复合材料结构力学认识
复合材料结构力学

复合材料结构力学
复合材料结构力学是指在复合材料结构中,力学特性与工程设计的关系。
复合材料结构力学的主要任务是分析和设计具有优良性能的复合材料结构,使结构具有较高的强度、刚度和耐久性。
复合材料结构力学所涉及的主要内容包括复合材料的应力分析、弹性、蠕变和疲劳特性分析、裂纹扩展和断裂特性分析等。
这些分析都是用来评估复合材料结构的力学性能,以确定最佳的材料组合和结构设计。
因为复合材料的性质和结构相对比较复杂,所以在复合材料结构力学的分析中,需要运用材料力学、结构力学、断裂力学、热力学等相关学科的知识。
同时,因为复合材料结构的制造过程也是非常重要的,因此需要运用相关的制造技术来考虑制造工艺对复合材料结构力学性能的影响。
总之,复合材料结构力学在设计和制造高强度、高性能的复合材料结构中起着至关重要的作用,同时也是未来材料研究的重要发展方向之一。
复合材料力学和复合材料结构力学
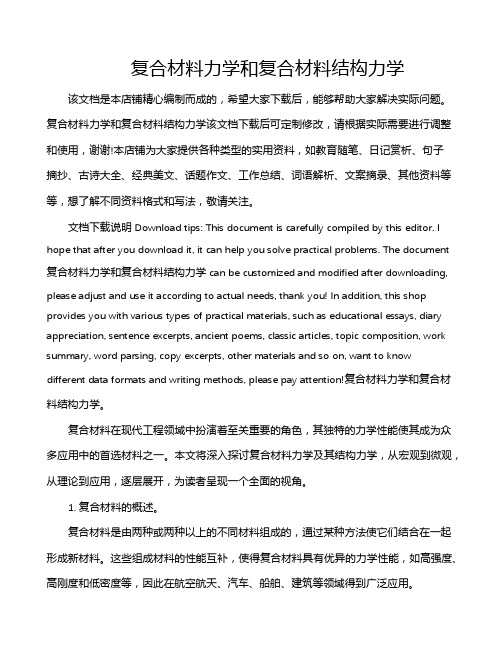
复合材料力学和复合材料结构力学该文档是本店铺精心编制而成的,希望大家下载后,能够帮助大家解决实际问题。
复合材料力学和复合材料结构力学该文档下载后可定制修改,请根据实际需要进行调整和使用,谢谢!本店铺为大家提供各种类型的实用资料,如教育随笔、日记赏析、句子摘抄、古诗大全、经典美文、话题作文、工作总结、词语解析、文案摘录、其他资料等等,想了解不同资料格式和写法,敬请关注。
文档下载说明Download tips: This document is carefully compiled by this editor. I hope that after you download it, it can help you solve practical problems. The document 复合材料力学和复合材料结构力学can be customized and modified after downloading, please adjust and use it according to actual needs, thank you! In addition, this shop provides you with various types of practical materials, such as educational essays, diary appreciation, sentence excerpts, ancient poems, classic articles, topic composition, work summary, word parsing, copy excerpts, other materials and so on, want to knowdifferent data formats and writing methods, please pay attention!复合材料力学和复合材料结构力学。
复合材料结构力学分析

复合材料结构力学分析随着科技不断发展和进步,人们将越来越多的材料运用到各种领域中去,例如建筑、交通、海洋等,而复合材料作为一种性能优异的材料,其应用也越来越广泛。
然而,复合材料结构力学分析也成为了解决其应用问题的重要方法之一。
一、复合材料结构力学分析的概念复合材料是由两个或两个以上不同成分的材料组成,其重要特点是由各成分的各自优点组合成材料的无与伦比的性能。
而结构力学分析是指,对于复杂结构体,在了解其静力学性能的基础上,确定各部件的应变状态,并依据力学原理或有关理论计算得到结构体的内应力分布和变形情况的工程分析方法。
因此,复合材料结构力学分析是如何对复合材料的组成和结构进行研究,了解其力学性能,并根据其力学原理和相关理论进行力学计算。
这种方法对于指导材料的选取和结构的设计具有重要意义。
二、复合材料结构力学分析的步骤复合材料结构力学分析的过程较为复杂,需要经过以下几个步骤:1.基础分析:包括材料的力学性能参数,如弹性模量,剪切模量,泊松比等;以及材料组成和微观结构的分析,是整个分析的基础。
2.力学分析:在基础分析的基础上,进行应力和应变的计算,了解材料承受载荷的情况。
3.结构分析:根据结构的几何形态,进行杆件等的应力分析,确定各部位的应力分布规律。
4.材料疲劳分析:了解材料在循环载荷下的疲劳性能,以预测材料的寿命。
5.工程设计:依据分析的结果,对材料的选择和设计进行综合分析,确定合理的结构和制造参数。
三、复合材料结构力学分析存在的问题及解决方案虽然复合材料具有优异的力学性能和广泛的应用前景,但是在结构力学分析中也存在一些问题,这些问题包括:1.材料性能不均匀:由于复杂结构体中材料的组成和微观结构的不同,会导致材料的力学性能存在一定的差异,给计算带来了一定的难度。
2.结构复杂性:复杂结构体的几何形态存在变化,例如曲率半径的变化,杆件的斜角和弯曲等。
这些变化使得分析过程变得复杂。
3.工艺难度和成本高:制造复合材料结构需要经过复杂的工艺过程,这些过程存在成本高和时间长等问题。
复合材料结构力学认识

复合材料结构力学认识复合材料是由两种或以上不同的物质通过其中一种适当的方式结合而成的材料,具有多种性能的综合优势。
复合材料的结构力学是研究复合材料在外力作用下的变形和破坏行为,了解复合材料的力学性能和设计合理的复合材料结构具有重要意义。
本文将从复合材料的基本组成、力学行为以及设计原则等方面对复合材料结构力学进行认识。
一、复合材料的基本组成和结构形式复合材料由基体和增强相组成。
基体是复合材料的主体,其功能是使增强相能够均匀地分布在整个材料中。
基体可以是金属、聚合物、陶瓷等,具有一定的韧性和抗冲击性能。
增强相是提高复合材料力学性能的关键,可以是纤维、颗粒、片层等形式。
增强相可以是碳纤维、玻璃纤维、陶瓷颗粒等,具有较高的强度和刚度。
复合材料的结构形式可以分为两类:层合结构和型材结构。
层合结构是由多层基本相同的薄板材料通过粘接在一起形成的,常见的有层合板材、层合筋板等。
型材结构是将复合材料加工成特定形状的截面,常见的有管材、型钢等。
二、复合材料的力学行为复合材料的力学行为取决于基体和增强相之间的相互作用以及组成和结构的特点。
基体和增强相的力学性质不同,其中增强相的强度和刚度较高,而基体的韧性较好。
在受力情况下,基体和增强相之间会产生应力传递和应力转移现象。
复合材料的力学行为主要包括弹性行为、塑性行为、断裂行为等。
复合材料的弹性模量和强度通常低于增强相,而韧性则由基体决定。
复合材料具有方向性,力学性能随着不同方向的变化而变化。
通过正交叠层层合结构可以提高复合材料的韧性和抗疲劳性能。
三、复合材料结构设计原则在层合结构中,为了保证应力的平衡,通常采用对称结构和等厚度的层面分布。
增加层数可以提高复合材料的强度,但也会增加材料的重量和成本。
通过选择合适的增强相定向和布局,可以最大限度地发挥材料的力学性能。
在应用中,还需要考虑到复合材料的热膨胀系数和湿热性能等因素。
由于复合材料的热膨胀系数通常较低,与金属的匹配性较差,容易产生应力集中和失效。
材料力学结构设计知识点总结

材料力学结构设计知识点总结在材料力学结构设计领域,掌握一系列的知识点是非常重要的。
这些知识点可以帮助工程师们更好地理解材料的力学性质,并设计出更加稳定和高效的结构。
本文将对一些关键的材料力学结构设计知识点进行总结。
1. 材料的力学性质1.1 弹性模量:弹性模量是衡量材料抵抗外力变形的能力的物理量。
它描述了材料在受到外力作用后的应力和应变关系。
常见的弹性模量包括杨氏模量、剪切模量和泊松比等。
1.2 抗拉强度:抗拉强度是材料能够承受的最大拉伸力。
它是衡量材料抵抗拉伸变形能力的重要指标。
1.3 延伸率:延伸率是材料在受到拉伸力作用下能延展的程度。
它表示材料能够在拉伸过程中产生的应变。
1.4 硬度:硬度是材料抵抗局部压力的能力。
常用的硬度测试方法包括洛氏硬度和布氏硬度等。
2. 材料的疲劳性能2.1 疲劳强度:疲劳强度是指材料在长期受到交变载荷作用下能够承受的最大应力。
它是衡量材料抵抗疲劳破坏的能力的重要指标。
2.2 疲劳寿命:疲劳寿命是指材料在一定载荷作用下能够承受的循环次数。
了解材料的疲劳寿命可以帮助工程师预测结构的使用寿命。
2.3 疲劳裂纹扩展:疲劳裂纹扩展是指在疲劳载荷作用下,由于应力集中或者材料缺陷导致的裂纹逐渐扩展。
对疲劳裂纹扩展进行研究可以提高结构的疲劳寿命。
3. 结构设计方法3.1 单材料结构设计:单材料结构设计是指使用一种材料进行结构设计。
在设计过程中,需要综合考虑材料的力学性能、制造工艺和成本等因素。
3.2 复合材料结构设计:复合材料结构设计是指使用多种材料进行结构设计。
复合材料具有高强度、高刚度和轻质等优良性能,在设计过程中需要考虑不同材料的相互作用和界面效应。
3.3 结构优化设计:结构优化设计是指通过调整结构参数,使得结构在给定约束条件下具有最佳的性能。
常用的优化方法包括参数优化和拓扑优化等。
4. 结构力学分析4.1 静力学分析:静力学分析是研究结构在静力平衡下的力学行为。
通过计算结构的受力情况和应力分布,可以评估结构的强度和稳定性。
复合材料力学矫桂琼知识点总结
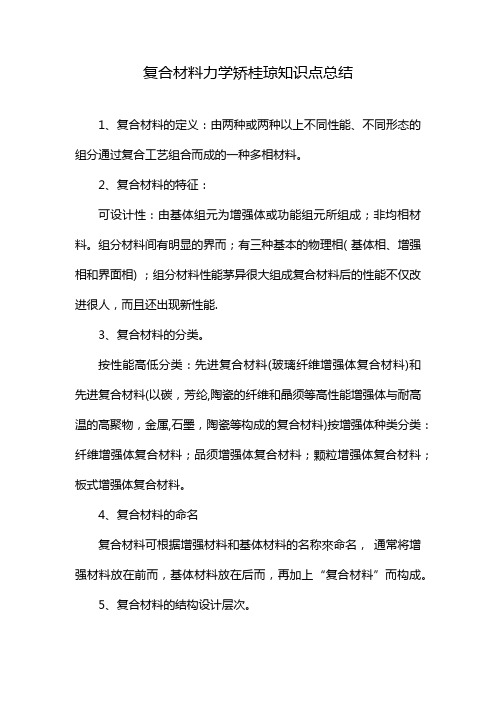
复合材料力学矫桂琼知识点总结
1、复合材料的定义:由两种或两种以上不同性能、不同形态的组分通过复合工艺组合而成的一种多相材料。
2、复合材料的特征:
可设计性:由基体组元为增强体或功能组元所组成;非均相材料。
组分材料间有明显的界而;有三种基本的物理相( 基体相、增强相和界面相) ;组分材料性能茅异很大组成复合材料后的性能不仅改进很人,而且还出现新性能.
3、复合材料的分类。
按性能高低分类:先进复合材料(玻璃纤维增强体复合材料)和先进复合材料(以碳,芳纶,陶瓷的纤维和晶须等高性能增强体与耐高温的高聚物,金属,石墨,陶瓷等构成的复合材料)按增强体种类分类:纤维增强体复合材料;品须增强体复合材料;颗粒增强体复合材料;板式增强体复合材料。
4、复合材料的命名
复合材料可根据增强材料和基体材料的名称來命名,通常将增强材料放在前而,基体材料放在后而,再加上“复合材料”而构成。
5、复合材料的结构设计层次。
次结构:单层设计... 微观力学方法二次结构:层合体设计.宏观力学方法三次结构产品结构设计结构力学方法单层材料的性能取决于增强相、基体相和结合界而的力学性能,增强相的含量、分布方向等。
设计内容包括正确选择原料的种类和配比。
层合体的性能:取决于单层材料的力学性能和铺层方法(厚度、纤维交叉方式、顺序等)。
设计内容包括:对铺层方案作出合理的安排。
产品结构性能:取决于层合体的力学性能、结构几何组合与连接方式设计内容:最终确定产品结构的形状、尺寸、连接方法等。
复合材料结构的力学性能测试与分析

复合材料结构的力学性能测试与分析引言复合材料是由不同材料组合而成的一种新型材料,具有很多优异的机械性能,因此在航空、航天、汽车等领域得到广泛应用。
然而,复合材料的力学性能与其结构密切相关,因此对其进行力学性能测试与分析是十分关键的。
一、复合材料结构的力学性能测试方法1. 拉伸试验拉伸试验是评估复合材料材料强度和刚度的常用方法之一。
通过在拉伸机上施加一定的拉力,测量拉伸试样的应变和应力来分析材料的拉伸性能。
该方法能够得到材料的拉伸强度、弹性模量、屈服强度等参数。
2. 压缩试验压缩试验用于评估复合材料在受压状态下的抗压性能。
在压力机上施加一定的压力,测量压缩试样的应变和应力来分析材料的抗压性能。
该方法能够得到材料的压缩强度、弹性模量、破坏形态等参数。
3. 剪切试验剪切试验用于评估复合材料在受剪切状态下的抗剪性能。
通过施加剪切力,测量试样剪切区域的切应变和切应力来分析材料的抗剪切性能。
该方法能够得到材料的剪切强度、剪切模量等参数。
4. 冲击试验冲击试验用于评估复合材料在受冲击载荷下的性能表现。
通过施加冲击载荷,测量试样的冲击吸收能力和冲击强度来分析材料的抗冲击性能。
该方法能够得到材料的冲击韧性、断裂能量等参数。
二、复合材料结构力学性能分析1. 有限元分析有限元分析是一种常用的力学性能分析方法,通过将结构离散化为有限个单元,在每个单元内建立方程组,最终求解整个结构的力学行为。
通过有限元分析,可以得到复合材料结构在不同载荷条件下的应力和应变分布,并可以进行累积疲劳分析、刚度分析等。
2. 弹性力学分析弹性力学分析可以用来研究复合材料的静力响应。
通过应变-应力关系和材料的力学参数,可以计算出复合材料在受力作用下的应变和应力分布。
弹性力学分析可用于优化设计和评估复合材料结构的强度。
3. 疲劳寿命评估复合材料结构在长期受到变化载荷作用下会发生疲劳破坏。
通过进行疲劳寿命评估,可以预测结构在特定载荷下的寿命。
疲劳寿命评估可以使用实验方法和数值模拟方法,如基于有限元分析的疲劳分析。
纤维增强复合材料的力学性能分析
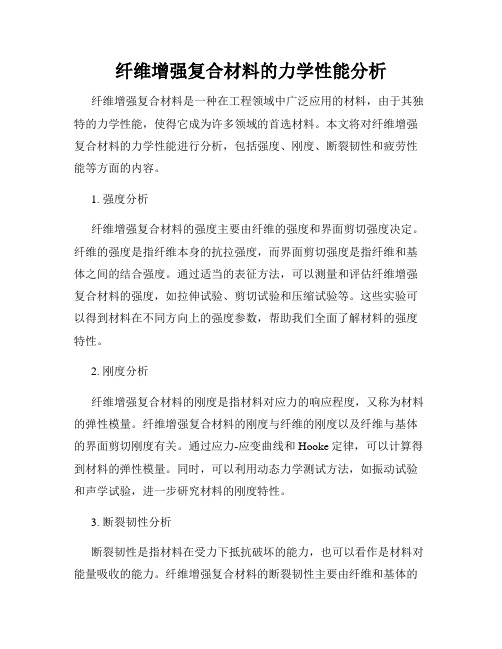
纤维增强复合材料的力学性能分析纤维增强复合材料是一种在工程领域中广泛应用的材料,由于其独特的力学性能,使得它成为许多领域的首选材料。
本文将对纤维增强复合材料的力学性能进行分析,包括强度、刚度、断裂韧性和疲劳性能等方面的内容。
1. 强度分析纤维增强复合材料的强度主要由纤维的强度和界面剪切强度决定。
纤维的强度是指纤维本身的抗拉强度,而界面剪切强度是指纤维和基体之间的结合强度。
通过适当的表征方法,可以测量和评估纤维增强复合材料的强度,如拉伸试验、剪切试验和压缩试验等。
这些实验可以得到材料在不同方向上的强度参数,帮助我们全面了解材料的强度特性。
2. 刚度分析纤维增强复合材料的刚度是指材料对应力的响应程度,又称为材料的弹性模量。
纤维增强复合材料的刚度与纤维的刚度以及纤维与基体的界面剪切刚度有关。
通过应力-应变曲线和Hooke定律,可以计算得到材料的弹性模量。
同时,可以利用动态力学测试方法,如振动试验和声学试验,进一步研究材料的刚度特性。
3. 断裂韧性分析断裂韧性是指材料在受力下抵抗破坏的能力,也可以看作是材料对能量吸收的能力。
纤维增强复合材料的断裂韧性主要由纤维和基体的界面特性以及纤维与基体的剥离、拉伸和剪切等行为决定。
通过断裂力学试验,如缺口拉伸试验和冲击试验,可以评估材料的断裂韧性。
4. 疲劳性能分析疲劳性能是指纤维增强复合材料在交变载荷下长时间使用的能力。
疲劳性能的分析可以通过应力-寿命曲线和疲劳寿命评估得到。
材料的纤维类型、纤维体积分数、界面质量、载荷幅值和频率等因素都会影响材料的疲劳性能。
为了提高纤维增强复合材料的疲劳寿命,可以采用增加纤维含量、改善界面质量、降低应力集中等方法。
综上所述,纤维增强复合材料的力学性能对其使用所处环境和预期寿命有着重要影响。
通过详细的力学性能分析,我们可以更好地了解材料的特性,并针对性地进行设计和工程应用。
纤维增强复合材料的力学性能分析是科学设计和工程应用的重要基础,也为材料学和结构力学领域的研究提供了有价值的参考。
- 1、下载文档前请自行甄别文档内容的完整性,平台不提供额外的编辑、内容补充、找答案等附加服务。
- 2、"仅部分预览"的文档,不可在线预览部分如存在完整性等问题,可反馈申请退款(可完整预览的文档不适用该条件!)。
- 3、如文档侵犯您的权益,请联系客服反馈,我们会尽快为您处理(人工客服工作时间:9:00-18:30)。
暨南大学研究生课程论文题目:复合材料结构力学认识学院:理工学院学系:土木工程专业:建筑与土木工程课程名称:复合材料结构力学学生姓名:陈广强学号:1339297001电子邮箱:chengq09@指导教师:王璠复合材料结构力学认识主题词:复合材料力学;复合材料结构力学;力学特性;力学基础复合材料结构力学研究复合材料的杆、板、壳及基组合结构的应力分析、变形、稳定和振动等各种力学问题,,在广议上属于复合材料力学的一个分支。
由于其内容丰富,问题重要和研究对象不同,已成为和研究复合材料力学问题的狭义复合材料力学并列的学科分支。
一、复合材料结构力学研究内容和办法目前复合材料结构力学以纤维增强复合材料层压结构为研究对象,主要研究内容包括:层合板和层合壳结构的弯曲,屈曲与振动问题,以及耐久性、损伤容限、气功弹性剪裁、安全系数与许用值、验证试验和计算方法等专题。
研究中采用宏观力学模型,可以分辩出层和层组的应力。
这些应力的平均值为层合板应力。
研究方法以各向异性弹性力学方法为主,同时采用有限元素法、有限差分法、能量变分法等方法。
对耐久性、损伤容限等较新的课题则采用以试验为主的研究方法。
二、复合材料结构的力学特性1、复合材料的比强度和比刚度较高材料的强度除以密度称为比强度;材料的刚度除以密度称为比刚度。
这两个参量是衡量材料承载能力的重要指标。
比强度和比刚度较高说明材料重量轻,而强度和刚度大。
这是结构设计,特别是航空、航天结构设计对材料的重要要求。
现代飞机、导弹和卫星、复合电缆支架、复合电缆夹具等机体结构正逐渐扩大使用纤维增强复合材料的比例。
复合材料的力学性能可以设计,即可以通过选择合适的原材料和合理的铺层形式,使复合材料构件或复合材料结构满足使用要求。
例如,在某种铺层形式下,材料在一方向受拉而伸长时,在垂直于受拉的方向上材料也伸长,这与常用材料的性能完全不同。
又如利用复合材料的耦合效应,在平板模上铺层制作层板,加温固化后,板就自动成为所需要的曲板或壳体。
2、复合材料的抗疲劳性能良好一般金属的疲劳强度为抗拉强度的40~50%,而某些复合材料可高达70~80%。
复合材料的疲劳断裂是从基体开始,逐渐扩展到纤维和基体的界面上,没有突发性的变化。
因此,复合材料在破坏前有预兆,可以检查和补救。
纤维复合材料还具有较好的抗声振疲劳性能。
用复合材料制成的直升飞机旋翼,其疲劳寿命比用金属的长数倍。
3、复合材料的减振性能良好纤维复合材料的纤维和基体界面的阻尼较大,因此具有较好的减振性能。
用同形状和同大小的两种梁分别作振动试验,碳纤维复合材料梁的振动衰减时间比轻金属梁要短得多。
4、复合材料通常都能耐高温在高温下,用碳或硼纤维增强的金属其强度和刚度都比原金属的强度和刚度高很多。
普通铝合金在400℃时,弹性模量大幅度下降,强度也下降;而在同一温度下,用碳纤维或硼纤维增强的铝合金的强度和弹性模量基本不变。
复合材料的热导率一般都小,因而它的瞬时耐超高温性能比较好。
5、复合材料的安全性好在纤维增强复合材料的基体中有成千上万根独立的纤维。
当用这种材料制成的构件超载,并有少量纤维断裂时,载荷会迅速重新分配并传递到未破坏的纤维上,因此整个构件不至于在短时间内丧失承载能力。
6、复合材料的成型工艺简单纤维增强复合材料一般适合于整体成型,因而减少了零部件的数目,从而可减少设计计算工作量并有利于提高计算的准确性。
另外,制作纤维增强复合材料部件的步骤是把纤维和基体粘结在一起,先用模具成型,而后加温固化,在制作过程中基体由流体变为固体,不易在材料中造成微小裂纹,而且固化后残余应力很小。
三、复合材料结构的力学的基础1、复合材料的结构力学设计基础一种新复合材料制品的开发设计,遵守的程序是首先是复合材料制品的造型(构造)设计,其次是复合材料的物化性能设计和复合材料制品的结构设计,接下来是复合材料制品的成型工艺设计,最后是复合材料制品的质量检验。
1.1复合材料结构设计过程复合材料结构设计是选用不同材料综合各种设计(如层合板设计、典型结构件设计、连接设计等)的反复过程。
在综合过程中必须考虑的因素:结构质量、研制成本、制造工艺、结构鉴定、质量控制、工装模具的通用性及设计经验。
(1) 明确设计条件。
如性能要求、载荷要求、环境条件、形状限制等;(2) 材料设计。
包括原材料选择、铺层性能的确定、复合材料层合板的设计等。
(3) 结构设计。
包括复合材料典型结构件(如杆、梁、板、壳等) 和复合材料结构(如刚架、硬壳式结构等)的设计。
原材料的选择与复合材料的性能关系甚大,因此,正确选择合适的原材料就能得到需要的复合材料的性能。
原材料选择必须遵循一些原则,(1) 比强度、比刚度高的原则;(2) 材料与结构的使用环境相适应的原则,要求材料的主要性能在结构整个使用环境条件下下降幅度应不大于10%。
(3) 满足结构特殊性要求的原则;(4) 满足工艺性要求的原则;(5) 成本低、效益高的原则。
纤维选择,根据结构的功能选取能满足一定的力学、物理和化学性能的纤维。
首先要确定纤维的类别,其次要确定纤维的品种规格。
(1) 若结构要求有很好的透波、吸波性能,则可选E或S玻璃纤维、氧化铝纤维等。
(2) 若结构要求有很高的刚度,可选用高模量碳纤维或硼纤维。
(3)若结构要求有很高的抗冲击性能,可选用玻璃纤维、凯夫拉纤维。
(4)若结构要求有很好的低温工作性能,可选用低温下不脆化的碳纤维。
(5)若结构要求尺寸不随温度变化,可选用凯夫拉纤维或碳纤维。
它们的热膨胀系数可以为负值,可设计成零膨胀系数的复合材料。
(6)若结构要求既有较大强度又有较大刚度时,可选用比强度和比刚度均较高的碳纤维或硼纤维。
树脂选择。
树脂的选择是按如下各种要求选取的:(1) 要求基体材料能在结构使用温度范围内正常工作。
工作温度一般应低于玻璃化温度30℃,模量下降率不应超过8%。
(2) 要求基体材料具有一定的力学性能。
(3) 要求基体材料的断裂伸长率大于或者接近纤维的断裂伸长率。
以确保充分发挥纤维的增强作用。
(4) 要求基体材料具有满足使用要求的物理、化学性能。
物理性能主要指吸湿性,化学性能主要指耐介质、耐候性能要好。
(5) 要求具有一定的工艺性。
主要指粘性、凝胶时间、固化后的尺寸收缩率等。
2 单层的刚度与强度纤维增强复合材料是由两种基本原材料——基体和纤维组成的,构成复合材料的基本单元是单层板(简称单层,又名铺层)。
所以,单层的刚度与强度是分析层合板刚度与强度的基础。
从力学的角度来分析复合材料,依照分析的对象,一般可分为宏观力学方法和细观力学方法。
前者以复合材料的单层、或层合板、或层合板结构作为研究对象,分析复合材料表观的力学性能,忽略两相材料各自的性能差别及其相互作用,而将两相材料的影响反映征平均的表观性能上。
后者是考虑两相材料的各自性能及其相互作用,研究其如何反映在平均的表观性能(即宏观的力学性能)上。
用宏观力学方法分析单层时,是假设单层为连续、均匀、正交各向异性的材料;而在用纫观力学大法分析单层时,除宏观假设与上述相同外,还需纫观假设组分材料分别是均匀(即纫观单层是非均匀的)、连续、各向同性的材料,并将这些分析限于线四性与小变形的范围内。
所谓线弹性,是指材料在外力作用下,其变形与外力成线性变比.且当外力除去后材料能恢复到原来状态。
所渭小变形,是指材料构件在外力作用下的变形与其原始尺寸相比十分微小。
2.1 单层的正轴刚度单层的正细则度是指单层在正轴[即单层材料的那性主方向(见因2—I)]上所显水的刚度性能。
表达刚皮性能的参数是由应力—应变关系所朋定的。
由于踩层的厚度与其仙尺寸相比较小,因此,一般按平而应力状态进行分析。
也就是只考虑单层面内的应力,不考虑牧层而上应力,即认为单层面上应力很小,可以忽略不计。
对于各向同性材料,表达其刚度性能的参数是工程弹性常数z 、”J ,它们分别为拉压弹性模量、剪切弹性模量与泊松比,且三者之间有如下关系:所以,独立的弹性常数只有2个。
而对于呈正交各向异性的单层,表达其刚废性能的工程弹性常数将增加到5个,独立的弹性常数为4个。
2.1.1 单层的正轴应力—应变关系单层在正轴下的平面应力状态只有叭祖2、、2三个应力分量。
本书约定应力的符号规则为,正面正向或奴而负向均为正,否则为负。
所泅叮的正负是指该而外法线方向与坐标方向同向还是反向。
所谓向的正负是指应力方向与坐标方向同向还是反向。
因2—1示出的应力分量均为正。
由于本书讨论的复合材料限于在线弹性与小变形情况下,)1(2ν+=EG所以材料力学中应受的叠加原理仍能适用复合材料。
也即所有应力分量风A、?M引起的某一应变分量等于各个应力分量引起该匝变分量的代数和。
面且,在正轴方向一点处的线虚变q、h只与该点处的正应力叭、纳有关,而与剪应力?。
无关:同时,该点处的剪应变b:也仅与剪废力?m有关。
本书约定应变的符号规则为,线应变伸长为正,缩短为负6剪应变是与两个坐标方向一致的直角变小为正,变大为负。
因此,由σ1引起的应变为由σ2的引起的应变为而由τ12引起的应变为合式(2—2)至式(2—4),利用叠加原理即得单层在正轴方向的应变—应力关系式:应变—应力关系式(2—5)可以写成矩阵形式:其中系数短阵各分显可写成:这些量称为柔员分量。
用柔量分虽表示的应变—应力关系式为由式(2—7)或(2-9)解出引σ1、σ1、τ12,可得到应力—应变关系式:共Lf2系数矩阵各分量与工程弹性常数的关系如—[::这些量豹;为模员分量,其中模量分量与柔量分量之间存在互逆关系:无论是模量分量还是柔量分量,与工程弹性常数一样,一共有5个,但独立的分量也为4个。
同样可以证明,模量分量或柔量分量存在如下的对称性关系式:实际复合材料工程中,还常常坦到一种纵向和横向弹性性能相同的单层,如由,121经纬Z织布形成的单层就是如此。
它的刚皮参数还存在如下关系:这种单层称为正方对称单层。
dJ于这种正方对称单层的工程弹性常数之间多了一个关系式,所以,这种材料66独立弹性常数又减少了一‘个,只有3个。
这种材料的工程抑性常数测3个就够了。
2.1.2 各种复合材料的单层正轴刚度参数各种复合材料测试所得的工程弹性常数(即单层的正油工程弹性常数)见表2—[。
根据式(2—11)计算得到的模员分量(即单层的正铀校量分量)见表2—2。
根据式(2—8)计算得到的柔量分量(即单层的正彻柔员分量)见表2—3。
可以证明,单层的弹性校退、具有巫复—[;标的柔量分显及横员分足均为正佰,即另外,由于QII=’n从,而QlI与儿均为正位,所以pM>o,即式(2—6)、式(2—16)和式(2—20)称作单层为正交各向异性材料时工程弹性常数的限制条件。
这些限制条件用以判断材料加以验数砒或正交各向品性的材料权型是否正确。