铸造工艺设计基础
铸造工艺基础知识及理论

铸造工艺基础知识及理论目录一、基础概念 (2)1.1 铸造的定义与意义 (3)1.2 铸造工艺的种类与应用 (4)二、铸造材料 (6)三、铸造设备 (7)3.1 熔炼设备 (9)3.2 锻造设备 (10)3.3 后处理设备 (11)四、铸造工艺过程 (12)五、铸造工艺设计 (13)5.1 工艺方案的确定 (15)5.2 工艺参数的选择 (16)5.3 工艺文件的编制 (18)六、铸造质量与控制 (20)6.1 铸造缺陷的产生原因及防止措施 (22)6.2 铸造质量检测方法与标准 (23)七、铸造生产与环境 (24)7.1 铸造生产的环保要求 (26)7.2 环保设备的应用与管理 (27)八、现代铸造技术的发展趋势 (28)8.1 快速凝固与近净形铸造技术 (30)8.2 数字化与智能化铸造技术 (31)8.3 生物铸造与绿色铸造技术 (33)一、基础概念铸造工艺是指将熔炼好的液态金属浇入铸型,待其凝固后获得所需形状和性能的金属制品的过程。
它是制造业中非常重要的工艺之一,广泛应用于汽车、航空、建筑、电子等领域。
铸造工艺的基础知识主要包括液态金属的性质、铸型(即模具)的设计与制造、浇注系统、凝固过程以及后处理等。
这些知识是理解和掌握铸造工艺的基本前提。
液态金属的性质:液态金属在铸造过程中的流动性、填充能力、冷却速度等对其最终的产品质量有着决定性的影响。
了解液态金属的成分、温度、粘度等基本性质对于铸造工艺的设计和实践都是非常重要的。
铸型的设计与制造:铸型是形成金属制品形状和内部结构的重要工具。
铸型的设计需要考虑到金属液的流动性和凝固特性,以及制品的精度和表面质量要求。
铸型的制造也需要选用合适的材料,并经过精密加工才能达到设计要求。
浇注系统:浇注系统是连接铸型和液态金属的通道,包括浇口杯、直浇道、横浇道和内浇道等部分。
合理的浇注系统设计可以确保金属液均匀地注入铸型,并有利于热量和气体的排出,从而提高制品的质量和生产效率。
铸造、热处理、锻造工艺基础

5.2锻造比 • 锻造比是锻造时金属变形程度的一种表示方法。 锻造比以金属变形前后的横 断面积的比值来表示。不同的锻造工序,锻造比的计算方法各不相同。 • 1、拔长时,锻造比为y=F0/F1或y=L1/L0 • 式中F0,L0—拔长前钢锭或钢坯的横断面积和长度; • F1 ,L1—拔长后钢锭或钢坯的横截面积和长度。 • 2、镦粗时的锻造比,也称镦粗比或压缩比,其值为 • y=F1/F0或y=H0/H1 • F0, H0—镦粗前钢锭或钢坯的横截面积和高度; • F1, H1—镦粗后钢锭或钢坯的横截面积和高度。
三箱造型浇注位置和分型面
5/
2.3浇注位置选择原则
(1)铸件的重要加工面应朝下或侧立。因铸件的上表面容易产生砂眼、气孔、 夹渣等缺陷,组织也不如下表面致密; (2)铸件的大平面应朝下。大平面朝上容易产生夹砂缺陷 (3)为防止铸件薄壁部分产生浇不足或冷隔缺陷,应将面积较大的薄壁部分 置于铸型下部或使其处于垂直或倾斜的位置; (4)对于容易产生缩孔的铸件,应使厚的部分放在铸型的上部或侧面,以便 在铸件厚壁处直接安置冒口,使之实现自下而上的定向凝固。
两组数 铸铁选用
13/
4.1 PROCAST仿真简介 • Procast是为评价和优化铸造工艺与铸造产品而开发的专业CAE软件 • Procast是所有铸造模拟软件中集成化程度最高的 • 配备了功能强大的数据接口和自动网格划分工具 • 全部模块化设计,适合任何铸造过程的模拟 • 采用有限元技术,是目前唯一能对铸造凝固过程进行热——流动——应力完
24/
5.4锻造术语 • 锻件重量:锻件毛坯的实际重量 • 飞边重量:锻造过程中外轮廓分模面处多余的材料 • 料芯重量:锻造过程中内孔多余的材料 • 火耗重量: 锻件在锻打过程中的热损耗 • 下料重量(切料重量):锻打一件锻件所需要的钢坯重量 • 材料消耗定额:锻打一件锻件所需要的钢材消耗总重量
第五章铸造工艺基础

第五章铸造第二篇铸造工艺基础教学内容合金的铸造性能、流动性、收缩性、偏析性;铸件的常见缺陷分析及防止;常见合金铸件的生产;砂型铸造工艺基础;几种典型的特种铸造工艺方法;铸件结构与铸造工艺及合金铸造性能的关系。
目的与要求要求了解合金流动性和收缩的概念、影响因素及其对铸件质量的影响,为铸件设计,选材和制订铸造工艺提供理论基础。
常用合金铸件的生产,要求了解灰铸铁、球墨铸铁、可锻铸铁、铸钢、铜、铝及其合金铸件的生产特点。
砂型铸造要求掌握制定铸造工艺图的基本原则,主要工艺参数的选择原则,分析典型铸件图例,并为今后解决实际问题打好基础。
掌握铸造工艺和合金铸造性能对铸件结构的要求。
特种铸造重点了解金属型铸造、熔模铸造、压力铸造和离心铸造基本知识。
‘第一节液态合金的充型充型:液态合金填充铸型的过程。
充型能力:液态金充满铸型型腔,获得形状完整、轮廓清晰健全的铸件的能力。
影响充型能力的主要因素是合金的流动性、浇注条件、铸型填充条件和铸件结构。
一、合金的流动性1.流动性的概念流动性:液态态合金本身的流动能力。
流动性好,易于浇出轮廓清晰,薄而复杂的铸件。
流动性好,有利于液态金属中的非金属夹杂物和气体上浮,排除。
流动性好,易于对液态金属在凝固中产生的收缩进行补缩。
2.流动性的测定方法以螺旋形试件的长度来测定:如图5-1影响合金流动性的因素:合金成分结金温度范围浇注温度充型压力图5—3所示为铁碳合金的流动性与含碳量的关系。
由图可见,亚共晶铸铁随含碳量增加,结晶间隔减小,流动性提高。
愈接近共晶成分,愈容易铸造。
二、浇注条件浇注温度浇注温度对合金的充型能力有着决定性影响。
浇注温度愈高,液态金属所含的热量较多,粘度下降,在相同的冷却条件下,合金在铸型中保持流动的时间长。
但是,浇注温度过高会使金属液体的吸气量和总收缩量增大,铸件容易生产气孔、缩孔、缩松、粘砂、粗晶等缺陷,故在保证充型能力足够的前提下,浇注温度不易过高。
对于形状复杂的薄壁铸件,为避免产生冷隔和浇不足等缺陷,浇注温度以略高些为宜。
铸造工艺基础教学培训PPT

二、铸造成形基础
逐层凝固:液固金属间轮廓线清 晰。4.3%的铁碳合金,结晶在恒 温下进行,结晶过程有表及里,逐 层推进,凝固层的内表面比较光滑, 对尚未凝固合金流动阻力小,有利 于合金的充型,所以流动性好。 糊状凝固:先结晶的固态金属广泛 分布在没有结晶的液态金属中,液 固金属间没有明显的轮廓线。
二、铸造成形基础
• 2.合金的收缩
(4)铸造内应力、变形和裂纹
◆ 消除或减小铸造内应力的方法: ① 采用同时凝固的原则,通过设置冷铁、布置浇 冒口位置等工艺措施,使铸件各部分在凝固过程中 温差尽可能小;(不管壁厚如何,同时一起收缩, 可避免热应力的产生) ② 提高铸型温度,使整个铸件缓冷,以减小铸型 各部分温差; ③ 改善铸型与铸芯的退让性; ④ 进行去应力退火,这是消除铸造应力最彻底的 方法。
二、铸造成形基础
• 2.合金的收缩
(4)铸造内应力、变形和裂纹
◆ 变形: 当铸件中的内应力若超过合金的屈服强度,将使铸件产生变形。为防止变形,在铸件设计
时,应力求壁厚均匀、形状简单而对称。 ◆ 变形:
当铸件的内应力超过合金的抗拉强度时,铸件便会产生裂纹。裂纹是铸件严重的缺陷。 防止裂纹的主要措施: 合理的设计铸件结构;合理选用型砂和芯砂的粘结剂与添加剂,以改善其退让性;大的型 芯可制成中空的或内部填以焦炭;严格限制钢与铸铁中的硫含量;选用收缩量小的合金。
二、铸造成形基础
• 2.合金的收缩
• (2)缩松:液态合金在凝固过程中,若凝固时的收缩得不到及时补充,就会形成缩
孔,若缩孔是分散的,即为缩松。
又称分散缩孔) 形状:宏观缩松—肉眼可见的微小孔洞;
热加工工艺基础-铸造
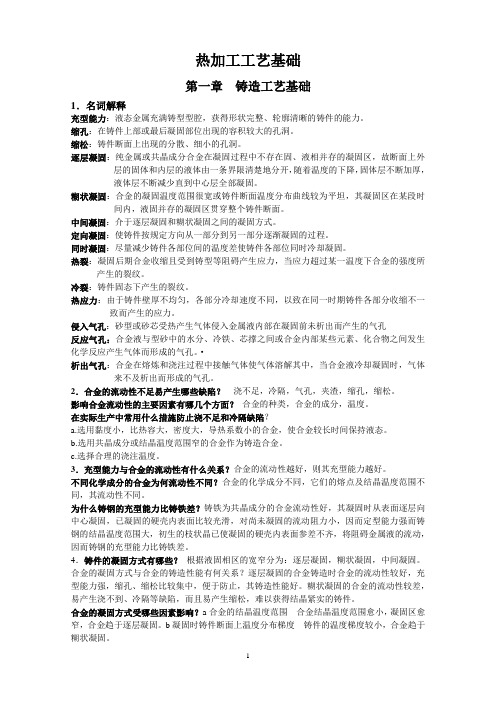
热加工工艺基础第一章铸造工艺基础1.名词解释充型能力:液态金属充满铸型型腔,获得形状完整、轮廓清晰的铸件的能力。
缩孔:在铸件上部或最后凝固部位出现的容积较大的孔洞。
缩松:铸件断面上出现的分散、细小的孔洞。
逐层凝固:纯金属或共晶成分合金在凝固过程中不存在固、液相并存的凝固区,故断面上外层的固体和内层的液体由一条界限清楚地分开,随着温度的下降,固体层不断加厚,液体层不断减少直到中心层全部凝固。
糊状凝固:合金的凝固温度范围很宽或铸件断面温度分布曲线较为平坦,其凝固区在某段时间内,液固并存的凝固区贯穿整个铸件断面。
中间凝固:介于逐层凝固和糊状凝固之间的凝固方式。
定向凝固:使铸件按规定方向从一部分到另一部分逐渐凝固的过程。
同时凝固:尽量减少铸件各部位间的温度差使铸件各部位同时冷却凝固。
热裂:凝固后期合金收缩且受到铸型等阻碍产生应力,当应力超过某一温度下合金的强度所产生的裂纹。
冷裂:铸件固态下产生的裂纹。
热应力:由于铸件壁厚不均匀,各部分冷却速度不同,以致在同一时期铸件各部分收缩不一致而产生的应力。
侵入气孔:砂型或砂芯受热产生气体侵入金属液内部在凝固前未析出而产生的气孔反应气孔:合金液与型砂中的水分、冷铁、芯撑之间或合金内部某些元素、化合物之间发生化学反应产生气体而形成的气孔。
·析出气孔:合金在熔炼和浇注过程中接触气体使气体溶解其中,当合金液冷却凝固时,气体来不及析出而形成的气孔。
2.合金的流动性不足易产生哪些缺陷?浇不足,冷隔,气孔,夹渣,缩孔,缩松。
影响合金流动性的主要因素有哪几个方面?合金的种类,合金的成分,温度。
在实际生产中常用什么措施防止浇不足和冷隔缺陷?a.选用黏度小,比热容大,密度大,导热系数小的合金,使合金较长时间保持液态。
b.选用共晶成分或结晶温度范围窄的合金作为铸造合金。
c.选择合理的浇注温度。
3.充型能力与合金的流动性有什么关系?合金的流动性越好,则其充型能力越好。
不同化学成分的合金为何流动性不同?合金的化学成分不同,它们的熔点及结晶温度范围不同,其流动性不同。
铸造工艺学讲义一(基础知识)

一.熔模铸造 二.金属型铸造 三.压力铸造
第五节 零件结构的铸造工艺性
一.铸件结构的合理性 二.铸件结构的工艺性 三.铸造方法对铸件结构的特殊要求
2
前言
商代司母戊鼎
中国商代晚期的青铜器。1939年于河南安阳殷墟商代晚期墓 出土。因腹内壁铸有“司母戊”三字而得名。该鼎造型庄严雄伟。 长方形腹,每面四边及足上部饰兽面纹。双耳,外侧饰双虎噬人 首纹。四足中空。高133厘米、口长110厘米、口宽79厘米、重 832.84千克。该鼎的化学成分为:铜84.77%,锡11.64%,铅2.79%, 其他0.8%。是中国目前已发现的最大、最重的古代青铜器。
b) 进行去应力退火 铸件机加工之前应先采用时效或去应力退
液态收缩与凝固收缩 主要表现为体积的缩减,
产生缩孔、缩松 固态收缩
导致尺寸减小,产生内 应力和出现裂纹。
18
(三) 影响合金收缩的因素
1. 化学成分 不同成分的合金其收缩率一般也不相同。在常用铸造 合金中铸刚的收缩最大,灰铸铁最小。 2. 浇注温度 合金浇注温度越高,过热度越大,液体收缩越大。 3. 铸件结构与铸型条件 铸件冷却收缩时,因其形状、尺寸的不同, 各部分的冷却速度不同,导致收缩不一致,且互相阻碍,又加之 铸型和型芯对铸件收缩的阻力,故铸件的实际收缩率总是小于其 自由收缩率。这种阻力越大,铸件的实际收缩率就越小。
图1-7 缩松形成过程示意图
21
比较缩孔和缩松的特征
缩孔:集中性,位于上部,呈倒锥形,内表面粗糙。
缩松: 分散性,为细小缩孔,位于铸件壁的轴线区域。
22
2.缩孔、缩松的防止措施 1).定向凝固与同时凝固
按铸件壁厚分布均匀程度不同(即冷却快慢不同),分为: 定向凝固(或称顺序凝固)-薄部先凝固,厚部后凝固,冒口最后 凝固。 同时凝固(厚薄不同部位趋近同时凝固,金属液从薄部引入)。
机械制造基础(金属工艺学) 第二章 铸造
第2章 铸造
01 铸造工艺基础 02 合金铸件的生产工艺 03 砂型铸造 04 特种铸造 05 铸件结构设计
第2章 铸造
铸造工艺特点 1)适合制造形状复杂的毛坯
第2章 铸造
铸造工艺特点 2)毛坯大小不受限制
第2章 铸造
铸造工艺特点 3)材料不受限制(能熔化的金属) 4)生产成本低(原材料来源广泛) 5)应用广泛(历史最久的金属成型方法,40%~80%)
2.3.2 浇注位置和分型面的选择—浇注位置 1)铸件的重要加工面应朝下或位于侧面
2.3 砂型铸造
2.3.2 浇注位置和分型面的选择—浇注位置 2)铸件宽大平面应朝下
2.3 砂型铸造
2.3.2 浇注位置和分型面的选择—浇注位置 3)面积较大的薄壁部分应置于铸型下部
2.3 砂型铸造
2.3.2 浇注位置和分型面的选择—分型面 分型面:铸型组元之间的结合面或分界面。 分型面影响: 1)铸件质量; 2)生产工序的难易; 3)切削加工的工作量。
2.2.1 铸铁件生产 2)球墨铸铁 由于石墨成球状,它对基体的缩减和割裂作用减至最低限度,球墨
铸铁具有比灰铸铁高的多的力学性能,塑韧性大大提高。
2.2 合金铸件的生产工艺
2.2.1 铸铁件生产 2)球墨铸铁
球墨铸铁的牌号、 性能及用途 QTXXX-X
2.2 合金铸件的生产工艺
2.2.1 铸铁件生产 3)可锻铸铁 将白口铸铁件经长时间的高温石墨化退火,使白口铸铁中的渗碳体
04 特种铸造 05 铸件结构设计
2.3 砂型铸造
铸造工艺
砂型铸造
特种铸造
手工造型 机器造型 金属型铸造 熔模铸造
压力铸造 低压铸造
陶瓷型铸造 离心铸造
2.3 砂型铸造
铸造工艺基础大全完整版.ppt课件.ppt
§2铸件的凝固与收缩
凝固—金属从液态转变为固态的过程。这个转变期 称为凝固期。
一 .铸件的凝固方式
实验:做几个直径相同
的球铸型,一次同时浇注
经过不同时间,先后拔掉
泥芯。倒出液态金属,
测量硬壳厚度,画出
凝固厚度—时间曲线。
泥 芯
精心整理
厚度 3 2 1
1--φ75
2—φ125
3—φ260
精心整理
3 . 中间凝固---凝固区介于1、2之间。大多数合 金的凝固方式属于这种凝固方式。
精心整理
铸件凝固方式对铸件质量的影响: 凝固过程实质是金属的结晶过程,它从两方 面影响铸件的性能: 1)形成的金相组织-----晶粒的大小、形状及晶 粒的内部缺陷等影响合金的机械性能; 2)金属的致密度-----液态金属结晶为固态,引 起的体积收缩所形成的孔洞,若得不到液态 金属的补缩,将产生铸造缺陷,影响合金的 致密性及强度。
精心整理
σ σ
精心整理
Al---Si 合金的高温强度
σ 500℃
固相线精心整理
T℃
影响热裂形成的因素 (1)合金性质
合金结晶温度 T℃
范围越宽,
热裂倾向性
越大。
热
裂
倾
向
精心整理
线收缩 开始温度
固 相 线
此外,合金中的一些其它元素对其热裂 倾向也有一定的影响。如:碳素钢中的S、
P、Si, Mn 四种因素对热裂性的影响。
精心整理
2 .机械应力(收缩应力)
由于收缩受阻,产生的都是拉应力或剪应力。
因为是产生在弹性状态下,落砂后随着产生弹 性变形而消失,为临时应力。(但产生弹性变 形的应力仍然留在弹性体内)
铸造工艺基础
一、合金的流动性 与以下因素有关: 1.化学成分 纯金属、共晶成分合金流动性好。 2.物理性质 如导热性、粘滞性、侵润性等。
铸造工艺基础
第二篇 铸 造
GB/T5611-1998规定: 铸造是指熔炼金属,制造铸型,并将熔融金属浇入铸型,凝固后获得一定形状、尺寸和性能的金属零件毛坯的成形方法。 用铸造方法获得的金属毛坯或零件称为铸件. 铸造被广泛采用,具有如下优点: 1. 适应性广
谓:性能改善形状精,加工量少成本低。 但是,铸造生产过程中的工艺控制较困难,因而铸件质量不稳定,废品率较高; 铸造劳动强度大,条件差,环境污染严重。 铸造按生产方式不同,可分为: 砂型铸造和特种铸造 砂型铸造的铸件占总产量的80%以上,其生产过程如图。
此两项形成体收缩是造成缩孔(松)的主要原因。 3.固态收缩 造成线收缩,形成应力、变形的原因。 影响收缩的因素: 1.化学成分 见附表 钢收缩大,灰铸铁收缩小(为什么?) 2.浇注温度 3.铸件结构与铸型条件
它适用于各种合金(如铸铁、铸钢和有色金属等),能制出外形和内腔很复杂的零件,铸件的尺寸、重量和生产批量都不受限制。 谓:材料能熔便可铸,尺寸形状复杂件 2. 成本低廉。 所用原材料来源广,设备投资少,节省工时,材料利用率高。铸件材质内在质量得到提高,一些现代铸造方法生产出来的铸件质量已接近锻件。
三、 铸件中的缩孔与缩松
1.缩孔与缩松的形成 1)缩孔—集中的凝固收缩孔洞,产生于铸件厚大热节处。 2)缩松—细小而分散的缩孔, 具体又分: 宏观缩松—肉眼可见分散小孔; 显微缩松—显微镜下可见分散小孔。 2.缩孔与缩松的防止
一般固态金属在再结晶温度以上(钢和铸铁为620~650℃)时,处于塑性状态的变形应力可自行消除; 在此温度以下金属呈弹性状态,而弹性状态下的变形应力将会继续存在。 结论: 铸件厚壁或心部受拉伸; “+”为拉应力;”-”为压应力。 薄壁或表层受压缩。
材料成形技术基础知识点总结
铸造:将熔融的液体浇注到与零件的形状相适应的铸型型腔中,冷却后获得逐渐的工艺方法。
1、铸造的实质利用了液体的流动形成。
2、铸造的特点A 适应性大(铸件分量、合金种类、零件形状都不受限制);B 成本低C 工序多,质量不稳定,废品率高D 力学性能较同样材料的锻件差。
力学性能差的原因是:铸造毛胚的晶粒粗大,组织疏松, 成份不均匀3、铸造的应用铸造毛胚主要用于受力较小,形状复杂(特别是腔内复杂)或者简单、分量较大的零件毛胚。
1、铸件的凝固(1)铸造合金的结晶结晶过程是由液态到固态晶体的转变过程.它由晶核的形成和长大两部份组成。
通常情况下,铸件的结晶有如下特点:A 以非均质形核为主B 以枝状晶方式生长为主.结晶过程中,晶核数目的多少是影响晶粒度大小的重要因素,因此可通过增加晶核数目来细化晶粒. 晶体生长方式决定了最终的晶体形貌,不同晶体生长方式可得到枝状晶、柱状晶、等轴晶或者混合组织等.(2)铸件的凝固方式逐渐的凝固方式有三种类型:A 逐层凝固B 糊状凝固C 中间凝固2、合金的铸造性能(1)流动性合金的流动性即为液态合金的充型能力,是合金本身的性能。
它反映了液态金属的充型能力,但液态金属的充型能力除与流动性有关,还与外界条件如铸型性质、浇注条件和铸件结构等因素有关,是各种因素的综合反映。
生产上改善合金的充型能力可以从一下各方面着手:A 选择挨近共晶成份的趋于逐层凝固的合金,它们的流动性好;B 提高浇注温度,延长金属流动时间;C 提高充填能力D 设置出气冒口,减少型内气体,降低金属液流动时阻力。
(2)收缩性A 缩孔、缩松形成与铸件的液态收缩和凝固收缩的过程中.对于逐层凝固的合金由于固液两相共存区很小甚至没有,液固界面泾渭分明,已凝固区域的收缩就能顺利得到相邻液相的补充,如果最后凝固出的金属得不到液态金属的补充,就会在该处形成一个集中的缩孔。
适当控制凝固顺序,让铸件按远离冒口部份最先凝固,然后朝冒口方向凝固, 最后才是冒口本身的凝固(即顺序凝固方式) ,就把缩孔转移到最后凝固的部位—- 冒口中去,而去除冒口后的铸件则是所要的致密铸件。
- 1、下载文档前请自行甄别文档内容的完整性,平台不提供额外的编辑、内容补充、找答案等附加服务。
- 2、"仅部分预览"的文档,不可在线预览部分如存在完整性等问题,可反馈申请退款(可完整预览的文档不适用该条件!)。
- 3、如文档侵犯您的权益,请联系客服反馈,我们会尽快为您处理(人工客服工作时间:9:00-18:30)。
铸造工艺设计基础铸造生产周期较长,工艺复杂繁多。
为了保证铸件质量,铸造工作者应根据铸件特点,技术条件和生产批量等制订正确的工艺方案,编制合理的铸造工艺流程,在确保铸件质量的前提下,尽可能地降低生产成本和改善生产劳动条件。
本章主要介绍铸造工艺设计的基础知识,使学生掌握设计方法,学会查阅资料,培养分析问题和解决问题的能力。
§1-1 零件结构的铸造工艺性分析铸造工艺性,是指零件结构既有利于铸造工艺过程的顺利进行,又有利于保证铸件质量。
还可定义为:铸造零件的结构除了应符合机器设备本身的使用性能和机械加工的要求外,还应符合铸造工艺的要求。
这种对铸造工艺过程来说的铸件结构的合理性称为铸件的铸造工艺性。
另定义:铸造工艺性是指零件的结构应符合铸造生产的要求,易于保证铸件品质,简化铸造工艺过程和降低成本。
铸造工艺性不好,不仅给铸造生产带来麻烦,不便于操作,还会造成铸件缺陷。
因此,为了简化铸造工艺,确保铸件质量,要求铸件必须具有合理的结构。
一、铸件质量对铸件结构的要求1.铸件应有合理的壁厚某些铸件缺陷的产生,往往是由于铸件结构设计不合理而造成的。
采用合理的铸件结构,可防止许多缺陷。
每一种铸造合金,都有一个合适的壁厚范围,选择得当,既可保证铸件性能(机械性能)要求,又便于铸造生产。
在确定铸件壁厚时一般应综合考虑以下三个方面:保证铸件达到所需要的强度和刚度;尽可能节约金属;铸造时没有多大困难。
(1)壁厚应不小于最小壁厚在一定的铸造条件下,铸造合金能充满铸型的最小壁厚称为该铸造合金的最小壁厚。
为了避免铸件的浇不足和冷隔等缺陷,应使铸件的设计壁厚不小于最小壁厚。
各种铸造工艺条件下,铸件最小允许壁厚见表7-1~表7-5合金种类铸件最大轮廓尺寸为下列值时/㎜﹤200200-400400-800800-12501250-2000﹥2000碳素铸钢低合金钢高锰钢不锈钢、耐热钢灰铸铁孕育铸铁(HT300以上)球墨铸铁88-98-98-113-45-63-499-101010-124-56-84-811121212-165-68-108-1014161616-206-810-1210-1216~18202020-258-1012-1612-14202525-10-1216-2014-16铸件最大轮廓为下列值时mm铸造铝合金﹤100100-200200-400400-800800-125034-55-66-88-12表1-2 熔模铸件的最小壁厚(单位:㎜)铸件尺寸/㎜最小壁厚/㎜碳钢高温合金铝合金铜合金10~50 1.5~2.00.6~1.0 1.5~2.0 1.5~2.0 50~100 2.0~2.50.8~1.5 2.0~2.5 2.0~2.5 100~200 2.5~3.0 1.0~2.0 2.5~3.0 2.5~3.0 200~350 3.0~3.5— 3.0~3.5 3.0~3.5﹥350 4.0~5.0— 3.5~4.0 3.5~4.0表1-3 金属型铸件的最小壁厚(单位:㎜)铸件尺寸/㎜最小壁厚/㎜铝硅合金铝镁合金、镁合金铜合金灰铸铁铸钢50×50 2.23 2.535100×100 2.53338225×22534 3.5410350×350454512压铸件面积/㎝2锌合金铝合金镁合金铜合金﹤250.7~1.00.8~1.2 1.5~2.025~100 1.0~1.6 1.2~1.8 2.0~2.5100~400 1.6~2.0 1.5~2.0 2.5~3.0﹥400 2.0~2.5 2.0~2.5 3.0~3.5(2)铸件的临界壁厚在铸件结构设计时,为了充分发挥金属的潜力,节约金属,必须考虑铸造合金的力学性能对铸件壁厚的敏感性。
厚壁铸件容易产生缩孔、缩松、晶粒粗大、偏析和松软等缺陷,从而使铸件的力学性能下降。
从这个方面考虑,各种铸造合金都存在一个临界壁厚。
铸件的壁厚超过临界壁厚后,铸件的力学性能并不按比例地随着铸件壁厚的增加而增加,而是显著下降。
因此,铸件的结构设计应科学地选择壁厚,以节约金属和减轻铸件重量。
在砂型铸造工艺条件下,各种合金铸件的临界壁厚可按最小壁厚的3倍来考虑。
铸件壁厚应随铸件尺寸增大而相应增大,在适宜壁厚的条件下,既方便铸造又能充分发挥材料的力学性能。
表7-5,表7-6给出砂型铸造各种铸造合金的临界壁厚。
表1-5 砂型铸造各种铸造合金的临界壁厚(单位:㎜)合金种类与牌号当铸件重量(㎏)为下列值时0.1~2.5 2.5~10﹥10灰铸铁HT100,HT150HT200,HT250HT300HT3508~1012~1512~1815~2010~1512~1515~1815~2020~2512~182525可锻铸铁KTH300-06 KTH390-8KTH350-10 KTH370-26~106~1012~1210~12----球墨铸铁QT400-15 QT450-10QT500-7 QT230-31014~1815~2018~205060碳素铸钢ZG200-400 ZG230-450ZG270-500 ZG310-570ZG340-640181515252020------铝合金镁合金锡合金6~1010~14--6~1212~186~810~14----含碳量0.100.200.300.400.50临界壁厚1113.518.52539(3)铸件的内壁厚度砂型铸造时,铸件内壁散热条件差,即使内壁厚度与外壁厚度相等,但由于它比外壁的凝固速度慢,力学性能往往要比外壁低,同时在铸造过程中易在内、外壁交接处产生热应力致使铸件产生裂纹。
对于凝固收缩大的铸造合金还易产生缩孔和缩松,因此铸件的内壁厚度应比外壁厚度薄一些。
图1-1 铸件内壁的合理结构a,b)不合理c)合理合金类别铸铁铸钢铸铝铸铜铸件内壁比外壁厚度应减少的相10~2020~3010~2015~20对值%注:铸件内腔尺寸大的取下限对于锻钢制造的轴类零件来说,增大直径便可提高承载能力。
但对铸件来说,随着壁厚的增加,中心部分晶粒粗大,承载能力并不随壁厚增加而成比例地增加。
因此,在设计较厚铸件时,不能把增加壁厚当作提高承载能力的唯一办法。
为了节约金属,减轻铸件重量,可以选择合理的截面形状,如承受弯曲载荷的铸件,可选用“T”型或“工”型截面。
采用加强筋也可减小铸件壁厚。
一般筋厚﹤内壁厚﹤外壁厚。
2 . 铸件壁应合理连接铸件壁厚不均,厚薄相差悬殊,会造成热量集中,冷却不均,不仅易产生缩孔、缩松,而且易产生应力、变形和裂纹。
所以要求铸件壁厚尽量均匀,如图1-2(a)所示结构中壁厚不均,在厚的部分易形成缩孔,在厚薄连接处易形成裂纹。
改为1-2(b)结构后,由于壁厚均匀,即可防止上述缺陷产生。
也可用薄壁加加强筋结构。
加强筋的布置应尽量避免或减少交叉,防止习惯年成热节。
例如钳工划线平台,其筋条布置如图1-3所示。
铸件各部分壁厚不均现象有时不可避免,此时应采用逐渐过渡的方式,避免截面突然变化。
接头断面的类型大致可分为L、V、K、T 和十字型五种。
在接头处,凝固速度慢,容易产生应力集中、裂纹、变形、缩孔、缩松等缺陷。
在接头形式的选用中,应优选L型接头,以减小与分散热节点及避免交叉连接。
逐渐过渡的形式与尺寸如表7-8所示。
由表可知,壁厚差别不很大时,采用圆弧过渡();壁厚差别很大时,采用L型过渡,在同等情况下,铸钢件的过渡尺寸比铸铁件要大。
两壁相交,其相交和拐弯处要作成圆角。
图1-2 均匀壁厚避免形成热节举例3.结构斜度进行铸件设计时,凡顺着拔模方向的不加工表面尽可能带有一定斜度以便于起模,便于操作,简化工艺。
铸件垂直度越小,斜度越大。
综合以上所述,为了保证铸件质量,铸件的合理结构为:1)壁厚力求均匀,减小厚大断面,防止形成热节。
办法是将厚大部位挖去一部分;图7-52)内壁厚度应小于外壁。
因为内壁冷却慢,适当减薄(图7-6)。
3)应有利于补缩和实现顺序凝固。
有些铸件铸锭厚度较大或厚度不均。
如果该件所用合金的体积收缩较大,则很容易形成缩孔、缩松。
此时应仔细审查零件结构,尽可能采取顺序凝固方式,让薄壁处先凝,厚壁处后凝,使在厚壁处易于安放冒口补缩,以防止缩孔、缩松。
图7-74)注意防止发生翘曲变形。
细长杆状铸件,大平板铸件,增加加强筋及改变截面形状床身一类的铸件,其截面形状不允许变化,为防止其变形可采用反挠度,即在模样上采取反变形量。
如果既不能设加强筋,又不能该变截面形状,只好采用人工失效方法消除应力减少变形。
5)应避免水平方向出现较大平面。
大平面铸件的上部型砂时间受金属液体烘烤,容易造成夹砂。
解决的办法是倾斜浇注或设计成倾斜壁。
应避免铸件收缩时受到阻碍,否则会造成裂纹,对于收缩大的合金铸件尤其要注意这一点。
4 . 铸件结构设计原则(1)设计铸件壁厚时应考虑到合金的流动性;流动性越好的合金,充型能力越强,铸造时就不容易产生浇不足、冷隔等缺陷,因此,能铸出的铸件最小壁厚尺寸也就越小。
(2)铸型型腔的形状与尺寸大小是根据铸件的形状与尺寸决定的。
不同的型腔形状和尺寸对液态金属的流动的阻力,散热情况是不同的,从而会导致液态金属在型腔内的流动与填充情况不同。
因此,铸件结构上应尽量避免突变性的转变、壁厚急剧的变化、细长结构、大的水平面、高度较大的凸台等。
(3)一个铸件在生产过程中是否出现缩孔、缩松、变形、热裂、冷裂等收缩类铸造缺陷,出现在哪个部位、严重程度如何,都与铸件结构密切相关。
由此可以得出指导铸件结构设计的原则:1)对凝固收缩大,容易产生集中缩孔的合金,如铸钢、球墨铸铁、可锻铸铁、黄铜、无锡青铜、铝硅共晶合金等,倾向于采用顺序凝固方式铸造。
这时在进行铸件结构设计时,应使铸件结构形式有利于顺序凝固。
2)对溶液产生缩松的合金,如锡青铜、磷青铜等采用冒口补缩效果不大,常采用同时凝固方式来使缩松更分散些;对收缩较小的合金,如铸铁更倾向于采用同时凝固方式铸造。
这时铸件的结构应是壁厚均匀,尽量减少金属的聚集与消除热节。
对于一些结构形状复杂的大铸件,也可将其各部分按顺序或同时凝固方式设计。
3)尽量使铸件结构有利于自由收缩,如尽量减少铸件的轮廓尺寸,减少突出部分,必要时可将一个铸件分成几个小铸件,然后用焊接或螺栓连接起来。
4)尽量避免产生应力集中的形状,如不应有尖角、不同壁厚之间的连接要平缓。
5)应考虑到各种铸造方法的工艺过程、凝固特点、铸型和型芯的特点。
尤其市使用金属铸型和型芯的铸造方法。
如金属型铸造、压力铸造,应便于铸件的抽芯和出芯。
二、从生产工艺考虑—简化工艺便于操作—角度对铸件结构提出的要求铸件结构不仅应有利于保证铸件质量,防止和减少铸造缺陷,而且应保证造型、制芯、清理等操作的方便,以利于提高生产率和降低成本。