湿法冶金浸出技术
湿法冶金新工艺新技术及设备选型应用手册

湿法冶金新工艺新技术及设备选型应用手册一、湿法冶金简介湿法冶金是一种从含金属的废水、废渣或土壤中回收有价金属的重要方法。
它通过化学或电化学过程,将金属从复杂的多金属氧化物或硫化物中提取出来,并转化为可溶性的离子形态,然后从溶液中提取出来。
湿法冶金广泛应用于工业生产中,尤其在环保和资源回收方面具有重要意义。
二、新工艺新技术1. 微生物浸出技术:利用某些特殊类型的微生物,能够将固体矿石中的金属离子转化为可溶性离子,提高金属提取效率。
2.化学沉淀法:通过添加沉淀剂,将金属离子转化为氢氧化物、碳酸盐或其他类型的沉淀,从溶液中分离并回收金属。
3. 膜分离技术:利用半透膜将溶液中的金属离子与杂质、有机物等分离,具有高效、选择性高的优点。
4. 电化学处理法:通过电解作用,将金属离子从溶液中提取出来,适用于处理高浓度金属离子废水。
三、设备选型应用1. 搅拌器:用于液体混合、搅拌,促进化学反应的进行。
2. 浸出罐:用于微生物浸出、化学沉淀等工艺过程的浸出作业。
3.沉淀池:用于金属离子的沉淀过程,回收金属。
4. 膜分离设备:用于处理含金属离子废水,回收金属。
5. 电镀槽:用于电化学处理法,将金属从溶液中提取出来。
四、总结湿法冶金新工艺新技术及设备选型应用日益多样化,包括微生物浸出、化学沉淀、膜分离和电化学处理等新工艺,以及相应的设备如搅拌器、浸出罐、沉淀池和电镀槽等。
这些新工艺和设备的选择和应用,将有助于提高金属回收效率,降低环境污染,实现资源的可持续利用。
以上内容仅供参考,具体选择和应用还需要根据实际情况进行考虑。
湿法冶金浸出新工艺

湿法冶金浸出新工艺1 技术领域本工艺适用于锌的湿法冶金行业。
2 背景技术无论是火法还是湿法炼锌,只能处理氧化物料,故硫化矿都需预先焙烧脱硫;低品位氧化锌矿、含锌残渣和烟尘等用烟化或威尔兹法处理。
2.1 焙烧广泛采用沸腾焙烧(湿法炼锌)和烧结焙烧(密闭鼓风炉),旧式的多膛炉和闪速焙烧已基本被淘汰。
为从低品位氧化锌矿、残渣、烟尘和其他含锌废料中回收锌,用烟化或威尔兹法富集,回收的氧化锌在经湿法或火法产出金属锌。
2.2 金属锌的生产当前,世界约80%的锌产自湿法,但最初是普遍采用火法炼锌。
约在1800年,在比利时和上西里西亚地区开始用平罐炼锌,后来美国开发了新泽西法,又称竖罐炼锌。
现在这两种工艺都已基本在国外被淘汰,主要的火法炼锌是密闭鼓风炉法。
(1)密闭鼓风炉法世界许多地方产出选矿难分离的Pb-Zn混合精矿,因此20世纪50年代英国就开发了密闭鼓风炉工艺,又称帝国熔炼法。
鼓风炉炼锌曾有较大发展,英国的斯温西、阿望茅斯,日本的八户和播磨,德国贝采留斯以及澳大利亚等,世界相继建立了十几家铅-锌鼓风炉工厂。
毕竟该工艺还有一些缺点,如需消耗昂贵的焦炭,环境问题也较严重,进入20世纪80年代就不再发展了。
(2)湿法炼锌现在,湿法炼锌技术已有较大发展,主要在提高锌回收率和原料综合利用方法、生产过程机械化和自动化控制。
一些难点技术相继得到解决:①黄钾铁矾法除铁。
过去,湿法炼锌的主要缺点之一是锌回收率低。
后来开发了高温高酸浸出工艺,使锌浸出率大大提高,但大量铁也被浸出,除铁成了问题。
黄钾铁矾法是除铁工艺之一。
从1960-1965年开发出该工艺后,在世界许多湿法炼锌厂采用。
最终浸出渣含锌量降至4%-6%,锌回收率提高到96%-98%。
缺点是黄钾铁矾渣含有部分可溶的锌,为防止环境污染,必须小心堆存或处理。
②针铁矿法。
浸出液加硫化锌使铁还原成两价,再在PH2-3.5和70-90℃温度下以FeO(OH)沉淀。
针铁矿法的渣量比黄钾铁矾渣少。
湿法冶金浸矿技术

湿法冶金——浸矿技术
一、浸出的定义和作用
1、定义:浸出是用化学试剂(如酸、碱、盐的水溶液和有机溶剂)将矿石或精矿中的有用组分转化为可溶性化合物,并有选择性地溶解出来,得到含金属的溶液,实现有用组分与杂质组分或脉石组分分离的过程,最终达到回收有价金属的目的。
2、浸出技术的最主要优点:(1)适合于处理低品位、细分散、组成复杂的矿石,以及精矿]表外矿、废矿石、矿渣和各种二次物料(如熔渣、烟道灰、废旧金属等);(2)方法操作方便、金属综合回收率较高,广泛用于黑色、有色、稀有、稀散金属以及非金属矿物原料的加工,也是使未利用资源的资源化和解决三废(废渣、废液和废气)处理及保护环境的有效方法。
(3)浸矿石技术在三废治理、废金属回收、化工等领域有着巨大的潜在优势。
二、浸矿技术发展简史
冶金技术有六千或更早历史,早在公元前2世纪,我国就记载发铁置换硫酸铜的技术,到唐朝或五代时期,出现了从硫酸铜中提取铜金属的生产方法(胆铜法)。
所以,我国是采用湿法冶金技术最早的国家。
随着科学技术的发展,特别是核工业技术的发展,湿法冶金技术得到了飞速发展。
同时,溶剂萃取技术的发展,为湿法冶金加上腾飞的翅膀。
目前,浸矿技术已在地质、采矿、选矿、冶金、化工、环保、废旧金属回收、水处理等领域,显示出愈来愈重要的作用和发展前景。
湿法炼铅工艺流程

湿法炼铅工艺流程
湿法炼铅是一种冶金技术,它通过化学浸出和电解过程从铅精矿中提取金属铅。
以下是该工艺的基本流程:
1. 浸出过程:在这一步骤中,铅精矿与盐类或碱溶液接触,通过化学反应将铅从固态矿物中转移到溶液中。
这个过程通常在较低的温度下进行,与火法冶金相比,能耗较低。
2. 电解过程:经过浸出的溶液中含有铅离子,将这些溶液送入电解槽中,通过电解作用,铅离子在阴极上还原成金属铅沉积下来。
这样可以得到纯度较高的铅金属。
3. 后处理:电解产出的金属铅可能需要进一步的精炼和纯化,以达到工业使用的标准。
总的来说,湿法冶金技术的优点包括操作温度低、能耗相对较低、环境污染小,并且可以处理一些火法冶金难以处理的物料。
然而,湿法炼铅在工业应用上还面临着一定的挑战,比如技术成熟度、经济效益等方面的考量。
《湿法冶金浸出》PPT课件
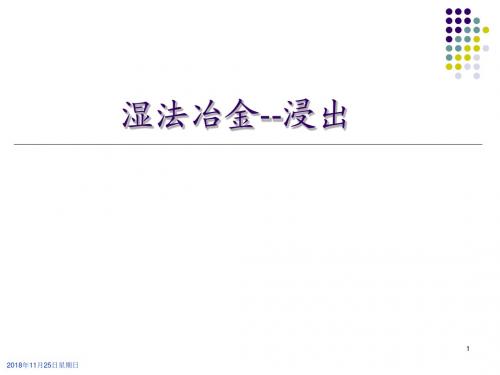
பைடு நூலகம்
( 6 )有配合物形成的溶解。用氰化钾或氰 化钠溶液溶解金或银的过程,是这类反应的 常见实例。如金的氰化钠溶解反应:
1 2Au+4NaCN+H2 O+ O2 ® 2NaAu(CN)2 +2NaOH 2
此外,硫化镍的氨溶浸也是一个重要实例, 其反应为:
1 Ni3S2 +10NH 4 OH+(NH4 )2SO4 +4 O2 ® 3Ni(NH3 )4 SO4 +11H2 O 2
湿法冶金--浸出
1 2018年11月25日星期日
第一节 概述
什么是湿法冶金?
利用某种溶剂,借助化学反应(包括氧化、 还原、中和、水解及络合等反应),对原 料中的金属进行提取和分离的冶金过程。
湿法冶金的应用
湿法冶金作为一项独立的技术是在第二次 世界大战时期迅速发展起来的,在金、银、 铜、镍、钴、锌、铀、钨、钼和稀有金属 的提取以及氧化铝的生产都要用到湿法冶 金。
2 2018年11月25日星期日
1. 关于浸出的知识
浸出的实质;
浸出剂的选择;
浸出过程的分类 浸出反应的分类
3 2018年11月25日星期日
1.1 浸出的实质
浸出的实质在于利用适当的溶剂使矿石、精 矿和半产品中的一种或几种有价成分优先溶出, 使之与脉石分离。
4 2018年11月25日星期日
NiS(s)+CuSO4(l) CuS(s)+NiSO4(l)反应。
白钨矿用苏打溶液进行的加压浸出,也是属于 这种类型,其反应如下:
CaWO4(g)+Na2CO3(l) CaCO3(s)+Na2WO4(l)
有色冶金原理第七章 湿法冶金浸出净化和沉积

3
0 G298 RT Me 0 即: ( ln ) Me ZF ZF Me
Z
RT Me ln / Me ZF Me
Z
② 计算步骤: 0 a:计算或查表求标准电极电位 Me / Me b:将R、T、Z、F、 Me 值代入上式求ε R=8.314 F=96500 Zn 0.1mol / l 时的平 例:求 Zn Z 2e Zn 反应在298K。 衡电极电位,并说明要做Zn2+以Zn的形式沉将析出,需 要电极电位多少? 0 14176( J ) 解:① 求反应 G298
§2. 浸出过程
一、浸出的实质及溶剂 浸出的实质是利用适当的溶剂,在一定条件下使矿石中 的一种或集中有价成分溶出,而与其中的脉石和杂质分离。 溶剂应具有以下特性 ⑴ 能选择性的迅速溶解原料中的有价成分; ⑵ 价格低廉并能大量获得; ⑶ 不与原料中的杂质或脉石发生作用; ⑷ 没有危险,便于使用; ⑸ 能够再生使用。 (6 )对设备没有腐蚀作用 。 工业中一般溶剂有:水、酸(硫酸、盐酸等)、氨溶液和碱 溶液、盐溶液(金银浸出时用氰化物)。
③ 将Z、F、n、T代入
0.42 Zn 2.303 8.314 298 2.303 8.314 298 lg PH 2 96500 Zn OH 2 2 96500
0.42 0.0591 PH
§1.4. 水的热力学稳定区分析
一、水的稳定区对生产的意义 1.判断参与过程的各种物质与溶剂(水)发生相互作用的可 能性。 2.它是金属-H2O系的ε -PH图的一个组成部分 二、水在过程中有可能发生的反应及ε -PH关系式 1.在给定条件下,溶液中有电极电位比氢更负的还原剂存 在,对于下二反应,其都属于有电子得失,也有H+参加 的氧化还原反应。 2H+ + 2e = H2 (酸性) 2H2O + 2e = H2 + 2OH(碱性)
湿法冶炼中的浸出与萃取

搅拌强度对混合效率和传质速率有重 要影响,搅拌强度不足会影响传质效 果,导致分离效率降低。
料液的浓度
料液中目标物质的浓度直接影响萃取 效果,浓度过高或过低都会影响分离 效果。
搅拌强度
温度和压力的变化会影响萃取剂的溶 解度和目标物质的挥发性,进而影响 萃取效果。
04
浸出与萃取的比较与选择
浸出与萃取的优缺点比较 浸 01
原料性质
对于某些特定原料,如 高品位矿石或易浸出的 矿物,浸出可能更合适
。
产品要求
如果需要高纯度产品, 萃取可能更合适。
生产规模
大规模生产时,浸出可 能更具优势。
浸出与萃取的联合流程
1 2
3
先浸出后萃取
原料经过浸出处理后,浸出液中的目标组分再进行萃取分离 。
先萃取后浸出
原料经过萃取处理后,萃取液中的目标组分再进行浸出处理 。
锌的浸出与萃取
锌的浸出
在锌的湿法冶炼过程中,通常采用硫酸作为浸出剂,将锌矿石中的锌离子浸出到溶液中。硫酸与矿石 中的锌反应生成硫酸锌,同时伴有其他金属离子的浸出。
锌的萃取
浸出液中的锌离子通过萃取剂(如环己酮)的选择性吸附作用,从浸出液中被提取出来。萃取剂将锌 离子从浸出液转移到有机相中,实现锌与其他金属离子的分离。
根据萃取剂的种类,萃取过程可分为 有机溶剂萃取、离子交换萃取和协同 萃取。
VS
有机溶剂萃取是利用有机溶剂对目标 物质的溶解度进行萃取分离;离子交 换萃取是利用离子交换剂对溶液中的 离子进行交换分离;协同萃取是利用 两种或多种萃取剂的协同作用进行萃 取分离。
萃取过程的设备
萃取设备主要包括混合器、分离器和 洗涤器。
同时浸出与萃取
湿法冶炼工艺技术

湿法冶炼工艺技术湿法冶炼工艺技术是一种将金属矿石经过溶解、离析、净化等一系列的工艺过程,将其中的有价金属从矿石中提取出来的方法。
具体来说,湿法冶炼工艺技术是通过将矿石与溶剂接触,在特定的条件下使金属溶解于溶液中,再通过降温、淬火等手段将其沉淀或凝固,最终得到金属。
湿法冶炼工艺技术主要有火法、浸出法、溶解法等多种方法,下面就分别讲解一下这几种常用的湿法冶炼工艺技术。
首先是火法,火法是一种通过高温将矿石中的有价金属转化为氧化物的方法。
在这个过程中,矿石会在高温下发生化学反应,使金属元素从硫化物、碳酸盐等矿石中转化为金属氧化物,然后再通过还原反应将氧化物还原为金属。
火法工艺技术的优点是操作简单、能耗低、生产成本相对较低。
其次是浸出法,浸出法是一种通过化学溶解将金属从矿石中提取出来的方法。
在这个过程中,矿石会和一种溶液或气体接触,在特定条件下使金属溶解于溶液中,然后再通过沉淀、电解、萃取等方法将金属从溶液中分离提取出来。
浸出法工艺技术的优点是提取效率高、生产成本相对较低。
最后是溶解法,溶解法是一种将金属矿石通过化学溶解得到金属的方法。
在这个过程中,矿石会和特定的溶剂接触,在特定温度、压力、PH值等条件下使金属溶解于溶液中,然后再通过浓缩、结晶等方法将金属从溶液中提取出来。
溶解法工艺技术的优点是提取效率高、工艺灵活性强、产品质量好。
当然,湿法冶炼工艺技术也存在一些问题。
首先是废水和废渣的处理问题,湿法工艺产生的废水和废渣含有一定的毒性和污染物质,需要特殊的处理方法才能达到环保要求。
其次是能源消耗问题,湿法工艺需要耗费大量的能源才能维持其正常运作。
此外,湿法工艺的设备投资和维护成本较高也是一个问题。
总的来说,湿法冶炼工艺技术是一种重要的金属提取方法,具有提取效率高、操作简单等优点,但同时也存在着废水和废渣处理问题、能源消耗问题以及设备投资和维护成本高等一系列问题。
未来,随着科技的进步和工艺技术的不断改进,相信湿法冶炼工艺技术会越来越完善,为金属冶炼行业带来更大的发展机遇。
- 1、下载文档前请自行甄别文档内容的完整性,平台不提供额外的编辑、内容补充、找答案等附加服务。
- 2、"仅部分预览"的文档,不可在线预览部分如存在完整性等问题,可反馈申请退款(可完整预览的文档不适用该条件!)。
- 3、如文档侵犯您的权益,请联系客服反馈,我们会尽快为您处理(人工客服工作时间:9:00-18:30)。
湿法冶金浸出技术
湿法冶金浸出技术是指利用液体介质将金、银、铜、铝等金属元素从矿石或其他固态
材料中溶解出来的技术。
这种技术被广泛应用于非铁金属冶炼、稀有金属冶炼、废弃物处
理等领域。
湿法冶金浸出技术的基本原理是,在液体介质中,矿石或其他固态材料中的金属元素
被化学反应或化学吸附溶解出来。
溶解后的金属离子可通过电解、沉淀、络合、溶解度等
方式进一步得到纯金属。
在湿法冶金浸出技术中,液体介质是非常重要的。
常见的液体介质有稀酸、酸、碱等。
这些液体介质中的化学成分与矿物中的金属元素发生反应,从而使金属元素溶解在介质
中。
金矿石的化学成分主要是金和硫化铁。
在使用氰化物溶解金矿石时,氰化物在水中形
成离子,和金化学反应,生成氰化金离子,溶解在水中。
硫化铁和氰化物反应,生成一氰
化化铁离子,通过氧化、水解等方式进行还原。
湿法冶金浸出技术在工业生产中有广泛应用。
在铜冶炼中,氧化和硫化铜矿是主要的
原料,其使用浸出法进行处理。
在硫酸亚铁盐中浸出铜矿,则使用的是酸性液体介质。
在
稀有金属冶炼中,常使用浸出法处理稀土矿。
湿法冶金浸出技术也被广泛应用于废弃物处理领域。
在锌处理厂,通过浸出法处理废
旧电池中的锌,将锌溶解出来。
在废弃电子产品中,含有如金、银、铜等贵金属,通过浸
出法可将其溶解并回收。
湿法冶金浸出技术在不同领域具有不同的应用特点和优势。
在非
铁金属冶炼领域,该技术可以处理各种类型的非铁矿,如铝土矿、磷灰石、锰矿和钾矿等。
通过浸出法处理非铁矿可以提高矿石回收率,降低运输成本,并减少对自然资源的消耗。
湿法冶金浸出技术的化学反应速度较快,操作过程相对简单,而且可以通过控制液体介质
的化学成分,实现精准的物质分离。
在稀有金属冶炼领域,湿法冶金浸出技术已被广泛应用于稀土元素的分离和提纯。
稀
土元素由于矿石中的含量极低,因此其提取成本较高。
但通过采用湿法浸出技术,将矿石
浸出后,可以将稀土元素与其他金属分离开来,提高浸出效率和提纯效率,从而降低稀土
元素的生产成本。
在废弃物处理领域,湿法冶金浸出技术可以处理各种含金属的废弃物和废料,如废旧
电子产品、废旧电池、废料等。
通过浸出法回收这些废料中的金属,不仅可以减少废弃物
的危害,还可以降低金属生产的成本。
虽然湿法冶金浸出技术在金属回收和生产领域具有广泛的应用前景和潜力,但该技术
也存在着一些问题和挑战。
液体介质的处理和回收会产生大量的废液和污水,会对环境造
成影响。
湿法冶金浸出技术需要大量的能量和资金投入,特别是在稀有金属冶炼领域,提
纯成本较高。
为了解决这些问题和挑战,在湿法冶金浸出技术研究中,人们通常采用一些新的方法
和技术。
利用生物浸出法对矿石进行处理,可以提高金属离子的得率。
通过控制液体介质
的pH值和温度等参数,可以优化金属离子的得率和质量。
借助互联网技术,可实现将废弃物分拣、处理和回收的信息化管理,提高废料回收效率。
湿法冶金浸出技术在不同领域应用广泛,并且在这些领域不断发展和创新。
通过继续
研究和开发该领域的新技术和新方案,可以不断提高金属回收和提纯效率,优化工艺流程,达到资源有效利用和环境友好的目标。
随着社会和经济的发展,湿法冶金浸出技术已从传
统的金属提取和冶炼领域逐渐延伸到高新技术领域。
例如在电器电子、信息通讯、新能源、海洋开发等领域,开发利用各种新型材料和新型设备,促进产业升级和发展。
在这些新兴
领域中,湿法冶金浸出技术发挥着重要的作用。
在电器电子领域,湿法浸出技术被广泛应用于电子器件和元件的制备和处理。
通过浸
出金、银、铜等金属的离子,可制备成不同化学形态的金属光子晶体、纳米管、催化剂等,这些新型材料具有较高的物理性质和应用价值。
在信息通讯领域,湿法冶金浸出技术也被广泛应用于制备半导体材料和器件。
在硅制
备过程中,应用湿法浸出技术可以提高硅的纯度和晶格性质。
利用湿法浸出技术,还可以
制备出铜铟镓硒等复合材料,这些材料可以被用于太阳能电池等新能源领域。
在海洋开发领域,湿法冶金浸出技术也被广泛应用于海洋矿产资源的提取和利用。
盐
湖镁盐是一种重要的海洋矿物资源,在湿法浸出技术的支持下,可提高镁盐的回收率和纯度,从而实现镁金属、氧化镁等产品的制备。
在新能源领域,湿法冶金浸出技术应用在燃料电池材料的制备和处理方面。
通过浸出钴、镍等金属元素,可以制备出高效的燃料电池催化剂材料,推动燃料电池产业的发展。
随着各个领域对于高质量金属和新型材料需求的不断增加,湿法冶金浸出技术将继续
发挥自身优势,并不断拓展应用范围。
该技术的应用还存在着一定的难题,例如液体介质
的开发和成本控制、处理液体产生的污染问题等。
为了优化该领域技术的发展,需要加强
研发和创新,探索更加高效、环保和经济的湿法冶金浸出技术和工艺路线。
湿法冶金浸出
技术的发展与应用,促进了相关产业的发展转型和生态环境的可持续发展。
在实际应用中,采用了很多新技术和新方法,使湿法浸出技术的效率和稳定性都得到了比较大的提高。
膜
分离技术、生物浸出技术、氧化铝陶瓷等先进材料的应用,都可以提高湿法冶金浸出技术
的性能和效益。
膜分离技术是一种高效分离技术,适合于分离浸出液中的杂质物和沉淀物,提高了金
属离子的回收率和品质。
在稀有金属冶炼、废弃物处理等领域的湿法浸出过程中,膜分离
技术能够提升工艺效率,提高纯度和质量。
生物浸出技术是一种环保型的湿法浸出技术,
通过微生物能够实现矿石的高效浸出和金属元素的提取,可缩短提取时间,降低能耗,减少废料和废液的排放。
氧化铝陶瓷是一种高温、高硬度的陶瓷材料,由于其优异的耐腐蚀、耐磨性能,在湿法冶金浸出技术中应用得较为广泛。
在铝冶炼过程中,常会产生含有高浓度氯化铝的液态废料,由于其对机械设备容易造成腐蚀,使用氧化铝陶瓷材料制作设备零部件能够很好地解决这一问题。
氧化铝陶瓷材料还具有氧离子传导、催化和过滤等功能,常被应用在湿法废料处理、废气净化和高温反应器等领域,起到了重要的作用。
湿法冶金浸出技术在不同领域的应用取得了显著的效益和成果。
对于该技术的研发和应用,应该继续注重创新和实践,探究出高效、低成本和环保型的新技术和新方法。
还需立足于市场需求和社会责任,协同各方力量,促进湿法冶金浸出技术的可持续发展和创新升级。