水玻璃模壳解决裂壳的方法讲述讲解
提高墙体强度的裂缝修补方法
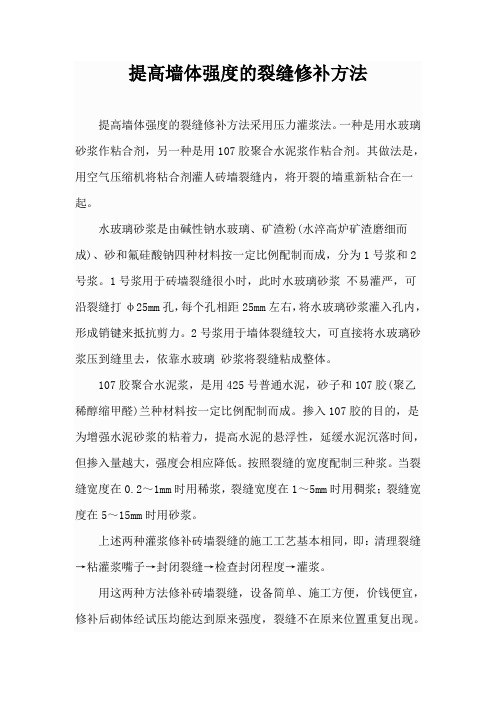
提高墙体强度的裂缝修补方法
提高墙体强度的裂缝修补方法采用压力灌浆法。
一种是用水玻璃砂浆作粘合剂,另一种是用107胶聚合水泥浆作粘合剂。
其做法是,用空气压缩机将粘合剂灌人砖墙裂缝内,将开裂的墙重新粘合在一起。
水玻璃砂浆是由碱性钠水玻璃、矿渣粉(水淬高炉矿渣磨细而成)、砂和氟硅酸钠四种材料按一定比例配制而成,分为1号浆和2号浆。
1号浆用于砖墙裂缝很小时,此时水玻璃砂浆不易灌严,可沿裂缝打φ25mm孔,每个孔相距25mm左右,将水玻璃砂浆灌入孔内,形成销键来抵抗剪力。
2号浆用于墙体裂缝较大,可直接将水玻璃砂浆压到缝里去,依靠水玻璃砂浆将裂缝粘成整体。
107胶聚合水泥浆,是用425号普通水泥,砂子和107胶(聚乙稀醇缩甲醛)兰种材料按一定比例配制而成。
掺入107胶的目的,是为增强水泥砂浆的粘着力,提高水泥的悬浮性,延缓水泥沉落时间,但掺入量越大,强度会相应降低。
按照裂缝的宽度配制三种浆。
当裂缝宽度在0.2~1mm时用稀浆,裂缝宽度在1~5mm时用稠浆;裂缝宽度在5~15mm时用砂浆。
上述两种灌浆修补砖墙裂缝的施工工艺基本相同,即:清理裂缝→粘灌浆嘴子→封闭裂缝→检查封闭程度→灌浆。
用这两种方法修补砖墙裂缝,设备简单、施工方便,价钱便宜,修补后砌体经试压均能达到原来强度,裂缝不在原来位置重复出现。
水玻璃注浆施工方案

水玻璃注浆施工方案1. 引言水玻璃注浆施工是一种常用于建筑工程中的修复方法,通过注入水玻璃浆料来加固和修复混凝土结构的裂缝和空洞。
本文将介绍水玻璃注浆施工的具体方案和步骤,以及施工前的准备工作和注意事项。
2. 施工准备在进行水玻璃注浆施工前,需要进行以下准备工作:2.1 施工材料准备•水玻璃浆料:根据具体工程需要选取合适的水玻璃浆料,要求浓度适宜;•注浆设备:包括注浆泵、注浆管道等;•注浆辅材:注浆管接头、止水带、胶带等。
2.2 施工工具准备•钻孔机:用于打孔,选择适合的孔径和深度;•喷枪和钢丝刷:用于清理钻孔孔壁和修复区域表面;•测量工具:用于测量孔深和孔径。
2.3 施工人员准备•注浆施工人员:具备相关施工经验和操作技能;•安全防护人员:负责施工现场的安全管理和监督。
3. 施工步骤水玻璃注浆施工的步骤如下:3.1 孔洞处理根据设计要求和实际情况,确定需要进行注浆修复的孔洞的位置和数量。
在施工前,先进行孔洞处理,包括以下步骤:1.使用钻孔机在需要修复的混凝土结构上钻孔,孔的直径和深度根据设计要求确定;2.清理钻孔孔壁的灰尘和碎块,确保孔洞的内壁干净;3.检查钻孔孔径和深度是否符合设计要求,如不符合,则进行调整。
3.2 样板制作在施工前,需要制作样板,用于控制注浆的位置和流动方向。
制作样板的步骤如下:1.根据设计要求,制作与钻孔孔径一致的样板;2.预留与注浆管道连接的孔口;3.将样板固定在需要修复的结构上,确保其位置准确。
3.3 注浆施工注浆施工是整个水玻璃修复过程中最重要的一步。
施工步骤如下:1.连接注浆设备,确保设备完好并处于正常工作状态;2.将注浆管道插入到预留的孔口中,确保与孔洞之间无泄漏;3.开启注浆设备,将水玻璃浆料注入到孔洞中;4.注浆时,应逐渐提高注浆压力,控制注浆流速;5.注浆过程中,注浆管道应保持稳定不动,确保注浆材料填充整个孔洞;6.注浆完毕后,检查注浆点的固化情况,确保修复效果良好。
水玻璃型壳熔模铸造制壳工艺过程控制

水玻璃型壳熔模铸造制壳工艺过程控制作者:董丽华来源:《中国科技纵横》2018年第21期摘要:近年来,随着中国的铸造业发展迅速。
其中由于熔模铸造可以做到少切削,不切削,复杂件成型率高,生产工艺水平越来越高,其市场也越来越大。
而大部分的铸件生产任然采用的是水玻璃工艺,这种工艺最大的问题就是不稳定性,所以对水玻璃制壳质量控制要求和生产管理要点的讨论就显得很有必要。
实践证明,通过加强关键工序的控制和质量因素的综合控制,产品质量和成品率会有了显著的提高。
关键词:水玻璃;熔模铸造;制壳;工艺;控制中图分类号:TG249.5 文献标识码:A 文章编号:1671-2064(2018)21-0086-02由于水玻璃粘结剂的价格低廉,制壳周期短,因此在我国广泛采用水玻璃工艺精密铸造。
但是,与传统砂型铸造相比,水玻璃壳型铸造成本高,工艺复杂,生产周期长。
型壳是影响铸件质量的重要因素之一。
如何控制其质量具有重要意义。
本文结合生产实践,对壳的原材料控制和管理和制壳工艺的改善,改善型壳强度及稳定性,从而提高铸件质量及其成品率。
1 原材料的选择与控制1.1 水玻璃硅酸钠的水溶液俗称水玻璃,南方一般被称为水玻璃,北方一般被称为泡化碱。
硅酸钠的形态可分为液体、固体和水淬三种形态。
水玻璃可分为钾水玻璃和钠水玻璃。
熔模铸造中一般采用的是钠水玻璃。
水玻璃中二氧化硅和氧化钠(或氧化钾)的摩尔比通常称为模数(M)。
硅酸钠是水分散体系中的无色、浅色透明或半透明粘稠液体。
固体硅酸钠是一种无色和浅色的透明或半透明玻璃。
硅酸钠在的凝固与石灰非常相似。
主要通过碳化、脱水、固化三个工序来实现。
随着二氧化硅含量的增加,游离水蒸发,硅胶脱水成固体SiO2并固化。
由于空气中CO2浓度低,碳化反应和固化过程非常缓慢。
1.2 水玻璃的特性熔模铸造生产时水玻璃应为液态,纯净的水玻璃是一种外观显无色透明的粘滞性溶液,含有杂质时则显青灰色或者淡黄色。
水玻璃溶液显碱性,一般高、中模数的水玻璃的PH值为11~13。
水玻璃模壳解决裂壳的方法

水玻璃模壳解决裂壳的方法-1;1.水玻璃模壳裂壳的概述;1.1低温蜡蜡模,水玻璃制壳工艺的裂壳行为;1.2由于冬天气温低,原材料的化学特性随着气温而;溶液都会变得黏稠;1.3天气温度降低,浆料的粘度相同粉液比低;硬化;为溶液黏稠而渗透效果变差,导致结晶氯化铝的硬化能;另外也不排除操作的因素导致模壳开裂;1.4实践证明,水玻璃模壳裂壳与气温有直接关系;制做的模水玻璃模壳解决裂壳的方法-11.水玻璃模壳裂壳的概述1.1低温蜡蜡模,水玻璃制壳工艺的裂壳行为。
1.2由于冬天气温低,原材料的化学特性随着气温而变化。
水玻璃溶液、氯化铝溶液都会变得黏稠。
1.3天气温度降低,浆料的粘度相同粉液比低;硬化液的溶解度也低、同时也因为溶液黏稠而渗透效果变差,导致结晶氯化铝的硬化能力显著下降。
另外也不排除操作的因素导致模壳开裂。
1.4实践证明,水玻璃模壳裂壳与气温有直接关系。
上个星期,气温接近零度,制做的模壳,每晚浇注都有裂壳的发生。
而这几天的气温有所回升,最低温度在3~5℃,晚上浇注的模壳裂壳就莫名其妙地消失了。
1.5熔模铸造用的是碱性水玻璃(硅酸钠)。
其理化指标:①外观:白灰色或淡青色,均匀分散相,无团絮状。
目测,要求一致性。
②PH值:11~13,用广泛试纸检测,色差对照,一般PH值是12.③密度:要求D=1.35~1.37.用玻璃密度计检测,密度多为1.36.2.工艺解决水玻璃模壳裂壳的方法2.1原水玻璃制壳参数①面层水玻璃密度1.30,9#石英粉,浆料45~55S,国标量杯,撒40~70目精白石英砂。
氯化铵溶液硬化,硬化时间10~15min。
②二层水玻璃密度1.35,200目莫来粉浆料,35~45S,国标量杯,撒30~6 0目莫来砂。
氯化铵溶液硬化,硬化时间15~25min。
③三层水玻璃密度1.35,200目莫来粉浆料,38~48S,国标量杯,撒16~30目莫来砂。
氯化铝溶液硬化,硬化时间35min以上。
④四、五、六层水玻璃密度1.35,耐火泥4:石英粉1混合浆料,50~60S,国标量杯,撒8~16目红砂。
水玻璃熔模铸造介绍

水玻璃熔模铸造介绍变量和公差熔模铸造又称“失蜡铸造”,通常是在蜡模表面涂上数层耐火材料,待其硬化干燥后,将其中的蜡模熔去而制成型壳,再经过焙烧,然后进行浇注,而获得铸件的一种方法。
由于获得的铸件具有较高的尺寸精度和表面光洁度,故又称“熔模精密铸造”。
可用熔模铸造法生产的合金种类有碳素钢、合金钢、耐热合金、不锈钢、精密合金、永磁合金、轴承合金、铜合金、铝合金、钛合金和球墨铸铁等。
熔模铸件的形状一般都比较复杂,铸件上可铸出孔的最小直径可达0.5mm,铸件的最小壁厚为0.3mm。
在生产中可将一些原来由几个零件组合而成的部件,通过改变零件的结构,设计成为整体零件而直接由熔模铸造铸出,以节省加工工时和金属材料的消耗,使零件结构更为合理。
熔模铸件的重量大多为零点几十牛(即几十克到几公斤),太重的铸件用熔模铸造法生产较为麻烦,但目前生产大的熔模铸件的重量已达800牛左右。
溶膜铸造是用易熔材料制成模型,然后在模型上涂挂耐火材料,经硬化后,在将模型熔化排出型外,从而获得无分型面的铸型,铸型焙烧后即浇注。
一. 工艺过程:1. 蜡模制作1) 压型:制蜡模的专用模具、钢、铜、铝、切削而成2) 蜡模的压制:石蜡、峰蜡、硬脂酸、松香等,将熔化的蜡料压入压型中,冷凝后取出,修去毛刺,得到蜡模3) 蜡模组装:若干蜡模焊在一个直浇棒上2. 结壳:蜡模涂上涂料、硬化、干燥等1) 浸涂料(石英粉+粘结剂的糊状物)表面光洁2) 撒砂(粗石英砂)的目的:增厚型壳3) 硬化(水玻璃+NH4CL—SIO2)化学硬化3. 脱蜡、焙烧1) 脱蜡:热水或水蒸气2) 焙烧:加热800~1000℃提高型壳强度4. 填砂:浇注1) 填砂:型壳放入铁箱中,周围干砂充填2) 浇注:趁热(600~700℃)进行浇注5. 落砂清理冷却后,破坏型壳,取出铸件,去浇口、毛刺、退火或正火,以便得到所需机械性能1) 铸造精度、光洁度高、且可浇注形状复杂的件2) 能铸造各种合金(型壳是高级耐火材料)3) 单件、小批、大批量生产均可4) 少无切削加工(Ra3.2~1.6um)稍磨5) 材料贵,工艺过程繁杂,生产周期长应用:使用高熔点合金精密铸件的成批、大量生产,形状复杂,难以切削加工的小零件。
熔模铸造水玻璃型壳质量控制

熔模铸造水玻璃型壳质量控制许晓兰,高明轩,陈学敏(霍州煤电集团机电修配分公司,山西霍州031400)摘 要:全过程论述了铸造水玻璃型壳的质量控制要点。
实践证明,通过对型壳质量影响因素的综合控制,使铸件的质量有了明显的提高。
关键词:铸造;水玻璃;型壳;质量中图分类号:T Q171 文献标识码:A 文章编号:1008-8725(2003)10-0084-021 水玻璃粘结剂的质量控制(1)水玻璃种类的选择:市场供应的水玻璃有两种,一种是纯碱与石英粉在1300~1400℃温度下反应得到的,杂质含量少,性能稳定;另一种是采用芒硝生产,杂质含量较高。
通常第一种方法生产的水玻璃较适合熔模铸造选用。
(2)水玻璃模数(M)、密度(ρ),控制M取决于S iO2和Na2O的相对含量,而ρ的高低又决定着S iO2的含量。
M和ρ直接影响型壳的表面强度、常温强度、高温强度及残留强度。
在我厂生产中,控制面层涂料水玻璃的M=3.0~3.2,ρ=1.27~1.29。
加固层M=3.0~3.2,ρ=1.30~1.34。
当M和ρ不符合要求时,用酸或碱来调整M,用水或高密度的水玻璃调整ρ,使用效果良好,既保证了壳体的各种常温、高温性能,又有较低的溃散强度。
在实际生产中,水玻璃的假模数对型壳高温强度的影响很大。
当M>310时,水玻璃存放时间越长粘度越大。
由于水玻璃中有游离的S iO2存在,储存一定时间后,S iO2沉积在容器的底部,导致水玻璃模数下降,严重影响型壳的高温强度。
这主要是由于生产厂制做水玻璃时,S iO2和Na2O不是以化合态存在,或者为了提高模数,加入细石英粉造成的。
所以,在使用过程中,为了防止游离S iO2存在使模数高的假象,当水玻璃卸车时化验一次,存放24h后再化验一次。
以保证型壳的质量。
对于沉积于容器底部的杂质,必须在一定时间内予以清理,一般容量在15~20t的储罐,每二年要清理一次。
2 粉料粒度分布对型壳质量的影响与控制生产中,较粗的粉料(手感)所制得的涂料沉淀快,流杯粘度大,工艺稳定性差,生产出的铸件表面粗糙。
熔模铸造型壳六大缺陷分析 入木三分
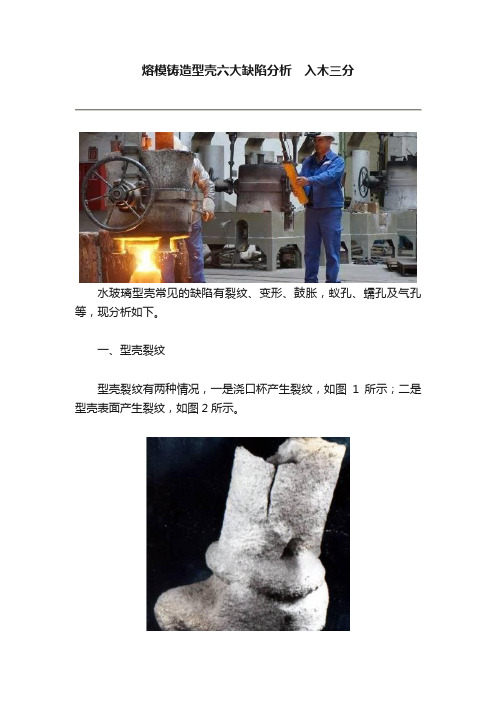
熔模铸造型壳六大缺陷分析入木三分水玻璃型壳常见的缺陷有裂纹、变形、鼓胀,蚁孔、蠕孔及气孔等,现分析如下。
一、型壳裂纹型壳裂纹有两种情况,一是浇口杯产生裂纹,如图1所示;二是型壳表面产生裂纹,如图2所示。
图1 浇口杯裂纹图2 型壳表面裂纹浇口杯裂纹特征:型壳的浇口杯有裂纹,严重时浇口杯开裂。
型壳表面裂纹:在型壳的表面上有弯曲的、深浅不等的裂纹。
1.产生原因(1)涂料中水玻璃的模数、密度过高或过低;涂料中的粉液比过低;或硬化剂的浓度、温度和硬化时间不当,硬化不充分;或型壳在硬化前的自然风干时间不够,不利于硬化剂的继续渗透硬化,影响了硅凝胶的连续性和致密性;或型壳的层数不够等原因,导致型壳的强度低,出现了裂纹。
(2)涂料层涂挂的不均匀,或撒砂层厚薄不均;尤其是浸涂料后没有撒上砂的部位,硅凝胶在收缩时受力不均匀,导致型壳产生裂纹。
(3)脱蜡液的温度低,脱蜡时间太长。
由于蜡料的热膨胀系数大于型壳的热膨胀系数,脱蜡缓慢将导致型壳在脱蜡的过程中受到各种应力的作用;如果超过此时型壳的强度极限,就会产生裂纹,甚至开裂。
(4)焙烧时,型壳入炉温度高,升温过快,或高温出炉急冷;或型壳多次焙烧,产生微裂纹,甚至裂纹,降低了强度;或型壳的高温强度低,使型壳在焙烧时产生裂纹。
(5)清理浇口杯时,机械损伤浇口杯。
2.防止措施(1)采用下列措施,型壳的高温强度就高。
①水玻璃的模数M=3.0~3.4,密度ρ=1.30~1.33 g/cm3配制的加固层涂料。
②采用合理的涂料配制工艺,并执行涂料的“配比-温度-粘度”曲线。
③采用合理的硬化工艺,控制硬化剂的“浓度-温度-硬化时间”;或选用氯化铝代替氯化铵硬化型壳。
④合理的制壳工艺,如涂料粘度与撒砂粒度的合理配合,硬化工艺参数要确保型壳充分硬化。
⑤采取措施增加型壳强度,如常用的增加型壳层数,或采用复合型壳等;必要时大件型壳可用铁丝加固等。
(2)蜡模浸入检验合格的涂料中,上下移动和不断地转动,提起后滴去多余的涂料,使涂料均匀地覆盖在模组的表面上;不能出现涂料的局部堆积或缺少涂料(漏涂);并及时、均匀撒砂。
水玻璃注浆施工方案

水玻璃注浆施工方案水玻璃注浆施工方案为了解决某建筑物的裂缝问题,需要进行水玻璃注浆施工。
本文将详细介绍该施工方案。
一、施工准备工作1.安全措施:在施工现场设置明显的警示标志,并佩戴好安全帽、防护手套等个人防护设备。
2.清理现场:清理施工现场,清除周围的杂物和尘土,确保施工区域的整洁。
3.准备材料:准备好水玻璃注浆所需的材料,包括水玻璃、注浆泵、注浆管等。
二、施工步骤1.检查裂缝情况:对建筑物的裂缝进行检查,确定裂缝的位置、长度和宽度。
2.清洁裂缝:用清洁剂和刷子清洁裂缝,确保裂缝表面干净无尘。
3.注浆准备:将水玻璃按照比例与清水混合,搅拌均匀,制成均质的注浆液。
4.注浆施工:使用注浆泵将注浆液注入裂缝中,从裂缝的底部开始注入,逐渐向上注满整个裂缝。
三、验收及保养1.施工完毕后,对注浆施工的质量进行验收,检查注浆是否充实、均匀,无漏注现象。
2.保养施工区域,防止施工后再次出现裂缝。
在注浆完成后,尽量避免人员和设备的碰撞,确保注浆得以充分固化。
3.定期对施工区域进行巡检,发现及时处理可能出现的问题。
四、施工注意事项1.施工人员必须具备一定的工程质量监督经验,了解水玻璃注浆施工技术和过程,能够熟练操作注浆设备。
2.在施工过程中,要注意注浆液的比例和搅拌均匀度,确保注入裂缝的注浆液质量合格。
3.施工现场必须保持干燥,避免水或雨水进入裂缝,影响注浆质量。
4.注意施工区域的通风,避免注浆液散发的气味对施工人员造成伤害。
通过以上施工方案,可以有效地解决建筑物裂缝问题,提高建筑物的稳定性和安全性。
同时,在施工过程中必须严格按照安全操作规程进行,确保施工人员的人身安全。
- 1、下载文档前请自行甄别文档内容的完整性,平台不提供额外的编辑、内容补充、找答案等附加服务。
- 2、"仅部分预览"的文档,不可在线预览部分如存在完整性等问题,可反馈申请退款(可完整预览的文档不适用该条件!)。
- 3、如文档侵犯您的权益,请联系客服反馈,我们会尽快为您处理(人工客服工作时间:9:00-18:30)。
水玻璃模壳解决裂壳的方法-1;1.水玻璃模壳裂壳的概述;1.1低温蜡蜡模,水玻璃制壳工艺的裂壳行为;1.2由于冬天气温低,原材料的化学特性随着气温而;溶液都会变得黏稠;1.3天气温度降低,浆料的粘度相同粉液比低;硬化;为溶液黏稠而渗透效果变差,导致结晶氯化铝的硬化能;另外也不排除操作的因素导致模壳开裂;1.4实践证明,水玻璃模壳裂壳与气温有直接关系;制做的模水玻璃模壳解决裂壳的方法-11.水玻璃模壳裂壳的概述1.1低温蜡蜡模,水玻璃制壳工艺的裂壳行为。
1.2由于冬天气温低,原材料的化学特性随着气温而变化。
水玻璃溶液、氯化铝溶液都会变得黏稠。
1.3天气温度降低,浆料的粘度相同粉液比低;硬化液的溶解度也低、同时也因为溶液黏稠而渗透效果变差,导致结晶氯化铝的硬化能力显著下降。
另外也不排除操作的因素导致模壳开裂。
1.4实践证明,水玻璃模壳裂壳与气温有直接关系。
上个星期,气温接近零度,制做的模壳,每晚浇注都有裂壳的发生。
而这几天的气温有所回升,最低温度在3~5℃,晚上浇注的模壳裂壳就莫名其妙地消失了。
1.5熔模铸造用的是碱性水玻璃(硅酸钠)。
其理化指标:①外观:白灰色或淡青色,均匀分散相,无团絮状。
目测,要求一致性。
②PH值:11~13,用广泛试纸检测,色差对照,一般PH值是12.③密度:要求D=1.35~1.37.用玻璃密度计检测,密度多为1.36.2.工艺解决水玻璃模壳裂壳的方法2.1原水玻璃制壳参数①面层水玻璃密度1.30,9#石英粉,浆料45~55S,国标量杯,撒40~70目精白石英砂。
氯化铵溶液硬化,硬化时间10~15min。
②二层水玻璃密度1.35,200目莫来粉浆料,35~45S,国标量杯,撒30~6 0目莫来砂。
氯化铵溶液硬化,硬化时间15~25min。
③三层水玻璃密度1.35,200目莫来粉浆料,38~48S,国标量杯,撒16~30目莫来砂。
氯化铝溶液硬化,硬化时间35min以上。
④四、五、六层水玻璃密度1.35,耐火泥4:石英粉1混合浆料,50~60S,国标量杯,撒8~16目红砂。
氯化铝溶液硬化,硬化时间60min以上。
⑤半层水玻璃密度1.35,耐火泥4:石英粉1混合浆料,30~35S,国标量杯。
氯化铝溶液硬化,硬化时间60min以上.⑥半层后过4h进行脱蜡。
2.2涂层硬化指标氯化铵溶液的密度1.10,PH 6.0~6.5,硬化模壳涂层前搅动,然后再硬化壳层。
结晶氯化铝溶液的密度1.18~1.20之间,低于1.18就补加氯化铝,PH值2.5~3.0之间。
PH值高于3.0就加入盐酸降低PH值。
另补加润湿剂降低氯化铝的粘稠度,润湿剂的加入量0.1%。
每个星期加入一次。
2.3改进水玻璃制壳参数面层石英粉浆料,撒40~70目石英砂。
氯化铵硬化。
二层石英粉浆料,撒20~40目石英砂,氯化铵硬化。
三层耐火泥+石英粉浆料,撒16~30目红砂,氯化铝硬化。
四层、五层耐火泥+石英粉浆料,做8~16目红砂,氯化铝硬化。
半层耐火泥+石英粉浆料,浆料要稀,能够黏住砂子即可,氯化铝硬化。
注:这种改进后的参数制壳,对于裂壳有好转,但是还有裂壳的。
2.4用复合工艺做找出裂壳的原因所在前三层用硅溶胶制壳,后面加固层用水玻璃制壳。
用复合工艺找出裂壳的原因所在。
3.导致水玻璃模壳裂壳的因素3.1裂壳检查:①秋天的时候,裂壳的模壳敲开看,壳层用力可以搓碎。
而现在冬天的裂壳壳层强度很高,用手搓不碎的,要使劲才可以扳断,证明冬天的模壳刚性比较大。
②将开裂的模壳敲开看检查:A,边角部位比其他部位要薄一些(而模壳开裂也都是边角部位)。
并且模壳开裂处是有规律性的,都是大法兰面的棱角开裂的。
B,用一片模壳,由面层向外折,用力才可以折断;从半层往里折,一折就断。
同一片模壳,加固层断面结构疏松,强度低。
注:对于模壳太酥,强度低。
明显是硬化不好,也证明前三层氯化铵硬化效果比加固层氯化铝的硬化效果好的多。
3.2裂壳因素①在细砂做层数多的情况下,而模壳层数也多,模壳就容易裂壳。
②加固层浆料浓有两个缺点:一是浆料浓导致模壳高温时收缩过大而开裂;二是浆料浓导致氯化铝硬化不透而硬化不好,导致壳层强度低。
③加固层硬化后的干燥时间短,导致硬化液没有有效地渗透以及涂层表面有残留的硬化液妨碍层间有效结合。
④氯化铝硬化液,加盐酸后,模壳会变脆,变脆后,容易裂壳。
⑤加固层用氯化铝溶液硬化,硬化时间太长导致模壳的刚性加大,也会发生裂壳。
⑥如果裂壳部位是规律性在棱角处,一是操作的时候将砂擦掉了一部分,二是棱角部位的浆砂粘的比较少。
⑦模壳入炉初始的火力不能太猛,火力太旺也会导致裂壳。
⑧白天脱蜡的模壳,随即在晚上焙烧、浇注,模壳也会开裂(这是因为水脱蜡的模壳,壳层中的水分还未来得及挥发,模壳入炉后,水分快速蒸发从而产生急剧收缩,产生应力收缩而导致模壳开裂)。
⑨还有一种可能,就是前三层的耐火粉、耐火砂的膨胀系数比加固层的耐火粉、耐火砂的膨胀系数大,在高温时,前三层因为膨胀率比加固层大,所以将加固层撑胀开裂了。
4.裂壳原因及改进措施4.1浆料没有充分搅拌润湿的生料也会导致裂壳。
改进措施:①新配浆料充分搅拌;补充浆料每次在制壳之前进行搅拌均匀后再做涂层。
②每次做加固层之前,将浆料表面的结皮、结块和杂物捞掉。
4.2浆料粘度不正确引起的裂壳:①加固层的浆料太浓,硬化时导致涂层硬化不透,焙烧时导致涂层收缩过剧,模壳就会开裂。
改进措施:浆料不能浓,也不能稀,让下一层的砂子能够钻进本层的浆料、上层的砂子的空隙中去(浆料浸涂后,可以看到上层的砂子露出尖率30%)。
②半层浸浆后进入硬化池硬化,拿出后发现,模壳表面会产生裂隙(纹),浆料越浓裂隙越大(这是粉粒聚集收缩产生的裂隙)。
改进措施:半层的浆料应该稀薄,只要能够糊住砂子就可以了,避免裂隙的发生。
4.3加固层浆料中的粉料比例不当引起的裂壳:①如果耐火泥有问题:改进措施:换质量好的耐火泥,或者换河包粉配制浆料。
②粉料比例不当:改进措施加固层配浆是用耐火泥+石英粉,提高石英粉的比例,或者改为耐火泥+莫来粉(石英粉在高温时会产生相变,容易裂壳)。
4.4浆料温度低导致粘滞加大引起的裂壳:改进措施:①寒冷的冬季,为防止浆料结冰和影响使用。
浆料一般须是放在有暖气的房屋内,或者用绝热材料进行保温。
②如果浆料在室外,须给浆料加温后再进行制做涂层。
4.5用砂不当引起的裂壳:①加固层砂子粒度太细引起的裂壳:改进措施:选用粒度粗的型砂。
②加固层撒红砂只做一层半导致裂壳:改进措施:从三层就使用红砂,这样会使加固层在高温时收缩一致,表面壳层开裂。
4.6正确选用粉砂①由于淮北莫来砂粉,杂质含量低,在高温时不能再次烧结,所以模壳强度低会开裂。
改进措施:使用章丘产的C 级莫来粉和C级莫来砂。
②加固层使用红砂,由于红砂属于生料,在高温时会产生相变,导致壳层收缩不一致而裂壳。
改进措施:实践证明,水玻璃制壳用再生回用的粉砂,模壳就不会开裂(因为再生的粉砂是经过高温焙烧过,性能稳定)。
③实践证明,前三层使用石英粉浆料,加固层使用莫来粉浆料,这二者在高温时的膨胀系数不同,往往会导致裂壳。
改进措施:从二层起就使用莫来粉、莫来砂。
4.7氯化铵氯化铝溶液硬化不当引起的裂壳①面层、二层氯化铵溶液硬化的时间不能过长,过长会导致壳层开裂。
改进措施:缩短面层、二层氯化铵溶液的硬化时间。
②冬天气温低,氯化铝的粘滞性加大;加上氯化铵、氯化铝的溶解度随温度降低而降低,都会造成硬化速度慢和硬化不透。
改进措施:A, 氯化铝池子里定期加入润湿剂,以期提高氯化铝的渗透效果。
B, 氯化铝溶液在硬化前加热。
C, 加固层加长在氯化铝溶液里的硬化时间,半层在氯化铝硬化池里过夜。
D, 涂层硬化后风干时间也要延长。
③控制氯化铝溶液的质量:A,单纯用密度、酸碱度控制硬化液浓度是有偏差的,随着硬化液里氯化钠溶解量的增加,硬化液比重虽然不变但有效硬化剂含量却减小了,硬化效果也越来越差。
因此须根据生产情况定期整体更换硬化液。
B, 氯化铝硬化液长期使用,钠盐含量越来越多,须检测氯化钠的浓度,当浓度超过8%,就需要彻底更换硬化液(重配新液)。
C,氯化铵溶液、氯化铝溶液的密度和PH每天都检测。
如不合格,调整到正常后使用。
4.8涂层硬化效果的检测:当模壳(涂层)进入硬化池,硬化的过程中,拿起模壳,用手指抠涂层或者用手搓浇口杯边上的涂层,如果还是软化的,表示涂层没有硬化透。
5.其他解决裂壳的方法5.1蜡模边角是直角,面层二层浆粘不上;边角锋利,导致浆砂粘附的很少,局部壳层就很薄在高温时就会开裂。
改进措施:将蜡件的边角在模具上做出R角,模具上做不出的,就要求工人将边角倒角。
5.2由于模壳棱角部位浆砂粘附的比较少, 在四层或者五层后绑铁丝加固。
棱角处砂子粘得少,在制壳时撒砂须撒匀,尖角处轻轻按上撒的砂子。
5.3对于容易裂壳的产品,组树时,将蜡模(产生裂隙)的两边平面上组焊长方形的工艺钉,使壳层在高温时收缩受阻(定位钉阻碍壳层收缩),防止裂壳。
5.4用氯化铵、氯化铝交替硬化涂层:面层氯化铵硬化,二层用氯化铝硬化;三层氯化铵硬化,四层氯化铝硬化。
这样交替硬化各层涂层,其硬化效果可能会好一些。
5.5加固层用氯化铝和氯化铵混合溶液(氯化铵与氯;硬化,这样硬化的壳层强度会更好一些(氯化铝内掺氯;5.6模壳制好,须在8小时后脱蜡;5.7焙烧模壳时不要一直升温,升到350度左右保;850℃保温;5.8下班前洒水在浆料表面解决结皮,此法操作不当;为给浆料桶加盖;6.裂壳的补救措施;6.1焙烧后裂开的模壳,将模壳拿到一边,让模壳稍;层的稀浆料浸渍一下,让浆料5.5加固层用氯化铝和氯化铵混合溶液(氯化铵与氯化铝按照一定的比例配制)硬化,这样硬化的壳层强度会更好一些(氯化铝内掺氯化铵或氯化镁做复合型硬化剂进行硬化)。
5.6模壳制好,须在8小时后脱蜡。
另外模壳焙烧前最好先风干。
5.7焙烧模壳时不要一直升温,升到350度左右保温0.5~1小时,然后再升温至850℃保温。
5.8下班前洒水在浆料表面解决结皮,此法操作不当会造成型壳强度降低,须改为给浆料桶加盖。
6.裂壳的补救措施6.1焙烧后裂开的模壳,将模壳拿到一边,让模壳稍稍冷却之后,用水玻璃加固层的稀浆料浸渍一下,让浆料渗进裂开的缝隙之中去,然后就可以拿去接钢水。
6.2模壳焙烧后发生裂隙,从焙烧炉内拿出,让模壳浇口杯朝下防置,让其冷却到常温后,用塑料袋将浇口杯口套住,然后将模壳按进水玻璃溶液中,让水玻璃溶液进入裂隙中,拿出、风干,再将模壳在加固层浆料中补做一层涂层,再做一下半层,半层硬化后,自然晾干,然后就可以直接浇注钢水了,当然能够烘烤一下更好。
6.3裂壳的模壳用树脂砂胶合剂直接修补,烘烤下就可以浇注,效果很好。
7.结论语水玻璃模壳裂壳,是熔模铸造行业的一个通病,在生产过程中时有发生,给企业造成了不小的损失。