钻井队物体打击事故
钻探企业物体打击事故主要原因分析及防范对策

钻探企业物体打击事故主要原因分析及防范对策根据《GB6441-86企业职工伤亡事故分类》标准中,物体打击事故位列首项,可见在我国各行各业中,该类事故是所有企业防范事故发生的重点。
本文通过统计企业近年伤害事故,同样得出钻井现场物体打击事故为高发事故类型的结论,从列举物体打击事故中,分析事故发生共性特点,有针对性地制定事故防范对策,并提出见解。
标签:物体打击;事故原因分析;防范对策引言为了持续提升企业HSE管理水平,有必要对钻探企业以往历年人身伤害事故统计分析,查找事故共性特点,降低安全生产事故发生概率,本文以人身伤害事故类型统计为事实依据,深度剖析导致物体打击事故发生的管理原因,引申出企业所属部分单位在变更管理、危害辨识、过程监管、安全培训等均存在明显的管理缺陷问题,由此提出了事故预防对策和建议。
1.人身伤害事故统计经近年来企业事故的统计分析,物体打击事故仍是企业多发的主要事故类型,物体打击事故已占所有事故类型46%的比例。
所以,有必要对物体打击事故详细剖析事故发生原因,并制定具体的事故防范控制措施。
2.物体打击事故典型事故举例案例1:某队盘大绳作业。
司钻在操作绞车发现不能运转,活绳头无法入位,大班立即维修绞车滚筒。
副队长在钻机滚筒前用管钳卡住大绳,一名钻工准备用大锤敲击管钳使活绳头就位,另一名钻工使用撬棍别活绳头,大绳约2米左右拖在地面。
大班排除设备故障后离开。
此时,绞车滚筒突然转动约一圈,卷起的大绳瞬间抽到一名钻工左后背,造成全身多处骨折。
案例2:某队进行钻进作业。
班组在从场地向钻台吊垫杠上最后一根加重钻杆,此时,场地工负责挂绳套,站在场地坡道右侧距离管排约2米处,扭头发现垫杠朝他滚过来,因躲闪不及,垫杠一端砸到其右小腿倒地,造成右小腿骨折。
3.物体打击事故共性原因分析根据上述两起典型物体打击事故总结分析得出,此类事故在人的不安全行为、管理缺陷方面均具有相似的共性特点,究其根本原因则是由于人安全意识不足和管理不到位促使了事故发生的必然性,原因分析如下:3.1人的不安全行为3.1.1违反操作规程案例1中设备检维修未执行挂牌上锁能量隔离程序,致使能量意外释放。
西南石油工程有限公司四川钻井分公司“4.23”物体打击事故
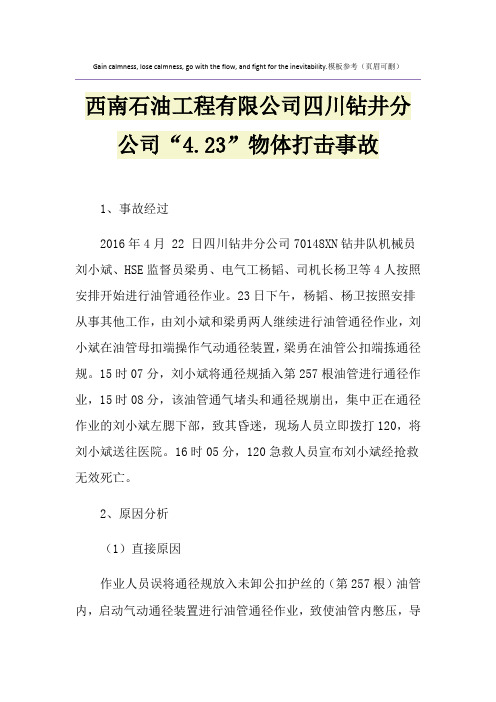
Gain calmness, lose calmness, go with the flow, and fight for the inevitability.模板参考(页眉可删)西南石油工程有限公司四川钻井分公司“4.23”物体打击事故1、事故经过2016年4月 22 日四川钻井分公司70148XN钻井队机械员刘小斌、HSE监督员梁勇、电气工杨韬、司机长杨卫等4人按照安排开始进行油管通径作业。
23日下午,杨韬、杨卫按照安排从事其他工作,由刘小斌和梁勇两人继续进行油管通径作业,刘小斌在油管母扣端操作气动通径装置,梁勇在油管公扣端拣通径规。
15时07分,刘小斌将通径规插入第257根油管进行通径作业,15时08分,该油管通气堵头和通径规崩出,集中正在通径作业的刘小斌左腮下部,致其昏迷,现场人员立即拨打120,将刘小斌送往医院。
16时05分,120急救人员宣布刘小斌经抢救无效死亡。
2、原因分析(1)直接原因作业人员误将通径规放入未卸公扣护丝的(第257根)油管内,启动气动通径装置进行油管通径作业,致使油管内憋压,导致通气堵头和通径规由母扣端崩出,击中作业人员左腮下部,致其昏迷,后送医院经枪救无效死亡。
(2)管理原因一是违章作业。
通径作业前,作业人员偷懒图省事,未按《BGT1扣特殊密封镍基合金油管使用注意事项》将油管解捆排放和拆卸全部护丝,给误操作和事故埋下隐患。
二是气动通径装置设计、制造、试用、鉴定和使用无规范约束。
气动通径装置设计、加工随意,装置的通气堵头由非承压元件油管母扣护丝临时改装而成,缺少安全技术评估,使用无章可循。
三是风险分析、安全技术措施落实不到位。
《元坝12-1H井作业危害分析》表中未识别出通径作业憋压导致物体打击的风险,未制定相应的安全措施;作业入员没有全员参加风险分析,未对全部作业人员进行书面安全交底。
(3)根原因公司对油管通径作业长期不重视,习惯性违章作业。
中石油七起事故案例统计
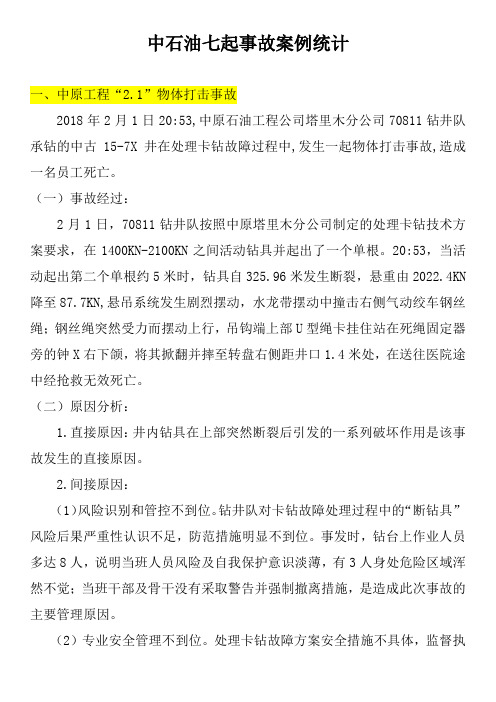
中石油七起事故案例统计一、中原工程“2.1”物体打击事故2018年2月1日20:53,中原石油工程公司塔里木分公司70811钻井队承钻的中古15-7X井在处理卡钻故障过程中,发生一起物体打击事故,造成一名员工死亡。
(一)事故经过:2月1日,70811钻井队按照中原塔里木分公司制定的处理卡钻技术方案要求,在1400KN-2100KN之间活动钻具并起出了一个单根。
20:53,当活动起出第二个单根约5米时,钻具自325.96米发生断裂,悬重由2022.4KN 降至87.7KN,悬吊系统发生剧烈摆动,水龙带摆动中撞击右侧气动绞车钢丝绳;钢丝绳突然受力而摆动上行,吊钩端上部U型绳卡挂住站在死绳固定器旁的钟X右下颌,将其掀翻并摔至转盘右侧距井口1.4米处,在送往医院途中经抢救无效死亡。
(二)原因分析:1.直接原因:井内钻具在上部突然断裂后引发的一系列破坏作用是该事故发生的直接原因。
2.间接原因:(1)风险识别和管控不到位。
钻井队对卡钻故障处理过程中的“断钻具”风险后果严重性认识不足,防范措施明显不到位。
事发时,钻台上作业人员多达8人,说明当班人员风险及自我保护意识淡薄,有3人身处危险区域浑然不觉;当班干部及骨干没有采取警告并强制撤离措施,是造成此次事故的主要管理原因。
(2)专业安全管理不到位。
处理卡钻故障方案安全措施不具体,监督执行不严格。
(3)“三基”工作存在薄弱环节。
日常培训不到位,基层员工的安全意识、岗位风险识别能力、操作技能、制度执行力亟待加强。
3.下步措施:(1)狠抓“三基”工作。
强化日常培训,切实提高广大干部员工的风险和自我保护意识;狠反“三违”和“低、老、坏”现象,切实提高规章制度的执行力。
(2)狠抓风险管控。
严格工作安全分析,严格作业许可制度执行。
(3)狠抓专业安全管理。
严格钻具和工具管理,防止不合格钻具和工具入井;严格工艺参数,避免满负荷作业,杜绝超载作业;严格安全措施,任何工程技术措施实施必须充分考虑人身安全。
某油田钻井工程公司物体打击事故案例分析
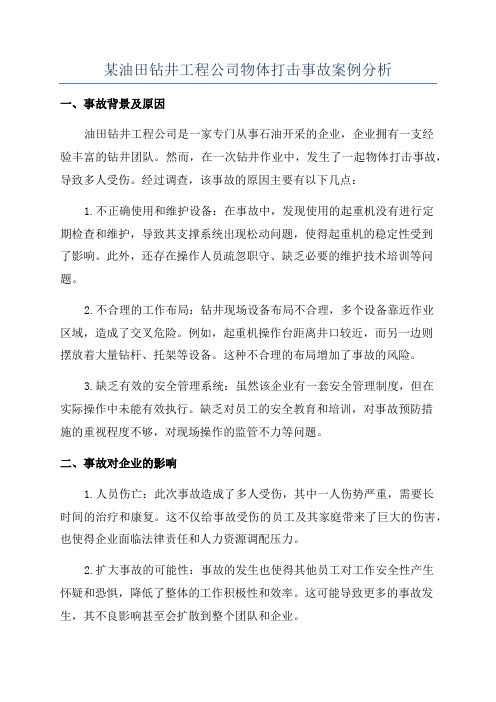
某油田钻井工程公司物体打击事故案例分析一、事故背景及原因油田钻井工程公司是一家专门从事石油开采的企业,企业拥有一支经验丰富的钻井团队。
然而,在一次钻井作业中,发生了一起物体打击事故,导致多人受伤。
经过调查,该事故的原因主要有以下几点:1.不正确使用和维护设备:在事故中,发现使用的起重机没有进行定期检查和维护,导致其支撑系统出现松动问题,使得起重机的稳定性受到了影响。
此外,还存在操作人员疏忽职守、缺乏必要的维护技术培训等问题。
2.不合理的工作布局:钻井现场设备布局不合理,多个设备靠近作业区域,造成了交叉危险。
例如,起重机操作台距离井口较近,而另一边则摆放着大量钻杆、托架等设备。
这种不合理的布局增加了事故的风险。
3.缺乏有效的安全管理系统:虽然该企业有一套安全管理制度,但在实际操作中未能有效执行。
缺乏对员工的安全教育和培训,对事故预防措施的重视程度不够,对现场操作的监管不力等问题。
二、事故对企业的影响1.人员伤亡:此次事故造成了多人受伤,其中一人伤势严重,需要长时间的治疗和康复。
这不仅给事故受伤的员工及其家庭带来了巨大的伤害,也使得企业面临法律责任和人力资源调配压力。
2.扩大事故的可能性:事故的发生也使得其他员工对工作安全性产生怀疑和恐惧,降低了整体的工作积极性和效率。
这可能导致更多的事故发生,其不良影响甚至会扩散到整个团队和企业。
3.影响公司声誉:事故的发生首先暴露了企业安全管理有缺陷的问题,会对公司声誉和客户信任造成重大打击。
随着事故的传播,公司可能面临各种监管部门的调查和罚款,进一步损害了企业形象。
1.不正确使用和维护设备问题:在事故中起重机的松动是导致物体打击事故发生的根本原因。
这与公司未能及时进行定期检查和维护有关。
在这种风险较高的作业环境中,对设备进行定期维护和检查至关重要。
此外,需要确保操作人员熟悉设备的使用,以及掌握设备的维护方法和技巧。
2.不合理的工作布局问题:不合理的作业布局也增加了事故的风险。
胜利石油渤海钻井物体打击事故分析2021
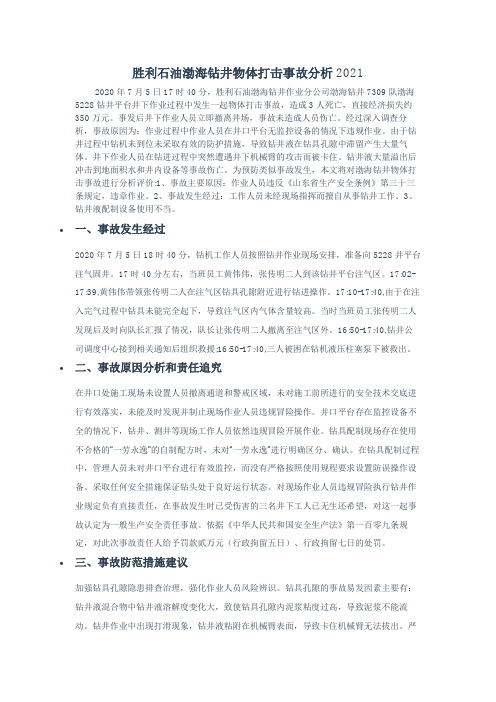
胜利石油渤海钻井物体打击事故分析20212020年7月5日17时40分,胜利石油渤海钻井作业分公司渤海钻井7309队渤海5228钻井平台井下作业过程中发生一起物体打击事故,造成3人死亡,直接经济损失约350万元。
事发后井下作业人员立即撤离井场,事故未造成人员伤亡。
经过深入调查分析,事故原因为:作业过程中作业人员在井口平台无监控设备的情况下违规作业。
由于钻井过程中钻机未到位未采取有效的防护措施,导致钻井液在钻具孔隙中滞留产生大量气体。
井下作业人员在钻进过程中突然遭遇井下机械臂的攻击而被卡住。
钻井液大量溢出后冲击到地面积水和井内设备等事故伤亡。
为预防类似事故发生,本文将对渤海钻井物体打击事故进行分析评价:1、事故主要原因:作业人员违反《山东省生产安全条例》第三十三条规定,违章作业。
2、事故发生经过:工作人员未经现场指挥而擅自从事钻井工作。
3、钻井液配制设备使用不当。
•一、事故发生经过2020年7月5日18时40分,钻机工作人员按照钻井作业现场安排,准备向5228井平台注气固井。
17时40分左右,当班员工黄伟伟,张传明二人到该钻井平台注气区。
17:02-17:39,黄伟伟带领张传明二人在注气区钻具孔隙附近进行钻进操作。
17:10-17:40,由于在注入完气过程中钻具未能完全起下,导致注气区内气体含量较高。
当时当班员工张传明二人发现后及时向队长汇报了情况,队长让张传明二人撤离至注气区外。
16:50-17:40,钻井公司调度中心接到相关通知后组织救援;16:50-17:40,三人被困在钻机液压柱塞泵下被救出。
•二、事故原因分析和责任追究在井口处施工现场未设置人员撤离通道和警戒区域,未对施工前所进行的安全技术交底进行有效落实,未能及时发现并制止现场作业人员违规冒险操作。
井口平台存在监控设备不全的情况下,钻井、测井等现场工作人员依然违规冒险开展作业。
钻具配制现场存在使用不合格的“一劳永逸”的自制配方时,未对“一劳永逸”进行明确区分、确认。
1402固井队“5·16”物体打击事故

2006 年 5 月 16 日华北石油局轮台项目部 1402 固井队在塔河基 地进行卧式灰罐组改建完毕试压时,发生一起物体打南事故到使一个 死亡。
二、事故原因和事故定性备在 利用,违章作业是导致这起事故发生的直接原因。
事故间接原因:改造施工随意性过大,改建工程项目安全设施未 及时进行“三同时”工作;安全管理工作不到位,特殊工种管理不严, 无焊接资质人员进行焊接作业。现场作业人员安全意识淡薄,部分施 工人员戴安全帽,违反试压现场安全规定。
钻修井业务承包商事故通报
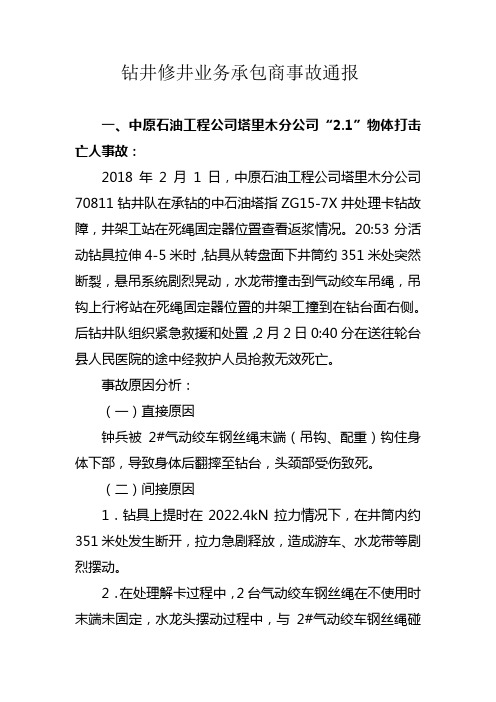
钻井修井业务承包商事故通报一、中原石油工程公司塔里木分公司“2.1”物体打击亡人事故:2018年2月1日,中原石油工程公司塔里木分公司70811钻井队在承钻的中石油塔指ZG15-7X井处理卡钻故障,井架工站在死绳固定器位置查看返浆情况。
20:53分活动钻具拉伸4-5米时,钻具从转盘面下井筒约351米处突然断裂,悬吊系统剧烈晃动,水龙带撞击到气动绞车吊绳,吊钩上行将站在死绳固定器位置的井架工撞到在钻台面右侧。
后钻井队组织紧急救援和处置,2月2日0:40分在送往轮台县人民医院的途中经救护人员抢救无效死亡。
事故原因分析:(一)直接原因钟兵被2#气动绞车钢丝绳末端(吊钩、配重)钩住身体下部,导致身体后翻摔至钻台,头颈部受伤致死。
(二)间接原因1.钻具上提时在2022.4kN拉力情况下,在井筒内约351米处发生断开,拉力急剧释放,造成游车、水龙带等剧烈摆动。
2.在处理解卡过程中,2台气动绞车钢丝绳在不使用时末端未固定,水龙头摆动过程中,与2#气动绞车钢丝绳碰撞,造成钢丝绳大幅摆动。
3.钻台面杂物较多,逃生通道不畅。
二、塔里木油田承包商巴州兆石钻井公司“3.14”物体打击亡人事故:2018年3月14日9:15,塔里木油田承包商巴州兆石钻井公司Z8004钻井队在吐北401井拆甩设备进行甩钻操作,工作人员在用钻杆钩子钩钻具过程中跌落跑道被钻具压倒,造成1人钻具打击伤害死亡。
事故原因分析(一)直接原因场地工豪某使用钻杆钩校正钻杆方向,不慎从猫道跌落地面,滑落的钻杆砸中其头部导致受伤,送医抢救无效死亡。
(二)间接原因1. 猫道设计存在缺陷,钻杆未进入猫道卡槽,用滚杠作为支撑向管桥架移动钻杆,滚杠在钻杆滚动过程中易发生偏斜,导致钻杆发生偏斜,猫道右侧滚落。
酸化压裂作业时移开猫道右侧管桥架,施工结束未及时恢复,甩钻具作业时未识别出钻具向右侧滚落和人员跌落的风险。
现场干部员工安全意识淡薄,甩钻具作业时场地工豪某站位不当,干部未对甩钻具作业的员工进行风险告知。
某油田钻井工程公司物体打击事故案例分析

某油田钻井工程公司物体打击事故案例分析2004年9月17日22时59分左右,某油田钻井工程公司第二钻井公司50648钻井队在进行下套管作业中,发生一起物体打击事故,造成1人死亡。
一、事故经过2004年钻井工程公司通过议标的方式获取某油田公司官69-46井的施工权,官69-46井位于河北省沧县王官屯乡何官屯村东。
承钻该井的50648队于7月22日搬迁,7月28日开钻。
该井于9月10日完钻,完钻井深3368米,2004年9月17日10时30分起钻完,之后作下套管准备工作,至13时15分开始下油层套管(?139.7mm)作业。
下套管前由对队长谢某主持召开了特殊作业安全会,并对班组人员进行了分工,即当班人员分成两组,由司钻孙某和副司钻李某各带一组,大班、队部人员插入到两个小组当中,轮流下套管。
司钻一组由孙某操作刹把,副司钻一组由副队长董某操作刹把。
当副司钻一组下套管作业进行到22时35分左右时,开始向套管内灌泥浆(套管下深1859.04m,入井套管189根)。
这时,副队长葛某、技术员刘某、司钻孙某、大班司钻赵某等6人上钻台接替副司钻一组人员。
副司钻李某走到钻台前端左侧小绞车处与操作小绞车的钻台大班赵某闲聊了几句,便走下钻台。
此时,已灌满泥浆,时间在22时50分左右,钻台人员继续下套管作业,由司钻孙某操作刹把,技术员刘某和井架工张某负责井口操作,副队长葛某和钻工康某负责卸护丝和小鼠洞操作。
在游车将第190根套管提出小鼠洞后,赵某操作小绞车将第191根套管放入小鼠洞内。
此时因游车摆动较大,井口操作人员感觉第190根套管越来越倾斜,这时就听到有人喊了一声“吊卡开了”,葛某急忙抬头看,发现第190根套管向钻台坡道口方向倒下,随即喊了一声“快跑”,井口操作人员马上向钻台两侧躲开。
第190根套管在倾倒的过程中,先砸在左侧钻台盒的钻杆立柱上,又砸在坡道左边防护链桩的左侧,在侧向力和惯性力的作用下套管改变了下落方向,以左侧防护链桩和钻台护栏端面为支点,迅速滑向钻台左侧的梯子,在向前滑落的过程中,套管的前端冲击到梯子的外侧挡板,在梯子挡板的作用下,套管又改变方向,顺着钻台梯子向下滑落,直至套管的母扣戳在地面。
- 1、下载文档前请自行甄别文档内容的完整性,平台不提供额外的编辑、内容补充、找答案等附加服务。
- 2、"仅部分预览"的文档,不可在线预览部分如存在完整性等问题,可反馈申请退款(可完整预览的文档不适用该条件!)。
- 3、如文档侵犯您的权益,请联系客服反馈,我们会尽快为您处理(人工客服工作时间:9:00-18:30)。
钻井队物体打击事故集团企业公司编码:(LL3698-KKI1269-TM2483-LUI12689-ITT289-
某钻井队“10·31”物体打击事故2005年10月31日3时20分,某石油管理局钻探集团钻井一公司第二分公司30646钻井队在葡220—105井执行完井甩钻具作业时,钻杆打在谷某左胸部,送医院途中死亡。
一、事故经过
钻井一公司第二分公司成立于1982年,位于大庆市让胡路区乘风南路6号,是以钻井施工为主的生产单位。
30646钻井队组建于2005年8月,由10519钻井队部分人员及新召的青工组成,使用ZJ30DB型钻机。
2005年10月30日11时,30646钻井队作业人员操作ZJ30DB型钻机,在位于大同区老山头乡保山村附近的葡220—105井执行完井作业,准备甩钻具。
31日凌晨3时,四班接班后七名作业人员继续甩钻具。
3时20分,甩到第28柱(当班第二柱)钻杆时,第三根钻杆甩到大门坡道上,钻杆母扣台肩卡在大门坡道上沿处,负责在地摆正钻杆的场地工谷某(男,22岁,2005年8月新召市场化用工)为了让钻杆滑下来,站在滑道右侧用撬杠撬钻杆底部,钻杆在受力下滑的过程中,钻杆上端弹出坡道,由坡道外滚下,谷某躲闪不及,被钻杆打在左胸部,将谷某砸倒。
该班当即停止甩钻具作业,迅速将谷某送往油田总医院集团庆葡医院救治,因伤势过重,送医院途中死亡。
二、事故原因
(一)直接原因
安全意识淡薄,思想麻痹,对可能发生的危险预测不够,为让钻杆滑下,违章撬动钻杆,致使钻杆上端弹出坡道,由坡道外滚下,将谷某砸伤致死。
(二)间接原因
1、对甩钻具等关键和复杂工序,把关不严,未按照安全生产责任制的要求,认真执行技术规程,实行标准化作业,从而导致事故的发生。
2、30646钻井队发生事故的时间是交接班前后,这时准备下班的职工心理放松了,而刚接班的精神上还没有完全进入状态。
3、安全保障措施不落实,安全操作规程执行不严格。
基层队只强调对岗位人员如何加强自身安全防护,而忽视了对他人安全的监督和照顾,班组作业还没有完全形成互相联动的安全防护机制。
(三)管理原因
1、“师带徒”的传、帮、教措施落实不到位。
2、专职安全监督员未提示到位、指导到位、监督到位,不能疏于职守,造成生产过程中的安全控制“真空”,导致安全事故的发生。
3、值班干部不够认真负责,仅仅满足于跟班作业,未承担起班组安全监督的职责。
4、在队伍管理和队伍建设方面,基层钻井队未能始终如一地把安全工作当作首要任务来抓,尤其在夜间施工和交接班前后是各类事故的多发期,不能提醒上岗职工互相照顾,注意安全,搞好配合。
5、员工的安全培训教育不到位,特别是新员工的培训教育不够,风险识别能力弱,自我保护能力不强,岗位操作规程不清,操作技能水平低。
三、事故教训及防范措施
(一)现场安全管理存在漏洞,个别基层队把抓生产抓效益作为重点,麻痹大意,侥幸松懈,在劳动组织上存在不协调的现象。
要牢固树立“安全第一、预防为主”的安全工作方针,认真落实各级安全生产责任制,时时讲安全,事事重安全,处处抓安全。
从基础工作入手,狠抓基层建设,配齐配全符合岗位要求的作业人员,杜绝事故的重复发生。
(二)员工风险识别能力弱,自我保护能力不强,岗位操作规程不清,操作技能水平低,岗位安全培训效果差。
因此,要结合近年来新入厂青工多的实际,进一步加强安全教育培训,提高现场作业人员、管理人员和各级管理者的安全意识;改进教育培训的方式、方法,提高培训的质量和效果;落实“师带徒”的传、帮、教等措施,尽快提高青工的操作技能和安全技能。
(三)个别基层队忽视细节管理,不注重钻井施工全过程的控制和管理,施工作业流程中存有习惯性违章现象,有些安全隐患得不到有效根除。
因此,各级管理人员要把安全管理工作的重点放到基层,放在岗位,要充分发挥基层干部和班组长在安全管理上的监督和引导作用,杜绝“三违”行为。
(四)重点生产施工环节安全措施不落实,安全管理不到位。
因此,要切实做到“没有计划不施工,没有方案不施工,没有进行危害识别不施工,没有落实安全防范措施不施工,没有检查确认不施工”。