缸套及具有其的发动机、缸套的设计方法与设计方案
缸套生产工艺

缸套生产工艺
缸套是发动机的重要部件,起着密封气缸的作用。
其生产工艺主要包括材料选用、加工工艺和检测工序。
材料选用是缸套生产的第一步,通常使用的材料有铸铁、铅青铜等。
铸铁材料具有良好的热传导性和机械性能,适合用于发动机工作环境较为恶劣的缸套。
铅青铜材料具有良好的耐高温和抗磨损性能,适合用于高性能发动机的缸套。
加工工艺是缸套生产的核心环节。
首先,经过设计师的设计,将缸套的形状、尺寸等参数确定下来。
然后,从选材得到的铸坯中切割出缸套的预制坯。
接下来,对预制坯进行车削加工,使其形成光滑的内外表面。
最后,将加工好的缸套进行热处理,提高其硬度和细晶度。
检测工序是缸套生产的重要环节。
一般来说,缸套需要进行尺寸、表面质量和物理力学性能的检测。
尺寸检测主要包括内径、外径以及长度的测量,确保其与设计要求相符。
表面质量检测主要包括光洁度和平坦度的检验,确保缸套的表面光滑平整。
物理力学性能检测主要包括硬度和拉伸强度的测试,确保缸套具有足够的机械性能。
总之,缸套的生产工艺包括材料选用、加工工艺和检测工序。
通过科学的工艺流程和严格的检测标准,可以生产出质量优良的缸套产品,满足发动机的工作要求。
气缸套标准
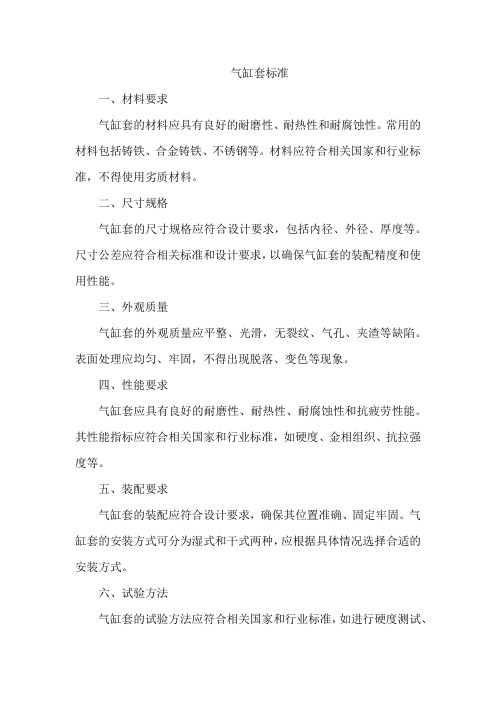
气缸套标准
一、材料要求
气缸套的材料应具有良好的耐磨性、耐热性和耐腐蚀性。
常用的材料包括铸铁、合金铸铁、不锈钢等。
材料应符合相关国家和行业标准,不得使用劣质材料。
二、尺寸规格
气缸套的尺寸规格应符合设计要求,包括内径、外径、厚度等。
尺寸公差应符合相关标准和设计要求,以确保气缸套的装配精度和使用性能。
三、外观质量
气缸套的外观质量应平整、光滑,无裂纹、气孔、夹渣等缺陷。
表面处理应均匀、牢固,不得出现脱落、变色等现象。
四、性能要求
气缸套应具有良好的耐磨性、耐热性、耐腐蚀性和抗疲劳性能。
其性能指标应符合相关国家和行业标准,如硬度、金相组织、抗拉强度等。
五、装配要求
气缸套的装配应符合设计要求,确保其位置准确、固定牢固。
气缸套的安装方式可分为湿式和干式两种,应根据具体情况选择合适的安装方式。
六、试验方法
气缸套的试验方法应符合相关国家和行业标准,如进行硬度测试、
耐磨性试验、耐热性试验等。
试验过程中应严格控制试验条件,确保试验结果的准确性和可靠性。
七、检验规则
气缸套的检验规则应符合相关国家和行业标准,包括出厂检验和型式检验。
检验项目应包括外观质量、尺寸规格、性能要求等,检验结果应符合标准要求。
八、包装、运输、贮存
气缸套的包装应牢固可靠,防止在运输和贮存过程中出现损坏。
运输时应防止剧烈振动和碰撞,贮存时应保持干燥、通风良好的环境,避免阳光直射和潮湿环境。
高性能中速柴油机气缸套设计研究
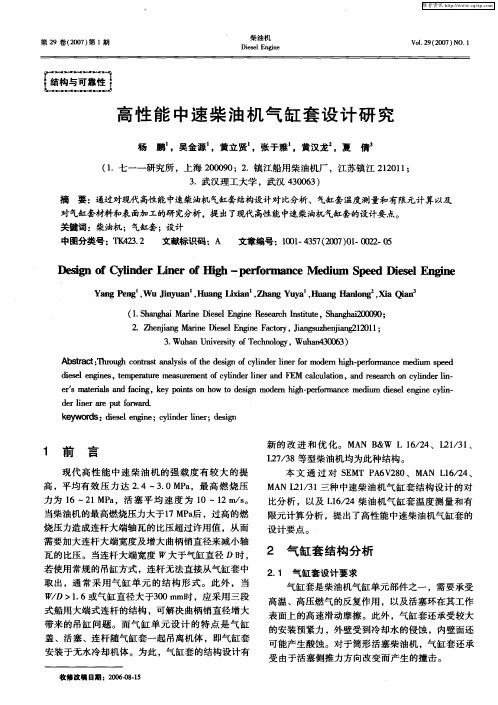
MA 2/ 1三种 中速 柴 油 机气 缸 套 结 构设 计 的对 NL 13 比分 析 ,以及 L6 2 1/4柴 油 机气 缸 套 温 度 测 量 和有
限元计算分析 ,提出了高性能 中速柴油机气缸套的
设 计要 点 。
2 气 缸 套 结构 分 析
2 1 气 缸套 设计 要 求 .
若使用常规的吊缸方式 ,连杆无法直接从气缸套中
中图分类号 :T 432 K 2. 文献标识码 :A 文章编号 :10 — 37 2 3) 1 O 2— 5 0 1 4 5 (07 0 一 O2 0
De in o l d r Li e Ig -p r o m a c e im p e e e gn sg fCyi e n r o Iih n f e f r n e M du S e d Dis lEn ie
d rl e r u r ad e n ra e p t w r . i o f
ky od : e l n n ; yi e nr ds e w rs d s g e cl dr ie; ei i e ei n l n g 新 的 改 进 和 优 化 。 M N B W 6 2 、L 1 3 、 A & L 1/ 4 2 / 1
气缸 套是 柴 油机气 缸 单元部 件 之一 ,需 要 承受 高 温 、高压燃 气 的反 复作 用 ,以及 活 塞环 在其 工作 表 面上 的高 速 滑动摩 擦 。此外 ,气缸 套还 承受 较大 的安装 预 紧力 ,外 壁受 到冷却 水 的侵 蚀 ,内壁面还 可能 产生 酸蚀 。对 于筒 形 活塞柴 油 机 ,气 缸 套还 承 受 由于 活塞侧 推力 方 向改 变而 产生 的撞 击 。
1 前
言
L7 3 型柴 油机 均 为此种 结构 。 2/ 8等
气缸体加工工艺及夹具设计

毕业设计(论文)课题气缸体加工工艺及夹具设计院系机械工程学院专业机械制造及自动化班级姓名完成日期指导教师摘要本说明书涵盖了气缸体零件从毛坯的选择到工艺过程拟定再到各加工步骤计算的全部过程,此外,对于用到的镗床及钻床夹具也做了简要说明。
首先对于零件上的一些主要加工表面,通过查阅大量专业资料确定了其加工工艺,确保达到零件的精度要求,对于所涉及的尺寸公差也是通过各种详细的计算而得来。
为了给加工零件提供完整的书面说明,在本说明书中还对气缸体的作用及工作环境做了详细的介绍,对于所涉及到的参考文献也详尽列出。
最后,对于在加工过程中所用到的夹具设计原则也有所阐述,并给出了一套镗夹具的设计方案。
总之,本着完整,详尽,正确的原则,对于需要分析计算的地方在本说明书中都有相应的体现,最终给零件的生产加工提供最原始的数据资料。
关键词:气缸体工艺过程镗床钻床AbstractThis specification covers the gas cylinder body parts from blank selection to process to the processing steps for calculating all the process, in addition, for use in the boring and drilling fixture also do a brief explanation.First of all for the parts on some of the main processing surface, access to a large number of professional material to decide its processing technology, ensure the precision of parts, demands for dimensional tolerance is also involved through various detailed calculation and evolve. In order to give processing components to provide complete written explain, in this manual of the role of the cylinder block and working environment of a detailed introduction, involved in the reference also detailed list. Finally, in the course of processing for the kind of fixture design principles will be discussed, and gives a boring and fixture design scheme.In short, in line with complete, detailed, correct principles, the need for analysis and calculation of the place in this manual all has the corresponding reflect, and finally to the production and processing of parts provide the original data.目录绪论 (5)(1)课题背景及发展趋势 (5)(2)夹具的基本结构及夹具设计的内容 (5)第一章零件的分析 (7)1.1零件的作用 (7)1.2零件的工艺分析 (8)第二章确定毛坯 (9)第三章工艺规程设计 (10)3.1 定位基准的选择 (10)3.2 制定工艺路线 (11)3.3选择加工设备及刀,夹,量具 (13)3.4 加工工序设计 (14)3.4.1 切削用量的确定 (14)3.4.2 基本时间的确定 (18)第五章夹具设计 (19)5.1 夹具的基本要求与设计步骤 (19)5.2 定位机构的确定 (20)5.3 定位方案的论证 (20)总结 (22)参考文献 (24)感谢 (25)绪论机械制造与自动化专业毕业设计是对所学专业知识的一次巩固,是在进行社会实践之前对所学各课程的一次深入的综合性的总复习,也是理论联系实际的训练。
缸体的机械加工工艺与设计

缸体的机械加工工艺与设计发动机缸体在发动机零件中属于结构较为复杂的箱体类零件,它精度要求高,加工工艺较复杂,其加工质量的优良影响发动机整体性能,因此,它是发动机生产厂家所需注意的重点零件。
1,发动机缸体的工艺特性发动机缸体为发动机的骨架和基础零件,又是发动机装配时用到的基准零件。
缸体作用:支承活塞、曲轴、连杆等活动部件,保证工作时位置准确:保证发动机冷却、润滑和换气:提供各类辅助系统、组成部件以及发动机安装。
1.1工艺特性缸体是整体铸造结构,其上有四个缸套安装孔,缸体的水平隔板将其分成两部分,缸体的前端面排列有三个同轴线的惰轮轴孔和凸轮轴安装孔。
缸体工艺特点:形状、结构复杂:加工的孔、平面多:壁厚不均匀,刚度较低;加工精度要求较高,是典型的箱体类零件。
缸体主要加工面包括顶面、缸孔、主轴承座侧面、凸轮轴孔及主轴承孔等,它们的加工精度影响发动机的工作性能和装配精度,主要靠设备的精度、工夹具的可靠性及加工工艺的合理性来确保。
2.发动机缸体工艺设计方案的原则与依据工艺设计方案是工艺准备工作的前提,是工艺规程的设计以及工艺装备设计过程中的指导文件。
合理的工艺方案,有利于系统运用新型科学成果与先进的生产经验,从而保证产品质量,有效改善劳动条件,提高了工艺管理水平及工艺技术。
2.1艺的方案设计原则设计工艺方案在保证产品质量的同时,要考虑生产周期、成本与环境保护,根据企业能力,采用国内外先进的工艺装备与技术,提高企业的工艺水平。
发动机缸体的工艺设计应遵循以下准则:(1)加工设备选用原则:采取刚柔结合原则,选用加工设备,加工设备以卧式机床加工为主,少量工序用立式机床加工,关键工序一一用具有高精度的高速卧式加工中心加工缸孔、曲轴孔、平衡轴孔:非关键工序一一使用高效且有一定调动范围的专用机床铣削上下前后四个平面:(2)工序集中原则:关键工序一一精加工发动机缸孔、平衡轴孔、曲轴孔以及精铣缸盖结合面,用工序集中,装夹一次,一道工序就完成全部的加工内容,确保产品精度符合缸体关键性能的工艺能力及相关要求:(3)所有夹具采用美国或德国产的优质可靠液压装置,夹紧元件、液压泵以及液压控制元件:(4)整线均采用湿式加工,使用单机独立排屑,卧式加工中心关键的高精度加工使用恒温冷却并且其精过滤系统附加有高压高精度双回路带旁通,加工中心均带有高压内冷。
汽车发动机构造教案

第二章
曲柄连杆机构的构造与维修
学习目标
知识目标 1.能够正确描述曲柄连杆机构的组成、构 造和装配关系; 2.能够正确叙述曲柄连杆机构主要机件的 受力情况和工作
原理; 3.能够正确描述曲柄连杆机构的装配要求。
能力目标 1.会进行易损零件检测、修理或更换; 2.会进行曲柄连杆机构的装配与调整;
第一节
2.下止点 :活塞离曲轴回转中心最近处,一般指活塞下 行到最低位置,一般用英文缩写词BDC表示。
3.活塞行程(S):
上、下止点间的距离。
4.曲柄半径(R) :与连杆下端(即连杆大头)相连的曲柄
销中心到曲轴回转中心的距离(mm)。
显然,S=2R。曲轴每转一周,活塞移动两个行程。
5.气缸工作容积(Vh) :活塞从上止点到下止点所让出的空间
气缸盖
气缸盖上有冷却水套、燃烧室、进排气门道、气门导管孔和 进排气门座、火花塞孔(汽油机)或喷油器座孔。
气作缸用垫:保证气缸体与气缸盖间的密封,防止漏水、漏气。
构造: (1)金属—石棉垫 (2)金属骨架—石棉垫 (3)纯金属垫 安装注意:金属皮的金 属—石棉垫,缸口金属卷边 一面应朝向易修整接触面或硬平面。因卷边一面会对与其接触 的平面造成压痕变形。
单缸发动机 多缸发动机
水冷式发动机 风冷式发动机 直列式发动机 V形发动机和对置式发动机 汽油机 柴油机
现代汽车采用:四冲程、多缸、水冷式
往复活塞式
转子式
四冲程发动机
二冲程发动机
直列式发动机
V形发动机
二、发动机工作原理
发动机的工作过程是周期性地将燃料燃烧的热能 转变为机械能的过程。
2.压缩行程 曲轴带动活塞从上止点向下止点运动,进气门开启, 排气门关闭,气缸内活塞上腔容积逐渐减小,空气被压 缩,压力、温度升高。
摩托车发动机重要零部件材料与工艺总结

摩托车发动机重要零部件材料与工艺总结一、曲轴曲轴是发动机的重要旋转部件,它的材料和工艺直接影响着发动机的可靠性和耐久性。
目前,大多数摩托车发动机的曲轴采用高强度锻造钢材制作。
这种材料具有良好的机械性能和耐疲劳性能,能够承受发动机的高速旋转和震动负荷。
曲轴的制造工艺包括锻造、精密加工和热处理,以保证曲轴的强度和精度。
二、活塞活塞是发动机的重要运动部件,它的材料和工艺对发动机的燃烧效率和密封性能起着重要作用。
通常情况下,活塞材料应具有良好的导热性、机械性能和耐磨性。
目前,大多数摩托车发动机的活塞采用铝合金材料制作。
铝合金具有较好的导热性和机械强度,能够快速散热并承受活塞的工作负荷。
活塞的制造工艺包括铸造和机械加工,以保证活塞的精度和表面质量。
三、气缸和缸套气缸和缸套是发动机的重要固定部件,它们的材料和工艺对发动机的密封性和耐久性起着重要作用。
一般情况下,气缸和缸套材料应具有良好的导热性、机械性能和耐磨性。
目前,大多数摩托车发动机的气缸和缸套采用铸铁材料制作。
铸铁具有较好的导热性和机械强度,能够快速散热并承受气缸和活塞的工作负荷。
气缸和缸套的制造工艺包括铸造和机械加工,以保证其尺寸和表面质量。
四、气门和气门座气门和气门座是发动机的重要控制部件,它们的材料和工艺对发动机的密封性和耐久性起着重要作用。
一般情况下,气门和气门座材料应具有良好的耐热性、耐磨性和耐腐蚀性。
目前,大多数摩托车发动机的气门和气门座采用高温合金材料制作。
高温合金具有较好的耐热性和耐磨性,能够承受高温气体的冲击和磨损。
气门和气门座的制造工艺包括锻造、加工和表面处理,以保证其尺寸和表面质量。
综上所述,摩托车发动机的重要零部件的材料和工艺选择对发动机的性能和可靠性起着重要影响。
正确选择适合的材料和工艺,可以提高发动机的性能和可靠性,延长发动机的使用寿命。
因此,在摩托车发动机的设计和制造过程中,需要充分考虑这些因素,以提高整车的竞争力和市场表现。
汽轮机中压缸设计

汽轮机中压缸设计汽轮机中的压缸是汽轮机的一个重要组成部分,负责将蒸汽从锅炉输入到涡轮机中,将其压缩并加热,以产生动力。
压缸设计的好坏直接影响汽轮机的性能和效率。
首先,在设计压缸时,需要考虑汽轮机的工作参数,如蒸汽流量、蒸汽温度和压力等。
这些参数将直接影响压缸的尺寸和结构设计。
此外,还需要考虑到运行时的压力波动、冲击和振动等因素。
设计师需要根据这些综合因素制定设计方案。
其次,压缸的设计应根据汽轮机的实际使用情况,选择适当的材料。
通常情况下,高温高压蒸汽会导致金属的蠕变和疲劳破坏。
因此,通常选择的材料是高温合金,如铬钼钢和镍基合金。
这些材料具有良好的耐高温、耐蠕变和抗疲劳破坏的特性,可以确保压缸的长期使用寿命。
另外,压缸的内部结构设计也非常重要。
压缸内部需要有适当的排气装置和导向装置,以保证蒸汽在压缸内的流动顺畅,并尽可能地减小能量损失。
此外,导向装置的设计还应考虑到排气冲击、振动和噪音等问题。
这些设计细节的合理性将直接影响汽轮机的运行稳定性和效率。
此外,还需要考虑到压缸的密封性能。
由于蒸汽温度较高,如果压缸的密封不够好,在运行过程中会导致蒸汽泄漏,造成能量损失和效率降低。
因此,在压缸设计中需要采取一些密封措施,如采用密封环、填料密封或金属密封等方式,确保蒸汽在压缸内的流动过程中不发生泄漏。
最后,压缸的制造和安装也需要严格控制。
制造过程需要保证材料的质量和工艺的准确性,以确保压缸的可靠性和稳定性。
安装过程需要注意对所有零部件的正确安装和调整,以确保压缸的性能和效率。
总而言之,汽轮机中压缸的设计是一个复杂的工程,需要综合考虑多种因素。
在设计过程中,需要根据汽轮机的工作参数、材料选择、内部结构设计、密封性能和制造安装等方面进行综合考虑,以确保压缸的性能和效率达到最佳水平。
同时,设计师还需要不断进行测试和优化,以解决问题,并不断提高汽轮机的性能和效率。
- 1、下载文档前请自行甄别文档内容的完整性,平台不提供额外的编辑、内容补充、找答案等附加服务。
- 2、"仅部分预览"的文档,不可在线预览部分如存在完整性等问题,可反馈申请退款(可完整预览的文档不适用该条件!)。
- 3、如文档侵犯您的权益,请联系客服反馈,我们会尽快为您处理(人工客服工作时间:9:00-18:30)。
本技术属于发动机技术领域,具体涉及一种缸套及具有其的发动机、缸套的设计方法。
所述缸套包括缸套本体,在所述缸套本体的内壁上设有第一润滑区和位于第一润滑区下方的第二润滑区,第一润滑区上设有多个第一凹坑,第二润滑区上设有多个第二凹坑,第一凹坑的直径与深度比小于第二凹坑的直径与深度比。
根据本技术的缸套,在第一润滑区上设置小而深的第一凹坑,增加第一润滑区的油膜增加,从而降低第一润滑区的摩擦力,避免活塞或缸套过早磨损的情况,在第二润滑区上设置大而浅的第二凹坑,润滑油的一部分进入大而浅的凹坑中,在活塞环刮油能力一定的情况下,分布在第二润滑区的油膜厚度减小,从而减小活塞运动阻力。
权利要求书1.一种缸套,其特征在于,所述缸套包括缸套本体,在所述缸套本体的内壁上设有第一润滑区和位于所述第一润滑区下方的第二润滑区,所述第一润滑区上设有多个第一凹坑,所述第二润滑区上设有多个第二凹坑,所述第一凹坑的直径与深度的比值小于所述第二凹坑的直径与深度的比值。
2.根据权利要求1所述的缸套,其特征在于,所述第一凹坑的直径为20微米至80微米,所述第一凹坑的深度为4微米至10微米。
3.根据权利要求1所述的缸套,其特征在于,所述第二凹坑的直径为活塞环直径的0.15倍至0.5倍,所述第二凹坑的深度为1微米至4微米。
4.根据权利要求1所述的缸套,其特征在于,所述多个第一凹坑占所述第一润滑区的面积比小于所述多个第二凹坑占所述第二润滑区的面积比。
5.根据权利要求4所述的缸套,其特征在于,所述多个第一凹坑占所述第一润滑区的面积为10%至20%。
6.根据权利要求4所述的缸套,其特征在于,所述多个第二凹坑占所述第二润滑区的面积为30%-70%。
7.根据权利要求1所述的缸套,其特征在于,所述缸套本体的内壁上未设有所述第一凹坑与所述第二凹坑的区域的粗糙度范围为小于等于2微米。
8.根据权利要求1所述的缸套,其特征在于,所述第一凹坑与所述第二凹坑分别均匀地布置在所述第一润滑区与所述第二润滑区。
9.一种发动机,其特征在于,包括根据权利要求1至8中任一项所述的缸套。
10.一种缸套的设计方法,其特征在于,所述设计方法用于设计权利要求1至8中任一项所述的缸套,包括以下步骤:S1:根据实测温度计算出缸套的实际粘度:(1)式中,为粘度,T为实测温度,a和c为常数;根据缸压、活塞环弹力、活塞环与缸套的接触面积计算出载荷:载荷=(经验系数×缸压+活塞环弹力)/活塞环与缸套接触面积(2)根据实测的活塞的运动速度、载荷、粘度计算出轴承系数:轴承系数(缸套润滑系数)=粘度*速度/载荷(3)S2:将不同的轴承系数输入到摩擦试验机中,即可得到相关的摩擦系数,根据轴承系数与摩擦系数绘制斯特贝克曲线,并通过斯特贝克曲线的第一拐点区分边界润滑区域与混合润滑区域,通过第二拐点区分混合润滑区域与动压润滑区域;S3:根据轴承系数与曲轴转角的关系绘制第一曲线,根据活塞行程与曲轴转角绘制第二曲线,将第二拐点的值带入到第一曲线中对应相应的曲轴转角的值,将曲轴转角的值带入到第二曲线中得到活塞行程的对应值,从而得动压润滑区域对应在缸套中的位置;S4:在缸套上的动压润滑区域加工浅而大的凹坑,在缸套上的边界润滑区域及混合润滑区域加工深而小的凹坑。
技术说明书缸套及具有其的发动机、缸套的设计方法技术领域本技术属于发动机技术领域,具体涉及一种缸套及具有其的发动机、缸套的设计方法。
背景技术活塞式内燃机通过活塞在缸套内的往复运动来做功,活塞作往复运动时缸套与活塞、活塞环的摩擦占到总摩擦的50%以上,为了有效降低缸套与活塞、活塞环的摩擦,通常采用织构技术在缸套的内壁打孔使润滑油储存在孔中,通过润滑油增加缸套与活塞、活塞环的润滑以减小摩擦,此外,该结构还能增强缸套的耐磨能力。
由于缸套内不同的润滑区所需的润滑条件不同,而现有的缸套大多采用同一打孔模式在整个缸套的内壁进行打孔,造成有的润滑区域油膜太厚,阻碍活塞的运动,或造成有的润滑区域油膜太薄,增大缸套与活塞之间的摩擦,发生过早磨损的情况。
技术内容本技术的目的是至少解决现有缸套结构难以满足润滑需求的问题。
该目的是通过以下技术方案实现的:本技术第一方面提出了一种缸套,所述缸套包括缸套本体,在所述缸套本体的内壁上设有第一润滑区和位于所述第一润滑区下方的第二润滑区,所述第一润滑区上设有多个第一凹坑,所述第二润滑区上设有多个第二凹坑,所述第一凹坑的直径与深度的比值小于所述第二凹坑的直径与深度的比值。
根据本技术实施例的缸套,在所述缸套本体的内壁上设有第一润滑区和第二润滑区,根据不同的润滑区设置不同的直径与深度比的凹坑,在第一润滑区上设置小而深的第一凹坑,增加第一润滑区的油膜增加,从而降低第一润滑区的摩擦力,避免活塞或缸套过早磨损的情况,在第二润滑区上设置大而浅的第二凹坑,润滑油的一部分进入大而浅的凹坑中,在活塞环刮油能力一定的情况下,分布在第二润滑区的油膜厚度减小,从而减小活塞运动阻力。
另外,根据本技术实施例的缸套,还可以具有如下的技术特征:在本技术的一些实施例中,所述第一凹坑的直径为20微米至80微米,所述第一凹坑的深度为4微米至10微米。
在本技术的一些实施例中,所述第二凹坑的直径为活塞环直径的0.15倍至0.5倍,所述第二凹坑的深度为1微米至4微米。
在本技术的一些实施例中,所述多个第一凹坑占所述第一润滑区的面积比小于所述多个第二凹坑占所述第二润滑区的面积比。
在本技术的一些实施例中,所述多个第一凹坑占所述第一润滑区的面积为10%至20%。
在本技术的一些实施例中,所述多个第二凹坑占所述第二润滑区的面积为30%-70%。
在本技术的一些实施例中,所述缸套本体的内壁上未设有所述第一凹坑与所述第二凹坑的区域的粗糙度范围为小于等于2微米。
在本技术的一些实施例中,所述第一凹坑与所述第二凹坑分别均匀地布置在所述第一润滑区与所述第二润滑区。
本技术第二方面提出了一种发动机,所述发动机包括根据上述任一实施例所述的气缸盖。
根据本技术实施例的发动机,在所述缸套本体的内壁上设有第一润滑区和第二润滑区,根据不同的润滑区设置不同的直径与深度比的凹坑,在第一润滑区上设置小而深的第一凹坑,增加第一润滑区的油膜增加,从而降低第一润滑区的摩擦力,避免活塞或缸套过早磨损的情况,在第二润滑区上设置大而浅的第二凹坑,润滑油的一部分进入大而浅的凹坑中,在活塞环刮油能力一定的情况下,分布在第二润滑区的油膜厚度减小,从而减小活塞运动阻力。
本技术第三方面提供了一种缸套的设计方法,所述设计方法用于设计上述任一实施例所述的缸套,包括以下步骤:S1:根据实测温度计算出缸套的实际粘度:(1)式中,为粘度,T为实测温度,a和c为常数;根据缸压、活塞环弹力、活塞环与缸套的接触面积计算出载荷:载荷=(经验系数×缸压+活塞环弹力)/活塞环与缸套接触面积(2)根据实测的活塞的运动速度、载荷、粘度计算出轴承系数:轴承系数(缸套润滑系数)=粘度*速度/载荷(3)S2:将不同的轴承系数输入到摩擦试验机中,即可得到相关的摩擦系数,根据轴承系数与摩擦系数绘制斯特贝克曲线,并通过斯特贝克曲线的第一拐点区分边界润滑区域与混合润滑区域,通过第二拐点区分混合润滑区域与动压润滑区域;S3:根据轴承系数与曲轴转角的关系绘制第一曲线,根据活塞行程与曲轴转角绘制第二曲线,将第二拐点的值带入到第一曲线中对应相应的曲轴转角的值,将曲轴转角的值带入到第二曲线中得到活塞行程的对应值,从而得动压润滑区域对应在缸套中的位置;S4:在缸套上的动压润滑区域加工浅而大的凹坑,在缸套上的边界润滑区域及混合润滑区域加工深而小的凹坑。
根据本技术实施例的缸套的设计方法,通过该设计方法首先根据现有的参数计算出轴承系数,然后通过摩擦试验机得出轴承系数与摩擦系数之间的关系并找到不同润滑区域的拐点,再将拐点带入到轴承系数与曲轴转角曲线、活塞行程与曲轴转角,并得出不同润滑区域对应在缸套的位置,最后在缸套不同的润滑区域内通过织构技术加工不同的凹坑。
通过该设计方法得到的缸套,根据不同的润滑区设置不同的直径与深度比的凹坑,在第一润滑区上设置小而深的第一凹坑,增加第一润滑区的油膜增加,从而降低第一润滑区的摩擦力,避免活塞或缸套过早磨损的情况,在第二润滑区上设置大而浅的第二凹坑,润滑油的一部分进入大而浅的凹坑中,在活塞环刮油能力一定的情况下,分布在第二润滑区的油膜厚度减小,从而减小活塞运动阻力。
附图说明通过阅读下文优选实施方式的详细描述,各种其他的优点和益处对于本领域普通技术人员将变得清楚明了。
附图仅用于示出优选实施方式的目的,而并不认为是对本技术的限制。
而且在整个附图中,用相同的附图标记表示相同的部件。
在附图中:图1为本技术实施例的缸套结构示意图;图2为斯特贝克曲线图;图3为做功冲程缸套润滑系数、活塞行程分别与曲轴转角的关系图。
附图中各标记表示如下:100:缸套本体;10:第一润滑区、11:第一凹坑;20:第二润滑区、21:第二凹坑。
具体实施方式下面将参照附图更详细地描述本公开的示例性实施方式。
虽然附图中显示了本公开的示例性实施方式,然而应当理解,可以以各种形式实现本公开而不应被这里阐述的实施方式所限制。
相反,提供这些实施方式是为了能够更透彻地理解本公开,并且能够将本公开的范围完整的传达给本领域的技术人员。
应理解的是,文中使用的术语仅出于描述特定示例实施方式的目的,而无意于进行限制。
除非上下文另外明确地指出,否则如文中使用的单数形式“一”、“一个”以及“所述”也可以表示包括复数形式。
术语“包括”、“包含”、“含有”以及“具有”是包含性的,并且因此指明所陈述的特征、步骤、操作、元件和/或部件的存在,但并不排除存在或者添加一个或多个其它特征、步骤、操作、元件、部件、和/或它们的组合。
尽管可以在文中使用术语第一、第二、第三等来描述多个元件、部件、区域、层和/或部段,但是,这些元件、部件、区域、层和/或部段不应被这些术语所限制。
这些术语可以仅用来将一个元件、部件、区域、层或部段与第二区域、层或部段区分开。
除非上下文明确地指出,否则诸如“第一”、“第二”之类的术语以及其它数字术语在文中使用时并不暗示顺序或者次序。
因此,以下讨论的第一元件、部件、区域、层或部段在不脱离示例实施方式的教导的情况下可以被称作第二元件、部件、区域、层或部段。
为了便于描述,可以在文中使用空间相对关系术语来描述如图中示出的一个元件或者特征相对于第二元件或者特征的关系,这些相对关系术语例如为“内部”、“外部”、“内侧”、“外侧”、“下面”、“下方”、“上面”、“上方”等。
这种空间相对关系术语意于包括除图中描绘的方位之外的在使用或者操作中装置的不同方位。
例如,如果在图中的装置翻转,那么描述为“在其它元件或者特征下面”或者“在其它元件或者特征下方”的元件将随后定向为“在其它元件或者特征上面”或者“在其它元件或者特征上方”。