水泥窑炉空气分级燃烧及SNCR烟气脱硝技术
水泥厂低氮燃烧及SNCR脱硝技术简介
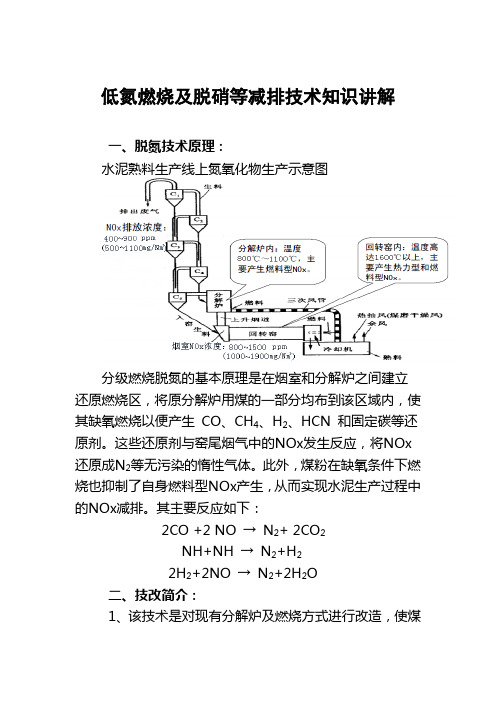
低氮燃烧及脱硝等减排技术知识讲解一、脱氮技术原理:水泥熟料生产线上氮氧化物生产示意图分级燃烧脱氮的基本原理是在烟室和分解炉之间建立还原燃烧区,将原分解炉用煤的一部分均布到该区域内,使其缺氧燃烧以便产生CO、CH4、H2、HCN 和固定碳等还原剂。
这些还原剂与窑尾烟气中的NOx发生反应,将NOx还原成N2等无污染的惰性气体。
此外,煤粉在缺氧条件下燃烧也抑制了自身燃料型NOx产生,从而实现水泥生产过程中的NOx减排。
其主要反应如下:2CO +2 NO →N2+ 2CO2NH+NH →N2+H22H2+2NO →N2+2H2O二、技改简介:1、该技术是对现有分解炉及燃烧方式进行改造,使煤粉在分解炉内分级燃烧,在分解炉锥部形成还原区,将窑内产生的NOx还原为N2,并抑制分解炉内NOx的生成。
根据池州海螺3#天津院设计的TDF分解炉结构,技改方案采用川崎公司窑尾新型燃烧器,并在分解炉锥部新增两个喂煤点,最大限度形成还原区,提高脱氮效率。
改造整体示意图2、窑尾缩口由圆形改成方形,高度改为1600mm,并设置跳台,防止分解炉塌料现象发生,通过在分解炉锥部增设喷煤点,在分解炉锥部形成还原区。
改造前锥部改造后锥部3、对窑尾烟室入炉烟气进行整流,将上升烟道改造成方形,同时,将上升烟道的直段延长,使窑内烟气入炉流场稳定,降低入炉风速。
其次在分解炉锥部设计脱氮还原区,将分解炉煤粉分4点、上下2层喂入,增加了燃烧空间。
在保证煤粉充分燃烧的同时,适当增加分解炉锥部的煤粉喂入比例,保证缺氧燃烧产生的还原气氛,从而在分解炉锥部区域形成一个“还原区”,部分生成的氮氧化物在该区域被还原分解,降低系统氮氧化物浓度。
改造前窑尾燃烧器改造后窑尾燃烧器三、SNCR脱硝技术基本原理SNCR选择性非催化还原是指无催化剂的作用下,在适合脱硝反应的“温度窗口”内喷入含有NHx基的还原剂将烟气中的氮氧化物还原为无害的氮气和水。
该项目技术采用炉内喷氨水(浓度20-25%)作为还原剂还原分解炉内烟气中的NOx。
水泥窑炉SNCR烟气脱硝工艺设计
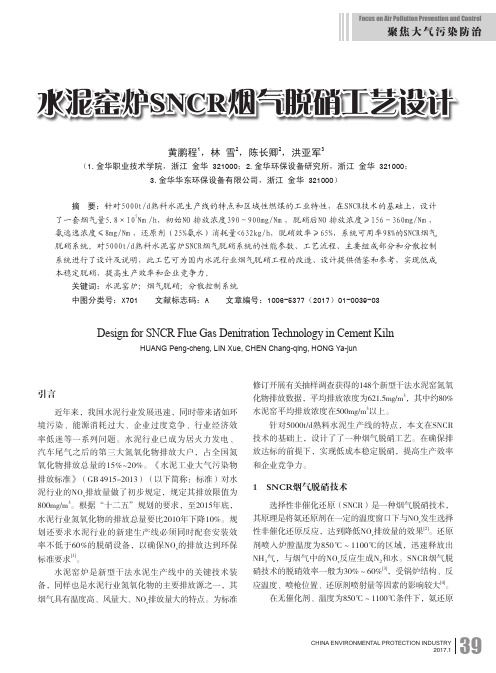
相对于选择性催化还原(SCR)技术,SNCR技术的 脱硝效率较低,约为60%。但是,SNCR技术的成本只有 SCR技术的1/5,且对水泥窑炉正常运行的影响较小。
2 设计依据及主要技术参数
2.1 设计依据 水泥行业回转窑炉的主要燃烧对象是燃煤, 在物料 烧制过程中, 会产生大量的烟气, 烟气中含有大量NOx 。 本SNCR烟气脱硝系统主要是为长期稳定确保5000t/d熟 料水泥生产线水泥窑炉的NOx排放量达到环保标准而设 计的,烟气参数见表1所示。生产线上每台窑炉的耗煤 量为27.6t/h,所燃烧的煤种是产自福建清流县的无烟煤 (掺加30%的烟煤),其工业分析见表2所示。
Design for SNCR Flue Gas Denitration Technology in Cement Kiln
HUANG Peng-cheng, LIN Xue, CHEN Chang-qing, HONG Ya-jun
引言
近年来,我国水泥行业发展迅速,同时带来诸如环 境污染、能源消耗过大、企业过度竞争、行业经济效 率低迷等一系列问题。水泥行业已成为居火力发电、 汽车尾气之后的第三大氮氧化物排放大户,占全国氮 氧化物排放总量的15%~20%。《水泥工业大气污染物 排放标准》(GB 4915-2013)(以下简称:标准)对水 泥行业的NOx排放量做了初步规定,规定其排放限值为 800mg/m3。根据“十二五”规划的要求,至2015年底, 水泥行业氮氧化物的排放总量要比2010年下降10%。规 划还要求水泥行业的新建生产线必须同时配套安装效 率不低于60%的脱硝设备,以确保NOx的排放达到环保 标准要求 。 水泥窑炉是新型干法水泥生产线中的关键技术装 备,同样也是水泥行业氮氧化物的主要排放源之一,其 烟气具有温度高、风量大、NOx排放量大的特点。为标准
《安全环境-环保技术》之水泥窑尾烟气SCR脱硝技术

水泥窑尾烟气SCR脱硝技术一前言2015年全国氮氧化物排放量1851.9万吨,其中,水泥排放氮氧化物约占全国排放总量的10%,仅次于火电和机动车行业,位居第三。
2016年年底,国务院印发《“十三五”节能减排综合工作方案》,提出到2020年氮氧化物排放总量比2015年下降15%以上的主要目标。
《水泥工业大气污染物排放标准》(GB 4915-2013)要求氮氧化物排放限值400 mg/Nm3,重点地区320 mg/Nm3;在氮氧化物排放要求日趋严格背景下,2017年5月,江苏省环保厅《关于开展全省非电行业氮氧化物深度减排的通知》要求,水泥行业2019年6月1日前氮氧化物排放不高于100 mg/Nm3;2018年9月,《唐山市生态环境深度整治攻坚月行动方案》提出氮氧化物排放浓度不高于50 mg/Nm3。
现行的脱硝技术大体分为氧化法脱硝和催化还原法脱硝。
氧化法脱硝采用强氧化剂,如臭氧、亚氯酸钠等强氧化剂,把NOx氧化成高价氮氧化物,然后通过水或者碱液体进行吸收,但是存在耗电高、二次污染物废水排放问题。
催化还原法,一般指SCR法,因其无二次污染排放问题,脱硝效率高,可以实现超净排放,运行可靠稳定、适应负荷波动等优点,广泛的应用在各个工矿企业中。
SCR脱硝技术作为全世界应用最广泛高效的氮氧化物脱除技术,符合水泥行业日趋严格的氮氧化物排放要求,是一种理想的水泥窑脱硝技术。
研究高效水泥窑SCR脱硝技术,具有现实意义。
二水泥窑尾烟气特点(1)NOx含量高,为300~1300mg/Nm3。
(2)湿度大,水含量8~16%;水蒸气露点一般为45~55℃。
(3)粉尘含量高,烟尘浓度达60~120 g/Nm3,并含有碱土金属氧化物等腐蚀性成分。
(4)粉尘粒径小(小于10μm的颗粒约占75~90%)、比电阻高,除尘难度大。
(5)粉尘中碱金属氧化物含量高。
以上这些烟气特点均增加了脱硝的难度和投资成本。
表1某水泥窑尾飞灰与燃煤锅炉飞灰主要成分对比三水泥窑尾烟气SCR脱硝难点目前,国外有一些水泥生产线 SCR运行案例,但未见其长期稳定运行且各项指标满意、完全可推广的技术案例报导,其主要原因是,水泥生产工艺的高效脱硝技术路线尚达不到电厂燃煤锅炉脱硝技术的成熟度和可靠度。
水泥炉窑SNCR及SCR烟气脱硝技术比较
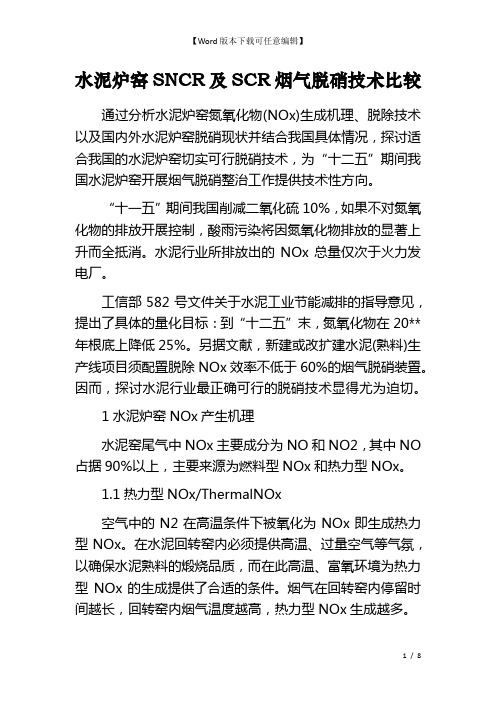
水泥炉窑SNCR及SCR烟气脱硝技术比较通过分析水泥炉窑氮氧化物(NOx)生成机理、脱除技术以及国内外水泥炉窑脱硝现状并结合我国具体情况,探讨适合我国的水泥炉窑切实可行脱硝技术,为“十二五”期间我国水泥炉窑开展烟气脱硝整治工作提供技术性方向。
“十一五”期间我国削减二氧化硫10%,如果不对氮氧化物的排放开展控制,酸雨污染将因氮氧化物排放的显著上升而全抵消。
水泥行业所排放出的NOx总量仅次于火力发电厂。
工信部582号文件关于水泥工业节能减排的指导意见,提出了具体的量化目标:到“十二五”末,氮氧化物在20**年根底上降低25%。
另据文献,新建或改扩建水泥(熟料)生产线项目须配置脱除NOx效率不低于60%的烟气脱硝装置。
因而,探讨水泥行业最正确可行的脱硝技术显得尤为迫切。
1水泥炉窑NOx产生机理水泥窑尾气中NOx主要成分为NO和NO2,其中NO 占据90%以上,主要来源为燃料型NOx和热力型NOx。
1.1热力型NOx/ThermalNOx空气中的N2在高温条件下被氧化为NOx即生成热力型NOx。
在水泥回转窑内必须提供高温、过量空气等气氛,以确保水泥熟料的煅烧品质,而在此高温、富氧环境为热力型NOx的生成提供了合适的条件。
烟气在回转窑内停留时间越长,回转窑内烟气温度越高,热力型NOx生成越多。
1.2燃料型NOx/FuelNOx燃料中的含氮化合物被氧化成燃料型NOx,此类NOx 主要在分解炉和预热器等温度低于1200℃区域生成。
据文献报道,燃料型NOx生成约有60%左右的燃料N被转化为燃料型NOx。
1.3原料型NOx/FeedNOx煅烧水泥的原料主要成分为石灰石,另有黏土、沙石等,不同原料中氮含量由20×10-6~100×10-6不等。
原料型NOx主要在温度窗口为300~800℃内生成。
带预分解炉或预热器的窑型,较之其他传统窑型,熟料产量大,生成的原料型NOx较少。
1.4快速型NOx/PromptNOx在复原性气氛下燃料相对过量,过量的燃料中的CH自由根与助燃空气中的N2快速反应生成快速型NOx。
水泥窑炉烟气SCR脱硝技术行业应用情况简述
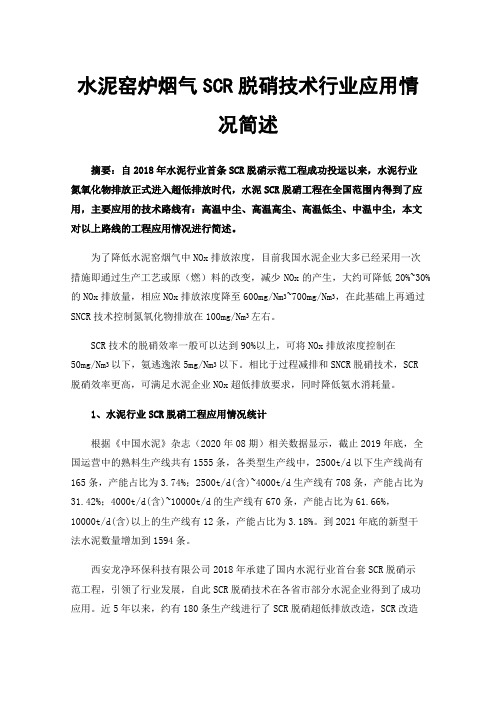
水泥窑炉烟气SCR脱硝技术行业应用情况简述摘要:自2018年水泥行业首条SCR脱硝示范工程成功投运以来,水泥行业氮氧化物排放正式进入超低排放时代,水泥SCR脱硝工程在全国范围内得到了应用,主要应用的技术路线有:高温中尘、高温高尘、高温低尘、中温中尘,本文对以上路线的工程应用情况进行简述。
为了降低水泥窑烟气中NOx排放浓度,目前我国水泥企业大多已经采用一次措施即通过生产工艺或原(燃)料的改变,减少NOx的产生,大约可降低20%~30%的NOx排放量,相应NOx排放浓度降至600mg/Nm3~700mg/Nm3,在此基础上再通过SNCR技术控制氮氧化物排放在100mg/Nm3左右。
SCR技术的脱硝效率一般可以达到90%以上,可将NOx排放浓度控制在50mg/Nm3以下,氨逃逸浓5mg/Nm3以下。
相比于过程减排和SNCR脱硝技术,SCR脱硝效率更高,可满足水泥企业NOx超低排放要求,同时降低氨水消耗量。
1、水泥行业SCR脱硝工程应用情况统计根据《中国水泥》杂志(2020年08期)相关数据显示,截止2019年底,全国运营中的熟料生产线共有1555条,各类型生产线中,2500t/d以下生产线尚有165条,产能占比为3.74%;2500t/d(含)~4000t/d生产线有708条,产能占比为31.42%;4000t/d(含)~10000t/d的生产线有670条,产能占比为61.66%,10000t/d(含)以上的生产线有12条,产能占比为3.18%。
到2021年底的新型干法水泥数量增加到1594条。
西安龙净环保科技有限公司2018年承建了国内水泥行业首台套SCR脱硝示范工程,引领了行业发展,自此SCR脱硝技术在各省市部分水泥企业得到了成功应用。
近5年以来,约有180条生产线进行了SCR脱硝超低排放改造,SCR改造占比约11.3%。
水泥行业已实施和在实施的SCR脱硝工程项目所在区域如表1所示。
表1水泥行业已实施和在实施的SCR脱硝工程项目所在区域2、水泥SCR脱硝技术业绩应用情况及代表单位根据水泥SCR脱硝的设计温度与除尘器形式的不同,技术路线分为高温中尘、高温高尘、高温低尘、中温中尘,水泥SCR脱硝的技术路线及代表单位简介详见下表:2.1高温中尘技术路线西安龙净环保科技有限公司是最早开展水泥行业SCR脱硝研究和应用的环保企业,西安龙净自主研发的高温中尘即“高温电除尘器+SCR脱硝一体化技术”已在国内多个水泥生产线成功应用,该技术具有成熟可靠、投资适中等优点,近年来西安龙净通过对水泥脱硝技术的多次升级与创新,在不设旁路烟道的前提下,实现了众多水泥SCR脱硝系统的长期稳定、高效经济运行,业绩在行业内遥遥领先。
水泥厂脱硝技术简介及SNCR方案介绍
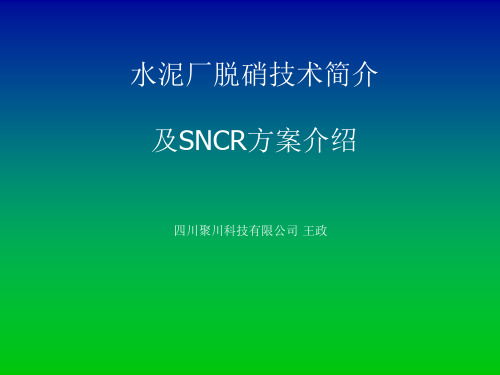
SNCR系统对生产线的影响
SNCR系统喷射点位于分解炉,最合适的位置需要视实际 的温度点而定,一般来说有4-10个常用位置及4-10个备 用位置,因此不需要对分解炉进行改变;
对生产线的工艺影响; 还原剂的喷射对烟气的温度有细微的影响,大约下降2℃; 对生产线产能的影响 SNCR对生产线的产能没有影响; SNCR对热耗的影响
域的温度为(870-1090℃)将NOx还原成N2和H2O; 在NH3/NOx摩尔比0.8-3的情况下,降氮效率20-70%。如 果降氮效率达到85%时,此时氨氮摩尔比超过3,氨的逃逸率太 高,成本增加太大。
逃逸的氨基本都被生料吸收,很少有氨可以逃逸到大气中。
SNCR性能影响因素
反应温度范围; 最佳温度区的滞留时间;至少0.5s以上 喷入的反应剂与烟气混合程度; 处理前烟气NOx本底浓度; 喷入的反应剂与NOx的摩尔比; 氨的逃逸量; SNCR只有在喷射量很大时对窑系统操作有较明显影响,主
XX水泥有限公司SNCR方案
运行成本分析
脱硝幅度
1000~400 mg/Nm3
脱销率 % 60
喷射 氨氮比 1.5—2.5
还原剂喷射量 t/h
0.58—0.97
运行成本 ¥/吨熟料
3—5.1
800~400 mg/Nm3
50
1.5—2.5 0.39—0.65
2—3.4
备注
按照20%浓度的氨水,氨水按照1100元/吨到厂价计算;氨 氮比按照最高2.5计算。
SNCR降氮工艺特点
SNCR工艺中: 氨自由基与NOX反应,烟气中的氧参与反应,为放热反应,但 不足以弥补CO与O2反应放热;
《安全环境-环保技术》之水泥窑尾烟气SCR脱硝技术

水泥窑尾烟气SCR脱硝技术一前言2015年全国氮氧化物排放量1851.9万吨,其中,水泥排放氮氧化物约占全国排放总量的10%,仅次于火电和机动车行业,位居第三。
2016年年底,国务院印发《“十三五”节能减排综合工作方案》,提出到2020年氮氧化物排放总量比2015年下降15%以上的主要目标。
《水泥工业大气污染物排放标准》(GB 4915-2013)要求氮氧化物排放限值400 mg/Nm3,重点地区320 mg/Nm3;在氮氧化物排放要求日趋严格背景下,2017年5月,江苏省环保厅《关于开展全省非电行业氮氧化物深度减排的通知》要求,水泥行业2019年6月1日前氮氧化物排放不高于100 mg/Nm3;2018年9月,《唐山市生态环境深度整治攻坚月行动方案》提出氮氧化物排放浓度不高于50 mg/Nm3。
现行的脱硝技术大体分为氧化法脱硝和催化还原法脱硝。
氧化法脱硝采用强氧化剂,如臭氧、亚氯酸钠等强氧化剂,把NOx氧化成高价氮氧化物,然后通过水或者碱液体进行吸收,但是存在耗电高、二次污染物废水排放问题。
催化还原法,一般指SCR法,因其无二次污染排放问题,脱硝效率高,可以实现超净排放,运行可靠稳定、适应负荷波动等优点,广泛的应用在各个工矿企业中。
SCR脱硝技术作为全世界应用最广泛高效的氮氧化物脱除技术,符合水泥行业日趋严格的氮氧化物排放要求,是一种理想的水泥窑脱硝技术。
研究高效水泥窑SCR脱硝技术,具有现实意义。
二水泥窑尾烟气特点(1)NOx含量高,为300~1300mg/Nm3。
(2)湿度大,水含量8~16%;水蒸气露点一般为45~55℃。
(3)粉尘含量高,烟尘浓度达60~120 g/Nm3,并含有碱土金属氧化物等腐蚀性成分。
(4)粉尘粒径小(小于10μm的颗粒约占75~90%)、比电阻高,除尘难度大。
(5)粉尘中碱金属氧化物含量高。
以上这些烟气特点均增加了脱硝的难度和投资成本。
表1某水泥窑尾飞灰与燃煤锅炉飞灰主要成分对比三水泥窑尾烟气SCR脱硝难点目前,国外有一些水泥生产线 SCR运行案例,但未见其长期稳定运行且各项指标满意、完全可推广的技术案例报导,其主要原因是,水泥生产工艺的高效脱硝技术路线尚达不到电厂燃煤锅炉脱硝技术的成熟度和可靠度。
水泥窑废气脱硝技术选择

水泥窑废气脱硝技术选择摘要:干法水泥窑炉的氮氧化物减排迫在眉睫,水泥企业如何选择脱硝工艺,以及各种脱硝工艺的技术特点和投资费用等。
文章对目前的主流脱硝技术及技术经济做了介绍。
关键词:水泥、氮氧化物、脱硝1 水泥窑氮氧化物排放现状经过“十一五”期间的快速发展,我国水泥产量已经达到约18.8亿吨,其中的新型干法水泥熟料产能为12.6亿吨。
水泥煅烧产生了大量NOx,国外回转窑废气中氮氧化物排放浓度为300mg/Nm3~2200mg/Nm3,国内运行的新型干法水泥窑排放浓度根据一些不完整的监测数据显示,大约750~1500 mg/Nm3。
2 当前水泥炉窑氮氧化物排放环保控制标准氮氧化物是“十二五”期间我国新增的减排指标之一,目标是5年内降低10%。
目前最新颁布的GB 13223-2011《火电厂大气污染物排放标准》将火力发电行业的氮氧化物排放标准从450-1100 mg/Nm3提高到了100mg/Nm3。
同时国内部分发达地区对水泥炉窑的氮氧化物排放也提高了要求:3 脱硝技术种类3.1 低氮燃烧技术最常用的低NOx燃烧技术是分级燃烧技术,它包含了低过量空气燃烧、空气分级燃烧、燃料分级燃烧等技术。
分级燃烧是把燃烧分阶段完成,通过调整燃烧工况来达到低NOx生成的一种炉内控制技术。
形成缺氧富燃区并设法降低局部高温区的燃烧温度以抑制NOx的生成,使温度和氧浓度的高点值不同时存在;减少燃料周围的氧浓度,形成还原性气氛并加入还原剂,使已生成的NOx被还原。
3.1.1空气分级燃烧煤在传统的燃烧器中要求燃料和所有空气快速混合,并在过量空气状态下进行充分燃烧。
从NOX 形成机理中可以知道,反应区内的空燃比极大地影响着NOX 的生成,反应区的空气过剩越多,NOX的排放量越大。
3.1.1燃料分级燃烧燃料分级燃烧,也称为再燃烧,是把燃料分成两股或多股燃料流,这些燃料流经过三个燃烧区发生燃烧反应。
第一燃烧区为富氧燃烧区,第二燃烧区通常称为在燃烧区,该区空气过剩系数小于1,为缺氧燃烧区。
- 1、下载文档前请自行甄别文档内容的完整性,平台不提供额外的编辑、内容补充、找答案等附加服务。
- 2、"仅部分预览"的文档,不可在线预览部分如存在完整性等问题,可反馈申请退款(可完整预览的文档不适用该条件!)。
- 3、如文档侵犯您的权益,请联系客服反馈,我们会尽快为您处理(人工客服工作时间:9:00-18:30)。
水泥窑炉空气分级燃烧及SNCR烟气脱硝
技术
江苏省盐城市兰丰环境工程科技有限公司 苗长江 陈森林
224000
摘要:本文从以下几个方面系统介绍了我公司治理水泥窑炉烟气中NOx的烟气脱硝技术,希望能对水泥窑炉NOx治理起到一定的借鉴作用。
关键词: 回转窑 分解炉 NOx 空气分级燃烧 SNCR脱硝技术
引言
近年来,水泥工业随着现代城市建设的需要而得到了快速的发展,但是水泥生产过程中产生的废气对环境的污染也在不断加剧,特别是废气中的NOx对大气环境的影响已非常严重。
由此,本文从以下几个方面系统介绍了我公司治理水泥窑炉烟气中NOx的烟气脱硝技术,希望能对水泥窑炉NOx治理起到一定的借鉴作用。
1 水泥窑炉NOx产生机理
在新型干法水泥生产工艺中,回转窑和分解炉是水泥物料烧成的两个关键设备。
然而,回转窑和分解炉也是NOx生成的主要来源。
在水泥熟料生产过程中,大约有40%左右的煤粉从回转窑窑头的多通道燃烧器喷入窑内,并进行高温燃烧,为煅烧物料的熔融和矿物重结晶提供足够的温度,但物料温度必须超过1400℃时才会发生物料熔融和矿物重结晶现象,因此通常需要将窑头燃烧器形成的火焰温度控制在1800~2200℃之间,然而这样在回转窑内就会生成热力型NOx和燃料型NOx,且均有较多的形成比例,其中尤以热力NOx为主。
同时,大约60%左右的
煤粉进入分解炉,炉内的温度一般在850~1100℃范围内,在此温度下,基本可以不考虑热力型NOx的形成,主要是燃料型NOx。
由此,本文系统介绍了我公司治理水泥窑炉烟气中NOx的空气分级燃烧及SNCR脱硝技术,希望能对水泥窑炉NOx治理起到一定帮助。
2 水泥窑炉空气分级燃烧技术
2.1 基本原理
水泥窑炉空气分级燃烧是目前最为普遍的降低NOx排放的燃烧技术之一。
其基本原理如图(一)所示:将燃烧所需的空气量分成两级送入,使第一级燃烧区内过量空气系数小于1,燃料先在缺氧的富燃料条件下燃烧,使得燃烧速度和温度降低,从而降低了热力型NOx的生成。
同时,燃烧生成的CO与NOx发生还原反应,以及燃料氮分解成中间产物(如NH、CN、HCN和NHx等)相互作用或NOx还原分解,从而抑制了燃料型NOx的生成,具体反应如下:
2CO + 2NO → 2CO2 + N2 (1)
NH + NH → N2 + H2 (2)
NH + NO → N + OH (3)
在二级燃烧区(燃尽区内,将燃烧用空气的剩余部分以二次空气的形式输入,成为富氧燃烧区。
此时,空气量增多,一些产物被氧化生成NOx,但因温度相对常规燃烧较低,因而总的NOx生成量不高,具体反应如下:
CN + O → CO + NO (4)
图(一)水泥窑炉空气分级燃烧技术示意图
2.2 改造方案及效果
如图(一)所示,保持原分解炉主体结构不变,在分解炉烟室预留的脱硝还原区设置高速喷煤嘴,让喷入的煤粉在此区域内缺氧燃烧,产生适量的还原气氛,与窑气中的NOx发生反应,将NOx转化为无污染的N2。
同时将三次风管入分解炉的部分管道抬高到相应位置。
整个窑尾用煤总量与改造前保持一致,只是进入分解炉及还原区的用煤量不同。
水泥窑炉经过空气分级燃烧技术改造后,其脱硝效率一般可达20%左右。
3 水泥窑炉SNCR烟气脱硝技术
3.1 基本原理
SNCR脱硝技术即选择性非催化还原(Selective Non-Catalytic
Reduction,以下简写为SNCR)技术,是一种不用催化剂,在850~1100℃的温度范围内,将含氨基的还原剂(如氨水,尿素溶液等)喷入炉内,将烟气中的NOx还原脱除,生成氮气和水的清洁脱硝技术。
在合适的温度区域,且氨水作为还原剂时,其反应方程式为:
4NH3 + 4NO + O2→4N2 + 6H2O (1)
然而,当温度过高时,也会发生如下副反应:
4NH3 + 5O2→4NO + 6H2O (2)
3.2 SNCR脱硝还原剂的选择
目前,SNCR脱硝工艺最常用的还原剂有氨水和尿素两种。
然而,在SNCR脱硝系统中,还原剂是最大的消耗品,脱硝还原剂的选择是整个脱硝工艺中很重要的一个环节。
(1)氨水和尿素的特性对比
氨水的特性:氨水与无水氨都属于危险化学品。
作为脱硝原剂时,通常采用20%~25%浓度的氨水。
无色透明液体,易分解放出氨气,温度越高,分解速度越快。
如果溢出,氨水液体扩散范围较无水氨小,浓度范围较易控制,较无水氨相对安全。
尿素的特性:尿素是白色或浅黄色的结晶体,易溶于水。
不同浓度的尿素水溶液有不同的结晶温度。
与无水氨及氨水相比,尿素是无毒、无害的化学品,是农业常用的肥料,无爆炸可能,完全没有危险。
(2)占地面积对比
氨水作为还原剂时,仅需考虑氨水储罐的位置,占地面积较小。
而尿素作为还原剂时,需要设计专门的尿素溶液制备系统,占地面积较
大。
(3)工艺系统对比
尿素需要经过溶解制成50%以下的尿素溶液,需要蒸汽加热,且存在结晶等问题。
而氨水作为还原剂时,不存在结晶问题,其工艺系统最简单、最可靠。
(4)还原剂利用率对比
由于水泥窑分解炉内温度正常为850~950℃之间,当氨水作为还原剂喷入分解炉时,水分迅速蒸发为气态而散失在烟气中,氨则有选择性地与烟气中的NOx反应,从而脱除NOx;而尿素溶液作为还原剂喷入分解炉时,水分也迅速蒸发,但尿素粒子并不能立即与烟气中的NOx反应,还需要在高温状态下进行分解,生成NH3后,再与烟气中的NOx反应。
因此,综合以上分析,笔者认为氨水作为还原剂比较可靠!
3.3 SNCR脱硝工艺流程
如图(二)所示,水泥窑炉SNCR烟气脱硝工艺系统主要包括还原剂储存系统、循环输送模块、稀释计量模块、分配模块、背压模块、还原剂喷射系统和相关的仪表控制系统等。
图(二)典型水泥窑炉SNCR工艺流程图
3.4 脱硝效果
在SNCR脱硝系统中,还原剂喷入水泥窑分解炉内合适的温度区间,在NH3/NOx摩尔比为1.0~1.8情况下,脱硝效率可达30%~60%左右,氨逃逸≤10ppm。
4 结论与展望
通过以上两种水泥脱硝技术的介绍和分析,笔者建议:在水泥窑炉烟气中NOx初始浓度不高或环保排放标准要求不高时,采用几乎没有运行成本的空气分级燃烧脱硝技术比较经济;而在NOx初始浓度较高或环保排放标准苛刻时,同时使用空气分级燃烧和SNCR脱硝相结合脱硝技术,可以最终实现高脱硝效率和低运行成本的两重目标。