压铸模成形零件设计
压铸工艺及模具设计:第7章 成型零件和模架设计
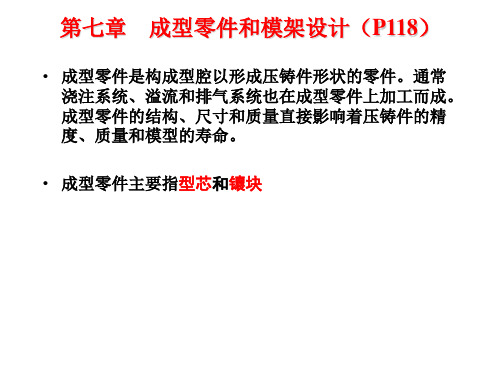
(一)主型芯的结构及固定形式 • 图7-6
(二)小型芯的结构及固定形式 • 图7-7,图7-8。
(二)小型芯的结构及固定形式
六、镶块和型芯的止转形式。
七、镶块和型芯的结构尺寸
(一)镶块壁厚尺寸
(二)整体镶块台阶尺寸
表7-8 整体镶块台阶尺寸推荐值
(三)组合式成型镶块固定部分长度
• 表7-9 组合式成型镶块固定部分长度推荐值
铸件实际尺寸的差与模具成型尺寸之比。即:
• A型-----室温下模具的成型尺寸(mm), • A实-----室温下压铸件的实际尺寸(mm)。
一、压铸件的收缩率 • (二)计算收缩率
• A’-----计算得到的模具成型零件的尺寸(mm), • A-----压铸件的公称尺寸(mm)。
常用压铸合金的计算收缩率腔尺寸(包括型腔深度尺寸) ②型芯尺寸(包括型芯高度尺寸)
③成型部分的中心距离和位置尺寸
(一)成型尺寸的分类及计算要点
成型尺寸计算的要点: • 因型腔磨损后尺寸增大,故计算型腔尺寸时应使得压
铸件外形接近于最小极限尺寸。
• 因型芯磨损后尺寸减小,故计算型腔尺寸时应使得压
铸件内形接近于最大极限尺寸。
• 1.壳体压铸件的成型尺寸分类
压铸件的①、②、③属于型腔尺寸;④、⑤、⑥属于 型芯尺寸;⑦、⑧属于中心距离、位置尺寸。另外, ②、⑤受到分型面的影响,高压、高速的金属液充填 型腔时,闭合的动、定模会出现微小的分离倾向,使 与分型面有关的尺寸略微增大。为消除这种影响,通 常将计算所得的公称尺寸减去0.05mm。
第七章 成型零件和模架设计(P118)
• 成型零件是构成型腔以形成压铸件形状的零件。通常 浇注系统、溢流和排气系统也在成型零件上加工而成。 成型零件的结构、尺寸和质量直接影响着压铸件的精 度、质量和模型的寿命。
第7章成型零件及模架设计详述

成型尺寸的计算要点如下: ①型腔磨损后尺寸增大,计算型腔尺寸时应使压铸件外 形接近于最小极限尺寸。 ②型芯磨损后尺寸减小,计算型芯尺寸时应使压铸件内 形接近于最大极限尺寸。 ③两个型芯或型腔之间的中心距离和位置尺寸与磨损量 无关,应使压铸件尺寸接近于最大和最小两个极限尺寸的 平均值。
2.成型尺寸标注形式及偏差分布的规定 上述三类成型尺寸,分别采用三种不同的计算方法。
镶块壁厚尺寸推荐值见表7-7。
2.整体镶块台阶尺寸 整体镶块台阶尺寸推荐值见表7-8
3.组合式成型镶块固定部分长度 组合式成型镶块固定部分长度推荐值见表7-9
4.圆形型芯结构尺寸 圆形型芯结构尺寸推荐值见表7-10
7.2成型零件成型尺寸的计算 7.2.1压铸件的收缩率 1.实际收缩率
压铸件的收缩率是指室温时,模具成型尺寸与压铸件对 应尺寸的相对变化率。又称为实际收缩率。即
L模 L铸 100%
L模
常用压铸合金的计算收缩率见表7-11。
2.计算收缩率(室温下压铸件尺寸与模具尺寸的相对差值) 设计模具时,计算成型零件成型尺寸所采用的收缩率为
计算收缩率。它包括了压铸件收缩值及模具成型零件在工作 温度时的膨胀值,即
计
L模 L铸 L铸
100%
L模 L铸(1%)
3.收缩率的确定 压铸件的收缩率应根据压铸件的结构特点、收缩条件
φ50的尺寸要换算成单向公差尺寸,其结果是: 49.900.22
计算结果如下表:
序号 类别
压铸件 尺寸
计算公式
模具尺寸
1
型 径向 腔
500.10 0.32
2
尺 深度
寸
2000.12
50.0500.055
20.04
压铸模设计及成型零件制造工艺与压铸工艺设计
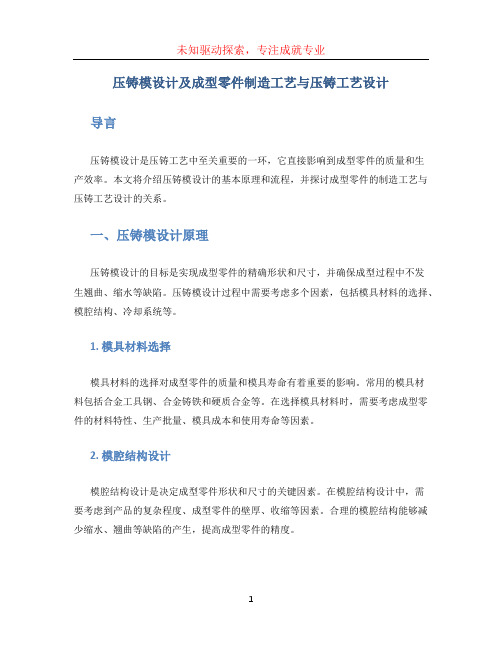
压铸模设计及成型零件制造工艺与压铸工艺设计导言压铸模设计是压铸工艺中至关重要的一环,它直接影响到成型零件的质量和生产效率。
本文将介绍压铸模设计的基本原理和流程,并探讨成型零件的制造工艺与压铸工艺设计的关系。
一、压铸模设计原理压铸模设计的目标是实现成型零件的精确形状和尺寸,并确保成型过程中不发生翘曲、缩水等缺陷。
压铸模设计过程中需要考虑多个因素,包括模具材料的选择、模腔结构、冷却系统等。
1. 模具材料选择模具材料的选择对成型零件的质量和模具寿命有着重要的影响。
常用的模具材料包括合金工具钢、合金铸铁和硬质合金等。
在选择模具材料时,需要考虑成型零件的材料特性、生产批量、模具成本和使用寿命等因素。
2. 模腔结构设计模腔结构设计是决定成型零件形状和尺寸的关键因素。
在模腔结构设计中,需要考虑到产品的复杂程度、成型零件的壁厚、收缩等因素。
合理的模腔结构能够减少缩水、翘曲等缺陷的产生,提高成型零件的精度。
3. 冷却系统设计冷却系统的设计对模具寿命和生产效率有着重要的影响。
合理的冷却系统能够快速降低模具温度,提高成型速度,减少成本。
冷却系统的设计需要考虑到模腔形状、成型零件的特性、模具材料等因素。
二、成型零件制造工艺与压铸工艺设计成型零件的制造工艺和压铸工艺设计是紧密相关的。
成型零件的制造工艺包括材料准备、熔炼、浇注、固化、清理等过程;而压铸工艺设计包括模具设计、模具制造、成型参数设置等过程。
1. 材料准备材料准备是成型零件制造工艺的第一步。
在压铸工艺中,常用的材料包括铝合金、锌合金、镁合金等。
材料的准备需要考虑到成型零件的要求和使用环境,选择合适的材料,并进行加热、熔化等处理。
2. 熔炼熔炼是将原材料加热至熔点并进行熔化的过程。
在熔炼过程中,需要控制温度、时间和熔炼速度等参数,确保材料的均匀性和纯度。
熔炼后的材料会通过浇注口注入压铸模中进行成型。
3. 浇注与固化浇注是将熔融的材料注入压铸模中的过程。
在浇注过程中,需要控制浇注速度、浇注压力和浇注位置等参数,以确保材料均匀填充模腔。
压铸型(模)设计
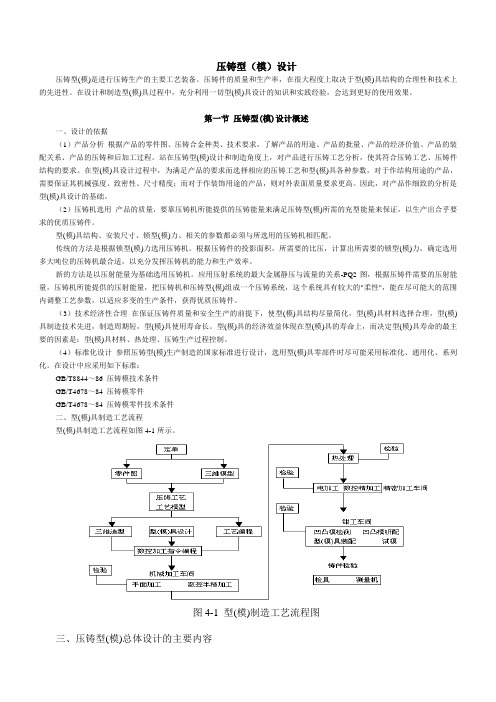
压铸型(模)设计压铸型(模)是进行压铸生产的主要工艺装备。
压铸件的质量和生产率,在很大程度上取决于型(模)具结构的合理性和技术上的先进性。
在设计和制造型(模)具过程中,充分利用一切型(模)具设计的知识和实践经验,会达到更好的使用效果。
第一节压铸型(模)设计概述一、设计的依据(1)产品分析根据产品的零件图、压铸合金种类、技术要求,了解产品的用途、产品的批量、产品的经济价值、产品的装配关系、产品的压铸和后加工过程。
站在压铸型(模)设计和制造角度上,对产品进行压铸工艺分析,使其符合压铸工艺、压铸件结构的要求。
在型(模)具设计过程中,为满足产品的要求而选择相应的压铸工艺和型(模)具各种参数,对于作结构用途的产品,需要保证其机械强度、致密性、尺寸精度;而对于作装饰用途的产品,则对外表面质量要求更高。
因此,对产品作细致的分析是型(模)具设计的基础。
(2)压铸机选用产品的质量,要靠压铸机所能提供的压铸能量来满足压铸型(模)所需的充型能量来保证,以生产出合乎要求的优质压铸件。
型(模)具结构、安装尺寸、锁型(模)力、相关的参数都必须与所选用的压铸机相匹配。
传统的方法是根据锁型(模)力选用压铸机。
根据压铸件的投影面积,所需要的比压,计算出所需要的锁型(模)力,确定选用多大吨位的压铸机最合适,以充分发挥压铸机的能力和生产效率。
新的方法是以压射能量为基础选用压铸机。
应用压射系统的最大金属静压与流量的关系-PQ2图,根据压铸件需要的压射能量,压铸机所能提供的压射能量,把压铸机和压铸型(模)组成一个压铸系统,这个系统具有较大的"柔性",能在尽可能大的范围内调整工艺参数,以适应多变的生产条件,获得优质压铸件。
(3)技术经济性合理在保证压铸件质量和安全生产的前提下,使型(模)具结构尽量简化,型(模)具材料选择合理,型(模)具制造技术先进,制造周期短,型(模)具使用寿命长。
型(模)具的经济效益体现在型(模)具的寿命上,而决定型(模)具寿命的最主要的因素是:型(模)具材料、热处理、压铸生产过程控制。
压铸成形工艺与模具设计
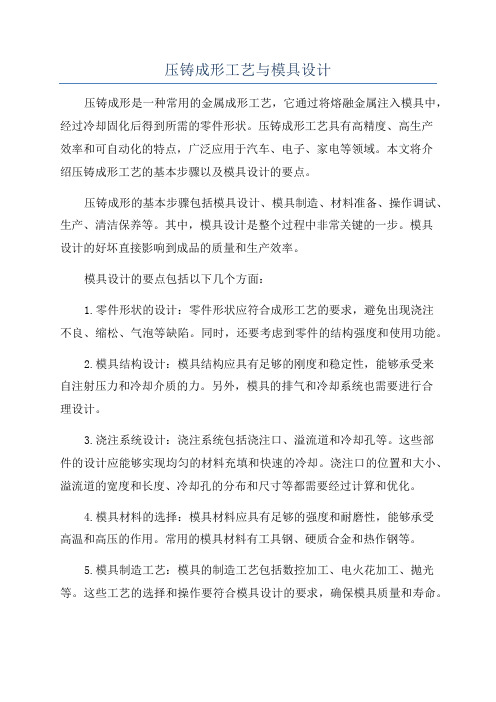
压铸成形工艺与模具设计压铸成形是一种常用的金属成形工艺,它通过将熔融金属注入模具中,经过冷却固化后得到所需的零件形状。
压铸成形工艺具有高精度、高生产效率和可自动化的特点,广泛应用于汽车、电子、家电等领域。
本文将介绍压铸成形工艺的基本步骤以及模具设计的要点。
压铸成形的基本步骤包括模具设计、模具制造、材料准备、操作调试、生产、清洁保养等。
其中,模具设计是整个过程中非常关键的一步。
模具设计的好坏直接影响到成品的质量和生产效率。
模具设计的要点包括以下几个方面:1.零件形状的设计:零件形状应符合成形工艺的要求,避免出现浇注不良、缩松、气泡等缺陷。
同时,还要考虑到零件的结构强度和使用功能。
2.模具结构设计:模具结构应具有足够的刚度和稳定性,能够承受来自注射压力和冷却介质的力。
另外,模具的排气和冷却系统也需要进行合理设计。
3.浇注系统设计:浇注系统包括浇注口、溢流道和冷却孔等。
这些部件的设计应能够实现均匀的材料充填和快速的冷却。
浇注口的位置和大小、溢流道的宽度和长度、冷却孔的分布和尺寸等都需要经过计算和优化。
4.模具材料的选择:模具材料应具有足够的强度和耐磨性,能够承受高温和高压的作用。
常用的模具材料有工具钢、硬质合金和热作钢等。
5.模具制造工艺:模具的制造工艺包括数控加工、电火花加工、抛光等。
这些工艺的选择和操作要符合模具设计的要求,确保模具质量和寿命。
总之,压铸成形工艺与模具设计是密不可分的,模具设计的好坏直接影响到产品的质量和生产效率。
要设计出性能良好的模具,需要综合考虑零件形状、模具结构、浇注系统、材料选择和制造工艺等方面的因素。
只有不断优化和改进,才能满足不同产品的要求,推动压铸成形工艺的发展。
压铸成型零件与模架设计

压铸工艺及模具设计
影响压铸件收缩率的因素较多,主要如下: (1) 铸件结构越复杂,型芯数量越多,收缩率就小,反 之收缩率就大。 (2) 薄壁铸件收缩率小,厚壁铸件收缩率大。 (3) 包住型芯的径向尺寸收缩受阻,收缩率较小,而轴 向尺寸收缩自由,收缩率较大。 (4) 浇注温度高时收缩率大,反之收缩率小。 (5) 有镶嵌件的铸件收缩率变小。 (6) 在模具中停留时间越短,脱模温度越高,铸件的收 缩率越大,反之收缩率则越小。 因此,要精确确定收缩率很困难,在计算成型尺寸时, 往往综合上述诸多因素的影响,选用综合收缩率进行计算, 可参考表6-2进行选取。
(1) 不通孔形式,套板结构简单,强度较高,可用螺钉 和套板直接紧固,不用座板和支承板。但当动、定模均为不 通孔时,对多型腔模具要保证动、定模镶块安装孔的同轴度 和深度尺寸全部一致比较困难。不通孔形式用于圆柱形镶块 或型腔较浅的模具,如为非圆形镶块,则只适用于单腔模具。
(2) 通孔形式,套板用台阶固定或用螺钉和座板紧固。 在动、定模上,镶块安装孔的形状和大小应一致,以便加工 和保证同轴度。
(3) 通孔台阶式用于型腔较深的或一模多腔的模具,以 及对于狭小的镶块不便使用螺钉紧固的模具。通孔无台阶式 用于镶块与支承板(或座板)直接用螺钉紧固的情况。
压铸工艺及模具设计
6.1.4 型芯的固定形式 型芯固定时,必须保持与相关构件
之间有足够的强度和稳定性,便于加工 和装卸,在金属液的冲击下或铸件卸除 包紧力时不发生位移、弹性变形和弯曲 断裂现象。型芯普遍采用台阶式固定 图6-4 型芯固定形式 方式。型芯靠台阶的支撑固定在镶块、滑块或动模套板内, 制造和装配比较简便,应用广泛。另外,台阶用座板压紧 后,适用于推板推出结构模具中的活动型心的使用,如图 6-4所示。
压铸模设计—第九章 成型零件和模架设计

2、镶拼式结构的缺点 、
增加装配时的困难, 增加装配时的困难,且难以满足较高的组合尺 寸精度; 寸精度; 模具的热扩散条件变差; 模具的热扩散条件变差; 镶拼处的缝隙易产生飞边, 镶拼处的缝隙易产生飞边,既影响模具使用寿 命,又会增加铸件去毛刺的工作量; 又会增加铸件去毛刺的工作量; 模具的热扩散条件变差。 模具的热扩散条件变差。
图9-5 通孔套板台阶固定形式
28
图9-6 通孔套板时镶块固定形式 1. 套板 2. 镶块 4. 导套
29
(2)通孔套板无台阶式固定形式
图9-7 通孔套板无台阶形式
30
五、型芯的结构和固定形式
(一)主型芯的结构及固定形式
图9-8 主型芯的结构和固定形式
31
(二)小型芯的结构及固定形式
图8-9 圆形小型芯的固定形式
底部受冲击较大的型芯
23
底部易弯曲或折断的型芯
24
6、不影响压铸件外观,便于去除飞边。 、不影响压铸件外观,便于去除飞边。
ቤተ መጻሕፍቲ ባይዱ
25
四、镶块的固定形式
1、不通孔的套板
图9-3 不通孔套板镶块固定形式
26
图9-4 不通孔套板时镶块固定形式 1. 套板 2. 镶块 3. 螺钉
27
2、通孔的套板 、
(1)通孔套板台阶式固定形式
(二)计算收缩率
设计模具时, 设计模具时,计算成型零件所采用的收缩率 为计算收缩率φ 为计算收缩率 ,它包括了压铸件收缩值和成型零 件在工作温度时的膨胀值, 件在工作温度时的膨胀值,即:
A′ − A ϕ= × 100% A
式中 A′—通过计算的模具成型尺寸(mm) A —压铸件的公称尺寸(mm)
41
第9章 压铸模成型零部件与模体设计
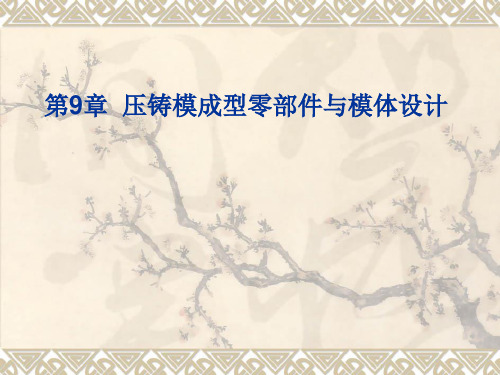
9.1.2 9.1.3 9.1.4 9.1.5
成型零件结构形式 镶拼式结构设计要点 成型零件的固定 成型零件结构尺寸 成型零件成型尺寸计算
9.1 成型零件结构设计
压铸模成型零件主要是指镶块和型芯。一般浇注系统、 溢流与排气系统也在成型零件上加工而成。这些零件直 接与金属液接触,承受着高速金属液流的冲刷和高温、 高压作用。成型零件的质量决定了压铸件的精度和质量, 也决定了模具的寿命。
9.1.5 成型零件成型尺寸计算
9.1.5 成型零件成型尺寸计算
2.影响压铸件精度的因素 压铸件尺寸精度受压铸件本身结构及合金材料、压铸工艺、压铸模设计制造、压 铸机性能等多方面的影响。确定成型尺寸时,应综合考虑各影响因素。 (1) 压铸件收缩率的影响 压铸过程中,合金的凝固收缩是影响压铸件尺寸精度的主要因素。对合金冷却 收缩的规律和收缩量掌握得越全面越准确,则计算出成型尺寸准确程度越高。 合金收缩过程可分三个阶段。第一阶段是液态收缩。由于金属液的过热度(超过 液相线的温度)一般都不高,所以这一阶段的收缩值不大。第二阶段是金属由液 态转变为固态的凝固收缩。这阶段的收缩值虽大,但因这个阶段是在模具中完 成的,受模具限制,自由收缩很困难,其收缩值在压铸件总收缩值中占的比例也 不是最大。第三阶段是压铸件随模冷却到开模脱出的固态收缩。开始收缩仍在 模具中,脱模后便处于自由收缩状态。这阶段收缩值的大小根据压铸件脱模时的 温度而定。压铸件脱模温度越高,收缩值越大。形状简单的、壁厚较厚的压铸件 收缩值比复杂的薄壁压铸件收缩值大。此外,收缩率在同一铸件的各个部位可能 是不同的。如压铸件包住型芯的径向尺寸收缩率小于轴向尺寸收缩率。又如在模 具中处于模温较高部位的收缩率就要大些。
- 1、下载文档前请自行甄别文档内容的完整性,平台不提供额外的编辑、内容补充、找答案等附加服务。
- 2、"仅部分预览"的文档,不可在线预览部分如存在完整性等问题,可反馈申请退款(可完整预览的文档不适用该条件!)。
- 3、如文档侵犯您的权益,请联系客服反馈,我们会尽快为您处理(人工客服工作时间:9:00-18:30)。
7.1 成形零件的结构形式
• 7.1.4
• • 1. • 模套组合式的结构形式如图7-7所示。 • 图7-7(a)所示的型腔外形结构比较复杂,采用整体结构很难加工,所
以将其分拆成几块镶件:底拼块1、端面拼块2和侧拼块3,分别加工 后,装入模板的模套4中, 组合成形腔,保证了成形件的精度,降低 了加工难度。
上一页 下一页 返回
7.1 成形零件的结构形式
• 7.1.3
• • 图7-4为局部组合式型腔的结构实例。 • 图7-4(a)为压铸件底部有较为复杂的成形形状,很难加工,因此在型
腔底部铣出形状简单的模套,将加工好的成形底芯压入,在背面用螺
• 图7-4(c)~(f) • 局部组合式型腔多用于局部形状较为复杂,整体加工较为困难的场合。
上一页 下一页 返回
7.1 成形零件的结构形式
• 图7-7(b)为直角型腔的拼接形式。 图7-7(c)是圆角型腔的拼接形式, 为避免明显的接缝痕迹,应将拼接处设在圆角的切点处。加工研合后,
• 图7-7(d) • 为了增强各拼块间相互拼接的强度和刚度,均采用T字槽的连接方式,
上一页 下一页 返回
7.1 成形零件的结构形式
• 图7-2(b)是模板用线切割机床,切割成贯通的模套,将矩形型腔镶块 从背面装入模框,并设置台肩,用螺栓固定在垫板上。
• 图7-2(c)是另一种组合形式,在模腔镶块中心用螺栓将其固定在垫板
上,为防止转动,需设置止转销。
上一页 下一页 返回
7.1 成形零件的结构形式
• 整体组合式型芯的基本结构和固定形式如图7-3 • 图7-3(a)是将模板加工成与型芯相对应的安装孔,采用H7/h6的
第7章 压铸模成形零件设计
• 7.1 成形零件的结构形式 • 7.2 成形零件的尺寸计算 • 7.3 成形零件的常用材料
7.1 成形零件的结构形式
• 7.1.1
• 型腔和型芯均由整块材料加工而成,即型腔或型芯直接在模板上加 工成形,如图7-1所示。图7-1(a)、(b)为整体式型腔结构,图7-1(c)为
上一页 下一页 返回
7.1 成形零件的结构形式
• 图7-5 • 图7-5(a)所示的压铸件的内腔为带有盲孔的凸台,通过局部镶拼的形
• 图7-5(b)是芯中镶芯的结构形式,将难于加工的部位分拆成几个容易
• 当成形细长的通孔时,为防止细成形芯受压射力的冲击而产生变形, 采用图7-5(c)所示的形式,将型芯固定在动模一侧,型芯的顶部插入 到定模板的通孔中,这样做除了加固型芯外,还起到为型腔排气的作
• • (1 • (2 • (3 • (4 • (5
下一页 返回
7.1 成形零件的结构形式
• 7.1.2
• 型腔和型芯由整块材料制成,然后装入模板的模套内,再用台肩或 螺栓固定。模套应采用圆形或矩形,以便于加工和装配。整体组合式 型腔的基本结构和固定形式如图7-2
• 图7-2(a)是将模板作成盲孔的模套,将型腔镶块整体嵌入,在其背面 用螺栓紧固。
配合精度,将型芯嵌入后,在背面用螺栓固定。 • 对于外部形状比较复杂的型芯,可采用图7-3(b)和图7-3(c)所示的结
构形式。用线切割机床将模套孔作成贯通的形式,用台肩或螺栓固定。 • 对于外部形状复杂的型芯,当现场没有电火花切割机床时,也可采用
7-3(d) 所示的结构形式,将型芯的固定部分改制成容易加工的 圆柱形或矩形凸台,在模板上加工出相应形状的模套孔,将型芯装入 模套孔后,从背面固定,必要时,可设置止转圆销。
上一页 下一页 返回
7.1 成形零件的结构形式
• 7.1.6
• 小型芯常用的固定形式如图7-9所示。 • 图7-9(a)、(b)采用的是台肩的固定形式。图7-9(c)所示是为了缩短型
芯的长度,在底部设置了圆柱销,将小型芯顶紧。这种形式多用在模
• 当模板较厚时,也可采用图7-9(d)所示的方式,用螺塞紧固。当型芯 成形面积较大时,可采用图7-9(e)所示的固定方式,即在型芯的背面 用螺栓固定。这两种固定方式可在省去垫板或不设垫板的情况下采用。
• 2. • 需要整体侧分型的压铸件,多采用瓣合式的组合形式。压铸模的型腔
往往由两瓣或多瓣成形体组合而成,如图7-8 • 图7-8(a) • 图7-8(b)为框架式结构的压铸件。当侧抽芯距离较大时,可在四边
采用瓣块组合形式。在斜销的带动下,分别从4式
• 7.1.5
上一页 下一页 返回
7.1 成形零件的结构形式
• 图7-5(d)和(e)是根据压铸件的特殊结构,采用局部组合形式的实例。 • 图7-5(f)是带六角孔的压铸件,在主型芯上镶入六角型芯。为了使用 • 遇有窄边的矩形孔,可采用图7-5(g)所示的方式,将其固定长度做得
短一些,以便于加工。
上一页 下一页 返回
7.1 成形零件的结构形式
• 图7-6 • 图7-6(a)~(c)都是局部结构较为复杂的压铸件。 • 图7-6(d)是在缺口处镶嵌一块突起的镶件,它的特点是制造简单,不
涉及型腔,但镶件与型腔形成一个垂直的擦合面,如果处理不好,会
• 图7-6(e)是在动模板上紧靠主型芯镶嵌一个贯通的型芯,在型腔相对 应的部位,做一个与型芯相互配合的缺口,缺口应有5°左右的斜接 触面,并应研合良好,以防溢料。
• (1 • ① 将组成成形空腔的各部分分解成若干个独立的镶块,简化加工工
• ② 各组合件均可采用机械加工,特别是在淬硬处理后可采用高精度 的磨削加工,保证了各部分的精度要求,提高了成形零件的使用寿命。
• ③ 提高机械设备的利用率,减少了繁重的人工工作量,从而相应提 高了生产效率,降低了做模成本。
上一页 下一页 返回
7.1 成形零件的结构形式
• ④ 有利于沿脱模方向开设脱模斜度,方便研磨,保证了成形零件的 • ⑤ 拼合面有一定的排气作用。必要时也可在需要的部位另外开设排 •⑥ • ⑦ 当易损的成形零件失效时,可随时修理或更换,不至于使整套模 •⑧
上一页 下一页 返回
7.1 成形零件的结构形式
• (2 • ① 具有过多的镶块拼合面,难以满足组合尺寸的配合精度要求,增 • ② 镶拼处处理不当,会引起缝隙飞边,增加压铸件去除毛刺的工作 •③