富氧固定床连续汽化技术
固定床气化工艺简介:2、固定床气化的过程原理.
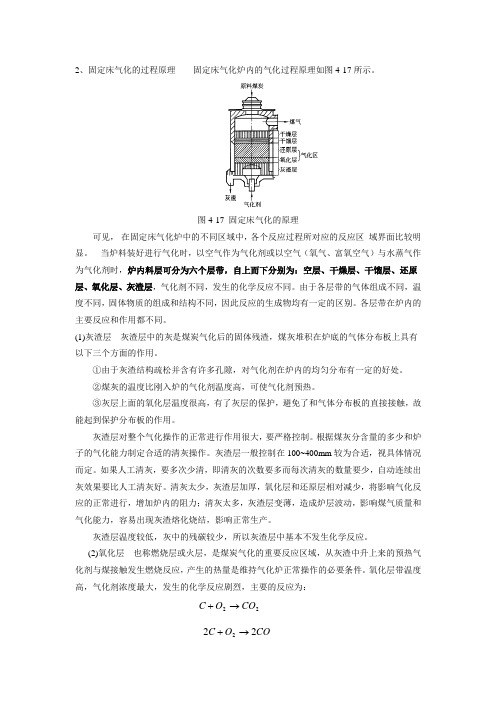
2、固定床气化的过程原理 固定床气化炉内的气化过程原理如图4-17所示。
图4-17 固定床气化的原理可见, 在固定床气化炉中的不同区域中,各个反应过程所对应的反应区 域界面比较明显。
当炉料装好进行气化时,以空气作为气化剂或以空气(氧气、富氧空气)与水蒸气作为气化剂时,炉内料层可分为六个层带,自上而下分别为:空层、干燥层、干馏层、还原层、氧化层、灰渣层,气化剂不同,发生的化学反应不同。
由于各层带的气体组成不同,温度不同,固体物质的组成和结构不同,因此反应的生成物均有一定的区别。
各层带在炉内的主要反应和作用都不同。
(1)灰渣层 灰渣层中的灰是煤炭气化后的固体残渣,煤灰堆积在炉底的气体分布板上具有以下三个方面的作用。
①由于灰渣结构疏松并含有许多孔隙,对气化剂在炉内的均匀分布有一定的好处。
②煤灰的温度比刚入炉的气化剂温度高,可使气化剂预热。
③灰层上面的氧化层温度很高,有了灰层的保护,避免了和气体分布板的直接接触,故能起到保护分布板的作用。
灰渣层对整个气化操作的正常进行作用很大,要严格控制。
根据煤灰分含量的多少和炉子的气化能力制定合适的清灰操作。
灰渣层一般控制在100~400mm 较为合适,视具体情况而定。
如果人工清灰,要多次少清,即清灰的次数要多而每次清灰的数量要少,自动连续出灰效果要比人工清灰好。
清灰太少,灰渣层加厚,氧化层和还原层相对减少,将影响气化反应的正常进行,增加炉内的阻力;清灰太多,灰渣层变薄,造成炉层波动,影响煤气质量和气化能力,容易出现灰渣熔化烧结,影响正常生产。
灰渣层温度较低,灰中的残碳较少,所以灰渣层中基本不发生化学反应。
(2)氧化层 也称燃烧层或火层,是煤炭气化的重要反应区域,从灰渣中升上来的预热气化剂与煤接触发生燃烧反应,产生的热量是维持气化炉正常操作的必要条件。
氧化层带温度高,气化剂浓度最大,发生的化学反应剧烈,主要的反应为:22CO O C →+CO O C 222→+2222CO O CO →+上面三个反应都是放热反应,因而氧化层的温度是最高的。
富氧连续化工艺的利与弊

1前言煤的气化技术,是指将煤炭洁净、高效地“变”成—种合成气体。
该技术是煤炭加工成化工产品、煤变油等工业的基础性技术,也是以煤炭为原料的诸多行业的关键技术。
煤气化工艺过程的发展已有百余年的历史,迄今为止已开发的气化方法不下数百种,按照煤在气化炉的运行和接触方式,主要可以分为(1)移动床气化(固定床)、(2)流化床气化、(3)气流床气化。
其中移动床气化主要包括鲁奇气化技术、固定床间歇气化技术、富氧连续气化技术等。
流化床气化技术主要包括恩德气化技术、灰熔聚气化技术等。
气流床气化技术主要包括GE水煤浆加压气化技术、壳牌(SHELL)干粉煤加压气化技术、GSP干粉煤加压气化技术、对置式多喷嘴水煤浆加压气化技术等。
由于投资和煤种的原因,目前在我国中小氮肥行业应用最广的气化技术是固定床间歇气化技术。
该技术虽不先进,但较实用,而且投资低、建设周期短、操作简单易管理。
经过小氮肥企业几十年的革新改造,现在的固定床间歇煤气化技术已不是传统意义上的固定床气化技术,如气化炉的改进、原料煤的消耗降低及吹风气回收利用等技术革新,因此这么多年来一直受中小氮肥企业青睐。
但是,由于国家发改委已经将固定床间歇气化技术列为了限制发展的落后技术,因此各地区的行政主管部门和环境保护部门均开始限制采用固定床间歇气化技术工程项目的审批。
目前,很多中小型氮肥企业开始关注富氧连续气化技术,并且有很多工程项目拟采用该技术,特别是以白煤为原料的氮肥生产企业。
2富氧连续气化工艺简介富氧连续气化是在间歇气化工艺基础上发展起来的一种常压连续气化工艺,其流程和设备与固定床间歇气化基本相同。
2.1工艺流程简述从空分装置来的氧气与造气风机来的空气混合配制成体积分数为50%~60%的富氧空气,进入空气蒸汽混合器;低压蒸汽经流量调节控制合适的汽/气比后也进入空气蒸汽混合器,与富氧空气充分混合,然后进入造气炉底部,连续上吹制取水煤气,制得的水煤气从造气炉上部出来,首先经过除尘器除去气体中的粉尘,然后进入废热锅炉回收显热,经洗气塔洗涤除尘降温后去后续工段。
富氧气化简介090612

富氧气化技术简介江西昌昱实业富氧连续气化技术一、概述富氧连续气化技术是一项综合了粉煤成型技术、固定床煤气炉技术和空气分离制氧技术为一体的系统工程技术。
它把粉煤成型用于气化,使煤气化工业企业避开了以优质块煤焦为原料的独木桥,走上了以本地粉煤为气化原料,成本低、资源丰富的广阔大道。
同时,也避开了采用国外粉煤气化技术,投资大、消化期长、见效慢的曲折道路。
走上了投资少、见效快、节能减排效果好的发展道路。
更重要的是,型煤富氧连续气化技术,它是一项可以在众多煤气化企业现有装置的基础上,进行设备改造,技术提升,即可实现的技术。
它是由多项已经用于生产实践的成熟技术的组合,是一种零风险的技术。
我国富氧连续气化(固定床煤气炉)始于60年代末,是在固定床间歇气化炉的基础上发展的。
主要用于UGI型煤气炉。
发展四十余年,炉型没有大的技术进步,仍然是UGI煤气炉的基本设计,流程没有大的变化,自控技术发展到今天,老的工艺也没有明显的变化。
主要原因:历史上这种富氧气化生产成本偏高,与其它气化技术相比,没有生命力,因此一直没有得到明显的发展。
它的主要缺点是:1、装置不合理,热损失大,有效气体成份达不到要求;2、煤价较低,而制氧成本偏高,用价格偏高的氧来节约用煤,生产成本不合算;3、富氧气化CO2偏高,脱C系统成本升高。
而随着科学技术进步,现在出现了一系列变化:1、装置技术含量大幅度提高,煤气炉、炉箅、自控水平、余热回收技术、自动下灰技术、变压吸附脱C技术等;2、制氧成本大幅度下降,由0.6元/m3下降到0.25元/m3;3、煤价翻了两番,中块煤由原来的200元/T 升至800元/T,粉煤由100元/T升至450元/T;4、型煤制造技术飞速发展。
新的历史条件和历史使命注定了型煤富氧气化技术将重新焕发出勃勃生机,为我国煤化工事业的发展增加活力。
二、型煤富氧连续气化技术的组成1、型煤技术富氧连续气化要求型煤要具备如下特性:热稳定性≥80%,热强度≥50kg/cm2,固定C≥60%,化学活性较好。
简析富氧连续气化工艺1

富氧连续气化工艺的利与弊1 前言煤的气化技术,是指将煤炭洁净、高效地“变”成—种合成气体。
该技术是煤炭加工成化工产品、煤变油等工业的基础性技术,也是以煤炭为原料的诸多行业的关键技术。
煤气化工艺过程的发展已有百余年的历史,迄今为止已开发的气化方法不下数百种,按照煤在气化炉的运行和接触方式,主要可以分为(1)移动床气化(固定床)、(2)流化床气化、(3)气流床气化。
其中移动床气化主要包括鲁奇气化技术、固定床间歇气化技术、富氧连续气化技术等。
流化床气化技术主要包括恩德气化技术、灰熔聚气化技术等。
气流床气化技术主要包括GE 水煤浆加压气化技术、壳牌(SHELL)干粉煤加压气化技术、GSP干粉煤加压气化技术、对置式多喷嘴水煤浆加压气化技术等。
由于投资和煤种的原因,目前在我国中小氮肥行业应用最广的气化技术是固定床间歇气化技术。
该技术虽不先进,但较实用,而且投资低、建设周期短、操作简单易管理。
经过小氮肥企业几十年的革新改造,现在的固定床间歇煤气化技术已不是传统意义上的固定床气化技术,如气化炉的改进、原料煤的消耗降低及吹风气回收利用等技术革新,因此这么多年来一直受中小氮肥企业青睐。
但是,由于国家发改委已经将固定床间歇气化技术列为了限制发展的落后技术,因此各地区的行政主管部门和环境保护部门均开始限制采用固定床间歇气化技术工程项目的审批。
目前,很多中小型氮肥企业开始关注富氧连续气化技术,并且有很多工程项目拟采用该技术,特别是以白煤为原料的氮肥生产企业。
2 富氧连续气化工艺简介富氧连续气化是在间歇气化工艺基础上发展起来的一种常压连续气化工艺,其流程和设备与固定床间歇气化基本相同。
2.1工艺流程简述从空分装置来的氧气与造气风机来的空气混合配制成体积分数为50%~60%的富氧空气,进入空气蒸汽混合器;低压蒸汽经流量调节控制合适的汽/气比后也进入空气蒸汽混合器,与富氧空气充分混合,然后进入造气炉底部,连续上吹制取水煤气,制得的水煤气从造气炉上部出来,首先经过除尘器除去气体中的粉尘,然后进入废热锅炉回收显热,经洗气塔洗涤除尘降温后去后续工段。
固定床连续气化法富氧制气概述
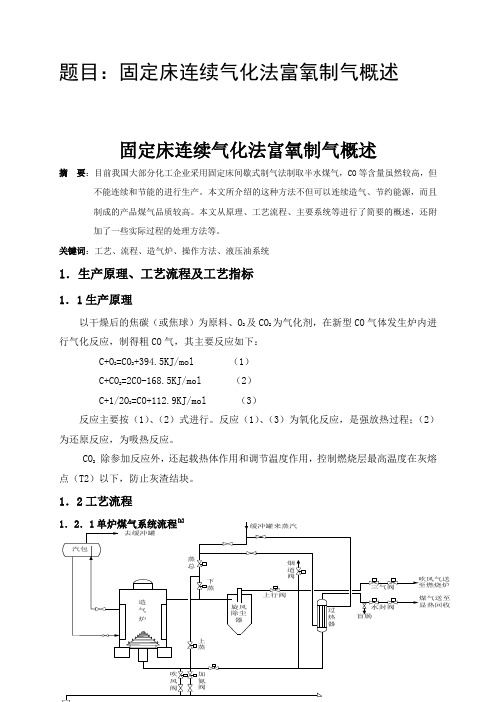
题目:固定床连续气化法富氧制气概述固定床连续气化法富氧制气概述摘要:目前我国大部分化工企业采用固定床间歇式制气法制取半水煤气,CO等含量虽然较高,但不能连续和节能的进行生产。
本文所介绍的这种方法不但可以连续造气、节约能源,而且制成的产品煤气品质较高。
本文从原理、工艺流程、主要系统等进行了简要的概述,还附加了一些实际过程的处理方法等。
关键词:工艺、流程、造气炉、操作方法、液压油系统1.生产原理、工艺流程及工艺指标1.1生产原理以干燥后的焦碳(或焦球)为原料、O2及CO2为气化剂,在新型CO气体发生炉内进行气化反应,制得粗CO气,其主要反应如下:C+O2=CO2+394.5KJ/mol (1)C+CO2=2CO-168.5KJ/mol (2)C+1/2O2=CO+112.9KJ/mol (3)反应主要按(1)、(2)式进行。
反应(1)、(3)为氧化反应,是强放热过程;(2)为还原反应,为吸热反应。
CO2除参加反应外,还起载热体作用和调节温度作用,控制燃烧层最高温度在灰熔点(T2)以下,防止灰渣结块。
1.2工艺流程1.2.2该流程示意图如下[2]:1—CO2罗茨机 2—混合器 3—预热器 4—造气炉5—废热锅炉 6—洗气塔 7—气柜 8—脱硫1.2.3生产流程简述(内蒙古宜化生产工艺)将粒度为25~60mm的合格焦碳加入到自动加焦机,自动加焦机定量将焦炭加入气化炉内,从界区外来的合格的O2和CO2严格按一定比例(1.8~2.1)混合后,从气化炉底部进入,与焦炭进行氧化和还原反应,气化炉产生的粗炉气经过旋风除尘器除去大部分灰尘,并经废热锅炉回收热量后,再进入联合洗气塔,将煤气温度降到45℃以下,同时除去煤气中的大部分粉尘后送至后工段。
1.2.4工艺特点:(1)在常压下连续加料,连续排灰,连续气化,干法排灰气化工艺。
(2)工艺流程简单,为防止CO泄漏,设计上采用严格防泄漏措施。
(3)气化炉生产强度大,易于检修,特殊的炉篦结构,具有均匀布气,破渣、排渣三个功能,并可根据原料特性调整各层布气。
固定床连续气化法富氧制气概述
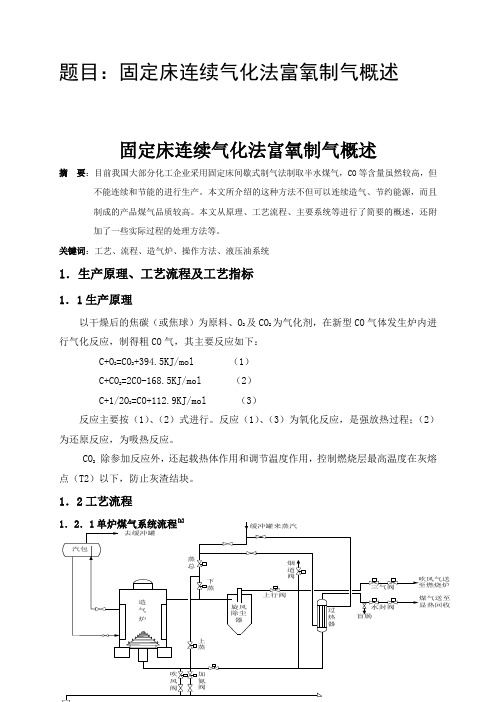
题目:固定床连续气化法富氧制气概述固定床连续气化法富氧制气概述摘要:目前我国大部分化工企业采用固定床间歇式制气法制取半水煤气,CO等含量虽然较高,但不能连续和节能的进行生产。
本文所介绍的这种方法不但可以连续造气、节约能源,而且制成的产品煤气品质较高。
本文从原理、工艺流程、主要系统等进行了简要的概述,还附加了一些实际过程的处理方法等。
关键词:工艺、流程、造气炉、操作方法、液压油系统1.生产原理、工艺流程及工艺指标1.1生产原理以干燥后的焦碳(或焦球)为原料、O2及CO2为气化剂,在新型CO气体发生炉内进行气化反应,制得粗CO气,其主要反应如下:C+O2=CO2+394.5KJ/mol (1)C+CO2=2CO-168.5KJ/mol (2)C+1/2O2=CO+112.9KJ/mol (3)反应主要按(1)、(2)式进行。
反应(1)、(3)为氧化反应,是强放热过程;(2)为还原反应,为吸热反应。
CO2除参加反应外,还起载热体作用和调节温度作用,控制燃烧层最高温度在灰熔点(T2)以下,防止灰渣结块。
1.2工艺流程1.2.2该流程示意图如下[2]:1—CO2罗茨机 2—混合器 3—预热器 4—造气炉5—废热锅炉 6—洗气塔 7—气柜 8—脱硫1.2.3生产流程简述(内蒙古宜化生产工艺)将粒度为25~60mm的合格焦碳加入到自动加焦机,自动加焦机定量将焦炭加入气化炉内,从界区外来的合格的O2和CO2严格按一定比例(1.8~2.1)混合后,从气化炉底部进入,与焦炭进行氧化和还原反应,气化炉产生的粗炉气经过旋风除尘器除去大部分灰尘,并经废热锅炉回收热量后,再进入联合洗气塔,将煤气温度降到45℃以下,同时除去煤气中的大部分粉尘后送至后工段。
1.2.4工艺特点:(1)在常压下连续加料,连续排灰,连续气化,干法排灰气化工艺。
(2)工艺流程简单,为防止CO泄漏,设计上采用严格防泄漏措施。
(3)气化炉生产强度大,易于检修,特殊的炉篦结构,具有均匀布气,破渣、排渣三个功能,并可根据原料特性调整各层布气。
型煤富氧连续气化生产技术及能耗分析_王富铭

62型煤富氧连续气化生产技术及能耗分析王富铭(福建三钢(集团)三明化工有限责任公司技术中心,福建三明 365001)摘 要:总结了粘结剂型煤生产技术,固定床型煤富氧连续气化生产技术。
对型煤连续富氧气化与间歇气化优缺点进行了对比,提出型煤连续富氧气化设备改造及设想。
并对粘结型型煤连续富氧气化能耗进行了分析,提出了节能措施。
关键词:型煤;富氧连续气化;能耗分析;节能引言我国70%以上合成氨生产厂家是以块煤为原料UGI间歇气化工艺,自2003年以来,随着世界能源出现紧张局面,我国煤炭供应困难,尤其是用于合成氨煤气化的优质山西晋城块煤供应严重不足,价格不断攀升,与粉煤价格差距日益加大,采用粉煤和地产煤制型煤并配套富氧连续气化生产半水煤气成为合成氨降低生产成本,提高企业产品竞争力的主要方法。
用地产粉煤制成的腐植酸粘结剂型煤特点:(1)型煤的冷强度低;(2)型煤热强度与成渣性不好;(3)型煤的热稳定性不好;(4)地产粉型煤的反应活性差。
通过吹风阶段强风短吹、延长下吹制气来提高固定层间歇制气热效率的方法,显然对气化用型煤很不适应,降低吹风强度的结果直接导致型煤气化炉生产能力大幅度降低。
另外,由于空气中N2含量高达79%,在保证合成氨对(CO+H2)/ N2要求3︰1前提下,制气过程难以达到自热平衡,间歇制气集中供热、分段吸热工艺特点,也局限了型煤间歇制气的消耗和生产强度。
连续富氧气化是以现有UGI间歇炉为基础,采用富氧空气(O2含量>50%)为气化剂,连续制取半水煤气或其他合成气、城市煤气的工艺技术。
目前变压吸附制氧技术以及深冷制氧技术的进步,降低了富氧、纯氧生产成本,加上煤价高企,大大推动了型煤连续富氧气化技术的发展,成为固定床煤气化今后的发展方向。
1 粘结剂型煤生产技术简介无机粘结剂型煤如碳化煤球因煤球的含碳量低,生产设备庞大,碳、蒸汽消耗高,环境污染严重等因素,而受到局限。
近年来,复合腐植酸粘结剂型煤由于可以提高煤球的孔隙率,通过添加各种组分提高反应活性、改善热稳定性和成渣性等优势,得以推广应用[1]。
★间歇法、富氧法、纯氧法气化技术的特点及优缺点比较

固定床间歇、富氧、纯氧气化技术的特点及优缺点比较田守国江西昌昱实业有限公司注1:根据贵公司的要求,对照分析三种固定床气化工艺的经济性、可行性。
注2:因贵公司生产工艺需求无氮水煤气,下面只重点介绍固定床煤气炉生产水煤气的工艺比较。
注3:工艺比较的条件;∮2800煤气炉(截面积6.2㎡)、质量比较好的无烟块煤。
一、普通间歇法、富氧法、纯氧法煤气的组分?H2、CO、CO2的组分比例?有效气比例?单台炉产气量?1.固定床间歇气化生产水煤气:煤气成份:CO2=7—9%、O2=0.4-0.5%、CO=38-39%、H2=43—46%、N2=4—6%、DH4=1-2%。
有效气体含量80%左右。
固定床煤气炉间歇气化生产水煤气,是最不经济的气化工艺。
单位面积的气化强度仅为650—750m3/㎡.h。
而且,吹风过程前后都要有排除氮气的过程,氮气是由煤气带出去的,排氮过程伴有大量煤气浪费。
间歇气化生产水煤气,煤气中氮气含量控制越低,煤耗越高、发气量越小,如果氮气含量控制小于4%单位面积的气化强度仅为650m3/㎡.h。
而且出气温度高,显热损失大,灰渣残炭量≥20%,吹风带出物达到了10%左右,型煤气化能达到15—20%。
因此,间歇气化生产水煤气原料转化利用率仅为65%左右,吨醇原料煤消耗2吨左右。
而且吹风过程有大量烟气排放,不但降低了煤气炉的热效率,更不符合国家洁净煤气化的产业政策。
2.固定床富氧连续气化生产半水煤气:半水煤气成份:CO2=16-19%、O2=0.2-0.5%、CO=28-32%、H2=36-39%、N2=10—14%、DH4=1-3%。
有效气体含量70%左右。
入炉富氧气中氧浓度50—58%单位面积的气化强度仅为1200—1300m3/㎡.h。
富氧连续气化只能生产半水煤气,不适应醇类产品生产。
3.纯氧+蒸汽生产水煤气成份:纯氧连续气化的水煤气成份因原煤质量、装备条件、控制条件而不同而有一定差距。
(太化)半焦(也称“兰炭”)气体成份:CO2=16.5-17%、02=0.2—0.4%、CO=38—39.8%、H2=44.4%、N2=0、CH4=≤1.0%。
- 1、下载文档前请自行甄别文档内容的完整性,平台不提供额外的编辑、内容补充、找答案等附加服务。
- 2、"仅部分预览"的文档,不可在线预览部分如存在完整性等问题,可反馈申请退款(可完整预览的文档不适用该条件!)。
- 3、如文档侵犯您的权益,请联系客服反馈,我们会尽快为您处理(人工客服工作时间:9:00-18:30)。
富氧固定床连续汽化技术
(2021-01-0715:25:09)前言;
我国以煤焦为原料生产合成氨、甲醇的中小型企业就有几百家,90%以上的企业都是
采用间歇式固定床气化技术,而这些企业的生产能耗均在50―60gj,近年来随着国内煤价的不断的上涨,使不少的企业处于严重亏损状态。
而造气煤气发生炉是中型合成氨、甲醇
企业的关键设备,其中造气煤耗要占总能耗的65%以上,从而使不少的企业在寻找一条相应投资少,又符合国情,以改造现有的造气工艺设备,来完成节能降耗和环保目的。
近十
年来,富氧固定床连续气化技术随着国内原料煤价格的不断飙升,在煤化工合成氨、甲醇
企业中得到快速发展,由于原料煤价格的原因,该技术和现在的固定床技术相比,该技术
既环保又节能,大约要节约1/3--1/4还要多的原料煤,这样就及大的显示出该技术的
优点,所以说发展很快,从而引起了不少企业领导的高度重视。
根据贵公司的情况,在现
有直径2650--2800mmugi型气化炉气化工艺作为基础,建议采用固定床富氧连续气化、制
氧采用变压吸附制氧技术,对原固定床工艺稍加改造,就能达到节能降耗和环保目的,该
技术相应投资较少,单炉发气量大、操作简单,可降低操作工的劳动强度、和节省劳动力,单炉发气量可提高2.5--3倍,将来六台炉子就可满足现有的15万吨合成氨和5万吨甲醇
气量的需求,在现有的16台造气炉的基础上将9台炉子可省掉,这样既可降低检修费用
又可节省劳动力、还可节省地盘。
节省下来的地方可以建富氧装置,所以说要达到节能降
耗和环保目的,上富氧固定床连续气化技术是最佳方案。
一;富氧连续气化技术经济分析
论正
我以2021―2021年吨氨耗煤情况,以20万吨合成氨算是每年大概消耗原料煤,当时
的价格,与以参照。
表中;(一)名称吨氨耗煤吨氨耗煤20万吨氨耗煤20万吨氨耗煤20万吨平均值煤耗吨1.6―1.71.6―1.733万吨33万吨焦煤吨单价900元、吨1000元、吨
按900元吨算是按1000元算是950元算是吨氨耗煤价1485元、吨1650元、吨29700万
元33000万元31350万元据近几年的介绍,搞出富氧固定窗固定床已连续气化技术的企业
多了,原因就是原料煤价格的攀升,加之富氧已连续气化和原来的紧固间歇气化较之可以
节约原料煤在1/3--1/4以上。
表;(二)按1/4计算采用富氧连续气化技术,每年的消耗情况。
名称顿氨耗煤顿
氨耗煤20万吨氨耗煤20万吨氨耗煤20万吨平均表一情况介绍。
一;大家都晓得,现在这种间歇气化工艺,在生产半水煤气工艺过程中,造气制气工
艺常分成五个阶段,Alappuzha、吹起净、上吹起、下吹起、吹起净,Alappuzha阶段主要的目的就是向气化炉Alappuzha去提升碳层温度,吹起风气从烟筒Grignols,这样既污染了环境又必须消耗大量的碳,备注;(当时我在2021年给贵公司建议,评估上了一套三
废废旧技术,从而化解了环保问题、和节能环保的问题。
当时也曾建议过上富氧已连续气
化技术,主要也就是考虑到吹起风气中的有效率碳问题,由于着急须要化解政府的环保管
制问题必须上三废废旧项目,再加之资金问题,富氧项目就一拖再拖下来了)。
跟据当时
的吹起风气、和半水煤气成份,排序出来每立方米烟气中要消耗0.12的有效率碳,而每
立方米半水煤气消耗0.22的碳,因为制气和Alappuzha就是交错展开,这样算下来其中原料煤中1/3多的有效率碳消耗至吹起风气中回去,就是说假如每吨合成氨乏原料煤在1.65―1.7吨时,如果使用富氧已连续气化技术,每吨合成氨按1/4节省算是0.4―0.45吨原料煤,按过去07―08年的焦炭900--1000元排序,每吨合成氨的生产成本就可以减少380--400元。
当然这必须乘以整个的制氧装置投资运转一切费用。
二;通过以上两表的参数、如果采用富氧固定床连续气化技术,每年在原料煤消耗方面就可节约8.5万吨原料煤,原料煤价格按950元算,在原料煤方面每年就可节约8075万元,当然这没有计算制氧装置的投资费用,银行贷款利息、设备折旧费、每吨合成氨氧气消耗成本。
下面在了解制氧装置建设、贷款利息、运转费用,及整个的消耗情况。
三;制氧装置设备投资及运转成本;表中;(三)名称制氧装置每年银行利息年设备折旧费氧气耗电量m3投资规模m38000--9000按6%15年算是0.3―0.35/度每立方米、元4000--4500240万元/年212万元电价0.5元/度总计4000万元240万元212万元0.20元煤耗吨
1.2251.22524.5万吨24.5万吨焦煤吨单价900元、吨1000元、吨按900元吨算是按1000元算是950万算是吨氨耗煤价110
2.5、吨1225元、吨22050万元24500万元22800万元四;每吨合成氨的消耗成本,表中;(四)名称银行利息设备折旧费吨氨耗氧/m3吨氨耗吸附剂/kg合计表中;三、四了解
按贵公司年产20万吨合成氨计算,需要建一个每小时8000―9000立方米的制氧空分装置,这一块的投资在4000万元左右,再按化工设备15年的折旧费算,每年的设备折旧费为266万元,银行利息按4000万元年息百分之6算,年利息为240万,看来这个数字有点大,算大一点比较好,这样240+266=506万元,按年产20万吨合成氨计算每吨合成氨的成本25.3元,每吨合成氨耗氧气按450立方米算,生产每立方米氧气要耗电
0.35―0.4度,电价按支农产品0.5元算,每立方米氧气耗电价在0.2元再乘以450立方=90元,每吨合成氨耗吸附剂分之筛为0.5―0.6公斤,每公斤分之筛按10元计,就是5--6元,水耗按吨氨耗1.0元。
以上几种数据相加,就是制氧工序每吨合成氨所需费用为121.8元,工人的工资可除外,因为造气岗位腾出来的人员可到制氧岗位去。
三;年产20万吨合成氨年所消耗费用
通过以上表格和表明,所有的费用都出了,我们再来算一下20万吨合成氨每年制氧系统所消耗的费用,再用121.8除以20万吨,就是一年的费用。
这样每年的费用为2436万元,制氧部分的消耗算是出了,再用富氧固定床已连续气化挹注原料煤的费用乘以制氧部分的消耗,就是每年的利润,用8075万乘以2436万等同于5639万元。
四;附注
以上是理论和当时07―08年我在该单位的原料煤实际消耗、和半水煤气成份、吹风气成份所消耗的碳算出来的有关数据,地就是从工业生产实际中考虑,节约原料煤再少一点,富氧消耗在大一点,不管怎么说投资4千多万,8--10个月可收回成本。
这还没有计算现造气鼓风机的消耗,因为富氧连续气化技术,不用空气鼓风机,按现造气共十六台造气炉,平常四台炉子一台鼓风机要开四台鼓风机,每台
鼓风机的耗电量也非常大,大约每年的电费也在3―4百万,所以说道使用富氧固定
床已连续气化技术,年节约在5--6千万还是没问题的,8―10个月全然可收回
单价元1213.3450/m36合计元1213.3906121.3投资成本。
所以说采用固定床连续气
化技术是现企业节能降耗的当务之及,也是领导明智之选。
附件;
下面就是一种最简单的计算方法,再去证实该技术的节能环保效果。
1;以现有的炉型造气每吨合成氨的消耗计算,目前每吨合成氨消耗在1.6―1.7,平
均按1.65吨原料煤算,每吨煤的单价平均为950元/吨。
这样每吨合成氨生产成本为1567.5元。
2;在去排序使用富氧已连续气化技术的消耗,每吨合成氨的消耗为 1.225吨原料煤,每吨还按950算是,每吨的生产成本为1163.75元/吨
3;每吨合成氨所消耗氧气及分子筛和水的成本,合成氨每吨消耗氧气按450立方米
计算,分子筛按0.5―0.6计算,水按1元算,
每立方氧气耗电量按0.4度排序,吸附剂分子筛按10元计,0.35*450等同于157.5
度电,每度电按0.5元计,05*157.5等同于90元再加之5.5+1等同于96.5元4;综合上述,再用1567.5―1163.75-96.5=307.25元,
5;贷款利息、设备折旧费,按40000万计算,每年的利息为240万,设备折旧费按
15年算,每年为266万,再用240+266=506万,506万再除以20万吨,就是每吨合成氨
所摊的成本,每吨的成本为25.3元,再用307.25-25.3=281.95.2元。
这样每吨合成氨的
节约成本就出来了,再用281.95乘以20万吨,这就是每年的效益,每年的效益为5639
万元。