智能搬运小车
自动搬运小车毕业设计

自动搬运小车毕业设计【毕业设计题目】:基于自动化技术的搬运小车设计与实现【摘要】:本毕业设计基于自动化技术,设计并实现一种自动搬运小车,旨在解决人力搬运过程中的繁琐和劳动强度问题。
该小车将具备自动导航、定位、搬运等功能,通过控制系统实现智能化操控,大幅提高工作效率和操作便捷性。
设计过程中将采用模块化和可编程的方法,以方便扩展和改进。
【关键词】:自动化技术、搬运小车、自动导航、定位、模块化、可编程【引言】:随着科技的发展,自动化技术的广泛应用改变了许多传统工作方式。
搬运工作作为生产和物流过程中不可或缺的一环,其劳动强度和操作效率对企业运作至关重要。
本毕业设计旨在设计并实现一种自动搬运小车,通过引入自动导航和定位技术,提高小车的智能化水平,减少人工干预和劳动强度,从而达到提高工作效率和操作便捷性的目的。
【设计目标】:1. 实现小车的自动导航和定位功能,能够按照设定的路径自主行驶,避免碰撞和危险区域;2. 设计一个搬运装置,能够根据需求搬运货物,并具备自动装卸功能;3. 开发一个可编程的控制系统,能够对小车进行远程控制和指令调整,方便操作和管理;4. 设计小车的电力系统,实现长时间的工作并能够自主充电或充电桩充电;5. 模块化设计,方便对小车的功能进行扩展和改进。
【设计方法】:1. 硬件设计:选择适用的电机、传感器和执行器,设计和制造搬运装置,以及构建稳定的底盘结构;2. 软件设计:使用嵌入式系统和编程语言开发控制系统,实现自动导航和定位功能;3. 系统集成:将硬件和软件进行集成,测试系统的稳定性和性能;4. 调试和优化:反复测试并根据实际情况进行参数调优,提高小车的性能和可靠性。
【预期成果】:1. 自动搬运小车的硬件设计和制造;2. 小车自动导航和定位的软件开发和调试;3. 功能完善、稳定可靠的自动搬运小车原型;4. 设计文档和使用说明书;5. 毕业论文和答辩材料。
【创新点】:1. 引入自动导航和定位技术,实现小车的智能化行驶和定位功能;2. 设计可编程的控制系统,方便远程操控和指令调整;3. 搬运装置具备自动装卸功能,提高小车的搬运效率;4. 模块化设计,方便后续功能扩展和改进。
AGV基础知识介绍

AGV基础知识介绍
AGV(自动小车)是一种自动驾驶的机器人,用于在工厂中自动控制和转移物料的过程中,减少或避免人工干预。
它是一种无人驾驶的智能搬运车,可实现自动化、智能化和高效的物料搬运。
经过几十年的发展,AGV发展到现在,从单功能搬运车发展到多功能搬运车,多样化、智能化的搬运系统,让现代制造业更加智能化、高效化,助力企业可持续发展。
AGV具有自主导航、自动控制和智能控制等特点,可以实现在设定的路径上自动行驶,并通过对传感器的识别,避免碰撞并在转弯处处理和控制。
AGV不仅可以实现搬运,而且还可以实现无人驾驶。
AGV系统通常由传感器、控制器、算法、车辆及充电站等组成。
传感器用于监测车辆运行环境,收集信息并将信息发送给控制器。
控制器用于对收集的信息进行处理并发送控制命令。
算法用于对收集的信息进行处理并发出控制命令。
车辆根据控制命令行驶,并根据环境进行调整。
充电站用于给AGV充电,使其能够维持连续的行驶。
AGV虽然具有自动导航、自动控制和智能控制等特点,但在硬件的控制上,由于存在控制参数设置的困难、安全性低等缺点,使得AGV不适合搬运大型物件。
智能小车设计ppt课件

当检测到障碍物时,采用绕行、停止等策略进行避障操作。
避障策略
硬件调试
检查电路连接是否正确,电源供电是否稳定,传感器是否工作正常等。
软件调试
采用单步调试、断点调试等方法对程序进行逐步排查,找出问题所在并进行修改。
问题解决方法
针对常见问题,如传感器失灵、小车无法直行等,提供相应的解决方法。同时,也可通过查阅相关资料、请教专业人士等方式寻求帮助。
问题三
智能小车的成本控制仍需改进。建议通过优化设计方案、降低采购成本、提高生产效率等措施,降低小车的制造成本和售价。
随着人工智能、物联网、云计算等技术的不断发展,智能小车将更加智能化、自主化和网络化,实现更高级别的自动驾驶和协同作业。
技术趋势
智能小车将在更多领域得到应用,如智能交通、智慧城市、智能家居等,成为未来智能生活的重要组成部分。
精确性
提高智能小车的导航精度和搬运精度,确保准确无误地完成任务。
设计目标
设计一款具有自主导航、避障、搬运等多种功能的智能小车,实现智能化、自动化运行。
稳定性
确保智能小车在各种环境下都能稳定运行,不出现意外情况。02CHAPTER
智能小车硬件设计
选用高性能、低功耗的微控制器,如STM32系列。
主控芯片类型
主控芯片原理
主控芯片优势
通过内部CPU、存储器和外设接口等资源,实现对小车各项功能的精确控制。
具有高集成度、高可靠性和易于开发等特点,满足智能小车复杂控制需求。
03
02
01
红外传感器
超声波传感器
陀螺仪传感器
加速度传感器
01
02
03
04
用于检测障碍物,实现避障功能。
agv搬运小车检验标准

agv搬运小车检验标准
AGV搬运小车的检验标准应包括以下几个方面:
1. 外观检验:检查车身外观是否完整,无明显变形、划痕或损坏;
检查车身表面的喷涂是否均匀,无起泡、脱落等现象。
2. 电气系统检验:检查电气系统的接线是否牢固,无松动或接触不
良的现象;检查电气元件的固定是否牢固;检查电气系统的绝缘性
能是否符合要求,无漏电现象。
3. 机械系统检验:检查车轮和驱动装置的安装是否牢固,无松动或
脱落的现象;检查车轮的转动是否灵活,无阻滞或卡滞的现象;检
查传动装置的工作是否正常,无异常噪音或振动。
4. 导航系统检验:检查导航系统的安装是否牢固,无松动或脱落的
现象;检查导航系统的定位精度是否符合要求,无误差过大的现象;检查导航系统的反应速度是否快速,无延迟或卡顿的现象。
5. 安全系统检验:检查安全传感器和防碰撞装置的安装是否牢固,
无松动或脱落的现象;检查安全系统的反应速度是否快速,无延迟
或误判的现象;检查安全系统的报警装置是否正常工作,无故障或
失效的现象。
以上是一般情况下的检验标准,具体的标准可能会因不同厂商或使
用环境的不同而有所差异。
在进行检验时,应参考相关的技术规范
和标准,确保AGV搬运小车的质量和性能符合要求。
基于UWB的智能搬运小车

基于UWB的智能搬运小车曾贵苓;王苹;张玉明;段争光【摘要】在循迹、避障等基本功能的基础上,融入UWB(Ultra Wideband)技术以实现智能搬运小车的高精度目标跟随,使得智能搬运小车能实现多种场景的货物搬运.通过在车身安装2个UWB基站模块,在目标体上携带1个UWB标签模块,利用定位算法来获取目标相对于小车的实时空间几何位置.另外,车身的磁条传感器、防撞条、超声波传感器和RFID标签传感器用于实现小车基本功能的传感单元.综合UWB模块获取的目标位置信息和其他传感器获取的传感信息,小车的控制器做出相应的决策,以差速驱动的方式控制电机向目标位置移动.经过现场测试,智能小车在手动模式、跟随模式和循迹模式下均良好运行,因此多种模式运行的智能小车能适应多种货运场景下工作,对于工业自动化具有重要的意义.【期刊名称】《湖北民族学院学报(自然科学版)》【年(卷),期】2019(037)002【总页数】5页(P223-227)【关键词】智能搬运小车;目标跟随;UWB技术;差速驱动;循迹;定位【作者】曾贵苓;王苹;张玉明;段争光【作者单位】芜湖职业技术学院电气工程学院,安徽芜湖241006;芜湖职业技术学院电气工程学院,安徽芜湖241006;芜湖职业技术学院电气工程学院,安徽芜湖241006;芜湖职业技术学院电气工程学院,安徽芜湖241006【正文语种】中文【中图分类】TN92随着工业自动化的发展,智能化设备的研究越来越受人们关注.在仓储领域以及其他需要大量货物搬运的领域,智能搬运小车凭借其具有成本低、效率高等诸多优势成为了搬运工具的主力军[1].智能搬运小车按照导引方式不同可分为固定路径导引小车和自由路径导引小车[2].文献[3]中利用RFID(Radio Frequency Identification)标签和磁导航传感器导引小车运动,实现了小车系统沿固定路线循迹[3].文献[4]利用色带铺设的道路的方式导引小车沿固定路线运动[4].虽然固定路径导引小车可以适用于一些常见的搬运场景,但在复杂的搬运场景中,自由路径导引小车则能更好的满足实际需求.目标牵引小车和自主路径规划小车都属于自由路径导引小车[5].目标牵引小车需要利用空间定位技术获取目标实时的空间位置[6],自主路径规划小车则根据事先构建的地图来判断自身在空间中的位置,并规划一条最优路径向作业点运行[7].综合上述信息,为了使本系统的小车适应更多的搬运场景,本系统利用UWB(Ultra Wideband)传感器、超声波传感器、磁条传感器、防撞条、串口屏和RFID标签传感器获取多种传感信息,并以差速驱动的方式控制小车向目标位置移动[8-9].本系统设计的小车可按固定路径导引和自由路径导引两种方式运动,可实现多种场景下的货物搬运.图1 系统总体设计Fig.1 Overall system design图2 系统的电源设计Fig.2 System power supply design图3 UWB模块电路Fig.3 UWB module circuit1 系统总体设计如图1所示为系统的总体框图,主要分为小车和目标两个部分.但除了图中的小车和目标两个部分外,该系统还包括根据应用场景需要铺设的磁条道路和指示小车运动的标签站点[10].目标由赛普拉斯控制器和一个UWB标签模块组成,控制器通过SPI(Serial Peripheral Interface)通信可控制UWB模块工作在标签模式.小车的目标跟随模块由赛普拉斯控制器和两个UWB模块组成,控制器通过SPI协议控制两个UWB模块工作在基站模式.两个UWB基站模块通过UWB通信获取UWB标签模块与自身的距离信息,通过两路距离信息以及系统已知的参数便可计算出目标相对于小车的空间几何位置.小车的主控制器采用STM32控制器,其通过TTL电平的串口和赛普拉斯控制器通信,用于获取采集到的目标位置信息.STM32控制器还通过232串口和磁条传感器、RFID标签传感器以及超声波传感器相连,用于获取循迹、避障的感应信息.此外,STM32控制器还通过GPIO(General Purpose Input Outpu)口和防撞条相连,以便发生碰撞时能及时停止小车.通过上述传感器获取的传感信息,STM32控制器做出小车移动位置的决策.STM32控制器通过PWM控制两个电机驱动,以差速驱动的方式控制左右两个电机向目标位置移动.除了传感和驱动单元,小车还通过232串口和串口屏相连,串口屏可设置小车的工作模式也可显示小车的实时运行参数.2 系统硬件设计2.1 电源电路设计系统的电源使用24 V的锂电池,LED灯D1可指示锂电池是否接入本系统.如图2所示,由于本系统的电机驱动模块需要5 V的电压输入,锂电池输入的24 V电压经过LM2576SX芯片后降压为5 V,为系统中工作电压为5 V的模块提供电源,LED灯D2可指示5 V电源工作.系统的控制器均采用3.3 V电压,AMS1117芯片将5 V电压降压为3.3 V,为系统工作电压为3.3 V的模块提供电源,D3可指示3.3 V电源工作.2.2 UWB定位模块UWB是一种短距离无线通信技术,其广泛应用于精确的室内定位,其利用纳秒至微秒级的非正弦波窄脉冲传输数据,所以具有非常高的通信速率.本系统为了实现小车的跟随功能,需要获取实时、精确的目标空间位置,所以UWB技术是开发本系统的最佳无线通信方式.本系统为实现UWB通信采用DWM1000芯片,其电路如图3所示.控制器控制该芯片的GPIO5、GPIO6可以设置该模块工作在基站模式和标签模式.UWB基站模块主要用来接收返回的脉冲来测量UWB标签模块的距离,测距完成后通过该芯片的SPI口将测量数据传输给控制器.图4 UWB空间目标定位原理Fig.4 UWB space target positioning principle图5 光耦输出电路Fig.5 Optocoupler output circuit图6 电机驱动模块Fig.6 Motor drive module本系统的定位原理如图4所示,L和R分别为安装在小车左右侧的UWB基站模块,S为目标携带的UWB标签模块.两个基站模块的距离LR为固定值,以其中心O为空间坐标原点,小车的正前方为Y轴正反向,小车的正右方为X轴的正方向,小车的正上方为Z轴正方向建立空间坐标系.点S1为S点在XY平面的投影,距离SS1代表目标相对于小车的高度.根据UWB基站模块的测距结果可得到距离SL和SR的大小,根据直角三角形三边关系,可得公式(1):(1)得到LS1和RS1的数值后,可根据公式(2)求出∠S1RL的大小.(2)求得了∠S1RL的大小,其补角∠S1RB便可计算得到,由此便可得出目标S的空间坐标为:(3)2.3 基本传感模块磁条传感器选用CCF-D08传感器,其使用高灵敏度的霍尔传感器检测磁条,可输出八路开关量信号.磁条传感器用于判断小车和磁条道路的偏离程度,进而调整小车使其沿着磁条道路运行不偏离轨迹.在小车运动轨迹上铺设指示小车运动的标签站点,RFID标签传感器使用CCF-RFID-126K传感器,通过射频技术识别标签站点携带的信息,可指示小车接下来的运动状态.标签站点中可携带指示小车向左、向右、向前、向后以及停止等状态的信息;超声波传感器采用CCF-SR2传感器,其通过测量超声波遇到障碍物的回波来测量障碍物的距离,通过该超声波传感器可实现小车的避障功能.此外,防撞条为一个开关,如果小车在运行过程中遇到意外撞击,防撞条被触发后可控制小车及时停止.2.4 电机驱动模块电机驱动模块需要5 V的IO口方可驱动,所以本系统在主控制器的IO口后增加了如图5所示的光耦输出模块,以提高IO口的输出能力.端口In1和控制器的普通IO口相连,经过EL357N芯片可控制Out1输出高低电平控制电机驱动模块.端口In2和控制器的PWM输出端口相连,经过6N137S芯片控制Out2输出.不同占空比的PWM波来作为电机驱动模块的PWM输入信号.电机驱动采用ZM-6510M模块,该模块可使用PWM和485串口控制,本系统应用PWM对该模块进行控制.将无刷电机接入本模块,使用24 V电源供电,便可通过PWM控制电机工作.该模块的PU端口为PWM脉冲波的输入口,可通过输入不同占空比的PWM波控制电机的转动速度.DIR端口可选择电机的正反转,BREAK端口和EN端口分别控制电机的停止与启动.另外,该模块可以输出电机的转速信息和一些运行中的警告信息.3 系统软件设计3.1 软件总体流程图图7为本系统的软件总体流程图.首先,系统要对一些资源进行初始化,包括系统的串口、中断、传感器的参数等资源的初始化操作.初始化完成后,可通过串口屏设置小车的工作模式,包括小车工作在手动模式、循迹模式和跟随模式.根据小车工作模式的不同,可选择获取一种或者多种传感器的传感数据.获取数据后,根据小车的工作模式对各种传感器的感应数据进行分析处理,对小车接下来的运动做出决策.在驱动小车运动前,先判断防撞条是否被触发,如果被触发则停止小车;如果防撞条未被触发,则根据上一步得到的决策信息驱动电机向目标位置移动.在小车的移动过程中,串口屏也会显示一些小车运行的参数.如果小车处于停止状态,可通过串口屏设置使小车继续运行,也可关闭小车结束程序.图7 测量节点软件设计Fig.7 Measurement node software design图8 三种速度下小车的实时速度Fig.8 Real-time speed of the car at three speeds3.2 用户界面设计为了实现对小车的操作、选择不同的模式以及显示小车运行中的一些参数,选用串口屏来设计系统的用户界面.通过Visual TFT软件可自定义串口屏的用户界面,并为界面上的操作生成特定的指令.操作串口屏时会通过串口向小车的控制器发送代表该次操作的指令,小车的控制器接收到指令后控制小车完成相应的动作.操作者可通过手动模式控制小车向前、向后、向左、向右以及停止等动作,也可设置小车的运行速度以及显示小车当前的移动速度.除了手动模式外,小车还可设置在跟随模式和循迹模式,每种模式下有其特定的用户界面.另外,还可通过设置界面设置一些小车固定的参数.4 测试与结果4.1 手动模式下的测试为了验证本系统的可行性,分别在三种模式下测试小车的运行状态.首先设置小车在手动模式,手动模式下小车根据操作者的指令完成指定的运行轨迹.分别设置小车的向前、向后、向左、向右的功能,小车可在操作者设置后迅速向指定方向运动.操作者设置高速、中速、低速时,可明显观测小车的运行速度发生变化.如图8所示为小车设置3种速度时通过编码器反馈回的小车实时速度,设定每5 min速度采样一次,可知小车能够在设定速度下稳定运行.所以小车在手动模式下运行状态良好,可满足系统需求.4.2 循迹模式下的测试为了测试小车的循迹模式,以磁条传感器铺设黑色道路,路口处设置白色站点——RFID标签传感器.在实际测试中,小车沿着预先铺设的道路运行,未曾偏离运行轨迹.小车经过标签站点时,根据标签传感器携带的信息进行接下来的运动,标签传感器可携带向左、向右、向前、向后、停止、速度选择等信息.在循迹模式的测试过程中,小车保持良好的状态运行.4.3 跟随模式下的测试在一些搬运场景中,需要搬运小车与工人或者其他智能设备保持一定的距离运动(此处的距离是指小车实时坐标系的原点与目标在XY平面投影的距离).跟随模式使用的传感器有UWB模块、防撞条和超声波传感器.为了测试小车在该模式下的运动,测试者手持目标模块以1.2 m/s的步速在操场上运动,跟随距离设置在10~200 cm范围内,无论测试者向左、向右、向前、向后,小车均可跟随测试者良好的运动.若小车在测试过程中遇到意外撞击或者遇到其他障碍物时,小车也可及时停止.图9为分别设置小车跟随距离为50、100和150 cm时的几组小车与目标的实际距离数据,从图9可以看出小车与目标的实际距离与设置的跟随距离十分接近,所以本系统的跟随模式也可正常工作.图9 跟随模式下小车与目标的实际距离Fig.9 Actual distance between the car and the target in the following mode5 结论为了实现多种场景的货物搬运,开发了智能搬运小车系统.系统由UWB传感器、超声波传感器、磁条传感器、RFID标签传感器和防撞条组成小车的感应单元,由串口屏界面进行人机交互操作,由左右两个电机以差速驱动的方式控制小车运动.实现了一个具备人机交互、目标跟随、磁条道路和标签站点循迹、测距避障和撞击后急停的智能搬运小车.通过现场测试,本系统的小车可在手动模式、循迹模式和跟随模式下良好运行,并准确地完成预期的动作.测试结果证明了本系统设计的小车可适应多种搬运场景,本系统设计对工业自动化中的实际应用具有重要的意义. 参考文献:【相关文献】[1] 向楠,陆会娥.物流自动化智能可避障搬运小车系统设计[J].广东石油化工学院学报,2017,27(4):30-33.[2] MEHAMI J,NAWI M,ZHONG R Y.Smart automated guided vehicles for manufacturing in the context of Industry 4.0[J].Procedia Manufacturing,2018,26:1077-1086.[3] LU S P,XU C,ZHONG R T,et al.A passive RFID tag-based locating and navigating approach for automated guided vehicle[J].Computers & IndustrialEngineering,2018,125:628-636.[4] 李万敏,韩致信,赵耕云.基于摄像头智能车典型路径图像识别算法研究[J].兰州工业学院学报,2017,24(1):69-72.[5] 罗怀菊,赵琦,罗继亮.智能小车任务执行系统的Petri网设计方法[J].控制工程,2018,25(3):522-526.[6] 陈二阳,张修军,袁姜红.基于图像识别的自主驾驶智能小车的设计与实现[J].现代电子技术,2018,41(18):162-165,169.[7] 张辉,王永杰,赵海敏,等.自主寻迹智能小车的激光路径跟随系统设计[J].合肥工业大学学报(自然科学版),2013,36(10):1170-1173.[8] 赵旭磊,耿召里,李小华.智能小车避障算法和速度调节算法研究[J].辽宁科技大学学报,2018,41(3):212-217.[9] 丁柏文,金琦淳,任俊,等.基于IAP15F2K61S2单片机的红外与无线搬运小车[J].仪表技术与传感器,2017(10):110-114.[10] 叶方,车克文,李一兵.超宽带信道频率域AR模型建立与仿真[J].黑龙江八一农垦大学学报,2011,23(2):69-72.。
基于STM32的模拟工业自动化智能搬运小车设计

基于STM32的模拟工业自动化智能搬运小车设计作者:周磊磊余家天一郭婋赫周丽蓉谢光前来源:《电脑知识与技术》2020年第09期摘要:本文研究的智能小车又叫轮式机器人,模拟工业自动化过程中自动化物流系统的作业过程。
选用稳定的三轮结构车体,通过差速度,实现左转右转各种角度。
采用STM32芯片作为嵌入式控制中心的核心,智能搬运小车系统由嵌入式STM32最小系统板结合稳压电源模块、电机驱动模块、灰度传感器模块、颜色识别模块等组成。
关键词:智能小车;自动化;STM32;颜色识别;嵌入式中图分类号:G642.0 文献标识码:A文章编号:1009-3044(2020)09-0257-031 引言随着工业4.0的发展,越来越多的工业工厂开始转向自动化和智能化的方向。
工业4.0是一个利用信息技术促进工业转型的时代,包括从集中控制到分散强化控制的基本模式转变。
目的是为个性化和数字化产品和服务创建方便快捷的生产形式。
在这种形式下,以前的工业界限将消散,各类新的模式和合作方式将出现。
缔造新价值的过程正逐渐变化,产业链中的各个部分将会重组。
工业4.0是一个工业的技术改造和工业改造。
工业4.0所讲到的智能制造面向商品的整个生命周期,在无处不在的传感条件下完成信息化制造。
经过感知、人机交互、决策、实行和应答,实现智能产品生产、制造过程和工厂智能化管理。
它是信息技术与制造业的深度集成和集成技术[1-4]。
最近几年,国内先后出现了一系列机器人竞赛,机器人比赛一方面能够推动技术进步,很多比赛项目都是基于一些实际社会生产中的问题,以中国工程机器人大赛的搬运组比赛而言,比赛的任务是将不同颜色的物料送到对应颜色的位置,模拟了工业自动化生产中物流运输。
现如今,很多工业正向自动化、智能化转型,提高生产效率。
另一方面机器人比赛促进学校教育,想要设计一辆符合比赛要求的轮式小车,需要多方面的知识,以及一定的实践经验。
通过参加比赛,将所学的知识应用于实际,增加动手能力,逻辑分析能力,进一步巩固学到知识。
agv小车原理

agv小车原理AGV小车原理。
AGV(Automated Guided Vehicle)是一种自动导引车,它能够在不需要人工操控的情况下,按照预设的路线和程序,完成货物的搬运和运输任务。
AGV小车是利用先进的导航技术和自动控制技术,实现对物料的自动搬运和运输,广泛应用于仓储、物流、生产线等领域。
本文将介绍AGV小车的原理及其工作过程。
AGV小车的原理主要包括导航系统、传感器系统、控制系统和动力系统。
首先是导航系统,AGV小车通常采用激光导航、磁导航、视觉导航等技术,通过地面标识、磁条、激光反射器等设备进行定位和导航。
其次是传感器系统,AGV小车配备了多种传感器,如激光传感器、红外传感器、超声波传感器等,用于检测障碍物、识别地标、测量距离等功能。
控制系统是AGV小车的大脑,通过预先设定的程序和算法,实现对小车的路径规划、速度控制、动作执行等功能。
最后是动力系统,AGV小车通常采用电池、超级电容等作为动力源,驱动车轮或履带进行运动。
AGV小车的工作过程一般包括路径规划、定位导航、障碍物避障、动作执行等步骤。
首先,根据任务需求和环境条件,系统对小车的路径进行规划,确定起点、终点和途经点等信息。
然后,小车利用导航系统进行定位和导航,沿着预设的路径行驶,同时通过传感器系统检测周围环境,避开障碍物。
在行驶过程中,控制系统实时监测小车的状态,调整速度和方向,确保安全和高效地完成任务。
最后,小车到达目的地后,根据任务要求执行相应的动作,如装卸货物、与设备对接等。
AGV小车的原理和工作过程决定了它具有高效、灵活、安全的特点。
相比传统的人工搬运和叉车搬运,AGV小车能够实现自动化操作,提高搬运效率,降低人力成本,减少货物损坏和事故风险。
同时,AGV小车还能够根据任务需求和环境变化,灵活调整路径和动作,适应不同的工作场景和任务要求。
总之,AGV小车是一种基于先进技术的自动化搬运设备,其原理和工作过程体现了先进的导航、传感、控制和动力技术。
智能循迹小车在搬运过程中出现的若干问题及解决办法
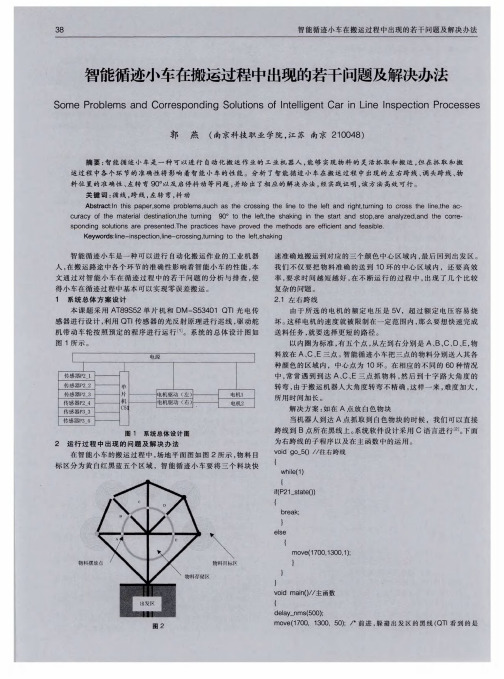
mo v e ( 1 7 0 0 ,1 3 0 0 , 9 ) : / / 排除干扰 mo v e ( 1 7 0 0 , 1 5 0 0 , 4 O ) : / / 以右轮为轴 , 旋转 9 0
r un
_
o n l i n e ( 1 5 ) ; / / 巡线走 1 5个脉冲
2 . 4左转弯 9 O 。 困难
5 所 示 。根 据 以上经 验 , 在 其他 角 度上 面很 多 问题也 迎 刃而 解 。
上 此 时 的 位 置 就 是 中心 位 置 。
但 由于 小 车 是 以全 速 行 驶 , 物 料 的移动速度也是全速 , 有 一
定 的惯性 , 当 机器 人 把 物 料 送 到 目的 地 时 , 总是 发 现 物 料 被
s t a t e ( )
p u t 1 一 ma t e r i a l ( ) ; / / 放下白木快 r un o n l i n e ( 1 5 ) :
—
{ r e t u r n( P 2 & O x 0 4 ) ? l : 0 : }
i n t P2 3
一
r un
_
个 QT I 的 返 回信 号 , 返 回值 : 1 : 高 电平 , 看 到 黑
o n l i n e ( 2 0 ) ;
线; 0 : 低 电平 , 看 到 白线 。
g e t _ ma t e r i a l ( ) ;/ / 拿 到白物块
mo v e ( 1 7 0 0 , 1 7 0 0 , 2 2 ) ; / / 向右双轮旋转 9 0度 g o _ 5 0 ; / / 向右跨 线
传感 器
2 . 2 调 头 跨 线 在 智 能 小 车 的 搬 运 过 程 中 ,常 常 会 碰 到 跨 线 的 现 象 。 以
- 1、下载文档前请自行甄别文档内容的完整性,平台不提供额外的编辑、内容补充、找答案等附加服务。
- 2、"仅部分预览"的文档,不可在线预览部分如存在完整性等问题,可反馈申请退款(可完整预览的文档不适用该条件!)。
- 3、如文档侵犯您的权益,请联系客服反馈,我们会尽快为您处理(人工客服工作时间:9:00-18:30)。
智能搬运小车
摘要:
设计一个轮式小型机器人,在比赛场地里移动,将不同颜色、形状或者材质的物体分类搬运到不同的对应位置。
比赛的记分根据机器人将物体放置的位置精度和完成时间来决定分值的高低。
它模拟了工业自动化过程中自动化物流系统实际工作过程。
关键词:单片机,PWM,光电传感器,运货小车
1.引言
1.1智能搬运小车研究的背景和目的:
运货是各个行业不可或缺的过程,人工运货随着经济的快速发展,不能完全满足市场的需求。
世界上许多国家都在积极进行智能车辆的研究和开发设计。
移动机器人是机器人学中的一个重要分支,出现于20世纪60年代。
当时斯坦福研究院的Nils Nilssen和charles Rosen等人,在1966年至1972年中研制出了取名shakey的自主式移动机器人,目的是将人工智能技术应用在复杂环境下,完成机器人系统的自主推理、规划和控制。
从此,移动机器人从无到有,数量不断增多,智能车辆作为移动机器人的一个重要分支也得到越来越多的关注。
智能搬运小车可以安装不同的末端以完成各种不同形状和状态的工件搬运工作,可以广泛应用于机床上下料,冲压机自动化生产线,自动装配流水线,码垛搬运,集装箱等的自动搬运,大大减轻了人类繁重的体力劳动,具有广阔的市场前景。
1.2智能搬运小车的功能介绍:
智能搬运小车希望能够希望得到可以自动抓取货物,循迹行进,自动卸货物的功能。
2.总体方案及论证
2.1系统结构框图:
停止
是否到达取物
处
否是
夹取货物
抬起机械臂
后退
掉头
循迹
是否到达卸货
处循迹
是
否
放下货物
松开货物
后退
掉头停止
图1.系统结构框图
2.2具体设计:
整个系统包括单片机控制模块、电机驱动模块、光电传感器模块、机械手
模块、模拟电源模块、小车车体。
将单片机控制模块,驱动模块固定在小车上端;光电电传感器安装在小车底部;将机械手安装在小车上部的前端.
2.2.1系统布局部分
为节省时间和经费,并且考虑到小车的重量和整体布局。
我们选择直接购买小车模块。
然后经过后期的电路设计,在电路板上加所需要的电气元件组成我们的搬运小车。
在此我们的小车达到了轻便,经济的效果。
上图为未加传感器等电气元件和机械手时的图像。
2.2.2系统电路部分
单片机最小系统
单片机最小系统由复位电路、时钟振荡电路、数据采集接口和电机控制接口组成,单片机最小系统图如图所示。
2.2.2.1电机驱动模块:
驱动模块采用专用芯片L298N 作为电机驱动芯片,L298N 是一个具有高电压大电流的全桥驱动芯片,其响应频率高,一片L298N可以分别控制两个直流
电机。
以下为L298N的引脚图和输入输出关系表。
图11.L298N外部引脚表1. L298N输入输出关系
采用左右两轮分别驱动,前万向轮转向的方案。
即左右轮分别用两个转速和力矩基本完全相同的直流电机进行驱动,车体前部装一个万向轮。
当两轮的间存在速度差时,可以实现转弯。
当两个直流电机转向相反同时转速相同时就可以实现小车的原地旋转。
由此可以轻松的实现小车坐标不变的90度和180度的转弯。
安装时保证两个驱动电机同轴。
当小车前进时,左右两驱动轮与前万向轮形成了三点结构。
这种结构使得小车在前进时比较平稳。
前万向轮起支撑作用。
2.2.2.2光电传感器模块:
小车的路线检测部分是整个小车最重要的,就如同人的眼睛。
故采用光电传感器GP2A25实现要求。
黑色和白色路面对光的反射程度不同,白色反射程度强,黑色反射程度弱。
在小车行驶过程中不断地向地面发射红外光,当红外光遇到白色纸质地板时发生漫反射,反射光被装在小车上的接收管接收;当红外线遇到黑线时红外光被吸收,小车上的接收管接收不到红外光。
当光电传感器检测检测到黑线时,将输出一个高电平的信号给单片机。
当光电传感器检测检测到白色区域时,将输出一个低电平的信号给单片机。
单片机按照光电传感器反馈回来的信号来确定小车的位置,判断小车是否偏
移轨道。
图11.光电传感器部分电路图
2.2.2.3机械手模块:
采用3个舵机来实现要求。
舵机控制电路板接受来自信号线的控制信号,控制电机转动,电机带动一系列齿轮组,减速后传动至输出舵盘。
舵机的输出轴和位置反馈电位计是相连的,舵盘转动的同时,带动位置反馈电位计,电位计将输出一个电压信号到控制电路板,进行反馈,然后控制电路板根据所在位置决定电机的转动方向和速度,从而达到目标停止。
机械手的夹取通过左右两个舵机的配合来实现,左边的的舵机向右转一定的角度,右边的舵机向左一定的角度,从而实现夹取货物的目的。
机械手的抬起是通过中间舵机的顺时针转一定的角度来实现的。
2.2.2.4模拟电源模块
光电耦合模块:
图11.电路原理图
2.2.3系统软件部分:
采用PWM(Pulse Width Modulation,脉冲宽度调制)来调节直流电机的速
度。
PWM是通过控制固定电压的直流电源开关频率,从而改变负载两端的电压,进而达到控制要求的一种电压调整方法。
PWM可以应用在许多方面,如电机调速、温度控制、压力控制等。
在PWM驱动控制的调整系统中,按一个固定的频率来接通和断开电源,并根据需要改变一个周期内“接通”和“断开”时间的长短。
通过改变直流电机电枢上电压的“占空比”来改变平均电压的大小,从而控制电动机的转速。
在脉冲作用下,当电机通电时,速度增加;电机断电时,速度逐渐减少。
只要按一定规律,改变通、断电的时间,即可让电机转速得到控制。
本系统中通过控制51单片机的定时器T0,T1的时间,从而可以实现P0.4和P0.5,P1.0,P1.1,P1.2产生PWM信号。
定时器每中断一次, 使单片机的指定管脚根据条件输出高电平或低电平。
将直流电机的速度分为N个等级, 因此一个周期就有个N脉冲, 周期为N 个脉冲的时间。
速度等级对应一个周期的高电平脉冲的个数。
占空比为高电平脉冲个数占一个周期总脉冲个数的百分数。
一个周期加在电机两端的电压为脉冲高电压乘以占空比。
占空比越大, 加在电机两端的电压越大, 电机转动越快。
电机的平均速度等于在一定的占空比下电机的最大速度乘以占空比。
当我们改变占空比时, 就可以得到不同的电机平均速度, 从而达到调速的目的。
精确地讲, 平均速度与占空比并不是严格的线性关系, 在一般的应用中, 可以将其近似地看成线性关系。
系统总体流程
图12.程序流程图取物函数详细流程
取货卸货函数详细流程图
循迹处理软件流程
在白色背景中有一条黑色的线,小车就是要沿着这条黑线行走,通过判断反射式光电传感器所接收到的反射光来判断小车所应行走的方向。
以三个反射式光电传感器为例进行说明循线的原理。
光电传感器与黑线位置关系示意图如图4-4所示。
光电传感器与黑线位置关系示意图
检测环节中一共有4个这样的光电传感器单元,实现组合式的控制方向的检测。
4个光电传感器电路组合功能见表4-1。
表4-1 光敏传感器状态真值表
循迹流程图
循迹流程图
3.参考文献
[1]黄开胜 金华民 蒋狄南.韩国智能模型车技术方案分析. 电子产品世界, 2006,3. [2]石振东,吕 科, 喻清洲等. 基于红外路径识别的智能车控制系统设计. 湖北汽车工业学院学报, 2007,3.
[3]陈东,向巍. 基于光电管的智能车模设计. 机床与液压,2007,7.。