什么是真空热处理
浅谈真空热处理
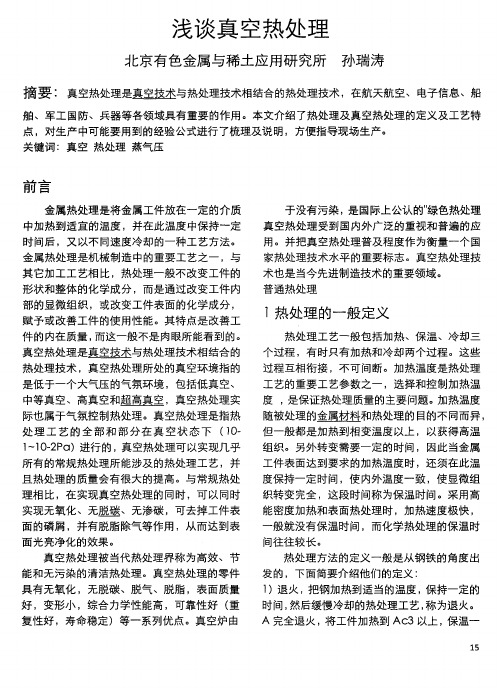
时 间 ,使 钢 中的碳 化 物 变成球 状 的退 火 方法 ; 1) 表 面淬 火 :表 面淬 火 是将 钢 件 的表 面 淬 透到
C 去应 力退 火 ,将 钢加 热到 略 低于 A1的一 定 一 定 深 度 ,而 心部 仍保 持 未 淬 火状 态 的一 种淬
温 度 ,保 温 后缓 慢 冷 却的 退 火方 法叫 做 去应 力 火 方法 ;A 感应 淬 火 ;
15
定 时 间 ,使 其 完全转 变 为奥 氏体 并 均 匀化 然后 B中温 回火 (回火 温度 250~500℃ ):
缓慢 冷却 的退 火 方法 ,叫完全 退 火 ;
C 高 温 回火 (回火温 度 500~600℃ )。
B球 化退 火 ,将 钢加 热 到 Ac3以 上 ,保 温一定 表面 热处 理
保 温后 缓冷 的 工艺 过程 。
2)化 学 热处 理 :将工 件 置于 一定 温 度的 活体 介
2) 正 火 ,将 钢 加 热 到 Ac3 或 Accm 以 上 质 中保 温 ,使 一 种或 几 种 元素 渗人 其 表 面层 ,
(30 ̄50℃ )。C,保 温 后在 空气 中冷 却 的热 处理 以改 变表 面 层 的化 学成 分 、组 织 和性 能 的热 处
真 空 热 处理 被 当代 热处 理界 称 为 高效 、 节 能 和 无 污染 的清 洁 热处理 。真 空热 处理 的零件 具有无氧化 ,无脱碳 、脱气 、脱脂 ,表面质量 好 ,变形 小 ,综 合 力学性 能 高 ,可靠 性 好 (重 复 性好 ,寿命 稳定 )等 一 系列 优点 。真空 炉 由
浅谈 真 空 热 处 理
北 京有色金属与稀土应 用研 究所 孙瑞 涛
摘 要 :真空热处理是真窒蕉 与热处理技术相结合的热处理技术,在航天航空、电子信息、船
真空热处理作用
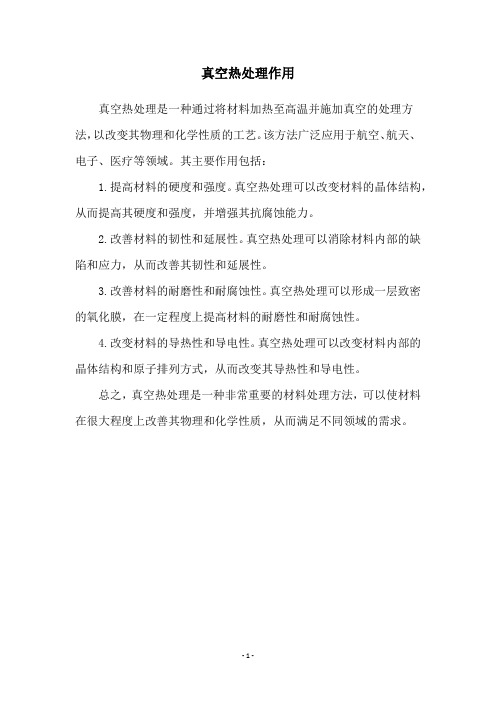
真空热处理作用
真空热处理是一种通过将材料加热至高温并施加真空的处理方法,以改变其物理和化学性质的工艺。
该方法广泛应用于航空、航天、电子、医疗等领域。
其主要作用包括:
1.提高材料的硬度和强度。
真空热处理可以改变材料的晶体结构,从而提高其硬度和强度,并增强其抗腐蚀能力。
2.改善材料的韧性和延展性。
真空热处理可以消除材料内部的缺陷和应力,从而改善其韧性和延展性。
3.改善材料的耐磨性和耐腐蚀性。
真空热处理可以形成一层致密的氧化膜,在一定程度上提高材料的耐磨性和耐腐蚀性。
4.改变材料的导热性和导电性。
真空热处理可以改变材料内部的晶体结构和原子排列方式,从而改变其导热性和导电性。
总之,真空热处理是一种非常重要的材料处理方法,可以使材料在很大程度上改善其物理和化学性质,从而满足不同领域的需求。
- 1 -。
真空热处理开裂的原因

真空热处理开裂的原因真空热处理是一种常用的金属材料加工方法,它通过加热材料至高温后在真空环境中快速冷却,以改善材料的物理和化学性能。
然而,有时候在真空热处理过程中会出现开裂的问题,影响材料的质量和使用寿命。
本文将深入探讨真空热处理开裂的原因。
真空热处理开裂的原因可以分为内应力和化学因素两大类。
内应力是由于材料在加热过程中发生体积变化或温度梯度引起的,而化学因素主要是指材料中的元素相互作用导致的。
内应力是真空热处理开裂的主要原因之一。
在加热过程中,材料会因为热胀冷缩而产生应力。
当材料的应力超过其强度极限时,就会发生开裂。
例如,当材料表面与内部的温度梯度差异较大时,会导致表面收缩速度快于内部,从而引起开裂。
此外,材料的形状和厚度也会影响内应力的分布,进而影响开裂的倾向性。
化学因素也是导致真空热处理开裂的重要原因之一。
在真空环境下,材料表面容易吸附氧气、氮气等气体,从而在材料内部形成气体孔隙。
当材料迅速冷却时,气体孔隙不能及时排出,导致内部应力集中,从而发生开裂。
此外,材料中的杂质、非金属夹杂物等也会加剧开裂的倾向性。
为了解决真空热处理开裂的问题,可以采取以下措施。
首先,优化热处理工艺参数,例如控制加热和冷却速率,减小温度梯度等,以降低内应力的产生。
其次,可以通过添加合适的合金元素来改善材料的抗开裂性能。
此外,定期清理真空炉腔和炉具,以减少化学因素对开裂的影响。
总结起来,真空热处理开裂是由于内应力和化学因素导致的。
为了避免开裂问题,需要优化热处理工艺参数,控制内应力的产生,并注意材料中的杂质和非金属夹杂物对开裂的影响。
只有这样,才能确保真空热处理的质量和效果,提高材料的性能和使用寿命。
真空热处理操作流程

真空热处理操作流程
真空热处理是一种利用特殊工艺,将材料加热到一定温度并在真空环
境下进行处理的方法。
下面将详细介绍真空热处理的操作流程。
一、材料准备
在进行真空热处理前,需要对材料进行准备。
首先要对材料进行分类,并根据材料的性质选择合适的加工方法。
其中最重要的便是确定适宜
的加热温度和持温时间。
二、真空加热
当材料准备就绪后,需要进行真空加热。
首先将加工好的材料放入真
空炉内,然后将炉门关闭。
随后,要进行抽真空,将炉内空气排除,
直到达到预定的真空度。
接下来,设定加热温度,将温度控制在预定的范围内,并保持一定的
持温时间。
此时,材料就可以在高温条件下进行处理,以达到预定的
目的。
三、冷却处理
完成真空热处理后,需要进行冷却处理。
通常采用的方法是通过水循环来进行快速冷却,以降低材料的温度。
此时,需要注意控制冷却速度和冷却时间,避免材料受到过度温度变化的影响。
四、处理结束
当冷却操作完成后,即可打开炉门,取出处理好的材料。
此时,需要对材料进行检测,以确保热处理效果达到要求。
如果材料质量符合要求,即可完成真空热处理,否则需要重新处理。
总之,真空热处理是一种非常重要的材料加工方法,其操作流程必须严格按照工艺要求进行。
只有这样才能确保材料的质量和性能达到最佳的状态。
真空热处理技术

真空热处理技术
真空热处理技术是一种在低于一个大气压的气氛环境中进行热处理的工艺,包括真空环境下的加热、冷却和保温等。
真空热处理可以实现无氧化、无脱碳、无渗碳,去掉工件表面的磷屑,并有脱脂除气等作用,从而达到表面光亮净化的效果。
同时,真空热处理技术还可以实现气氛控制热处理,将金属工件在1个大气压以下加热,加速化学热处理的吸附和反应过程。
真空热处理技术广泛应用于各种特殊合金热处理和一般工程用钢的热处理中,可以提高热处理质量和产品性能,同时降低生产成本和维护成本。
此外,真空热处理还可以实现多元共渗等特殊热处理工艺,如渗碳、渗氮、渗铬、渗硼等。
在设备方面,真空热处理炉的维修是真空炉管理的重要内容之一,需要定期进行维修和保养。
同时,根据不同的生产需求和工艺要求,选择合适的真空炉和热处理工艺也是非常重要的。
总的来说,真空热处理技术是一种高效、高质量、低成本的热处理工艺,在制造业和材料科学领域有着广泛的应用前景。
真空热处理群

真空热处理群"真空热处理群"在当今的工业发展中,真空热处理作为一项重要的工艺技术,正在被广泛应用于各个领域。
真空热处理群是一个由专业人士组成的社群,旨在分享知识和经验,推动该领域的进一步发展。
首先,我们来了解一下真空热处理的基本概念。
真空热处理是通过在高温下将材料置于真空环境中进行加热处理的一种工艺。
这种处理方式可以改变材料的微观结构和性能,从而提高其硬度、强度、耐磨性等特性。
真空热处理广泛应用于航空航天、汽车、机械制造等行业,对提高产品质量和性能起到了至关重要的作用。
真空热处理群为行业内的从业人员提供了一个交流与学习的平台。
在这个群体中,人们可以分享自己的研究成果、工艺经验以及遇到的问题和解决方案。
通过互相借鉴和学习,真空热处理技术不断得到提升和完善。
同时,真空热处理群也定期举办研讨会和培训课程,邀请国内外专家进行分享和授课,以促进行业的发展和进步。
然而,作为一个专业的群体,真空热处理群也需要遵守一些基本规则和原则。
首先,群内成员应保持良好的交流态度,尊重他人的观点和意见。
在讨论问题时,应理性思考,不得进行人身攻击或言辞激烈的争论。
其次,群内成员应遵守法律法规,不得传播与真空热处理无关的信息,更不能传播侵犯他人版权的内容。
此外,群内成员也要注意言行举止,不得发布包含敏感词或其他不良信息的内容。
总之,真空热处理群作为一个专业的交流平台,为行业内的专业人士提供了一个分享与学习的机会。
通过互相交流和学习,真空热处理技术得以进一步提升和完善。
在群内,成员应遵守规则,保持良好的交流态度和行为举止。
相信随着真空热处理群的不断发展壮大,该领域的技术和应用将会取得更大的突破和进步。
真空热处理作业指导书
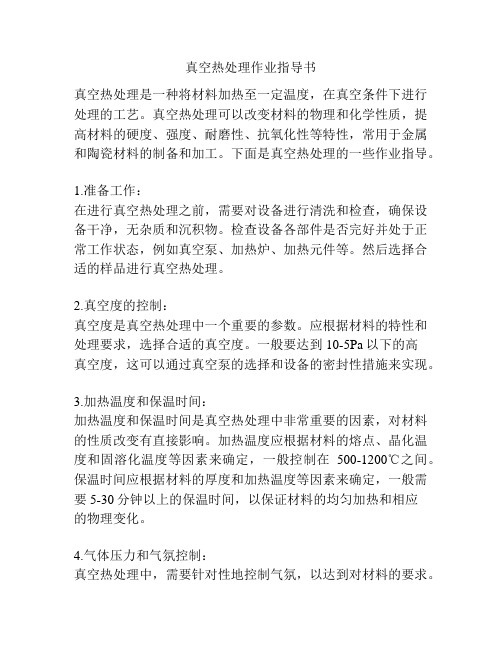
真空热处理作业指导书真空热处理是一种将材料加热至一定温度,在真空条件下进行处理的工艺。
真空热处理可以改变材料的物理和化学性质,提高材料的硬度、强度、耐磨性、抗氧化性等特性,常用于金属和陶瓷材料的制备和加工。
下面是真空热处理的一些作业指导。
1.准备工作:在进行真空热处理之前,需要对设备进行清洗和检查,确保设备干净,无杂质和沉积物。
检查设备各部件是否完好并处于正常工作状态,例如真空泵、加热炉、加热元件等。
然后选择合适的样品进行真空热处理。
2.真空度的控制:真空度是真空热处理中一个重要的参数。
应根据材料的特性和处理要求,选择合适的真空度。
一般要达到10-5Pa以下的高真空度,这可以通过真空泵的选择和设备的密封性措施来实现。
3.加热温度和保温时间:加热温度和保温时间是真空热处理中非常重要的因素,对材料的性质改变有直接影响。
加热温度应根据材料的熔点、晶化温度和固溶化温度等因素来确定,一般控制在500-1200℃之间。
保温时间应根据材料的厚度和加热温度等因素来确定,一般需要5-30分钟以上的保温时间,以保证材料的均匀加热和相应的物理变化。
4.气体压力和气氛控制:真空热处理中,需要针对性地控制气氛,以达到对材料的要求。
一般来说,真空热处理中的气氛可以分为氧化性气氛、还原性气氛和惰性气氛等。
对于金属材料,氧化性气氛会使其表面产生氧化层,而还原性气氛可以去除氧化层。
对于陶瓷材料,惰性气氛可以保持其表面平整,防止其在真空加热过程中变形或变色。
应根据材料的特性和处理要求,选择合适的气氛,设置相应的气体压力。
5.冷却方式:真空热处理完成后,需要合理选择冷却方式,以保证材料晶体结构的稳定。
快速冷却会使材料硬化,但也会产生过度热处理现象。
缓慢冷却可以保证材料的物理状态相对稳定,但这也会造成材料的结构不稳定。
因此,应根据材料的特性和处理要求,选择合适的冷却方式和速度。
总之,真空热处理是一项非常复杂而且技术含量较高的工艺,需要在密封、真空度、加热温度、保温时间、气氛控制和冷却方式等方面进行综合考虑,以保证材料的质量和硬度。
真空热处理技术

真空热处理技术真空热处理真空热处理是真空技术与热处理技术相结合的新型热处理技术,真空热处理所处的真空环境指的是低于一个大气压的气氛环境,包括低真空、中等真空、高真空和超高真空,真空热处理实际也属于气氛控制热处理。
真空热处理是指热处理工艺的全部和部分在真空状态下进行的,真空热处理可以实现几乎所有的常规热处理所能涉及的热处理工艺,但热处理质量大大提高。
与常规热处理相比,真空热处理的同时,可实现无氧化、无脱碳、无渗碳,可去掉工件表面的磷屑,并有脱脂除气等作用,从而达到表面光亮净化的效果。
真空热处理其实还分成以下四个技术要点1.真空高压气冷淬火技术当前真空高压气冷淬火技术发展较快,相继出现了负压(<1×105Pa)高流率气冷、加压(1×105~4×105Pa)气冷、高压(5× 105~10×105Pa)气冷、超高压一(10×105~20×105Pa)气冷等新技术,不但大幅度提高了真空气冷淬火能力,且淬火后工件表面光亮度好,变形小,还有高效、节能、无污染等优点。
真空高压气冷淬火的用途是材料的淬火和回火,不锈钢和特殊合金的固溶、时效,离子渗碳和碳氮共渗,以及真空烧结,钎焊后的冷却和淬火。
用6×105Pa高压氮气冷却淬火时、被冷却的负载只能是松散型的,高速钢(W6Mo5Cr4V2)可淬透至70~100mm,高合金热作模具钢(如 4Cr5MoSiV)可达25~100mm。
用10×105Pa高压氮气冷却淬火时,被冷却负载可以是密集型的,比6×105Pa 冷却时负载密度提高约30%~4O%。
用20×105Pa超高压氮气或氦气和氮气的混合气冷却淬火时,被冷却负载是密集的并可捆绑在一起。
其密度较6×105Pa氮气冷却时提高80%~150%,可冷却所有的高速钢、高合金钢、热作工模具钢及Cr13%的铬钢和较多的合金油淬钢,如较大尺寸的9Mn2V钢。
- 1、下载文档前请自行甄别文档内容的完整性,平台不提供额外的编辑、内容补充、找答案等附加服务。
- 2、"仅部分预览"的文档,不可在线预览部分如存在完整性等问题,可反馈申请退款(可完整预览的文档不适用该条件!)。
- 3、如文档侵犯您的权益,请联系客服反馈,我们会尽快为您处理(人工客服工作时间:9:00-18:30)。
真空热处理真空热处理是真空技术与热处理技术相结合的新型热处理技术,真空热处理所处的真空环境指的是低于一个大气压的气氛环境,包括低真空、中等真空、高真空和超高真空,真空热处理实际也属于气氛控制热处理。
真空热处理是指热处理工艺的全部和部分在真空状态下进行的,真空热处理可以实现几乎所有的常规热处理所能涉及的热处理工艺,但热处理质量大大提高。
与常规热处理相比,真空热处理的同时,可实现无氧化、无脱碳、无渗碳,可去掉工件表面的磷屑,并有脱脂除气等作用,从而达到表面光亮净化的效果。
技术要点真空高压气冷淬火技术当前真空高压气冷淬火技术发展较快,相继出现了负压(<1×105Pa)高流率气冷、加压(1×105~4×105Pa)气冷、高压(5× 105~10×105Pa)气冷、超高压一(10×105~20×105Pa)气冷等新技术,不但大幅度提高了真空气冷淬火能力,且淬火后工件表面光亮度好,变形小,还有高效、节能、无污染等优点。
真空高压气冷淬火的用途是材料的淬火和回火,不锈钢和特殊合金的固溶、时效,离子渗碳和碳氮共渗,以及真空烧结,钎焊后的冷却和淬火。
用6×105Pa高压氮气冷却淬火时、被冷却的负载只能是松散型的,高速钢(W6Mo5Cr4V2)可淬透至70~100mm,高合金热作模具钢(如 4Cr5MoSiV)可达25~100mm。
用10×105Pa高压氮气冷却淬火时,被冷却负载可以是密集型的,比6×105Pa冷却时负载密度提高约30%~4O%。
用20×105Pa超高压氮气或氦气和氮气的混合气冷却淬火时,被冷却负载是密集的并可捆绑在一起。
其密度较6×105P a氮气冷却时提高80%~150%,可冷却所有的高速钢、高合金钢、热作工模具钢及Cr13%的铬钢和较多的合金油淬钢,如较大尺寸的9Mn2V钢。
具有单独冷却室的双室气冷淬火炉的冷却能力优于相同类型的单室炉。
2×105Pa氮气冷却的双室炉的冷却效果和4×105Pa的单室炉相当。
但运行成本、维修成本低。
由于我国基础材料工业(石墨、钼材等)和配套元器件(电动机)等水平有待提高。
所以在提高6×105Pa单室高压真空护质量的同时,发展双室加压和高压气冷淬火炉比较符合我国的国情。
真空高压气冷等温淬火形状复杂的较大工件从高温连续进行快速冷却时容易产生变形甚至裂纹。
以往可用盐浴等温淬火解决。
在单室真空高压气冷淬火炉中能否进行气冷等温淬火呢?图1为在带有对流加热功能的单室高压气冷淬火炉中对两组φ320mm×120mm两块叠装的碳素结构钢用不同冷却方式淬火后的对化结果。
图中一组曲线是在102O℃加热后,在6×105Pa压力下连续用高纯氮气冷却(风向是上、下相互交替,40s切换一次)的结果。
另一组是对试样表面、心部进行370℃时的控制冷却。
从两组曲线的对比可以看出,心部温度通过50O℃的时间(半冷时间)只差约2min。
从表面进行控制冷却开始到心部温度到达370℃附近,需27min。
由此可见,在单室真空高压气淬火炉进行等温气冷淬火是可行的。
真空渗氮技术真空渗氮是使用真空炉对钢铁零件进行整体加热、充入少量气体,在低压状态下产生活性氮原子渗入并向钢中扩散而实现硬化的;而离子渗氮是靠晖光放电产生的活性N离子轰击并仅加热钢铁零件表面,发生化学反应生成核化物实现硬化的。
真空渗氛时,将真空炉排气至较高真空度0.133Pa(1×10-3Torr)后,将工件升至,530~560℃,同时送入氨气或NH3+CXHY+N2O复合气体,并对各种气体的送入量进行精确控制,炉压控制在0.667Pa(5Torr),低压状态能加快工件表面的气体交换,活跃的N元素(或N,C)来自化学反应及NH3(或在处理温度500-570℃NH3和CXHY的裂解),保温3~5h后,用炉内惰性气体进行快速冷却。
不同的材质,经此处理后可得到渗层深为20~80μm、硬度为600~1500HV的硬化层。
真空渗氮有人称为真空排气式氮碳共渗,其特点是通过真空技术,使金属表面活性化和清净化。
在加热、保温、冷却的整个热处理过程中,不纯的微量气体被排出,含活性物质的纯净复合气体被送入,使表面层相结构的调整和控制、质量的改善、效率的提高成为可能。
经X射线衍射分析证实,真空渗氮处理后,渗层中的化合物层是ε单相组织,没有其他脆性相(如Fe3C、Fe3O4)存在,所以硬度高,韧性好,分布也好。
“白层”单相ε化合物层可达到的硬度和材质成分有关。
材质中含Cr量越高,硬度也呈增加趋势。
Cr13%时,硬度可达到1200HV;含Cr18%(质量分数,余同)时,硬度可达 1500HV;含Cr25%时,硬度可达1700HV。
无脆性相的单相ε化合物层的耐磨性比气体氮碳共渗组织的耐磨性高,抗摩擦烧伤、抗热胶合、抗熔敷、抗熔损性能都很优异。
但该“白层”的存在对有些模具和零件也有不利之处,易使锻模在锻造初期引起龟裂,焊接修补时易生成针孔。
真空渗氮还有一个优点,就是通过对送入炉内的含活化物质的复合气体的种类和量的控制,可以得到几乎没有化合物层(白层),而只有0.1-1mm扩散层的组织。
其原因可能是在真空炉排气至 0.l33Pa(1×10-3Torr)后形成的,另一个原因是带有活性物质的复合气体在短时间内向钢中扩散形成的组织。
这种组织的优点是耐热冲击性、抗龟裂性能优异。
因而对实施高温回火的热作模具,如用高速钢或4Cr4MoSiV(H13)钢制模具可以得到表面硬度高、耐磨性好、耐热冲击性好、抗龟裂而又有韧性的综合性能;但仅有扩散层组织时,模具的抗咬合性、耐熔敷、熔损性能不够好。
由于模具或机械零件的服役条件和对性能的要求不一,在进行表面热处理时,必需调整表面层的组织和性能。
真空渗氮除应用于工模具外,对提高精密齿轮和要求耐磨耐蚀的机械零件以及弹簧等的性能都有明显效果,可接受处理的材质也比较广泛。
真空清洗与干燥技术目前有的热处理还离不开清洗干燥工序,尤其需油冷的各类热处理,清洗干燥的任务更繁重、难度也更大。
国际上使用效果最佳的清洗剂是卤素系清洗剂。
发达国家,如日本使用的卤素系清洗剂的比例如表1所示。
其中三氯乙烷、氟里昂因属破坏大气臭氧层物质,已被禁止使用。
其他卤素系物质也因对生态环境、人、畜有害而被限制使用。
所以各国都在研究各种替代型的清洗干燥技术。
历史起源真空热处理是将金属工件在 1个大气压以下(即负压下)加热的金属热处理工艺。
20世纪20年代末,随着电真空技术的发展,出现了真空热处理工艺,当时还仅用于退火和脱气。
由于设备的限制,这种工艺较长时间未能获得大的进展。
60~70年代,陆续研制成功气冷式真空热处理炉、冷壁真空油淬炉和真空加热高压气淬炉等,使真空热处理工艺得到了新的发展。
在真空中进行渗碳,在真空中等离子场的作用下进行渗碳、渗氮或渗其他元素的技术进展,又使真空热处理进一步扩大了应用范围。
模具的真空热处理工艺热处理的发展是伴随着机械制造业的发展而发展,机械制造又对热处理提出了更新更高的要求,模具的热处理又是热处理中技术含量最高的部分。
众所周知,模具热处理就是为了发挥模具材料的潜力,提高模具的使用性能。
模具的性能必须满足:高的强度,(包括高温强度,抗冷热疲劳性能)高的硬度(耐磨性能)和高的韧性,并且还要求有良好的机械加工性、(包括良好的抛光性)可焊接性及抗腐蚀性等等。
对模具寿命影响最大的是模具的设计(包括了正确的选择材料)模具的材料,模具的热处理,模具的使用和维护等。
如果模具的设计合理,材料优质,那么热处理的好坏直接决定了模具的使用寿命。
目前国内外都在设法采用更先进的热处理手段来提高模具的性能延长模具的使用寿命。
而真空热处理则是模具热处理中较先进的方式之一。
所以从模具热处理来看,热处理加工设备的状态、热处理的工艺、生产过程的控制显得尤为重要。
而设备的先进性是保证先进工艺实现的前提。
真空高压气淬炉是实现真空热处理最为理想的设备。
真空炉具有不脱碳,不氧化的效果,具有温度均匀,加热和冷却速度可控,可以实现不同的工艺过程,真空炉由于没有污染,是国际上公认的“绿色热处理”。
现在国际上已有2-20bar的真空高压气淬炉,可以完全满足模具的真空热处理的要求。
模具热处理过程中,所采用的工艺参数对模具性能也有着至关重要的影响:它包括了加热温度、加热速度、保温时间、冷却方式、冷却速度等。
正确的热处理工艺参数可以保证模具获得最佳性能,反之,将产生不良甚至严重后果。
实践表明,正确的热处理工艺可以获得优良的组织,优良的组织形态才能保证优良的机械性能。
合适的工艺方法可以有效的控制模具热处理时的变形和开裂。
从实践中发现:模具在加热和冷却过程中,模具表面温度和心部温度的差异(加热的不均匀性和冷却的不均匀性)是造成模具变形的主要因素。
(真空炉具有控制加热速度和冷却速度的能力)。
不同的工艺方法可以使模具满足不同的使用条件和不同的性能要求。
从模具的使用寿命来看,满足硬度的要求只是达到模具技术要求的一个方面,它还有些性能要求是不好测量的,如强度韧性等等。
模具质量的好坏并不能完全用硬度指标来进行认定,它不可能用硬度测量方法最终来检验出模具的使用寿命,热处理作为特殊工序(即特殊过程),它只能通过工艺验证,性能实验,确认合理的工艺参数,并严格实施经确认的工艺参数(工序过程控制)来保证产品质量的可靠性和稳定性。
大量数据表明,真空热处理加工的冷冲模具变形较小、很少发生线切割开裂、磨裂的现象。
压铸模采用先进的工艺方法,在一定程度上减少模具的龟裂以及使用中粘模的现象。
总而言之,真空高压气淬工艺具有加热和冷却速度自由控制的优点,可以编制不同的工艺参数,得到预想的金相组织和性能。
技术的应用零件经真空热处理后,畸变小,质量高,且工艺本身操作灵活,无公害。
因此真空热处理不仅是某些特殊合金热处理的必要手段,而且在一般工程用钢的热处理中也获得应用,特别是工具、模具和精密耦件等,经真空热处理后使用寿命较一般热处理有较大的提高。
例如某些模具经真空热处理后,其寿命比原来盐浴处理的高40~400%,而有许多工具的寿命可提高3~4倍左右。
此外,真空加热炉可在较高温度下工作,且工件可以保持洁净的表面,因而能加速化学热处理的吸附和反应过程。
因此,某些化学热处理,如渗碳、渗氮、渗铬、渗硼,以及多元共渗都能得到更快、更好的效果。