生产过程中防止污染和交叉污染管理规程
质量管理体系 防止污染和交叉污染管理
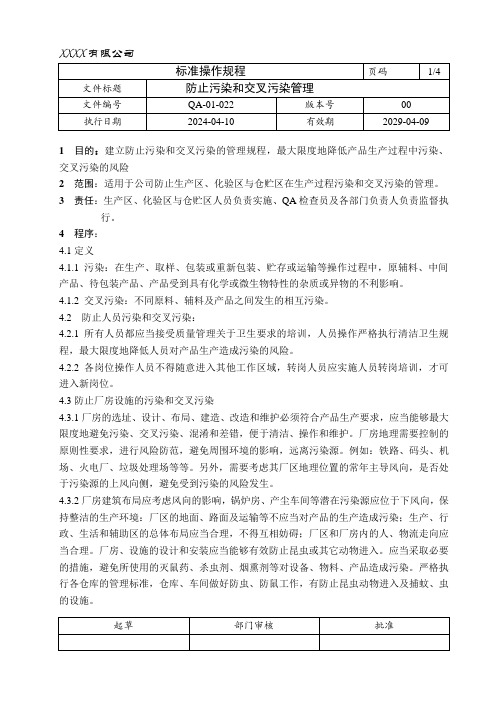
1 目的:建立防止污染和交叉污染的管理规程,最大限度地降低产品生产过程中污染、交叉污染的风险2 范围:适用于公司防止生产区、化验区与仓贮区在生产过程污染和交叉污染的管理。
3 责任:生产区、化验区与仓贮区人员负责实施、QA检查员及各部门负责人负责监督执行。
4 程序:4.1定义4.1.1 污染:在生产、取样、包装或重新包装、贮存或运输等操作过程中,原辅料、中间产品、待包装产品、产品受到具有化学或微生物特性的杂质或异物的不利影响。
4.1.2 交叉污染:不同原料、辅料及产品之间发生的相互污染。
4.2 防止人员污染和交叉污染:4.2.1 所有人员都应当接受质量管理关于卫生要求的培训,人员操作严格执行清洁卫生规程,最大限度地降低人员对产品生产造成污染的风险。
4.2.2 各岗位操作人员不得随意进入其他工作区域,转岗人员应实施人员转岗培训,才可进入新岗位。
4.3防止厂房设施的污染和交叉污染4.3.1厂房的选址、设计、布局、建造、改造和维护必须符合产品生产要求,应当能够最大限度地避免污染、交叉污染、混淆和差错,便于清洁、操作和维护。
厂房地理需要控制的原则性要求,进行风险防范,避免周围环境的影响,远离污染源。
例如:铁路、码头、机场、火电厂、垃圾处理场等等。
另外,需要考虑其厂区地理位置的常年主导风向,是否处于污染源的上风向侧,避免受到污染的风险发生。
4.3.2厂房建筑布局应考虑风向的影响,锅炉房、产尘车间等潜在污染源应位于下风向,保持整洁的生产环境:厂区的地面、路面及运输等不应当对产品的生产造成污染;生产、行政、生活和辅助区的总体布局应当合理,不得互相妨碍;厂区和厂房内的人、物流走向应当合理。
厂房、设施的设计和安装应当能够有效防止昆虫或其它动物进入。
应当采取必要的措施,避免所使用的灭鼠药、杀虫剂、烟熏剂等对设备、物料、产品造成污染。
严格执行各仓库的管理标准,仓库、车间做好防虫、防鼠工作,有防止昆虫动物进入及捕蚊、虫的设施。
制药企业防止生产过程中的污染、交叉污染及混淆的措施(GMP课件)
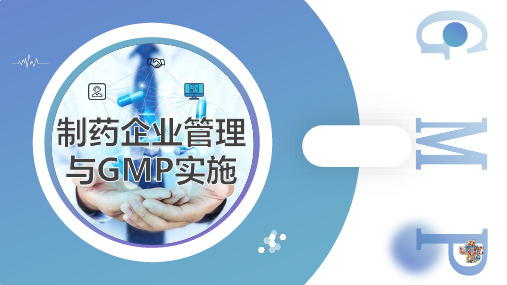
三、培训防止生产过程中的污染、交叉污染及其混淆的措施
2.生产区域专一 在同一生产区域包括相应的辅助生产区域,只能生产同一批号、同一规格的相同产品。在同一
生产区域包括相应的辅助生产区域同时生产不同品种、规格或批号的药品是混淆产生的最主要的原 因,必须坚决制止,以防止混叉污染及其混淆的措施
3.生产前检查 每品种或每批号生产开始前,应认真检查设备、器械、容器等是否洁净或灭菌,以
及是否有前次生产的遗留物,否则不能进行新的生产操作。 4.状态标志明确
每一生产操作间、每一台生产设备、每一盛物容器均应有能够指明正在加工的 产品或物料、批号及数量等的状态标志。在生产中无状态标志是造成混药事故的主要原 因之一。
⑤在易产生交叉污染的生产区内,操作人员应当穿戴该区域专用的防护服; ⑥采用经过验证或已知有效的清洁和去污染操作规程进行设备清洁;必要时,应当对与物料直接接触的 设备表面的残留物进行检测; ⑦采用密闭系统生产; ⑧干燥设备的进风应当有空气过滤器,排风应当有防止空气倒流装置; ⑨生产和清洁过程中应当避免使用易碎、易脱屑、易发霉器具;使用筛网时,应当有防止因筛网断裂而 造成污染的措施; ⑩液体制剂的配制、过滤、灌封、灭菌等工序应当在规定时间内完成;软膏剂、乳膏剂、凝胶剂等半固 体制剂以及栓剂的中间产品应当规定贮存期和贮存条件。
二、混淆的产生
(一)混淆: 混淆是指一种或一种以上的其他原材料或成品已标明品名等的原材
料或成品相混,通俗的说法,称为“混药”。 如原料与原料,成品与成品,标签与标签,有标志的与未标志的,
已包装的与未包装的混淆等。 (二)产生混淆的原因: 1、厂房:生产区域狭小、拥挤,同一区域有不同规格、品种、批号的 药品同时生产;生产中物料流向不合理,生产线交叉;生产、运贮、 仓贮无保证措施;非生产人员进入等造成无意或有意混淆事件等。 2、设备:生产中使用的设备、容器无状态标志,清场不彻底等造成。
防止交叉污染和外来污染制度范文(3篇)

防止交叉污染和外来污染制度范文为防止饲料生产过程中的原料、半成品及成品交叉污染和被外来物污染,影响公司产品的安全卫生,对有可能产生外来污染的各个环节进行有效控制,特制定本制度。
1、为防止不同品种饲料之间的混料或交叉污染,影响公司产品的安全卫生,将原料库设为饲料添加剂区域、大宗原料区域、药物饲料添加剂区域、矿物质原料区域,在各个区域内合理安排原料垛位,各原料品种垛位要间隔一定距离(不小于30cm)每个原料垛位要以垛位卡标识清楚。
2、生产过程中使用同一生产含药物饲料添加剂和不含药物添加剂‘无药物在先,有药物在后’,‘低浓度在先,高浓度在后’的生产顺序。
3、成品保管在入库时,根据成品料的类型将成品库划分区域,标识清楚,成品库原料库分开布局。
4、为防止饲料生产过程中的原料、半成品及成品被外来物污染,影响公司产品的安全卫生,采购原料时运输车辆不得存在沙石、铁屑、秸秆、农药、害虫、化肥、霉变物料等外来掺杂物污染原料,卸车时,控制霉变、杂质、生芽、生虫等外来掺杂物。
5、生产过程中要保持生产现场良好的清洁状态,及时清扫杂物,不得在生产过程中进行维修、焊接、气割等作业。
6、车间、仓库有防鼠、防鸟措施,及时清理杂物防止害虫滋生。
7、当发现或怀疑物料受到交叉污染或异物污染时,应立即报告车间主任、质监员,分析原因,做出处理决定,并采取有效措施防止类似事件再次发生。
防止交叉污染和外来污染制度范文(2)一、背景介绍随着社会的发展和经济的繁荣,人们对环境和健康的关注度也越来越高。
交叉污染和外来污染是当前面临的主要环境问题之一。
为了有效预防和控制交叉污染和外来污染,制定一套科学、完善的制度是非常必要的。
二、总体原则1. 科学合理:制度应基于科学研究和实践经验,确保其有效性和可操作性。
2. 综合治理:综合考虑不同环境组分的交互作用和各方面的影响,采取综合治理措施,全面保护环境安全。
3. 强制执行:制度应有明确的法律效力,必须得到各方的认同和遵守。
防止污染及交叉污染管理规程

纯化水日常监控及检测管理制度目的:建立纯化水日常监控及检测管理制度,加强管理,确保纯化水质量。
二、适用范围:适用于纯化水的日常监控及检测。
三、责任者:生产部工艺员、质保部纯化水检测人员、纯化水制备岗位操作人。
四、管理制度:1、纯化水制备岗位的日常监控:1.1 上岗时,随时检查纯化水生产线各部件的运行情况,确保纯化水生产线的正常运转。
1.2 随时查看纯化水生产线自动监测系统显示器上的数据(进水电导、出水电导、终端水质、进水电导为一级RO进水电导、出水电导为一级RO产品水的电导,终端水质为混合床出水经超滤后的电阻),并每两小时记录一次。
每两小时测定一纯化水的酸碱度、氯离子、氨盐含量。
并做好记录,见《纯化水制备岗位操作记录》(编码:RD0103700)。
1.3 测酸碱度、氯离子、氨盐的试液由质保部统一配制,交给纯化水制备岗位使用。
1.4 酸碱度、氯离子、氨盐含量测定方法及合格标准为2000版《中国药典》二部。
1.4.1 酸碱度:取纯化水10ml,加甲基红指示液2滴,不得显红色;另取纯化水10ml,加活一香草酚蓝指示液5滴,不得显蓝色。
1.4.2 氯离子:取纯化水50ml,加硝酸5滴与硝酸银试液,不得发生浑浊。
1.4.3 氨:取本品50ml,加碱性碘化录钾试液20ml,放置15分钟,如显色,与氯化铵溶液(取氯化铵31.5mg,加无氨水适量使溶解并稀释成1000ml)1.5ml,加无氨水48ml与碱性碘化录钾试液2ml制成的对照液比较,不得更深。
1.5 对纯化水生产线各部件的进水压力进行控制,并每2小时作一次记录,见《纯化水生产线操作数据记录》(编码:RD0106400)。
2、质保部的检测:2.1纯化水生产线正常运转投入使用后,质保部每7天做一次纯化水检测,包括微生物含量。
取样时,纯化水送水总口,回水总口,纯水箱每次取样,各使用点随机轮换取样,每次取5个。
但保证各使用点每月至少取样一次。
取样点见纯化水使用分布图。
饲料厂防止生产过程中交叉污染制度

饲料厂防止生产过程中交叉污染制度一、目的建立生产过程中防止交叉污染的管理制度,防止因控制或人为操作不当造成交叉污染.二、适应范围适用于生产操作过程中交叉污染的控制.三、职责1.生产员工负责该制度的具体实施;2.现场品控负责实施过程的监督.四、具体内容为了防止交叉污染,饲料厂的选址和设计要求最大限度地防止饲料贮存、生产加工过程中受到污染,厂区周围无污染源,生产区、生活区、办公区隔离.现生产部起草防止生产过程中交叉污染制度,从以下方面对如何避免生产过程中的交叉污染做出更加明确具体的规定:1合理安排生产顺序,要尽量避免交叉污染.按照“无药物的在先,有药物的在后”原则制定生产计划;生产含有药物饲料添加剂的饲料时,应根据药物类型,先生产药物含量低的饲料,再生产药物含量高的饲料;2建立生产线清洗操作规程.生产含有药物饲料添加剂的饲料产品后更换另一品种时,应使用豆粕或玉米粉等原料对生产线进行清洗.用于清洗的原料只能回置于同品种产品中,并保存生产线清洗记录配合料该记录含在中控岗位操作记录中和清洗料使用记录;3盛放饲料添加剂、药物饲料添加剂、添加剂预混合饲料、含有药物添加剂的饲料产品和中间产品的器具应标识清楚,并保证器具专用,不得交叉混用;4原料贮存期间严格按照原料仓储管理制度进行,避免交叉污染.5生产设备每天进行清理,及时清除残存料、粉尘积垢等残留物,并填写设备清理记录.6各岗位人员严格按照环境卫生管理制度打扫生产场区环境卫生,在更换品种时,对大料、小料投料口要及时清扫,清除桌设备上、地板、墙壁等处的粉尘及残余物.7生产内勤每周不定期时抽查一次生产区环境的清洁情况,并填写生产部卫生检查记录表.8从事引起粉尘量较大的工作,如称量、粉碎、投料等,应尽量靠近排尘口,并将动作放轻,经常擦拭工作间及工作台表面,减少积尘.9当发现或怀疑物料受到交叉污染时,应立即报告技术经理,分析原因,做出处理决定,并采取有效措施防止类似事件再次发生.10正在进行生产时,使用的器具、已经领取的核心料及小品种原料要有明确的状态标志,标明器具或核心料及小品种原料的名称,以防器具混用或核心料及小品种原料混淆.11中控工应具备岗位资格证书,具备熟练的岗位操作技能,避免因岗位操作不熟练造成串仓现象;12严禁不同车间配合料车间、核心料车间和预混料车间人员随意串动,生产工具相互串用.13运输用车辆、工具、铺垫物、遮盖物必须清洁,不得将原料、成品与易燃、易爆、有辐射及有毒、有害物品的污染物混装、混运.五、相关文件及记录1.文件1原料仓储管理制度2环境卫生管理制度2.记录1生产线清洗记录 YQ-SLS02-JL012中控岗位操作记录 YQ-SLS02-JL023清洗料使用记录 YQ-SLS02-JL034设备清理记录 YQ-SLS04-JL04-1-35生产部卫生检查记录表 YQ-SLS02-JL04。
027防止污染和交叉污染管理规程

Q/JGR 集安广润中药饮片有限公司企业管理标准SMP-SC-027-01 防止污染和交叉污染管理规程2020-06-15 发布 2020-07-15 实施集安广润中药饮片有限公司发布防止污染及交叉污染管理规程1 目的建立防止污染及交叉污染管理规程,防止因控制或人为操作不当造成污染及交叉污染。
2 范围生产车间3 责任生产部责任:制定本规程并监督实施质量管理部责任:进行监督和确认设备管理部责任:保证生产用设备、设施满足药品质量要求生产车间责任:执行本规程4 内容4.1 防止人员污染和交叉污染4.1.1 所有人员都应当接受卫生要求的培训,人员操作严格执行《人员卫生管理规程》,最大限度地降低人员对药品生产造成污染的风险。
4.1.2 各级管理人员严格监控,防止体表有伤口、患有传染病或其他可能污染药品疾病的人员从事直接接触药品的生产。
患有污染药品疾病的人员必须积极主动地配合主管部门的工作。
4.2 防尘措施4.2.1 生产中对产尘操作区域安装防护罩。
4.2.2 员工操作时对于易产尘的物料要轻拿轻放,避免产生粉尘。
4.3 防止厂房设施的污染和交叉污染4.3.1 厂房的选址、设计、布局、建造、改造和维护必须符合药品工艺流程,应当能够最大限度的避免污染、交叉污染、混淆和差错,便于清洁、操作和维护。
厂房地理位置需要控制的原则性要求,进行风险防范,避免受周围环境的影响,远离污染源。
4.3.2 厂区的地面、路面及运输等不应对药品生产造成污染;生产、行政、生活和辅助区总体布局要合理,不得互相妨碍;厂区和厂房内的人、物流走向应当合理。
厂房的设施和安装能够有效的防止昆虫或其它动物进入。
应当采取措施,避免所用的灭鼠药、杀虫剂等对设备、物料、产品造成污染。
严格执行各仓库的管理标准,仓库、车间做好防虫、防鼠工作,有防止昆虫动物进入,并装有捕蚊、虫的设施。
4.3.3 药品生产厂房不得用于生产对药品质量有不利影响的非药品产品。
4.3.4 称量间、外清间,应当保持清洁,防止粉尘扩散、避免交叉污染。
防止交叉污染和外来污染制度(5篇)
防止交叉污染和外来污染制度为防止饲料生产过程中的原料、半成品及成品交叉污染和被外来物污染,影响公司产品的安全卫生,对有可能产生外来污染的各个环节进行有效控制,特制定本制度。
1、为防止不同品种饲料之间的混料或交叉污染,影响公司产品的安全卫生,将原料库设为饲料添加剂区域、大宗原料区域、药物饲料添加剂区域、矿物质原料区域,在各个区域内合理安排原料垛位,各原料品种垛位要间隔一定距离(不小于30cm)每个原料垛位要以垛位卡标识清楚。
2、生产过程中使用同一生产含药物饲料添加剂和不含药物添加剂‘无药物在先,有药物在后’,‘低浓度在先,高浓度在后’的生产顺序。
3、成品保管在入库时,根据成品料的类型将成品库划分区域,标识清楚,成品库原料库分开布局。
4、为防止饲料生产过程中的原料、半成品及成品被外来物污染,影响公司产品的安全卫生,采购原料时运输车辆不得存在沙石、铁屑、秸秆、农药、害虫、化肥、霉变物料等外来掺杂物污染原料,卸车时,控制霉变、杂质、生芽、生虫等外来掺杂物。
5、生产过程中要保持生产现场良好的清洁状态,及时清扫杂物,不得在生产过程中进行维修、焊接、气割等作业。
6、车间、仓库有防鼠、防鸟措施,及时清理杂物防止害虫滋生。
7、当发现或怀疑物料受到交叉污染或异物污染时,应立即报告车间主任、质监员,分析原因,做出处理决定,并采取有效措施防止类似事件再次发生。
防止交叉污染和外来污染制度(2)防止交叉污染和外来污染是一项重要的制度措施,旨在减少和预防环境污染和传染病传播。
这种制度包括一系列的措施和规定,以确保环境的洁净和健康。
为了更好地了解和应用这一制度,首先需要明确什么是交叉污染和外来污染。
交叉污染是指不同区域或环境之间,由于人员、物品或其他方式的接触,导致污染物传播的现象。
例如,医院中不同患者之间的病菌传播,或者食品加工过程中不同原料之间的交叉污染等。
外来污染是指由外部环境引入的污染物。
这些污染物可能是通过人员、物品或其他方式带进环境中的。
生产过程防止污染交叉污染混淆和差错的管理规程
生产过程防止污染、交叉污染、混淆和差错的管理规程目的:建立防止污染、交叉污染、混淆和差错管理规程,规定了在药品生产活动过程中防止污染、交叉污染、混淆和差错管理内容和要求适用范围:适用于药品生产活动过程中防止污染、交叉污染、混淆和差错的管理职责:生产技术部、质保部、车间对实施本规程负责内容:1.定义1.1污染:在生产、取样、包装或重新包装、贮存或运输等操作过程中,原辅料、中间产品、待包装产品、成品受到具有化学或微生物特性的杂质或异物的不利影响。
1.2 交叉污染:不同原料、辅料及产品之间发生的相互污染。
1.3混淆:在生产或包装的过程中,误将一种或一批物料当成了另一种或另一批物料进行使用、操作。
1.4 差错:在生产过程中,因为计量器具未调试到位、或计量方式不正确、或计数不准确而造成的错误2. 产生污染、交叉污染、混淆和差错的原因2.1 人员:操作人员患有传染病、皮肤病等,或未接受卫生方面的培训,未按要求穿戴工作服,行为不规范、人员带来外部污染,生产人员未按工艺规程和SOP 要求操作,工作责任心不强,工作量过大,操作中随意性大等。
2.2 设备:表面不光洁、平整,材质不稳定,不易清洁,设备选型不合理,维修、保养不及时,没有定期验证或没有保持验证状态。
生产中使用的设备、容器无状态标志,清场不彻底等造成混淆。
2.3 物料:购进的原辅料本身质量不好,或在运输、贮存、检验取样、配料过程中造成污染。
原辅料微生物指标超限。
原辅料、包装材料、半成品、中间体等无明显标志,放置混乱,散装或放在易破损的包装中,印刷性包装材料管理不善等。
2.4 文件:文件管理制度不健全,或执行不力,无复核、监控,发现问题未及时查找原因等,特别是配料、包装等重要部门管理不严格。
2.5 环境:厂房设计不合理,生产环境如空气中粒子过多,车间地面、墙壁、天花板等不平整、易脱落、长霉、消毒不严格等造成污染。
2.6 清洁:清洁效果不能保证微生物除去水平及残留限度,清洁剂残留、消毒剂效果不能保证;生产结束后不及时清洁清场等造成污染。
防止生产过程污染和交叉污染的管理规程
防止生产过程污染和交叉污染的管理规程一、目的:建立防止生产过程污染与交叉污染的管理规程最大限度地降低医用氧充装过程中污染、交叉污染的风险。
二、适用范围:适用于防止生产区、化验区与仓贮区在生产过程污染与交叉污染的管理三、职责:生产区、化验区与仓贮区人员负责实施,QA检查员及各部门负责人负责监督执行四、内容:1医用氧车间布局工艺及设备人员卫士管理1.1由质量管理部负责车间布局工艺流程图的制定,防止布局不合理造成污染、并负责检查监督.1.2生产部负责对员工安全卫士知识与安全生产操作管理,并对生产设备保护清洗消毒管理防止交叉污染。
2 化验室仓库管理 (门卫对医用氧运输车辆人员 ,卫士消毒管理负责)2.1化验员对原液氧进行取样检查,对充装中氧气检查充装后复查杜绝不合格产品2.2仓库保管员负责医用气瓶产品清洁消毒安全存放及出库管理负责程序:1 目的:搞好生产过程中的卫生管理,防止因交叉污染而造成产品质量问题。
2 范围:适用于医用氧生产全过程。
3 职责:3.1质量管理部负责车间的布局工艺流程图的制定。
3.2生产部负责对员工进行规范操作及卫生培训,负责生产过程中的卫生操纵,负责对生产设备进行常规保护与清洗消毒与维修改造。
3.3 质量操纵部负责生产过程中交叉污染的监督检查。
4 工作程序4.1 防止车间布局不合理造成的污染4.1.1 操纵要求a)保证车间建筑设施的完好。
b)根据医用氧生产工艺流程要求进行合理布局,气瓶充装区域应有明显标识、空瓶与不一致阶段产品的气瓶应清晰标识并分开放置,生产区与储存区应有与生产规模相习惯的面积与空间,并有通风照明防火防爆防静电等设施c)医用氧充装间应保持整洁,并设置专用更衣室,充装间应与维修间分开d)每班开工前/生产务必对管道置换,检查确保检验合格的自备医用气瓶已清洁消毒并抽真空或者置换、储存过程中随时监视杜绝交叉污染。
b)班组日常监控,化验室不定期抽查。
4.1.2. 纠正措施检查中发现问题,由抽查员跟踪解决。
交叉污染车间管理制度
一、总则为了确保交叉污染车间(以下简称“车间”)的生产安全和产品质量,预防交叉污染的发生,保障员工健康,特制定本制度。
二、适用范围本制度适用于公司所有交叉污染车间的生产、管理及监督工作。
三、交叉污染的定义交叉污染是指在生产过程中,由于各种原因导致的污染物质从一种产品或生产环境转移到另一种产品或生产环境的现象。
四、管理职责1. 车间主任负责本车间的交叉污染预防管理工作,确保本制度的有效实施。
2. 生产部负责对交叉污染车间的生产过程进行监督,确保生产安全。
3. 质量部负责对交叉污染车间的产品质量进行检测,确保产品质量符合国家标准。
4. 安全环保部负责对交叉污染车间的环保设施进行管理,确保环保设施正常运行。
5. 设备部负责对交叉污染车间的生产设备进行维护,确保设备正常运行。
五、预防措施1. 设备与设施(1)车间内所有设备、工具、容器等均应具备防污染功能,如采用防静电、防腐蚀、防泄漏等设计。
(2)车间内应设置独立的空气净化系统、消毒设施、废弃物处理设施等。
2. 生产过程(1)严格按照生产工艺流程进行操作,避免交叉污染。
(2)生产过程中,应使用专用的工具、容器,并保持清洁、卫生。
(3)生产过程中,操作人员应穿戴符合要求的防护用品,如手套、口罩、防护服等。
3. 物料管理(1)物料入库、出库、使用过程中,应严格执行物料管理制度,确保物料质量。
(2)物料存放区域应分区管理,防止不同物料之间的交叉污染。
4. 人员管理(1)操作人员应定期接受交叉污染预防培训,提高防范意识。
(2)操作人员应遵守操作规程,不得擅自更改生产过程。
六、交叉污染事故处理1. 事故报告(1)发生交叉污染事故后,当事人应立即停止生产,并向车间主任、生产部、质量部报告。
(2)车间主任应在接到报告后,立即组织人员进行事故调查,查明事故原因。
2. 事故处理(1)针对事故原因,采取相应的整改措施,防止类似事故再次发生。
(2)对事故责任人员进行追责,并根据情节轻重给予相应的处罚。
- 1、下载文档前请自行甄别文档内容的完整性,平台不提供额外的编辑、内容补充、找答案等附加服务。
- 2、"仅部分预览"的文档,不可在线预览部分如存在完整性等问题,可反馈申请退款(可完整预览的文档不适用该条件!)。
- 3、如文档侵犯您的权益,请联系客服反馈,我们会尽快为您处理(人工客服工作时间:9:00-18:30)。
生产过程中防止污染和交叉污染管理规程1.目的:建立防止污染和交叉污染措施的管理规程,最大限度地降低生产过程中的污染和交叉污染,避免混淆和差错。
2.范围:适用于公司生产过程中防止污染和交叉污染的管理。
3.职责:车间管理人员对规程的实施负责,QA监督规程的实施。
4.规程:4.1 定义4.1.1 污染:在生产、取样、包装或重新包装、贮存或运输等操作过程中,原辅料、中间产品、待包装产品、成品受到具有化学或微生物特性的杂质或异物的不利影响。
4.1.2 交叉污染:不同原料、辅料及产品之间发生的相互污染。
4.2 生产过程中应当尽可能采取措施,防止污染和交叉污染4.2.1 在分割的区域内生产不同品种的药品;4.2.2 采用阶段性生产方式;4.2.3 设置必要的气锁间和排风;空气洁净级别不同的区域应当有压差控制;4.2.4 应当降低未经处理或未经充分处理的空气再次进入生产区导致污染的风险;4.2.5 在产生交叉污染的生产区内,操作人员应当穿戴该区域专用的防护服;4.2.6 采用经过验证或已知有效的清洁和去污染的操作规程进行设备清洁;必要时,应当对与物料直接接触的设备表面的残留物进行检测;4.2.7 采用密闭系统生产;4.2.8 干燥设备的进风应当有空气过滤器,排风应当有防止空气倒流装置;4.2.9 生产和清洁过程中应当避免使用易碎、易脱屑、易发霉器具;应当有防止筛网断裂而造成污染的措施;4.2.10 液体制剂的配制、过滤、灌封、灭菌等工序应当在规定的时间内完成。
4.3 厂房、设施、设备防止污染和交叉污染的措施:4.3.1 空调净化系统采用的措施:4.3.1.1 初效、中效过滤器的阻力达到设定值(设定值为初始阻力的1.5倍)报警:阻力小于设定值,绿灯亮;阻力大于设定值时,红灯亮,需对过滤器进行清洗或更换。
4.3.1.2 空调净化系统有缺风报警功能。
4.3.1.3 空调净化系统有机组故障及停机报警功能。
4.3.1.4 A/B级洁净区空调净化系统能显示分装间的温湿度、分装间对洗瓶间的压差。
4.3.1.5 B级洁净区、C级洁净区及D级洁净区现场有空调系统停机报警装置。
4.3.1.6 A/B级洁净区及C级洁净区所有单向流风机有停机报警装置。
4.3.1.7 绿灯亮时空调净化系统或单向流风机运行正常,红灯亮时风机故障,操作工应停止生产,立即向车间主任或工程设备部反映,按《注射剂车间生产紧急情况处理管理规程》(SMP-PM-0xx)执行。
4.3.1.8 悬浮粒子在线检测报警:A/B级洁净区分装及轧盖隔离器内装有悬浮粒子在线检测,监控系统在空调机房值班室,有声光报警功能,如报警,空调机房值班人员应立即通知报警岗位工序负责人或QA,并查明原因,采取相应措施。
4.3.2 工艺用水系统采用的措施:4.3.2.1 纯化水系统在线检测:当一级反渗透产水电导率>10μs/cm(25℃)时,自动排放;当二级反渗透产水电导率>2μs/cm(25℃)时,回到中间水箱;循环系统回水电导率>2μs/cm(25℃)时,报警红灯亮。
4.3.2.2 注射用水系统在线检测:当多效蒸馏水机产水电导率>1μs/cm或温度<90℃时报警;循环系统回水电导率>2.5μs/cm时报警,回水温度<72℃时,自动排放。
4.3.2.3 当纯化水及注射用水循环水(现场检查或者是在线监控)不合格时,制水岗位操作工应通知车间停止使用,把水排净,并按《偏差管理规程》(SMP-QA-0xx)查明原因。
4.3.3 厂房措施:4.3.3.1 厂房有防止昆虫动物进入及捕蚊、虫的设施,严格执行各仓库的管理标准,仓库、车间做好防虫、防鼠工作。
避免所使用的灭鼠药、杀虫剂、烟熏剂等对设备、物料、产品造成污染。
4.3.3.2 头孢固体车间使用专用设施(如独立的空气净化系统)和设备,并与其他药品生产区严格分开;4.3.3.3 头孢固体车间排至室外的废气经过净化处理并符合要求,排风口远离其他空气净化系统的进风口;4.3.4 注射剂车间设施设备措施:4.3.4.1 人流系统安装了门禁或互锁装置:系防止气流倒灌、混流的措施,报警时门外人不得推门进入或互锁,一扇门打开时,另一扇门则打不开,以防止两扇门同时打开;传递窗门有互锁功能,两扇门不能同时打开。
4.3.4.2 隧道烘箱报警:当隧道烘箱压差不在设定范围内或高温段温度低于设定值8℃时声光报警,确保瓶子能充分灭菌。
4.3.4.3 胶塞清洗机和铝盖清洗机排水阀在打开时都有信号反馈控制,如排水阀不能及时关闭,将报警并停机,不能进入下一个程序;脉动真空灭菌器、干热灭菌柜、胶塞清洗机及铝盖清洗机前后门有互锁功能,胶塞清洗机和铝盖清洗机的排水阀异常时,在PLC操作屏上显示异常,提示操作工及时检查并解决,防止下水倒灌造成污染。
4.3.4.4 分装和轧盖都是隔离器封闭生产,分装间、轧盖间有局部排风,轧盖机轧盖头处有吸尘装置,防止粉尘扩散,并有防止空气倒流的截止阀。
4.3.5 固体制剂车间设施、设备措施:4.3.5.1 人流及物流缓冲间的门有互锁装置一扇门打开时,另一扇门则打不开,以防止两扇门同时打开;传递窗门有互锁功能,两扇门不能同时打开。
4.3.5.2 产尘的工序(粉碎、称量、制粒、混合、压片、包衣及胶囊充填)都有捕尘设施及操作间相对走廊为负压,以防止污染和交叉污染。
4.3.5.3粉碎、制粒、干燥、混合、压片、包衣及胶囊充填等采用密闭系统生产。
4.3.5.4 干燥机、包衣机、料斗清洗站及烘箱进风有高效空气过滤器;粉碎机、流化床干燥机、包衣机、料斗清洗站等设备排风、除尘机排风及产尘房间排风都有防止空气倒流的截止阀。
4.4 防止人员污染和交叉污染:4.4.1 所有人员都应当接受卫生要求的培训,人员操作严格执行《人员进出洁净区净化管理规程》(SMP-PM-0XX),最大限度地降低人员对药品生产造成污染的风险。
4.4.2 各级管理人员严格监控防止体表有伤口、患有传染病或其他可能污染药品疾病的人员从事直接接触药品的生产。
可能患有污染药品疾病及身体不适的人员必须积极主动地配合主管部门的管理要求。
4.4.3 控制进入洁净区的人和物的数量。
4.4.4 进入洁净区的人和物严格执行《人员进出洁净区净化管理规程》(SMP-PM-0XX)和《物料、工器具进出洁净区管理规程》(SMP-PM-0XX)。
4.4.5 进入洁净区的操作人员不得随意离开自己的工作区域而进入其它操作间,确需进入时,应再次执行《人员进出洁净区净化管理规程》(SMP-PM-0XX)后方可进入。
4.4.6 进入A/B级洁净区的人员应经更衣确认合格后方可进入;所有授权在生产时进入A/B 级洁净区的人员,包括QA和维修人员,每年至少应参加一次成功的培养基模拟灌装试验。
4.5 物料防止污染与交叉污染的措施:4.5.1 药品生产厂房不得用于生产对药品质量有不利影响的非药用产品。
4.5.2 建立物料和产品的操作规程,确保物料和产品的正确接收、贮存、发放、使用和发运,防止污染、交叉污染、混淆和差错。
4.5.3 物料管理关键环节严格执行物料平衡检查标准,进行严格的收率控制和质量记录,使之在合理的范围内并便于质量追溯。
4.5.4 生产区和贮存区存放设备、物料、中间产品、待包装产品和成品做到“有序存放”,避免不同产品或物料的混淆、交叉污染,预防风险避免生产或质量控制操作发生遗漏或差错。
生产区与贮存区的空间、放置地点需要根据生产实际需要进行计算和预留,原材料:必须的接收和暂存间以及物料运输/存放空间;生产:部件、物料、中间体、半成品、待包装品和包装定置管理;成品的暂存间和物料运输、存放空间;原料、半成品和成品的废弃物料。
4.6 生产管理措施:4.6.1 生产所用的设备、器械、容器具尤其与药品接触的部分必须使用不锈钢材质。
每台设备中有与药品接触风险的部件,其维修保养使用的润滑油应为食用级或药用级,设备的传动部件要密封良好,结构上要防止运转时润滑油、冷却剂等对物料的污染。
4.6.2 生产设备清洁操作规程应当规定具体而完整的清洁方法、清洁用设备或工具、清洁剂的名称和配制方法、去除前一批次标识的方法、保护已清洁设备在使用前免受污染的方法、已清洁设备最长的保存时限、使用前检查设备清洁状况的方法,使操作者能以可重现的、有效的方式对各类设备进行清洁。
4.6.3 清洁方法应当经过验证,证实其清洁的效果,以有效防止污染和交叉污染。
清洁验证应当综合考虑设备使用情况、所使用的清洁剂和消毒剂、取样方法和位置以及相应的取样回收率、残留物的性质和限度、残留物检验方法的灵敏度等因素。
4.6.4 生产时限的规定:工艺规程规定了最长生产时间,物料规定了清洗后的存放时间及灭菌后有效期,避免了超效期带来的污染;生产用设备、容具及工作服等规定使用后的最长存放清洗时间以及清洗后的存放时间,并规定干燥存放。
灭菌后容器具及工作服规定了灭菌后有效期,避免了设备、容器具及工作服等超效期带来的污染。
4.6.5 注射剂车间所有与药品接触的分装机部件、容器、器具及工作服采用1%氢氧化钠浸泡去除活性物质,清洁验证效果表明能有效去除活性残留物质,避免了交叉污染。
4.6.6 除中转容器外,不允许为了工作方便将设备搬到其它房间操作,特殊原因需搬动时,需QA同意并报生产副总批准方可执行。
4.6.7 使用蒸汽夹层加热的设备生产时,随时检查是否有蒸汽泄漏,一旦发生,立即停止生产并上报,等待处理措施的批准。
4.6.8 周转箱、设备不能有裂缝,否则应及时维修或者淘汰。
4.6.9 严格清场管理:清场是防止污染和交叉污染最有效的措施,各岗位生产结束必须清场彻底,必须收到QA签发清场合格证方可离开下班。
4.7 质量管理措施:4.7.1 正常生产时,质量管理部QA对各工序巡回检查,及时发现潜在的问题,纠正发生的微小偏差。
4.7.2 工艺用水系统微生物的监测:微生物检测连续3次超过警戒限或1次超过纠偏限,停止生产,并采取有效措施,启动《偏差管理规程》查明原因,制定纠正、预防措施;对所涉及产品的质量进行风险评估。
4.7.3 生产环境及表面微生物的监测:微生物检测连续3次超过警戒限或1次超过纠偏限,停止生产,并采取有效措施,启动《偏差管理规程》查明原因,制定纠正、预防措施。
4.7.4 A/B级洁净区人员日常监控:生产过程中对A/B级洁净区的人员进行表面微生物监测,如1个月内有1次超过警戒限,应向本人提出警告;如1个月内有3次超过警戒限或1次超过纠偏限或有3个月没有进入A/B级洁净区,应当接受再培训、再考核或调离A/B级洁净区,并评估是否进行一次模拟灌装试验。
4.7.5 每年由质量管理部对空气净化系统、工艺用水系统及生产环境进行趋势分析,及时发现不良趋势并采取有效措施进行整改与预防。