(整理)国际先进的感应淬火技术
感应加热淬火热处理

感应加热淬火热处理一、引言感应加热淬火热处理是一种常见的金属材料加工技术,它通过感应加热将金属材料加热到高温状态,然后迅速冷却以改变其物理和化学性质。
该技术广泛应用于汽车、航空航天、机械制造等领域,以提高材料的硬度、强度和耐腐蚀性能。
二、感应加热原理感应加热是一种非接触式电磁加热方式,其原理是利用高频电流在金属导体内产生涡流,并使导体内部发生自发加热。
感应加热设备由高频电源、线圈和工件组成。
高频电源将交流电转换成高频电流,线圈将高频电流传递到工件中,工件在涡流作用下发生自发加热。
三、淬火原理淬火是指将金属材料从高温状态迅速冷却以改变其物理和化学性质的过程。
淬火可使钢材表面形成硬度较高的马氏体组织,并增强钢材的强度和耐腐蚀性能。
淬火过程中,金属材料的温度迅速下降,导致其组织结构发生相变。
淬火介质通常为水、油或空气。
四、感应加热淬火工艺感应加热淬火工艺是将感应加热和淬火技术结合起来的一种金属材料加工方式。
该工艺通常分为以下几个步骤:1. 准备工作:对待处理的金属材料进行清洗、去除表面污垢和氧化物等预处理。
2. 加热:将待处理的金属材料放置在感应加热设备中,通过高频电流产生涡流并使其自发加热到所需温度。
3. 保温:在达到所需温度后,保持一定时间使其均匀受热并达到稳定状态。
4. 淬火:在保温结束后,将金属材料迅速浸入淬火介质中进行冷却。
淬火介质的选择取决于待处理材料的类型和要求。
5. 清洗:将已经淬火完成的金属材料从淬火介质中取出,并进行清洗以去除表面污垢和残留的淬火介质。
6. 回火:在淬火后,金属材料的硬度较高,容易产生裂纹和变形。
因此,需要进行回火处理以消除内部应力和改善其塑性。
五、应用领域感应加热淬火工艺广泛应用于汽车、航空航天、机械制造等领域。
在汽车制造中,感应加热淬火技术常用于制造发动机零部件、传动轴和齿轮等;在航空航天领域,该技术则用于制造高强度金属材料的部件;在机械制造中,感应加热淬火技术可提高钢材的硬度和强度,以满足不同工作环境下的使用要求。
国际先进的感应淬火技术
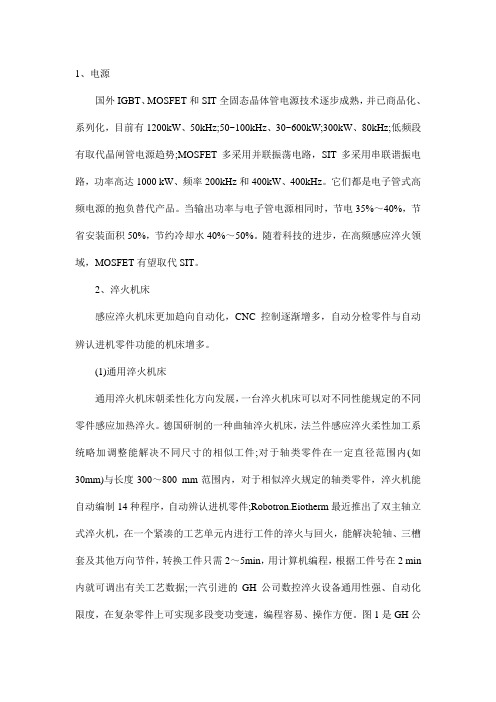
1、电源国外IGBT、MOSFET和SIT全固态晶体管电源技术逐步成熟,并已商品化、系列化,目前有1200kW、50kHz;50~100kHz、30~600kW;300kW、80kHz;低频段有取代晶闸管电源趋势;MOSFET多采用并联振荡电路,SIT多采用串联谐振电路,功率高达1000 kW、频率200kHz和400kW、400kHz。
它们都是电子管式高频电源的抱负替代产品。
当输出功率与电子管电源相同时,节电35%~40%,节省安装面积50%,节约冷却水40%~50%。
随着科技的进步,在高频感应淬火领域,MOSFET有望取代SIT。
2、淬火机床感应淬火机床更加趋向自动化,CNC控制逐渐增多,自动分检零件与自动辨认进机零件功能的机床增多。
(1)通用淬火机床通用淬火机床朝柔性化方向发展,一台淬火机床可以对不同性能规定的不同零件感应加热淬火。
德国研制的一种曲轴淬火机床,法兰件感应淬火柔性加工系统略加调整能解决不同尺寸的相似工件;对于轴类零件在一定直径范围内(如30mm)与长度300~800 mm范围内,对于相似淬火规定的轴类零件,淬火机能自动编制14种程序,自动辨认进机零件;Robotron.Eiotherm最近推出了双主轴立式淬火机,在一个紧凑的工艺单元内进行工件的淬火与回火,能解决轮轴、三槽套及其他万向节件,转换工件只需2~5min,用计算机编程,根据工件号在2 min 内就可调出有关工艺数据;一汽引进的GH公司数控淬火设备通用性强、自动化限度,在复杂零件上可实现多段变功变速,编程容易、操作方便。
图1是GH公司的数控淬火机床。
(2)专用淬火机床专用淬火机床更加专用化,采用机械手上下零件,加热、淬火、回火、校直、检查完全自动进行。
先进的计算机控制技术可以监控并屏幕显示淬火过程和工艺参数,跟踪所有操作过程,如发现故障或工艺参数偏离给定值,便自动修正或自动列出不合格零件,使控制系统暂停工作并报警,同时屏幕上显示故障性质和所要修正的动作。
感应淬火 (2)
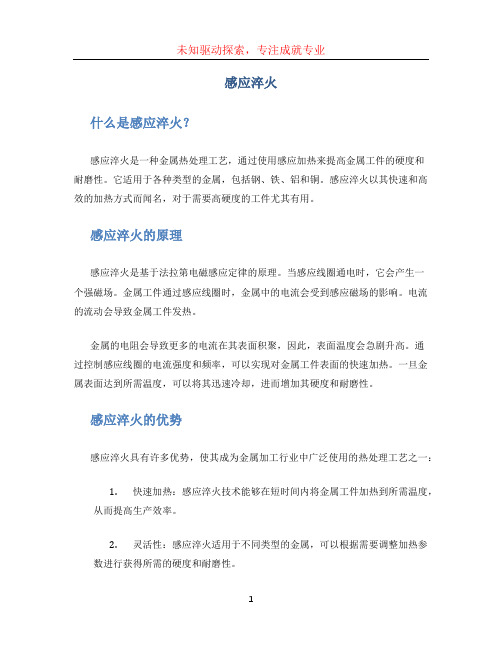
感应淬火什么是感应淬火?感应淬火是一种金属热处理工艺,通过使用感应加热来提高金属工件的硬度和耐磨性。
它适用于各种类型的金属,包括钢、铁、铝和铜。
感应淬火以其快速和高效的加热方式而闻名,对于需要高硬度的工件尤其有用。
感应淬火的原理感应淬火是基于法拉第电磁感应定律的原理。
当感应线圈通电时,它会产生一个强磁场。
金属工件通过感应线圈时,金属中的电流会受到感应磁场的影响。
电流的流动会导致金属工件发热。
金属的电阻会导致更多的电流在其表面积聚,因此,表面温度会急剧升高。
通过控制感应线圈的电流强度和频率,可以实现对金属工件表面的快速加热。
一旦金属表面达到所需温度,可以将其迅速冷却,进而增加其硬度和耐磨性。
感应淬火的优势感应淬火具有许多优势,使其成为金属加工行业中广泛使用的热处理工艺之一:1.快速加热:感应淬火技术能够在短时间内将金属工件加热到所需温度,从而提高生产效率。
2.灵活性:感应淬火适用于不同类型的金属,可以根据需要调整加热参数进行获得所需的硬度和耐磨性。
3.均匀加热:感应淬火能够实现金属表面的均匀加热,可以避免局部热应力和变形。
4.环保:相比传统的加热方式,感应淬火减少了能源消耗和排放,对环境更友好。
感应淬火的应用感应淬火广泛应用于各个行业,包括汽车、机械、航空航天等。
以下是几个常见的应用领域:1.汽车零部件:感应淬火可用于加工发动机气门、凸轮轴和传动轴等零部件,使其具有更高的硬度和耐磨性。
2.钢铁加工:对于一些需要高硬度和耐磨性的钢材,如轴承钢和切割工具钢,感应淬火可以提供更好的性能。
3.电力行业:感应淬火可用于制造电机转子和发电机组件等关键元件,提高其耐用性和效率。
4.金属模具:通过感应淬火处理,金属模具可以获得更高的硬度和表面耐磨性,延长使用寿命。
感应淬火的挑战尽管感应淬火具有许多优势,但也存在一些挑战需要考虑:1.设备成本:感应加热设备的价格相对较高,这可能对小型企业和初创公司构成一定的挑战。
2.参数控制:感应淬火需要准确控制加热参数,包括电流强度、频率和加热时间等。
sdf同步双频淬火工艺
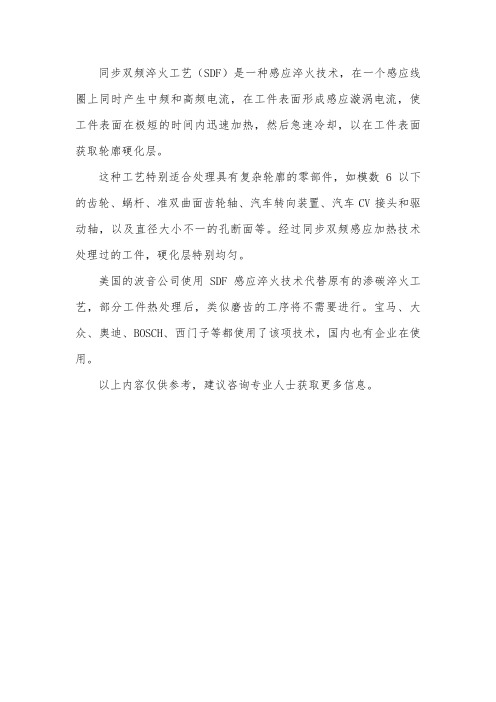
同步双频淬火工艺(SDF)是一种感应淬火技术,在一个感应线圈上同时产生中频和高频电流,在工件表面形成感应漩涡电流,使工件表面在极短的时间内迅速加热,然后急速冷却,以在工件表面获取轮廓硬化层。
这种工艺特别适合处理具有复杂轮廓的零部件,如模数6以下的齿轮、蜗杆、准双曲面齿轮轴、汽车转向装置、汽车CV接头和驱动轴,以及直径大小不一的孔断面等。
经过同步双频感应加热技术处理过的工件,硬化层特别均匀。
美国的波音公司使用SDF感应淬火技术代替原有的渗碳淬火工艺,部分工件热处理后,类似磨齿的工序将不需要进行。
宝马、大众、奥迪、BOSCH、西门子等都使用了该项技术,国内也有企业在使用。
以上内容仅供参考,建议咨询专业人士获取更多信息。
简述感应加热表面淬火的原理及特点

简述感应加热表面淬火的原理及特点一、感应加热表面淬火的原理感应加热表面淬火就是利用电磁感应在工件内产生涡流,然后让工件表面迅速被加热到淬火温度,之后快速冷却的一种淬火方法。
咱打个比方啊,就好像是给工件表面做一个超级快速的“热桑拿”。
当把工件放到感应器里的时候,感应器里通着交变电流呢,这交变电流就会产生交变磁场,这个磁场在工件里就会产生感应电动势啦。
因为工件是导电的嘛,所以就会产生涡流,这个涡流可不得了,它能让工件表面迅速升温,就像小蚂蚁搬家一样,热量快速地聚集在工件表面,然后再喷水或者其他冷却介质进行快速冷却,这样工件表面就淬火成功啦。
二、感应加热表面淬火的特点1. 加热速度特别快这速度快到啥程度呢?就像一阵风“嗖”地一下就把东西吹热了。
因为加热速度快,所以工件表面的氧化脱碳就特别少,就像给工件表面穿上了一层保护衣,能很好地保持工件表面的质量呢。
2. 淬火硬度比较高经过感应加热表面淬火的工件,表面硬度那是相当不错的。
就好比给工件表面注入了一股强大的力量,让它变得更加坚硬耐磨,在很多需要耐磨的地方,这种淬火方式就很吃香。
3. 淬火层深度容易控制咱想让淬火层深一点或者浅一点都比较容易做到。
这就像是做菜的时候放盐,想放多少就放多少,多一点少一点都能根据自己的需求来调整。
通过调整感应电流的频率啊,功率啊,加热时间啊这些参数,就能很精准地控制淬火层的深度。
4. 生产效率高这个淬火方式就像是一个高效的小机器人,工作起来可快了。
因为加热速度快,而且可以连续作业,所以在生产线上能大大提高生产效率,能让生产像小火车一样跑得飞快。
5. 节能它比较节能哦。
就像咱平时节约用电一样,这种淬火方式不会浪费很多能量,它把能量都用在了刀刃上,集中加热工件表面,不像一些其他的加热方式,可能到处浪费能量。
6. 易于实现机械化和自动化它很适合和现代的机械化、自动化生产结合起来。
就好像它天生就是为了现代大生产而生的,能够很好地融入到自动化生产线上,不需要费太多的力气去改造,就能实现高效的自动化生产。
高端数控感应淬火机床原理

高端数控感应淬火机床原理1.引言随着制造业的发展,数控机床在金属加工领域的应用日益广泛。
感应淬火机床作为一种高端数控机床,其原理与传统的淬火机床有所不同,具有更高的加工精度和效率。
本文将介绍高端数控感应淬火机床的原理及其工作过程。
2.感应淬火的基本原理感应淬火是一种利用电磁感应原理进行加热和淬火的方法。
在感应淬火机床中,通过电磁感应线圈产生高频交流电场,使工件表面产生感应加热,然后通过快速冷却来实现淬火过程。
感应淬火具有加热均匀、温度可控、淬火速度快等优点,因此在金属加工领域中得到了广泛的应用。
3.高端数控感应淬火机床的结构高端数控感应淬火机床由数控系统、感应装置、冷却系统、夹具等部分组成。
其中数控系统为感应淬火机床的核心,控制整个加工过程的参数和轨迹,具有高精度、高效率、高自动化程度等特点。
3.1数控系统数控系统是感应淬火机床的核心部件,其主要功能是控制电磁感应线圈的工作状态,调节加热功率和加热时间,实现对工件的精准加热和淬火。
数控系统通常采用PLC或CNC控制,能够实现多轴联动控制、自动化加工流程、参数设定和调整等功能。
3.2感应装置感应装置是感应淬火机床中的重要部件,通过高频交流电场对工件进行感应加热。
感应装置通常由电磁感应线圈、电源装置、冷却系统等部分组成。
电磁感应线圈根据工件的形状和尺寸设计成不同的形状和尺寸,有效地实现对工件的均匀加热。
3.3冷却系统冷却系统是感应淬火机床中的关键部件,其主要作用是对经过加热的工件进行快速冷却,实现淬火过程。
冷却系统通常采用循环水冷却或喷水冷却的方式,能够实现对工件的快速冷却和温度控制。
3.4夹具夹具是感应淬火机床中的辅助部件,用于固定和夹持工件,确保加工过程中工件的位置和姿态的稳定性。
夹具通常根据工件的形状和尺寸设计成不同的形状和尺寸,能够适应不同加工需求。
4.高端数控感应淬火机床的工作原理高端数控感应淬火机床的工作原理是将工件放置在感应装置中,通过数控系统对电磁感应线圈进行控制,实现对工件的精准加热和淬火。
感应淬火原理
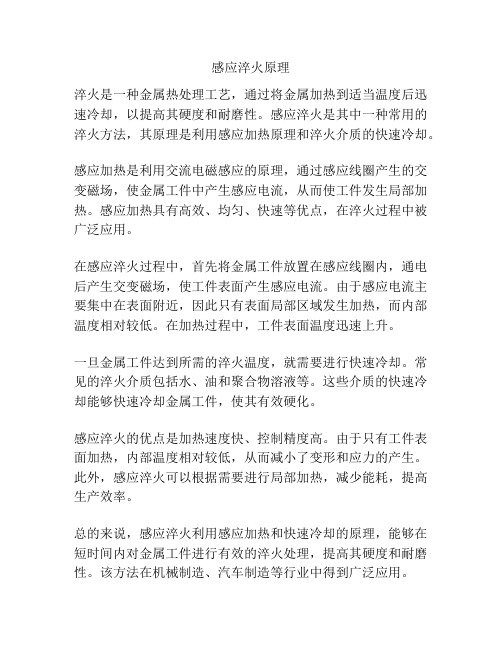
感应淬火原理
淬火是一种金属热处理工艺,通过将金属加热到适当温度后迅速冷却,以提高其硬度和耐磨性。
感应淬火是其中一种常用的淬火方法,其原理是利用感应加热原理和淬火介质的快速冷却。
感应加热是利用交流电磁感应的原理,通过感应线圈产生的交变磁场,使金属工件中产生感应电流,从而使工件发生局部加热。
感应加热具有高效、均匀、快速等优点,在淬火过程中被广泛应用。
在感应淬火过程中,首先将金属工件放置在感应线圈内,通电后产生交变磁场,使工件表面产生感应电流。
由于感应电流主要集中在表面附近,因此只有表面局部区域发生加热,而内部温度相对较低。
在加热过程中,工件表面温度迅速上升。
一旦金属工件达到所需的淬火温度,就需要进行快速冷却。
常见的淬火介质包括水、油和聚合物溶液等。
这些介质的快速冷却能够快速冷却金属工件,使其有效硬化。
感应淬火的优点是加热速度快、控制精度高。
由于只有工件表面加热,内部温度相对较低,从而减小了变形和应力的产生。
此外,感应淬火可以根据需要进行局部加热,减少能耗,提高生产效率。
总的来说,感应淬火利用感应加热和快速冷却的原理,能够在短时间内对金属工件进行有效的淬火处理,提高其硬度和耐磨性。
该方法在机械制造、汽车制造等行业中得到广泛应用。
先进的感应热处理技术在哪里(上)
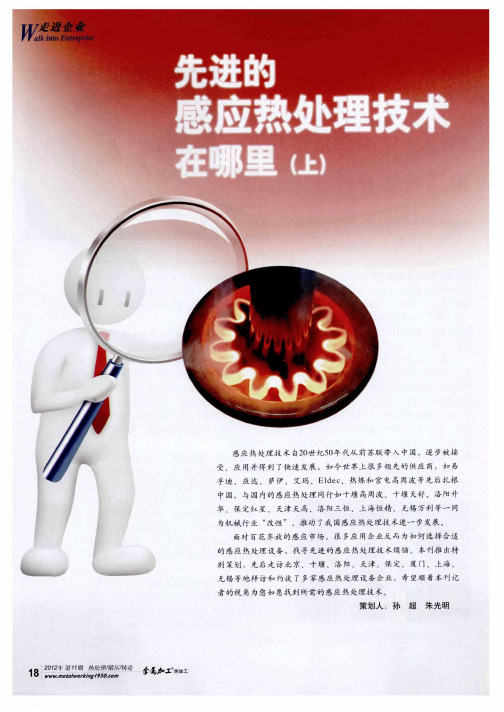
温 度 ,加 热 功率 、保温 时 间 、保温 功 率和 冷 却时 间 都 可 以调节 ,操 作 比较 方便 。 本 刊记 者 还 了 解 到 ,宫 电 的 设 备 采 用I T GB 功
器,拥有一套完整的质量管理体系,可确保工件在
感应热处理的加工过程中完全达标 。其负责人朱会
文 百 忙 中挤 出时 间陪 本 刊记 者 拜访 了宫 电高 周 波设
宫 电副经理石神聪子
便 ,操 作 简单 ,启 动 快 ,通 水 通 电 后 即可 启 动 加 热 。 另外 ,还 通 过 设定 加 热时 间来 控 制工 件 加热 的
宫 电高 周 波设 备 上 海 热处 理 工 厂为 完 善 每一 个 工 件 感 应 热 处 理 要 求 , 配 备 了 全 做 精 。在 一 进车 间 的门 口有 台 加 热设 备 ,石 神聪 子 告 诉记 者 ,这 台设 备 是 用来 给
简短 的 宫电车 间参观 ,本 刊记者 最大 的感触
就是宫 电高周波 在企业做 大还是做 强的选择 上 , 他们 并 不 急 于将 企 业 规 模做 到 很 大 的规 模 ,而 是 更 加 追 求 完 美 的技 术 ,更 注 重在 细 节上 下 功 夫 ,企 业
感应加热成套设备制造商提供竞争平 台,同时 ,表 明中国的感应加热成套设备制造技术已接近或达到 国际的先进水平。十堰高周波有幸为神龙公司配套
曲轴 感 应淬 火机 床 ,这 是 十堰 高 周 波 公 司长 期追 求 ‘ 术 创新 ’的成 果 。” 技 神 龙 公 司 的 曲轴 热 处理 生 产 线采 用 步 进 式 的 自 动 化结 构 ,曲轴 感 应 淬火 工 艺 :感 应 淬火 自动 上料
曲轴 的5 主轴 轴 颈 同时 加 热 淬 火 ; 曲轴 的 感 应 淬 个
- 1、下载文档前请自行甄别文档内容的完整性,平台不提供额外的编辑、内容补充、找答案等附加服务。
- 2、"仅部分预览"的文档,不可在线预览部分如存在完整性等问题,可反馈申请退款(可完整预览的文档不适用该条件!)。
- 3、如文档侵犯您的权益,请联系客服反馈,我们会尽快为您处理(人工客服工作时间:9:00-18:30)。
1、电源国外IGBT、MOSFET和SIT全固态晶体管电源技术逐步成熟,并已商品化、系列化,目前有1200kW、50kHz;50~100kHz、30~600kW;300kW、80kHz;低频段有取代晶闸管电源趋势;MOSFET多采用并联振荡电路,SIT多采用串联谐振电路,功率高达1000 kW、频率200kHz和400kW、400kHz。
它们都是电子管式高频电源的理想替代产品。
当输出功率与电子管电源相同时,节电35%~40%,节省安装面积50%,节约冷却水40%~50%。
随着科技的进步,在高频感应淬火领域,MOSFET有望取代SIT。
2、淬火机床感应淬火机床更加趋向自动化,CNC控制逐渐增多,自动分检零件与自动识别进机零件功能的机床增多。
(1)通用淬火机床通用淬火机床朝柔性化方向发展,一台淬火机床可以对不同性能要求的不同零件感应加热淬火。
德国研制的一种曲轴淬火机床,法兰件感应淬火柔性加工系统略加调整能处理不同尺寸的相似工件;对于轴类零件在一定直径范围内(如30mm)与长度300~800 mm范围内,对于相似淬火要求的轴类零件,淬火机能自动编制14种程序,自动识别进机零件;Robotron.Eiotherm最近推出了双主轴立式淬火机,在一个紧凑的工艺单元内进行工件的淬火与回火,能处理轮轴、三槽套及其他万向节件,转换工件只需2~5min,用计算机编程,根据工件号在2 min 内就可调出有关工艺数据;一汽引进的GH公司数控淬火设备通用性强、自动化程度,在复杂零件上可实现多段变功变速,编程容易、操作方便。
图1是GH公司的数控淬火机床。
(2)专用淬火机床专用淬火机床更加专用化,采用机械手上下零件,加热、淬火、回火、校直、检查完全自动进行。
先进的计算机控制技术可以监控并屏幕显示淬火过程和工艺参数,跟踪全部操作过程,如发现故障或工艺参数偏离给定值,便自动修正或自动列出不合格零件,使控制系统暂停工作并报警,同时屏幕上显示故障性质和所要修正的动作。
更先进的控制系统还适应材料化学成分的波动,并自动调整比功率或加热时间,以保证感应淬火零件的质量。
例如日本高周波热炼株式会社川崎工厂的卧式半轴淬火机床,上尾厂可同时淬三根半轴,群马厂可同时淬两根半轴,机床实际上是感应热处理生产线,全过程除校直、荧光探伤检查需一名工人外,其余全部自动进行。
(3)机器人的应用日本高周波热炼株式会社制造的一台立式通用淬火机床上配置一台机器人,机器人将一个二匝的感应器进行依次平面扫描,使一块塑料板变色,虽然使用电源功率只3 kW,但也可以看出机器人在感应热处理中的应用趋势。
(4)机电一体化将电源、淬火机床、冷却系统组成成套装置,具有占地面积小、生产效率高、一次安装调试容易等优点。
国外最近问世的曲轴固定加热淬火装置占地面积仅为组合式成套装置的1/4。
3、淬火工艺(1)静止式曲轴感应淬火采用静止式曲轴感应淬火新技术的最初的两台装置在福特公司V6和V8曲轴淬火和回火工艺中得以应用,表现出了良好的市场前景。
其特点是:加热时间短,一般仅为1.5~4s,传统工艺是7~12s;电效率高、成本低;感应器与工件之间允许有较大间隙,调整方便;操作简单、重复性好、易于维护;占地面积小,仅为原来的20%左右。
(2)低淬透性钢齿轮淬火现在俄罗斯许多汽车工厂广泛采用低淬透性钢进行整体感应加热表面淬火,已大量应用于汽车、拖拉机后桥齿轮、挖掘机齿轮、传动十字轴、火车车厢用滚动轴承、汽车板簧、铁路螺旋弹簧等,取得了较大的经济效益。
(3)双频感应加热淬火国外双频淬火主要用于齿轮。
20世纪90年代,美国用10kHz中频和150kHz 高频电源,先让齿轮在中频感应器中加热,然后迅速降到高频感应器中加热,最后落入油中淬火。
进入21世纪,此工艺又有新进展,如GH公司采用电力电子开关转换频率,使齿轮的齿顶和齿跟的加热更加均匀,更好地保证了齿轮的淬火质量。
我国汽车工业应用感应热处理技术现状1、电源电源是感应加热的关键设备之一,随着感应加热技术的发展,经历了机械式中频发电机组和真空管式高频电源、晶闸管中频电源及全晶体管电源三个发展阶段。
在20世纪80年代后期,在工业发达国家,晶闸管中频电源已完全取代了中频发电机组,我国自90年代中期也已逐步取代。
同机械式中频发电机组相比,晶闸管(SCR)中频电源具有以下优点:体积小、重量轻、材料消耗少;电效率高,逆变停止时几乎不消耗电能,逆变效率可达90%以上;无机械运动、噪音小、运行可靠、负载匹配容易,可以根据负载情况确定电源的频率;启动停止方便,频率能自动跟踪以保持最佳运行状态;产品设计简单、制造周期短;安装容易,不需要特殊的基础;维修方便等。
我国的晶闸管中频电源的共同特点是全集成化控制线路数字化程度高于90%、启动成功率几乎达到100% 、除具有常规的水压不足、快熔熔断、过流、过压等保护功能外,还具有限流、限压等保护功能、功能较齐全的晶闸管电源还配置逆变失败、水温监视等可选功能,其频率最高可以作到8kHz,额定功率可以作到1000kW左右,如果在装配工艺上再进一步改进的话,可以接近世界先进水平。
随着技术的进步,跟踪80年代国际感应加热技术水平,我国于90年代中期开发出第一台电效率较高的50kW/50kHz IGBT电流型超音频感应加热电源(图2)。
目前可做到频率0.4~50kHz、最大功率可达到800 kW,频率达到100kHz 时功率达到100 kW 。
图2 IGBT电流型超音频感应加热电源IGBT应用同期,我国还成功研制出20 kW/300kHz MOSFET高频电源,缩小了同国际先进水平的差距,随着大功率MOSFET器件的问世,大功率的晶体管高频电源有望年内在感应淬火中应用。
2、淬火工艺随着汽车工业的迅速发展,我国采用感应淬火的零件的种类和品种不断增加。
目前我国汽车零件感应淬火用材料包括:45#、40Cr、55MnVS、40MnB、42CrMo、35#、ZG45、球铁、合金铸铁等。
感应加热淬火介质包括:水、聚乙烯醇、聚迷水溶性淬火介质、UCON、豪富顿251等。
所采用的加热方式及应用主要包括:横向磁场静止一次加热淬火(销轴类零件、凸轮轴);横向磁场连续加热淬火(减振器杆、变速叉轴、扭杆等);横向磁场多段连续加热淬火(起动机轴、空压机轴等);纵向磁场整体一次加热淬火(半轴等);仿形感应器零件旋转加热淬火(球头销);感应接触加热淬火(转向齿条);内孔的一次及连续加热淬火(输出法兰、钟型壳内腔);阶梯轴类零件的旋转加热淬火(小红旗后轮毂轴、转向节);平面类零件的一次及连续加热淬火(钢板弹簧横向限位板);薄壁类复杂零件一次及连续加热淬火(前轮毂、滑动轴叉);复杂形状零件的一次加热淬火(钟型壳变截面轴);槽口一次淬火(变速叉);复杂回线工件旋转一次加热淬火(曲轴)等。
3、淬火机床为了适应多品种的批量生产,在汽车生产应用中,我国引进的感应淬火机床种类由传统的专用设备逐步向柔性化程度较高的通用设备和专用淬火自动生产线发展。
通用淬火机床方面,一汽技术中心开发的卧式数控淬火机床(图3)主驱动采用交流伺服电机拖动,移动速度稳定均匀、定位准确、重复精度高;零件旋转采用变频调速,能适应多方面工艺要求;采用能量和数控技术对不同性能要求的不同零件感应加热淬火,甚至在同一零件上实现多段变功变速,编程容易可操作性强。
图3 通用数控淬火机床专用淬火机床方面,二汽和天舒机电科技有限公司经过多年努力,攻克一个个难关,采用功率脉冲分配技术、尾座自由顶尖技术、薄型淬火变压器技术、独立悬挂技术、悬挂平衡技术等分别研制成功曲轴全自动淬火机床(图4),与电源、水冷系统组成成套淬火设备可对车用内燃机曲轴进行各轴径的圆角+轴径淬火、轴径淬火自回火,采用计算机控制,通过显示屏对设备的加热、淬火工艺参数诸如电压、电流、频率、时间、压力、流量温度等进行监控和显示,目前国内多家采用。
图4 工作中的全自动曲轴淬火机床这些机床在传动系统方面主要采用机械传动,代表现代机械传动技术的滚珠丝杠和直线导轨等先进技术被广泛采用;主驱动采用伺服数控、变频调速,移动速度稳定均匀;拖架定位准确,重复精度高;工件旋转采用变频调速取代固定转速,能适应多方面工艺要求;上下料系统采用较先进的步进链传动、托盘送进料、人工送取料。
另外,在一条生产线中,大功率电源用于淬火,然后用较低功率回火,两个工序在一条生产线上自动完成,减少了重复上下工件的工序,降低了劳动强度,提高了生产效率。
4、其他器件及冷却系统在气动式和接触器式功率切换器、电热电容器、淬火变压器、动作顺序控制及显示、变压器三维移动快换接头等方面,我国也取得了很多技术进步,使淬火技术和工艺水平不断提高。
对于冷却和淬火水循环装置,在消化理解国际感应加热成套设备用水冷系统最新技术基础上,我国自行研制成功适合我国国情的新型、高效、价廉的软水冷却机和水-水冷却机,换热效率高,大大提高了加热设备的可靠性,延长了设备的使用寿命。
认清差距,开拓进取虽然近年来我国感应淬火技术得到了迅速发展,但与工业发达国家相比,还有相当大的差距。
MOSFET高频电源是工业发达国家的首选产品,而我国在高频段仍以晶闸管交流调压、高压硅堆整流、节能型电子管振荡器式电源为主;IGBT超音频电源有部分取代晶闸管中频电源的趋势,而我国在这方面的应用还不够普及;近些年来虽然晶闸管中频电源应用较为普遍,但由于老企业改造步伐的限制,还有部分中频停留在发电机组。
必须指出,虽然我国能够生产MOSFET、IGBT和SIT感应加热淬火用电源,但品种和规格没有国外那么多、那么细,由于关键主要电力电子器件国内还不能生产,必须进口,所以从性能和技术水平方面和国外相比仍有相当大的差距。
总体来说,和工业发达国家相比,我国的数控及全自动淬火机床开发属起步阶段。
在自动化水平上,国内设备大部分是人工上下料,自动化程度较低;能量监控虽有应用但技术还不够成熟;FUNAC、SIMENS伺服系统有所应用,但多为点位直线运动,属简易型,多轴连动类型的数控系统尚未得到应用。
另外,计算机控制技术在感应加热淬火中应用远不如国外那样成熟,例如自动识别进机零件、不合格零件自动剔除;工艺参数跟踪及偏离给定值修正等。
在感应器制造技术、感应器快换、导磁体材料与利用、冷却水循环系统、淬火介质研究与应用等方面也有相当大的差距。
鉴于这些差距,我国应积极行动,建立严格的引进消化政策,避免重复引进,限期淘汰耗能严重的电源,集中力量开发短缺部件,提高淬火机床配套质量等,使感应加热技术迅速赶上世界先进水平。