压力容器常见缺陷及无损检测方法
压力容器的检测方法
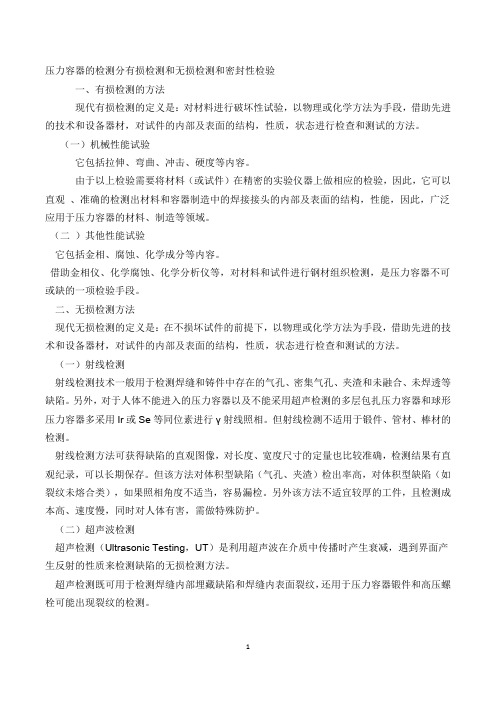
压力容器的检测分有损检测和无损检测和密封性检验一、有损检测的方法现代有损检测的定义是:对材料进行破坏性试验,以物理或化学方法为手段,借助先进的技术和设备器材,对试件的内部及表面的结构,性质,状态进行检查和测试的方法。
(一)机械性能试验它包括拉伸、弯曲、冲击、硬度等内容。
由于以上检验需要将材料(或试件)在精密的实验仪器上做相应的检验,因此,它可以直观、准确的检测出材料和容器制造中的焊接接头的内部及表面的结构,性能,因此,广泛应用于压力容器的材料、制造等领域。
(二)其他性能试验它包括金相、腐蚀、化学成分等内容。
借助金相仪、化学腐蚀、化学分析仪等,对材料和试件进行钢材组织检测,是压力容器不可或缺的一项检验手段。
二、无损检测方法现代无损检测的定义是:在不损坏试件的前提下,以物理或化学方法为手段,借助先进的技术和设备器材,对试件的内部及表面的结构,性质,状态进行检查和测试的方法。
(一)射线检测射线检测技术一般用于检测焊缝和铸件中存在的气孔、密集气孔、夹渣和未融合、未焊透等缺陷。
另外,对于人体不能进入的压力容器以及不能采用超声检测的多层包扎压力容器和球形压力容器多采用Ir或Se等同位素进行γ射线照相。
但射线检测不适用于锻件、管材、棒材的检测。
射线检测方法可获得缺陷的直观图像,对长度、宽度尺寸的定量也比较准确,检测结果有直观纪录,可以长期保存。
但该方法对体积型缺陷(气孔、夹渣)检出率高,对体积型缺陷(如裂纹未熔合类),如果照相角度不适当,容易漏检。
另外该方法不适宜较厚的工件,且检测成本高、速度慢,同时对人体有害,需做特殊防护。
(二)超声波检测超声检测(Ultrasonic Testing,UT)是利用超声波在介质中传播时产生衰减,遇到界面产生反射的性质来检测缺陷的无损检测方法。
超声检测既可用于检测焊缝内部埋藏缺陷和焊缝内表面裂纹,还用于压力容器锻件和高压螺栓可能出现裂纹的检测。
该方法具有灵敏度高、指向性好、穿透力强、检测速度快成本低等优点,且超声波探伤仪体积小、重量轻,便于携带和操作,对人体没有危害。
《压力容器安全技术监察规程》无损检测

无损检测的常用方法
1. 超声检测
利用超声波在材料中传播时遇到 不同界面产生的反射和折射现象, 来检测材料内部和表面缺陷的一 种方法。
2. 射线检测
利用不同物质对射线的吸收和衰 减程度不同,通过观察穿透后的 射线强度来检测材料内部缺陷的 一种方法。
总结词
常见的无损检测方法包括超声检 测、射线检测、磁粉检测、涡流 检测等。
详细描述
随着科技的不断发展,无损检测技术正朝着智能化、高 精度、高效率的方向发展。新型的无损检测设备和技术 不断涌现,如激光超声检测、红外热成像检测等。同时 ,随着人工智能和机器学习技术的发展,无损检测技术 也将逐渐实现自动化和智能化。与其他先进技术的结合 也将成为未来的趋势,如将无损检测技术与数值模拟技 术、大数据分析技术等相结合,以提高检测精度和效率 ,更好地服务于工业生产和产品质量控制。
在压力容器使用过程中,定期进行无损检 测是预防事故发生的重要手段。通过无损 检测,可以及时发现容器内部的裂纹、腐 蚀等缺陷,避免因缺陷扩展导致的事故发 生。常见的无损检测方法包括超声波检测 、射线检测等。
案例三:压力容器维修过程中的无损检测应用
总结词
提高维修效率
详细描述
在压力容器维修过程中,无损检测技术可以 帮助维修人员快速定位缺陷位置,提高维修 效率。通过无损检测,可以确定需要维修的 部位和程度,避免盲目维修和过度维修的情 况发生。常见的无损检测方法包括超声波检 测、射线检测、涡流检测等。
压力容器维修过程中的无损检测
维修过程中无损检测
在压力容器的维修过程中,无损检测 技术同样发挥着重要的作用。它可以 检测出容器在维修过程中可能产生的 新的缺陷,例如焊接过程中产生的焊 接缺陷。
目的
通过无损检测,可以及时发现并处理 维修过程中产生的新缺陷,确保压力 容器的维修质量和安全性。
检验在用压力容器常见缺陷与处理论文

浅谈检验在用压力容器常见缺陷与处理【摘要】:在用压力容器定期检验过程中,经常会遇到各种需要处理的缺陷,本文就一些常见缺陷的处理和注意事项进行了探讨,分别分析了宏观缺陷,表面裂纹,埋藏缺陷等,最后给出了具体的实例.【关键词】:压力容器;定期检验;缺陷处理【中图分类号】th49压力容器,英文:pressure vessel,是指盛装气体或者液体,承载一定压力的密闭设备。
贮运容器、反应容器、换热容器和分离容器均属压力容器。
在化工、能源、机械等行业应用非常广泛,国家为了确保它的安全运行制订了一系列的法规标准,本文结合自身检验工作的实际经验、根据相关法规对压力容器检验中常见缺陷的检验和处理进行探讨。
一、在用压力容器定期检验压力容器是一种广泛使用且具有爆炸危险的特种设备。
它承受着一定的压力、温度,且盛装的多是易燃、易爆、有毒的介质。
在使用中虽然没有运转机械那样的剧烈磨损、震动或高周次疲劳,但其工作条件十分恶劣,在使用中损坏的可能性非常大。
这是因为:(1)容器使用温度、压力的波动或频繁加载、卸压、使器壁受到较大的交变应力,因此在结构不连续部位(如焊接缺陷部位等应力集中处)会引起疲劳裂纹;(2)腐蚀介质使器壁减薄,造成受压时容器薄膜应力加大,或由于晶间腐蚀使材料的塑性、韧性变差;(3)部分容器的器壁长期在高温下承受压力载荷的作用,材料会发生蠕变;(4)用碳素钢、普通低合金钢等制造低温容器时,因这类钢材的韧性在低温下会大大降低,有脆性破裂的可能;(5)由于容器的支座、管道等安装不当或受震动造成容器附加应力增大;(6)压力容器停用时维护保养不当,器壁内外部都将受到腐蚀,而且腐蚀速度又往往比使用时更快;(7)压力容器由于结构不合理或制造原因存在着一些缺陷,这些缺陷有可能在使用中不断发展。
由于上述种种因素,即使是一台设计、制造质量符合规范的容器,投用以后随着时间的延长,也会不断产生这样或那样的缺陷。
因此,必须对每台容器进行定期检验,以便通过检验,及早发现缺陷,及时消除,确保压力容器安全运行,防止事故发生。
解析压力容器制造过程常见缺陷

解析压力容器制造过程常见缺陷1. 压力容器的概述作为盛装气体或液体的设备,压力容器最高的工作压力范围≥0.1MPa,多在特殊的环境(如高温、高压、易腐蚀)下使用。
为满足不同行业客户的多样化需求,压力容器的形态、结构和参数都向着多样化的方向发展,这意味着压力容器制造过程中涉及到多种规范性标准和条件的限制,因此必须采取严格的质量控制措施。
压力容器制造过程具有如下特征:(1)压力容器不同于通用机械产品,在运用软件技术对产品进行设计时,不仅要求设计人员掌握先进的计算机技术,更要具备化工设备的整体设计思想;(2)压力容器生产过程涉及金属冶金、材料化工、材料力学、机加工和检验检测等多个领域的内容,生产过程中受到多种条件的影响,因此生产过程具备较高的复杂性,生产人员需要具备相应的技术资格且对生产流程进行严格控制;(3)压力容器的工作条件比较苛刻且要求有较长的使用寿命,所盛装的介质又多是有毒有害、易燃易爆的气体或液体,因此压力容器制造过程中要特别重视安全性;(4)压力容器制造过程中是以钣金件的焊接质量为主要质量控制点,因此焊接质量是制造過程中相对薄弱的环节,需要采取特定的质量控制措施。
2. 压力容器制造过程的常见缺陷及质量控制对策2.1 材料使用的问题及质量控制对策在压力容器制造过程中,受到采购困难或对现有材料进行充分利用等因素的限制,材料代用问题在压力容器制造过程中时有发生,这给压力容器的安全性能埋下了极大的隐患。
压力容器制造过程中材料使用问题主要可以归纳为如下方面:选材考虑不周,过分强调材料某性能的优越性而导致其他性能的不合格;材料入库检验制度不完善,致使材质与所需不符,最终使用不符合标准的材料而导致压力容器质量不合格;(3)没有落实材料订货的技术要求,在订购材料时没有将设计文件的技术质量要求向供货商进行说明;(4)选择和使用的焊接材料不符规范,导致焊缝性能难以满足使用需求。
笔者认为,压力容器制造过程中材料的质量控制应从如下几个方面着手:第一,制造单位要在熟悉国家标准及图样设计要求的基础上,严格控制材料的采购流程,通过对材料进行复验或对供货单位进行考察、评审及追踪等办法,切实确保使用的压力容器材料符合相关标准。
压力容器检测中常见问题剖析
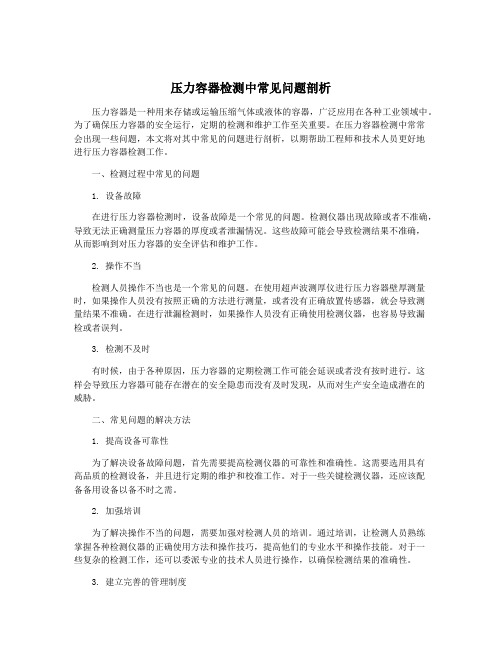
压力容器检测中常见问题剖析压力容器是一种用来存储或运输压缩气体或液体的容器,广泛应用在各种工业领域中。
为了确保压力容器的安全运行,定期的检测和维护工作至关重要。
在压力容器检测中常常会出现一些问题,本文将对其中常见的问题进行剖析,以期帮助工程师和技术人员更好地进行压力容器检测工作。
一、检测过程中常见的问题1. 设备故障在进行压力容器检测时,设备故障是一个常见的问题。
检测仪器出现故障或者不准确,导致无法正确测量压力容器的厚度或者泄漏情况。
这些故障可能会导致检测结果不准确,从而影响到对压力容器的安全评估和维护工作。
2. 操作不当检测人员操作不当也是一个常见的问题。
在使用超声波测厚仪进行压力容器壁厚测量时,如果操作人员没有按照正确的方法进行测量,或者没有正确放置传感器,就会导致测量结果不准确。
在进行泄漏检测时,如果操作人员没有正确使用检测仪器,也容易导致漏检或者误判。
3. 检测不及时有时候,由于各种原因,压力容器的定期检测工作可能会延误或者没有按时进行。
这样会导致压力容器可能存在潜在的安全隐患而没有及时发现,从而对生产安全造成潜在的威胁。
二、常见问题的解决方法1. 提高设备可靠性为了解决设备故障问题,首先需要提高检测仪器的可靠性和准确性。
这需要选用具有高品质的检测设备,并且进行定期的维护和校准工作。
对于一些关键检测仪器,还应该配备备用设备以备不时之需。
2. 加强培训为了解决操作不当的问题,需要加强对检测人员的培训。
通过培训,让检测人员熟练掌握各种检测仪器的正确使用方法和操作技巧,提高他们的专业水平和操作技能。
对于一些复杂的检测工作,还可以委派专业的技术人员进行操作,以确保检测结果的准确性。
3. 建立完善的管理制度为了解决检测不及时的问题,需要建立完善的压力容器管理制度。
在制度中规定压力容器的定期检测周期和方法,并严格执行。
也可以利用信息化技术,建立压力容器检测的信息系统,对检测过程和结果进行记录和管理,以便对压力容器的安全状况进行及时监控和评估。
压力容器何时进行无损检测以及无损检测方法的选择

压力容器何时进行无损检测以及无损检测方法的选择为了确保压力容器的安全质量,从压力容器使用的原材料开始都要通过无损检测来进行质量控制。
压力容器使用的原材料包括金属板材、管材、棒材、锻件和铸件等,需根据这些材料制造工艺和几何形状采用不同的无损检测技术。
1.1 压力容器用金属板材的无损检测压力容器用金属板材一般包括钢板、不锈钢板、双相钢板、铝及铝合金板材、钛及钛合金板材等,主要用于压力容器筒体和封头的制造。
所有的压力容器制造规范或标准均规定,处于剧毒、腐蚀、高压等较苛刻工作条件下的压力容器,其金属板材必须逐张进行超声检测。
此超声检测所用的探头为单晶或双晶直探头,主要用于检测金属板材在冶炼和轧制过程中产生的分层、白点和裂纹等缺陷。
大面积的钢板检测(包括边区检测和面积检测)一般都用充水耦合探头进行。
1.2 压力容器用管材的无损检测1 P% M3 u* e9 @: s" 压力容器用管材包括无缝钢管、焊接钢管、铜及铜合金管、铝及铝合金管、钛及钛合金管等,# F9 l: o- v# Y5 z三维网技术论坛主要用于换热器的制造。
7 n$ h* f4 M7 ]7 X无缝钢管采用液浸法或接触法超声波检测,主要检测纵向缺陷。
液浸法检测使用线聚焦或点聚1 l1 x. b, k, A7 a# E焦探头,接触法检测使用与钢管表面吻合良好的斜探头或聚焦斜探头。
; Z& C2 T0 Q" b2 w5 q: 所有类型的金属管材都可用涡流检测法探测其表面和近表面缺陷。
铁磁性钢管一般用外穿过式5 y6 A9 R& g1 |. {6 ?三维,cad,机械,技术,汽车,catia,pro/e,ug,inventor,solidedge,solidworks,caxa,时空,镇江线圈或放置式线圈检测;对于非铁磁性材料,管材口径较小时一般用外穿过式线圈检测。
三维网技术论坛7 Y& e0 l# P- ^. O2 a$ j; P1.3 压力容器用钢锻件的无损检测0 o5 r' I0 e3 V三维|cad|机械|汽车|技术|catia|pro/e|ug|inventor|solidedge|solidworks|caxa压力容器用钢锻件主要包括接管、法兰、凸元、管板和圆筒等。
锅炉压力容器的无损检测

锅炉压力容器的无损检测锅炉压力容器是用于贮存和输送液体和气体的压力容器,其工作环境的高温、高压等特殊条件会导致容器内部出现裂纹、腐蚀等缺陷,从而危及安全。
因此,对锅炉压力容器进行无损检测具有非常重要的意义。
无损检测是一种不破坏材料及物体的安全检测方法,包括多种技术手段,如超声波检测、磁粉检测、液体渗透检测、射线检测等。
下面将分别介绍几种常用的无损检测方法。
1. 超声波检测超声波检测是利用超声波在物体中传播的物理特性,通过探头向被测物体发射超声波,并通过超声波的反射、折射等特性来检测物体内部的缺陷。
具有高效、非接触、高灵敏度等优点,常用于检测锅炉压力容器壁厚、裂纹、孔洞等缺陷。
2. 磁粉检测磁粉检测是一种利用铁磁性材料表面磁场变化来检测表面裂纹、焊缝缺陷等的非接触检测方法。
该方法可以检测出微小的表面缺陷,特别适合于检测焊缝、螺纹等部位的裂纹缺陷。
3. 液体渗透检测液体渗透检测是一种通过毛细作用来检测表面微小缺陷的方法。
其原理是将一种渗透液体涂布在被测物表面,待渗透液体充分渗入缺陷中后,再将其表面擦干,再涂上一种能发出荧光的显色剂,观察被测物表面是否出现荧光信号。
该方法适用于检测表面裂纹、气孔等缺陷。
4. 射线检测射线检测是利用X射线、γ射线等辐射性物质的特性,通过将辐射源置于被测物体一侧,辐射能量穿透被测物体后,利用存储器、观察器等设备对被测物体进行成像和分析的检测方法。
该方法可以检测出内部结构和成分的缺陷。
总之,无损检测是一种重要的工程技术手段,可以有效地检测锅炉压力容器内部的裂纹、缺陷等问题,保障设备安全运行。
各种无损检测技术有其各自的优缺点,需要根据不同的实际情况进行选择。
同时,无损检测的技术水平、设备质量等也是保障检测质量的重要因素。
压力容器无损检测

利用人工智能技术 进行远程数据分析 和诊断
利用虚拟现实技术 进行远程检测和操 作训练
1
2
3Leabharlann 4绿色环保检测技术
01
超声波检测:利用超声波对 02
射线检测:利用射线对压力
压力容器进行无损检测,减
容器进行无损检测,减少对
少对环境的影响
环境的影响
03
红外热成像检测:利用红外热 04
激光检测:利用激光对压力
演讲人
目录
01. 无损检测技术 02. 无损检测的应用 03. 无损检测的发展趋势
1
无损检测技术
超声波检测
原理:利用超声波在介质中的传播和反射特 性,检测缺陷和厚度
优点:灵敏度高,可检测微小缺陷,对工件 表面要求低
应用:广泛应用于金属、非金属、复合材料 等材料的检测
局限性:对缺陷的定性和定量分析有一定难 度,需要结合其他检测方法进行综合分析
03
02
优点:检测灵 敏度高,可检 测出微小缺陷
04
应用:广泛应用 于压力容器、管 道、轴承等设备 的无损检测
2
无损检测的应用
压力容器制造
压力容器制造过程中,无损检测技术用于检测材料 缺陷和焊接质量。
无损检测技术可以及时发现并纠正制造过程中的问 题,提高压力容器的质量和安全性。
无损检测技术在压力容器制造过程中应用广泛,包 括超声波检测、射线检测、磁粉检测等。
无损检测技术的应用可以降低压力容器制造成本, 提高生产效率。
压力容器维修
01
压力容器无 损检测在维 修中的应用
02
检测压力容 器的缺陷和
损伤
03
确定维修方 案和修复方
法
- 1、下载文档前请自行甄别文档内容的完整性,平台不提供额外的编辑、内容补充、找答案等附加服务。
- 2、"仅部分预览"的文档,不可在线预览部分如存在完整性等问题,可反馈申请退款(可完整预览的文档不适用该条件!)。
- 3、如文档侵犯您的权益,请联系客服反馈,我们会尽快为您处理(人工客服工作时间:9:00-18:30)。
一、压力容器基本现状
2008年各类特种设备事故发生起数及所占比例 2008年各类特种设备事故发生起数及所占比例
二、压力容器常见缺陷
(一)腐蚀
最易产生的一种缺陷。存在就会腐蚀,只是程度的问题。 概念:金属与其接触的介质产生化学或者电化学的结果。 腐蚀的表现形式(破坏形态): 1.匀蚀:设计时考虑了腐蚀裕量,解决办法周期性的壁 1.匀蚀:设计时考虑了腐蚀裕量,解决办法周期性的壁 厚测量。 2.坑蚀:坑深度小于坑直径,局部的,超声波难测量其 2.坑蚀:坑深度小于坑直径,局部的,超声波难测量其 厚度,需要打磨修平。 3.缝蚀:介质聚集在缝隙浓缩而发生局部腐蚀,不绣钢 3.缝蚀:介质聚集在缝隙浓缩而发生局部腐蚀,不绣钢 易发生缝蚀。 (磨损腐蚀)
避免晶间腐蚀的方法:使用Ti、Nb不锈钢;使用低炭、超低炭; 避免晶间腐蚀的方法:使用Ti、Nb不锈钢;使用低炭、超低炭; 低N、P、Si等有害杂质不锈钢;经过固熔化或者稳定化处理。 Si等有害杂质不锈钢;经过固熔化或者稳定化处理。 焊缝热影响区是最易产生晶间腐蚀的敏感区域。 晶间腐蚀产生的条件:(1 晶间腐蚀产生的条件:(1)酸性介质,如,工业醋酸、硝酸、 盐酸、甲酸等,但气相酸一般不产生晶间腐蚀。 (2)温度> 50℃ 。 50℃ 晶间腐蚀外观仍保持金属光泽。
一、压力容器基本现状
(二)2008年特种设备安全状况 (二)2008年特种设备安全状况
3、事故特点 锅炉和电梯事故上升最大。与2007年相比,锅炉和电梯 锅炉和电梯事故上升最大。与2007年相比,锅炉和电梯 事故起数分别上升32%和15%,主要是小型蒸汽锅炉事 事故起数分别上升32%和15%,主要是小型蒸汽锅炉事 故和电梯维修保养环节事故上升。气瓶、压力管道、场 (厂)内专用机动车辆、大型游乐设施、压力容器事故 (厂)内专用机动车辆、大型游乐设施、压力容器事故 则明显下降,事故起数同比分别下降55%、44%、42%、 则明显下降,事故起数同比分别下降55%、44%、42%、 25%、24%。 25%、24%。
一、压力容器基本现状
(二)2008年特种设备安全状况 (二)2008年特种设备安全状况
2、事故原因 因安全附件失效或安全装置损坏引发的事故17起,占事 因安全附件失效或安全装置损坏引发的事故17起,占事 故总起数的5.5%。其中主要是锅炉、压力容器、压力管 故总起数的5.5%。其中主要是锅炉、压力容器、压力管 道、电梯和起重机械安全装置失效或者损坏的问题。 因设备制造安装缺陷引发的事故16起,占事故总起数的 因设备制造安装缺陷引发的事故16起,占事故总起数的 5.2%。表现为焊接缺陷、材质劣化、未按工艺要求制造、 5.2%。表现为焊接缺陷、材质劣化、未按工艺要求制造、 维修质量低劣等,集中发生在压力容器、电梯、起重机 械和锅炉等特种设备中。 因违规充装引发的气瓶事故9起,占事故总数的2.9%。 因违规充装引发的气瓶事故9起,占事故总数的2.9%。 主要表现为充装不符合安全技术规范或标准的气瓶、未 按规定进行充装前安全检查、气瓶混装、野蛮装卸等。 集中发生在工业气瓶和车用气瓶中。
压力容器常见缺陷 及无损检测方法介绍
周献民 岳阳市特种设备检验检测所
提 纲
(一)压力容器基本现状 (二)压力容器常见缺陷 (三)压力容器常见破坏形式 (四)压力容器常用检测方法 (五)补充:特种设备作业人员的责任
一、压力容器基本现状
(一)2008年特种设备基本情况 (一)2008年特种设备基本情况
1、特种设备使用情况 2008年全国已办理使用登记的特种设备数量达到521.11 2008年全国已办理使用登记的特种设备数量达到521.11 万台,比2007年增加17.5%。另有气瓶1.32亿只,压力管 万台,比2007年增加17.5%。另有气瓶1.32亿只,压力管 道63.3万公里。全国现有持证的特种设备作业人员473.15 63.3万公里。全国现有持证的特种设备作业人员473.15 万人,其中,2008年考核发证152.47万人。 万人,其中,2008年考核发证152.47万人。
特种设备数量分布
2008年特种设备分布见下图 2008年特种设备分布见下图
一、压力容器基本现状
2008年特种设备数量分布图 2008年特种设备数量分布图
一、压力容器基本现状
(一)2008年特种设备基本情况 (一)2008年特种设备基本情况
2、特种设备生产情况 至2008年底,现有特种设备生产(含设计、制造、安装、 2008年底,现有特种设备生产(含设计、制造、安装、 改造、维修、气瓶充装)单位4.26万家,比2007年增加 改造、维修、气瓶充装)单位4.26万家,比2007年增加 5.7%。其中,设计单位2767家,制造单位12403家,安装 5.7%。其中,设计单位2767家,制造单位12403家,安装 改造维修单位15857家,气瓶充装单位11620家。 改造维修单位15857家,气瓶充装单位11620家。
一、压力容器基本现状
(二)2008年特种设备安全状况 (二)2008年特种设备安全状况
3、事故特点 各类事故的行业分布状况。工业锅炉事故主要发生在化 工与热电联产行业,小型蒸汽锅炉事故主要发生在服装 加工、食品加工、造纸、木材加工等中小型轻工行业, 热水锅炉事故主要发生在宾馆、洗浴中心等服务业。压 热水锅炉事故主要发生在宾馆、洗浴中心等服务业。压 力容器事故主要发生在造纸、小型轻化工、食品、建材、 力容器事故主要发生在造纸、小型轻化工、食品、建材、 服装、饲料等行业。气瓶事故主要发生在气瓶充装、运 服装、饲料等行业。 输行业。起重机械事故主要发生在造船、公路桥梁建设、 建材等行业。电梯事故中客梯事故主要发生在建设工程、 医院、学校、宾馆、商场等建设和服务业;货梯事故主 要发生在服装加工、包装等小型轻工行业。场(厂)内 专用机动车辆事故主要发生在金属加工与机械制造业和 公路、水利建设以及港口等物流运输业。
二、压力容器常见缺陷
(一)腐蚀
腐蚀的表现形式(破坏形态): 4.晶间腐蚀:Cr-Ni不锈钢处于400~850℃(也有说 4.晶间腐蚀:Cr-Ni不锈钢处于400~850℃ 317~816℃为敏感温度区)时,在晶界形成Cr23C6使晶 317~816℃为敏感温度区)时,在晶界形成Cr23C6使晶 界贫铬,如果铬含量降到钝化极限12%以下,贫铬区开 界贫铬,如果铬含量降到钝化极限12%以下,贫铬区开 始活化,晶界和晶粒形成原电池而产生腐蚀。这是贫铬 理论,还有偏析理论。
一、压力容器基本现状
2001年至 2001年至2008年万台事故起数趋势图 年至2008年万台事故起数趋势图
一、压力容器基本现状
(二)2008年特种设备安全状况 (二)2008年特种设备安全状况
2、事故原因 因违规使用造成的事故244起,占事故总数的79.5%。违 因违规使用造成的事故244起,占事故总数的79.5%。违 规使用是特种设备事故发生的主要原因,表现为使用非 法设备、使用管理混乱、作业人员违章操作、操作不当 甚至无证作业、维护缺失等。集中发生在起重机械、电 梯、锅炉、场(厂)内专用机动车辆、压力容器等特种 设备中。 因未按规定检验或因客观原因无法实施检验,致使未及 时发现和消除设备缺陷引发的事故21起,占事故总起数 时发现和消除设备缺陷引发的事故21起,占事故总起数 的6.8%。其中主要是起重机械钢丝绳检验、维护不当导 6.8%。其中主要是起重机械钢丝绳检验、维护不当导 致钢丝绳断裂的问题。
二、压力容器常见缺陷
(一)腐蚀
腐蚀的表现形式(破坏形态): 6.氢腐蚀:包括氢脆和氢浸蚀两种形态。H原子半径最小,容易渗 6.氢腐蚀:包括氢脆和氢浸蚀两种形态。H 入金属晶格造成晶格畸变,导致晶粒间结合力降低而发生氢脆。氢 浸蚀则表现为材料表面或内部脱碳,或产生氢鼓包。
(二)裂纹
表现为应力裂纹(腐蚀裂纹)和疲劳裂纹。 腐蚀裂纹的形成:腐蚀在表面形式缺口或原有缺口扩大而 产生应力集中,或者削弱金属的晶间结合力,应力则加速 腐蚀的进展。 疲劳裂纹的产生:交变应力(包括温度应力)、局部。
二、压力容器常见缺陷
(一)腐蚀
腐蚀的表现形式(破坏形态): 5.应力腐蚀:条件:特定材料、特定腐蚀介质、静拉应 5.应力腐蚀:条件:特定材料、特定腐蚀介质、静拉应 力、裂纹形态。
应力腐蚀裂纹形态是单一的或者混合的。 应力足够低都会发生,成为低应力破坏的重要形式之一。 液氨对碳钢或者低合金钢应力腐蚀条件: 液态氨,含水量小(≤0.2%),且可能受空气(主要是O2 液态氨,含水量小(≤0.2%),且可能受空气(主要是O2 或者CO2)污染的场合; 或者CO2)污染的场合; 使用温度≥ 使用温度≥5℃。 H2S对钢质材料的应力腐蚀 H2S对钢质材料的应力腐蚀 热碱对钢质材料的应力腐蚀 Cl离子对不锈钢的应力腐蚀等。 Cl离子对不锈钢的应力腐蚀等。
特种设备生产单位 2008年特种设备生产单位数量分布见下图
一、压力容器基本现状
2008年特种设备生产单位数量分布图 2008年特种设备生产单位数量分布图
一、压力容器基本现状
(二)2008年特种设备安全状况 (二)2008年特种设备安全状况
1、事故总体情况 2008年共发生特种设备事故307起,死亡317人,受伤461 2008年共发生特种设备事故307起,死亡317人,受伤461 人,直接经济损失9789.48万元,与2007年同期相比,事 人,直接经济损失9789.48万元,与2007年同期相比,事 故总起数增加20%,死亡人数减少2.5%,受伤人数增加 故总起数增加20%,死亡人数减少2.5%,受伤人数增加 62%。其中,重大事故3起,较大事故74起,一般事故 62%。其中,重大事故3起,较大事故74起,一般事故 230起,未发生特大事故。 230起,未发生特大事故。 2008年万台设备事故起数为0.74起,万台设备死亡人数 2008年万台设备事故起数为0.74起,万台设备死亡人数 为0.82人,比2007年分别下降8.6%、8.9%(扣除停用设 0.82人,比2007年分别下降8.6%、8.9%(扣除停用设 备,下同),完成了国务院安委会下达的特种设备事故 死亡318人以下的控制指标。 死亡318人以下的控制指标。 2001年至2008年万台事故起数趋势图(见下页图) 2001年至2008年万台事故起数趋势图(见下页图)