利用酸性蚀刻废液合成氧化铜工艺的探讨
酸性蚀刻液电解回收铜工艺条件的研究
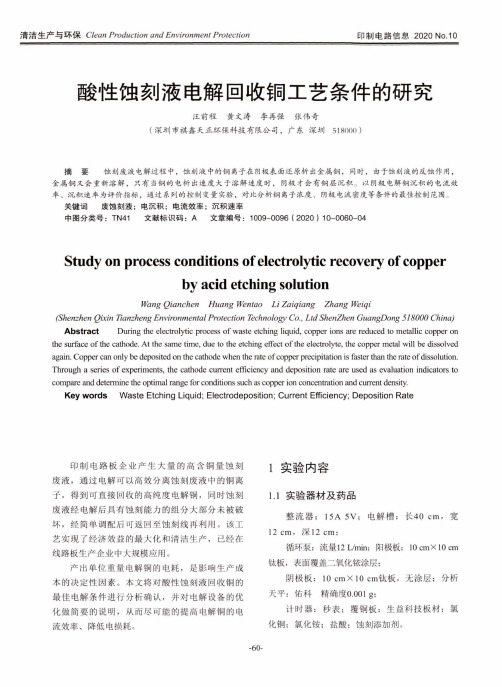
酸性蚀刻液电解回收铜工艺条件的研究汪前程黄文涛李再强张伟奇(深圳市祺鑫天正环保科技有限公司,广东深圳518000)摘要蚀刻废液电解过程中,蚀刻液中的铜离子在阴极表面还原析出金属铜,同时,由于蚀刻液的反蚀作用,金属铜又会重新溶解,只有当钢的电析出速度大于溶解速度时,阴极才会有铜层沉积。
以阴极电解铜沉积的电流效率、沉积速率为评价指标,通过系列的控制变量实验,对比分析铜离子浓度、阴极电流密度等条件的最佳控制范围,关键词废蚀刻液;电沉积;电流效率;沉积速率中图分类号:TN41 文献标识码:A文章编号:1009-0096 (2020) 10-0060-04Study on process conditions of electrolytic recovery of copperby acid etching solutionWang Qianchen Huang Wentao Li Zaiqiang Zhang Weiqi(Shenzhen Qixin Tianzheng Environmental Protection Technology Co.,Ltd ShenZhen GuangDong518000 China) Abstract During the electrolytic process of waste etching liquid,copper ions are reduced to metallic copper on the surface of the cathode.At the same time,due to the etching effect of the electrolyte,the copper m etal will be dissolved again.Copper can only be deposited on the cathode when the rate of copper precipitation is faster than the rate of d issolution. T T irough a series of experiments,the cathode current efficiency and deposition rate are used as evaluation indicators to compare and determine the optimal range for conditions such as copper ion concentration and current density.Key words Waste Etching Liquid;Electrodeposition;Current Efficiency;Deposition Rate印制电路板企业产生大量的高含铜量蚀刻废液,通过电解可以高效分离蚀刻废液中的铜离 子,得到可直接回收的高纯度电解铜,同时蚀刻 废液经电解后具有蚀刻能力的组分大部分未被破 坏,经简单调配后可返回至蚀刻线再利用。
PCB酸蚀刻废液制备电镀级硫酸铜方法研究

1 . 2 实验 试剂 及仪 器
混 合碱液 , 已除 杂 酸 蚀 刻 废 液 ( 已除去铁 、 砷等杂质 , 含 铜
8 %) , 9 8 %浓 硫 酸 。
5 0 0 0 ml 普通烧杯 , 5 0 0 0 ml 带 溢 流 口烧 杯 , 封 闭 式 电 炉 , 电
动 搅拌 器 . 抽滤装置 , 原 子 吸 收 光谱 仪 。
从图 1 可 以看 出 : 不同p H 值 下 氧 化 铜 中 氯离 子含 量 不 同 。 p H> 1 0 . 0时 , 氯 离 子含 量 较 高 , 这 是 因为 p H 值高 , 碱液残 留多, 粘稠 、 难洗涤 ; 当p H≤ 1 0 . 0时 , 氧 化 铜 中氯 离 子 含 量 < 0 . 0 1 %, 达 到国标 C U O9 8 5和氧 化 铜 中控 指 标 对 氯 离子 含 量 的要 求 。 从 表 1中可 以看 出 ,随 着 p H 升 高 ,氧 化 铜 中 C u含 量 增 大, 但当p H> 9 . 5时 , 增 大趋 势变 缓 。 这是 因 为 p H 过低 不 能 满 足 反 应 中 间 体 分解 所 需 的条 件 , 仍有 部 分 中 间产 物 残 留 。所 以 考 虑 到 生产 成 本 及 产 品 品质 . 实验 p H值选择 9 . 5 — 1 0 . 0之 间 。
反 应p H 值
应 生 成 热 的 硫 酸 铜饱 和 溶 液 ,然后 冷却 结 晶 得 到 五水 硫 酸 铜 。
涉 及 到 的反 应 如 下 : 3 C u Cl 2 + 2 Na OH+ 2 Na 2 CO3 = 3 Cu O + 6 Na c l + H o+ 2 co2 T
,
岳
1 实验部分
1 . 1 实验 原理
酸性蚀刻液回收铜设备基本原理及工艺流程
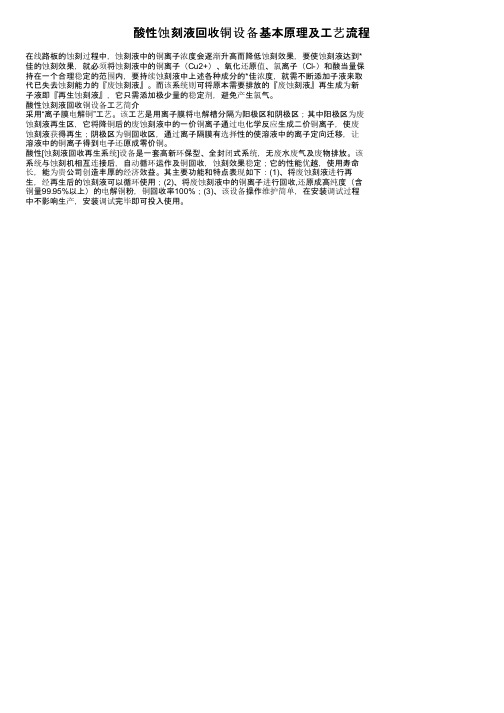
酸性蚀刻液回收铜设备基本原理及工艺流程在线路板的蚀刻过程中,蚀刻液中的铜离子浓度会逐渐升高而降低蚀刻效果,要使蚀刻液达到*佳的蚀刻效果,就必须将蚀刻液中的铜离子(Cu2+)、氧化还原值、氯离子(Cl-)和酸当量保持在一个合理稳定的范围内,要持续蚀刻液中上述各种成分的*佳浓度,就需不断添加子液来取代已失去蚀刻能力的『废蚀刻液』。
而该系统则可将原本需要排放的『废蚀刻液』再生成为新
子液即『再生蚀刻液』,它只需添加极少量的稳定剂,避免产生氯气。
酸性蚀刻液回收铜设备工艺简介
采用“离子膜电解铜”工艺。
该工艺是用离子膜将电解槽分隔为阳极区和阴极区;其中阳极区为废蚀刻液再生区,它将降铜后的废蚀刻液中的一价铜离子通过电化学反应生成二价铜离子,使废
蚀刻液获得再生;阴极区为铜回收区,通过离子隔膜有选择性的使溶液中的离子定向迁移,让
溶液中的铜离子得到电子还原成零价铜。
酸性[蚀刻液回收再生系统]设备是一套高新环保型、全封闭式系统,无废水废气及废物排放。
该系统与蚀刻机相互连接后,自动循环运作及铜回收,蚀刻效果稳定;它的性能优越,使用寿命长,能为贵公司创造丰厚的经济效益。
其主要功能和特点表现如下:(1)、将废蚀刻液进行再
生,经再生后的蚀刻液可以循环使用;(2)、将废蚀刻液中的铜离子进行回收,还原成高纯度(含铜量99.95%以上)的电解铜粉,铜回收率100%;(3)、该设备操作维护简单,在安装调试过程
中不影响生产,安装调试完毕即可投入使用。
酸碱性蚀刻液再生及铜回收系统
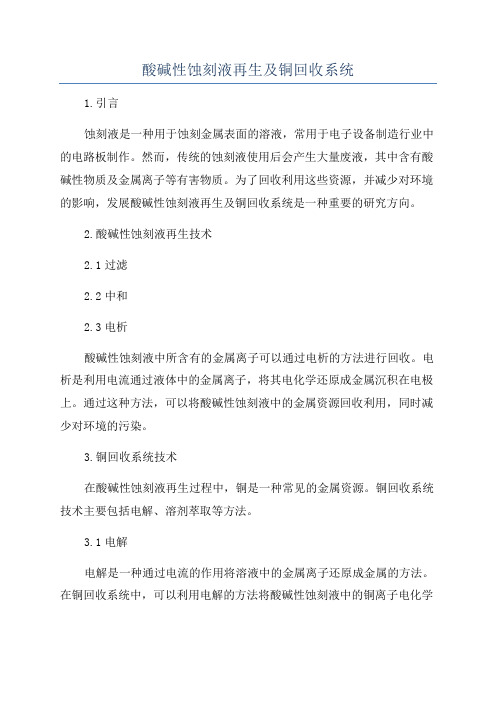
酸碱性蚀刻液再生及铜回收系统1.引言蚀刻液是一种用于蚀刻金属表面的溶液,常用于电子设备制造行业中的电路板制作。
然而,传统的蚀刻液使用后会产生大量废液,其中含有酸碱性物质及金属离子等有害物质。
为了回收利用这些资源,并减少对环境的影响,发展酸碱性蚀刻液再生及铜回收系统是一种重要的研究方向。
2.酸碱性蚀刻液再生技术2.1过滤2.2中和2.3电析酸碱性蚀刻液中所含有的金属离子可以通过电析的方法进行回收。
电析是利用电流通过液体中的金属离子,将其电化学还原成金属沉积在电极上。
通过这种方法,可以将酸碱性蚀刻液中的金属资源回收利用,同时减少对环境的污染。
3.铜回收系统技术在酸碱性蚀刻液再生过程中,铜是一种常见的金属资源。
铜回收系统技术主要包括电解、溶剂萃取等方法。
3.1电解电解是一种通过电流的作用将溶液中的金属离子还原成金属的方法。
在铜回收系统中,可以利用电解的方法将酸碱性蚀刻液中的铜离子电化学还原成铜金属。
这种方法具有高效、环保的特点,能够有效地回收利用酸碱性蚀刻液中的铜资源。
3.2溶剂萃取溶剂萃取是通过溶剂选择性地吸附和分离溶液中的特定成分的方法。
适当选择合适的溶剂,可以实现对酸碱性蚀刻液中的铜离子的吸附和回收。
这种方法具有操作简单、回收率高的特点,是一种常用的铜回收系统技术。
4.酸碱性蚀刻液再生及铜回收系统的优势4.1资源回收利用通过再生技术可以将酸碱性蚀刻液中的酸碱物质和金属离子回收利用,减少对自然资源的消耗。
4.2环境友好再生系统能够有效地处理和减少酸碱性蚀刻液中的废液,减少对环境的污染。
4.3经济效益通过再生和回收技术,可以降低酸碱性蚀刻液的成本,提高资源利用效率,从而带来经济效益。
5.结论酸碱性蚀刻液再生及铜回收系统是一种重要的研究方向,通过过滤、中和和电析等方法可以实现酸碱性蚀刻液的再生和回收利用。
通过电解和溶剂萃取等方法可以实现酸碱性蚀刻液中的铜离子的回收。
这些技术具有资源回收利用、环境友好和经济效益等优势,对于推动电子设备制造行业的可持续发展具有重要意义。
目前PCB行业酸性蚀刻制程废酸性蚀刻液处理方法浅谈

目前PCB行业酸性蚀刻制程废酸性蚀刻液处理方法浅谈关于目前PCB行业酸性蚀刻制程废酸性蚀刻液处理方法浅谈目前PCB铜回收行业正在蓬勃发展,自2002年以来国际铜价飙升,企业越来越重视开流节源,铜回收设备制造企业如雨后春笋般遍地开花。
但由于含铜废液回收铜行业入行门槛低,各企业素质参差不齐。
真正成规模,有实力的铜回收设备企业很少,大多数企业员工不超过20人,业务能力开展差,能安装一套设备也美其名曰环保科技公司。
此种现象造就PCB 企业无法真正了解到技术的发展程度,技术的可行性以及盲目安装设备后对自身造成的损失等;本文通过针对目前许多铜回收企业自称“已突破技术瓶颈,技术成熟稳定”的《PCB 酸性蚀刻废液再生与铜回收装置》的分析来让广大PCB企业更加直观更加清楚的了解目前的技术发展。
首先,要了解一个技术的稳定性我们需要了解其工艺流程及产物、企业工艺介绍是否符合生产工艺等。
众所周知PCB酸性蚀刻制程在蚀刻过程中,氯化铜中的Cu2+具有氧化性,能将板面上的铜氧化爲Cu+,形成的Cu2Cl2是不易溶于水的,在有过量的Cl-存在下,可形成可溶性的络离子,随着蚀刻的进行,溶液中的Cu+越来越多,蚀刻能力很快下降,以至最后失去蚀刻能力。
爲保持蚀刻能力,一般通过加入氧化剂对蚀刻液进行再生,使Cu+氧化重新转变爲Cu2+,使蚀刻得以连续的进行。
酸性废蚀刻液中酸性子液只是很少一部分,而大部分为生产中所添加的盐酸。
一般低酸生产子液与盐酸的比例大概为:1:1.5-2,高酸生产子液与盐酸比例大概为1:2-3。
通过酸性蚀刻的生产工艺我们可以得出,目前许多蚀刻铜回收企业所描述的酸性铜回收系统处理后废液可完全回用是不可能达到的。
以月废酸性蚀刻液100T为例,经提铜后回用再生液100T,酸性蚀刻生产中盐酸添加与再生液中的氯离子、铜离子含量均无关,固在处理完100T废液后将会超过150T的废液产生,如此循环废液量将是无限增长。
有人说可以回用一部分,另一部分排入PCB厂废水处理站。
铜蚀刻废液制备氧化铜

文献 报道 , 氧化 铜 在 8 氢 O℃ 以 上 就 分 解 成 氧 化 铜, 但是 当温度 升 到 1 0 0 0℃ 时 , 化 铜 进一 步 分 解 成 氧 氧 化亚 铜 , 以分 解 温度 一 定要 控 制 在 1 0 0 0℃ 所 0 ~1 0
之间。
从 图 3可 以看 出 , 5倍 于 沉 淀 的 自来 水 洗 涤 3 取 次、 纯净水 洗 涤 3 后 , 品 中基本 不含 氯离子 和 铵离 次 产
I .0 I - 一 — 蠖 鼷 / 8
加 的影 响 , 果见 图 1 结 。
: 。
0
质量/ g 温度/ ℃ 分 解 前 分 解 后 质 量 差/ g
1
7
9
1 0
1 2
p n值
图 1 p H值 对 氢 氧化 铜 沉 淀 的 影 响
Fi . Ef e to H a u n o pe d o i e i t to g1 f c f p v l e o c p r hy r x de pr c pi a i n
铜 蚀 刻 废 液 制 备 氧 化 铜
张晃初 龚 俊 潘湛 昌。 肖楚 民 胡光辉 魏 志钢 。 。 , , 。
( . 宏科技 ( 1胜 惠州) 限公 司 , 东 惠 州 5 6 0 ; . 东工 业 大学轻x  ̄ x 学院 , 东 广 州 5 0 0 ) 有 广 10 02 广 _ - 广 1 0 6
物。
1 3 分 析 检 测 .
蚀 刻 废 液 , 中 酸 性 蚀 刻 废 液 主要 含 氯 化 铜 和 盐 酸 其 等 、 性蚀 刻 废 液 主 要 含 铜 氨 配 离 子 。 目前 蚀 刻 废 碱 液 的处 理方 法 有 溶 剂 萃 取 法 、 学 沉 淀 法 、 子 交 换 化 离 法 、 络 处 理 法 、 解 法 等口 ] 破 电 。沉 淀 法 是 通 过 加 入 试 剂 , 废 液 中 的铜 离 子 转 变 成 氢 氧 化 铜 沉 淀 , 后 将 然 加 热 煅烧 , 到最 终 产 品 氧化 铜 。该 方 法 不 仅 经 济 , 得 而且 去 除 铜 效 果 较 好 , 由 于 废 液 中含 有 大 量 的氯 但 离子 和 铵 离 子 , 品在 沉 淀 过 程 中会 吸 附 这 些 杂 质 产
膜电解法在线再生酸性蚀刻液及回收铜新技术研究

膜电解法在线再生酸性蚀刻液及回收铜新技术研究摘要:本文主要通过在线式电解再生酸性的蚀刻液模拟实验,对膜电解处理方法酸性的蚀刻液在线再生与铜回收的新技术进行深入研究,实验操作结果表明了:通过监控阳极液的ORP变化状况与析氯反应,能够有效防止氯气被析出;分步式电解处理方法之下,能够有效防止氢气被析出,且促使致密金属的铜块形成;电流处于9-24A区间时,经23.5h分步式电解处理后,再生酸性的蚀刻液约为23.5L,电沉积可回收铜510g,在线式电解再生酸性的蚀刻液与铜回收最佳效果可实现,电解处理期间并未析出氢气、氯气,无需加入蚀刻子液、盐酸,未排放出废液,属于回收铜一种新技术。
关键词:膜电解法;在线再生;酸性;蚀刻液;回收铜;新技术;前言:酸性的蚀刻液自身具备着易于控制、较高熔铜容量、较快的蚀刻速率等各项优势,属于PCB的生产企业现阶段应用较为广泛的一种蚀刻液。
由于传统酸性的蚀刻液再生、回收铜各项技术方法,均需添加次氯酸钠、氯酸钠、双氧水等相关氧化剂,会大量析出氯气、氢气等,还有大量废液、废渣在排放出来,极易造成严重的环境污染情况。
鉴于此,本文主要针对膜电解处理方法酸性的蚀刻液在线再生与铜回收的新技术开展深入研究,以便于能够研究出一种最具节能环保型的膜电解处理方法酸性的蚀刻液在线再生方法与铜回收的新技术。
1、实验部分1.1 配置实验溶液PCB的生产企业所常用酸性的蚀刻液所有成分浓度有效范围即为:Cl-240-300g/L、H+1.5-2.5mol/L、Cu2+120-180g/L。
实验室分析纯为:37%的盐酸、NaCl、CuCl、CuCl2•2H2O、离子水等进行酸性的蚀刻液配置,成分包括:280g/LCl-、2mol/LHCl、2-10g/LCu+、164g/LCu(Cu2++Cu+)。
1.2 在线式电解再生酸性的蚀刻液模拟实验电解槽由PVC材质所制作,阴离子的交换膜把它分隔成阳极室与阴极室。
阳极:DSA自制阳极网,阴极为钛管。
酸性碱性蚀刻液回收铜可行性报告

酸性碱性蚀刻液回收铜可行性报告
摘要
本研究旨在探讨铜蚀刻液的回收可行性,回收后的铜价值可以获得更多的经济收益。
对市场上的铜蚀刻液种类进行了详细研究,主要包括酸性碱性蚀刻液。
在这种介质中,酸性和碱性蚀刻液都含有大量的有价值的铜锌等金属离子,可获得经济收益。
因此,本研究中着重考察了如何从酸性碱性蚀刻液中有效回收铜,从而获得更多经济收益。
本研究将先分析酸性和碱性蚀刻液的特性,以及其中含有的金属离子种类和含量,例如铜、锌等有价值的金属元素。
然后,将分析铜蚀刻液中的铜回收方法,主要包括离子交换法、沉淀法和抽滤法等。
最后,将分析具体的回收工艺和操作步骤,以及采取哪些措施以确保回收的有效性和经济性。
关键词:酸性碱性蚀刻液;铜回收;离子交换;沉淀;抽滤
1绪论
目前,国家对铜资源的持续性利用越来越重视,因此针对酸性碱性蚀刻液回收铜的可行性进行研究具有重大现实意义。
本研究主要考察酸性碱性蚀刻液中铜的回收方法,以及回收后的经济收益及实现这些收益的技术措施。
(1)分。
- 1、下载文档前请自行甄别文档内容的完整性,平台不提供额外的编辑、内容补充、找答案等附加服务。
- 2、"仅部分预览"的文档,不可在线预览部分如存在完整性等问题,可反馈申请退款(可完整预览的文档不适用该条件!)。
- 3、如文档侵犯您的权益,请联系客服反馈,我们会尽快为您处理(人工客服工作时间:9:00-18:30)。
利用酸性蚀刻废液合成氧化铜工艺的探
讨
摘要:在废蚀刻液回收工艺中采用酸性蚀刻废液与强碱高温下合成的氧化铜已得到广泛工艺生产,但得到的产品粒度细,压滤、洗涤工序耗时长、难度大,
-N难于洗涤。
为了提高氧化铜产最终产品含水率高铜含量在50%以下,Cl-、NH
3
品粒度,使其易滤过洗涤,降低氧化铜杂质含量,提高氧化铜产品品质。
本工艺实验探索一种用碳酸钠与氢氧化钠协同合成氧化铜新方法。
关键词:酸性蚀刻废液;合成;氧化铜;工艺方法
一、试验内容
1.1工艺流程(如图一所示)
图1 氧化铜工艺流程图
1.2主反应
CuCl2 + 2NaOH== Cu(OH)2 + Na2Cl
CuCO3 + 2NaOH== Cu(OH)2 + Na2CO3
Cu(OH)2==△==CuO+H2O
二、关键工序及调试参数
1.
中试时,先打开自来水阀门,先向碱转罐中投加一定量的水,打开搅拌,打
开加热盘管阀门,对自来水进行加热,投加相应量的Na
2CO
3
,开启碱转罐自循环
泵,检测罐内温度,如温度达到90℃以上,即可进行下一步操作。
2.
观察自循环管道出液是否澄清透明、无白色块状物,如果无白色块状物则说
明Na
2CO
3
完全溶解,可进行下一步操作,如有白色块状物则继续搅拌溶解并保持
水温度达到80℃以上,直至完全溶解。
3.
Na
2CO
3
完全溶解后,开启液碱泵及开关,调节NaOH流量,在不损坏设备和管
道的情况下使流量尽可能小。
为了防止生产中的原料波动导致投加配比与实验有差异,先投70%的量的液碱,pH调节到位后,如果碱转罐空间剩余空间足够,则继续投加液碱和酸性蚀刻液至足量;如果碱转罐空间剩余不足,则根据具体情况投加适量液碱和酸性蚀刻液。
投加液碱的同时,打开酸性蚀刻液提升泵和阀门,保持罐内温度为90℃以上,从自循环管取液测pH,调节酸性蚀刻液流量,保持罐内pH在10~11之间。
4.
NaOH投加足量时,停止NaOH和酸性蚀刻液进料,测罐内pH,如pH不在10.5附近,则投加少量NaOH或酸性蚀刻液将pH调至10.5附近。
5.
反应完成后控制罐内温度为90℃以上,搅拌、循环保温30min。
6.
保温结束后,罐内物料加冷却水至80℃后压滤。
取少量罐内液在实验室抽滤后,母液送检,测铜、氨氮含量。
7.
压滤机准备就绪,进料阀及所有压滤水出水阀打开,滤布压紧,做好进水准备。
开启氧化铜碱转提升泵,开始压滤。
观察压滤出水颜色并记录。
压滤完成后
吹气、洗水三次,再进行压滤,最终产品取样送检,测铜、水、氯离子含量。
同时取盐碱废水送检,测铜含量、氨氮、氯离子含量。
三、现象分析
3.1碱转现象及分析
1)碱转时需要将原料区的液碱泵和杂铜泵阀门关小,降低原料流量。
通过调节原料区的液碱泵和杂铜泵阀门,可调节液碱和氯化铜流量,调试中将阀门开度都拧小一半,以延长反应时间,便于PH调节。
如果阀门全开,最终调节PH时,容易出现短时开启原料泵产生较大的PH变化的现象,导致PH难以控制,需要反复调节,延长碱转时间。
2)混合碱比例波动。
由于每天的原料酸碱度变化,碳酸钠投量固定,故每次碱转并不能保证混合碱比例完全一致,会有一定的波动。
3)通过开循环管、降低原料流量,操作人员可实现维持反应中PH变化在1之间。
4)碳酸钠用量500kg、混合碱比例维持在3.4:1左右较为适宜,提高碳酸钠用量没有必要。
保持原料、压力等条件不变,将碳酸钠用量从500kg提高到800kg,产品铜含量没有显著提高。
同时,提高碳酸钠用量,不仅增加生产成本,为溶解更多的碳酸钠还需要加更多的自来水,还占用了碱转罐中的空间,使罐中铜浓度降低,每罐生产产品量降低。
因此碳酸钠用量从500kg、混合碱比例维持在3.4:1左右较为适宜,提高碳酸钠用量没有必要。
5)原料铁含量高可能会影响产品纯度。
7月7日产品干基铜含量只有72.04%,为所有调试样品中最低的,而其原料
中铁含量为所有原料中最高的。
原料铁含量高可能会对影响产品纯度产生影响,
但由于此现象只出现一次,不能排除偶然因素的影响,还需后续调试证明此猜想。
6)先中和不升温,再调高PH升温的碱转方式可能有效。
7月10号下午调试中,采用与上午调试相同参数,只是先不升温,并将ph
控制为8~9,待进料至罐体积的80%时,再升温,并将ph调回。
此想法目的是想
将先反应生成碱式碳酸铜再调高ph并升温,以生成氧化铜。
目前从产品数据上看,此方法制作的氧化铜铜含量有略微提高但并不明显,还需要后续多次试验证
明该方法的有效性。
7)出水母液氨氮随原料氨氮的升高而升高,原料氨氮为1600mg/L以下时,
出水母液氨氮含量为700mg/L以下。
本次检测母液为碱转后直接抽滤母液,其氨氮含量较高。
后续调试中,需要
检测混合了洗涤水、冷却水等的母液出水氨氮,预计其氨氮含量会降低。
8)母液出水铜含量超标。
母液铜含量第一次检测结果较高,与快速检测结果严重不符,于是第二次重
新检测,检测结果大幅度降低,但仍高于快速检测结果。
据第二次华保检测结果,母液出水铜含量自7月8号开始超标,这与前期实
验结果不符。
观察发现,母液放置一段时间后,底部出现了黑色沉淀,可能是一
些微小的氧化铜颗粒滤纸无法截留,检测时底部沉淀和母液一并通过原子吸收分
光光度计,使其铜检测结果较高。
后续调试中,可加测混合后的母液。
后续调试中,需要关注母液的铜含量问题,降低其含量。
3.2 压滤现象及分析
1)压榨程序在去除产品水分上,起至关重要的作用,不能省去。
第三次吹气完成后,从压滤机中取少许样品,挤压样品发现样品含水率过高,呈泥状,说明氯化铜制氧化铜工序中,不能只将产品水洗吹气,后续的压榨工序
必不可少。
第三次吹气后出水较少,接下来的压榨程序出水量很少,但之后的第
四次吹气却大量出水,这说明压榨程序压出了大量的水,一部分仍存在于滤饼空
隙间,但已于氧化铜分离;另一部分由于管道连接问题,仍在滤板间。
后续吹气
工序将这部分水份吹出。
这说明压榨程序在去除产品水分上,起至关重要的作用。
2)建议选取压榨压力为14公斤,不必延长吹气时间。
7月7号到9号上午碳酸钠投量均为500kg,混合碱比例保持在3.4:1左右,从表2中数据可以看出,随着压力的提高,产品湿基铜含量也相应提高,压滤压
力从12公斤提高到14公斤时,湿基铜含量从48.56%提高到54.81%,含水率从32.59%降低至27.22%,说明提高压榨压力,对降低产品含水率提高铜含量有促进
作用。
压力为13公斤时,产品铜含量接近50%;压力为14公斤时,产品铜含量
维持在53%以上,所以建议选取压榨压力为14公斤,再提高压榨压力,有损坏设
备的风险。
对比7月8号上午和下午的产品数据发现,上午延长吹气时间,并不能显著
降低产品含水率,说明延长吹气时间是不必要的。
四、总结与建议
碱转时需要将原料区的液碱泵和杂铜泵阀门关小,以降低原料流量。
投料时
混合碱比例会有波动,但对结果影响不大,只要控制在一定范围内即可。
操作中
通过开循环管、降低原料流量,操作人员可实现维持反应中PH变化在1之间。
最优的工艺参数为:碳酸钠用量500kg、混合碱比例维持在3.4:1左右,碱
转中控制PH为10~11,终点PH为10.5左右,压榨压力为14公斤,压滤机内工
序时间为:洗水6min、吹气6min,重复3次,再压榨5min,最后吹气10min。
原料氨氮为1600mg/L以下时,出水母液氨氮含量为700mg/L以下。
建议:
(1)氧化铜母液碱性较高,还含有未反应完全的碳酸钠,建议将压滤进料
时出水的母液单独收集到一罐中,将这部分水重复利用,用于溶解片碱等工序。
(2)压滤机出水管可安装一取样阀,便于将母液和洗水水区别取样。
检测
洗水最后一次的水样成分,研究其用于第一次洗水的可能性。
结束语
本论文采用酸性蚀刻废液为原料,通过用碳酸钠与氢氧化钠协同合成氧化铜,制备的活性氧化铜粉具有较高的纯度和较低的杂质含量。
该工艺具有较好的经济效益。
参考文献
[1]由酸性氯化铜蚀刻废液制备氢氧化铜工艺技术研究[J]. 汤政涛,刘后传,张启凯,吕照辉,戚健剑,于少明. 安徽化工. 2020(01)
[2]利用蚀刻废液生产碱式氯化铜过程中二英类污染物的去除[J]. 兰永辉,高仁富,许世爱,王璞,张庆华. 环境化学. 2014(10)
[3]氯化铜催化二噁英生成实验及指纹特性分析[J]. 张梦玫,李晓东,陈彤. 环境科学学报. 2019(08)
[4]低能耗制备试剂级二水氯化铜的新工艺[J]. 宋传京,黄萍,朱欢. 化学与生物工程. 2017(11)。