金属的低倍组织缺陷分析
金属的低倍组织的缺陷分析
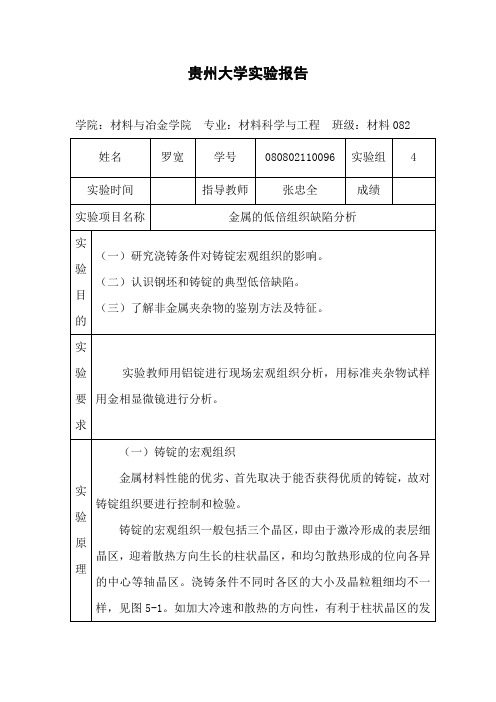
学院:材料与冶金学院专业:材料科学与工程班级:材料082
姓名
罗宽
学号
080802110096
实验组
4
实验时间
指导教师
张忠全
成绩
实验项目名称
金属的低倍组织缺陷分析
实验目的
(一)研究浇铸条件对铸锭宏观组织的影响。
(二)认识钢坯和铸锭的典型低倍缺陷。
(三)了解非金属夹杂物的鉴别方法及特征。
凝固时枝晶间隙得不到液体寂充,形成的显微缩孔
方框偏析
方框形暗色条带
原钢锭为方形,凝固时杂质被推向柱状晶的前沿,聚焦在与中心等轴晶相遇处,酸蚀后出现腐蚀较深的方框区域
皮下气泡
靠近表皮呈圆或椭圆形光滑孔洞,热加工后呈垂直表面的裂纹
浇铸条件不良,如锭模涂料中的水分与钢液作用产生气体形成表皮层所泡
白点
在横向酸蚀试样上为细和三发丝状裂纹,无次序分布。在纵向断口上呈银亮色白斑
钢中氢原子析出并聚集成氢分子,产生巨大压力,使钢低温相变时开裂
缩孔残余
中心树根状孔洞
缩孔未切除干净
(三)非金属夹杂分析
金属材料中的非金属夹杂物、不仅降低零件的性能,还会导致灾难性事故,故应严加控制和检查。
对一些已知特征的非金属夹杂,如纯钢中的氧化铜夹杂,钢中的氧化物、硫化物,氮化物等,可用常规金相方法来辨别;对那些难以在昔通光学显微镜下鉴别的未知夹杂物,还需采用其它研究手段,如电子探针,透射电镜、X射线铅构分析以及二次离子质谱仪(SIMS)等来确定其组成和结构。
实验总结
钢坯的典型低倍缺陷,为控制钢材质量,铸锭开坯后,需对成材前的钢坯按国家标准进行低倍组织检验,并对缺陷进行评级。常见的低倍缺陷有:疏松、方框偏析、蜂窝气泡、白点及缩孔残余等。对一些已知特征的非金属夹杂,如纯钢中的氧化铜夹杂,钢中的氧化物、硫化物,氮化物等,可用常规金相方法来辨别;对那些难以在昔通光学显微镜下鉴别的未知夹杂物,还需采用其它研究手段。
高强船板低倍组织缺陷原因分析
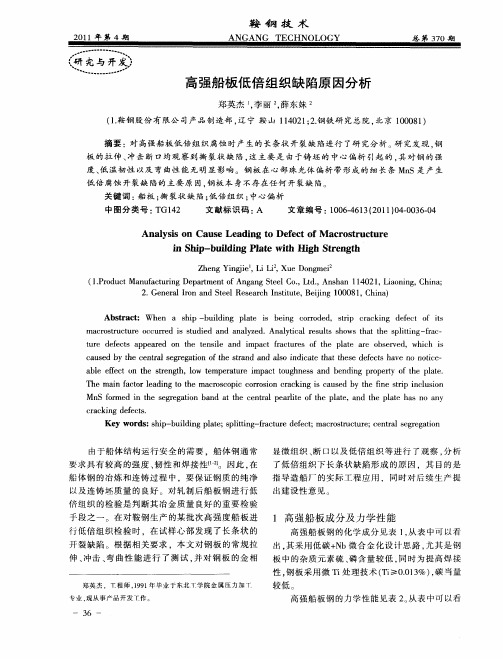
修 回 日期 :0 1 0 — l 2 1- 6 0
米 米 米 米 米 米 米 米 米 米 米 米 米 米 米 米 米 米 米 米 米 米 米 米 米 米 米 米 米 米 米 米 米 米 米 米 米 米 米 米 米 米 米 米
山 东 钢 铁 注 资非 洲 矿 业 协 议 终 成 定 局
T noi 铁 矿 已探 明资 源 储量 为 15亿 t平 均 品位 3 %左 右 , 全球 已探 明的 资源 量 最 大 的磁 铁 okli l 0 , 0 是
摘 要 : 高强船板 低倍 组 织腐蚀 时产 生的 长条状 开 裂缺 陷进 行 了研 究 分析 。 究发 现 , 对 研 钢 板 的拉 伸 、 冲击 断 口均观 察 到撕 裂 状缺 陷 , 主要 是 由于铸 坯 的 中心偏析 引起 的 , 对钢 的 强 这 其
度 、 温韧 性 以及 弯曲性 能 无 明显影 响 。钢 板在 心 部珠 光体 偏 析 带形 成的 细 长条 Mn 低 S是 产生
属 ,0பைடு நூலகம்0 1 : 一 0 2 1()1l.
变为 断续 的单 个 或几 个 点坑 呈长 条 状排 列 。深 入 观察 单个 点坑 可 以看 出 , 点坑 的边缘 光 滑 圆润 . 为
典 型 的腐 蚀后 产 生 的腐蚀 孑 洞 。 因 此 , 于 心 部 L 由
组 织 中存 在 大 量 细 长 条 Mn S夹 杂 ,低 倍 观察 时 采 用 酸蚀 检 验后 容 易 出现腐 蚀 孔洞 。这 些 长条 状 孔 洞 并非 钢板 本 身存 在 的缺 陷 。从 高强 船板 的生
c u e y t e c n r ls g e ai n o e s a d a d as n i ae t a h s e e t a e n oi e a s d b h e t e r g t ft t n n lo i d c t h t e e d f cs h v o n t — a o h r t c a l f c n t e sr n t ,lw e e a u e i a t tu h e s a d b n i g p o e t ft e p ae b e e f t o h te gh o tmp r t r mp c o g n s n e d n rp r o h l t . e y T e ma n f c o e d n o t e ma r s o i o r so r c i g i c u e y t e f e sr n l so h i a t rla i g t h c o c p c c ro i n c a k n s a s d b h n t p i c u i n i i Mn o me n t e s g e ai n b n t t e c n r lp a l e o h l t , n h l t h s n n S fr d i h e r g t a d a h e ta e ri ft e p a e a d t e p ae a o a y o t c a k n ee t. rc ig d fcs Ke r s s i — u l i g p a e s l t g fa t r ee t ma r sr c u e c n r l e r g t n y wo d : h p b i n lt ; p i i — r cu e d f c; c o tu t r ; e t g e a i d tn a s o
低倍组织检验
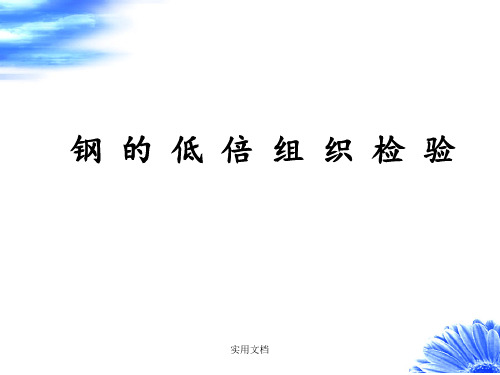
不均匀现象。
实用文档
偏析
方框偏析 局部偏析
实用文档
偏析
主要危害:造成钢材中化学成分的不均匀性 ; 将导致钢材的机械性能、物理性能的降低。
硫偏析:能 破坏金属 的连续性, 锻造和轧 制时会引起 热脆而开裂。
磷偏析:会造 成冷脆,并促 进钢的回火
脆性。
实用文档
实用文档
危害
发纹
实用文档
发纹
如何检 验
根据 GB/T10121-2008《钢材塔形发纹磁粉检验方 法》,将钢材车制成塔形试样,经磁力探伤或热 酸洗后计算发纹数量和长度。
实用文档
发纹
酸蚀检验法优点:真实地反应表面缺陷,不会 把皮下缺陷也显示出来,缺点是侵蚀过深会使缺 陷扩大,或把流线误判为发纹。
实用文档
主要缺陷评定原则
实用文档
注意事项
1、试样粗糙度要保证,不得有油污和加工伤痕; 2、酸洗时温度和时间要适宜; 3、清洗时试样表面的腐蚀产物要刷干净,用热水喷淋后立
即吸干或吹干; 4、酸洗之后样品尽可能立即评定; 5、对于酸洗不合格样品在重新酸洗之前,须重新进行磨加
工,磨去腐蚀层。
实用文档
检测结果描述
发纹的最大长度
实用文档
实用文档
实用文档
样品制备
取样部位:检验目的不同,选取部位不同。
检验钢材表面缺陷:选取钢材和零件的外表面; 检验钢材质量:钢材的两端,钢锭的头部; 失效分析:缺陷处取样。 横向试样厚度:20mm 表面粗糙度:不大于1.6um。
实用文档
热酸蚀试剂和试验规范
实用文档
主要操作步骤
样品制备
加热酸洗
冲洗吹干
第十章 低倍检验
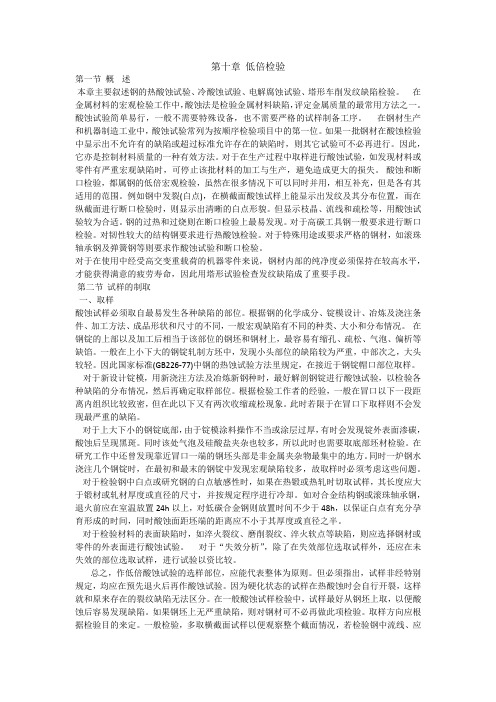
第十章低倍检验第一节概述本章主要叙述钢的热酸蚀试验、冷酸蚀试验、电解腐蚀试验、塔形车削发纹缺陷检验。
在金属材料的宏观检验工作中,酸蚀法是检验金属材料缺陷,评定金属质量的最常用方法之一。
酸蚀试验简单易行,一般不需要特殊设备,也不需要严格的试样制备工序。
在钢材生产和机器制造工业中,酸蚀试验常列为按顺序检验项目中的第一位。
如果一批钢材在酸蚀检验中显示出不允许有的缺陷或超过标准允许存在的缺陷时,则其它试验可不必再进行。
因此,它亦是控制材料质量的一种有效方法。
对于在生产过程中取样进行酸蚀试验,如发现材料或零件有严重宏观缺陷时,可停止该批材料的加工与生产,避免造成更大的损失。
酸蚀和断口检验,都属钢的低倍宏观检验,虽然在很多情况下可以同时并用,相互补充,但是各有其适用的范围。
例如钢中发裂(白点),在横截面酸蚀试样上能显示出发纹及其分布位置,而在纵截面进行断口检验时,则显示出清晰的白点形貌。
但显示枝晶、流线和疏松等,用酸蚀试验较为合适。
钢的过热和过烧则在断口检验上最易发现。
对于高碳工具钢一般要求进行断口检验。
对韧性较大的结构钢要求进行热酸蚀检验。
对于特殊用途或要求严格的钢材,如滚珠轴承钢及弹簧钢等则要求作酸蚀试验和断口检验。
对于在使用中经受高交变重载荷的机器零件来说,钢材内部的纯净度必须保持在较高水平,才能获得满意的疲劳寿命,因此用塔形试验检查发纹缺陷成了重要手段。
第二节试样的制取一、取样酸蚀试样必须取自最易发生各种缺陷的部位。
根据钢的化学成分、锭模设计、冶炼及浇注条件、加工方法、成品形状和尺寸的不同,一般宏观缺陷有不同的种类、大小和分布情况。
在钢锭的上部以及加工后相当于该部位的钢坯和钢材上,最容易有缩孔、疏松、气泡、偏析等缺馅。
一般在上小下大的钢锭轧制方坯中,发现小头部位的缺陷较为严重,中部次之,大头较轻。
因此国家标准(GB226-77)中钢的热蚀试验方法里规定,在接近于钢锭帽口部位取样。
对于新设计锭模,用新浇注方法及冶炼新钢种时,最好解剖钢锭进行酸蚀试验,以检验各种缺陷的分布情况,然后再确定取样部位。
铝锻件低倍组织检验方法
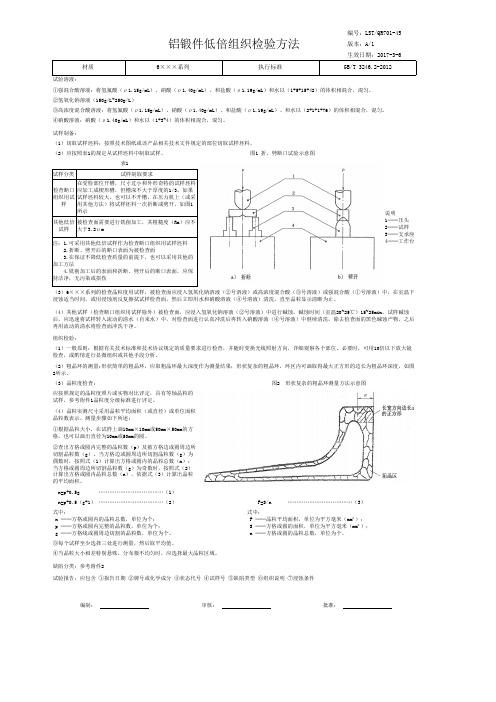
试样分类编制:审核:批准:①根据晶粒大小,在试样上画10mm×10mm或50mm×50mm的方格,也可以画出直径为10mm或50mm的圆。
②查出方格或圆内完整的晶粒数(p)及被方格边或圆周边所切割晶粒数(g)。
当方格边或圆周边所切割晶粒数(g)为偶数时,按照式(1)计算出方格或圆内的晶粒总数(n);当方格或圆周边所切割晶粒数(g)为奇数时,按照式(2)计算出方格或圆内晶粒总数(n),依据式(3)计算出晶粒的平均面积。
(2)应按照表1的规定从试样坯料中制取试样。
式中:F ──晶粒平均面积,单位为平方毫米(mm²); S ──方格或圆的面积,单位为平方毫米(mm²); n ──方格或圆的晶粒总数,单位为个。
(2)粗晶环的测量:形状简单的粗晶环,应取粗晶环最大深度作为测量结果;形状复杂的粗晶环,环区内可画取得最大正方形的边长为粗晶环深度,如图2所示。
图2 形状复杂的粗晶环测量方法示意图(3)晶粒度检查:应按照规定的晶粒度照片或实物对比评定,具有等轴晶粒的试样,参考附件1晶粒度分级标准进行评定。
(4)晶粒实测尺寸采用晶粒平均面积(或直径)或单位面积晶粒数表示,测量步骤如下所述:组织检验:(1)一般原则:根据有关技术标准和技术协议规定的质量要求进行检查,并随时变换光线照射方向,详细观察各个部位。
必要时,可用10倍以下放大镜检查,或酌情进行显微组织或其他手段分析。
(4)其他试样(检查断口组织用试样除外)被检查面,应浸入氢氧化钠溶液(②号溶液)中进行碱蚀,碱蚀时间(室温20~25℃)15~25min。
试样碱蚀后,应迅速将试样转入流动的清水(自来水)中,对检查面进行认真冲洗后再转入硝酸溶液(④号溶液)中继续清洗,除去检查面的黑色碱蚀产物,之后再用流动的清水将检查面冲洗干净。
③每个试样至少选择三处进行测量,然后取平均值。
④当晶粒大小相差特别悬殊,分布极不均匀时,应选择最大晶粒区域。
低倍组织检验
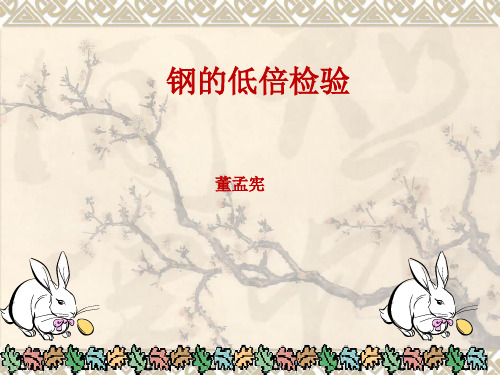
试样的保存: 为了将试样保存一定的时间,建议采用下列方法: a、中和法:用10%氨水酒精溶液浸泡后,再以热水冲洗刷净,并吹干; b、钝化法:短时间地浸入浓硝酸(大约5 s);钝化后的试样用热水冲洗刷 净并干燥;
c、涂层保护法:涂清漆、塑料膜等
d、典型低倍组织用数码相机将图像拍照下来,供以后学习参考。
钢的低倍检验
董孟宪
概述
低倍检验的地位 在产品验收、新品试制、工艺调整与控制方面占有十分重要的地位。 低倍检验为金相检验的一部分,低倍相对于高倍而言。 低倍试验包括酸蚀低倍、塔形发纹、S印、P印、流线等方法。 验收检验项目: 1、圆钢 (优质、高级优质、特级优质)
1)优钢:横截面酸浸低倍组织为合格级别: 一般疏松、中心疏松、锭型偏析,而低倍缺陷一 般要求不得有目视可见的缩孔、气泡、裂纹、夹杂、翻皮和白点等。 2)合结钢:横截面酸浸低倍组织为合格级别: 一般疏松、中心疏松、锭型偏析、一般点状偏 析、边缘点状偏析,而低倍缺陷一般要求不得有目视可见的缩孔、气泡、裂纹、夹杂、翻皮 、白点、晶间裂纹等。 3)轴承钢:产品标准自带评级标准,横截面酸浸低倍组织为合格级别: 一般疏松、中心疏松 、锭型偏析、一般点状偏析、边缘点状偏析,而低倍缺陷一般要求不得有目视可见的缩孔、 皮下气泡、裂纹、夹杂、白点、过烧等 2、圆坯、方坯 1) 管坯横截面酸浸低倍组织试片上的中心疏松、 缩孔、 中心裂纹、 中间裂纹、 皮下裂纹、 皮下气泡应按附录A评定, 其合格级别应分别不大于2 级。结晶组织。 2)优钢及合结钢按YB/T153-1999,评定项目:中心疏松、中心偏析、缩孔、内部裂纹(角部 裂纹、皮下裂纹、中间裂纹、中心裂纹) 、皮下气泡、非金属夹杂物、白亮带、夹渣、异金 属夹杂、翻皮等。 优质非合金钢、 特殊质量非合金钢、 合金钢连铸坯应按 Y B / T1 5 3 进行低倍组织评定, 其合格级别由供需双方协商确定, 如供方能保证低倍合格, 可不作检验 普钢、高强钢方坯参照YB/T153-1999进行评定。
金属的低倍组织缺陷分析
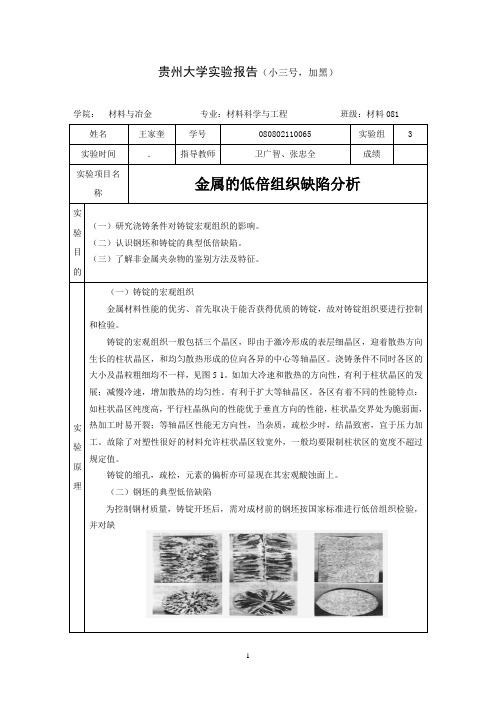
贵州大学实验报告(小三号,加黑)
学院:材料与冶金专业:材料科学与工程班级:材料081
图5-1 不同浇铸条件下铝锭的宏观组织
℃浇铸,3mm厚铁模 b)800℃浇铸,10mm厚铁模 c)680℃浇铸,100mm厚铁模加硅铁粉
图5-2 钢中常见的低倍缺陷
a)一般疏松 b)方框偏析 c)皮下气泡 d)白点 e)缩孔残余
次消光和发亮现象。
对于
透明的,各向同性的球形夹物,
SiO 2,在明场下呈深灰 图5-3 钢中的非金属夹杂
Al 2O 3 b )MnS c )TiN d )玻璃质SiO 2明场下光环特征 e )玻璃质SiO 2,偏
图5-4 偏振光装置示意图
几种非金属夹杂物的特征
暗场偏振光
,不规则外形小颗粒成群分布,透明、淡黄色透明,弱各向异性
注:各学院可根据教学需要对以上栏目进行增减。
表格内容可根据内容扩充。
低倍组织检验分析
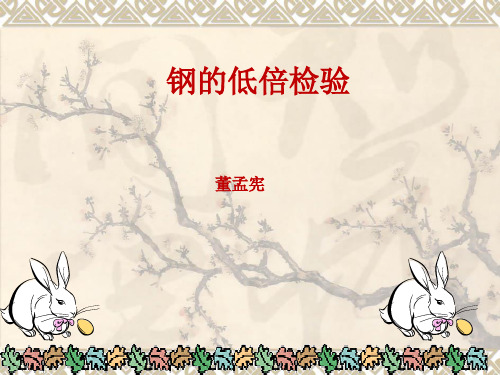
酸浸装置:常用的酸洗槽有,铅槽、玻璃钢槽、塑料槽、华岗石槽以及瓷盆或 烧杯等。瓷盆或烧杯不建议使用。二者都均易坏漏和破碎。有不安全隐患。
加热体:根据所用的容器可采用相应的加热体,如蒸汽、电热石英管、电炉等。 刷 子:将腐蚀后的试样用毛刷将试样表面的沉积物刷去。 吹风机:将刷洗清洗的试样用吹风即吹干。
a、热切时不小于20mm; b、冷切时不小于10mm; c、烧割时不小于40mm 热酸浸试样表面粗糙度应不大于Ra1.6μm,冷酸浸蚀试样表面粗糙度不 大于Ra0.8μm。 试样尺寸: 棒材:试样厚度一般为20mm,试样面垂直于钢材(坯)的延伸方向。 钢板:低倍试面的尺寸一般长为250mm
20mm
排风设备酸洗装置及酸洗必备工具
样表面的铜层,后用水冲净。
(1)不锈钢表层有一层黑色可用不锈钢洗液刷洗,用5%重铬酸钾 清洗不锈钢和结
+10%硫酸水溶液
构钢溶液
H2So4 1升 +K2Cr2O7 500克+H2O10升 (2)结构钢用10%硝酸水溶液刷擦
酸洗过程注意事项: 试样酸浸前,应将试样面上的油污洗净,去污时可采用去污粉。当
酸浸试样到了预期腐蚀程度后,将试样从酸洗容器中取出,然后用毛刷 将试样表面上的腐蚀产物在热水洗下刷洗后将试样吹干。
当酸浸试样为不锈钢时,酸浸后将试样从酸池中取出用清水冲净, 然后用不锈钢清洗液将表面黑色沉淀物刷洗干净后将试样吹干。
如果试样腐蚀过深,必需将试样重新进行加工,除去1mm,在进行酸浸 试验。
钢与合金
碳素结构钢,合金 钢
合金钢
硝酸60 mL,盐酸200 mL,氯化高铁,过硫酸铵,水50 mL
- 1、下载文档前请自行甄别文档内容的完整性,平台不提供额外的编辑、内容补充、找答案等附加服务。
- 2、"仅部分预览"的文档,不可在线预览部分如存在完整性等问题,可反馈申请退款(可完整预览的文档不适用该条件!)。
- 3、如文档侵犯您的权益,请联系客服反馈,我们会尽快为您处理(人工客服工作时间:9:00-18:30)。
金属的低倍组织缺陷分析一、原理概述金属的低倍组织缺陷检验也称为宏观检验。
它是用肉眼或不大于十倍的放大镜检查金属表面、断口或宏观组织及其缺陷的方法。
宏观检验在金属铸锭、铸造、锻打、焊接、轧制、热处理等工序中,是一种重要的常用检验方法。
这种检验方法操作简便、迅速,能反映金属宏观区域内组织和缺陷的形态和分布特点情况。
使人们能正确和全面的判断金属材料的质量,以便指导科学生产、合理使用材料。
还能为进一步进行光学金相和电子金相分析作好基础工作。
宏观检验包括低倍组织及缺陷检验(包括酸蚀、硫印、塔形车削以及无损控伤等方法)和断口分析等。
1.较典型的宏观缺陷较典型的宏观缺陷有偏析、疏松、缩孔、气泡、裂纹、低倍夹杂、粗晶环等。
(1) 偏析合金化学成分不均匀的现象叫做偏析。
根据偏析的范围大小和位置的特点,一般可以分为三种。
即晶内偏析和晶间偏析、区域偏析、比重偏析。
晶内偏析和晶间偏析如固溶体合金浇注后冷凝过程中,由于固相与液相的成分在不断的变化,因此,即使在同一个晶体内,先凝固的部分和后凝固的部分其化学成分是不相同的。
这种晶内化学成分不均匀的现象叫晶内偏析。
这种偏析常以树枝组织的形式出现,故又称为枝间偏析。
这种偏析一般通过均匀退火可以将其消除。
基于同样的原因,在固溶体合金中先后凝固的晶体间成分也不相同,这种晶体间化学成分不均匀现象叫做晶间偏析。
区域偏析在铸锭结晶过程中,由于外层的柱状晶的成长把低熔点组元、气体及某些偏析元素推向未冷却凝固的中心液相区,在固、液相之间形成与锭型外形相似形状的偏析区。
这种形态的偏析多产生在钢锭结晶过程,由于钢锭模横断面多为方形,所以一般偏析区也是方框形,故常称为方框偏析。
在酸浸试片上呈腐蚀较深的,并由暗点和空隙组成的方形框带。
这种偏析是一种下偏析,即铸锭的外层是富集高熔点组元,而铸锭心部则富集了低熔点的组元和杂质。
与正偏析相反的是反偏析。
反偏析恰与正偏析相反。
当合金的铸锭发生反偏析时,铸锭表面溶质高于合金的平均成分,中心人溶质低于合金的平均成分;有时铸锭表面富集低熔点组元和杂质,严重时可在铸锭表面形成反偏析瘤。
反偏析的形成原因,一般认为,结晶温度范围宽的合金,在凝固过程中形成粗大树枝晶时,枝晶间富溶质的金属液在凝壳的收缩压力、熔液内部释出的气体压力、液柱静压力、大气压力的作用下,沿着枝晶间的毛细管通道向外移动,到达铸锭表层,冷凝后形成反偏析。
在有色合金中Cu-Sn和Al-Cu合金是发生反偏析的典型合金。
重力偏析在合金凝固过程中,如果初生的晶体与余下的溶液之间比重差较大,这些初生晶体在溶液中便会下沉或上浮。
由此所形成的化学成分不均匀现象称为重力偏析,亦称为比重偏析。
Cu-Pb、Sn-Sb、Al-Sb等合金易于产生重力偏析。
(2) 缩孔和疏松在铸锭的头部、中部、晶界及枝晶间,常常有一些宏观和显微的收缩孔洞,统称为缩孔。
容积大而集中的缩孔称为集中缩孔;细小而分散的缩孔称为疏松。
其中出现在晶界和枝晶间的缩孔又称为显微疏松。
缩孔和疏松的形状不规则,表面不光滑,易与较圆滑的气孔相区别。
产生缩孔和疏松的直接原因,是金属液凝固时发生的凝固体收缩。
残余缩孔在金属材料的横向酸浸试片的轴心部位,易于识别。
疏松在横向酸浸试片上呈暗黑色的小点和细小的孔隙。
这是因为疏松本身就是显微孔洞,而且在这些显微孔洞的周围总是伴随着偏析,因而容易受到浸蚀。
疏松小点可能分布在试片检验面的各个部位。
根据其所在位置,可将疏松分为中心疏松和一般疏松。
(3) 气孔根据气孔在铸锭中出现的位置,可将其分为表面气孔、皮下气孔和内部气孔三类。
根据气孔的成因,又可分为析出型气孔和反应型气孔两类。
析出型气孔是由于金属在熔融状态时能溶解大量的气体,在冷凝过程中,又由于溶解度随温度的降低而急剧的下降,特别是在金属凝固时,由于气体溶解度的剧烈下降而析出大量的气体。
当金属完全凝固,气体不能逸出时,在铸锭或件内部形成了气孔。
反应型气孔是金属在凝固过程中,与模壁表面水份、涂料及润滑剂之间或金属液内部发生化学反应,因而产生的气体形成气泡,且来不及上浮逸出而形成的气孔。
气孔一般是圆形的,表面较光滑。
压力加工时气孔可被压缩,但难以压合,常常在热加工和热处理过程中产生起皮起泡现象。
(4) 裂纹大多数成分复杂或杂质总量较高或有少量非平衡共晶的合金,都有较大的裂纹倾向。
尤其是大型铸锭。
在冷却强度大的连铸条件下,产生裂纹的倾向更大。
在凝固过程中产生的裂纹称为热裂纹。
凝固后冷却过程中产生的裂纹称为冷裂纹。
热裂纹多沿晶界扩展,曲折而不规则,冷裂纹常为穿晶裂纹,多呈直线扩展。
除开铸锭裂纹外,由于热加工如轧制、锻压、热处理过程中都可能出现裂纹。
锻轧裂纹多是由于不适当的锻造或轧制操作以及加热工艺而造成的。
产生在中心部位具有龟裂特征。
有时也产生在工件边缘,这是表现为垂直于边缘呈开放开裂。
除开上述裂纹外,发纹也是钢材中易于出现的一种缺陷。
发纹是纲中气孔和夹杂在加工变形过程中沿锻轧方向被延伸所形成的细粘裂纹。
发纹是应力集中的地方,对疲劳强度有着严重的影响。
一般对制造重要机件所用钢材,都要做塔形车削发纹的检验。
对发纹的数量、大小及分布情况都有严格的限制。
塔形发纹检验是将钢材按规定车成阶梯形的试样,后用酸蚀法或磁力探伤法进行检查。
(5) 低倍夹杂在酸浸低倍试样上,有的肉眼可以看到耐火材料、炉渣及其它非金属夹杂物,这些较粗大的夹杂称为低倍夹杂。
它们在酸浸试片上以镶嵌的形式存在,并保持其固有的各种颜色,常见的有灰白色、米黄色和暗灰色等。
有些低倍夹杂在制片时可能脱落,而表面为空洞。
空洞的特点区别于气泡是它的边缘不整齐,呈海绵状。
通过低倍检验在钢坯或钢材酸浸试片上显露出的夹杂物,分为3类:(1)外来金属。
由误入钢锭模内钢水中的金属条、块、片及未来得及熔化的脱氧合金残余等所造成的。
由于被浸蚀的情况与钢不同,外来金属多呈边缘清晰、颜色与周围显著不同的几何图形,并有的在边缘上有密集的针孔;(2)外来非金属夹杂。
主要来源于未来及浮出而被凝固在钢锭中的熔渣及耐火材料。
小的非金属夹杂颗粒,一般被腐蚀掉而在试样上留下细小的圆形孔隙。
较大的非金属颗粒,特别是硅酸盐和氧化铝,常残留在试样上;(3)翻皮。
下注时钢锭模内钢流冲破上升的钢液面上的半凝固膜,并将其卷入钢中所致。
在钢坯和钢材中,翻皮可以任何形状和大小存在。
在热酸蚀横向试样上,一般呈颜色与周围不同、形状不规则的弯曲狭长条形,且其中或周边常有氧化物夹杂和气孔等存在。
(6) 流线流线是金属中的低熔点成分和带状组织偏析在轧制或挤压时伸展而形成的。
同时,铸锭的晶粒在轧制过程中也被拉长成条状。
经过再结晶加热过程能使长条形晶粒恢复成等轴晶粒,但是由于低熔点成分和带状组织伸长所形成的条纹分布仍然存在。
在钢材的纵向截面上经抛光和酸浸后,用肉眼可以看到这种条纹状的线条。
这种宏观组织称为纤维组织,又称为流线。
不能认为合理分布的流线是一种缺陷。
因为几乎所有经过轧制、挤压或锻造的金属型材、制件中都存在着流线。
但是应认识到由于这种流线的分布,会引起在性能上各向异性反映。
试验也表明:在钢中顺纤维方向切取的试样机械性能要比横纤维方向试样的高。
因此,控制流线的合理分布;了解应力与流线分布及机械性能间的关系是至为重要的。
(7) 粗晶环粗晶环是铝合金挤压制品中的主要缺陷之一。
铝合金挤压件在随后的加热时引起外层晶粒粗大,这种现象称为粗晶环。
其表征特点是:对单孔挤压棒材来说,粗大组织区呈对称环状。
多孔挤压棒材呈偏心月牙状。
粗晶环的存在会剧烈降低机械性能。
粗晶环还具有组织“遗传性”。
用有粗晶环的毛坯进行模压后,原来的粗晶区仍然保留,造成模压件之组织不匀及影响表面质量。
甚至在热处理过程中还易于引起开裂。
研究表明,形成粗晶环根本原因是挤压变形的不均匀笥所致。
2.低倍组织及缺陷浸蚀方法低倍组织浸蚀方法分为热酸浸蚀法、冷酸浸蚀法和电解腐蚀法三种。
本次实验采用冷酸浸蚀,有关酸浸蚀液成分参见附录1-1。
冷酸浸蚀操作要点如下:(1) 根据材料种类选用合适的和一定配比的浸蚀液。
(2) 试样检验面的光洁度应在7以上,酸蚀前应将检验面擦净,去除油污。
(3) 用擦蚀法时,将酸液慢慢倒在置地耐酸盆中的试样同上,然后用刷子将酸液刷匀,直至清晰显示出低倍组织和缺陷为止。
(4) 浸蚀好后,用水冲掉酸液,并用碱水中和,然后用再热水冲洗,立即吹干。
3.断口分析金属断口按其断裂方式可分为脆性断口(晶粒状断口)、韧性断口(纤维状断口)和疲劳断口。
根据其断口的形状可以研究金属的强度和零件受力破裂的原因。
脆性断口金属断裂前未经过塑性变形,有的沿晶界断裂(称为晶间断裂)有的沿晶内断裂(称为穿晶断裂),这种断口原来的晶粒未被歪曲,其大小和形状能保持焉。
晶界断裂的原因除了金属的本性以外,往往是由于金属过烧,晶界上发生氧化或杂质存在于晶界,因而降低了晶界的强度。
晶内断裂是由于晶粒本身强度不高,或在结晶过程中沿晶粒内某些晶面夹入了杂质。
断口的形状见实物。
韧性断口断裂以前发生了塑性变形。
原晶粒被歪曲(拉长或破碎),不再保持原来的大小、形状,因而不能从这些断口中研究金属内部组织。
断口的形状见实物。
疲劳断口承受交变应力的机械零件(例如轴)破裂首先由表面小裂纹开始。
由于交变应力的作用,一边摩擦一边扩大,形成了螺旋形光滑平面。
这种断口称为疲劳断口。
在断口上常常看见气孔、裂纹和疏松等缺陷。
在工厂中进行断口检验除利用破断零件自然断裂表面外,一般可用宏观检验完了的试样来制备成断口试样。
打断口的试样其锯切深度不应大于试样总厚度的1/3,锯切部位应在要求检查处。
断口上应有油污和水痕,在观察时也和低倍磨片一样,应转换试样方向和光线入射角度。