锻件超声波探伤仪纵波探伤技术
第八章 锻件与铸件超声波探伤

D f
空心圆柱体:
20 lg
PB 2x d 20 lg 10 lg ( x 3N ) Pf D D f 2
试块调节法(用于X<3N) : 要求CSⅠ试块上Φ2平底孔声程等于或大于锻件厚度; 当试块平底孔声程小于工件时要进行计算求得声程引起的回波高差进 行修正得到检测灵敏度。
• 试块CSⅠ
试块序号 L D
CSⅠ-1 50 50
CSⅠ-2 100 60
CSⅠ-3 150 80
CSⅠ-4 200 80
试块CSⅡ
试块序号 CSⅡ-1
孔径 φ2
检测距离L 1 2 3 4 5 6 7 8 9
CSⅡ-2
CSⅡ-3 CSⅡ-4
φ3
φ4 φ6
5
10
15
20
25
30
35
40
45
试块CS Ⅲ
•
• • •
检测面选择:应符合JB/T4730标 准的要求。 原则上应从两个相互垂直的方向 进行检测,尽可能地检测到锻件 的全体积。主要检测 斜探头:周向、轴向各正、反二 个方向。 注:↑为应检测方向; ※为参考 检测方向 锻件厚度超过400mm时,应从相 对两端面进行100%的扫查。 检测时机:检测原则上应安排在 热处理后,孔、台等结构机加工 前进行,检测面的表面粗糙度 Ra≤6.3μm。 材质衰减测定
8.2 铸件超声波探伤
8.2.6 距离—波幅曲线测试与灵敏度调整 1)纵波直探头距离—波幅曲线制作 2)纵波双晶探头 3)横波斜探头 8.2.7 缺陷的判别与测定 1)缺陷判别 缺陷回波幅度大于或等于距离—波幅曲线位置; 底面回波幅度降低量≥12dB的位置; 不论缺陷回波幅大小,凡出现线状和片状特征缺陷显示的位置。 2)缺陷测定 平面型缺陷:对具有线状和片状特征的缺陷显示,用6dB法画出缺陷范 围,测出长度、面积; 非平面型缺陷:缺陷回波幅度等于或大于距离—波幅曲线者用6dB法在 探伤面画出缺陷范围; 用底面回波降低量≥12dB时,以底面回波降低12dB为条件作为缺陷边 界,划出探伤面上位置。
锻钢件的超声波探伤检查方法缺陷等级分类及判定标准

锻钢件的超声波探伤检查方法缺陷等级分类及判定标准1•目的规范公司锻钢件的超声波探伤检查方法,规范缺陷等级分类及判定标准2•内容2.1探伤装置使用脉冲反射式超声波探伤仪。
2.2探伤方法原则上采用单晶头垂直探伤法。
但是精密探伤及有特殊要求的部位,将同时采用其他探伤方法。
2.3探伤方向及探伤范围按下表实施探伤。
但是,认定有缺陷等异状时,必须从所有方向开始探伤。
探伤方向及扫查范围向:对半圆周进行全面探伤。
但小齿轮、螺纹轴、蜗轮、辊子等表层附近特别重要的锻钢件,要从整周开始进行全面探伤。
轴类锻钢件径向:外周全面探伤轴向:从两个方向进行全面探伤轴向:从两个方向开始进行全面探伤从长度方向,宽度方向,板厚方向三个方向开始进行全面探伤。
但齿条等表层附近特别重要的锻钢件,三个方向均需从两面开始全面探伤。
径向:对外周进行全面探伤轴向:从一个方向开始全面探伤。
但是,齿圈等表层附近特别重要的锻钢件要从两个方向起全面探伤。
径向:对外周进行全面探伤轴向:从一个方向开始全面探伤。
但是,齿轮、车轮等表层附近特别重要的锻钢件要从两个方向起全面探伤。
探伤表面的表面粗糙度要达至【Ra12.5以上较好精加工状态。
2.5测量范围的调整原则上,测定范围要调整至底面回波在显示屏时间轴上显现2次。
2.6探伤方式、使用频率和使用探头探伤方式,使用频率和使用探头见下表。
2.7探伤灵敏度的设定2.7.1底面回波方式的灵敏度设定⑴直径或壁厚在2mm以下的部位,将各不同直径或壁厚的致密部位上第1次底面回波高度(BG)调整至探伤仪显示器刻度板的80%。
然后,根据图4进行灵敏度的增幅,以此作为探伤起始灵敏度。
另外,对于超过检查部位的壁厚1/2以上的区域进行探伤时,需要进一步提高灵敏度12dB进行探伤。
关于小齿轮、螺纹轴、蜗轮、齿轮、齿条、车轮等表层附近特别重要的锻钢件,则用提高了12dB后的灵敏度进行全面或是从两面开始探伤。
⑵试验部位的壁厚超过2m时,使用探头专用的DGS曲线图。
关于锻件超声波探伤的标准及规程
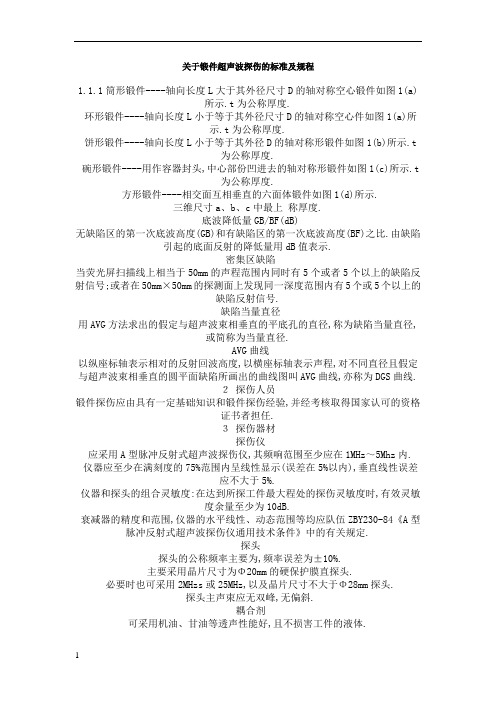
关于锻件超声波探伤的标准及规程1.1.1筒形锻件----轴向长度L大于其外径尺寸D的轴对称空心锻件如图1(a)所示.t为公称厚度.环形锻件----轴向长度L小于等于其外径尺寸D的轴对称空心件如图1(a)所示.t为公称厚度.饼形锻件----轴向长度L小于等于其外径D的轴对称形锻件如图1(b)所示.t为公称厚度.碗形锻件----用作容器封头,中心部份凹进去的轴对称形锻件如图1(c)所示.t为公称厚度.方形锻件----相交面互相垂直的六面体锻件如图1(d)所示.三维尺寸a、b、c中最上称厚度.底波降低量GB/BF(dB)无缺陷区的第一次底波高度(GB)和有缺陷区的第一次底波高度(BF)之比.由缺陷引起的底面反射的降低量用dB值表示.密集区缺陷当荧光屏扫描线上相当于50mm的声程范围内同时有5个或者5个以上的缺陷反射信号;或者在50mm×50mm的探测面上发现同一深度范围内有5个或5个以上的缺陷反射信号.缺陷当量直径用AVG方法求出的假定与超声波束相垂直的平底孔的直径,称为缺陷当量直径,或简称为当量直径.AVG曲线以纵座标轴表示相对的反射回波高度,以横座标轴表示声程,对不同直径且假定与超声波束相垂直的圆平面缺陷所画出的曲线图叫AVG曲线,亦称为DGS曲线.2探伤人员锻件探伤应由具有一定基础知识和锻件探伤经验,并经考核取得国家认可的资格证书者担任.3探伤器材探伤仪应采用A型脉冲反射式超声波探伤仪,其频响范围至少应在1MHz~5Mhz内. 仪器应至少在满刻度的75%范围内呈线性显示(误差在5%以内),垂直线性误差应不大于5%.仪器和探头的组合灵敏度:在达到所探工件最大程处的探伤灵敏度时,有效灵敏度余量至少为10dB.衰减器的精度和范围,仪器的水平线性、动态范围等均应队伍ZBY230-84《A型脉冲反射式超声波探伤仪通用技术条件》中的有关规定.探头探头的公称频率主要为,频率误差为±10%.主要采用晶片尺寸为Φ20mm的硬保护膜直探头.必要时也可采用2MHzs或25MHz,以及晶片尺寸不大于Φ28mm探头.探头主声束应无双峰,无偏斜.耦合剂可采用机油、甘油等透声性能好,且不损害工件的液体.4探伤时机及准备工作探伤时机探伤原则上应安排在最终热处理后,在槽、孔、台级等加工前,比较简单的几何形状下进行.热处理后锻件形状若不适于超声波探伤也可在热处理前进行.但在热处理后,仍应对锻件尽可能完全进行探伤.准备工作探伤面的光洁度不应低一地5,且表面平整均匀,并与反射面平等,圆柱形锻件其端面应与轴线相垂直,以便于轴向探伤.方形锻件的面应加工平整,相邻的端面应垂直.探伤表面应无划伤以及油垢和油潜心物等附着物.锻件的几何形状及表面检查均合格后,方可进行探伤.重要区锻件的重要区应在设计图样中或按JB 755-85《压力容器锻件技术条件》予以注明.5探伤方法锻件一般应进行纵波探伤,对简形锻件还应进行横波探伤,但扫查部位和验收标准应由供需双方商定.横波探伤横波探伤应按附录B的要求进行.纵波探伤扫查方法锻件原则上应从两相互垂直的方向进行探伤,尽可能地探测到锻件的全体积,主要探测方向如图2所示,其他形状的锻件也可参照执行.扫查范围:应对锻件整个表面进行连续全面扫查.扫查速度:探头移动速度不超过150mm/s.扫查复盖应为探头直径的15%以上.当锻件探测厚度大于400mm时,应从相对两端面探伤.探伤灵敏度的校验原则上利用大平底采用计算法确定探伤灵敏度,对由于几何形状所限,以及缺陷在近场区内的工件,可采用试块法(见附录A).用底波法校正灵敏度,校正点的位置应选以工件上无缺陷的完好区域.曲面补偿:对于探测面是曲面而又无法采用底波法的工件,应采用曲率与工件相同或相近倍)的参考试块(见附录A);或者采用小直径晶片的探头,使其近场区的长度小于等于1/4工件半径,这样可不需进行曲面补偿.探伤灵敏度不得低于Φ2mm当量直径.缺陷当量的确定采用AVG曲线及计算法确定缺陷当量.计算缺陷当量时,当材质衰减系数超过4dB/m时,应考虑修正.材质衰减系数的测定a. 应在被测工件无缺陷区域,选取三处有代表性的闰,求B1/B2的值,即第一次底波高度(B1)与第二次底波高度(B2)之比的dB差值.b. 衰减系数a(dB/m)的计算为式中 T----声程,m.AVG曲线图见附录C.灵敏度的重新校验除每次探伤前应校准灵敏度外,遇有下述情况时,必须对探伤灵敏度进行重新校准.a. 校正后的探头、耦合剂和仪器调节旋钮等发生任何改变时;b. 开路电压波动或操作者怀疑灵敏度有变动时;c. 连续工作4以上;d. 工作结束时.当增益电平降低2dB以上时,应对上一次校准以来所有检查锻件进行复探;当增益电平升高2dB以上时,应对所有的记录信号进行重新评定.6记录记录当量直径超过Φ4mm的单个缺陷的波幅的位置.密集性缺陷:记录密集性缺陷中最大当量缺陷的位置和分布.饼形锻件应记录大于等于Φ4mm当量直径的缺陷密集区.其他锻件应记录大于等于Φ3mm当密集区.缺陷密集区面积以50mm×50mm的方块作为最小量度单位,其边界可由半波高并法决定.应按表2要求记底波降低量衰减系数,若供需双方有规定时,应记录衰减系数.7等级分类单个缺陷反射的等级见表1.表1 单个缺陷反射的等级等级ⅠⅡⅢⅣⅤ缺陷当量直径≤Φ4 >Φ4+(>5~8dB) Φ4+(>8~12dB) Φ4+(>12~16dB) >Φ4+16dB)底波降低量的等级见表2.表2 由缺陷引起底波防低量的等级等级ⅠⅡⅢⅣⅤ底波降低量BG/BF ≤8 >8~14 >14~20 >20~26 >26注: ①在计算缺陷引起的底面反射降低量时,应扣除4dB/m的材质衰减.②表2仅适用于声程大于一倍近场区的缺陷.密集区缺陷等级见表3.表3 密集区缺陷引起的等级等级ⅠⅡⅢⅣⅤ密集区缺陷占探伤总面积百分比H 0 >0~5% >5~10% >10~20% >20%注:表1至表3的等级应作为独立的等级分别使用.如果工件的材质衰减对探伤效果有较大的影响时,应重新进行热处理. 按、、节认定级别的缺陷,如果被探伤人员判定为危害性缺陷时,可以不受上述条文的限制.8探伤报告探伤报告不应少于以下内容.工件情况工件名称、材料牌号、编号、材质衰减、主要部位尺寸草图、探伤面的光洁度.探伤条件探伤仪型号、探头频率、晶片尺寸(k值)、探测方向、探伤灵敏度、参考反射体、耦合剂等.探伤结果8.3.1 缺陷位置、缺陷当量直径、底波降低区及缺陷分布示意图.缺陷等级及其他.探伤人员的资格证号、等级、姓名、报告签发人的资格证号、等级、姓名、日期.附录A试块要求(补充件)远场区使用,探测表面为平面时,应采用CS2型标准试块.近场区使用,探测表面为平面时,应采用CS1型标准试块.探伤面是曲面时,原则上应采用与工件具有大致相当曲率半径的对比试块,其具体形状如图A1.附录B横波探伤(补充件)横波探伤仅适用于内外径之比大于等于75%的环形和筒形锻件.探头探头公称频率主要为,也可用2MHz.探头晶片面积为140-400mm2.原则上应采用K1探头,但根据工件几何形状的不同,也可采用其他的K值探头.参考反射体为了调整探伤灵敏度,利用被探工件壁厚或长度上的加工余部份制作对比试块,在锻件的内外表面,分别沿轴向和周向加工平行的V形槽作为标准沟槽.V形槽长度为25mm,深度为锻件壁厚的1%,角度为60°.也可用其他等效的反射体(如边角反射等).探伤方法扫查方法扫查方向见图B1.探头移动速度不应超过150mm/s.扫查复盖应为探头宽度的15%以上.灵敏度检验从锻件外圆面将探头对准内圆面的标准沟槽,调整增益,使最大反射高度为满幅的80%,将该值在面板上作一点,以其为探伤灵敏度;再移动探头探外圆面的标准沟槽,并将最大反射高度亦在面板上作一点,将以上二点用直线连接并延长,使之包括全部探伤范围,绘出距离---振幅曲线.内圆面探伤时以同一顺序进行,但探头斜楔应与内圆面曲率一致.记录记录超---振幅曲线一半的缺陷反射和缺陷检出位置.附录CAVG 曲线图(参考件)AVG曲线参考图例如下:AVG曲线图必须在CS1和CS2型标准试块上测定后绘制.。
锻件纵波探伤步骤
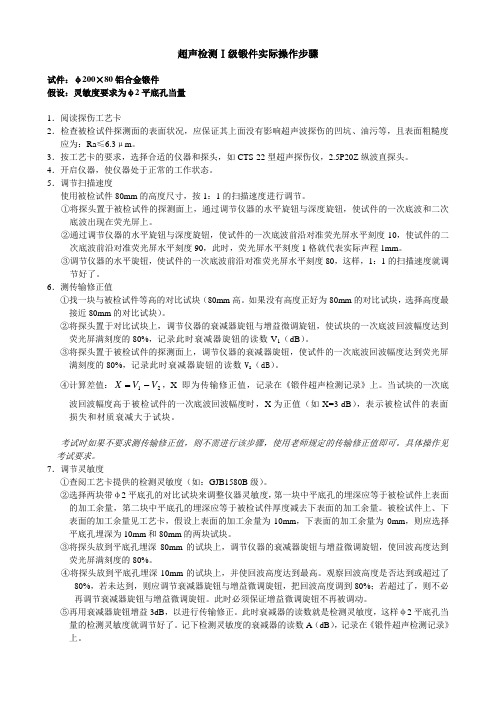
超声检测Ⅰ级锻件实际操作步骤试件:φ200×80铝合金锻件假设:灵敏度要求为φ2平底孔当量1.阅读探伤工艺卡2.检查被检试件探测面的表面状况,应保证其上面没有影响超声波探伤的凹坑、油污等,且表面粗糙度应为:Ra ≤6.3μm 。
3.按工艺卡的要求,选择合适的仪器和探头,如CTS-22型超声探伤仪,2.5P20Z 纵波直探头。
4.开启仪器,使仪器处于正常的工作状态。
5.调节扫描速度使用被检试件80mm 的高度尺寸,按1:1的扫描速度进行调节。
①将探头置于被检试件的探测面上,通过调节仪器的水平旋钮与深度旋钮,使试件的一次底波和二次底波出现在荧光屏上。
②通过调节仪器的水平旋钮与深度旋钮,使试件的一次底波前沿对准荧光屏水平刻度10,使试件的二次底波前沿对准荧光屏水平刻度90,此时,荧光屏水平刻度1格就代表实际声程1mm 。
③调节仪器的水平旋钮,使试件的一次底波前沿对准荧光屏水平刻度80,这样,1:1的扫描速度就调节好了。
6.测传输修正值①找一块与被检试件等高的对比试块(80mm 高。
如果没有高度正好为80mm 的对比试块,选择高度最接近80mm 的对比试块)。
②将探头置于对比试块上,调节仪器的衰减器旋钮与增益微调旋钮,使试块的一次底波回波幅度达到荧光屏满刻度的80%,记录此时衰减器旋钮的读数V 1(dB )。
③将探头置于被检试件的探测面上,调节仪器的衰减器旋钮,使试件的一次底波回波幅度达到荧光屏满刻度的80%,记录此时衰减器旋钮的读数V 2(dB )。
④计算差值:21V V X -=,X 即为传输修正值,记录在《锻件超声检测记录》上。
当试块的一次底波回波幅度高于被检试件的一次底波回波幅度时,X 为正值(如X=3 dB ),表示被检试件的表面损失和材质衰减大于试块。
考试时如果不要求测传输修正值,则不需进行该步骤,使用老师规定的传输修正值即可。
具体操作见考试要求。
7.调节灵敏度①查阅工艺卡提供的检测灵敏度(如:GJB1580B 级)。
锻件与铸件超声波探伤详细教程(附实例解析)重点讲义资料
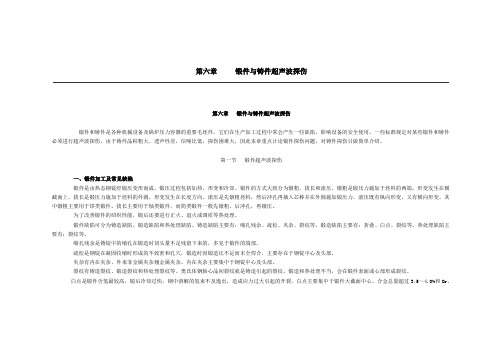
第六章锻件与铸件超声波探伤第六章锻件与铸件超声波探伤锻件和铸件是各种机械设备及锅炉压力容器的重要毛坯件。
它们在生产加工过程中常会产生一些缺陷,影响设备的安全使用。
一些标准规定对某些锻件和铸件必须进行超声波探伤。
由于铸件晶粒粗大、透声性差,信噪比低,探伤困难大,因此本章重点计论锻件探伤问题,对铸件探伤只做简单介绍。
第一节锻件超声波探伤一、锻件加工及常见缺陷锻件是由热态钢锭经锻压变形而成。
锻压过程包括加热、形变和冷却。
锻件的方式大致分为镦粗、拔长和滚压。
镦粗是锻压力施加于坯料的两端,形变发生在横截面上。
拔长是锻压力施加于坯料的外圆,形变发生在长度方向。
滚压是先镦粗坯料,然后冲孔再插入芯棒并在外圆施加锻压力。
滚压既有纵向形变,又有横向形变。
其中镦粗主要用于饼类锻件。
拔长主要用于轴类锻件,而简类锻件一般先镦粗,后冲孔,再镦压。
为了改善锻件的绍织性能,锻后还要进行正火、退火或调质等热处理。
锻件缺陷可分为铸造缺陷、锻造缺陷和热处理缺陷。
铸造缺陷主要有:缩孔残余、疏松、夹杂、裂纹等。
锻造缺陷主要有:折叠、白点、裂纹等。
热处理缺陷主要有:裂纹等。
缩孔残余是铸锭中的缩孔在锻造时切头量不足残留下来的,多见于锻件的端部。
疏松是钢锭在凝固收缩时形成的不致密和孔穴,锻造时因锻造比不足而末全焊合,主要存在于钢锭中心及头部。
夹杂有内在夹杂、外来菲金属夹杂栩金属夹杂。
内在夹杂主要集中于钢锭中心及头部。
裂纹有铸造裂纹、锻造裂纹和热处理裂纹等。
奥氏体钢轴心晶间裂纹就是铸造引起的裂纹。
锻造和热处理不当,会在锻件表面或心部形成裂纹。
白点是锻件含氢最较高,锻后冷却过快,钢中溶解的氢来不及逸出,造成应力过大引起的开裂,白点主要集中于锻件大截面中心。
合金总量超过3.5~4.0%和Cr、Ni、Mn的合金钢大型锻件容易产生白点。
白点在钢中总是成群出现。
二、探伤方法概述按探伤时间分类,锻件探伤可分为原材料探伤和制造过程中的探伤,产品检验及在役检验。
大规格铝合金锻件超声波纵波探伤缺陷判定方法

大规格铝合金锻件超声波纵波探伤缺陷判定方法通过使用不同规格探头、不同类型超声波探伤仪对大规格铝合金锻件进行超声波探伤对比试验,确定了超声波探伤仪在实际应用过程中易产生幻像波的条件,积累了超声波探伤实践经验,避免造成误判现象的发生。
标签:锻件;超声波;幻像波;重复频率前言采用超声波纵波对铝合金锻件进行无损检测是保证锻件产品内部质量最有效的检测手段,依据国家标准GB/T6519-2000《变形铝合金产品超声波检验方法》进行验收。
正常情况下,超声波纵波探伤的缺陷判定方法是在始波与底波中间出现的反射波为缺陷波,但是在探伤实践中我们发现,在始波与底波中间出现的反射波并非一定是缺陷波反射。
在一次供某用户铝合金锻件200多件的A级检测过程中,废品率在80%以上,我们对其中两件不合格品进行定位取样加工,而在精确定位时未发现缺陷,为了得出正确的超声波探伤结果,我们采用不同的超声波探伤仪、不同的探头、设定不同的探伤参数进行超声波探伤对比试验,通过探伤生产实践总结出怎样能正确判定反射波是真实缺陷波的经验。
1 A型超声波纵波脉冲反射法原理A型超声波纵波脉冲反射法是由超声波探头发射脉冲波到试件内部,通过观察来自试件内部缺陷及底面反射波的情况来对试件进行检测的方法。
图1是A 型脉冲反射法探伤的基本原理,当试件中不存在缺陷时,显示图形中仅有发射脉冲T和底面回波B两个信号;当被检试件中存在缺陷时,在发射脉冲与底面回波之間将出现来自缺陷的反射回波F,通过观察F的反射波高度可对缺陷的大小进行评估,再通过观察回波F距发射脉冲的距离,可得到缺陷的埋藏深度。
2 铝合金锻件超声波探伤2.1 探伤灵敏度调试方法——试块比较法按照GB/T 6519-2000《变形铝合金产品超声波检验方法》标准要求:根据被检件上下表面机械加工余量来选择对比试块。
通常应有两块,第一块平底孔的埋藏深度等于被检件上表面机械加工余量,第二块等于被检件的厚度,将两块对比试块平底孔的反射波高分别调到荧光屏满刻度的80%,比较两者的增益(或衰减)dB值,取灵敏度较低者即为检测灵敏度。
锻件超声波探伤方法简介

原材料的缺陷造成的锻件缺陷通常有:
1.表面裂纹:
表面裂纹多发生在轧制棒材和锻制棒材上,一般呈直线 形状,和轧制或锻造的主变形方向一致。造成这种缺陷的原 因很多,例如钢锭内的皮下气泡在轧制时一面沿变形方向伸 长,一面暴露到表面上和向内部深处发展。又如在轧制时, 坯料的表面如被划伤,冷却时将造成应力集中,从而可能沿 划痕开裂等等。这种裂纹若在锻造前不去掉,锻造时便可能 扩展引起 锻件裂纹。
一、锻件加工及常见缺陷
锻造用的原材料为铸锭、轧材、挤材及锻坯。而轧
材、挤材及锻坯分别是铸锭经轧制、挤压及锻造加 工成的半成品。一般情况下,铸锭的内部缺陷或表 面缺陷的出现有时是不可避免的。例如,内部的成 分与组织偏析等。原材料存在的各种缺陷,不仅会 影响锻件的成形,而且将影响锻件的最终质量。 根据不完全的统计,在航空工业系统中,导致航空 锻件报废的诸多原因中,由于原材料固有缺陷引起 的约占一半左右。因此,千万不可忽视原材料的质 量控制工作。
近场区
干涉:频率相同的两列波叠加,使某些区域的振动加强,某
些区域的振动减弱,而且振动加强的区域和振动减弱的区域 相互隔开。这种现象叫做波的干涉。
近场区:波源附近由于波的干涉而出现一系列声压极大极小
值的区域,称为超声波的近场区。 近场区探伤定量是不利的,处于声压极小值处的较大缺陷回 波可能较低,而处于声压极大值处的较小缺陷回波可能较高, 这样就容易引起误判,甚至漏检,因此应尽可能避免在近场 区探伤定量。
轴类锻件的锻造工艺主要以拔长为主,因而
大部分缺陷的取向与轴线平行,此类缺陷的 探测以纵波直探头从径向探测效果最佳,考 虑到会有其他的分布及取向,因此轴类锻件 探伤,还应辅以直探头轴向和斜探头周向探 测及轴向探测。
锻钢件超声波探伤方法

锻钢件超声波探伤方法1996-09-03 发布1997-07-01 实施中华人民共和国机械工业部发布前言本标准非等效采用AS T M A 38 8—84《大型锻钢件超声波探伤方法标准》.本标准力求以规定的检测设备,检测要求,检测方法,保证探伤结果的一致性.大型锻钢件的质量等级分类,由于质量要求差异太大,在本标准中不宜做统一的规定.对锻件的质量验收,由供需双方根据技术要求协商解决.本标准由机械工业部德阳大型铸锻件研究所提出并归口.本标准起草单位:太原重型机械集团公司.本标准主要起草人:宋书林.JB/T 8467-199611 范围本标准规定了锻钢件纵波或横波接触式脉冲反射法超声波探伤方法.本标准适用于厚度或直径等于或大于100 mm碳素钢及低合金钢锻钢件.奥氏体不锈钢锻件的超声波探伤也可参照执行.2 引用标准下列标准所包含的条文,通过在本标准中引用而构成为本标准的条文.本标准出版时,所示版本均为有效.所有标准都会被修订,使用本标准的各方应探讨使用下列标准最新版本的可能性. GB/T 12604.1—90 无损检测术语超声检测JB 4126—84 超声波检验用钢质试块的制造和控制JB 4730—94 压力容器无损检测ZBY 230—84 A型脉冲反射式超声波探伤仪通用技术条件ZBY 231—84 超声波探伤用探头性能测试方法3 定义本标准所用术语除了根据GB/T 12604.1 外,还采用下列定义.3. 1 当量直径在条件相同的情况下,缺陷回波的幅度与超声波束相垂直的某一直径平底孔的回波幅度相等,称该直径为缺陷当量直径,简称为当量直径.3. 2 连续缺陷回波在某个测距上缺陷当量直径不小于 2 mm,回波的波动幅度范围,在探头持续移动距离等于或大于30 mm的间距内不大于2 dB的缺陷回波.3. 3 密集缺陷边长小于或等于50 mm正方体内,有五个或五个以上的缺陷回波.注:译自ASTM A388/A388M—84中8.1.3.2.3. 4 波底降低量BG/BF(dB)无缺陷完好区第一次底波幅度BG值与有缺陷区的第一次底波幅度BF值之比的dB差值.注:根据JB 4730—94 中 3.2.3. 5 单个缺陷回波间距大于50 mm,当量直径不小于2 mm的缺陷回波.3. 6 分散缺陷回波在边长为50 mm正方体内,缺陷回波的数量少于五个,缺陷的当量直径不小于2 mm的缺陷回波.机械工业部1996-09-03 批准中华人民共和国机械行业标准锻钢件超声波探伤方法JB/T 8467-19961997-07-01 实施JB/T 8467-199623. 7 游动缺陷回波在锻件的表面上移动探头,缺陷回波的前沿移动距离相当于锻件厚度25 mm 或25 mm以上的缺陷回波.4 技术要求4. 1 一般要求4. 1. 1 从事大型锻钢件超声波探伤人员,应具有一定的冶炼,锻造,热处理的基础知识和锻件探伤经验,并经过认可的有关部门考核合格,且取得相应等级资格证的探伤人员方可从事锻件的超声波探伤.4. 1. 2 锻件探伤表面,不得有影响探伤灵敏度的附着物,如油漆,氧化皮,污物等.4. 1. 3 锻件探伤面的表面粗糙度Ra值,应不大于6.3 μm.4. 1. 4 锻件探伤应在相互垂直的两个探伤面上进行,应尽可能地对锻件的整体做全面扫查.饼形,长方形锻件,探伤面应选在相互垂直的两个面上.轴类锻件应在外圆表面做径向探测,必要时在轴的端面做轴向探测.4. 1. 5 锻件探伤的钢质对比试块应符合JB 4126 的规定.4. 1.5. 1 纵波直探头平面对比试块,采用CS-1 和CS -2 试块,也可以自行加工,其形状和尺寸应符合有关标准的规定.检测曲面时,采用的曲面对比试块见图 1.注:R为工件曲面半径的0.9~1. 5.图1 曲面对比试块4. 1.5. 2 横波斜探头的对比试块,应采用化学成分,热处理条件,表面粗糙度,曲率等都应与检测锻件相同或相似的锻件制作.4. 1.5. 3 对空心锻件用的对比试块的内壁切成与轴平行的矩形或60°V形槽,其长度为25 mm.推荐槽深为锻件厚度3%的试块.槽深最大不超过6 mm的试块.4. 2 探伤设备和探头4. 2. 1 探伤设备应符合ZBY 230 的规定.4. 2. 1. 1 探伤仪的工作频率至少为1~5 M Hz,配备的衰减器精度在任意相邻12 dB,误差在±1 dB.总调节量应大于60 dB.4. 2. 1. 2 探伤仪的垂直线性至少在屏高的75%范围内,其误差应小于5%.水平线性误差应不大于2%.JB/T 8467-199634. 2. 1. 3纵波直探头探伤发现深度为200 mm,φ2平底孔时,灵敏度余量应不小于40 dB,远场分辨力应大于或等于30 dB.4. 2. 2 探头应符合ZBY 231 的规定.4. 2. 2. 1 纵波直探头的晶片直径为12~28 mm,斜探头晶片最大有效面积为25mm×25 mm ,各种探头都应在标称频率下使用,频率误差不超过标称值的±10%.4. 2. 2. 2 探头的其余参数都应符合ZBY 231 的规定.4. 3 耦合剂推荐采用机油,甘油,有机浆糊.在不影响探伤灵敏度的条件下,也可以采用其他耦合剂.5 探伤要求5. 1 原则上锻件应在最终热处理以后进行超声波探伤.如锻件要在热处理以前进行钻孔,切槽,车锥度等加工工序使探伤受到影响时,锻件也可在此加工工序前进行超声波探伤,热处理以后凡可探测部位,必须进行100%的复探.5. 2 探头扫查速度应不大于150 mm/s.5. 3 探头移动每次至少重叠覆盖晶片宽度的15%.5. 4 对锻件进行复探或重新评定时,应选用可比较的探伤条件.6 探伤方法6. 1 纵波法探伤6. 1. 1 探伤频率通常为1~5 MHz,一般锻件探伤推荐2~2.5 MHz探伤频率.6. 1. 2 探伤灵敏度的调节,原则上推荐底面回波反射法调节.由于锻件的几何形状,尺寸的限制,也可以用对比试块法调节.6. 1. 3 用底面回波反射法调节将探头置于锻件入射面与反射面相平行的探伤面上,且无缺陷和边界反射波.调节探伤仪灵敏度旋钮,将底面回波调到屏高的40%~80%,然后按如下的计算公式调节锻件的增益值:a) 实心锻件的增益值ΔdB = 20lg22πφλT (1)式中:ΔdB——需要提高的增益值,dB;T——探测锻件的厚度或直径,mm;φ——要求探伤灵敏度平底孔直径,mm;λ——波长,mm.b) 有中心孔锻件的增益值ΔdB = 20lg22πφλT-10lgdD (2)式中:D——探测锻件部位的外径,mm;d——探测锻件部位的内径,mm.6. 1. 4 对比试块法调节灵敏度6. 1. 4. 1 使用的对比试块的材质,表面粗糙度,热处理条件应与检测锻件相同或相似.6. 1. 4. 2 用CS -1 或CS-2 对比试块或具有等效作用的其他试块上进行调节.JB/T 8467-199646. 1. 4. 3 按6.1.4.2 选取的CS试块平底孔的反射波调到屏高的40%~80%.6. 1. 5 计算缺陷当量时,锻件的材质衰减超过4 dB/m时,应进行修正. 衰减系数的测定按式(3)计算:α=()TBB2dB621 (3)式中:B1——一次底面回波的dB值;B2——二次底面回波的dB值;T——锻件的厚度,mm;α——衰减系数,dB/mm.6. 1. 6 锻件探伤时,要注意底面回波明显降低的部位,并查明底面回波下降的原因,对底面回波明显下降的任何区域都要复探.6. 2 横波法探伤6. 2. 1 横波探伤主要用于环形或空心锻件,其轴向长度应大于50 mm,外径与内径之比应小于2:1.6. 2. 2 如锻件外径与内径之比或锻件的几何形状不影响所要求的探伤灵敏度时,则采用折射角45°的斜探头探伤.为了用斜探头探测外径与内径之比达2:1 的空心锻件,可在探头上加一个曲面楔块或接触块形成所需的波形和角度,以达到要求的灵敏度.6. 2. 3 横波探伤灵敏度的校正从外圆探测内壁上平行于锻件轴向的矩形或60°V形槽,得到一个满屏高60%的回波.也可以采用单独的对比试块进行校正,对比试块制作与选择应符合 4.1.5 的要求.若锻件成批生产,则取其中一件制成校正用的对比件,在其内壁切一个槽,槽深为工件最大厚度的3%,但最深不得超过 6 mm,槽长为25 mm.对比件的厚度应与被检工件厚度相同.在同一仪器条件下探伤,从外圆上的一个类似槽上得到一个反射回波,通过内,外槽一次反射波峰画一条对比振幅线.如可能,最好在检验件上或其余料上直接切槽.实际探伤中,可能从外圆面上探不出外圆上的槽,如可行(有的锻件内径小,无法探伤),应从内,外表面进行探伤,在外表面探测内表面的槽,在内表面探测外表面的槽.必要与可能时,也可以采用曲面楔块或接触块进行探伤.6. 3 重新调节探伤灵敏度6. 3. 1 锻件探伤过程中,如探头,耦合剂,仪器的设定值有任何改变都要重新调节探伤灵敏度.6. 3. 2 锻件在探伤过程中应至少校验一次探伤灵敏度.在探伤结束后应校验探伤灵敏度.当探伤灵敏度变化2 dB以上时,应重新调节探伤灵敏度.在此之前所探的锻件都要重新复探.7 测量与记录7. 1 纵波缺陷定量采用当量法,横波采用百分比法.7. 2 缺陷当量直径大于或等于探伤灵敏度的单个或分散缺陷回波时,都要记录.7. 3 按技术条件要求记录密集缺陷回波,并标记缺陷的位置和分布范围.7. 4 记录游动缺陷回波的当量直径,位置和分布范围.7. 5 记录底面回波严重降低或消失的部位和分布范围.7. 6 横波探伤,记录不小于对比槽回波幅度60%的缺陷回波的位置和分布范围.JB/T 8467-199658 探伤报告探伤报告应包括如下的内容:8. 1 锻件的名称,材质,尺寸简图,探伤位置,探伤面的粗糙度.8. 2 委托日期,委托单位,委托编号.8. 3 探伤条件:探伤仪的型号,探头的频率,晶片的尺寸,斜探头的K值和β值.8. 4 探伤灵敏度,耦合剂的名称,对比试块的型号.8. 5 探伤结果,评定等级.8. 6 探伤人员的姓名,资格证号,资格等级,复审人员的姓名,资格证号,等级及日期.JB/T 8467-1996中华人民共和国机械行业标准锻钢件超声波探伤方法JB/T 8467-1996。
- 1、下载文档前请自行甄别文档内容的完整性,平台不提供额外的编辑、内容补充、找答案等附加服务。
- 2、"仅部分预览"的文档,不可在线预览部分如存在完整性等问题,可反馈申请退款(可完整预览的文档不适用该条件!)。
- 3、如文档侵犯您的权益,请联系客服反馈,我们会尽快为您处理(人工客服工作时间:9:00-18:30)。
锻件超声波探伤仪纵波探伤技术
要进行锻件超声波探伤首先要了解什么叫锻件,为什么要进行锻压,锻件的种类有哪些,所谓的锻件就是对金属坯料(不含板材)施加外力,使其产生塑性变形、改变尺寸、形状及改善性能,用以制造机械零件、工件、工具或毛坯的成形加工方法。
锻件的种类有:飞机锻件、柴油机船用锻件、兵器锻件、石油化工矿山锻件、核电锻件、火电锻件、水电锻件。
那么要对锻件进行超声探伤,应该如何做呢?
1.锻件超声波探伤仪探伤时机:
探伤原则上应安排在最终热处理后,在槽、孔、台级等加工前,比较简单的几何形状下进行.热处理后锻件形状若不适于超声波探伤也可在热处理前进行.但在热处理后,仍应对锻件尽可能完全进行探伤.
2.锻件超声波探伤仪探伤准备工作:
(1)探伤面的光洁度不应低一地5,且表面平整均匀,并与反射面平等,圆柱形锻件其端面应与轴线相垂直,以便于轴向探伤.方形锻件的面应加工平整,相邻的端面应垂直.
(2)探伤表面应无划伤以及油垢和油潜心物等附着物.
(3)锻件的几何形状及表面检查均合格后,方可进行探伤.
3.锻件超声波探伤探伤方法
锻件一般应进行纵波探伤,对简形锻件还应进行横波探伤,但扫查部位和验收标准应由供需双方商定.
(1)纵波探伤扫查方法
①锻件原则上应从两相互垂直的方向进行探伤,尽可能地探测到锻
件的全体积,主要探测方向如图2所示,其他形状的锻件也可参照执行.
②扫查范围:应对锻件整个表面进行连续全面扫查.
③扫查速度:探头移动速度不超过150mm/s.
④扫查复盖应为探头直径的15%以上.
⑤当锻件探测厚度大于400mm时,应从相对两端面探伤.
(2)探伤灵敏度的校验
①原则上利用大平底采用计算法确定探伤灵敏度,对由于几何形状所限,以及缺陷在近场区内的工件,可采用试块法.
②用底波法校正灵敏度,校正点的位置应选以工件上无缺陷的完好区域.
③曲面补偿:对于探测面是曲面而又无法采用底波法的工件,应采用曲率与工件相同或相近(0.7-1.1倍)的参考试块;或者采用小直径晶片的探头,使其近场区的长度小于等于1/4工件半径,这样可不需进行曲面补偿.
④探伤灵敏度不得低于Φ2mm当量直径.
(3)缺陷当量的确定
①采用A VG曲线及计算法确定缺陷当量.
②计算缺陷当量时,当材质衰减系数超过4dB/m时,应考虑修正.
③材质衰减系数的测定,应在被测工件无缺陷区域,选取三处有代表性的闰,求B1/B2的值,即第一次底波高度(B1)与第二次底波高度(B2)之比的dB差值.。