连铸工艺简介
炼钢连铸工艺流程介绍

炼钢连铸工艺流程介绍引言炼钢连铸是钢铁生产中的关键工艺之一,它通过高温熔炼钢料并在连续铸造过程中将其形成连续铸坯。
炼钢连铸工艺具有高效、节能、环保等优点,是现代钢铁工业的重要环节。
工艺流程概述炼钢连铸工艺流程可以分为炼钢、连铸两个主要环节。
炼钢环节炼钢环节包括原料准备、高炉冶炼、转炉冶炼等步骤。
原料准备炼钢的原料包括铁矿石、石灰石、焦炭等。
在原料准备环节,先对原料进行破碎、筛分等处理,以便于在后续步骤中充分混合。
高炉冶炼高炉冶炼是一种常用的炼钢方式,它通过将铁矿石、焦炭和石灰石等原料放入高炉中,并喷入空气使之燃烧,产生高温,从而使铁矿石还原成铁。
在高炉过程中,还会生成一些副产品,如炉渣。
转炉冶炼转炉冶炼是另一种常用的炼钢方式,它通过将熔融的铁水和生铁放入转炉中,通过喷吹氧气使其氧化,从而去除不需要的杂质。
转炉冶炼通常配合高炉冶炼使用,以提高炼钢效率。
连铸环节连铸环节将炼钢环节中获得的熔融钢水以连续流动的方式注入到铸造结晶器中,以形成连续铸坯。
结晶器结晶器是连铸的核心设备,它由冷却器壳体和冷却装置组成。
结晶器的作用是通过冷却装置将熔融钢料迅速冷却并形成铸坯。
冷却装置冷却装置包括水冷却、喷水冷却、喷雾冷却等方式,其目的是将熔融钢水迅速冷却,使其凝固成连续铸坯。
液态钢水的连续注入熔融钢水在结晶器内连续注入,经过冷却装置的处理后,逐渐凝固成为连续铸坯。
坯料切割和堆垛连续铸坯经过切割设备切割成合适长度的坯料,然后进行堆垛,以便于后续的加工和运输。
工艺优势及应用炼钢连铸工艺具有以下优势:1.高效:炼钢连铸工艺相比传统工艺更高效,能够实现连续生产,大大提高了生产效率。
2.节能:炼钢连铸工艺中的连铸环节省去了热轧等后续工序,节约了能源。
3.环保:炼钢连铸工艺减少了废气、废水等排放,有利于环境保护和可持续发展。
炼钢连铸工艺广泛应用于钢铁工业,特别是大型钢铁企业。
它不仅可以生产优质的钢材,还能够提供高效、可靠的生产线。
炼钢连铸工艺流程介绍
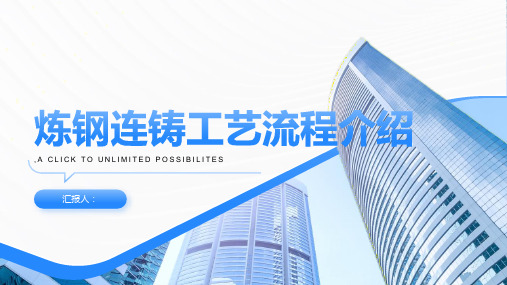
主要方法:采 用脱硫、脱磷、
脱碳等方法
设备:铁水预 处理设备,如 脱硫罐、脱磷
罐等
效果:提高铁 水质量,降低 钢中杂质含量, 提高钢的力学 性能和耐腐蚀
性
转炉炼钢原理:利用高温熔融的钢水与氧气反应,生成铁水与钢渣
转炉炼钢设备:包括转炉、氧枪、钢包等 转炉炼钢过程:将铁水倒入转炉,加入氧气进行反应,生成铁水与钢渣, 然后进行钢渣分离和钢水精炼 转炉炼钢优点:生产效率高,产品质量好,成本低,环保性能好
连铸机的维护:定期检查、维护和 保养,确保连铸机的正常运行
提高生产效率:采用先进的自动化技术,提高生产效率,降低生产成本 节能减排:采用节能环保技术,减少能源消耗,降低环境污染 提高产品质量:采用先进的工艺技术,提高产品质量,满足市场需求 智能化发展:采用先进的智能化技术,实现生产过程的智能化控制,提高生产效率和产品质量
工艺流程:钢液在炉外精炼 设备中进行脱硫、脱氧、脱
碳等处理
优点:提高钢液质量,减少 杂质,降低成本,提高生产
效率
连铸工艺:将钢水连续铸造成钢坯 的工艺
关键技术:连铸机的设计、控制和 维护
连铸机的类型:立式连铸机、卧式 连铸机等
连铸机的工作原理:钢水通过连铸 机,冷却凝固成钢坯
连铸机的控制:温度、速度、压力 等参数的控制
切割速度:根据铸坯尺寸和材质选择合适的 切割速度
切割温度:控制切割温度在1000℃左右, 防止铸坯过热或过冷影响切割质量
切割后处理:切割后对铸坯进行冷却、打 磨等处理,保证铸坯表面光滑、无毛刺
切割质量控制:定期对切割设备进行维护和 校准,确保切割质量稳定可靠。
目的:去除铁 水中的杂质和 气体,提高铁
电炉炼钢原理: 利用电弧热能 熔化废钢和铁 水,生产出钢
连铸机操作及工艺介绍

2.1连铸设备连铸机的机型
按结晶器是否移动分为: ☆固定式结晶器(包括固定振动结晶器)的各种连铸机
如立式连铸机、立弯式连铸机、弧形连铸机、椭圆形连铸
机、水平式连铸机等; ☆同步运动式结晶器的各种连铸机
按铸坯断面形状分为:方坯连铸机、圆坯连铸机、板坯连铸机 、
异型连铸机
1—立式连铸机;2—立弯式连铸机;3—直结晶器多点弯曲连铸机 4—直结晶器弧形连铸机;5—弧形连铸机; 6—多半径弧形(椭圆形)连铸机;7—水平式连铸机
单位长度的坯重:2.0976t/m, Q=226.54t/h
d=51.8mm
中间包用塞头与水口相配合来控制注流。
塞棒长时间在高温钢液中浸泡,容易
软化、变形,甚至断裂。为提高塞棒使用 寿命,一般用厚壁钢管作棒芯,浇注时在 芯管内插入直径稍小的钢管引入压缩空气
进行冷却,这对延长塞棒寿命有一定效果。
也可以将塞棒作为中间包吹氩棒,这样不 仅可以控制注流,还可以在一定程度上起 到净化钢液的作用。
长水口的材质有熔融石英质和铝碳质等
3.中间包
中间包是位于钢包与结晶器之间用于钢液浇注的装置,起着减 压、稳流、去渣、贮钢、分流及中间包冶金等重要作用。
中间包的容量是钢包容量的20%-40%。在通常浇注条件下,钢 液在中间包内停留时间应在8-10min,才能起到上浮夹杂物和 稳定注流的作用,为此,中间包目前是朝大容量和深熔池方向 发展,容量可达60-80t,熔池深为1000-1200mm。
1
式中
S下 S上 S 上 lm
100%
ε1—结晶器每米长度的倒锥度,%/m; S下—结晶器下口断面积,mm2; S上—结晶器上口断面积,mm2 lm—结晶器的长度,m。
倒锥度主要取决于铸坯断面、拉速和钢的高温收缩率 。浇铸 <0.08%的低碳钢的小方坯结晶器,其倒锥度为-0.5%/m;对于 >0.40%的高碳钢,倒锥度在(-0.8~-0.9)%/m。 板坯的宽厚比悬殊很大,厚度方向的凝固收缩比宽度方向收缩 要小得多。一般板坯结晶器宽边设计成平行的。其锥度按下式 计算:
连铸工艺

连铸:转炉生产出来的钢水经过精炼炉精炼以后,需要将钢水铸造成不同类型、不同规格的钢坯。
连铸工段就是将精炼后的钢水连续铸造成钢坯的生产工序,主要设备包括回转台、中间包,结晶器、拉矫机等。
连铸的工艺流程:将装有精炼好钢水的钢包运至回转台,回转台转动到浇注位置后,将钢水注入中间包,中间包再由水口将钢水分配到各个结晶器中去。
结晶器是连铸机的核心设备之一,它使铸件成形并迅速凝固结晶。
拉矫机与结晶振动装置共同作用,将结晶器内的铸件拉出,经冷却、电磁搅拌后,切割成一定长度的板坯。
连铸自动化控制主要有连铸机拉坯辊速度控制、结晶器振动频率的控制、定长切割控制等控制技术。
连铸的主要工艺设备介绍:钢包回转台钢包回转台:设在连铸机浇铸位置上方用于运载钢包过跨和支承钢包进行浇铸的设备。
由底座、回转臂、驱动装置、回转支撑、事故驱动控制系统、润滑系统和锚固件6部分组成。
单臂钢包回转台:由底座、立柱、上转臂、上转臂驱动装置、下转臂、下转臂驱动装置组成。
蝶形钢包回转台:由底座、升降液压缸、回转架、钢包支座、回转臂、平行连杆、驱动装置、防护板组成。
钢包回转台是连铸机的关键设备之一,起着连接上下两道工序的重要作用。
钢包回转台的回转情况基本上包括两侧无钢包、单侧有钢包、两侧有钢包三种情况,而单个钢包重量已超过140吨。
三种情况下,钢包回转台受力有很大不同,但无论在何种情况下,都要保证钢包回转台的旋转平稳,定位准确,起停时要尽可能减小对机械部分的冲击,为减少中间包液面波动和温降,要缩短旋转时间。
因此,我们在变频器的容量选择上,留有余地,即比电机功率加大一级。
同时利用变频器的s曲线加速功能,通过调整s曲线保证加、减速曲线平滑快速,减少对减速机的冲击,再通过PLC判断变速限位、停止限位实现旋转过程中高、低速自动变换及到位停车,同时满足了对旋转时间和平稳运行的要求。
顺时针,逆时针,旋转中间包是短流程炼钢中用到的一个耐火材料容器,首先接受从钢包浇下来的钢水,然后再由中间包水口分配到各个结晶器中去。
连铸工艺流程

连铸工艺流程连铸是一种常用的铸造工艺,适用于生产长条状或板状金属材料。
它是通过将熔化的金属直接倒入连续流动的水冷铜板中,使其冷却并形成连续的长条状或板状产品。
连铸工艺具有高效率、低能耗、高品质等优点,广泛应用于钢铁、铝合金等行业。
连铸工艺流程主要包括准备工作、连续浇铸、冷却和切割四个阶段。
首先是准备工作。
这个阶段包括准备熔炉、铜板、铸模、流动水和其他所需设备和材料。
熔炉中加入合适的金属原料,加热使其熔化。
同时,准备好冷却水,并确保其具有足够的流动性和温度适宜。
铜板和铸模是制造连铸机的主要部件,需要进行充分的清洗和检查,以确保表面平整和无缺陷。
接下来是连续浇铸。
将熔化的金属倒入连铸机的铜板中,通过喷头将金属喷向铸模,并使其连续地流动。
连铸机的喷头是一个关键部件,可以调整金属流动的速度和方向,以保证产品的质量。
同时,需要控制好浇注速度和温度,以避免金属过热或过冷,影响产品的性能。
然后是冷却。
在连铸过程中,金属材料与铜板接触,通过快速传热,使金属迅速冷却并凝固。
冷却水通过铜板流过,吸收金属的热量,并保持适宜的温度。
冷却水的流量和温度需要根据不同金属材料进行调整,以确保产品的结晶组织和力学性能。
最后是切割。
冷却后的连铸坯可以根据需要进行切割成适当的长度,以便进一步加工。
切割可以通过割断或切削进行。
割断是指使用切割设备将连铸坯切成所需长度,并去除不良部分。
切削是指使用机械切割工具将连铸坯切割成规定的尺寸和形状。
总之,连铸工艺是一种高效、高品质的铸造工艺,适用于生产长条状或板状金属材料。
其主要流程包括准备工作、连续浇铸、冷却和切割。
通过合理调整浇注速度、温度和冷却设备,可以制造出具有良好结晶组织和优异性能的产品。
连铸工艺的应用范围广泛,为钢铁、铝合金等行业的发展提供了重要的支撑。
连铸原理与工艺
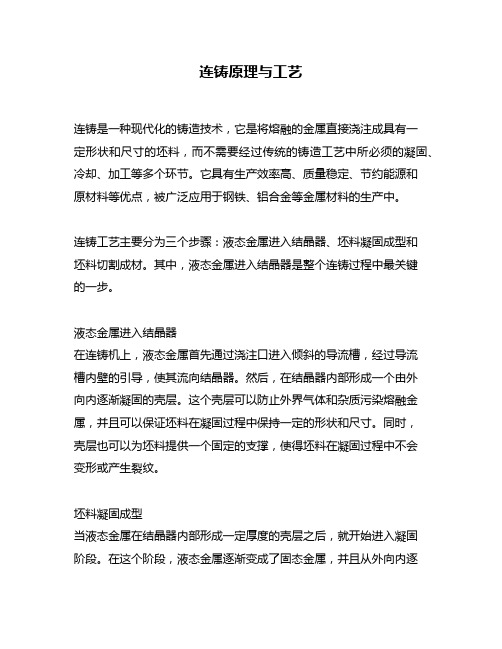
连铸原理与工艺连铸是一种现代化的铸造技术,它是将熔融的金属直接浇注成具有一定形状和尺寸的坯料,而不需要经过传统的铸造工艺中所必须的凝固、冷却、加工等多个环节。
它具有生产效率高、质量稳定、节约能源和原材料等优点,被广泛应用于钢铁、铝合金等金属材料的生产中。
连铸工艺主要分为三个步骤:液态金属进入结晶器、坯料凝固成型和坯料切割成材。
其中,液态金属进入结晶器是整个连铸过程中最关键的一步。
液态金属进入结晶器在连铸机上,液态金属首先通过浇注口进入倾斜的导流槽,经过导流槽内壁的引导,使其流向结晶器。
然后,在结晶器内部形成一个由外向内逐渐凝固的壳层。
这个壳层可以防止外界气体和杂质污染熔融金属,并且可以保证坯料在凝固过程中保持一定的形状和尺寸。
同时,壳层也可以为坯料提供一个固定的支撑,使得坯料在凝固过程中不会变形或产生裂纹。
坯料凝固成型当液态金属在结晶器内部形成一定厚度的壳层之后,就开始进入凝固阶段。
在这个阶段,液态金属逐渐变成了固态金属,并且从外向内逐渐缩小。
同时,由于液态金属的收缩率和晶粒长大率不同,所以在凝固过程中会形成一定数量的热裂纹和气孔。
为了解决这个问题,连铸工艺中采用了多种措施来控制坯料的凝固过程。
例如,在结晶器内部设置冷却水管道来降低壳层温度、使用高效保护气体来防止氧化等。
此外,在连铸工艺中还可以通过调整浇注速度、结晶器倾角、结晶器长度等参数来控制坯料的凝固速度和形状。
坯料切割成材当坯料完全凝固之后,它会被自动切割成一定长度的材料。
在连铸工艺中,切割方式主要分为两种:火焰切割和机械切割。
火焰切割是利用氧炔火焰将坯料加热到一定温度后进行切割,适用于较大尺寸的坯料。
机械切割则是使用钢丝、钢锯等工具将坯料进行切割,适用于较小尺寸的坯料。
总之,连铸工艺是一种高效、节能、环保的现代化铸造技术。
它通过控制液态金属的流动和凝固过程,使得金属材料可以以一种更加稳定和高效的方式生产出来。
同时,在连铸工艺中还可以通过调整参数、优化设备等手段来不断提高产品质量和生产效率,为现代制造业的发展做出了重要贡献。
连铸工艺知识点总结

连铸工艺知识点总结一、概述连铸是指在一台设备上同时进行浇铸和凝固过程的一种工艺。
它可以大幅度提高生产效率,减少材料浪费,提高产品质量。
在现代工业中,连铸工艺已经被广泛应用于钢铁、铝、铜等金属的生产中,成为了重要的生产工艺之一。
二、连铸的原理连铸的基本原理是利用连铸机,在一个连续的过程中,将金属液直接浇注至坯料模具中,然后通过顺序凝固、切割、堆垛等工序,最终产生坯料产品。
整个连铸过程中,金属液会先经过结晶器的处理,实现坯料的凝固,在这个过程中,还会进行一系列的拉伸、抽拉和冷却等操作,使得坯料的形状和尺寸得以控制和稳定。
三、连铸的优势1. 提高生产效率:相对于传统浇铸工艺,连铸可以大幅度提高生产效率。
因为它可以在同一个设备上连续进行浇铸和凝固过程,减少了生产过程中的空闲时间,从而实现了生产效率的提升。
2. 减少材料浪费:连铸工艺可以减少金属的二次加工过程,大大减少了金属的浪费,减少了材料的消耗,同时也减少了对环境的污染。
3. 提高产品质量:由于连铸工艺可以控制金属的凝固过程,使得坯料的材料结构更加均匀,从而提高了产品的质量。
4. 节省能源:相对于传统的浇铸工艺,连铸工艺可以在生产过程中更好地利用能源,降低能源的消耗。
四、连铸的工艺流程1. 铸坯模具的准备:连铸的第一步是准备好适用于连铸工艺的铸坯模具,通常采用的是一种特殊的铸坯模具,可以确保坯料的形状和尺寸的准确度。
2. 结晶器处理:在连铸的过程中,金属液会通过结晶器进行处理,实现坯料的凝固。
3. 拉伸、抽拉和冷却:在结晶器处理完后,金属液会经过一系列的拉伸、抽拉和冷却等操作,以控制坯料的形状和尺寸。
4. 切割和堆垛:最后,坯料会被切割为所需的尺寸,然后进行堆垛,完成整个连铸工艺的过程。
五、连铸的应用领域1. 钢铁生产:连铸工艺在钢铁生产中得到了广泛的应用,可以高效地生产出各种规格的钢铁坯料。
2. 铝合金生产:在铝合金生产中,连铸工艺可以提高产品质量,降低生产成本。
连铸工艺要点

连铸工艺要点连铸工艺是指连续铸造技术,是铁合金、钢铁等冶金行业中的一种主要生产工艺。
其工艺特点是连续铸造、高效能、高品质、节能环保等。
下面我们来了解一下连铸工艺的要点。
1. 连铸设备连铸设备是连铸工艺的核心,由铸机、结晶器、引伸器、切割机、输送机等组成。
铸机是整个设备的主体,结晶器是铸机的核心部分,引伸器是为了延长铸坯结晶器内的结晶长度,切割机是将连续铸坯切割成长度符合要求的坯料,输送机将坯料送到后续加工工序。
2. 连铸模具连铸模具是决定铸坯质量和工艺效果的重要因素,也是连铸设备的重要组成部分。
模具材料要求高强度、高温耐用、不易变形。
常用的模具材料有高硅铸铁、高铬铸铁、尿素醛树脂等。
模具结构形式有直立式、倾斜式、水平式等,不同结构形式适用于不同铸造条件。
3. 冷却水系统连铸过程中,冷却水系统起着非常重要的作用。
冷却水系统包括结晶器水口、结晶器壁面、引伸器、切割机等部位的冷却系统。
冷却水系统的稳定性和冷却效果直接影响铸坯的质量。
冷却水的温度、流量、压力等参数的调节需要精细控制。
4. 铸造工艺参数连铸工艺参数的优化对铸坯质量和生产效率有重要影响。
铸造参数包括结晶器冷却、引伸器速度、拉拔速度、切割位置等。
优化铸造参数可以控制铸坯中的缺陷、提高铸坯表面质量、降低成本并提高生产效率。
5. 质量控制质量控制是连铸工艺中的重要环节。
铸坯质量的稳定性和可控性直接影响产品的质量和生产效率。
质量控制包括铸坯表面质量检测、铸坯内部缺陷检测、坯料长度检测等。
不同的质量控制手段需要不同的检测设备和技术支持。
连铸工艺的要点包括连铸设备、连铸模具、冷却水系统、铸造工艺参数和质量控制。
在实际生产中,要根据不同的生产条件和产品要求,综合考虑这些要点,优化工艺流程,提高生产效率和产品质量。
- 1、下载文档前请自行甄别文档内容的完整性,平台不提供额外的编辑、内容补充、找答案等附加服务。
- 2、"仅部分预览"的文档,不可在线预览部分如存在完整性等问题,可反馈申请退款(可完整预览的文档不适用该条件!)。
- 3、如文档侵犯您的权益,请联系客服反馈,我们会尽快为您处理(人工客服工作时间:9:00-18:30)。
〃 设备高,建设费用大。 〃 钢液静压大,容易产生鼓肚。
10
机型的特点
(2)立弯式连铸机 结晶器下有垂直段,铸坯通过拉坯辊后
(钢水完全凝固或接近完全凝固),用顶弯 机使铸坯弯曲,进入圆弧段。
优点:
• 机身高度比立式低;
•有垂直段,夹杂物容易上浮且分布均匀;
连浇炉数
中间包连续浇注的炉数
冶金长度
铸坯的液芯长度 结晶器钢液面到铸坯中心液相完全凝固点的长度。
L
D2v 4K 2
冶金长度 结晶器内钢液面到拉矫机最后一对辊子中心线的长度。
18
3、拉坯速度(浇铸速度)
拉坯速度是指每分钟拉出铸坯的长度,单位是 m/min,简称拉速;
浇铸速度是指每分钟每流浇注的钢水量,单位是 t/(min•流),简称注速,
振动结晶器:1913年,瑞典人皮尔逊提出结晶器以可 变的频率和振幅做往复振动的想法。 1933年德国人 容汉斯(S.Junghans)真正将这一想法付诸实施。
4
1930年,铜和铝的连续铸造开始应用于生产。 钢的连铸要困难的多。钢的熔化温度高,导热性差,
不容易在短时间内形成足够厚的外壳,外壳很容易拉 断。 1947年美国的工程师和投资人I.Rossi开发出
缺点 结晶器内夹杂物不能上浮分离,且内弧集聚; 多半径,连铸机的对弧、安装、调整困难, 设备较复杂。
14
机型的特点
(6)水平连铸机
高度仅为立式连铸机的1/10节约基建费用 ; 技术不成熟。
15
3) 连铸机机型选择的原则
- 满足钢种和断面规格的要求; - 满足铸坯的质量要求; - 节约建设投资。
概述
模铸 过程:把钢水浇铸在由生铁制造的若干个钢锭模内 本质
• 钢水的热量传递给钢锭模 • 钢由液态(钢水)固态(钢锭)
产品:钢锭 方法:
上铸法 下铸法
1
连铸
连铸是使钢水连续的通 过连铸机变成固态钢坯 (连铸坯),发生连续 凝固。
主要设备包括钢包、 中间包、结晶器、结 晶器振动装置、二次 冷却和铸坯导向装置、 拉坯矫直装置、切割 装置、出坯装置等
按铸坯断面形状又可分为: 方坯连铸机、圆坯连铸机、板坯连铸机、异型连铸机、方/板 坯兼用型连铸机等.
机型
板坯
大方坯 小方坯
圆坯 异型坯
最大断面 mm×mm 300×2640 310×2500
600×600
160×160
φ 450
工字型 460×460×120 中空坯φ 450/6100
最小断面 mm×mm 130×250
6
连铸的优点(与模铸比较)
提高金属的收得率 7~12%。
建设费用降低30%左 右。
有助于实现钢铁生产的 紧凑化和连续化。
改善作业环境。 节约能源及原材料消耗,
降低人工费用.
7
连铸机的机型及其特点
按外形可分为: 立式连铸机、立弯式连铸机、弧形连铸机、椭圆形连铸 机、水平式连铸机等;
连铸机的机型及其特点
连铸的设想最早由英国 的发明家Bessemer提 出(1857年)
2
5.美国亚瑟(B.Atha)(1866年)和德 国土木工程师达勒恩(R.M.Daelen)(1877年)最 早提出以水冷、底部敞口固定结晶器为特征的常规连 铸概念。前者采用一个底部敞开、垂直固定的厚壁铁 结晶器并与中间包相连,施行间歇式拉坯;后者采用 固定式水冷薄壁铜结晶器、施行连续拉坯、二次冷却, 并带飞剪切割、引锭杆垂直存放装置。
最大理论拉速
k t 按结晶器出口处坯壳厚度计算
200×200 55×55 φ 100
经常浇注断面 mm×mm 180×700~ 300×2000
250×250~450×450 240×280~400×560
90×90~ 150×150 φ 200~φ 300
椭圆型120×140
2) 机型的特点
(1)立式连铸机:
结晶器、二冷段、拉坯和剪切沿垂直方向排列 优点:
例如:宝钢板坯连铸机: 直线段: 2.55m 弯曲半径:48.5/22.5/16.5/12/9.555m 矫直半径:9.555/11.5/16/31m 连铸机长度:39.39m
12
机型的特点
(4)弧形连铸机
分为弧形结晶器和直结晶器两种 优点:
机身高度为立式连铸机的1/2~1/3, 占地面积和 立弯式相同,基建费用低; 钢液静压小,鼓肚、裂纹等缺陷少; 加长机身容易,可高速浇铸,生产率高;
Junghans- Rossi连铸机,用来铸钢,获得成功。
5
从此,连铸技术经历了很长的发展历程: 40年代的试验开发。 50年代开始步入工业生产。 60年代弧形铸机的出现。 70年代由能源危机推动的大发展,新日铁大分钢厂实
现全连铸,推动了连铸技术的发展。 80年代日趋成熟的技术 90年代面临新的变革 凝固理论的研究,使连铸工艺科学化
16
连铸机的台数、机数、流数、连浇炉数
台数
共用一个盛钢桶,浇注1流或多流铸坯的1套连铸设备称为1台连铸机。
机数
凡具有独立传动系统和独立工作系统,当它机出现故障,本机仍能照常 工作的一组连续铸钢设备,称之为1个机组。1台连铸机可以由1个机 组或多个机组组成。
流数
1台连铸机能同时浇注铸坯的总根数称之为连铸机的流数。 1台连铸机有1个机组,又只能浇注1根铸坯,称为1机1流;若1台连铸 机有多个机组,又同时能够浇注多根铸坯,称其为多机多流;1个机组 能够同时浇注2根铸坯的称为1机2流。
缺点:
〃 机器设备占地面积较立式大; 〃 内弧夹杂物容易集聚; 〃 弧形结晶器加工较复杂; 〃 直结晶器在出口处为弧形和直线切点,容易漏钢。
13
机型的特点
(5)椭圆型连铸机(超低头连铸机) 优点:
机身高度低,厂房高度降低; 多次变形,每次变形量不大,铸坯 质量好; 钢液静压小,坯壳鼓肚量小,质量好。
•水平出坯,可以适当加长机身,铸坯的
定尺不受限制;
缺点:
•铸坯在一点弯曲,一点矫直,容易形成
裂纹;
•要求全凝固矫直,限制了生产率。
11
机型的特点
(3)带直线段的弧形连铸机 有垂直段,夹杂物容易上浮,具有立弯式 连铸机的优点; 多点弯曲。减小应力集中,裂纹少; 可在未完全凝固进入弧形段,故可以提高 生产率,增大拉速。