3成型零部件结构设计
热成型零部件设计规范
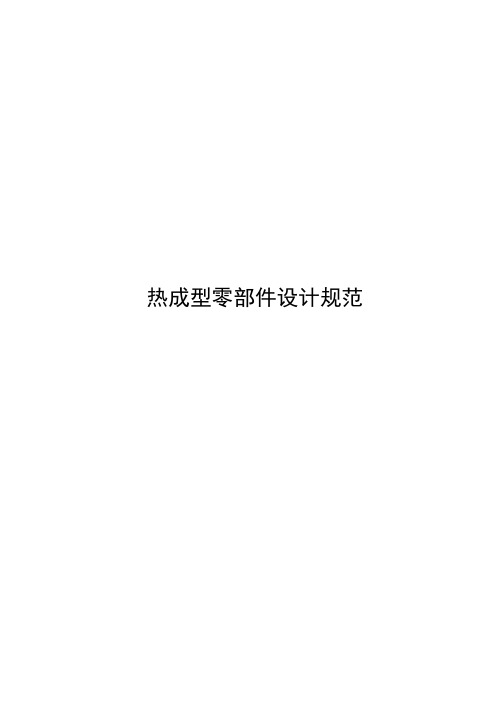
热成型零部件设计规范1. 概述1.1 规范的主要目的通过本次对热成型技术设计规范的整理和总结,梳理出热成型技术的结构设计共性和规范要求,引导热成型零部件的结构设计,满足产品质量要求。
降低产品设计过程中失误,达到提升产品品质目的。
1.2 规范的主要内容该规范主要针对公司现有车型的热成型技术开发过程中的知识积累和概括,为今后开发车型提供设计指导,通过规范热成型零部件的设计注意事项、结构设计一般性流程,设计校核及实验要求等,系统、全面地检查热成型零部件在设计阶段可能存在的问题,做到及早发现,及早整改。
2. 适用范围及规范性引用文件2.1范围本规范规定了汽车热成形零部件采用板材的分类和结构设计注意事项、技术要求、检验和试验等。
本规范适用于汽车汽车部件应用热成形钢板材料。
2.2规范性引用文件下列文件中的条款通过本标准的引用而成为本标准的条款。
凡是注日期的引用文件,其随后所有的修改单(不包括勘误的内容)或修订版均不适用于本标准,鼓励根据本标准达成协议的各方研究是否可使用这些文件的最新版本。
凡是不注日期的引用文件,其最新版本适用于本标准。
GB/ T 222 钢的化学分析用试样取样法及成品化学成分允许偏差GB/ T 223 钢铁及合金化学分析方法GB/ T 224 钢的脱碳层深度测定法GB/ T 228 金属材料室温拉伸试验方法GB/ T 4340 金属维氏硬度试验GB/ T 8170 数值修约规则GB/ T13298 金属显微组织检验方法GB/ T13299 钢的显微组织评定方法Q/ZTB 07.025 禁用物质Q/ZTB 07.008 金属材料取样标准3.术语和选材规格3.1 热成型热成型是把钢板加热到900℃左右的奥氏体区进行冲压成形,通过制件在冲压金属模内冷却淬火强化的一种成形工艺。
3.2 热成型钢热成形钢是一种低碳合金钢,含有一定量的锰、硼为主的合金元素,具有良好的热处理性能,可以通过直接热冲压成形或先预成形再热冲压成形同时模具内淬火,从而获得高强度。
阀门三维参数化建模与仿真分析

cnei pr e rbte m ico i to a e b ad t rnto ovro a m ts e a orn e s m l n prco i e sn a e e n n d a f e a o d a f w s p sIo ets u t p a eim dl h h e c fm a ri l a . r r t h am t oe w i h l il e ea e t r n o p r r d e e c s c a o ar v g a n lb d m ln, e c pt rt e etl s m t d aot tdf e o i t aie fwa h s nai aad h s uhw en d g h r l u o d s i d n e o b o o i t r e e cnt coapr e r osutnl m ts r i a e. a Te nl y iu r i a be ape i n si ds n t ho g o vt l l hs n ld i url i ad h e o f a e t c r a y e p i n ta eg n d p dco cm r e ilTi e nl y b n oltno i t w y r u i o p hnv y h tho g h e nt r s r n h a o tn e se. c o a e o n a fm g s s y e ad s e o ds n u ao a i t ee o p dco. s c n cndr eg, t avn n h fc f utn T iaie o i f i b l d c g s e t r i h r l o t ie a t thi e aes s t a ei, d iitttg ng t h e n ucacrt a uv ul t a v mte n, t re c q h tii b i r l e r c o r a y n i a ei t a s r o m n t p b m ot t un t thi e v t l i 让t e m ed r l a uhw sg e n u o i ar l c h o e b o o h c q f u e t h e i e r ay e p c s dsi dsn n hw uu t iitn em nf p dc r e oi url g, d tpt e ao epr e o r ut o s f t e a o o p mti x i t o . n a i h r Tiaie us iu o oei se cne ec o vl , d tc h rc d cs t s e pn g s ovr ne a e a p r t s l i t s h s f n t s g e r n v n r a o t g p ooei se cne ec, d dy ccle u e h h r h pn g s ovr ne n m i t au tf m l o t e f n t s g a o f h l a o a f a r e r e m s ts Ia i n haie t eeu y s e c vtog t o se . di , r lg h fc a p s ra u e uh t sn t t t e e t l r u n r h r d o e c t e d r h e iitttg mte i . a en s Ky r : e Pr eim d i , e i dv, sm l V t l e w d Vl , a t oen Dmno re As b , u os a v am r c lg i sn i e y ia r
模具基本结构简介之三板模

三板模的特点在于其多了一块第 三板,可以方便地实现侧向分型 和抽芯,适用于复杂形状的塑料 件生产。
三板模的应用范围
三板模广泛应用于各种塑料制品的生 产,如家电、汽车、日用品等领域的 塑料零部件。
由于其结构特点,三板模适用于形状 复杂、有侧孔或侧向凸出的塑料制品 生产。
三板模的历史与发展
三板模的历史可以追溯到上世纪末, 随着塑料工业的发展,三板模逐渐得 到广泛应用。
模具的顶出与取
顶出
当塑件冷却完成后,模具的上模部分开始向上运动,同时顶出杆推动中间板向上运动,将塑件从下模 中顶出。
取出
在顶出过程中,塑件会随着顶出杆从下模中移出。操作员可以轻松地取出塑件,进行后续处理或检查 。
04
三板模的制造工艺及要点
制造工艺流程
备料
根据模具设计要求, 准备所需材料,如钢 材、铝合金等。
粗加工
对备好的材料进行粗 加工,包括铣削、钻 孔等。
热处理
对粗加工后的模具零 件进行热处理,以改 善其机械性能。
精加工
对热处理后的零件进 行精加工,如磨削、 抛光等。
组装与调试
将所有零件组装成模 具,并进行调试,确 保其工作性能。
成型零件的加工要点
01
02
03
粗加工时留有余量
在粗加工阶段,应留有一 定的余量,以便后续精加 工时调整。
THANKS
谢谢您的观看
控制冷却时间
根据产品成型工艺要求,合理控制冷却时间,以确保模具及时冷 却到适宜的温度。
顶出系统的设计要点
合理选择顶出方式
根据产品形状和模具结构 ,选择合适的顶出方式, 如机械顶出、气动顶出等 。
确定顶出位置
根据产品脱模要求,确定 顶出位置,确保产品顺利 脱模。
3 结构设计方法

作用按随空间位置的变异分类: : 固定作用: 固定作用:在结构上具有固定分布的作用 自由作用: 自由作用:在结构上一定范围内可以任意分布的 作用 作用按结构的反应特点分类: : 静态作用: 静态作用:使结构产生的加速度可以忽略不计的 作用 动态作用: 动态作用:使结构产生的加速度不可忽略不计的 作用
2 + R 2 S
σ= σ σ Z
结构可靠指标 β
µ Z = µ R −µ S β= 2 2 σZ σR +σS
表3 —2
可靠指标β 与失效概率P f 的对应关系 与失效概率
2.7 3.5×10 × 3.2 3.7 4.2
β值
失效概率P f
-3
6.9×10 ×
-4
1.1×10 ×
-4
1.3×10 ×
3.1.1 结构的功能要求
安全性、适用性、 安全性、适用性、 耐久性
《标准》规定结构在规定的设计使用年限内应满足下列 功能要求: 在正常施工和正常使用时, 在正常施工和正常使用时,能承受可能出现的各种作用 在正常使用时具有良好的工作性能 在正常使用时具有良好的工作性能 在正常维护下具有足够的耐久性能 在正常维护下具有足够的耐久性能 在设计规定的偶然事件发生时及发生后,仍能保持必要 在设计规定的偶然事件发生时及发生后,仍能保持必要 的整体稳定性 结构在规定的使用期限内,在规定的条件下(正常设计、 结构在规定的使用期限内,在规定的条件下(正常设计、 正常施工、正常使用和维护),完成预定功能的能力, ),完成预定功能的能力 正常施工、正常使用和维护),完成预定功能的能力,称 结构的可靠性。 为结构的可靠性。
由可变荷载效应控制的组合对于一般排架框架结构可采用下列简化的组合一般情况下可取090当只有一个可变荷载时取10材料强度指标的取值原则按承载力极限状态设计时材料强度指标取设计值按正常使用极限状态设计时材料强度指标取标准值规范规定材料强度的标准值应不小于95保证率的强度值钢筋抗拉强度标准值有明显屈服点的热轧钢筋是以钢材出厂的废品限值作为钢筋强度的标准值其值保证率约为9773即相当于平均值减去二倍的标准差没有明显屈服点的钢筋取085b作为钢筋强度的标准值混凝土强度等级根据150mm的立方体标准试件按照标准养护和试验方法测得的具有95保证率的抗压强度cucucucu规范规定钢筋混凝土结构的混凝土强度等级不应低于c15当采用hrb335级钢筋时混凝土强度等级不宜低于c20当采用hrb400和rrb400级钢筋以及承受重复荷载的构件混凝土强度等级不得低于c30当采用钢绞线钢丝热处理钢筋作预应力钢筋时混凝土强度等级不宜低于c40混凝土的轴心抗压强度标准值规范假定混凝土的轴心抗压强度与相应混凝土强度等级的立方体强度具有相同的变异系数
塑胶件的结构设计(提纲)
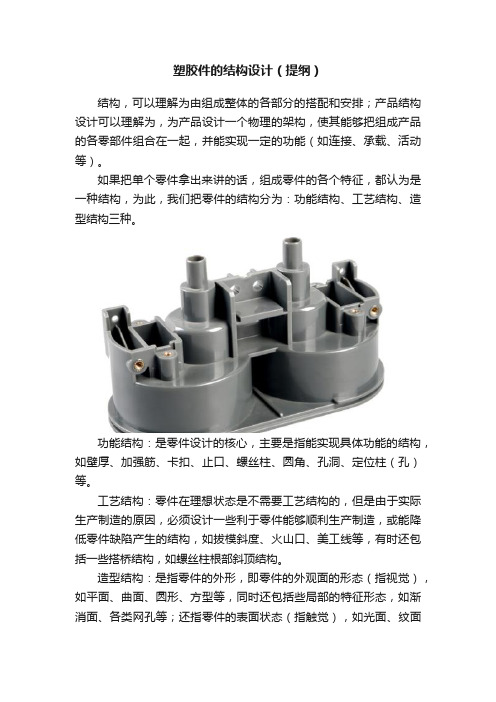
塑胶件的结构设计(提纲)结构,可以理解为由组成整体的各部分的搭配和安排;产品结构设计可以理解为,为产品设计一个物理的架构,使其能够把组成产品的各零部件组合在一起,并能实现一定的功能(如连接、承载、活动等)。
如果把单个零件拿出来讲的话,组成零件的各个特征,都认为是一种结构,为此,我们把零件的结构分为:功能结构、工艺结构、造型结构三种。
功能结构:是零件设计的核心,主要是指能实现具体功能的结构,如壁厚、加强筋、卡扣、止口、螺丝柱、圆角、孔洞、定位柱(孔)等。
工艺结构:零件在理想状态是不需要工艺结构的,但是由于实际生产制造的原因,必须设计一些利于零件能够顺利生产制造,或能降低零件缺陷产生的结构,如拔模斜度、火山口、美工线等,有时还包括一些搭桥结构,如螺丝柱根部斜顶结构。
造型结构:是指零件的外形,即零件的外观面的形态(指视觉),如平面、曲面、圆形、方型等,同时还包括些局部的特征形态,如渐消面、各类网孔等;还指零件的表面状态(指触觉),如光面、纹面等。
在之前文章有提到,本年度主要分享结构设计的知识多一些,以上就是需要介绍的主题提纲,即由功能结构、工艺介绍、造型结构组成的零件的结构设计。
需要声明的是,是以塑胶件的角度进行介绍,其他诸如压铸件,结构上虽与塑胶件有很大相似之处,但咱不做具体的分析介绍。
以上一些列的结构知识基本上囊括了一件塑胶零件的结构设计内容,(注意:特指结构,不包含CMF相关的内容)。
所以,大家可以随意拿出一件塑胶零件,仔细观察,零件的结构基本都可以从上面提到的三种结构分类找到具体的结构。
大家不要误解零件的结构就是产品的结构,实际上,产品的具体结构设计的内容不单单是零件的结构,还应包括零件之间的分配关系(即拆件)以及配合关系(即装配),这部分内容留到以后介绍,(注意:两个零件通过有些配合关系可视为一个零件,如双色件)。
可能有些小伙伴会问,这些内容太基础了,很多资料网上都有,甚至其他公众号都有相对应的介绍。
电脑键盘按键注塑模具设计【键盘键帽注塑模】
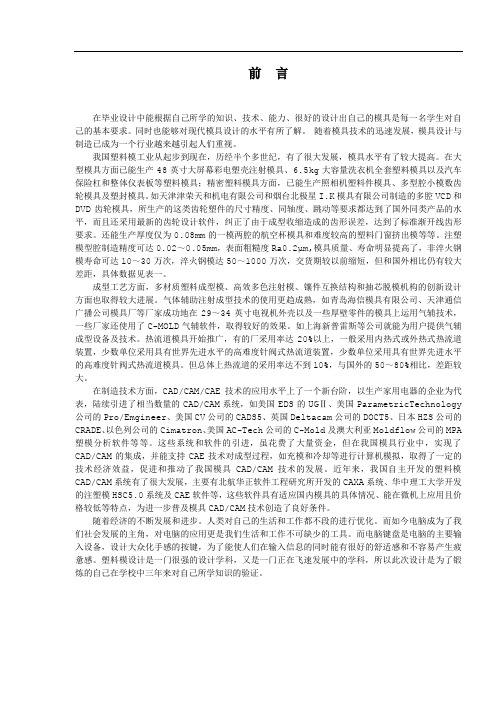
前言在毕业设计中能根据自己所学的知识、技术、能力、很好的设计出自己的模具是每一名学生对自己的基本要求。
同时也能够对现代模具设计的水平有所了解。
随着模具技术的迅速发展,模具设计与制造已成为一个行业越来越引起人们重视。
我国塑料模工业从起步到现在,历经半个多世纪,有了很大发展,模具水平有了较大提高。
在大型模具方面已能生产48英寸大屏幕彩电塑壳注射模具、6.5kg大容量洗衣机全套塑料模具以及汽车保险杠和整体仪表板等塑料模具;精密塑料模具方面,已能生产照相机塑料件模具、多型腔小模数齿轮模具及塑封模具。
如天津津荣天和机电有限公司和烟台北极星I.K模具有限公司制造的多腔VCD和DVD齿轮模具,所生产的这类齿轮塑件的尺寸精度、同轴度、跳动等要求都达到了国外同类产品的水平,而且还采用最新的齿轮设计软件,纠正了由于成型收缩造成的齿形误差,达到了标准渐开线齿形要求。
还能生产厚度仅为0.08mm的一模两腔的航空杯模具和难度较高的塑料门窗挤出模等等。
注塑模型腔制造精度可达0.02~0.05mm,表面粗糙度Ra0.2μm,模具质量、寿命明显提高了,非淬火钢模寿命可达10~30万次,淬火钢模达50~1000万次,交货期较以前缩短,但和国外相比仍有较大差距,具体数据见表一。
成型工艺方面,多材质塑料成型模、高效多色注射模、镶件互换结构和抽芯脱模机构的创新设计方面也取得较大进展。
气体辅助注射成型技术的使用更趋成熟,如青岛海信模具有限公司、天津通信广播公司模具厂等厂家成功地在29~34英寸电视机外壳以及一些厚壁零件的模具上运用气辅技术,一些厂家还使用了C-MOLD气辅软件,取得较好的效果。
如上海新普雷斯等公司就能为用户提供气辅成型设备及技术。
热流道模具开始推广,有的厂采用率达20%以上,一般采用内热式或外热式热流道装置,少数单位采用具有世界先进水平的高难度针阀式热流道装置,少数单位采用具有世界先进水平的高难度针阀式热流道模具。
但总体上热流道的采用率达不到10%,与国外的50~80%相比,差距较大。
钣金件结构设计知识

钣金件结构设计知识钣金件是一种广泛应用于机械制造领域的零部件,其结构设计对于产品的质量和性能具有重要影响。
以下是钣金件结构设计的相关知识。
一、结构设计原则1.符合功能要求:结构设计应符合产品的功能要求,例如强度、刚度、密封性等。
同时要考虑到产品的使用环境和工作条件,确保产品的可靠性和稳定性。
2.简化结构:结构设计应尽量简化,减少部件的数量和复杂性。
简化结构可以降低制造成本、提高生产效率,并且更容易进行维修和维护。
3.优化工艺:结构设计应考虑到钣金件的生产工艺特点,设计合理的连接方式、成形工艺和加工工艺,以便提高产品的制造质量和效率。
4.方便装配:结构设计应考虑到钣金件的装配方式和步骤,尽量减少装配难度,提高装配速度和准确性。
5.考虑材料特性:结构设计应充分考虑所选用材料的特性,例如强度、刚度、韧性、耐腐蚀性等,以确保产品在使用过程中不会出现材料失效。
二、常见结构设计要素1.板件形状:钣金件往往由平面板件构成,其形状通常为矩形、圆形、椭圆形等,应根据产品的实际要求合理选择板件形状和尺寸。
2.连接方式:钣金件的连接方式有很多种,常见的有焊接、螺栓连接、铆接、槽连接等。
连接方式的选择应根据产品的要求和钣金件的特性进行合理选择。
3.折弯方式:钣金件的折弯方式直接影响到产品的结构和外观质量。
常见的折弯方式有V形折弯、U形折弯、Z形折弯等,根据不同材料的特点选择合适的折弯方式。
4.强度增强结构:一些情况下,为了提高钣金件的强度和刚度,需要采用一些强度增强结构,如加强筋、折边、加强块等,以增加钣金件的强度和刚度。
5.表面处理:钣金件的外表面往往需要进行一定的处理,例如喷涂、电镀、防腐处理等。
结构设计应考虑到表面处理的要求和方法,以确保产品具有良好的外观和耐腐蚀性。
三、常见结构设计问题1.焊接变形:焊接过程中,钣金件往往会发生变形,导致结构不稳定或不符合要求。
为了解决这个问题,可以在设计阶段考虑到焊接变形的因素,合理选择焊接顺序和焊接位置,使用适当的辅助工具和夹具。
机械零部件的结构设计与分析

机械零部件的结构设计与分析简介:机械零部件的结构设计与分析是现代机械工程中一个重要的课题。
通过对机械零部件的结构进行合理的设计和分析,能够提高机械产品的性能和质量,同时降低制造成本和维修难度。
本文将从机械零部件的结构设计流程、结构设计基本原则、结构分析方法等方面进行讨论,希望能够对读者在机械零部件的结构设计与分析方面有所启发。
一、机械零部件的结构设计流程机械零部件的结构设计流程通常可以分为三个阶段:需求分析、概念设计和详细设计。
1. 需求分析:在需求分析阶段,设计师需要明确零部件的功能要求、工作环境、使用寿命等相关因素。
通过对这些需求的分析,可以确定零部件的基本结构形式和性能指标。
2. 概念设计:在概念设计阶段,设计师根据需求分析的结果,进行初步的结构设计。
这个阶段的关键是创新和选择,设计师需要结合自己的经验和创造力,找出不同的设计方案,并进行评比。
最终选择出一个相对合理的概念设计方案,作为后续详细设计的基础。
3. 详细设计:在详细设计阶段,设计师需要对概念设计方案进行细化和优化。
包括确定零部件的具体尺寸、材料和工艺要求等。
同时还需要进行一些结构分析,确保设计的可行性和合理性。
在详细设计完成后,还需要进行样机制造和测试,对设计进行验证和修正。
二、结构设计的基本原则在机械零部件的结构设计过程中,需要遵循一些基本原则以确保设计的可靠性和高效性。
1. 简洁性:结构设计应该尽量简洁,避免多余的复杂性。
简洁的设计不仅能够降低制造成本,还可以减少零部件的运动摩擦和能量损失,提高机械系统的传动效率。
2. 刚度与强度:结构设计应该具备足够的刚度和强度来承受工作负荷和环境力学影响。
设计师需要根据不同工况和材料的特性,选择合适的截面形状和尺寸以及合理的加工工艺,确保零部件在工作中不会出现过大的变形和破坏。
3. 可制造性:结构设计应该符合现有的加工工艺和设备能力。
设计师需要考虑到工艺的可行性,减少加工难度和成本。
同时,还应该注意材料的可获得性和成本,选择合适的材料以满足设计的要求。
- 1、下载文档前请自行甄别文档内容的完整性,平台不提供额外的编辑、内容补充、找答案等附加服务。
- 2、"仅部分预览"的文档,不可在线预览部分如存在完整性等问题,可反馈申请退款(可完整预览的文档不适用该条件!)。
- 3、如文档侵犯您的权益,请联系客服反馈,我们会尽快为您处理(人工客服工作时间:9:00-18:30)。
模腔布置-六腔模具
塑料成型模具
圆形和矩形布置皆可,下图皆为矩形布局。哪种最好 ?
模腔布置-三十二腔模具 塑料成型模具
模腔数是4的倍数 (最好为8的倍数) 的通用模腔布局。
将一个线性和H形流道配合使用,对太多腔就可以不用考 虑平衡的问题了。
三板式模腔布局
塑料成型模具
特点
模腔间可以相互紧靠着排列,因为不用安排主 流道各分流道。但还是考虑冷却水道、模具型 芯和顶杆位置等因素。
与二板式模具相比,在模腔数相同时,应该有 更短的流道长度。
排气道:W=5mm, DC=1mm,面积: 3.4mm2。
则至少需要的排气道数 =6.28/3.4=2
排气杆设计
塑料成型模具
排气镶件设计
塑料成型模具
多孔金属排气
塑料成型模具
注意:强度差;导热 性,过热易溢料;孔 易堵塞;表面粗糙, 可能在制品表面留下 粗糙痕迹。
负压及真空排气
塑料成型模具
流道排气
靠破孔的处理方式
放大后
塑料成型模具
型腔侧
PL面 型芯侧
红色线所示为分模 线﹐型腔型芯在此 靠破
靠破孔的处理方式
塑料成型模具
定模
侧面插破
动模
侧面靠破孔:插破面上必须做角度﹐且角度 越大越好﹐原则上拔模段差min=0.1mm。
筋处镶件的处理方式
十字筋处由于 筋较深﹐一般 为电加工﹐加 工难度大﹐易 造成工件异 常﹐将其拆成 镶件可方便加 工﹐缩短加工 周期﹐常见的 有以下几种组 合方式﹕
分型面塑料成型模具来自分型面设计很重要除了考虑模具整体结构外, 还要考虑钳工装配。
设计分型面时须检查:
分型面位置 分型面定位 分型面是否有尖角
分型面不能影响制品外观
塑料成型模具
通常的分型面位置
分型面不能影响制品外观
塑料成型模具
如果不能满足用户要求,再 好的模具设计也无用
用户要求的分型面位置
模具设计的分型面位置
塑料成型模具
分型面设置例子(滑雪靴)
滑雪靴上压板
Shoes High_back
排气槽设计
塑料成型模具
目的:将型腔内的气体顺利、完全地排出。 以免制品上有气孔、接缝、被烧焦、型腔不 能被充满。另外,气体不能被排出,产生很 高的型腔压力使充模速率降低。
尽量利用现成的间隙(分型面、顶出系统的配合 间隙、活动型芯与型芯孔配合间隙等)来排气。 否则必须另外设计排气措施。
塑料成型模具
槽深取0.01~0.015mm,槽宽1.5~6mm。尽量设计大些,对 不同的塑料品种,以不大于相应的溢料间隙为原则。比 如:ABS、HIPS、PC、PMMA、SAN取0.03~0.08mm, PE、PP、PA等取 0.02~0.03mm。
出口不要朝向操作工人一侧,以免塑料喷出发生事故。 排气槽弯曲渐宽以减小塑料冲出时的动能。
模腔布置-四腔模具
塑料成型模具
浇口开在宽边还是窄边取决于制品, 易于加工,只在X、Y轴变化。
流道短且轻
矩形布置的结构较紧凑
模腔布置-四腔模具
塑料成型模具
浇口开在宽边还是窄边取决于制品 此圆形平衡布局的H值都要比矩形布置的大
塑料成型模具
模腔布置-基数腔模具
➢5和9腔一般只能用圆形布局,可用热流道也 可用冷流道。分流道成辐射状与制品型腔相连, 这与一模三腔的结构相似。
较好,结构上 的平衡流道
比C好,流动 方向变化少些
流动方向变化 较多
模腔布置-八腔模具
圆形布局,流道短但 型腔数量受到限制,且
须用极坐标
矩形布局,可用方便的 X、Y坐标
塑料成型模具
分流道
主流道
模腔布置-八腔模具
塑料成型模具
比B的布局要好,但 各腔的流动有差别
比A差一些,但各腔的 流动在结构上完全平衡
一般筒形薄 壁制品
形状复杂的 多型芯制品
小型芯厚壁 芯制品
内有管状无螺 纹嵌件的制品
分型面设计
塑料成型模具
如果制合件的理同心度要求较高,哪个不设合计理合理?
原则:对一制件同心度要求高的部分最好皆设在动模 或定模(比如双联齿轮等),否则要很好地定位。
型腔侧 PL面
型芯侧
分型面设计
此设计有什么问题?
分型面形状可为平面或曲面,分型面可 垂直于(常用)、平行于或倾斜于开模 方向,或成阶梯状(难点)。
分型面
塑料成型模具
一般原则:
不影响制品外观 有利于制品尺寸精度 有利于模具加工,特别是型腔加工 有利于浇注系统、冷却系统和排气系统 有利于制品脱模(一般留于动模) 有利于镶嵌件的安装 由客户确定分型面位置,否则由设计人员 决定。
合理
分型面设计
塑料成型模具
有侧凹或侧孔的制品,抽拨距离小的作为侧 分型,抽拨距离长的作为主分型。(液压抽 芯除外)
投影面积大的作为主分型面,投影面积小的 作为侧分型面,以减小对锁紧楔的压力。
尽量将侧向分型抽芯机构放在动模一侧,以 简化模具的结构,抽拨距也可以更长。
如果利用分型面来排气,则分型面应设计在 料流的末端。
塑料成型模具
模腔布置-十六腔模具
最好的布局
A和B都是常用的布局形式
也可用A中的 X形分流道
模腔布置-二十四腔模具 塑料成型模具
什么作用?
与左图类似, 但末端为X分布
模腔布置-三十二腔模具 塑料成型模具
一般只用这种平衡布局方式,对细长制品,可用线性非 平衡式布局。图中红色表示可用X布局代替H型布局。 设计人员应尽量将流道设计成均衡的矩形布局,一般投 影面积的长边不要超过短边的2倍。
对多腔模而言,如果要节约空间可用蜂窝形布 局。
平衡式布局是期望的目标,但并不是绝对必须。
模腔布置-三腔模具
塑料成型模具
与两板式模具型腔布局相似,只是更紧凑些。
模腔布置-四腔模具
塑料成型模具
与两板式模具型腔布局相似,甚至可以更紧凑 些。也可以用H型布局,但没必要,因为流道 与制品不在一个面上,X型布局是最好的。
对左图的32腔,其长宽比有点太悬 殊了,可用右图的34腔来代替。
分型面
塑料成型模具
分型面:为了将制品及凝固的流道从模 腔中取出,模腔必须能夠分成两个或者 是多个主要的部分。这些可以分离部分 的接触表面,通称为分模面(PL面)。
分型面数量可以有一个(常用)或多个, 动定模之间的分型面为主分型面,其它 为次分型面。
模腔布置-双腔模具
塑料成型模具
哪一种更好?
t
2S a
t : 制品落下时间, s
S : 制品落下距离, m
a : 重力加速度, m / s2
比如:一制品成型周期3秒,每分钟成型20次,如 果每次制品下落时间少0.15,则每分钟可多注射一次, 提高效率5%。
模腔布置-三腔模具
塑料成型模具
仅为制品下落时间不同的差别。 只有圆形平衡布局,一般无矩形布置方式。
塑料成型模具
成型零部件结构设计
重点、难点
• 重点:
• 型腔布置方式 • 分型面确定方法 • 设计排气槽的目的 • 常用的组合式型芯和型腔设计原则
• 难点:
• 组合式型腔设计
塑料成型模具
成型零部件设计
成型零部件是指构成模 具型腔的所有零件。
型腔(凹模、母模) 型芯(凸模、公模) 成型杆、成型环 镶嵌件
塑料成型模具
此处只有用电加工,且制 品顶出困难,故不合理
分型面设计
塑料成型模具
型腔侧 PL面
型芯侧
将PL面设计在开口处, 便于加工,顶出容易。
分型面设计
塑料成型模具
哪一个设计合理?
可能需要用电加工
小型芯外形磨削即可
分型面设计
塑料成型模具
不合理
此面咬花或者抛光困难
分型面设计
塑料成型模具
此面容易咬花或者抛光
塑料成型模具
两板式模腔布置
单腔模具
塑料成型模具
中心开口制品的边缘浇口单腔模具
浇口数量任意,但要考虑熔结缝的数量和强度
模腔布置-单腔模具
塑料成型模具
中心无开口的投影连续制品用中心浇口(三板 式点浇口或两板式主流道型浇口)
如果用两板式边缘浇口,则造成模具偏心。可 在型腔对称位置加压力垫块,或其它方式?
塑料成型模具
型腔底部排气
塑料成型模具
常见分型面处理方式
1﹑平面分型面的选取
塑料成型模具
若 PL 面 与 开 模方向垂直﹐ 则可直接延伸 成PL面
常见分型面处理方式
2﹑斜面PL面的选取
塑料成型模具
型腔与型芯在红色点处相 接﹐容易在制品边沿产生 毛边(不合理)
哪一个设计合理?
型腔型芯直接在斜面上靠 破﹐彼此之间会产生错位 (不合理)
矩形布置的两种方式,哪种布局更好? 另一种矩形布局是在上面基础上旋转90度。
模腔布置-八腔模具
塑料成型模具
流道完全平衡, 但流道最长
流道差异小,在 高速注射时完全 可忽略此差别
流道的平衡度最 差,但流道最短
细长制品的矩形布置方式
塑料成型模具
模腔布置-十二腔模具
不可取,与F几乎无 差别,且F更简洁。
排气槽位置:料流的末端,一般在凹模上。
当制品设计不合理时,很难解决排气的问题。
塑料成型模具
排气槽设置例子(滑雪靴)
扣件
塑料成型模具
排气槽设置例子(滑雪靴)
塑料成型模具
排气槽设置例子(滑雪靴)