超声波加工在模具行业中的应用
先进制造——超声研磨技术

超声研磨加工技术摘要:本文介绍了一种基于新加工原理的先进超精密研磨技术——超声研磨。
首先简要介绍了磨削技术的发展现状并通过加工模型简述了其加工原理;然后从加工工艺及加工设备等方面阐述了其加工特点;最后以其在模具行业的应用为例,从加工设备、工艺分析等方面进行了简要分析。
关键词:超声加工;超声研磨;超精密加工;先进制造技术0、引言随着汽车、航空航天等行业的发展,陶瓷、玻璃、硬质合金等材料应用日益广泛。
这些材料硬度高、零件形状复杂、加工精度高,传统的磨削方式难以满足要求[1]。
超声研磨不仅能加工脆硬金属材料,而且能加工玻璃、陶瓷、半导体等不导电的非金属脆硬材料,特别适合电火花加工或铣削加工表面的研磨,对电火花线切割加工表面的软化层和电火花成型加工表面的硬化层均能快速研磨,改善其表面质量。
1、研磨技术现状相对于传统的研磨技术而言,目前,一些基于机械作用、机械—化学作用的超精密研磨技术以及液面研磨抛光技术的研究应用[2],在超精密磨削方面取得了不错的效果。
其中基于机械作用的弹性发射加工(EEM)兼有研磨和抛光的优点具有光明的发展前景。
然而,这些加工方法存在对加工设备及条件有特殊的要求;难以控制加工精度、表面质量等问题,如基于机械作用的弹性发射加工,需要高速高精度回转轴等,所以在实际应用中受到限制,达不到高的技术经济效果。
超声波研磨是功率超声在材料加工方面的一种重要运用,是一种非接触超精密研磨方法,具有加工表面质量高、精度高、切屑易处理、能很好地解决难加工材料、非金属材料、表面质量要求高的零件加工问题等一系列优点,如今已成为一种新型的先进制造加工技术。
2、超声研磨原理2.1超声研磨理论模型分析超声研磨是超声加工技术的一种特殊应用[3],其基于传统研磨加工原理,在研磨工具上附加以超声振动,工具与工件间的磨料在结合传统研磨加工运动和超声高频振动共同作用下,不断滑擦、磨削加工表面,以实现材料去除的目的,图1为超声研磨原理模型。
超声时效技术在微注塑模具制作中的应用

Da i n Un v riy o c n lg l i e st f Teh oo y,Da in 1 6 2 a la 1 0 4,C i a hn )
*C 0z u h r, - i : u i u @ d u . d . n 0 】 s , g a t o E ma l d lq n r r i lt e u c
E ua in Da inU ies yo eh oo y,D l n 1 2 , hn ; d c t , l nvri f T cn lg o a t a i 0 4 C ia a 1 6 2 .Ke a oao yf rM i o Na oT c n lg n y t o io ig P o ic , yL b r tr o c / n eh oo ya d S s m fL a nn rvn e r e
由 于 S 一 内应 力 过 大 引起 的破 裂 、 U 8胶 变形 甚 至从 基 底 脱 落 等 缺 陷 , 强 了 uv I GA技 术 制 作 微 注 塑 模 具 的 能 力 , 高 增 _I 提
超声波在精密加工中的应用研究

超声波在精密加工中的应用研究超声波技术是一种在材料加工过程中非常重要的工艺技术,它可以增强处理效果,优化工件质量,缩短加工周期,降低能源消耗。
近年来,随着科学技术的进步和工业化生产的不断发展,超声波技术在精密加工领域发挥的作用越来越大。
本文将探讨超声波在精密加工中的应用研究。
一、超声波在金属加工中的应用1. 拉伸加工中的应用超声波在拉伸加工中的应用较为普遍,它可以使金属材料在最小的变形条件下达到极限变形程度。
超声波是基于共振原理,在振幅足够大时,其作用力可以远远超过传统的拉伸加工。
目前,超声波拉伸加工已广泛应用于锻造、压铸、拉伸等金属加工领域。
2. 表面处理中的应用超声波在金属表面处理中的应用主要包括超声波磨料、超声波打磨、超声波除锈等。
这些处理方式可以使金属表面更加平滑,减少金属表面的缺陷,提高金属表面的质量和稳定性。
3. 金属切削加工中的应用超声波在金属切削加工中的应用与其他技术相比具有独特的优势,它可以提高加工质量,缩短加工周期,降低加工成本等。
目前,超声波在金属切削领域已得到广泛应用,如超声波加工中心、超声波切割机、超声波皮带磨削机等。
二、超声波在非金属加工中的应用除了在金属加工中广泛应用之外,超声波技术在非金属加工领域中也发挥了不同的作用。
1. 塑料加工中的应用超声波技术在塑料加工领域中具有广泛的应用前景,主要包括超声波焊接、超声波水处理和超声波清洗等。
这些应用可以提高产品的品质和稳定性,同时缩短生产周期。
2. 陶瓷加工中的应用超声波在陶瓷加工中的应用主要包括超声波破碎、超声波磨料和超声波鼓磨等。
这些应用可以提高陶瓷工件的质量和精度,同时降低加工难度和成本。
三、超声波在医疗领域中的应用除了在工业领域中应用之外,超声波技术在医疗领域中也具有广泛的应用。
超声波在医疗领域中的优点在于非侵入性、无放射性、低成本和可重复使用等方面。
目前,超声波医疗设备已非常普及,主要包括超声波诊断仪、超声波手术机和超声波治疗仪等。
超声波技术在材料加工中的应用

超声波技术在材料加工中的应用随着科技的不断发展,超声波技术在材料加工领域中的应用越来越广泛。
超声波技术通过声学振动来实现材料加工,可以减少加工过程中产生的热度和机械应力,从而有效提高材料的加工质量和效率。
本文将介绍超声波技术在材料加工中的应用,包括超声波切割、超声波焊接、超声波清洗等方面。
超声波切割超声波切割是利用超声波振动的动能,将刃口加速实现高速切割。
传统的机械切割容易引起材料表面的热度升高和材料变形,从而影响加工质量。
而超声波切割由于振动的特性,不会对材料表面产生热度和应力,加工质量更加稳定和可靠。
超声波切割主要应用于金属、玻璃、陶瓷等硬质材料的切割,在航空、汽车、电子、石化等领域都有广泛应用。
超声波焊接超声波焊接是利用超声波振动的作用,将加热的塑料或压接件在一起,实现焊接固化。
传统的热熔焊接方法,容易引起材料的变形和色差。
而超声波焊接利用了振动加热的原理,不仅可以避免热度的损失,而且可以控制加热的范围和速度,从而实现高质量的焊接固化。
超声波焊接主要应用于塑料、橡胶、陶瓷等材料的连接,在汽车工业、电子工业、医疗器械等领域都有广泛应用。
超声波清洗超声波清洗是利用超声波振动的作用,将材料表面的脏物和氧化物清除干净。
传统的喷水清洗方式,容易产生二次污染,同时也会对材料表面产生损伤。
而超声波清洗由于振动的特性,不会对材料表面产生损伤,而且清洗效果更加彻底。
超声波清洗主要应用于化工、食品、制药、电子等领域,可以有效提高产品质量和生产效率。
总之,超声波技术在材料加工领域中的应用,已经成为了一种不可替代的技术手段。
超声波技术不仅可以提高加工过程的质量和效率,而且能够满足人们对新技术、新材料的不断追求,推动着生产技术的提高,为人类的发展带来了新的机遇。
超声波模具的设计原理_概述说明以及解释

超声波模具的设计原理概述说明以及解释1. 引言1.1 概述超声波模具是一种应用超声波技术进行加工和成型的重要设备。
它可以通过超声波的传导和振动作用,有效地加工各种材料,并实现精确的形状控制和高效率生产。
随着现代科学技术的不断进步,超声波模具在许多领域得到了广泛应用,如塑料成型、金属焊接、食品加工等。
1.2 文章结构本文将首先介绍超声波原理简介,包括超声波的基本概念、传播方式以及其与材料相互作用的特点。
接着我们将详细阐述超声波模具的设计要点,包括模具结构、材料选择、连接方式等方面。
然后,我们将深入探讨模具设计原理与超声波相互作用关系,分析超声波对模具加工过程的影响和作用机制。
同时,还会介绍模具制备方法与工艺流程,并提出优化措施以提高生产效率和产品质量。
最后,我们将重点讨论在模具设计中需要考虑材料属性、结构特征、连接方式及节能效果评估等因素和挑战,并给出相应的解决方案。
1.3 目的本文的目的是系统地介绍超声波模具的设计原理、制备方法与工艺流程,分析模具设计中需考虑的因素和挑战,并总结重述主要观点和结果。
同时,对超声波模具设计提出启示和展望,为相关领域研究人员提供参考和借鉴。
通过全面而深入地探讨超声波模具的设计原理和实操经验,我们可以更好地理解超声波技术在工程领域的应用潜力,并为优化设计和改进工艺提供指导。
2. 超声波模具的设计原理2.1 超声波原理简介超声波是指频率高于人类听觉范围(20kHz)的机械振动波。
在超声波模具设计中,利用超声波的特性可以实现高效的材料切割、焊接和成型等工艺。
超声波通过在模具中产生机械振动,将能量传递给材料,从而实现所需的加工过程。
2.2 模具的设计要点在超声波模具设计中,需要考虑以下要点:- 模具形状和尺寸:根据加工要求和材料特性确定模具形状和尺寸,以确保超声波能够有效传递到待加工材料上。
- 超声波振动系统:选择合适的超声波振动系统,并确保其能够输出所需频率和幅度的振动。
超声波加工
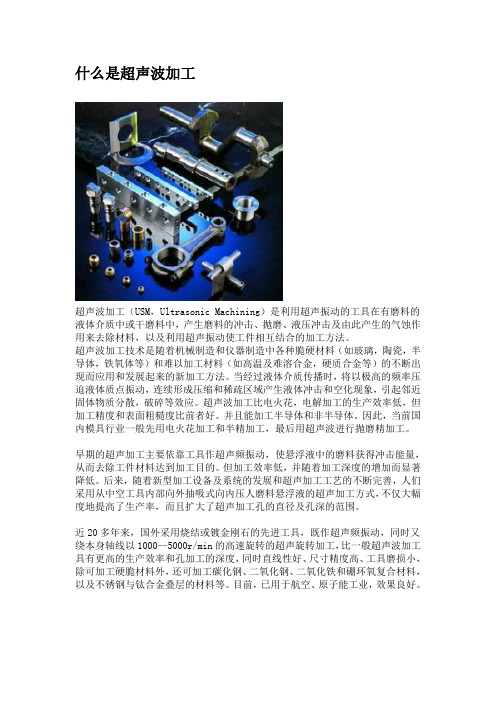
什么是超声波加工超声波加工(USM,Ultrasonic Machining)是利用超声振动的工具在有磨料的液体介质中或干磨料中,产生磨料的冲击、抛磨、液压冲击及由此产生的气蚀作用来去除材料,以及利用超声振动使工件相互结合的加工方法。
超声波加工技术是随着机械制造和仪器制造中各种脆硬材料(如玻璃,陶瓷,半导体,铁氧体等)和难以加工材料(如高温及难溶合金,硬质合金等)的不断出现而应用和发展起来的新加工方法。
当经过液体介质传播时,将以极高的频率压迫液体质点振动,连续形成压缩和稀疏区域产生液体冲击和空化现象,引起邻近固体物质分散,破碎等效应。
超声波加工比电火花,电解加工的生产效率低,但加工精度和表面粗糙度比前者好。
并且能加工半导体和非半导体。
因此,当前国内模具行业一般先用电火花加工和半精加工,最后用超声波进行抛磨精加工。
早期的超声加工主要依靠工具作超声频振动,使悬浮液中的磨料获得冲击能量,从而去除工件材料达到加工目的。
但加工效率低,并随着加工深度的增加而显著降低。
后来,随着新型加工设备及系统的发展和超声加工工艺的不断完善,人们采用从中空工具内部向外抽吸式向内压人磨料悬浮液的超声加工方式,不仅大幅度地提高了生产率,而且扩大了超声加工孔的直径及孔深的范围。
近20多年来,国外采用烧结或镀金刚石的先进工具,既作超声频振动,同时又绕本身轴线以1000—5000r/min的高速旋转的超声旋转加工,比一般超声波加工具有更高的生产效率和孔加工的深度,同时直线性好、尺寸精度高、工具磨损小,除可加工硬脆材料外,还可加工碳化钢、二氧化钢、二氧化铁和硼环氧复合材料,以及不锈钢与钛合金叠层的材料等。
目前,已用于航空、原子能工业,效果良好。
1 超声波加工基本原理加工时工具以一定的静压力作用于工件上,在工具和工件之间加入磨料悬浮液(水或煤油和磨料的混合物)。
超声波换能器产生16kHz以上的超声频轴向振动,并借助变幅杆把振幅放大到0.02~0.08mm,迫使工作液中悬浮的磨粒以很大的速度不断撞击,抛磨被加工表面,把加工区的材料粉碎成非常小的微粒。
超声波加工技术在制造业中的应用及发展
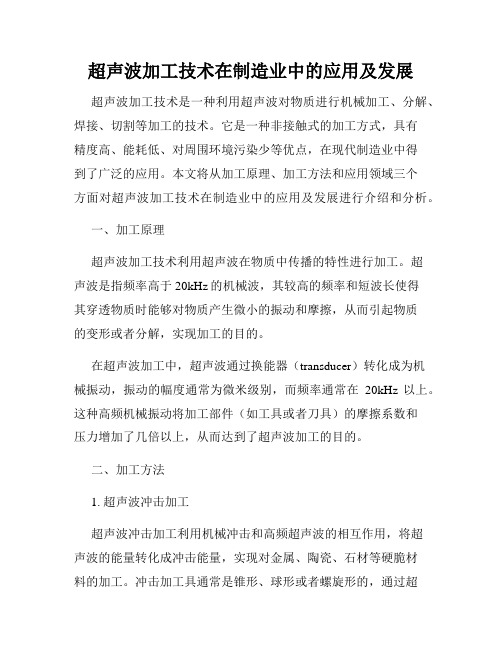
超声波加工技术在制造业中的应用及发展超声波加工技术是一种利用超声波对物质进行机械加工、分解、焊接、切割等加工的技术。
它是一种非接触式的加工方式,具有精度高、能耗低、对周围环境污染少等优点,在现代制造业中得到了广泛的应用。
本文将从加工原理、加工方法和应用领域三个方面对超声波加工技术在制造业中的应用及发展进行介绍和分析。
一、加工原理超声波加工技术利用超声波在物质中传播的特性进行加工。
超声波是指频率高于20kHz的机械波,其较高的频率和短波长使得其穿透物质时能够对物质产生微小的振动和摩擦,从而引起物质的变形或者分解,实现加工的目的。
在超声波加工中,超声波通过换能器(transducer)转化成为机械振动,振动的幅度通常为微米级别,而频率通常在20kHz以上。
这种高频机械振动将加工部件(如工具或者刀具)的摩擦系数和压力增加了几倍以上,从而达到了超声波加工的目的。
二、加工方法1. 超声波冲击加工超声波冲击加工利用机械冲击和高频超声波的相互作用,将超声波的能量转化成冲击能量,实现对金属、陶瓷、石材等硬脆材料的加工。
冲击加工具通常是锥形、球形或者螺旋形的,通过超声波的震动驱动,加工部分会发生爆炸性的形变和裂纹,从而实现加工的目的。
超声波冲击加工的优点是能够进行精细加工,但加工速度较慢,只适用于小加工量的生产。
2. 超声波切割加工超声波切割加工是利用超声波在物质中产生的高频振动,通过对切割工具施加高频振动,实现对材料的切割。
切割工具通常是金属薄板、金属丝、钻头和锯片等。
切割时,超声波的能量通过切割工具传递到材料中,使其发生振动和变形,从而实现切割的目的。
超声波切割加工的优点是能够进行高速切割,不会产生粉尘和机床磨损,但是对材料有一定的厚度限制。
3. 超声波焊接超声波焊接是利用超声波在物质中产生的高频振动,通过对金属表面施加振动,从而实现金属的焊接。
焊接时,将金属部分挤压在一起,在部件接触面上施加高频振动,使金属表面微观颗粒之间不断摩擦和碰撞,达到焊接的目的。
超声振动加工在科研和企业生产中的应用
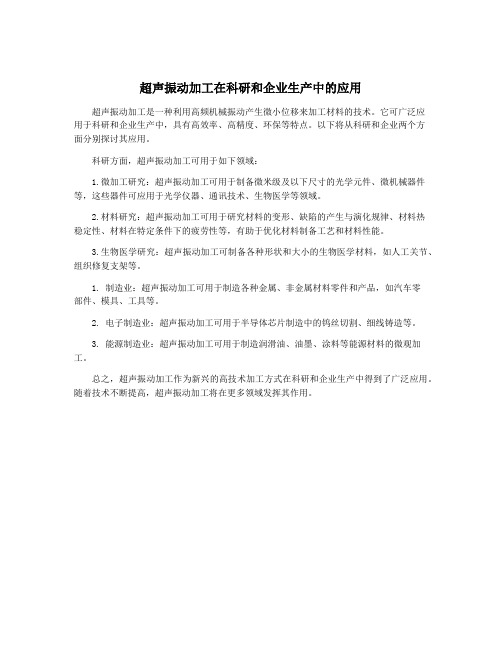
超声振动加工在科研和企业生产中的应用
超声振动加工是一种利用高频机械振动产生微小位移来加工材料的技术。
它可广泛应
用于科研和企业生产中,具有高效率、高精度、环保等特点。
以下将从科研和企业两个方
面分别探讨其应用。
科研方面,超声振动加工可用于如下领域:
1.微加工研究:超声振动加工可用于制备微米级及以下尺寸的光学元件、微机械器件等,这些器件可应用于光学仪器、通讯技术、生物医学等领域。
2.材料研究:超声振动加工可用于研究材料的变形、缺陷的产生与演化规律、材料热
稳定性、材料在特定条件下的疲劳性等,有助于优化材料制备工艺和材料性能。
3.生物医学研究:超声振动加工可制备各种形状和大小的生物医学材料,如人工关节、组织修复支架等。
1. 制造业:超声振动加工可用于制造各种金属、非金属材料零件和产品,如汽车零
部件、模具、工具等。
2. 电子制造业:超声振动加工可用于半导体芯片制造中的钨丝切割、细线铸造等。
3. 能源制造业:超声振动加工可用于制造润滑油、油墨、涂料等能源材料的微观加工。
总之,超声振动加工作为新兴的高技术加工方式在科研和企业生产中得到了广泛应用。
随着技术不断提高,超声振动加工将在更多领域发挥其作用。
- 1、下载文档前请自行甄别文档内容的完整性,平台不提供额外的编辑、内容补充、找答案等附加服务。
- 2、"仅部分预览"的文档,不可在线预览部分如存在完整性等问题,可反馈申请退款(可完整预览的文档不适用该条件!)。
- 3、如文档侵犯您的权益,请联系客服反馈,我们会尽快为您处理(人工客服工作时间:9:00-18:30)。
超声波加工在模具行业中的应用传统的机械加工技术对推动人类的进步和社会的发展起到了重大的作用。
随着科学技术的迅速发展,新型工程材料不断涌现和被采用,工件的复杂程度以及加工精度的要求越来越高,对机械制造工艺技术提出了更高的要求。
由于受刀具材料性能、结构、设备加工能力的限制,使用传统的切削加工方法很难完成,为了解决这些加工的难题,新型特种加工方法应运而生。
各种硬脆材料和硬脆复合材料很难用传统刀具进行加工,因而往往采用非传统的工艺方法进行加工,这些非传统工艺方法多数直接使用各种能量,如超声波加工和激光加工等。
超声波加工始于1927年,几十年来,超声加工技术的发展迅速,在超声振动系统、超声复合加工等领域均有较广泛的研究和应用,尤其是在难加工材料领域解决了许多关键性的工艺问题,如玻璃、陶瓷、石英、金刚石、硅等,取得了良好的效果一、超声波加工的系统构成:在工件和工具间加入磨料悬浮液,由超声波发生器产生超声振动波,经换能器转换成超声机械振动,使悬浮液中的磨粒不断地撞击加工表面,把硬而脆的被加工材料局部破坏而撞击下来。
在工件表面瞬间正负交替的正压冲击波和负压空化作用下强化了加工过程。
因此,超声波加工实质上是磨料的机械冲击与超声冲击及空化作用的综合结果。
超声波加工系统由机床、超声波电源、超声振动系统、主轴旋转系统、主轴轴向进给系统、轴向力反馈保护系统等组成,其中超声振动系统是超声加工设备的核心部分,由换能器、变幅杆和工具头等部分组成。
下面将系统的各个部分分别介绍。
1.1 超声波换能器超声波换能器的作用是将高频电振动转变为机械振动。
实现这种转变主要采用以下2种方法。
1)磁致伸缩法:某些铁磁体或铁氧化体在变化的磁场中,由于磁场的变化,其长度也发生变化的现象,称为磁致伸缩效应。
磁致伸缩换能器因为具有较低的Q 值(Q是能量峰值的锐度) ,所以它能传递很宽的频率。
这使变幅杆设计的灵活性增大,也使与变幅杆连接在一起的刀具允许在加工中磨损后可重磨。
磁致伸缩换能器工作时会大量生热,产生较大的电能损失,且使电声转换效率降低。
2)压电效应法:利用压电晶片在外电场中随电场方向的改变而形变发生相反变化的压电效应原理,将高频电振动转变为机械振动的器件称为压电换能器。
压电换能器电声转换效率高,不易有热量损失,不需要任何冷却措施,适应旋转操作,生产容易;但要加工0.1~1 GHz级的超高频超声波换能器是很困难,日本中村等提出用钛扩散、周期地形成自发极化反相区域,同时在表面配置叉指电极作成新型超高频超声换能器,可得到变换损失低于5.5dB、相对带宽为0.9的宽频带横波超声换能器。
1.2 变幅杆及工具:变幅杆的作用是将来自换能器的超声振幅由0.005 mm~0.01 mm放大至0.01mm~0.1 mm,以便进行超声波加工。
变幅杆之所以能放大振幅,是由于通过其任一截面的振动能量是不变的(传播损耗不计) ,截面小的地方能量密度大,振动振幅也就越大。
在进行大功率的超声加工及精密加工时,往往将变幅杆与工具设计制成一个整体;在进行小功率的超声加工及加工精度不高时,则将变幅杆与工具设计制成可拆卸式。
目前,对超声变幅杆的研究和优化已广泛应用了CAD /CAM技术和有限元分析技术。
如使用ANSYS软件对变幅杆进行优化:首先分析需要的所有数据(材料属性、频率范围等) ,定义结构的几何形状;然后求解,计算固有频率、位移、应变和应力;最后是估计分析结果和画出应力曲线工具是变幅杆的负载,其结构尺寸、质量大小以及与变幅杆连接的好坏,对超声振动共振频率和超声波加工性能均有很大影响。
工具可以通过焊接或螺钉固定在变幅杆上;也可以和变幅杆设计成整体。
采用可拆卸式,虽然能快速更换工具,但可能出现工具松懈、超声能量损失、疲劳破坏等问题。
二、超声波振动加工的研究状况2.1 超声振动加工国外研究状况:超声振动切削作为新兴的特种加工技术,引起了国内外专家学者的广泛兴趣和极大关注。
最早对振动切削进行比较系统的研究、可以称为振动切削理论与应用技术奠基人的是日本学者隈部淳一郎。
他在20世纪50—60年代发表了许多振动切削方面的论文,系统地提出了振动切削理论,并成功地实现了振动加工等。
随后美国也对振动切削进行研究,到20世纪70年代中叶,振动车削、振动钻孔、光整加工等均已达到实用阶段,取得了一系列研究成果,并在生产中得到推广应用。
俄罗斯科学院和英国拉伯运大学对超声振动切削的非线性过程进行了深入研究,利用流变模型对超声振动切削实验结果进行了理论解释。
通过对超声切削的动力学研究,得到了振动工具的非线性振幅特性曲线,并讨论了超声振动切削的优越性及其应用领域。
英国阿伯丁大学国王学院研究了超声钻削难加工材料时工艺参数对材料去除率的影响 ,建立了间断性冲击过程的非线性模型,对冲击力的特性进行了分析,提出了一种新的材料去除率的计算方法,这种方法首次解释了材料去除率在较高的静态力作用下减小的原因。
美国内布拉斯加大学和内华达大学对Al2O3 陶瓷材料微去除量精密超声加工技术进行了研究。
通过模拟陶瓷材料超声加工的力学特性对材料去除机制进行分析,研究发现,低冲击力会引起陶瓷材料结构的变化和晶粒的错位,而高冲击力会导致中心裂纹和凹痕。
美国内布拉斯加大学还第一次分析了Al2O3 陶瓷精密超声加工的机理、过程动力学以及发展趋势,并详细讨论了超声技术在陶瓷加工方面的应用情况。
2.2 超声振动加工国内的研究状况:山东大学对工程陶瓷的超声振动钻削加工曾进行过深入探索【2】了超声振动钻削中各项工艺参数对加工效果的影响,并从理论上分析了超声振动钻削时的材料去除机理。
上海交通大学也对超声椭圆振动切削技术进行了研究,概述了超声波椭圆振动切削原理和刀具椭圆振动系统,分析了超声波椭圆振动切削运动特性,详细介绍了超声波椭圆振动切削的实际切削效果。
长春汽车工业高等专科学校采用超声振动切削方法对一汽变速箱厂生产的一种直齿齿轮的滚齿加工进行了工艺实验,通过生产现场各种工艺参数实验及小批量试生产,收到了令人满意的效果,具有较好的发展前景。
北京航空航天大学和哈尔滨工业大学将超声振动引入普通聚晶金刚石(PCD)的研磨加工,显著地提高了研磨效率,并在分析PCD材料的微观结构和去除机理的基础上,对PCD超声振动研磨机理进行了深入研究。
研究指出,研磨轨迹的增长和超声振动脉冲力的作用是提高研磨效率的根本原因。
工程陶瓷的应用日益广泛,但其成形加工十分困难。
尤其是具有三维复杂型面的工程陶瓷零件至今尚无有效的加工手段,严重影响了工程陶瓷材料的推广应用。
大连理工大学提出了基于分层去除技术的超声铣削加工方法,研制了超声数控铣削机床,开辟了利用超声加工技术数控加工工程陶瓷零件的途径。
基于分层去除思想的超声铣削加工技术,解决了传统超声加工中工具损耗严重且不能在线补偿的难题,使加工带有尖角和锐边的三维复杂型面工程陶瓷零件成为可能,为工程陶瓷的广泛应用提供了有力的技术支持。
超声波椭圆振动切削已受到国际学术界和企业界的重视。
美国、英国、德国和新加波等国的大学以及国内的北京航空航天大学和上海交通大学已开始这方面的研究工作。
日本企业界如日立、多贺和Towa公司等已开始这方面的实用化研究。
但是,超声波椭圆振动切削在理论和应用方面还有许多工作要做。
尤其是对硬脆性材料的超精密切削加工、微细部位和微细模具的超精密切削加工等方面还需要进一步研究。
三、超声波复合加工的研究状况:将超声加工与其他加工工艺组合起来的加工模式,称为超声复合加工。
超声复合加工,强化了原加工过程,使加工的速度明显提高,加工质量也得到不同程度的改善,实现了低耗高效的目标。
将超声加工与其他加工工艺组合起来的加工模式,称为超声复合加工。
超声复合加工,强化了原加工过程,使加工的速度明显提高,加工质量也得到不同程度的改善,实现了低耗高效的目标。
热物理作用,与光刻加工相比又可加工高深宽比三维形状,这决定了超声加工技术在陶瓷、半导体硅等非金属硬脆材料加工方面有着得天独厚的优势。
随着东京大学生产技术研究所增泽研究室对微细工具的成功制作及微细工具装夹、工具回转精度等问题的合理解决,采用工件加振的工作方式在工程陶瓷材料上加工出了直径最小为<5μm的微孔,从而使超声加工作为微细加工技术成为可能。
在微小三维型面的加工中,利用简单形状电极、基于分层制造原理的微细电火花铣削技术正在受到重视,但该工艺加工效率偏低,同时由于其加工精度主要依赖于电极损耗的轴向补偿,而电极损耗的轴向补偿量则直接取决于电极损耗率,提高微细电火花铣削的加工效率和稳定性是一个重要的课题。
哈尔滨工业大学提出了超声辅助分层去除微细电火花加工技术,电极轴向的小幅超声振动对活化极间状、拉大极间间隙、增加排屑能力、提高有效脉冲利用率和放电稳定性等起到了极为重要的作用,因此该技术能改善微细电火花铣削时的放电状态,提高加工效率。
随着科学技术的发展,人们开始探索对环境污染少甚至没有污染的加工方法,研究新的工作介质是解决这个问题的关键。
山东大学的研究人员将超声振动引入气中放电加工技术,并对工程陶瓷进行了加工实验研究,加工效率提高了近3倍。
但该工艺的加工机理有待于进一步研究。
此外,超声加工技术在迅猛发展的汽车工业中已有非常广泛的应用,目前主要用于精密模具的型孔、型腔加工,难加工材料的超声电火花和超声电解复合加工,塑料件的焊接,以及清洁度要求较高的小孔窄缝零件的清洗。
可以推断,超声加工技术在世界汽车工业中将发挥越来越重要的作用。
综上所述,一方面需要推动和促进超声加工技术的发展,另一方面,超声加工技术提供的强有力加工手段,又促进了新材料的发展。
在材料加工研究方面取得的可喜成果,印证了超声加工技术是非常有效的加工手段。
可以预见:随着科学技术的不断发展,超声加工技术会在不断完善的过程中,向着高精度、微细化方向发展,真正成为一项有效的精密、超精密加工技术。
参考文献:1.曹凤国,张勤俭.超声加工技术[M].化学工业出版社.北京:2004,186-190.2.V.K1Astashev1etc.Ultrasonic Cutting as aNonlinear Process [ J ].Ultrason,1988:36:89-963.张勤河.声振动钻削加工陶瓷的研究[J].技术新工艺,1997,1,19-214.马春翔,胡德金.超声波椭圆振动切削技术[J].机械工程学报.2003,39:67-70。