第一部分合成氨生产工艺解析
合成氨生产工艺碳化工段

图9-2碳化塔1 一气体分布器;2—分气板; 3—冷却管;4一挡板0. 6MPa和1. 2MPa两个等级。
第九章碳化工段第一节工艺流程及主要设备—、本;段任务(一)碳化工段的任务在变换气中,除含有合成氨所需的氢及氮之外,还含有26K左右的二氧化碳、一氧化碳(3.0〜3.8%)等气体。
二氧化碳、一氧化碳等气体不仅不是合成氨所需要的,而且对合成触媒有毒害作用,所以必须清除。
碳化工段的任务就是用浓氨水吸收变换气中的二氧化碳,并制成合格的碳酸氢铵。
二氧化碳被碳化吸收后,变换气成为合格的原料气(C02<0.2%;NH3<0.lg/m3),送压缩工段进一步压缩后送精炼工段。
本工段还要保证全厂氨和二氧化碳的平衡及本工段的水平衡,确保均衡生产。
碳化工段全过程包括:浓氨水的制备、浓氨水吸收二氧化碳生产碳酸氢铵、氨的回收以及悬浮液的分离。
(二)水洗的任务碳化水洗流程的任务用压力水洗去变换气中的部分二氧化碳,解决碳铵生产过程中氨和二氧化碳的平衡,同时能增加氨水和液氨的产量。
中压联尿水洗的任务用高压水将变换气中的二氧化碳洗至18%左右,以保证联尿生产中氨与二氧化碳的平衡。
(三)等压吸收的任务用软水或稀氨水吸收氨罐弛放气及合成放空气中的氨气,制成浓氨水供碳化生产使用,其余的气体送锅炉燃烧回收热能,或送造气吹风气回收燃烧。
二、工艺流程简述(一)碳化气体流程如图9-1所示,压力为1.12MPa的变换气从塔底依次通过碳化主塔、副塔、综合塔,在塔内变换气与浓氨水鼓泡反应,二氧化碳被氨水吸收,成为合格的原料气送压缩机三段入口。
在生产甲醇的氮肥厂,为保证甲醇触媒不中毒,在综合塔后,增设活性炭脱硫塔,使原料气中H2S含量<2ppm。
液体流程稀氨水和母液用泵从贮槽打入高位吸氨器或喷射吸收器,的氨气反应,其方程式如下:NH3+HzO=NH4OH+QNH4OH+NH4HCO3=(nh4)2co3+HzO+Q制成的浓氨水再经冷却排管降温后,送浓氨水贮槽。
合成氨的生产工艺流程
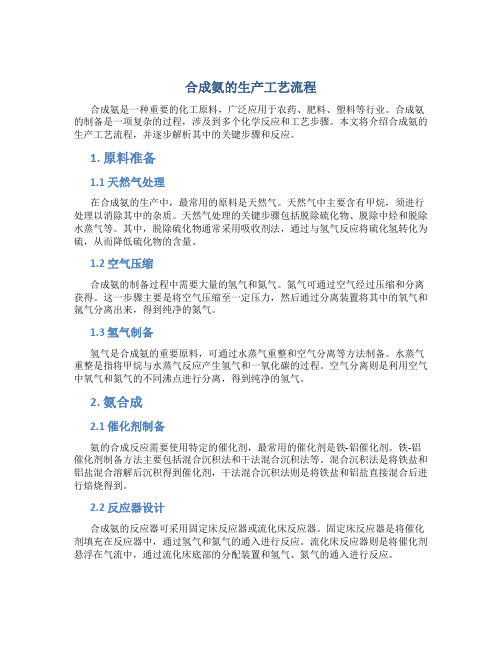
合成氨的生产工艺流程合成氨是一种重要的化工原料,广泛应用于农药、肥料、塑料等行业。
合成氨的制备是一项复杂的过程,涉及到多个化学反应和工艺步骤。
本文将介绍合成氨的生产工艺流程,并逐步解析其中的关键步骤和反应。
1. 原料准备1.1 天然气处理在合成氨的生产中,最常用的原料是天然气。
天然气中主要含有甲烷,须进行处理以消除其中的杂质。
天然气处理的关键步骤包括脱除硫化物、脱除中烃和脱除水蒸气等。
其中,脱除硫化物通常采用吸收剂法,通过与氢气反应将硫化氢转化为硫,从而降低硫化物的含量。
1.2 空气压缩合成氨的制备过程中需要大量的氢气和氮气。
氮气可通过空气经过压缩和分离获得。
这一步骤主要是将空气压缩至一定压力,然后通过分离装置将其中的氧气和氩气分离出来,得到纯净的氮气。
1.3 氢气制备氢气是合成氨的重要原料,可通过水蒸气重整和空气分离等方法制备。
水蒸气重整是指将甲烷与水蒸气反应产生氢气和一氧化碳的过程。
空气分离则是利用空气中氧气和氮气的不同沸点进行分离,得到纯净的氢气。
2. 氨合成2.1 催化剂制备氨的合成反应需要使用特定的催化剂,最常用的催化剂是铁-铝催化剂。
铁-铝催化剂制备方法主要包括混合沉积法和干法混合沉积法等。
混合沉积法是将铁盐和铝盐混合溶解后沉积得到催化剂,干法混合沉积法则是将铁盐和铝盐直接混合后进行焙烧得到。
2.2 反应器设计合成氨的反应器可采用固定床反应器或流化床反应器。
固定床反应器是将催化剂填充在反应器中,通过氢气和氮气的通入进行反应。
流化床反应器则是将催化剂悬浮在气流中,通过流化床底部的分配装置和氢气、氮气的通入进行反应。
2.3 反应条件合成氨的合成反应需要在一定的温度、压力和催化剂的存在下进行。
通常情况下,合成氨反应的温度约为350-450°C,压力约为200-300atm。
此外,还需要在反应器中加入适量的惰性气体(如氦气)以稀释氢气和氮气,以减少反应的热量和危险性。
2.4 反应过程合成氨的合成反应是一个多步骤的复杂过程。
合成氨合成工艺流程
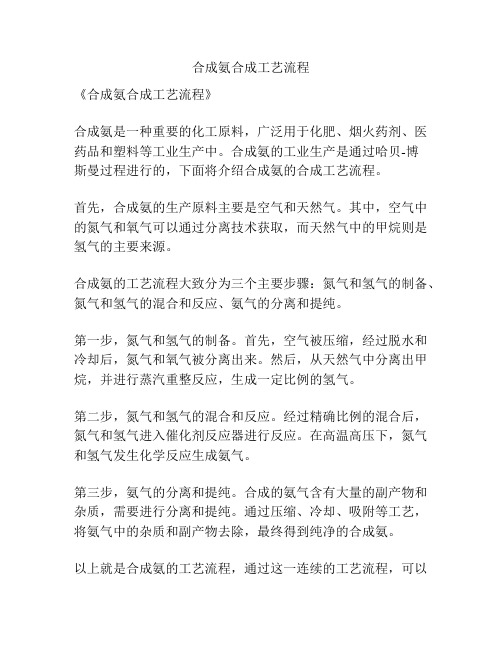
合成氨合成工艺流程
《合成氨合成工艺流程》
合成氨是一种重要的化工原料,广泛用于化肥、烟火药剂、医药品和塑料等工业生产中。
合成氨的工业生产是通过哈贝-博
斯曼过程进行的,下面将介绍合成氨的合成工艺流程。
首先,合成氨的生产原料主要是空气和天然气。
其中,空气中的氮气和氧气可以通过分离技术获取,而天然气中的甲烷则是氢气的主要来源。
合成氨的工艺流程大致分为三个主要步骤:氮气和氢气的制备、氮气和氢气的混合和反应、氨气的分离和提纯。
第一步,氮气和氢气的制备。
首先,空气被压缩,经过脱水和冷却后,氮气和氧气被分离出来。
然后,从天然气中分离出甲烷,并进行蒸汽重整反应,生成一定比例的氢气。
第二步,氮气和氢气的混合和反应。
经过精确比例的混合后,氮气和氢气进入催化剂反应器进行反应。
在高温高压下,氮气和氢气发生化学反应生成氨气。
第三步,氨气的分离和提纯。
合成的氨气含有大量的副产物和杂质,需要进行分离和提纯。
通过压缩、冷却、吸附等工艺,将氨气中的杂质和副产物去除,最终得到纯净的合成氨。
以上就是合成氨的工艺流程,通过这一连续的工艺流程,可以
高效地生产出合成氨,满足工业生产的需求。
合成氨的工艺流程是化学工程领域的重要研究课题,对于提高生产效率和减少能源消耗具有重要意义。
合成氨工艺流程简介

合成氨工艺流程简介在200MPa的高压和500℃的高温和催化剂作用下,N2+3H2==2NH3,经过压缩冷凝后,将余料在送回反应器进行反应,合成氨指由氮和氢在高温高压和催化剂存在下直接合成的氨。
世界上的氨除少量从焦炉气中回收副产外,绝大部分是合成的氨。
合成氨主要用作化肥、冷冻剂和化工原料。
生产方法生产合成氨的主要原料有天然气、石脑油、重质油和煤(或焦炭)等。
①天然气制氨。
天然气先经脱硫,然后通过二次转化,再分别经过一氧化碳变换、二氧化碳脱除等工序,得到的氮氢混合气,其中尚含有一氧化碳和二氧化碳约0.1%~0.3%(体积),经甲烷化作用除去后,制得氢氮摩尔比为3的纯净气,经压缩机压缩而进入氨合成回路,制得产品氨。
以石脑油为原料的合成氨生产流程与此流程相似。
②重质油制氨。
重质油包括各种深度加工所得的渣油,可用部分氧化法制得合成氨原料气,生产过程比天然气蒸气转化法简单,但需要有空气分离装置。
空气分离装置制得的氧用于重质油气化,氮作为氨合成原料外,液态氮还用作脱除一氧化碳、甲烷及氩的洗涤剂。
③煤(焦炭)制氨。
随着石油化工和天然气化工的发展,以煤(焦炭)为原料制取氨的方式在世界上已很少采用。
用途氨主要用于制造氮肥和复合肥料,氨作为工业原料和氨化饲料,用量约占世界产量的12%。
硝酸、各种含氮的无机盐及有机中间体、磺胺药、聚氨酯、聚酰胺纤维和丁腈橡胶等都需直接以氨为原料。
液氨常用作制冷剂。
贮运商品氨中有一部分是以液态由制造厂运往外地。
此外,为保证制造厂内合成氨和氨加工车间之间的供需平衡,防止因短期事故而停产,需设置液氨库。
液氨库根据容量大小不同,有不冷冻、半冷冻和全冷冻三种类型。
液氨的运输方式有海运、驳船运、管道运、槽车运、卡车运合成氨是以碳氨为主要原料, 我司可承包的合成氨生成成套项目, 规模有 4×104 吨/年, 6×104 吨/年, 10×104 吨/年, 30×104 吨/年, 其产品质量符合中国国家标准.1. 工艺路线:以无烟煤为原料生成合成氨常见过程是:造气 -> 半水煤气脱硫 -> 压缩机1,2工段 -> 变换 -> 变换气脱硫 ->压缩机3段 -> 脱硫 ->压缩机4,5工段 -> 铜洗 -> 压缩机6段 -> 氨合成 -> 产品NH3采用甲烷化法脱硫除原料气中CO. CO2 时, 合成氨工艺流程图如下:造气 ->半水煤气脱硫 ->压缩机1,2段 ->变换 -> 变换气脱硫 -> 压缩机3段 ->脱碳 -> 精脱硫 ->甲烷化 ->压缩机4,5,6段 ->氨合成 ->产品NH32.技术指标:(1) 原料煤: 无烟煤: 粒度15-25mm 或25-100mm固定75%蒸汽: 压力0.4MPa, 1-3MPa(2) 产品: 合成氨:氨含量(99.8%)残留物含量(0.2%)3. 消耗定额: ( 以4×104 吨/年计算)(1) 无烟煤( 入炉) : 1,300kg(2) 电: 1,000KWH( 碳化流程), 1,300KWH( 脱碳流程)(3) 循环水: 100M3(4) 占地: 29,000M24. 主要设备:(1) 造气炉(2) 压缩机(3) 铜洗(4) 合成塔。
合成氨工艺

合成氨工艺————————————————————————————————作者:————————————————————————————————日期:合成氨工艺流程(1)原料气制备将煤和天然气等原料制成含氢和氮的粗原料气。
对于固体原料煤和焦炭,通常采用气化的方法制取合成气;渣油可采用非催化部分氧化的方法获得合成气;对气态烃类和石脑油,工业中利用二段蒸汽转化法制取合成气。
(2)净化对粗原料气进行净化处理,除去氢气和氮气以外的杂质,主要包括变换过程、脱硫脱碳过程以及气体精制过程。
①一氧化碳变换过程在合成氨生产中,各种方法制取的原料气都含有CO,其体积分数一般为12%~40%。
合成氨需要的两种组分是H2和N2,因此需要除去合成气中的CO。
变换反应如下:CO+H2OH→2+CO2 =-41.2kJ/mol 0298HΔ由于CO变换过程是强放热过程,必须分段进行以利于回收反应热,并控制变换段出口残余CO含量。
第一步是高温变换,使大部分CO转变为CO2和H2;第二步是低温变换,将CO含量降至0.3%左右。
因此,CO变换反应既是原料气制造的继续,又是净化的过程,为后续脱碳过程创造条件。
②脱硫脱碳过程各种原料制取的粗原料气,都含有一些硫和碳的氧化物,为了防止合成氨生产过程催化剂的中毒,必须在氨合成工序前加以脱除,以天然气为原料的蒸汽转化法,第一道工序是脱硫,用以保护转化催化剂,以重油和煤为原料的部分氧化法,根据一氧化碳变换是否采用耐硫的催化剂而确定脱硫的位置。
工业脱硫方法种类很多,通常是采用物理或化学吸收的方法,常用的有低温甲醇洗法(Rectisol)、聚乙二醇二甲醚法(Selexol)等。
粗原料气经CO变换以后,变换气中除H2外,还有CO2、CO和CH4等组分,其中以CO2含量最多。
CO2既是氨合成催化剂的毒物,又是制造尿素、碳酸氢铵等氮肥的重要原料。
因此变换气中CO2的脱除必须兼顾这两方面的要求。
一般采用溶液吸收法脱除CO2。
第1章 合成氨1
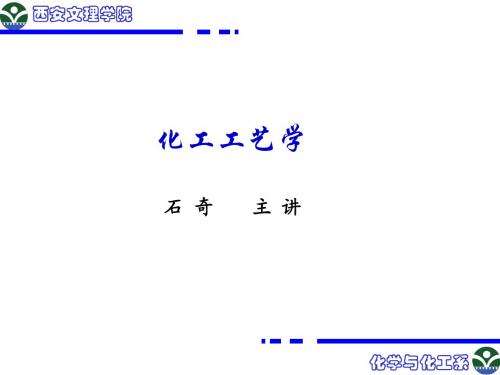
化学与化工系
西安文理学院
1.2.4 气态烃类蒸气转化催化剂
选择原则:高强度、高活性、抗析碳、抗中毒 高空隙率
组成:
主催化剂:
NiO(4-30%)
促进剂 : Al2O3、MgO、CaO、TiO2、K2O
载体: 铝酸钙连接型和氧化铝烧结型 装填:过筛、均匀、下降落差不能太大。 化学与化工系
还原后才能使用,卸出前必须钝化
log k p 2
备注: 此公式属经验公式,来源于试验, 化学与化工系
2.平衡常数的应用(计算平衡组成)
Nm,nw分别为进气中甲烷和水蒸气的量,kmol; x为甲烷蒸汽转化反应的甲烷转化量, kmol; y为变换反应转化的一氧化碳的量, kmol;
预计转化气组成
已知温度
求平衡常数
求平衡组成
选择工艺条件 判断工况
化学与化工系
西安文理学院
1.1.2 生产方法简介
主要包括3个步骤 (1)造气:即制备含有氢、氮的原料气; (2) 净化:不论采用何种原料和何种方法造气,原 料气中都含有对合成氨反应过程有害的各种杂质, 必须采取适当的方法除去这些杂质; (3) 压缩和合成:将合格的氮、氢混合气压缩到高 压,在铁催化剂的存在下合成氨。
化学与化工系
西安文理学院
胺.磺胺
氨 的 用 途
氨
炸药 医药
化学与化工系
西安文理学院
氨的发展概况
氨(Ammonia),分子式NH3,是1754年由普里斯特 里(Priestiy) 加热氯化铵和石灰石时发现的。1784年,伯 托里(C.L.Berthollet) 确定氨是由氮和氢组成的。其后,人 们便开始进行化学合成氨的研究.经过100多年的漫长岁月。 1901年,法国化学家吕查德里开创性地提出氨合成的条件 是高温、高压,并有催化剂存在。 终于在1913年实现了由氮和氢直接合成氨的工业化。 这是由哈伯 (Frite Haber) 与伯希 (Carl Bosch) 一起开发 的日产30t的工业化装置,在德国奥堡 (Oppau) 投入生产, 采用高温高压和铁系催化剂工艺,这就是著名的Haber— Bosch 法。因为保密和第一次世界大战(1914~1918)的关系, 除了德国和BASF公司外,该技术并未被很好利用。 化学与化工系
化工工艺学第1章合成氨9130

• 0.50
0.000025 0.0008 0.009
• 10
0.00055 0.018 0.20
• 20
0.005 0.16 1.80
• 实际上天然气等原料中水蒸气含量很低,所以即使温度在 400°C也可满足S含量<0.1×10-6的要求。 200°C含水20%时, S<0.005×10-6,因此氧化锌也用在变换工序作变换催化剂的 保护剂。
673 773 873 973 1073
使与一段的H2反应产生高温,
温度/°C
保证二段中转化较为完全。
图 1.6
• 2. 工艺条件
• 压力 通常为3~4MPa
• 采用加压条件的主要原因:
• 降低能耗
能量合理利用
• 提高余热利用价值
全厂流程统筹
• 减少设备体积降低投资 综合经济效益
• 温度
• 一段炉温度 主要考虑投资费用及设备寿命, 一般选择760~800°C
• 平衡常数 • 两个制气反应的平衡常数为
K
0 p1
pCO
p3 H2
p p CH4 H2O p0
2
(1.2.1)
•
K
0 p2
p p CO2 H2 pCO pH2O
(1.2.2)
• 上式是将体系视为理想气体混合物的结论,通常
转化过程压力不是太高,用它来计算误差不大。
但要求较高的设计需要计算逸度系数,用逸度代
3. Na2CO3 +H2S =NaHS+NaHCO3 然后再与偏钒酸钠反应
反 应 速 率
催化剂粒度
催 化 剂 内 表 面 利 用 率
催化剂粒度
• 1.2.3 过程析碳处理
• 碳黑生成后主要有以下几点不利:堵塞反应管道 增大压降、使局部区域高温损坏催化剂、增大反 应阻力。从热力学分析,几个析碳反应
化工工艺学简答题含答案

化工工艺学简答题含答案第一章合成氨1.合成氨的主要生产工序,各工序的作用和任务?答:1.原料气制备,制备含有氢、氮的原料气。
用煤、原油或天然气作原料,制备含氮、氢气的原料气。
2.净化,因为无论用何种方法造气,原料气中都含有对合成氨反应过程有害的各种杂质,必须采取适当的方法除去这些杂质,主要包括变换过程、脱硫脱碳过程以及气体精制过程。
3.压缩和合成,将纯净的氢、氮混合气压缩到高压,在铁催化剂的作用下合成氨。
2.写出烃类蒸汽转化的主要反应。
CH 4+H 2O(g)=CO+3H 2,CH 4=2 H 2+C3.简述常用脱硫方法及技术特点以及适用流程。
答:干法脱硫(氧化锌法脱硫;钴钼加氢脱硫法)是用固体吸收剂吸收原料气体中的硫化物一般只有当原料气中硫化氢质量浓度不高标准状态下在3-5g/m 3才适用。
特点:能脱除有机硫和无机硫而且可以把脱得很精细,但脱硫剂不能再生而且设备庞大占地多,不适用于脱除大量无机硫,只有天然气、油田气等含硫低时才使用;湿法脱硫(化学吸收法,物理吸收法,化学-物理综合吸收法)特点:脱硫剂是便于运输的液体物料,脱硫剂是可以再生并且能回收的硫磺,适用于脱除大量无机硫。
4.改良ADA 法脱硫的主要化学反应和脱硫原理是什么?ADA 法脱硫主要化学反应及脱硫原理:在脱硫塔中用PH 为8.5--9.2的稀碱溶液吸收硫化氢并生成硫化氢物:液相中的硫化氢物进一步与偏钒酸钠反应,生成还原性焦性偏钒酸钠盐并析出无素硫还原性焦性偏钒酸钠盐接着与氧化态ADA 反应,生成还原态的ADA 和偏钒酸盐还原态的ADA 被空气中的氧气氧化成氧化态的ADA ,其后溶液循环使用 4.少量 CO 的脱除方法有哪些?答:铜氨液洗涤法、甲烷化法、液氮洗涤法。
5.以天然气为原料生产合成气过程有哪些主要反应?答:主反应:CO+H 2O(g)=H 2+CO 2 ,CH 4+H 2O(g)=CO+3H 2副反应:CH 4=2 H 2+C ,2CO=C+CO 2,CO+H 2=H 2O+C6.简述一段转化炉的炉型结构。
- 1、下载文档前请自行甄别文档内容的完整性,平台不提供额外的编辑、内容补充、找答案等附加服务。
- 2、"仅部分预览"的文档,不可在线预览部分如存在完整性等问题,可反馈申请退款(可完整预览的文档不适用该条件!)。
- 3、如文档侵犯您的权益,请联系客服反馈,我们会尽快为您处理(人工客服工作时间:9:00-18:30)。
氮的固定 定义:将游离态氮转化为化合态氮的方法叫氮的固定
类别: ① 天然固定:豆科植物的根瘤菌固氮、 雷雨天产生NO气体 ② 人工固定:合成氨等。
主要化学性质 1、NH3(挥发性)遇HCl(挥发性)气体有白烟产生,可与氯气反应。 2、氨水(一水合氨,NH3·H2O)可腐蚀许多金属,一般若用铁桶装氨水, 铁桶应内涂沥青。 3、氨的催化氧化是放热反应,产物是NO,是工业制硝酸的重要反应, NH3也可以被氧化成N2。 4、NH3能使湿润的红色石蕊试纸变蓝。在水中产生少量氢氧根离子,呈 弱碱性. ⒌氨与酸反应生成铵盐:NH3+HCI=NH4CI
空气中含有大量的游离氮,但是只有极少数农作 物才能直接吸收空气中的氮。大多数作物只能吸 收化合态氮来供给生长所需主要养分。固氮是化 学化工研究中既古老又前沿的课题。
目前已投入工业生产的主要固氮方法: 1. 电弧法 2. 氰氨法 3. 合成氨法 目前最重要最经济的方法是合成氨法。
1.1 合成氨工业的重要性
合成氨工业是基础化学工业的重要组成部分
氨可生产多种氮肥,如尿素、硫酸铵、碳酸氢铵等; 还可生产多种复合肥,如磷复肥等。
氨也是重要的工业原料。基本化学工业中的硝酸 及各种含氮无机盐; 有机工业各种中间体,制药中磺胺 药物,高分子中氨基塑料、丁腈橡胶、冷却剂等。
国防工业中三硝基甲苯、硝化甘油、硝化纤维等
(1)原料气的制备
在工业生产中可行的方法从空气中获得氮气?
物理方法:将空气液化后再汽化分离出氮气 化学方法:将空气中O2与C作用生成CO2,除去CO2得到氮气。
高温
C + H2O ==
CO + H2
CO + H2O催=高化=温剂CO2 + H2
H2?
催化剂
催化剂
CH4 + H2O == CO + 3H2 CH4+2H2O===4H2+CO2
目前先进合成氨厂的规模已达到1000~1500t /日。
合成氨首先为农业生产提供了充足的肥料,使农 业生产产量大大提高,为人类社会发展和人口增 长作出了巨大贡献。
氨除了主要用作化学肥料的原料外,还是生产染 料、炸药、医药、有机合成、塑料、合成纤维、 石油化工等的重要原料。
1.3. 合成氨工艺条件
第一部分:合成氨工艺 第二部分:硫酸工艺 第三部分:纯碱与烧碱工艺
32学时,讲授与自学及研讨相结合;
采用N+2考试模式,期末试卷分最低分为50, 占50%,过程40%。其中过程考核次数N=3, 包 括:课堂测验(20%),综述1(10%),讨论 讲演1 (10%)。
Chp1: 概述 Chp2: 原料气的制取 Chp3: 粗原料气的净化 Chp4: 氨的合成 Chp5: 合成氨生产综述 Chp6: 尿素生产工艺*
脱硫
脱碳
(2)原料气的净化 :S CO CO2等
变换
净化
目的:防止催化剂中毒
1909年,德国人哈伯以锇为催化剂在17.5~20MPa和500~ 600℃温度下进行了合成氨研究,得到6%的氨。1909年7月成 功地建立了能生产80g.h-1氨的试验装置。
BASF公司认可该专利将获利,购买之,并聘请工业化学 家C. Bosch参与改进专利,哈伯-博施专利;
1911年化学家A. Mittasch 研究成功以铁为活性组分的合 成催化剂,铁基催化剂活性好、比锇催化剂价廉、易得。
氨极易溶于水,在常温、常压下,1体积水能溶解约700 体积的氨。
1.2. 合成氨工业发展简介
1754年,J.Priestley 发现氨; 1784年,C.L.Berthollet 证明氨是由氮、氢组成的。
1898年,A. Frank and N. Caro 发现碳化钙与氮气在1000度 左右加热时生成CaCN2, 申请了专利,而该物质可在2000C碱 性介质中水解生成氨。 1905年在德国建成第一座氰化法制氨装置,用于制造炸药等, 但该法能耗高,约190GJ/tNH3, 在合成法成功后逐渐失去竞 争力,至20世纪30年代后合成法成为主要的氨制备方法。
19世纪末,在热力学、动力学和催化剂等领域研究取 得进展后,对合成氨反应的研究有了新的进展。
1901 年 法 国 物 理 化 学 家 吕 ·查 得 利 ( Le Chatelier)提出氨合成的条件是高温、高压,并 有适当催化剂存在。(爆炸)
德国物理化学家W. Nernst 计算推断直接合成 不可行!
合 选择合适的压强:20 MPa~50 MPa
成 氨
选择合适的温度:450℃左右
的 适
使用催化剂:铁触媒
宜
条 浓度:不断补充氮气和氢气并及时液化分离出
件 氨,采用循环操作,将余下N2、H2送回合成塔,
以提高原料的利用率。
1.4. 合成氨的生产工艺
N2(g) + 3H2(g)
2NH3(g);△H = -92.4kJ·mol-1
氨的物理性质 (1)有刺激性气味的气体
氨对人体的眼、鼻、喉等有刺激作用,接触时应小心。 如果不慎接触过多的氨而出现病症,要及时吸入新鲜空气和 水蒸气,并用大量水冲洗眼睛。 (2)密度小
氨气的密度为0.771g/L(标准状况下) (3)沸点较高
氨很容易液化,在常压下冷却至-33.5℃或在常温下加压 至700kPa至800kPa,气态氨就液化成无色液体,放出大量的 热。液态氨汽化时要吸收大量的热,所以氨常作为制冷剂。 (4)易溶于水
哈伯(Fritz Haber),德国化学家。1918年,哈 伯因研制合成氨作出重大贡献而获得诺贝尔化 学奖 ( C. Bosch 1931年获得诺贝尔化学奖 )
哈伯 合成氨 实验
首例合成氨厂是1912年BASF公司在德国 Oppau 建立日产30吨合成氨的工厂,1913年 9月运转,1914年满负荷生产。
氨在英文中有时会被称作anhydrous ammonia(无水氨),中文中很 少有人会把氨气和氨水混为一谈。
一水合氨或称氨水是氨的水溶液,氨的水溶液为碱性: NH3+ H2O ⇌ NH4++ OH-
其性质和氨气完全不一样。实验室的稀氨水一的浓度一般为1M至2M。 氨的饱和水溶液(大约18M)的密度是0.880g cm,故可称之为.880 Ammonia。