是由于渗碳淬火过程中,金属材料的热膨胀和收缩引起的应力分布不均匀性,导致了
裂纹在特定方向上的扩展。
总的来说,渗碳淬火裂纹具有位置分布特殊、形态特征独特、尺寸密度不均匀和方向性明显等特征。
了解和掌握这些特征对于预防和解决渗碳淬火裂纹问题至关重要。
在工业生产中,通过合理的工艺参数和控制措施,可以有效地减少渗碳淬火裂纹的发生,提高金属制品的质量和可靠性。
铸造铝合金热处理质量缺陷及其消除与预防
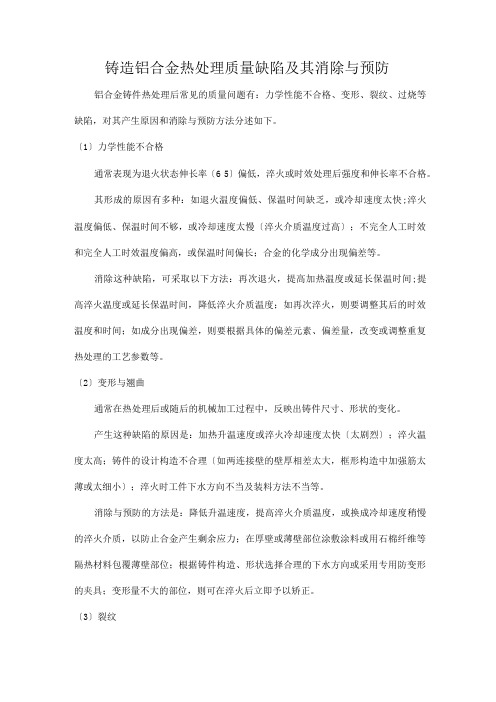
铸造铝合金热处理质量缺陷及其消除与预防铝合金铸件热处理后常见的质量问题有:力学性能不合格、变形、裂纹、过烧等缺陷,对其产生原因和消除与预防方法分述如下。
〔1〕力学性能不合格通常表现为退火状态伸长率〔6 5〕偏低,淬火或时效处理后强度和伸长率不合格。
其形成的原因有多种:如退火温度偏低、保温时间缺乏,或冷却速度太快;淬火温度偏低、保温时间不够,或冷却速度太慢〔淬火介质温度过高〕;不完全人工时效和完全人工时效温度偏高,或保温时间偏长;合金的化学成分出现偏差等。
消除这种缺陷,可采取以下方法:再次退火,提高加热温度或延长保温时间;提高淬火温度或延长保温时间,降低淬火介质温度;如再次淬火,则要调整其后的时效温度和时间;如成分出现偏差,则要根据具体的偏差元素、偏差量,改变或调整重复热处理的工艺参数等。
〔2〕变形与翘曲通常在热处理后或随后的机械加工过程中,反映出铸件尺寸、形状的变化。
产生这种缺陷的原因是:加热升温速度或淬火冷却速度太快〔太剧烈〕;淬火温度太高;铸件的设计构造不合理〔如两连接壁的壁厚相差太大,框形构造中加强筋太薄或太细小〕;淬火时工件下水方向不当及装料方法不当等。
消除与预防的方法是:降低升温速度,提高淬火介质温度,或换成冷却速度稍慢的淬火介质,以防止合金产生剩余应力;在厚壁或薄壁部位涂敷涂料或用石棉纤维等隔热材料包覆薄壁部位;根据铸件构造、形状选择合理的下水方向或采用专用防变形的夹具;变形量不大的部位,则可在淬火后立即予以矫正。
〔3〕裂纹表现为淬火后的铸件外表用肉眼可以看到明显的裂纹,或通过荧光检查肉眼看不见的微细裂纹。
裂纹多曲折不直并呈暗灰色。
产生裂纹的原因是:加热速度太快,淬火时冷却太快〔淬火温度过高或淬火介质温度过低,或淬火介质冷却速度太快〕;铸件构造设计不合理〔两连接壁壁厚差太大,框形件中间的加强筋太薄或太细小〕;装炉方法不当或下水方向不对;炉温不均匀,使铸件温度不均匀等。
消除与预防的方法是:减慢升温速度或采取等温淬火工艺;提高淬火介质温度或换成冷却速度慢的淬火介质;在壁厚或薄壁部位涂敷涂料或在薄壁部位包覆石棉等隔热材料;采用专用防开裂的淬火夹具,并选择正确的下水方向。
热处理专科毕业设计GCr15轴承钢球的热处理工艺及缺陷分析

GCr15轴承钢球的热处理工艺及缺陷分析摘要:本论文重点对GCr15轴承钢球热处理工艺的设计进行了讨论,同时对热处理后其可能存在的热处理工艺缺陷进行了分析。
钢球在不同热处理工艺下虽然都能达到其使用要求,但所需的成本却大不相同,因此在满足其使用要求的同时也应该注意生产成本。
热处理常常因操作、原材料等产生缺陷,但只要有正确的热处理工艺并严格按工艺进行加工热处理缺陷也是可以避免的,即使产生了缺陷也可以采取相应的措施及时修复缺陷。
关键词:GCr15 轴承钢球热处理设计热处理工艺热处理缺陷引言滚动轴承是机械工业十分重要的基础标准件之一;滚动轴承依靠元件间的滚动接触来承受载荷,与滑动轴承相比:滚动轴承具有摩擦阻力小、效率高、起动容易、安装与维护简便等优点。
缺点是耐冲击性能较差、高速重载时寿命低、噪声和振动较大。
图 1 轴承及钢球实物图滚动轴承的基本结构(图 1):内圈、外圈、滚动体和保持架等四部分组成。
常用的滚动体有球、圆柱滚子、滚针、圆锥滚子。
轴承的内、外圈和滚动体,一般是用轴承钢(如GCr15、GCr15SiMn)制造,热处理后硬度应达到61~65HRC。
当滚动体是圆柱或滚针时,有时为了减小轴承的径向尺寸,可省去内圈、外圈或保持架,这时的轴颈或轴承座要起到内圈或外圈的作用。
为满足使用中的某些需要,有些轴承附加有特殊结构或元件,如外圈带止动环、附加防尘盖等。
滚动轴承钢球的工作条件极为复杂,承受着各类高的交变应力。
在每一瞬间,只有位于轴承水平面直径以下的那几个钢球在承受载荷,而且作用在这些钢球的载荷分布也不均匀。
力的变化由零增加到最大,再由最大减小到零,周而往复得增大和减小。
在运转过程中,钢球除受到外加载荷外,还受到由于离心力所引起的载荷,这个载荷随轴承转速的提高而增加。
滚动体与套圈及保持架之间还有相对滑动,产生相对摩擦。
滚动体和套圈的工作面还受到含有水分或杂质的润滑油的化学侵蚀。
在某些情况下,轴承零件还承受着高温低温和高腐蚀介质的影响。
金属材料组织缺陷形成机理分析

金属材料组织缺陷形成机理分析金属材料的组织缺陷常常是导致其力学性能下降的主要原因之一。
对于金属材料组织缺陷形成机理的深入研究,有助于我们理解金属材料的性能变化规律,并进一步提高金属材料的性能。
金属材料的组织缺陷主要包括晶界、孔隙、位错和析出相等。
晶界是金属晶粒之间的界面,是金属材料中不可避免的一种缺陷形态。
晶界的存在对金属材料的塑性变形和热稳定性都会产生显著影响。
孔隙是金属材料中的空隙,常常由于金属材料的制备过程中留下的气体或液体引起。
孔隙的存在会导致金属材料的强度降低以及疲劳寿命缩短。
位错是金属晶体内部的线性缺陷,通常由于金属材料的加工过程或外力作用引起。
位错的存在会导致金属材料的变形行为和力学性能发生变化。
析出相是金属材料中存在的非基底相,常常由于固溶体中的固溶度限制或金相转变引起。
析出相的存在会引起金属材料的显微硬化和晶界强化效应。
金属材料组织缺陷的形成机理具有复杂性和多样性。
首先,金属材料的制备过程中存在的化学反应、相变行为和成分偏析等都会导致组织缺陷的形成。
例如,金属材料的合金化过程中,不同元素之间的化学反应会导致相变和析出相的形成。
其次,金属材料的加工过程中的机械变形会引起位错的形成和运动。
金属材料在加工过程中所经历的塑性变形会导致晶界的运动和分布的变化,从而形成晶界缺陷。
此外,金属材料在高温条件下的热处理也会影响组织缺陷的形成。
热处理过程中的相变行为和固溶体的析出相会改变金属材料的晶界、孔隙和位错等缺陷的分布和性质。
为了深入理解金属材料组织缺陷的形成机理,研究人员通常采用多种先进的材料表征技术和数值模拟方法。
例如,透射电子显微镜(TEM)和扫描电子显微镜(SEM)可以观察到金属材料中的晶界和位错等缺陷形态。
X射线衍射(XRD)和能谱分析技术可以分析金属材料中的析出相和化学成分。
此外,通过应用分子动力学模拟、有限元分析和相场模型等数值模拟方法,可以模拟金属材料的相变行为、位错运动以及晶界演化等过程。
金属材料的晶格缺陷及其对性能的影响研究

金属材料的晶格缺陷及其对性能的影响研究金属材料是我们生活中离不开的一种材料,具有良好的导电性、导热性、延展性、可塑性和强度等优良特性,因此被广泛应用于制造业、建筑业、能源产业、航空航天等领域中。
但是,金属材料在使用过程中存在着晶格缺陷,这些缺陷会影响其性能和使用寿命。
本文就金属材料的晶格缺陷及其对性能的影响进行探讨。
一、晶格缺陷的概念晶体是由原子、离子或分子的周期排列构成的,它具有完美的结晶性和有序性。
但是,在晶体的生长、加工、热处理等过程中,会形成各种缺陷。
晶格缺陷是指晶体中的原子位置发生了变化而导致的缺陷。
晶格缺陷主要包括点缺陷、面缺陷和体缺陷三种。
其中,最常见的是点缺陷,即晶体中某个原子没了或多了一个,包括晶格空位、间隙原子、替位原子、杂质原子等。
二、晶格缺陷对金属材料性能的影响晶格缺陷既可能改善金属的性能,也可能破坏其性能,具体表现如下:1. 强度晶格缺陷对金属材料的强度会产生影响。
例如,错位位错材料具有较高的强度,因为它们的原子排列更紧密,形成了劳厄位错区域,阻碍了位错的运动。
然而,过多的位错会导致晶体变脆,强度降低。
此外,晶格缺陷还会增加材料内部应力,并在位错滑移过程中产生新的位错,进而损伤材料。
2. 塑性晶格缺陷对金属材料的塑性也会产生影响。
晶体中的空位、替位原子和杂质原子等缺陷可以增强材料的塑性。
原子替位可使材料的晶格畸变,增强位错的滑移,提高材料的塑性。
但是,空位、杂质原子和间隙原子等缺陷会阻碍位错的滑移,降低材料的塑性。
3. 热稳定性晶格缺陷会降低金属材料的热稳定性。
晶格缺陷会使晶界、位错和相界的能量降低,从而促进缺陷的形成和蔓延,影响材料的结构和性能。
特别是在高温条件下,缺陷会更加明显,因此材料的热稳定性会下降。
4. 电性能晶格缺陷对金属材料的电性能也会产生影响。
空位和间隙原子等缺陷可形成导电空穴,提高材料的导电性能。
替位原子和杂质原子等缺陷则会改变材料的导电性能,使之成为n型或p型半导体。
热锻件常见缺陷及防止方法

热锻件常见缺陷及防止方法发布时间:2022-06-20T08:48:50.332Z 来源:《福光技术》2022年13期作者:乔石[导读] 当我们思考所有用金属制造一个部件的方法时,锻造是重要部件获得高质量和性能的最好方法。
中国第一重型机械股份公司黑龙江省齐齐哈尔市 161042摘要:锻造成形技术广泛应用于航空航天、汽车、钢铁、装备制造、兵器、能源、造船等国民经济的各个重要领域。
锻造生产具有显著的优越性,它不但能获得金属零件的形状,而且能改善金属的内部组织,提高金属的力学性能和物理性能。
一般对于承力大的重要机械零件,大多需用锻造方法制造,锻件质量的优劣直接影响着零件的性能及使用寿命。
然而,锻造过程异常复杂,锻件质量与原材料质量、锻造工艺及锻后热处理工艺密切相关,为此,本文就坯料加热、锻造过程的不当处理可能导致的锻件缺陷进行了分析研究,并提出了具体的解决方案,对工程实践中锻件产品质量的保证与控制具有重要指导。
关键词:热锻件;常见缺陷;防止方法1.锻造工艺表面缺陷分析当我们思考所有用金属制造一个部件的方法时,锻造是重要部件获得高质量和性能的最好方法。
用锻件有时候比用其他件(如铸件,粉末金属件,焊接件)花费多些,但是如果设计者已持续体验到锻件产品的高可靠性的话,那么这些花费是值得的。
用商业的说法就是他“投入多也得到了更多”。
然而,有时候锻造工艺不正确致锻件使用中失效,顾客不仅对锻件供应商不满而且也对其选择锻造作为生产工艺感到怀疑。
当一种产品失效时,不仅失去了顾客对选择锻造作为下一个主要部件的制造方法的信心,也产生了对产品责任的忧虑。
有时候缺陷来源于初始材料但更多地是来自锻造工艺本身。
伴随着每种缺陷的描述给出了该种缺陷可能的解决方法。
在一些情况下,会有超过一种的起因。
对每种材料或锻造工艺都讨论了其选择,见表1。
表1表面缺陷、成因和解决方法2.锻造过程常见的缺陷、原因分析和防止方法2.1锻件充填不满金属没有完全充满模具型腔,造成锻件棱角、筋条等细小部位缺肉,使锻件轮廓不清。
- 1、下载文档前请自行甄别文档内容的完整性,平台不提供额外的编辑、内容补充、找答案等附加服务。
- 2、"仅部分预览"的文档,不可在线预览部分如存在完整性等问题,可反馈申请退款(可完整预览的文档不适用该条件!)。
- 3、如文档侵犯您的权益,请联系客服反馈,我们会尽快为您处理(人工客服工作时间:9:00-18:30)。
165Х
165×
15
力学性能比较
状态 机械性能 σb σs δ5 (Mpa) (Mpa) (%) 正常45#钢组织 过热后,具有粗大晶粒者 过热后,经细化晶粒处理者 45#钢魏氏组织 600 629 669 524 355 330 442 337 16 15.5 26.1 9.5 Φ (%) 40 24.5 51.5 17.5 αK 3.9 1.6 5.4 1.3
2Fe3C+O2=6Fe+2CO Fe3C+2H2=3Fe+CH4 Fe3C+H2O=3Fe+CO+H2 Fe3C+CO2=3Fe+2CO×
1650×
6
45#钢边缘到心部的组织变化
7
边缘半脱碳层较薄,白色的为铁素体, 黑色的为珠光体,铁素体的转变量明显大 于黑色珠光体组织,导致硬度强度降低, 失去了使用性能 。
表3.2.1 不同情况下45#钢的力学性能指标
16
魏氏组织的影响
魏氏组织对钢的性能影响更甚于过热粗 晶组织,具有魏氏组织的钢的塑性和冲击韧 性更低。 魏氏组织一般可采取细化晶粒退火予以 清除,但严重的魏氏组织则必须通过锻造的 方法来消除。
17
3.过热
当超过热处理温度AC3以上时,就会形成 过热。 本实验以15#钢及945钢的两种典型过热 组织为例。
22
过热的预防及矫正
选择正确的加热温度,热压力加工时的 加热温度至少要低于钢的熔点100℃ 采用正确的加热方法 控制热加工时的变形量及终止温度 过热组织已经形成,如图中的晶粒粗大, 可采用细化晶粒的退火,正火或锻造等
23
4.过烧
W18Cr4V正常热处理工艺
24
W18Cr4V的过烧组织
由于加热温 度过高,以 至晶界局部 融化,产生 鱼骨状的莱 氏体共晶组 织。
1650×
25
过烧的预防及矫正
金属的过烧是不允许的,所以要在 热处理过程中进行积极的预防。 在加热时尽可能采用较低的温度,一般 的金属热变形应在低于融化温度100℃以 下进行。 对于加热炉均匀加热,采用还原性气氛, 掌握透热时间,避免火焰直接喷射到金 属的表面。 提高测温仪表的灵敏度和按期矫正。
12
2.魏氏组织
45#钢过热以后缓慢冷却至常温,得到 的是粗晶粒的组织,铁素体沿晶界呈网络状 分布。若在Ar3~Ar1温度区间冷速过快,由于 过冷度较大铁素体不能充分沿奥氏体晶界析 出,而是在奥氏体内部自发形成晶核,并沿 一定的晶面取向分布。
13
45# 魏氏组织
660Х
165Х
14
混合型魏氏组织
26
5.欠热
45#钢为亚共析钢,亚共析钢的加热温度 为AC3+(30~50)℃为正常加热温度。而欠 热温度低于奥氏体化温度,处于两相区, 没有完全奥氏体化,组织中的铁素体属 未溶铁素体,使材料的硬度强度降低。
27
45#钢的欠热组织
×
1650×
28
45#钢欠热组织
图中凹陷 组织为未 溶铁素体 组织,凸 出区域为 马氏体, 从图中我 们可以观 察到片状 和板条型 的马氏体。
31
3.过热:15#钢由于过热造成了晶粒粗大,并且 形成了一条沿晶界开裂的裂纹。945钢为典型 的船用钢,由于淬火温度过高,形成了粗大的 板条马氏体及残余奥氏体。 4.过烧:由于过烧,W18Cr4V晶界已经局部融化, 产生鱼骨状的莱氏体共晶组织。存在局部融化 的工件不能再用热处理的方法补救,应予报 废 。
常见金属热处理缺陷组织研究
学生:张琳 学号:06105228 指导老师:王桂芳
1
实验背景
在当今社会生产中,金属材料的 应用是十分广泛的,但是在热处理过 程中,受到加热时间,加热温度,保 温时间等多种因素的影响,会出现过 热,欠热,晶粒粗大,脱碳,魏氏组 织等多种热处理常见缺陷,为材料的 使用埋下隐患。
2
实验内容
1.实验材料及金相试样的制备
2.试样金相照片及扫描电镜照片的制备 3.试样的显微硬度测试 4.正常组织与缺陷组织的比较
3
实验仪器
OLYMPUS-311U金相显微镜 S-240扫描电镜 P-1抛光机 HRS—10显微硬度计
4
1.脱碳
脱碳是钢加热时表面碳含量降低的现象
32
5.欠热:欠热温度低于奥氏体化温度,处于两相 区,材料没有完全奥氏体化,铁素体的转变量 多于马氏体的转变量,铁素体硬度低,所以使 材料的硬度降低。
33
谢谢各位老师!
34
29
各种缺陷组织的硬度比较
各种缺陷组织的硬度 800 700 600 500 400 300 200 100 0 1 材料
45#钢1正常组织 945钢晶粒粗大 15#钢晶粒粗大 W18Cr4V过烧 45#钢2欠热组织 45#钢3魏氏组织 45#钢4脱碳组织
HV
30
结论
1.脱碳:通过45#钢的组织分析得出试样边缘的铁素 体转变量远远大于珠光体转变量 。通过显微硬度 测试,试样心部的硬度大于边缘的硬度。 2.魏氏组织:45#钢中铁素体沿晶界呈网络状分布, 在晶内形成羽毛状和垂直状的混合型魏氏组织。 通过显微硬度测试,其硬度大约为HV255.32,低于 正常硬度,因此魏氏组织影响了材料的性能,塑 性和冲击韧性较低。
18
15#钢的晶粒粗大组织
图中组 织晶粒粗 大。同时 我们还可 以看到一 条明显的 裂纹,沿 晶界分布。
165×
19
945钢的过热组织
945钢为 本质细晶粒 钢,但是由 于加热温度 远远超过奥 氏体化温度 以上所以造 成了严重的 晶粒粗大。
660×
20
945钢的过热组织
21
945钢的过热组织
8
正常组织与缺陷组织的组织比较
330×
330×
9
45#钢的正常组织扫描电镜图
10
正常组织与缺陷组织的硬度比较
45#钢正常组织与缺陷组织的硬度比较 250 200 150
HV
100 50 0 0 2 4 距边缘的距离/mm 6 8
45#钢缺陷组织 45#钢正常组织
11
脱碳的预防及补救
1.在热加工生产时尽可能降低钢的加热温 度及在高温下停留的时间 2.合理的安排工艺路线及留放加工余量. 3.调节空燃比,使炉气带还原性 4.制备气氛可控碳势,使碳势接近或等于 钢的碳含量