蒸发器尺寸设计
蒸发器尺寸设计

蒸发器工艺尺寸计算加热管的选择和管数的初步估计1加热管的选择和管数的初步估计蒸发器的加热管通常选用38*2.5mm无缝钢管。
加热管的长度一般为0.6—2m,但也有选用2m以上的管子。
管子长度的选择应根据溶液结垢后的难以程度、溶液的起泡性和厂房的高度等因素来考虑,易结垢和易起泡沫溶液的蒸发易选用短管。
根据我们的设计任务和溶液性质,我们选用以下的管子。
可根据经验我们选取:L=2M,38*2.5mm可以根据加热管的规格与长度初步估计所需的管子数n’,=124(根)式中S=----蒸发器的传热面积,m2,由前面的工艺计算决定(优化后的面积);d0----加热管外径,m;L---加热管长度,m;因加热管固定在管板上,考虑管板厚度所占据的传热面积,则计算n’时的管长应用(L—0.1)m.2循环管的选择循环管的截面积是根据使循环阻力尽量减小的原则考虑的。
我们选用的中央循环管式蒸发器的循环管截面积可取加热管总截面积的40%--100%。
加热管的总截面积可按n’计算。
循环管内径以D1表示,则所以mm对于加热面积较小的蒸发器,应去较大的百分数。
选取管子的直径为:循环管管长与加热管管长相同为2m。
按上式计算出的D1后应从管规格表中选取的管径相近的标准管,只要n和n’相差不大。
循环管的规格一次确定。
循环管的管长与加热管相等,循环管的表面积不计入传热面积中。
3加热室直径及加热管数目的确定加热室的内径取决于加热管和循环管的规格、数目及在管板撒谎能够的排列方式。
加热管在管板上的排列方式有三角形排列、正方形排列、同心圆排列。
根据我们的数据表加以比较我们选用三角形排列式。
管心距t为相邻两管中心线之间的距离,t一般为加热管外径的1.25—1.5倍,目前在换热器设计中,管心距的数据已经标准化,只要确定管子规格,相应的管心距则是定值。
我们选用的设计管心距是:确定加热室内径和加热管数的具体做法是:先计算管束中心线上管数nc,管子安正三角形排列时,nc=1.1* ;其中n为总加热管数。
薄膜蒸发器
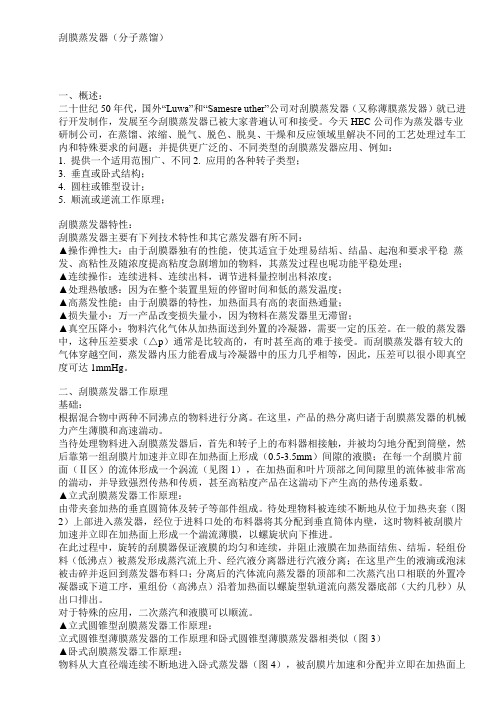
刮膜蒸发器(分子蒸馏)一、概述:二十世纪50年代,国外“Luwa”和“Samesre uther”公司对刮膜蒸发器(又称薄膜蒸发器)就已进行开发制作,发展至今刮膜蒸发器已被大家普遍认可和接受。
今天HEC公司作为蒸发器专业研制公司,在蒸馏、浓缩、脱气、脱色、脱臭、干燥和反应领域里解决不同的工艺处理过车工内和特殊要求的问题;并提供更广泛的、不同类型的刮膜蒸发器应用、例如:1. 提供一个适用范围广、不同2. 应用的各种转子类型;3. 垂直或卧式结构;4. 圆柱或锥型设计;5. 顺流或逆流工作原理;刮膜蒸发器特性:刮膜蒸发器主要有下列技术特性和其它蒸发器有所不同:▲操作弹性大:由于刮膜器独有的性能,使其适宜于处理易结垢、结晶、起泡和要求平稳蒸发、高粘性及随浓度提高粘度急剧增加的物料,其蒸发过程也呢功能平稳处理;▲连续操作:连续进料、连续出料,调节进料量控制出料浓度;▲处理热敏感:因为在整个装置里短的停留时间和低的蒸发温度;▲高蒸发性能:由于刮膜器的特性,加热面具有高的表面热通量;▲损失量小:万一产品改变损失量小,因为物料在蒸发器里无滞留;▲真空压降小:物料汽化气体从加热面送到外置的冷凝器,需要一定的压差。
在一般的蒸发器中,这种压差要求(△p)通常是比较高的,有时甚至高的难于接受。
而刮膜蒸发器有较大的气体穿越空间,蒸发器内压力能看成与冷凝器中的压力几乎相等,因此,压差可以很小即真空度可达1mmHg。
二、刮膜蒸发器工作原理基础:根据混合物中两种不同沸点的物料进行分离。
在这里,产品的热分离归诸于刮膜蒸发器的机械力产生薄膜和高速湍动。
当待处理物料进入刮膜蒸发器后,首先和转子上的布料器相接触,并被均匀地分配到筒壁,然后靠第一组刮膜片加速并立即在加热面上形成(0.5-3.5mm)间隙的液膜;在每一个刮膜片前面(Ⅱ区)的流体形成一个涡流(见图1),在加热面和叶片顶部之间间隙里的流体被非常高的湍动,并导致强烈传热和传质,甚至高粘度产品在这湍动下产生高的热传递系数。
双效蒸发器详细设计文件讲解

目录1.设计题目: 双效真空蒸发器及辅助设备的设计选择 22.任务书 22.1设计任务及操作条件 22.2 设计项目 23. 蒸发工艺设计计算 33.1各效蒸发量及完成液液浓度估算 33.1.1总蒸发量的计算 33.1.2加热蒸汽消耗量和各效蒸发量 33.2多效蒸发溶液沸点和有效温度差的确定 53.3 根据有效传热总温差求面积 83.3.1 则重新分配温差 83.3.2计算各效料液温度 83.4 温差重新分配后各效蒸汽的参数 83.5 计算结果列表 104. 蒸发器的主要结构尺寸设计 114.1加热管的选择和管数的初步估算 114.2 循环管的选择 114.3 加热室直径及加热管数目的确定 124.4 分离室直径与高度的确定 144.5 接管尺寸的确定 154.5.1 溶液的进出口径 154.5.2 加热蒸汽与二次蒸汽出口 154.5.2 冷凝水出口 164.6蒸发装置的流程图及蒸发器设备工艺简图 165.蒸发装置的辅助设备 185.1 汽液分离器 185.2 蒸汽冷凝器 186. 工艺计算汇总表 197. 对本设计进行评述 19参考文献 201.设计题目: 双效真空蒸发器及辅助设备的设计选择2.任务书2.1设计任务及操作条件含固形物16%(质量分率,下同)的鲜牛乳,拟经双效真空蒸发装置进行浓缩,要求成品浓度为46%,原料液温度为第一效沸点(60℃),加热蒸汽压力为250kPa(表,冷凝器真空度为92kPa,日处理量为24吨/天,日工作时间为8小时,试设计该蒸发过程。
假定采用中央循环管式蒸发器,双效并流进料,效间流动温差损失设为1K,第一效采用自然循环,传热系数为900w/(m2·k,第二效采用强制循环,传热系数为1800w/(m2·k,各效蒸发器中料液液面均为1m,各效加热蒸汽的冷凝液均在饱和温度下排出,并假设各效传热面积相等,忽略热损失。
2.2 设计项目2.1写出设计计算书(计算过程及计算结果尽量表格化)。
六效蒸发器施工方案
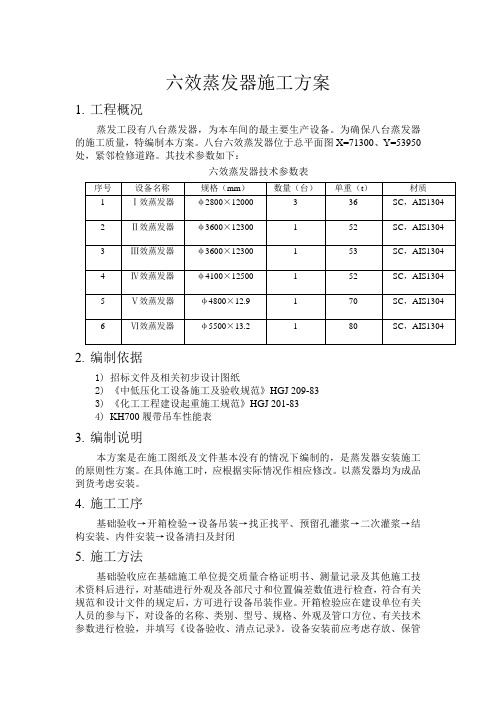
六效蒸发器施工方案1.工程概况蒸发工段有八台蒸发器,为本车间的最主要生产设备。
为确保八台蒸发器的施工质量,特编制本方案。
八台六效蒸发器位于总平面图X=71300、Y=53950处,紧邻检修道路。
其技术参数如下:六效蒸发器技术参数表2.编制依据1)招标文件及相关初步设计图纸2)《中低压化工设备施工及验收规范》HGJ 209-833)《化工工程建设起重施工规范》HGJ 201-834)KH700履带吊车性能表3.编制说明本方案是在施工图纸及文件基本没有的情况下编制的,是蒸发器安装施工的原则性方案。
在具体施工时,应根据实际情况作相应修改。
以蒸发器均为成品到货考虑安装。
4.施工工序基础验收→开箱检验→设备吊装→找正找平、预留孔灌浆→二次灌浆→结构安装、内件安装→设备清扫及封闭5.施工方法基础验收应在基础施工单位提交质量合格证明书、测量记录及其他施工技术资料后进行,对基础进行外观及各部尺寸和位置偏差数值进行检查,符合有关规范和设计文件的规定后,方可进行设备吊装作业。
开箱检验应在建设单位有关人员的参与下,对设备的名称、类别、型号、规格、外观及管口方位、有关技术参数进行检验,并填写《设备验收、清点记录》。
设备安装前应考虑存放、保管地点和方法,保证设备安全和性能不受破坏,保护配件不被损坏及丢失。
5.1蒸发器吊装1)吊装前,按设计图样或文件要求画定安装基准线及定位基准标记,并对八台蒸发器确定共同的基准。
2)对蒸发器附件及地脚螺栓进行检查,不得有损坏及锈蚀,要检查设备的方体温表标记、重心标记及吊挂点,不符合者,应予补充。
3)还要对内壁的基准圆周线检查,基准圆周线应与设备轴线相垂直,以保证内件安装的准确性。
4)厂房北侧结构框架横梁除(E)-(1)至(E)-(2)、(E)-(10)至(E)-(11)外,均应在吊装就位以后再行安装5.2吊装方案:因抱杆吊装需要的施工周期长,准备工作多,以及存在各种不安全因素,再考虑到吊装的吨位也不是太大,根据我公司目前的装备水平,选用150t履带吊进行吊装,下面以吊装Ⅵ效蒸发器为例说明方案的实施办法。
薄膜蒸发器原理及规格
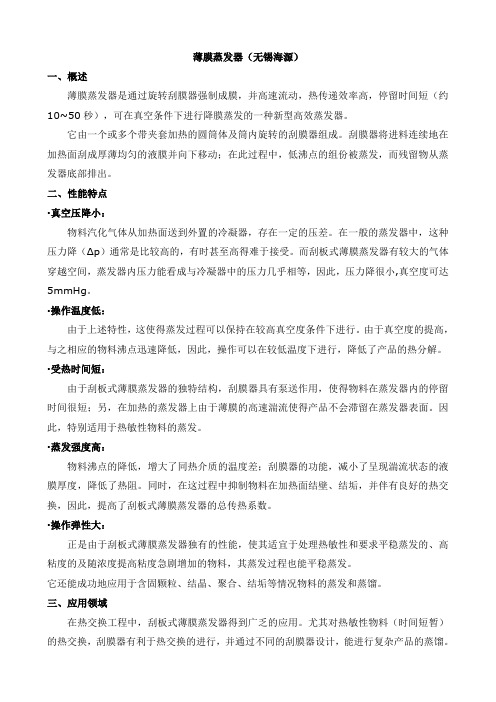
薄膜蒸发器(无锡海源)一、概述薄膜蒸发器是通过旋转刮膜器强制成膜,并高速流动,热传递效率高,停留时间短(约10~50秒),可在真空条件下进行降膜蒸发的一种新型高效蒸发器。
它由一个或多个带夹套加热的圆筒体及筒内旋转的刮膜器组成。
刮膜器将进料连续地在加热面刮成厚薄均匀的液膜并向下移动;在此过程中,低沸点的组份被蒸发,而残留物从蒸发器底部排出。
二、性能特点·真空压降小:物料汽化气体从加热面送到外置的冷凝器,存在一定的压差。
在一般的蒸发器中,这种压力降(Δp)通常是比较高的,有时甚至高得难于接受。
而刮板式薄膜蒸发器有较大的气体穿越空间,蒸发器内压力能看成与冷凝器中的压力几乎相等,因此,压力降很小,真空度可达5mmHg。
·操作温度低:由于上述特性,这使得蒸发过程可以保持在较高真空度条件下进行。
由于真空度的提高,与之相应的物料沸点迅速降低,因此,操作可以在较低温度下进行,降低了产品的热分解。
·受热时间短:由于刮板式薄膜蒸发器的独特结构,刮膜器具有泵送作用,使得物料在蒸发器内的停留时间很短;另,在加热的蒸发器上由于薄膜的高速湍流使得产品不会滞留在蒸发器表面。
因此,特别适用于热敏性物料的蒸发。
·蒸发强度高:物料沸点的降低,增大了同热介质的温度差;刮膜器的功能,减小了呈现湍流状态的液膜厚度,降低了热阻。
同时,在这过程中抑制物料在加热面结壁、结垢,并伴有良好的热交换,因此,提高了刮板式薄膜蒸发器的总传热系数。
·操作弹性大:正是由于刮板式薄膜蒸发器独有的性能,使其适宜于处理热敏性和要求平稳蒸发的、高粘度的及随浓度提高粘度急剧增加的物料,其蒸发过程也能平稳蒸发。
它还能成功地应用于含固颗粒、结晶、聚合、结垢等情况物料的蒸发和蒸馏。
三、应用领域在热交换工程中,刮板式薄膜蒸发器得到广乏的应用。
尤其对热敏性物料(时间短暂)的热交换,刮膜器有利于热交换的进行,并通过不同的刮膜器设计,能进行复杂产品的蒸馏。
蒸发器的设计计算
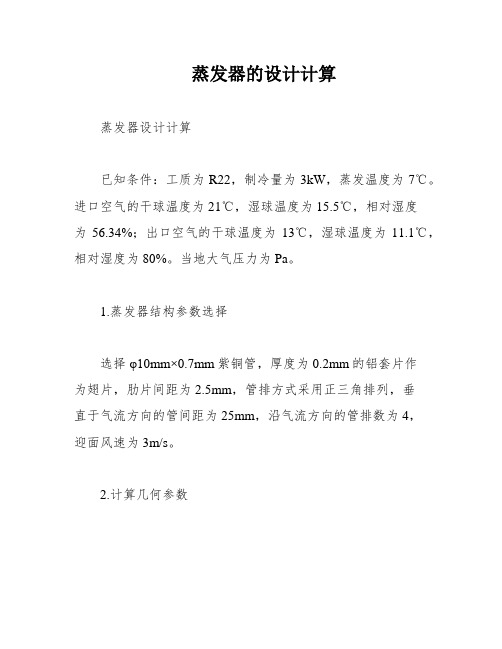
蒸发器的设计计算蒸发器设计计算已知条件:工质为R22,制冷量为3kW,蒸发温度为7℃。
进口空气的干球温度为21℃,湿球温度为15.5℃,相对湿度为56.34%;出口空气的干球温度为13℃,湿球温度为11.1℃,相对湿度为80%。
当地大气压力为Pa。
1.蒸发器结构参数选择选择φ10mm×0.7mm紫铜管,厚度为0.2mm的铝套片作为翅片,肋片间距为2.5mm,管排方式采用正三角排列,垂直于气流方向的管间距为25mm,沿气流方向的管排数为4,迎面风速为3m/s。
2.计算几何参数翅片为平直套片,考虑套片后的管外径为10.4mm,沿气流方向的管间距为21.65mm,沿气流方向套片的长度为86.6mm。
设计结果为每米管长翅片表面积为0.3651m²/m。
每米管长翅片间管子表面积为0.03m²/m。
每米管长总外表面积为0.3951m²/m。
每米管长管内面积为0.027m²/m。
每米管长的外表面积为0.m²/m。
肋化系数为14.63.3.计算空气侧的干表面传热系数1)空气的物性空气的平均温度为17℃。
空气在下17℃时的物性参数为:密度为1.215kg/m³,比热容为1005kJ/(kg·K)。
2)空气侧传热系数根据空气侧传热系数的计算公式,计算得到空气侧的干表面传热系数为12.5W/(m²·K)。
根据给定的数据,蒸发器的尺寸为252.5mm×1mm×10.4mm。
空气在最窄截面处的流速为5.58m/s,干表面传热系数可以用小型制冷装置设计指导式(4-8)计算得到,计算结果为68.2W/m2·K。
在确定空气在蒸发器内的变化过程时,根据进出口温度和焓湿图,可以得到空气的进出口状态点1和点2的参数,连接这两个点并延长与饱和气线相交的点w的参数为hw25kJ/kg。
dw6.6g/kg。
tw8℃。
2吨双效蒸发器
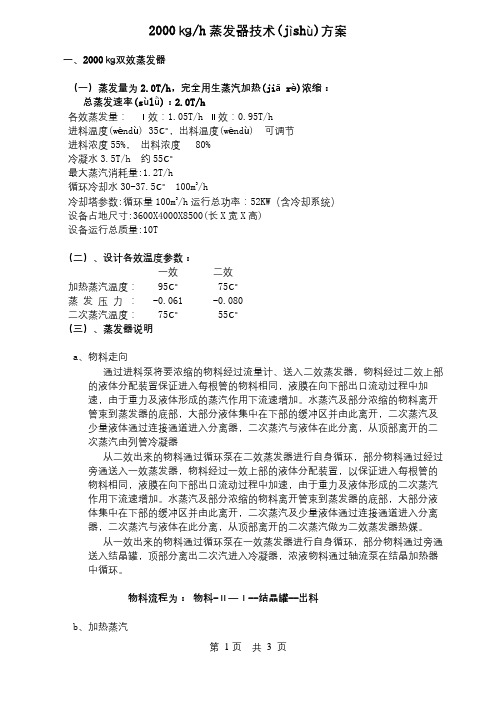
2000㎏/h蒸发器技术(jìshù)方案一、2000㎏双效蒸发器(一)蒸发量为2.0T/h,完全用生蒸汽加热(jiā rè)浓缩:总蒸发速率(sùlǜ):2.0T/h各效蒸发量:Ⅰ效:1.05T/h Ⅱ效:0.95T/h进料温度(wēndù) 35℃,出料温度(wēndù) 可调节进料浓度55%,出料浓度 80%冷凝水3.5T/h 约55℃最大蒸汽消耗量:1.2T/h循环冷却水30-37.5℃ 100m3/h冷却塔参数:循环量100m3/h运行总功率:52KW(含冷却系统)设备占地尺寸:3600X4000X8500(长X宽X高)设备运行总质量:10T(二)、设计各效温度参数:一效二效加热蒸汽温度: 95℃ 75℃蒸发压力: -0.061 -0.080二次蒸汽温度: 75℃ 55℃(三)、蒸发器说明a、物料走向通过进料泵将要浓缩的物料经过流量计、送入二效蒸发器,物料经过二效上部的液体分配装置保证进入每根管的物料相同,液膜在向下部出口流动过程中加速,由于重力及液体形成的蒸汽作用下流速增加。
水蒸汽及部分浓缩的物料离开管束到蒸发器的底部,大部分液体集中在下部的缓冲区并由此离开,二次蒸汽及少量液体通过连接通道进入分离器,二次蒸汽与液体在此分离,从顶部离开的二次蒸汽由列管冷凝器从二效出来的物料通过循环泵在二效蒸发器进行自身循环,部分物料通过经过旁通送入一效蒸发器,物料经过一效上部的液体分配装置,以保证进入每根管的物料相同,液膜在向下部出口流动过程中加速,由于重力及液体形成的二次蒸汽作用下流速增加。
水蒸汽及部分浓缩的物料离开管束到蒸发器的底部,大部分液体集中在下部的缓冲区并由此离开,二次蒸汽及少量液体通过连接通道进入分离器,二次蒸汽与液体在此分离,从顶部离开的二次蒸汽做为二效蒸发器热媒。
从一效出来的物料通过循环泵在一效蒸发器进行自身循环,部分物料通过旁通送入结晶罐,顶部分离出二次汽进入冷凝器,浓液物料通过轴流泵在结晶加热器中循环。
蒸发器设计
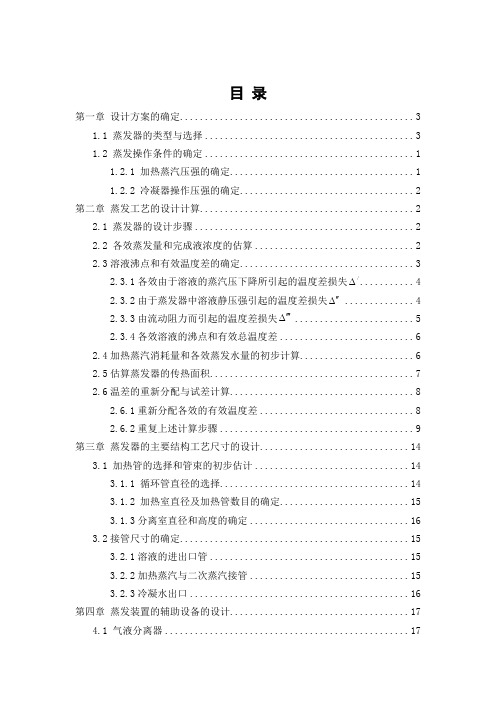
目录第一章设计方案的确定 (3)1.1 蒸发器的类型与选择 (3)1.2 蒸发操作条件的确定 (1)1.2.1 加热蒸汽压强的确定 (1)1.2.2 冷凝器操作压强的确定 (2)第二章蒸发工艺的设计计算 (2)2.1 蒸发器的设计步骤 (2)2.2 各效蒸发量和完成液浓度的估算 (2)2.3溶液沸点和有效温度差的确定 (3)2.3.1各效由于溶液的蒸汽压下降所引起的温度差损失∆/ (4)2.3.2由于蒸发器中溶液静压强引起的温度差损失∆'' (4)2.3.3由流动阻力而引起的温度差损失∆''' (5)2.3.4各效溶液的沸点和有效总温度差 (6)2.4加热蒸汽消耗量和各效蒸发水量的初步计算 (6)2.5估算蒸发器的传热面积 (7)2.6温差的重新分配与试差计算 (8)2.6.1重新分配各效的有效温度差 (8)2.6.2重复上述计算步骤 (9)第三章蒸发器的主要结构工艺尺寸的设计 (14)3.1 加热管的选择和管束的初步估计 (14)3.1.1 循环管直径的选择 (14)3.1.2 加热室直径及加热管数目的确定 (15)3.1.3分离室直径和高度的确定 (16)3.2接管尺寸的确定 (15)3.2.1溶液的进出口管 (15)3.2.2加热蒸汽与二次蒸汽接管 (15)3.2.3冷凝水出口 (16)第四章蒸发装置的辅助设备的设计 (17)4.1 气液分离器 (17)4.2蒸汽冷凝器主要类型 (17)4.3蒸汽冷凝器的设计与选用 (19)4.3.1工作水量的计算 (19)4.3.2喷射器结构尺寸的计算 (19)4.3.3射流长度的决定 (22)第五章设计结果一览表 (22)结束语.............................................. 错误!未定义书签。
主要参考文献........................................ 错误!未定义书签。
- 1、下载文档前请自行甄别文档内容的完整性,平台不提供额外的编辑、内容补充、找答案等附加服务。
- 2、"仅部分预览"的文档,不可在线预览部分如存在完整性等问题,可反馈申请退款(可完整预览的文档不适用该条件!)。
- 3、如文档侵犯您的权益,请联系客服反馈,我们会尽快为您处理(人工客服工作时间:9:00-18:30)。
蒸发器工艺尺寸计算
加热管的选择和管数的初步估计
1加热管的选择和管数的初步估计
蒸发器的加热管通常选用38*2.5mm无缝钢管。
加热管的长度一般为0.6—2m,但也有选用2m以上的管子。
管子长度的选择应根据溶液结垢后的难以程度、溶液的起泡性和厂房的高度等因素来考虑,易结垢和易起泡沫溶液的蒸发易选用短管。
根据我们的设计任务和溶液性质,我们选用以下的管子。
可根据经验我们选取:L=2M,38*2.5mm
可以根据加热管的规格与长度初步估计所需的管子数n’,
=124(根)
式中S=----蒸发器的传热面积,m2,由前面的工艺计算决定(优化后的面积);
d0----加热管外径,m;L---加热管长度,m;因加热管固定在管板上,考虑管板厚度所占据的传热面积,则计算n’时的管长应用(L—0.1)m.
2循环管的选择
循环管的截面积是根据使循环阻力尽量减小的原则考虑的。
我们选用的中央循环管式蒸发器的循环管截面积可取加热管总截面积的40%--100%。
加热管的总截面积可按n’计算。
循环管内径以D1表示,则
所以mm
对于加热面积较小的蒸发器,应去较大的百分数。
选取管子的直径为:循环管管长与加热管管长相同为2m。
按上式计算出的D1后应从管规格表中选取的管径相近的标准管,只要n和n’相差不大。
循环管的规格一次确定。
循环管的管长与加热管相等,循环管的表面积不计入传热面积中。
3加热室直径及加热管数目的确定
加热室的内径取决于加热管和循环管的规格、数目及在管板撒谎能够的排列方式。
加热管在管板上的排列方式有三角形排列、正方形排列、同心圆排列。
根据我们的数据表加以比较我们选用三角形排列式。
管心距t为相邻两管中心线之间的距离,t一般为加热管外径的1.25—1.5倍,目前在换热器设计中,管心距的数据已经标准化,只要确定管子规格,相应的管心距则是定值。
我们选用的设计管心距是:
确定加热室内径和加热管数的具体做法是:先计算管束中心线上管数nc,管子安正三角形排列时,
nc=1.1* ;其中n为总加热管数。
初步估计加热室Di=t(nc-1)+2b’,式中b’=(1—1.5)d0.然后由容器公称直径系列,试选一个内径作为加热室内径并以该内径和循环管外景作同心圆,在同心圆的环隙中,按加热管的排列方式和管心距作图。
所画的管数n必须大于初值n’,若不满足,应另选一设备内径,重新作图,直至合适。
由于加热管的外径为38mm,可取管心距为48mm;以三角形排列计算
,b’=(1—1.5)d0=1.5*d0,
Di=t(nc-1)+2b’=48*(13-1)+2*38*1.5=690mm,选取加热室壳体内径为800mm鄙厚为12mm;
4分离室直径与高度的确定
分离室的直径与高度取决于分离室的体积,而分离室的体积又与二次蒸汽的体积流量及蒸发体积强度有关。
分离室体积V的计算式为:
式中V-----分离室的体积,m3; W-----某效蒸发器的二次蒸汽量,kg/h;
P-----某效蒸发器二次蒸汽量,Kg/m3 ,U-----蒸发体积强度,m3/(m3*s);
即每立方米分离室体积每秒产生的二次蒸汽量。
一般用允许值为U=1.1~1.5 m3/(m3*s)
根据由蒸发器工艺计算中得到的各效二次蒸汽量,再从蒸发体积强度U的数值范围内选取一个值,即可由上式算出分离室的体积。
一般说来,各效的二次蒸汽量不相同,其密度也不相同,按上式计算得到的分离室体积也不会相同,通常末效体积最大。
为方便起见,各效分离室的尺寸可取一致。
分离室体积宜取其中较大者。
确定了分离
室的体积,其高度与直径符合关系,确定高度与直径应考虑一下原则:
(1)分离室的高度与直径之比H/D=1~2。
对于中央循环管式蒸发器,其分离室一般不能小于1.8m,以保证足够的雾沫分离高度。
分离室的直径也不能太少,否则二次蒸汽流速过大,导致雾沫夹带现象严重。
(2)在条件允许的情况下,分离室的直径尽量与加热室相同,这样可使结构简单制造方便。
(3)高度和直径都适于施工现场的安放。
现取分离室中U=1.2m3/(m3*s);
m3。
H=1.8m,,D=1.2m
2接管尺寸的确定
流体进出口的内径按下式计算
式中-----流体的体积流量m3/s ;U--------流体的适宜流速m/s ,
估算出内径后,应从管规格表格中选用相近的标准管。
1溶液进出口
于并流加料的三效蒸发,第一效溶液流量最大,若各效设备尺寸一致的话,根据第一效溶液流量确定接管。
取流体的流速为0.8 m/s;
所以取ф57X3.5mm规格管。
2加热蒸气进口与二次蒸汽出口
各效结构尺寸一致二次蒸汽体积流量应取各效中较大者。
所以取ф76X3.5mm规格管。
3冷凝水出口
冷凝水的排出一般属于液体自然流动,接管直径应由各效加热蒸气消耗量较大者确定。
所以取ф65X3.5mm规格管。