常用无损检测方法的特点及应用
五大类常用无损检测方法1500字

五大类常用无损检测方法1500字无损检测方法是一种对材料、零部件、构件进行检验、测量和评价的技术手段,无需破坏或损坏被测物体,可以对材料的内部缺陷进行检测和评价,广泛应用于航空航天、建筑、能源、交通、电力等领域。
常用的无损检测方法主要有五大类,分别是超声波检测、放射性检测、磁粉检测、涡流检测和红外检测。
超声波检测是利用超声波在材料中的传播和反射来检测材料的内部缺陷的一种方法。
这种方法适用于对金属、塑料、玻璃等材料进行检测。
超声波通过被测物体时,会发生超声波的传播和反射现象。
通过测量超声波的传播时间和反射强度,可以判断材料内部的缺陷情况,如裂纹、夹杂和孔隙等。
放射性检测是利用放射性同位素发出的射线对被测物体进行检测的一种方法。
这种方法适用于对金属材料、混凝土等材料进行检测。
放射性检测的原理是通过射线的衰减来判断材料的密度和缺陷情况。
射线在材料中的传播和衰减受材料的密度和吸收能力的影响,通过测量射线的强度和衰减情况,可以判断材料内部的缺陷情况。
磁粉检测是利用磁性材料在磁场中的磁特性对被测物体进行检测的一种方法。
这种方法适用于对金属材料的表面缺陷进行检测。
磁粉检测的原理是通过在被测物体表面施加磁场,当磁性材料中存在缺陷时,磁场会发生变化,通过观察磁粉的分布情况,可以判断材料表面的缺陷情况。
涡流检测是利用交变电磁场在导体中诱导涡流的原理对被测物体进行检测的一种方法。
这种方法适用于对导电材料的表面和近表面缺陷进行检测。
涡流检测的原理是当导体中存在缺陷时,交变电磁场会诱导涡流的产生,通过测量涡流的大小和分布情况,可以判断材料表面和近表面的缺陷情况。
红外检测是利用物质发射、吸收和反射红外辐射的特性对被测物体进行检测的一种方法。
这种方法适用于对温度和热传导性能进行检测。
红外检测的原理是通过测量被测物体发射、吸收和反射的红外辐射的强度,可以判断被测物体的温度和热传导性能。
以上五种常用的无损检测方法各有其适用范围和原理,可以根据被测物体的不同特点和需要进行选择。
无损检测技术的特点及其在质量控制领域的应用

无损检测技术的特点及其在质量控制领域的应用无损检测技术是一种能够在不破坏被测物体的前提下对其进行检测的技术手段。
它可以通过各种物理、化学和工程技术手段,对材料、组件和结构的缺陷、性能和结构的完整性进行检测和评估。
无损检测技术在质量控制领域具备一定的特点,广泛应用于航空航天、汽车、电力、核工业、钢铁等行业,为提高产品质量、确保工程安全和保护环境做出了重要贡献。
无损检测技术的特点主要体现在以下几个方面:1. 非破坏性:无损检测技术不需要对被测物体进行破坏性试验,能够在不影响其使用性能的前提下进行准确的检测,避免了对被测物体的损伤和浪费。
2. 全面性:无损检测技术可以对被测物体的各个方面进行检测,包括材料缺陷、结构完整性、性能评估等。
不同的无损检测方法可以相互补充,提高整体检测能力。
3. 高灵敏度:无损检测技术可以非常精确地检测到微小的缺陷,如内部裂纹、组织结构变化等。
这种高灵敏度可以帮助及早发现潜在的缺陷,避免事故的发生和人员的伤害。
4. 非接触性:无损检测技术可以通过非接触性的方式进行检测,不需要与被测物体直接接触。
这样可以避免操作人员受到危险物品的伤害和污染。
无损检测技术在质量控制领域有着广泛的应用。
以下是几个重要的应用领域:1. 航空航天领域:无损检测技术在航空航天领域中起着至关重要的作用。
它可以用于对飞机、火箭等运载工具的结构和材料进行检测,以确保其安全可靠。
无损检测技术可以及早发现隐蔽的缺陷,避免事故的发生。
2. 汽车制造领域:无损检测技术在汽车制造领域中被广泛应用。
它可以对汽车零部件的质量和性能进行检测,确保其达到设计要求。
无损检测技术可以提高汽车的安全性和可靠性,降低事故的发生率。
3. 电力行业:无损检测技术在电力行业中用于对电力设备和输电线路的检测。
它可以帮助检测电力设备的缺陷和故障,及早发现潜在的安全隐患,确保电力系统的可靠运行。
4. 核工业:无损检测技术在核工业中起着重要的作用。
无损检测的原理及应用
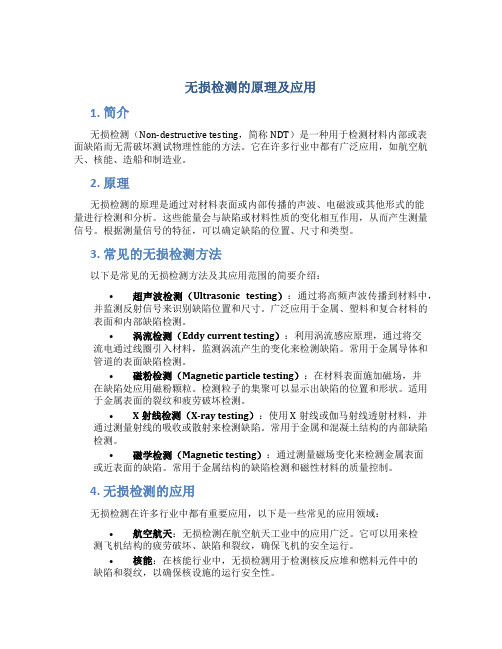
无损检测的原理及应用1. 简介无损检测(Non-destructive testing,简称NDT)是一种用于检测材料内部或表面缺陷而无需破坏测试物理性能的方法。
它在许多行业中都有广泛应用,如航空航天、核能、造船和制造业。
2. 原理无损检测的原理是通过对材料表面或内部传播的声波、电磁波或其他形式的能量进行检测和分析。
这些能量会与缺陷或材料性质的变化相互作用,从而产生测量信号。
根据测量信号的特征,可以确定缺陷的位置、尺寸和类型。
3. 常见的无损检测方法以下是常见的无损检测方法及其应用范围的简要介绍:•超声波检测(Ultrasonic testing):通过将高频声波传播到材料中,并监测反射信号来识别缺陷位置和尺寸。
广泛应用于金属、塑料和复合材料的表面和内部缺陷检测。
•涡流检测(Eddy current testing):利用涡流感应原理,通过将交流电通过线圈引入材料,监测涡流产生的变化来检测缺陷。
常用于金属导体和管道的表面缺陷检测。
•磁粉检测(Magnetic particle testing):在材料表面施加磁场,并在缺陷处应用磁粉颗粒。
检测粒子的集聚可以显示出缺陷的位置和形状。
适用于金属表面的裂纹和疲劳破坏检测。
•X射线检测(X-ray testing):使用X射线或伽马射线透射材料,并通过测量射线的吸收或散射来检测缺陷。
常用于金属和混凝土结构的内部缺陷检测。
•磁学检测(Magnetic testing):通过测量磁场变化来检测金属表面或近表面的缺陷。
常用于金属结构的缺陷检测和磁性材料的质量控制。
4. 无损检测的应用无损检测在许多行业中都有重要应用,以下是一些常见的应用领域:•航空航天:无损检测在航空航天工业中的应用广泛。
它可以用来检测飞机结构的疲劳破坏、缺陷和裂纹,确保飞机的安全运行。
•核能:在核能行业中,无损检测用于检测核反应堆和燃料元件中的缺陷和裂纹,以确保核设施的运行安全性。
•制造业:无损检测在制造业中用于产品质量的控制。
无损检测方法

无损检测方法
无损检测是一种非破坏性的检测方法,主要用于检测材料或零部件的内部质量和结构缺陷,例如裂纹、气孔、杂质等。
它可以通过不同的物理原理和技术手段来实现。
下面将介绍几种常用的无损检测方法。
一、X射线检测
X射线检测是利用X射线的穿透性质来检测材料内部的缺陷的一种方法。
该方法具有穿透力强、检测效率高的特点,适用于各种材料的检测。
在检测过程中,通过测量射线透射过程中的吸收和散射情况,可以确定材料的内部结构和缺陷。
二、超声波检测
超声波检测是利用超声波在材料中传播的特性来检测材料的内部缺陷的一种方法。
该方法采用超声波探测器向被测材料发射超声波,并记录超声波的传播时间和强度。
通过分析实测数据可以确定材料的内部结构和缺陷。
三、涡流检测
涡流检测是利用涡流感应现象来检测材料表面和近表面的缺陷的一种方法。
该方法通过将交变电流通过探测线圈引入被测材料中,当线圈靠近材料表面时,由于磁感应强度的变化,会产生涡流。
通过测量涡流的强度和分布情况,可以确定材料的表面和近表面的缺陷。
四、磁粉检测
磁粉检测是利用磁场分布的变化来检测材料表面和近表面缺陷
的一种方法。
该方法通过在被测材料表面或近表面施加磁场,并在磁场作用下将磁粉粘附在缺陷处。
通过观察磁粉的分布情况,可以确定材料的表面和近表面的缺陷。
以上介绍的是常用的几种无损检测方法,它们各具特点,在不同的检测场景中都有广泛应用。
无损检测方法能够实现对材料和零部件的内部结构和缺陷的快速、准确检测,对于保证产品质量和安全具有重要意义。
无损检测有哪些方法(优秀)

无损检测有哪些方法(优秀)无损检测是一种使用非破坏性方法来评估材料和构件内部的缺陷或变化的方法。
它广泛应用于各个行业,包括航空航天、汽车、能源、建筑等。
以下是几种常见和优秀的无损检测方法:1.超声波检测(UT):通过传送超声波波束到被检测材料中,检测物体的内部缺陷或变化。
它能够检测到各种类型的缺陷,如裂纹、气泡、夹杂物等,并能提供它们的大小、形状和位置信息。
2.射线检测(RT):使用射线(如X射线和伽马射线)照射材料或构件,通过对射线的衰减程度来检测内部缺陷或变化。
射线检测可以快速、准确地检测到各种类型的缺陷,并能够提供它们的位置和大小信息。
3.磁粉检测(MT):通过在被检测物体表面施加磁场,然后将磁粉散布在表面上,当磁粉与表面裂纹处的磁场相互作用时,可以形成可见的磁粉沉积。
这种方法可以检测到表面和近表面的裂纹。
4.渗透检测(PT):将可渗透性液体应用于被检测物体的表面,待其渗入表面裂纹或孔隙后,再用吸收液清洗表面,并施加显影剂使液体从裂纹或孔隙中渗透出来,可通过观察显影涂层的变化来检测缺陷。
5.磁疑检测(ET):利用电磁感应原理,通过在被检测物体上施加交变电流产生的磁场,来检测材料中的缺陷。
磁疑检测可以检测到各种类型的缺陷,如表面裂纹、疑似裂纹等。
6.红外热成像(IR):通过测量物体表面的热量分布来检测内部缺陷或问题。
红外热成像能够迅速扫描大面积,并提供高分辨率的热图,用于检测热损伤、漏水、电路问题等。
7.电涡流检测(ET):通过在被检测物体上施加交变电流产生的涡流,来检测材料中的缺陷或变化。
电涡流检测可以用于检测导体材料的电导率、厚度和附着度等。
除了以上方法,还有一些其他的无损检测方法,如声发射检测、微波检测、电磁超声波检测等。
每种方法都有其适用的领域和特点,选择最合适的方法将提高无损检测的效果和准确性。
无损检测综述
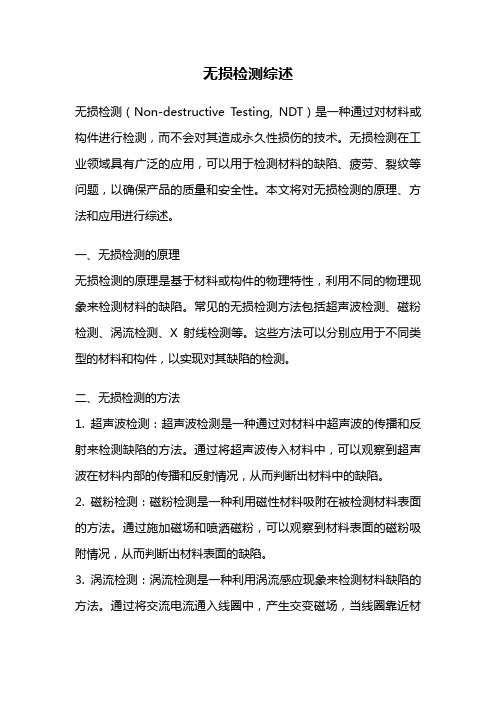
无损检测综述无损检测(Non-destructive Testing, NDT)是一种通过对材料或构件进行检测,而不会对其造成永久性损伤的技术。
无损检测在工业领域具有广泛的应用,可以用于检测材料的缺陷、疲劳、裂纹等问题,以确保产品的质量和安全性。
本文将对无损检测的原理、方法和应用进行综述。
一、无损检测的原理无损检测的原理是基于材料或构件的物理特性,利用不同的物理现象来检测材料的缺陷。
常见的无损检测方法包括超声波检测、磁粉检测、涡流检测、X射线检测等。
这些方法可以分别应用于不同类型的材料和构件,以实现对其缺陷的检测。
二、无损检测的方法1. 超声波检测:超声波检测是一种通过对材料中超声波的传播和反射来检测缺陷的方法。
通过将超声波传入材料中,可以观察到超声波在材料内部的传播和反射情况,从而判断出材料中的缺陷。
2. 磁粉检测:磁粉检测是一种利用磁性材料吸附在被检测材料表面的方法。
通过施加磁场和喷洒磁粉,可以观察到材料表面的磁粉吸附情况,从而判断出材料表面的缺陷。
3. 涡流检测:涡流检测是一种利用涡流感应现象来检测材料缺陷的方法。
通过将交流电流通入线圈中,产生交变磁场,当线圈靠近材料表面时,磁场会感应出涡流,从而观察到涡流的变化情况,判断出材料的缺陷。
4. X射线检测:X射线检测是一种利用X射线穿透材料并通过探测器接收的方法。
通过比较X射线的透射和吸收情况,可以判断出材料中的缺陷。
三、无损检测的应用无损检测在工业领域有着广泛的应用,可以用于检测各种类型的材料和构件。
以下是几个常见的应用领域:1. 航空航天:无损检测在航空航天领域中被广泛应用,用于检测飞机机身、发动机零部件等的缺陷,以确保航空器的安全性。
2. 石油化工:无损检测在石油化工行业中用于检测管道、储罐等设备的缺陷,以防止泄漏和事故的发生。
3. 汽车制造:无损检测在汽车制造领域中用于检测汽车零部件的缺陷,以提高汽车的质量和安全性。
4. 建筑工程:无损检测在建筑工程中用于检测混凝土、钢结构等的缺陷,以确保建筑物的结构安全。
无损检测技术的选择与应用方法
无损检测技术的选择与应用方法无损检测技术是一种通过非侵入性的手段对物体进行检测和评估的方法。
它可以检测出物体内部的缺陷、损伤或质量问题,而无需破坏物体本身。
无损检测技术在许多领域中得到了广泛的应用,包括工业制造、航空航天、石油化工、核能等。
选择适当的无损检测技术是非常重要的,因为不同的技术适用于不同的检测目标和要求。
本文将介绍几种常见的无损检测技术,并讨论它们的特点和应用方法。
1. 超声波检测技术超声波检测技术是一种利用声波在物体中传播时的特性进行检测的方法。
它通过发送超声波脉冲并记录其反射信号,从而确定物体中存在的缺陷或损伤。
超声波检测技术可以适用于各种材料,包括金属、陶瓷、复合材料等,广泛应用于焊接接头、管道、钢结构等领域。
应用超声波检测技术时,需要选择合适的探头和工作频率,以适应不同材料和尺寸的物体。
同时,还需考虑到材料的声波传播速度、反射信号的幅度和形态等因素,以确保检测结果的准确性。
2. 磁粉检测技术磁粉检测技术是一种利用磁场的变化来检测物体表面或近表面缺陷的方法。
它通过在被检测物体表面施加磁场,再用磁粉来观察磁力线是否发生变化,从而判断是否存在缺陷。
磁粉检测技术主要应用于金属材料的检测,如铁、钢等。
在应用磁粉检测技术时,需考虑到被检测物体的表面状况、磁场的强度和方向等因素。
同时,还需要根据不同的缺陷类型选择合适的磁粉颗粒和观察方法,以提高检测的准确性和可靠性。
3. 热红外检测技术热红外检测技术是一种利用物体辐射的红外热能来检测温度分布和表面缺陷的方法。
它通过测量物体表面的红外辐射强度,并通过图像处理技术来分析温度分布和发现异常区域。
热红外检测技术广泛应用于电力、电子、建筑等领域。
在应用热红外检测技术时,需考虑到被检测物体的辐射特性、环境温度和红外相机的灵敏度等因素。
同时,还需要根据不同的应用场景选择合适的测量方法和数据处理算法,以提高检测的准确性和可视化效果。
4. 射线检测技术射线检测技术是一种利用射线(如X射线、γ射线)通过物体并被接收器捕获的方法。
介绍几种常见的无损检测技术及其优缺点
介绍几种常见的无损检测技术及其优缺点无损检测技术是一种非破坏性检测方法,可用于检测工件内部和表面缺陷,而无需破坏工件的结构完整性。
它在工业、航空航天、汽车、建筑等领域广泛应用,以确保产品质量和安全性。
以下是几种常见的无损检测技术及其优缺点的介绍。
1. 超声波检测(Ultrasonic Testing):超声波检测是一种利用超声波传播和反射原理检测和评估材料内部缺陷的技术。
它通过发送超声波脉冲到被测物体,根据超声波在材料中传播的速度和反射情况来确定缺陷的位置和形状。
优点包括高灵敏度、无损伤、能检测小缺陷和定位准确。
缺点是对材料的声波传播特性敏感,受材料密度和纹理等因素影响。
2. 磁粉检测(Magnetic Particle Testing):磁粉检测是一种利用磁场和铁磁材料的磁性特性检测表面和近表面缺陷的方法。
它通过在被检测物体表面施加磁场,并在其上涂敷磁性颗粒,当有磁场漏磁或磁场被打断时,磁性颗粒会聚集在缺陷处,从而可视化缺陷的位置和形态。
优点包括简单易行、高灵敏度、能检测细小缺陷和形状多样化。
缺点是只能检测铁磁材料,灵敏度受表面状态和磁场均匀性影响。
3. 射线检测(Radiographic Testing):射线检测是一种利用X射线或γ射线穿透物体并投射到感光介质上的方法,从而检测物体内部缺陷的技术。
它通过感光介质上的黑化程度来评估缺陷的大小和位置。
优点包括能检测较深的缺陷,适用于各种材料。
缺点是设备昂贵,对操作人员和环境安全要求高。
4. 渗透检测(Dye Penetrant Testing):渗透检测是一种利用润湿性液体浸渍到表面开裂或孔隙处,然后涂覆上显色剂来检测这些表面缺陷的方法。
它通过液体的渗透和表面张力效应来展现缺陷的位置和形状。
优点包括简单易行、能够检测各种材料和形状的缺陷。
缺点是只能检测表面缺陷,对材料的清洁要求高。
5. 热红外检测(Thermal/Infrared Testing):热红外检测是一种利用热辐射和红外辐射原理检测表面和内部缺陷的技术。
无损检测知识点总结
无损检测知识点总结导言无损检测是现代工程领域中一项非常重要的技术,它通过使用一系列的检测方法和设备,来对材料和构件进行检测,以发现其中可能存在的缺陷和问题。
无损检测方法可以帮助工程师和技术人员及时发现并解决问题,确保工程的安全性和可靠性。
本文将对无损检测的基本知识点进行总结,包括常用的无损检测方法、设备及应用实例等。
一、无损检测方法无损检测方法是指在不破坏被检测材料的前提下,利用物理、化学、超声波、磁力学、光学以及计算机技术等方法进行对被检测材料缺陷的检测。
目前常用的无损检测方法主要包括以下几种:1. 超声波检测(UT)超声波检测是利用超声波在被检材料中传播的变化规律,来检测材料中的缺陷。
通过测量超声波的传播速度和反射波的能量,可以获取材料内部的缺陷信息,如裂纹、气泡、夹杂物等。
超声波检测方法可以分为接触式超声波检测和非接触式超声波检测两种。
2. 射线检测(RT)射线检测是利用射线照射被检材料,通过测量射线的衰减和散射来检测材料中的缺陷。
射线检测方法可以分为X射线检测和γ射线检测两种,常用于金属材料中裂纹、气泡等缺陷的检测。
3. 磁粉检测(MT)磁粉检测是利用磁场对被检材料进行磁化,并在磁场下添加磁粉颗粒,通过观察磁粉颗粒在被检材料表面的分布情况,来检测材料中的缺陷。
磁粉检测方法可以快速、高效地检测材料表面和近表面的缺陷,如裂纹、疲劳等。
4. 涡流检测(ET)涡流检测是利用涡流流动的规律,对被检材料进行缺陷检测。
当电磁场作用于导电材料时,会在材料中产生涡流,通过测量涡流的衰减和变化,可以发现材料中的缺陷。
涡流检测方法通常用于金属材料中的裂纹、夹杂物等缺陷的检测。
5. 磁记号检测(MPI)磁记号检测是利用磁场对被检材料进行磁化,并在磁场中添加磁记号液体,通过观察磁记号液体在材料表面的分布情况,来检测材料中的缺陷。
磁记号检测方法通常用于金属材料中裂纹、焊缝、表面夹杂物等缺陷的检测。
6. 热红外检测(IRT)热红外检测是利用红外热像仪和红外热辐射技术,对被检材料进行缺陷检测。
无损检测方案
无损检测方案无损检测是一种通过各种非破坏性手段来检测材料和构件内部缺陷的技术。
它在工程结构、航空航天、核能等领域具有重要应用。
本文将介绍几种常见的无损检测方案。
1. 超声波检测超声波检测利用超声波在材料中传播的特性来发现并定位缺陷。
它可以检测出金属材料中的气孔、夹杂、裂纹等缺陷。
超声波的频率、幅值和传播速度都可以提供关于缺陷的信息。
超声波检测设备通常包括超声发生器、探头和接收器。
该技术可应用于金属、塑料、陶瓷等材料的检测。
2. 磁粉检测磁粉检测是通过在被测零件的表面涂覆铁磁性材料,然后施加磁场来发现表面或近表面的裂纹、夹杂等缺陷的方法。
当有缺陷存在时,铁磁性材料会在缺陷周围产生漏磁场,从而形成磁粉堆积。
通过观察磁粉的分布情况和形态,可以确定缺陷的位置和形状。
磁粉检测适用于铁磁材料的表面和近表面缺陷的检测。
3. 渗透检测渗透检测是通过涂覆敏感液体(渗透剂)和吸附剂在被检测零件表面,然后去除表面多余的渗透剂,再施加显色剂来显示缺陷的方法。
渗透剂可以渗入缺陷,当显色剂施加后,渗入的渗透剂会显现出来,从而显示出缺陷的位置和形状。
渗透检测适用于金属、塑料、陶瓷等材料的表面缺陷的检测。
4. 射线检测射线检测是一种利用X射线或γ射线透射材料来显示隐藏在材料内部的缺陷的方法。
射线可以透过材料,当遇到缺陷时,部分射线会被吸收或散射,从而在胶片或探测器上形成缺陷的阴影。
射线检测广泛应用于金属材料的焊缝、铸件等的缺陷检测。
以上所述的无损检测方案只是其中的一部分,现实中还有许多其他的无损检测方法,如涡流检测、红外热成像等。
每种方法都有其适用的场景和具体应用。
无损检测的成功在很大程度上依赖于操作人员的经验和技术能力,同时设备的性能也会对检测结果产生影响。
无损检测在工程领域具有重要意义。
它可以在不破坏材料的情况下发现和评估缺陷,提高结构的安全性和可靠性。
例如,在航空航天行业,无损检测可以用于飞机零部件的质量检测和寿命评估。
- 1、下载文档前请自行甄别文档内容的完整性,平台不提供额外的编辑、内容补充、找答案等附加服务。
- 2、"仅部分预览"的文档,不可在线预览部分如存在完整性等问题,可反馈申请退款(可完整预览的文档不适用该条件!)。
- 3、如文档侵犯您的权益,请联系客服反馈,我们会尽快为您处理(人工客服工作时间:9:00-18:30)。
检测方法优点缺点应用
射线检测 1.检测结果有直接记录——底片
2.可以获得缺陷的投影图像,缺陷
定性定量准确1.体积型缺陷检出率很
高,而面积型缺陷的检
出率受到多种因素影
响
2. 不适宜检验较厚工
作。
3. 检测角焊缝效果较
差,不适宜检测板材、
楱材、锻件。
4. 对缺陷在工作中厚
度方向的位置、尺寸
(高度)的确定比较困
难。
5. 射线对人体有伤害
1.焊缝透照。
2.平板对接焊
缝透照。
3.角形焊缝照
射。
4.管件对接焊
缝照射。
超声检测 1.面积型缺陷的检出率较高,而体积
型缺陷的检出率较低。
2.适宜检验厚度较大的工件,不适
宜检验较薄的工件。
3.应用范围广,可用于各种试件。
4.检测成本低、速度快,仪器体积
小、重量轻,现场使用较方便
5.对缺陷在工件厚度方向上的定位
较准确。
1.无法得到缺陷直观图
像,定性困难,定量精
度不高。
2.检测结果无直接见
证记录。
3.材质、晶粒度对检测
有影响。
4.工件不规则的外形
和一些结构会影响检
测。
5.探头扫查面的平整
度和粗糙度对超声检
测有一定影响。
1.陶瓷气孔率
的检测。
2.陶瓷表面缺
陷检测。
3.钻孔灌注桩
的无损检测
磁粉检测 1.磁粉检测对工件中表面或近表面
的缺陷检测灵敏度最高。
2.对裂纹、折叠、夹层和未焊透等
缺陷较为灵敏,能直观地显示出缺
陷的大小、位置、形状和严重程度,
并可大致确定缺陷性质,检测结果
的重复性好。
1.随着缺陷的埋藏深度
的增加,其检测灵敏度
迅速降低。
因此,它被
广泛用于磁性材料表
面和近表面的缺陷
1.压力容器的
探伤。
2.锻件探伤。
3.疲劳缺陷探
伤。
渗透检测
1.渗透检测可以用于除了疏松多孔
性材料外任何种类的材料。
2.形状复杂的部件也可用渗透检
测,并一次操作就可大致做到全面
检测。
3.同时存在几个方面的缺陷,用一
次检测操作就可完成检测。
4.不需要大型的设备,可不用水、
电。
1.试件表面光洁度影响
大,检测结果往往容易
受操作人员水平的影
响。
2.可以检出表面开口
缺陷,但对埋藏缺陷或
闭合型表面缺陷无法
检出。
3.检测工序多,速度
慢。
4.检测灵敏度比磁粉
检测低。
1.钢铁,有色
金属,陶瓷和
塑料等材料
的表面开口
缺陷
2.对于形状复
杂的缺陷也
可一次性全
面检测
涡流检测 1. 适用于各种导电材质的试件检
测,包括各种钢、钛、镍、铝、铜
及其合金。
2.可以检出表面和近表面缺陷。
3. 探测结果以电信号输出,容易实
现自动化检测。
4.由于采用非接触式检测,所以检
测速度很快。
1.不能显示出缺陷图
形,因此无法从显示信
号判断出缺陷性质。
2.各种干扰检测的因
素较多,容易引起杂乱
信号。
3.由于集肤效应,埋藏
较深的缺陷无法检出。
5.不能用于不导电的
材料
1.探伤试件缺
陷。
2.测试材料物
性。
3.分选材料。
4.测量壁厚。
TOFD检测1.TOFD技术的定量精度高。
采用
衍射时差技术对缺陷定量,精度远
远高于常规手工超声波检测
2.TOFD检测简单快捷,最常用的
非平行扫查只需一人即可以操作,
探头只需沿焊缝两侧移动即可,不
需做锯齿扫查,检测效率高,操作
成本低。
3.TOFD能对缺陷深度位置进行精
确定位,对缺陷自身高度进行定量。
4.由于缺陷衍射信号与角度无关,
检测可靠性和精度不受角度影响。
5.根据衍射信号传播时差确定衍射
点位置,缺陷定量定位不依靠信号
振幅。
1.缺陷定性困难,需
要检测人员不断积累
经验,强化TOFD图像
的分析能力。
2.对横向缺陷检测能
力差,易将横向缺陷当
成点状缺陷。
3.对裂纹缺陷检出能
力强,但在检测尖端比
较圆滑的缺陷时,声波
减弱,检测效果较差。
4.表面缺陷与近表面
缺陷容易混淆。
1. 缺陷定量,
包括测高和
测长。
2. 缺陷定位。
3. 缺陷定性。