夹杂物控制攻关方案
科技成果——重轨钢中非金属夹杂物控制关键技术

科技成果——重轨钢中非金属夹杂物控制关键技术技术开发单位北京科技大学技术领域钢铁冶金成果简介铁路作为一种现代化交通运输工具,在世界范围内具有广阔的发展前景。
目前铁路发展的整体趋势是高速和重载化,对重轨钢质量提出了更高的要求,不仅要求高洁净度,高强度、高韧性,而且必须具有良好的抗疲劳性能。
重轨钢生产过程及使用过程中,非金属夹杂物是影响其质量最重要的原因之一,常引起探伤不合、易产生疲劳裂纹等,主要是由于其钢中非金属夹杂物控制存在以下三个难题:(1)夹杂物尺寸大且化学成分复杂;(2)冶炼工艺复杂,尤其在于脱氧及精炼等重要环节;(3)尖晶石类夹杂物突出,严重恶化钢轨性能。
因此合理控制重轨钢中的非金属夹杂物,对重轨钢产品质量的提升及铁路事业的进步具有重要意义。
(1)重轨钢冶炼脱氧及原辅料成分设计技术。
重轨钢采用无铝脱氧工艺,但是在脱氧剂的使用方式及用量上缺乏理论指导,因此,重轨钢脱氧过程中必须对脱氧剂的使用方式及用量进行合理优化控制,本项目提出仅在转炉出钢时加入少量硅钙钡脱氧剂控氧,同时配合精炼扩散脱氧,能将钢中T.O.含量控制在10ppm以下,不仅有效节约了生产成本,而且促进了夹杂物的去除、有效降低了夹杂物的尺寸。
在重轨钢冶炼原材料的控制方面,国内企业生产时更倾向于买价格低廉的铁合金等原材料,从而降低生产成本,但是对于铁合金及铁合金对重轨冶炼的影响研究几乎为空白。
本项目提出了使用低铝铁合金,降低钢中的酸溶铝含量,抑制钢中高Al2O3夹杂物的形成,从而提升夹杂物变形能力,有效防止因脆性夹杂物造成的疲劳缺陷。
(2)重轨钢中硫化物夹杂控制技术。
由于MnS有良好的变形能力,而且重轨钢轧制过程中变形量大,MnS夹杂物可能延伸很长,可能成为夹杂物超标和引起超声波探伤不合的重要原因之一。
此外,大尺寸长条状MnS可能成为裂纹的起点,在应力作用下首先在和钢基体的交界处形成裂纹源。
本项目首先通过优化精炼造渣制度进一步去除钢中S含量,提出将钢中得S降低到40ppm以下。
中间包夹杂物的去除与控制新技术
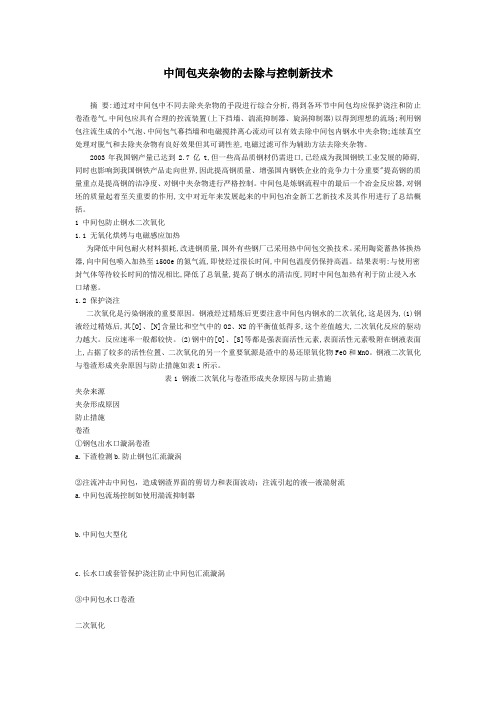
中间包夹杂物的去除与控制新技术摘要:通过对中间包中不同去除夹杂物的手段进行综合分析,得到各环节中间包均应保护浇注和防止卷渣卷气,中间包应具有合理的控流装置(上下挡墙、湍流抑制器、旋涡抑制器)以得到理想的流场;利用钢包注流生成的小气泡、中间包气幕挡墙和电磁搅拌离心流动可以有效去除中间包内钢水中夹杂物;连续真空处理对脱气和去除夹杂物有良好效果但其可调性差,电磁过滤可作为辅助方法去除夹杂物。
2003年我国钢产量已达到2.7亿t,但一些高品质钢材仍需进口,已经成为我国钢铁工业发展的障碍,同时也影响到我国钢铁产品走向世界,因此提高钢质量、增强国内钢铁企业的竞争力十分重要"提高钢的质量重点是提高钢的洁净度、对钢中夹杂物进行严格控制。
中间包是炼钢流程中的最后一个冶金反应器,对钢坯的质量起着至关重要的作用,文中对近年来发展起来的中间包冶金新工艺新技术及其作用进行了总结概括。
1 中间包防止钢水二次氧化1.1 无氧化烘烤与电磁感应加热为降低中间包耐火材料损耗,改进钢质量,国外有些钢厂已采用热中间包交换技术。
采用陶瓷蓄热体换热器,向中间包喷入加热至1500e的氮气流,即使经过很长时间,中间包温度仍保持高温。
结果表明:与使用密封气体等待较长时间的情况相比,降低了总氧量,提高了钢水的清洁度,同时中间包加热有利于防止浸入水口堵塞。
1.2 保护浇注二次氧化是污染钢液的重要原因。
钢液经过精炼后更要注意中间包内钢水的二次氧化,这是因为,(1)钢液经过精炼后,其[O]、[N]含量比和空气中的O2、N2的平衡值低得多,这个差值越大,二次氧化反应的驱动力越大。
反应速率一般都较快。
(2)钢中的[O]、[S]等都是强表面活性元素,表面活性元素吸附在钢液表面上,占据了较多的活性位置、二次氧化的另一个重要氧源是渣中的易还原氧化物FeO和MnO。
钢液二次氧化与卷渣形成夹杂原因与防止措施如表1所示。
表1 钢液二次氧化与卷渣形成夹杂原因与防止措施夹杂来源夹杂形成原因防止措施卷渣①钢包出水口漩涡卷渣a.下渣检测b.防止钢包汇流漩涡②注流冲击中间包,造成钢渣界面的剪切力和表面波动;注流引起的液—液湍射流a.中间包流场控制如使用湍流抑制器b.中间包大型化c.长水口或套管保护浇注防止中间包汇流漩涡③中间包水口卷渣二次氧化①钢包到中间包注流二次氧化钢包注流保护浇注②中间包到结晶器注流二次氧化中间包注流保护浇注③中间包裸露钢液面二次氧化中间包覆盖剂(上层为炭化稻壳下层为液体如铝酸钙渣系④钢包注流吸气中间包流场控制如使用湍流抑制器⑤中间包水口吸气防止中包汇流漩涡2 中间包内夹杂物去除与控制2.1 中间包结构对夹杂物去除与控制中间包的控流元件(如上下挡墙、湍流抑制器等)的设置对包内非金属夹杂物的上浮及均匀钢水温度、成分起着至关重要的作用。
20钢内部夹杂物来源及控制

$ 减少夹杂物的措施
)#$ 采用全程保护浇注,减少二次氧化。钢包挂接长水口,减少钢流对中间包钢液面的冲击作用。增加钢 包自动开浇成功率,减少钢包注流的裸露时间。如果“烧眼”引流,要求安装长水口时快捷。中减少了二次氧化的几率,铸坯内部夹杂物 明显降低。 )#! 增加中间包液面深度,保证稳定的拉速和生产节奏,上钢要及时,提高钢包自动开浇率。在多炉连浇过 程中,当中间包内渣层较厚时,实施放渣操作,将多炉连浇积累下的渣子从溢流槽放出,避免渣子被卷入结晶
!!0
器内,不能及时上浮产生夹杂。 !"! 选用与高效连铸及钢种相适应的保护渣
根据生产#$钢及小方坯高速连铸技术上的特点,选用的保护渣应具有低黏度、低熔点、高熔化速度和良 好的吸附夹杂物的性能,拉速变化较大时能保持有足够的消耗量,具有适当的熔渣层厚度,防止拉速高时熔 渣供应不足,保证熔渣厚度不变,使坯壳的润滑得到保证,连铸顺利拉坯并获得优良的连铸坯。 !"% 采用优质的耐火材料
熔融石英侵入式水口使用过程中融蚀速度较快,融蚀形成渣地剥落,有些渣滴留在钢中形成外来夹杂。 !#) 中间包熔池深度不够
高效连铸以后,由于拉速增加,每包钢水的浇注时间缩短,炉机生产节奏不一至,钢水经常来晚。同时钢 包自动开浇率较低烧眼时间长,造成换钢包浇注时,钢液面处于或低于临界值,并产生涡流将渣子卷入结晶 器,形成夹杂物残留于钢中。 !#% 保护渣性能
连铸过程中夹杂物来源分内生夹杂物(脱氧产物)和外来夹杂(保护渣卷入,耐火材料熔损卷入等)。 !#$ 二次氧化产物
底吹转炉钢中夹杂物的形成与控制技术
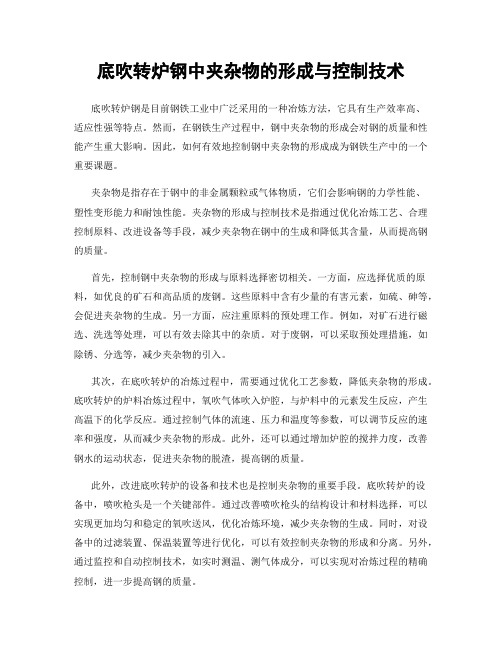
底吹转炉钢中夹杂物的形成与控制技术底吹转炉钢是目前钢铁工业中广泛采用的一种冶炼方法,它具有生产效率高、适应性强等特点。
然而,在钢铁生产过程中,钢中夹杂物的形成会对钢的质量和性能产生重大影响。
因此,如何有效地控制钢中夹杂物的形成成为钢铁生产中的一个重要课题。
夹杂物是指存在于钢中的非金属颗粒或气体物质,它们会影响钢的力学性能、塑性变形能力和耐蚀性能。
夹杂物的形成与控制技术是指通过优化冶炼工艺、合理控制原料、改进设备等手段,减少夹杂物在钢中的生成和降低其含量,从而提高钢的质量。
首先,控制钢中夹杂物的形成与原料选择密切相关。
一方面,应选择优质的原料,如优良的矿石和高品质的废钢。
这些原料中含有少量的有害元素,如硫、砷等,会促进夹杂物的生成。
另一方面,应注重原料的预处理工作。
例如,对矿石进行磁选、洗选等处理,可以有效去除其中的杂质。
对于废钢,可以采取预处理措施,如除锈、分选等,减少夹杂物的引入。
其次,在底吹转炉的冶炼过程中,需要通过优化工艺参数,降低夹杂物的形成。
底吹转炉的炉料冶炼过程中,氧吹气体吹入炉腔,与炉料中的元素发生反应,产生高温下的化学反应。
通过控制气体的流速、压力和温度等参数,可以调节反应的速率和强度,从而减少夹杂物的形成。
此外,还可以通过增加炉腔的搅拌力度,改善钢水的运动状态,促进夹杂物的脱渣,提高钢的质量。
此外,改进底吹转炉的设备和技术也是控制夹杂物的重要手段。
底吹转炉的设备中,喷吹枪头是一个关键部件。
通过改善喷吹枪头的结构设计和材料选择,可以实现更加均匀和稳定的氧吹送风,优化冶炼环境,减少夹杂物的生成。
同时,对设备中的过滤装置、保温装置等进行优化,可以有效控制夹杂物的形成和分离。
另外,通过监控和自动控制技术,如实时测温、测气体成分,可以实现对冶炼过程的精确控制,进一步提高钢的质量。
除了上述原料选择、工艺参数和设备技术的控制外,钢铁生产企业还可以通过改善管理和质量控制体系,进一步控制钢中夹杂物的形成。
科技成果——管线钢中非金属夹杂物控制关键技术

科技成果——管线钢中非金属夹杂物控制关键技术技术开发单位北京科技大学技术领域钢铁冶金成果简介石油和天然气是重要的能源矿产和战略资源,与国民经济、社会发展和国家安全息息相关。
在石油天然气的运输过程中,管道输送具有经济性、安全性和连续性等优点。
管线钢主要用于加工制造油气管线,性能上要求高强度、高韧性、良好的焊接性能和良好的抗腐蚀性能。
而非金属夹杂物是影响管线钢性能的主要因素之一,主要危害有:(1)会造成水口结瘤,影响生产顺行;(2)能够导致管线钢产生疲劳裂纹;(3)会影响管线钢的冲击韧性;(4)会降低管线钢的抗腐蚀性能,尤其是A类和B类夹杂物,会造成氢致裂纹的产生;(5)会恶化管线钢的焊接性能。
因此开发了管线钢中非金属夹杂物控制关键技术,为我国管线钢产品质量的提升做出了贡献,具体包括:(1)管线钢精准钙处理模型以及在线指导软件。
钙处理是管线钢夹杂物的最主要方式,通过钙处理能够将MnS夹杂物改性为CaS,将Al2O3为主的夹杂物改性为钙铝酸盐,从而降低夹杂物对管线钢性能的危害。
然而在大部分企业生产过程中,钙处理过程的钙线喂入量都缺乏一个标准,主要是依靠经验进行操作。
由于各炉次的钢渣成分和温度等的差异,导致不同炉次间的钙处理效果波动很大,有些炉次钙处理后产品性能还发生恶化。
本项目建立了管线钢精准钙处理模型,通过对管线钢不同钢液成分和温度条件下钙处理窗口进行的计算,确定了管线钢的不同成分条件下最优的喂钙线量。
与国外同类型模型相比,考虑的工艺条件更完全,考虑的反应物和产物也更全面,因此也更接近生产实际,准确率更高。
同时,以管线钢精准钙处理模型为基础开发出了钙处理在线指导软件,可实现管线钢生产过程中针对每一炉次的工况条件进行精准喂钙量的在线指导,并已实现了在管线钢生产中的在线应用,计算结果更直观。
T .S . (p p m )T.O. (ppm)T .S . (p p m )T.O. (ppm)Alt=0.03%管线钢钙处理液态窗口的全钙含量的最小值和最大值(2)低钙含量处理控制管线钢B 类夹杂物技术。
第6讲:中高碳钢夹杂物控制

其形貌如下图所示。
(2)夹杂物的能谱特征
对外来夹杂物进行能谱分析发现,不同来源的夹杂 物具有不同的能谱特征,主要差别是保护渣卷入时,有 明显的Na峰,而炉渣和耐火材料无此峰;耐火材料带入 的夹杂物Al峰较高,这是区别与其它夹杂物的特征元素; 炉渣卷入时,保留了原始炉渣Ca峰较高的特征,但也有 明显的Al峰。外来夹杂物的能谱特征对区分钢中大型夹杂 物的来源有帮助,可以有针对性地来采取措施,进一步 降低外来夹杂物。
1 钢中夹杂物的分类及特点
夹杂物来源及分类
1.1 夹杂物的分类
钢中的夹杂物按照来源可以分为内生夹杂物和 外来夹杂物。
内生夹杂物包括在脱氧、二次氧化或钢液冷却 和凝固过程中生产的氧化物,外来夹杂物包括炉渣 卷入或耐火材料侵蚀卷入钢液。
夹杂物的来源和分类如上图所示:
1.2 内生夹杂物
内生夹杂物是脱氧产物或者是钢水冷却凝固过程中的 析出物,包括脱氧产物以及在钢水冷却和凝固过程中产生 的沉淀析出夹杂物。
连铸板坯中大型夹杂物的尺寸分布
4 夹杂物对中、高碳钢性能的影响
钢中非金属夹杂物的存在是影响钢制品性能的重要因素,有 时甚至是决定性因素。非金属夹杂物对钢性能的影响程度与夹杂 物本身的性质,更确切地说与其相对于周围金属基体性质的差异 有密切关系。这里所说的性质差异主要包括:
1)各种温度下弹性模量的差值, 2)各种温度下形变能力的差值。 其原因在于当钢基体热加工时,由于夹杂物与基体的热物性 和界面特性不同,必然影响到夹杂物与基体间的连接情况,从而 导致夹杂物周围应力集中。
钢中夹杂物得去除与控制
钢中夹杂物去除与控制刘金刚 刘浏(钢铁研究总院冶金工艺研究所,北京100081)摘要:通过对钢包—中间包—结晶器中不同环节中的去除夹杂物的不同手段进行综合分析,得到各环节中间包均应保护浇注和防止卷渣卷气,中间包应具有合理的结构(上下挡墙、湍流抑制器、旋涡抑制器)以得到合理的流场;利用钢包注流的剪切破碎作用在中间包中生成的小气泡、中间包气幕挡墙和电磁搅拌离心流动可以有效去除钢水中夹杂物;电磁制动技术日趋成熟但其能耗较大,因此可以发展低能耗的中间包真空浇注对结晶器液面波动进行抑制。
电磁搅拌和电磁连铸有利于改善铸坯的内部质量和防止振痕的产生。
关键词:中间包夹杂物去除控制Inclusions Removal and Control in the Steel MeltLiu Jingang Liu Liu(CISRI, Beijing 100081)Abstract: Through synthetic analysis of various methods to remove inclusions during ladle-tundish-mold processes, it was found that using protective casting, avoiding gas and slag wrapping are important measures for clean steel production. The structure of the tundish should be reasonable, (dam, weir; turbulence inhibitor; vertex inhibitor) in order to get a preferred flow pattern. It could also utilize the shear flow from ladle to tundish to form small gas bubbles, utilize gas bubble curtain and electromagnetic stirring caused centrifugal flow to remove inclusions from steel melt. Electromagnetic braking technology is gradually raped but it was very energy consumed, thus it could develop low energy consumption vacuum tundish casting technology to control the fluctuation of melt surface in mold. Electromagnetic stirring is good for improving inner quality of slab and preventing the oscillation marks formation.Keywords: tundish, inclusion, remove, control二○○三年我国钢产量已达到2.7亿吨,但由于质量问题一些高品质钢材仍需进口,这已经成为我国钢铁工业发展的障碍,影响我国钢铁产品走向世界。
超低碳深冲钢中夹杂物的控制
影 响 主要 表现 在 锻 造 或 冷变 形 、 火 、 接 等容 易 淬 焊 在 夹 杂 物 聚集 部 位 产 生 裂 纹 。带 状 组 织 是造 成 钢
钢的切削加工性 。钢若 出现 了带状组织 , 加工时其 表面光洁度就差 , 渗碳时易引起不均匀 , 热处理时 易变形且硬度不均匀。非金属夹杂物的存在严重
影 响板 材 的力 学性 能 。
剂 。利用 R H真空炉开发 了冷轧超低碳钢 , 冶炼过
收稿 日期 :0 0 1 — 9 2 1—22
中图分类号 :F 0 T 73 文献标识码 : B 文章编号 :04 4 2 (0 10 — 0 7 O 10 — 6 0 2 1 )4 0 0 一 2
1 前
言
达到0 0 %以下 ; .1 0 板坯铸机4 其 中A P 台( S 薄板铸机 2 ) 台 。对低 碳低 硅钢 的冶炼采 用 K R铁水脱 硫处 理
非 金 属 夹 杂 物对 钢 的影 响主 要 表 现 在钢 的使
用 性 能 和 工 艺性 能 两 方 面 。使 用 性 能 的影 响 主要 表 现 在疲 劳性 能 、 冲击 韧性 和 塑性 等 ; 艺性 能 的 工
止 钢 水 过 氧 化 。 降 低 钢 中含 氧 量 (O] 0 [ <30×
铁 水 扒渣 要 干净 , 炉 铁水 S . 50 铁 水 比≥ 人 ≤0 0 %, 0
真空炉 控制 , 高钢水 的 洁净 度 , 提 改善其浇 注性能 。
8 %, 0 使用优质低硫废钢。
2 转 炉 冶炼 控 制 。终点 碳控 制 在一 定 范 围 , ) 防
科技成果——轴承钢中非金属夹杂物控制关键技术
科技成果——轴承钢中非金属夹杂物控制关键技术技术开发单位北京科技大学技术领域钢铁冶金成果简介随着我国国民经济的不断发展,对轴承钢性能提出了更高的要求。
超纯净轴承钢被广泛地应用于高速铁路、风电装备、航空发动机、高档轿车变速箱、高速精密机床和长寿命冶金轧机等对使用寿命、可靠性、承载能力严格要求的领域。
超纯净轴承钢炼钢冶炼难度极高,主要是由于其钢中非金属夹杂物控制存在以下两个难题:(1)超高洁净度,总氧含量低于5ppm;(2)大颗粒夹杂物数量要求少,尺寸小于15μm。
近30年来,通过引进、消化和吸收,实现了大部分高端装备的国产化,但对高端装备用高可靠长寿命轴承的国产化一直没有解决。
因此,开发超纯净轴承钢中非金属夹杂物控制关键技术,为打破此领域国外产品及技术垄断、实现国内自主生产有重要意义。
(1)超纯净轴承钢精炼渣成分设计技术。
铝脱氧轴承钢都是通过高碱度精炼渣提升钢材的洁净度,减少钢中夹杂物数量。
高碱度精炼渣具有很高的脱氧脱硫能力,效率高,可生产超低硫轴承钢。
由于高碱度精炼渣中CaO含量高,易被钢中[Al]还原而进入钢液,从而生成Ds类夹杂,对轴承钢性能产生不利影响。
另外,高碱度使精炼渣熔点变高,成渣慢,炉渣流动性变差,会影响脱氧脱硫效果,有可能引起卷渣。
低碱度精炼渣由于碱度低,降低了CaO-Al2O3类夹杂的影响,但脱氧能力下降使得氧化物夹杂上升。
本项目研究应用Fact Sage 热力学计算软件,研究了不同精炼渣成分对钢液成分、夹杂物成分的影响,通过对不同精炼渣系进行设计优化,确定精炼渣成分;同时,本项目在碱度7-12范围内进行工业试验,考虑了不同碱度精炼渣对轴承钢洁净度和夹杂物成分的影响,从而更系统准确地确定了有利于超纯净轴承钢夹杂物控制的最优精炼渣成分。
图1 精炼渣碱度对渣中Al2O3和CaO活度的影响(2)超纯净轴承钢VD精炼控制技术。
在真空状态下吹氩搅拌钢液,促使夹杂物从钢液内排除,使钢的洁净度提高。
钢中夹杂物控制,人机料法环
钢中夹杂物控制,人机料法环钢铁生产过程中,夹杂物的控制至关重要。
夹杂物不仅会影响钢材的力学性能和加工性能,还会导致钢材表面质量问题,甚至引发严重的安全事故。
因此,钢铁企业需要从人、机、料、法、环等多个方面入手,全方位加强夹杂物控制。
人是夹杂物控制的核心。
操作工人的技能水平和责任心直接关系到钢液品质。
企业应加强员工培训,提高其业务能力和质量意识。
同时建立严格的考核制度,将夹杂物控制指标纳入绩效评价,调动员工的积极性。
在生产设备方面,定期维护和更新设备是减少夹杂物的有效途径。
先进的精炼设备如RH真空脱气、LF精炼等,可显著提高钢液纯净度。
气力输送系统可避免转运污染。
此外,在关键工序配备在线夹杂物检测仪,实现夹杂物水平的实时监控。
原料把控是预防夹杂物的第一道关口。
优质原燃料虽成本较高,但可从源头减少杂质带入。
来料检验须严把质量关,对不合格品坚决清退。
原料配比要科学,最大限度利用高品质料。
操作规程和工艺参数的优化,可从工艺层面控制夹杂物。
细化生产流程,编制可操作性强的作业指导书。
工艺参数应适时优化,如调整脱氧剂用量、控制精炼温度等。
建立夹杂物控制台账,为工艺改进提供数据支持。
营造良好的生产环境,也有助于夹杂物控制。
厂区应保持整洁有序,防止灰尘污染。
定期清理除尘设施,确保其正常运行。
原料须分类存放,防止交叉污染。
转运通道要专人维护,避免夹杂物的二次污染。
钢中夹杂物控制是一项系统工程,贯穿钢铁生产的全流程。
在人员素质、设备性能、原料品质、操作规程、环境管理等方面形成合力,才能真正实现夹杂物的最小化。
这需要企业上下统一思想,部门通力合作。
只有长期坚持,持续改进,才能不断提升钢材品质,增强市场竞争力。
当前,钢铁行业竞争日趋激烈,用户对钢材品质提出更高要求。
一些高端领域如核电、航空等,对钢中夹杂物提出了极为严苛的指标。
这对钢铁企业的夹杂物控制能力提出了新的挑战。
未来,机器学习、大数据等先进技术在夹杂物控制中的应用前景广阔。
- 1、下载文档前请自行甄别文档内容的完整性,平台不提供额外的编辑、内容补充、找答案等附加服务。
- 2、"仅部分预览"的文档,不可在线预览部分如存在完整性等问题,可反馈申请退款(可完整预览的文档不适用该条件!)。
- 3、如文档侵犯您的权益,请联系客服反馈,我们会尽快为您处理(人工客服工作时间:9:00-18:30)。
夹杂物控制方案
夹杂物控制是高品质钢生产的关键环节,也是控制生产成本的重要环节。
非金属夹杂物降低了钢的塑形、韧性和疲劳寿命,使钢的冷热加工性能乃至某些物理性能变坏。
中厚板生产,采用铝脱氧工艺,容易出现B类夹杂超标,连铸过程往往在铸坯1/4处夹杂物富集,存在大量的大颗粒氧化物脆性夹杂,造成板材B类夹杂物超标。
除此之外,A类硫化物夹杂主要是在钢水凝固过程,随着温度的降低,1415℃时开始大量析出,1000℃左右全部析出,针对凝固过程控制冷却强度等控制A类夹杂物。
接下来要开展的工作方案如下:
一、B类夹杂物控制改善
1)转炉终点氧含量。
夹杂物的多少与钢水中氧含量有直接的关系,控制终点氧含量,通过副枪测定[%C]和[%O],保证波动在C-O平衡曲线附近。
通过炼几炉235B钢种,统计一下转炉终点[%O].
[%C]=0.16 T=1600℃ Pco=100KPa,得出理论[%O]=160ppm。
2)脱氧剂的选择。
ASM复合脱氧剂的脱氧能力大于单一Al脱氧剂,不同脱氧剂形成脱氧产物不同,脱氧剂的消耗量也不同。
选择不同的脱氧剂,加入量如何确定?
3)严禁转炉出钢下渣,通过检测包渣(FeO+MgO)。
4)出钢脱氧后吹氩去除脱氧产物。
不同脱氧剂形成的脱氧产物不同,大部分为低熔点液态大颗粒产物,氩气流量的控制加速夹杂物的上浮去除。
5)精炼工艺。
根据进站[%O],目标[%O]决定喂多少铝线,在此基础上进行Ca处理,喂多少Ca线必须通过理论计算,生成C12A7。
根据钙处理后变性产物,决定精炼渣系成分的选择,包括碱度、MI指数、w[%FeO+MgO]、w[Al2O3]。
出站前,软吹气量控制,是根据流量计还是根据渣眼裸露直径?
6)防止二次氧化。
全程保护浇注,长水口及浸入式水口氩封。
二、A类夹杂物控制改善
硫化物夹杂主要是在钢的凝固过程析出,控制工艺从两方面下手:1、LF深脱硫,使得钢中[%S]降低;2、改善冷却条件,调整冷却速率,二冷配水如何使得MnS选分析出。
而硫化物主要想控制生成I类硫化物,纺锤状,轧制不易变形。
措施:氧含量控制,w[%O]大于120ppm。
[Mn]/[S]比控制,[%S]40-100ppm,锰硫比控制20。
钙含量,控制钢中[%Ca]/[%S]大于0.2。
除此之外,冷却速率的增加,MnS 析出颗粒较细,数量增多,增加析出温度区域冷却强度(100℃/min)。
改善中心偏析。
轧制工艺,MnS的塑性变形温度在1000-1050℃较低,控制轧制温度在这个范围。
以上为综合考虑影响夹杂物超标的每个工艺点,具体改变哪个参数,如何选取合适的参数,需要下一步针对性研究,以上只是思路过程。
在调整一个工艺参数后,如何取样分析等都需要下一步严格制定。
比如转炉高拉碳控制氧含量多少ppm合适,需要摸清现在一次拉碳时氧含量,根据碳含量,确定终点碳氧积在不在平衡曲线附近等等。